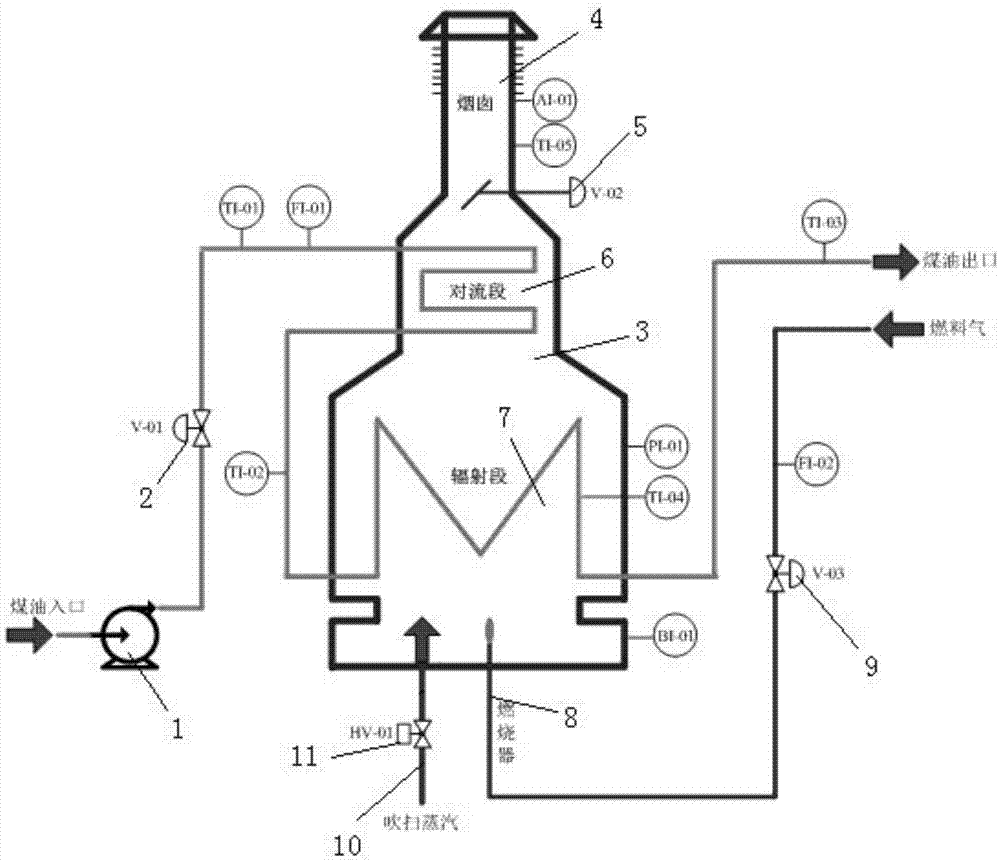
本发明属于加热炉
技术领域:
,涉及管式加热炉及建模仿真方法。
背景技术:
:现有的加热炉仿真装置有两种类型,基于全软件的仿真装置和半实物的仿真装置。全软件的加热炉仿真装置是由东方仿真开发的,仅有加热炉模型,没有外部输入和输出接口,无法和其它控制装置配合使用,灵活性差。半实物的仿真装置是由北京化工大学化工行业系统仿真工程技术中心生产的smpt1000半实物仿真设备,有相应的外部输入和输出接口,但由于是半模拟的仿真装置,有实际的小型工艺装置,包括加热炉等多个装置,占地面积大,价格昂贵,高达近40万,移动不方便,难以普及使用。技术实现要素:本发明的目的在于提供一种管式加热炉及建模方法,本发明的有益效果是采用计算机进行加热炉工作过程的建模,配有外部的输入和输出接口,成本低,灵活性强。本发明所采用的技术方案是包括炉膛,炉膛顶部为烟囱,烟囱下方为对流段,烟囱和对流段之间设有烟气挡板,对流段下方为辐射段,炉膛底部连接燃烧器和吹风装置,燃烧器连接燃料调节阀,燃料调节阀调节燃料气量,吹风装置连接蒸汽吹扫阀,煤油的吸热过程是煤油自对流段进入加热炉,经对流段吸热,再经炉膛的辐射段吸热后出加热炉。管式加热炉的建模方法:(1)加热炉相关数据所述管式加热炉的炉体和烟囱总高15米,被加热物料为煤油,煤油入口温度为240℃,燃料气各组分体积百分比为:ch434.5%,c2h611.3%,c3h86.6%,c4h104.9%,c5h100.7%,h238.2%,n23.8%;炉子稳态热效率为85.5%,空燃比为1.17;加热炉稳态数据包括:煤油对流段出口温度为260℃,出口温度为300℃;燃料的稳态流量为92.58kg/h;煤油稳态流量为30t/h;烟气的燃烧温度为1725℃,烟气进入对流室的温度为530℃,烟气出对流室温度为313℃,炉管表面温度为340℃;(2)加热炉机理建模燃料燃烧总放热分为两部分,一部分是炉内放热,占总热量的85.5%;一部分是由烟气排出,占总热量的14.5%,炉内放热又分为辐射段放热和对流段放热,而煤油吸热包括辐射段吸热和对流段吸热,将加热炉的数学模型分为三部分,分别是燃料燃烧放热、辐射段热交换和对流段热交换;1)燃料燃烧放热燃料气燃烧放出总热量为qgtotal=fmf·qlqgtotal为燃料燃烧放热,fmf为燃料流量,ql燃料气低发热值;2)辐射段热交换烟气的辐射段放热为qgf为燃料燃烧后的烟气在辐射段的放热,tg为烟气出辐射段温度(k),tw为辐射段炉管表面温度(k),kgf为比例系数可表达为kgf=kmg·fmgkmg为比例系数,可由加热炉稳态数据计算得到,fmg为烟气流量,tw是辐射段煤油入口温度和煤油流量的函数,可表达为tw=kwo·fmo+kwf·(fmf)0.8+αwc+273.15kwo,kwf,αwc均为比例系数或常数,由加热炉稳态数据计算得到;tg的计算可表达为tg=273.15+qgtotal/[cpg·(al·ra+1.0)·fmf]al为燃料的理论空气量,根据燃气的成分计算得到,cpg为燃料气的平均比热,ra为过剩空气系数,即实际空气量与理论空气量的比值,ra可表达为ra=a/ala为实际空气量,可表达为kp和δpcon为比例系数和常数,可通过稳态数据得到,vo2为烟气挡板阀的开度,0-100取值,来自外部的模拟量输入信号,δpl为炉膛内外的平均压差kl为系数kl=273·9.8·1.29=3451h为炉膛高度,取15米,采用辐射段烟气出口温度tgfout作为炉膛平均温度,也可直接取为500;烟气流量fmg可表达为fmg=fmf·(al·ra+1)煤油吸热与烟气辐射段放热相同,则煤油出口温度toout计算公式为toout=qgf/(fmo·cpo)+tofintofin为辐射段煤油入口温度,fmo为煤油质量流量,cpo为煤油比热;3)对流段热交换烟气对流段放热可表达为qgd=kc·act·δtkc为对流室总传热系数;act为对流管的表面积,可取为定值;δt为平均温差;kc可表达为hi均为管内传热系数,ri为管内垢层热阻;ho均为管外传热系数,ro为管外垢层热阻;均可通过加热炉稳态数据得到;δt可表达为δt=kdf·fmg·(tgdin-toin)toin为煤油入口温度,也是煤油进入对流室的温度,kdf为比例系数,tgdin为烟气进入对流室的温度,可表达为tgin=ctgd+qgdy/kgdqgdy为烟气进入对流室的热量,为燃料燃烧总放热减去辐射段放热。kgd和ctgd为比例系数和常数,可由加热炉稳态数据得到;煤油吸热与烟气对流段放热相同,则对流段煤油出口温度todout计算公式为todout=qgd/(fmo·cpo)+toin4)炉膛负压和氧含量的计算烟气中的氧含量(xo2)计算公式可以表达为xo2=(ra-1.0)·0.21/[(ra-1.0)+1.10]炉膛压力(p1)计算公式可以表达为p1=-δpl·vo2·100+0.79·fmf附图说明图1是管式加热炉结构示意图;图2是热量传递示意图。图中,1.煤油泵,2.煤油流量调节阀,3.炉膛,4.烟囱,5.烟气挡板,6.对流段,7.辐射段,8.燃烧器,9.燃料调节阀,10.吹风装置,11.蒸汽吹扫阀。具体实施方式下面结合具体实施方式对本发明进行详细说明。1、本发明管式加热炉如图1所示,包括炉膛3,炉膛3顶部为烟囱4,烟囱4下方为对流段6,烟囱4和对流段6之间设有烟气挡板5,对流段6下方为辐射段7,炉膛3底部连接燃烧器8和吹风装置10,燃烧器8连接燃料调节阀9,燃料调节阀9调节燃料气量,吹风装置连接蒸汽吹扫阀11,煤油泵1将煤油抽入炉膛3内,煤油在炉膛内被加热,经过对流段和辐射段。仿真装置的构成包括两大部分,分别是计算机和数据采集卡。计算机用于管式加热炉的数学建模与求解,并进行工艺流程的显示。数据采集卡用于仿真装置与外部设备的信号接口。数据采集卡要求是至少有3个模拟量输入通道、3个模拟量输出通道、1个数字量输出通道、5个数字量输入通道。可以采用多个数据采集卡完成所需的输入和输出。加热物料为煤油,燃料为燃料气。图1中各仪表的位号表示如下:ti-01:煤油入口温度,℃;ti-02:对流段煤油出口温度,℃;ti-03:煤油出口温度,℃;ti-04:辐射段炉管表面温度,℃;ti-05:烟气出口温度,℃;fi-01:煤油入口流量,t/h;fi-02:燃料气流量,kg/h;pi-01:炉膛压力,pa;v-01:煤油流量调节阀;v-02:烟气挡板开度;v-03:燃料气调节阀;hv-01:蒸汽吹扫阀;ai-01:烟气含氧量,%;bi-01:燃烧器火焰指示;本发明中管式加热炉工艺分两路,一路是煤油的吸热过程,一路是燃料气燃烧和烟气的放热过程。燃料燃烧和烟气放热过程是从燃料气燃烧开始,燃烧后的烟气经炉膛3的辐射段进行辐射放热,再到对流段进行对流放热,最后烟气由烟囱4排出;其中bi-01燃烧器的火焰检测,ti-04检测辐射段炉管表面温度,pi-01检测炉膛负压,v-02为烟气挡板阀,用于调节进入加热炉的空气量,ti-05检测烟囱的排烟温度,ai-01检测烟气的氧含量。v-03为燃料气调节阀。fi-02用于检测燃烧气的流量。煤油的吸热过程是煤油自对流段6进入加热炉,经对流段6吸热,再经炉膛3的辐射段7吸热后出加热炉。其中ti-01检测煤油入口温度,ti-02检测煤油辐射段7入口或对流段6出口温度,ti-03用于检测煤油出口温度。fi-01检测煤油入口的流量。v-01用于调节煤油入口的流量。v-01、v-02和v-03的开度由数据采集卡的模拟量输入通道接收外部的4-20ma信号或1-5v进行控制,开度范围均为0-100%。ti-03、fi-01和pi-01的数据经数据采集卡的模拟量输出通道转换。2、管式加热炉的数学建模(1)加热炉相关数据本设计中管式加热炉的炉体和烟囱总高15米,被加热物料为煤油,煤油入口温度为240℃。燃料气成分主要含甲烷和氢气,各组分体积百分比如下表。组分ch4c2h6c3h8c4h10c5h10h2n2百分比%34.511.36.64.90.738.23.8炉子稳态热效率为85.5%,空燃比为1.17。加热炉稳态数据包括:1)煤油对流段出口温度为260℃,出口温度为300℃;2)燃料的稳态流量为92.58kg/h;3)煤油稳态流量为30t/h;4)烟气的燃烧温度为1725℃,烟气进入对流室的温度为530℃,烟气出对流室温度为313℃。炉管表面温度为340℃。(2)加热炉机理建模加热炉的数学建模是基于热量平衡,图2所示为热传递示意图。燃料燃烧总放热分为两部分,一部分是炉内放热,占总热量的85.5%;一部分是由烟气排出,占总热量的14.5%。炉内放热又分为辐射段放热和对流段放热,而煤油吸热包括辐射段吸热和对流段吸热。将加热炉的数学模型分为三部分,分别是燃料燃烧放热、辐射段热交换和对流段热交换。1)燃料燃烧放热燃料气燃烧放出总热量为qgtotal=fmf·qlqgtotal为燃料燃烧放热,fmf为燃料流量,ql燃料气低发热值;2)辐射段热交换烟气的辐射段放热为qgf为燃料燃烧后的烟气在辐射段的放热,tg为烟气出辐射段温度(k),tw为辐射段炉管表面温度(k),kgf为比例系数可表达为kgf=kmg·fmgkmg为比例系数,可由加热炉稳态数据计算得到,fmg为烟气流量,tw是辐射段煤油入口温度和煤油流量的函数,可表达为tw=kwo·fmo+kwf·(fmf)0.8+αwc+273.15kwo,kwf,αwc均为比例系数或常数,由加热炉稳态数据计算得到;tg的计算可表达为tg=273.15+qgtotal/[cpg·(al·ra+1.0)·fmf]al为燃料的理论空气量,根据燃气的成分计算得到,cpg为燃料气的平均比热,ra为过剩空气系数,即实际空气量与理论空气量的比值,ra可表达为ra=a/ala为实际空气量,可表达为kp和δpcon为比例系数和常数,可通过稳态数据得到,vo2为烟气挡板阀的开度,0-100取值,来自外部的模拟量输入信号,δpl为炉膛内外的平均压差kl为系数kl=273·9.8·1.29=3451h为炉膛高度,取15米,采用辐射段烟气出口温度tgfout作为炉膛平均温度,也可直接取为500;烟气流量fmg可表达为fmg=fmf·(al·ra+1)煤油吸热与烟气辐射段放热相同,则煤油出口温度toout计算公式为toout=qgf/(fmo·cpo)+tofintofin为辐射段煤油入口温度,fmo为煤油质量流量,cpo为煤油比热;3)对流段热交换烟气对流段放热可表达为qgd=kc·act·δtkc为对流室总传热系数;act为对流管的表面积,可取为定值;δt为平均温差;kc可表达为hi均为管内传热系数,ri为管内垢层热阻;ho均为管外传热系数,ro为管外垢层热阻;均可通过加热炉稳态数据得到;δt可表达为δt=kdf·fmg·(tgdin-toin)toin为煤油入口温度,也是煤油进入对流室的温度,kdf为比例系数,tgdin为烟气进入对流室的温度,可表达为tgin=ctgd+qgdy/kgdqgdy为烟气进入对流室的热量,为燃料燃烧总放热减去辐射段放热。kgd和ctgd为比例系数和常数,可由加热炉稳态数据得到;煤油吸热与烟气对流段放热相同,则对流段煤油出口温度todout计算公式为todout=qgd/(fmo·cpo)+toin4)炉膛负压和氧含量的计算烟气中的氧含量(xo2)计算公式可以表达为xo2=(ra-1.0)·0.21/[(ra-1.0)+1.10]炉膛压力(p1)计算公式可以表达为p1=-δpl·vo2·100+0.79·fmf(3)加热炉数学模型计算过程和计算步骤1)按采样周期定时读取v-01、v-02和v-03的数据,计算各阀的开度;2)计算煤油流量fmo和燃料流量fmf;由模拟量输入通道读取v-01、v-03的数据作为阀开度,按直线阀计算煤油流量和燃料流量;3)计算燃料产生的总热量qgtotal;4)计算炉膛压力pl、空气量a、过剩空气系数ra、氧含量和烟气流量fmg;5)计算燃烧温度tg和管壁温度tw;6)计算辐射段放热qgf;7)计算对流段传热系数hi、ho,计算总换热系数kc和平均温差δt;8)计算对流段传热量qgd;9)根据qgd和qgf分别计算对流段煤油出口温度todout和辐射段煤油出口温度toout;10)按照一阶惯性环节对各部分温度进行处理,模拟实际温度上升过程。(2)规定的加热炉开车步骤1)检查所有阀全部关闭关闭阀门v-01、v-02、v-03、hv-01。2)将v-01开到10%,或煤油流量大于4t/h。3)将烟气挡板阀v-02开到50%。4)打开hv-01,进行蒸汽吹扫3分钟,3分钟后观察氧含量不低于15%,否则继续吹扫。5)关闭蒸汽hv-01。6)将v-03开到10%,按下点火按钮,进行点火。观察火焰检测bi-01是否有火焰指示,有则进行下一步,无则关闭v-03,返回到4)。7)提升负荷观察加热炉出口温度达到300℃度左右,调整v-01,使煤油流量增大到30t/h。8)稳定工况调整v-03开度,直到煤油出口温度上升并稳定到300℃左右,炉膛压力为负,烟气氧含量为1%-3%,则可认为开车过程结束。(3)规定的加热炉停车步骤1)关闭燃料气阀门v-03。2)等待煤油温度降到240℃左右,关闭煤油流量阀v-01。3)打开蒸汽阀hv-01吹扫3分钟,3分钟后观察氧含量不低于15%,否则继续吹扫。4)关闭蒸汽阀hv-01。以上所述仅是对本发明的较佳实施方式而已,并非对本发明作任何形式上的限制,凡是依据本发明的技术实质对以上实施方式所做的任何简单修改,等同变化与修饰,均属于本发明技术方案的范围内。当前第1页12