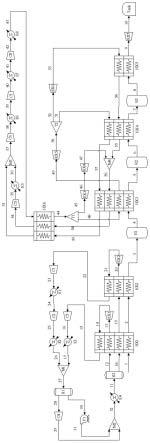
1.本发明涉及一种基于混合制冷剂预冷的氢液化系统及工艺,属于氢气液化技术领域。
背景技术:2.化石能源的过度使用已经带来了诸如环境污染和全球变暖等问题。在未来,使用清洁的可再生能源代替化石能源被认为是解决上述问题的一个重要的措施。氢气一种绿色和高效的可再生能源,具有来源广泛,能量密度大和燃烧热值高等优点,被视为最具有潜力的清洁能源,将在未来的能源结构中占主导地位。然而,较低的体积能量密度成为氢气长期储存和长距离运输的主要障碍。氢气的体积能量密度可以被增加当它被液化时。在环境条件下,液氢的体积能量密度为8.5mj/l。此外,液氢的体积是氢气的800倍,其输送效率可以提高6-8倍,因此非常便于运输和长期储存。然而,氢气的液化需要消耗大量的能量由于较低的温度。在理想情况下,氢气被液化需要的比能耗为2.7kwh/kg。事实上,目前世界上运行的氢气液化工厂的比能耗约在13-15 kwh/kg,能效较低。因此,设计更加高效的氢气液化工艺迫在眉睫。
技术实现要素:3.本发明的目的在于提供一种基于混合制冷剂循环预冷的氢气液化系统及工艺,以解决氢气液化工艺存在的液化效率低、能耗高的技术问题。本发明的氢气液化工艺使用混合制冷剂循环预冷原料氢气和氢气制冷剂制冷工艺过冷原料氢气。
4.为达到上述目的,本发明首先提供了一种基于混合制冷剂预冷的氢液化系统,该系统是采用混合制冷剂预冷、氢气制冷剂膨胀循环过冷的氢气液化系统,其中,该氢液化系统包括氢气液化管路、预冷冷箱模块、正仲氢转换模块、过冷冷箱模块、液氢储存模块、混合制冷剂压缩模块、氢气制冷剂压缩模块;其中:
5.所述氢气液化管路依次将所述预冷模块、所述正仲氢转换模块、所述过冷模块、所述液氢储存模块连接在一起;
6.所述混合制冷剂压缩模块与所述预冷冷箱模块连接,用于向所述预冷冷箱模块提供混合制冷剂;
7.所述氢气制冷剂压缩模块与所述过冷冷箱模块连接,用于向所述过冷冷箱模块提供氢气制冷剂。
8.在上述氢液化系统中,优选地,所述预冷冷箱模块包括第一级换热器、第一级两相膨胀机、第二级换热器和第二级两相膨胀机;
9.所述氢气液化管路依次连接所述第一级换热器的第一流道、第二级换热器的第一流道;
10.所述混合制冷剂压缩模块设有第一出口支路、第二出口支路、第一出口回路、第二出口回路,所述第一出口支路、第二出口支路分别与所述第一级换热器的第二流道的入口、
第三流道的入口连接,所述第一出口回路、第二出口回路分别与所述第一级换热器的第四流道的出口、第二级换热器的第三流道的出口连接;
11.所述第一级换热器的第二流道的出口与所述第二级换热器的第二流道的入口连接;
12.所述第一级换热器的第三流道的出口与所述第一级两相膨胀机的入口连接,所述第一级两相膨胀机的出口与所述第一级换热器的第四流道的入口连接;
13.所述第二级换热器的第二流道的出口与所述第二级两相膨胀机的入口连接,所述第二级换热器的出口与所述第二级换热器的第三流道的入口连接。
14.在上述氢液化系统中,优选地,所述混合制冷剂压缩模块包括第一级混合制冷剂压缩机、第一级混合制冷剂冷却器、第二级混合制冷剂压缩机、第二级混合制冷剂冷却器、第三级混合制冷剂压缩机、第三级混合制冷剂冷却器、第一混合制冷剂混合器、第一混合制冷剂相分离器、第四级混合制冷剂压缩机、第一级混合制冷剂泵、第二混合制冷剂混合器、第四级混合制冷剂冷却器和第二混合制冷剂相分离器;其中:
15.所述第一级混合制冷剂压缩机、第一级混合制冷剂冷却器、第二级混合制冷剂压缩机、第二级混合制冷剂冷却器依次连接,并且,所述第一级混合制冷剂压缩机的入口与所述第二出口回路连接,所述第二级混合制冷剂冷却器的出口与所述第一混合制冷剂混合器的入口连接;
16.所述第三级混合制冷剂压缩机、第三级混合制冷剂冷却器相互连接,并且,所述第三级混合制冷剂压缩机的入口与所述第一出口回路连接,所述第三级混合制冷剂冷却器的出口与所述第一混合制冷剂混合器连接;
17.所述第一混合制冷剂混合器的出口与所述第一混合制冷剂相分离器的入口连接;
18.所述第一混合制冷剂相分离器的气体出口、液体出口分别与所述第四级混合制冷剂压缩机的入口、所述第一级混合制冷剂泵的入口连接;
19.所述第四级混合制冷剂压缩机的出口、所述第一级混合制冷剂泵的出口分别与所述第二混合制冷剂混合器的入口连接;
20.所述第二混合制冷剂混合器的出口与第四级混合制冷剂冷却器的入口连接;
21.所述第四级混合制冷剂冷却器的出口和所述第二混合制冷剂相分离器的入口连接;
22.所述第二混合制冷剂相分离器的液体出口、气体出口分别与所述第一出口支路、第二出口支路连接。
23.在上述氢液化系统中,优选地,所述过冷冷箱模块包括第三级换热器、第四级换热器、第五级换热器、第六级换热器、第三级两相膨胀机、第四级两相膨胀机、第五级两相膨胀机、第六级两相膨胀机、第七级两相膨胀机、第一氢气分配器、第二氢气分配器和第二级氢气制冷剂混合器;
24.所述正仲氢转换模块包括第一级正仲氢转化器、第二级正仲氢转化器和第三级正仲氢转化器;
25.所述第一级正仲氢转化器的出口与所述第三级换热器的第一流道的入口连接,所述第三级换热器的第一流道的出口与所述第二级正仲氢转化器的入口连接,所述第二级正仲氢转化器的出口与所述第四级换热器的第一流道的入口连接;所述第四级换热器的第一
流道的出口与所述第三级正仲氢转化器的入口连接,所述第三级正仲氢转化器的出口与所述第五级换热器的第一流道的入口连接;
26.所述第三级换热器的第二流道的出口与所述第五级两相膨胀机的入口连接,所述第五级两相膨胀机的出口与所述第二氢气分配器的入口连接,所述第二氢气分配器的两个出口分别与所述第六级两相膨胀机的入口、所述第四级换热器的第三流道的入口连接,所述第四级换热器的第三流道的出口与所述第三级换热器的第四流道的入口连接,所述第三级换热器的第四流道的出口与所述第六级换热器的第一流道的入口连接,所述第六级换热器的第一流道的出口、第二流道的出口、第三流道的入口分别与所述氢气制冷剂压缩模块连接;
27.所述第六级换热器的第三流道的出口与所述第一氢气分配器的入口连接,所述第一氢气分配器的两个出口分别与所述第三级两相膨胀机的入口、所述第三级换热器的第二流道的入口连接;
28.所述第三级两相膨胀机的出口与所述第四级两相膨胀机的入口连接,所述第四级两相膨胀机的出口与所述第二级氢气制冷剂混合器的入口连接;
29.所述第二级氢气制冷剂混合器的出口与所述第三级换热器的第三流道的入口连接,所述第三级换热器的第三流道的出口与所述第六级换热器的第二流道的入口连接;
30.所述第六级两相膨胀机的出口与所述第五级换热器的第二流道的入口连接,所述第五级换热器的第二流道的出口与所述第四级换热器的第二流道的入口连接,所述第四级换热器的第二流道的出口与所述第二级氢气制冷剂混合器的入口连接;
31.所述第五级换热器的第一流道的出口与第七级两相膨胀机的入口连接,所述第七级两相膨胀机的出口与所述液氢储存模块连接。
32.在上述氢液化系统中,第六级换热器是作为回热换热器,用于预冷氢气制冷剂,从而能够充分利用氢制冷循环的冷能,最大程度避免冷能的浪费。
33.在上述氢液化系统中,优选地,所述氢气液化管路依次连接所述第一级正仲氢转化器、第三级换热器的第一流道、第二级正仲氢转化器、第四级换热器的第一流道、第三级正仲氢转化器、第五级换热器的第一流道、第七级两相膨胀机。
34.在上述氢液化系统中,优选地,所述第二级换热器的第一流道的出口与所述第一级正仲氢转化器的入口连接。
35.在上述氢液化系统中,优选地,所述氢气制冷剂压缩模块包括第一级氢气制冷剂压缩机、第一级氢气制冷剂冷却器、第一氢气制冷剂混合器、第二级氢气制冷剂压缩机、第二级氢气制冷剂冷却器、第三级氢气制冷剂压缩机、第三级氢气制冷剂冷却器、第四级氢气制冷剂压缩机和第四级氢气制冷剂冷却器;其中:
36.所述第一级氢气制冷剂压缩机的出口与所述第一级氢气制冷剂冷却器的入口连接,所述第一级氢气制冷剂冷却器的出口与所述第一氢气制冷剂混合器的入口连接;
37.所述第一氢气制冷剂混合器、第二级氢气制冷剂压缩机、第二级氢气制冷剂冷却器、第三级氢气制冷剂压缩机、第三级氢气制冷剂冷却器、第四级氢气制冷剂压缩机和第四级氢气制冷剂冷却器的出口、入口依次连接。
38.在上述氢液化系统中,优选地,所述第一氢气制冷剂混合器的入口与所述第六级换热器的第一流道的出口连接;
39.所述第一级氢气制冷剂压缩机的入口与所述第六级换热器的第二流道的出口连接;
40.所述第四级氢气制冷剂冷却器的出口与所述第六级换热器的第三流道的入口连接。
41.在上述氢液化系统中,优选地,所述氢气液化管路包括第一原料氢气管道、第二原料氢气管道、第三原料氢气管道、第四原料氢气管道、第五原料氢气管道、第六原料氢气管道、第七原料氢气管道、第八原料氢气管道、第九原料氢气管道、第十原料氢气管道,其中,依次连接的第一原料氢气管道、第一级换热器的第一流道、第二原料氢气管道、第二级换热器的第一流道、第三原料氢气管道、第一级正仲氢转化器、第四原料氢气管道、第三级换热器的第一流道、第五原料氢气管道、第二级正仲氢转化器、第六原料氢气管道、第四级换热器的第一流道、第七原料氢气管道、第三级正仲氢转化器、第八原料氢气管道、第五级换热器的第一流道、第九原料氢气管道、第七级两相膨胀机、第十原料氢气管道、液氢储存模块组合在一起形成原料氢气由气体到液氢的整个过程的流通通道。
42.本发明还提供了一种基于混合制冷剂预冷的氢液化工艺,其中,该氢液化工艺是采用上述基于混合制冷剂预冷的氢液化系统进行的;
43.其中,进入所述预冷冷箱模块的原料氢气被冷却至80k;
44.进入所述过冷冷箱模块的原料氢气被冷却至20k。
45.在上述氢液化工艺中,优选地,所述混合制冷剂压缩模块中的混合制冷剂包括 26.86%甲烷、22.23%乙烷、22.45%丙烷、13.65%异丁烷、12.85%氮气和1.96%氢气,以摩尔百分比计。
46.在上述氢液化工艺中,优选地,所述原料氢气的压力为2100kpa,温度为25℃,流量为3.5kg/s;
47.经压缩净化处理后的原料氢气进入所述预冷冷箱模块的换热器(优选进入第一级换热器和第二级换热器))被冷却至-193℃,然后进行第一次氢的正仲氢转化,组分转换为48.09%的仲氢+51.91%的正氢,以摩尔百分比计;
48.经第一次转换后的原料氢气进入所述过冷冷箱模块的换热器(优选进入第三级换热器)被冷却至-221℃,然后进行第二次氢的正仲氢转化,组分转换为73.38%的仲氢+26.62%的正氢,以摩尔百分比计;
49.经过第二次转换后的原料氢气进入所述过冷冷箱模块的换热器(优选进入第四级换热器)被冷却至-242℃,然后进行第三次氢的正仲氢转化,组分转换为96.48%的仲氢+3.52%的正氢,以摩尔百分比计;
50.经过第三次转换后的原料氢气进入所述过冷冷箱模块的换热器(优选进入第五级换热器)过冷到-253℃,然后降压到110~150kpa,进入液化氢气存储罐。
51.在上述氢液化工艺中,优选地,所述混合制冷剂压缩模块提供的混合制冷剂的总质量流量为273254.7kg/h,混合制冷剂被增压至4812.25kpa并冷却至25℃之后进行气液分离得到气相制冷剂和液相制冷剂,其中,气相制冷剂进入所述预冷冷箱模块的换热器(优选进入第一级换热器和第二级换热器)并被冷却至-193℃,然后降压至 228.99kpa,返回所述预冷冷箱模块的换热器(优选返回第二级换热器和第一级换热器)提供冷能;液相制冷剂进入所述预冷冷箱模块的换热器(优选进入第一级换热器) 并被冷却至-30℃,然后降压至
717.96kpa,返回所述预冷冷箱模块的换热器(优选返回第一级换热器)提供冷能;提供冷能之后的气相制冷剂和液相制冷剂返回所述混合制冷剂压缩模块;
52.所述氢气制冷剂压缩模块提供的氢气制冷剂的质量流量为50770.74kg/h,氢气制冷剂被增压至3297.08kpa并冷却至25℃之后进入所述过冷冷箱模块的换热器(优选进入第六级换热器)并被冷却至-167℃,随后分成第一氢气制冷剂和第二氢气制冷剂,其中,第一氢气制冷剂进入所述过冷冷箱模块的换热器(优选进入第三级换热器)并被冷却至-221℃,然后降压至352.29kpa,随后分成第三氢气制冷剂和第四氢气制冷剂,所述第三氢气制冷剂进入所述过冷冷箱模块的换热器(优选进入第三级换热器和第四级换热器)提供冷能,随后返回所述氢气制冷剂压缩模块,所述第四氢气制冷剂降压至113.63kpa,然后进入所述过冷冷箱模块的换热器(优选进入第五级换热器和第四级换热器)提供冷能,并与降压至113.63kpa的第二氢气制冷剂混合进入所述过冷冷箱模块的换热器(优选进入第三级换热器)提供冷能,随后返回所述氢气制冷剂压缩模块。
53.根据本发明提供的基于混合制冷剂循环预冷的氢液化系统的氢液化工艺可以包括如下具体步骤:
54.氢气液化管路:经压缩净化处理后的原料氢气依次进入预冷循环的第一级换热器和第二级换热器预冷后进入第一级正仲氢转化器进行正仲氢转化,随后进入第三级换热器冷却后进入第二级正仲氢转化器进行正仲氢转化,然后,进入第四级换热器冷却后进入第三级正仲氢转化器进行正仲氢转化,最后,进入第五级换热器进一步冷却后进入第七级两相膨胀机降压至液化氢气储存压力,从第七级两相膨胀机降压后出来的液氢进入液氢储存模块;
55.混合制冷剂循环:混合制冷剂经混合制冷剂压缩模块增压、冷却后进入第二混合制冷剂相分离器分离成两股制冷剂(气相制冷剂和液相制冷剂),其中,一股制冷剂 (液相制冷剂)依次进入第一级换热器和第一级两相膨胀机后再次进入第一级换热器提供冷能;另一股制冷剂(气相制冷剂)依次经过第一级换热器、第二级换热器降温后进入第二级两相膨胀机降压后在经过第二级换热器提供冷能;两股制冷剂经最后返回所述混合制冷剂压缩模块完成制冷循环;
56.氢气制冷剂循环:氢气制冷剂经混合制冷剂压缩模块增压、冷却后进入第六级换热器降温后进入第一个氢气分配器后分成两股制冷剂(第一氢气制冷剂和第二氢气制冷剂),其中,一股制冷剂(第二氢气制冷剂)进入第三级膨胀机、第四级膨胀机后进入第二级氢气混合器混合后进入第三级换热器、第六级换热器提供冷能;另一股制冷剂(第一氢气制冷剂)进入第三级换热器降温后进入第五级膨胀机后进入第一级氢气分配器分离成另外两股制冷剂(第三氢气制冷剂和第四氢气制冷剂),其中,一股制冷剂(第三氢气制冷剂)进入第四级换热器、第三级换热器、第六级换热器提供冷能,另一股制冷剂(第四氢气制冷剂)进入第六级膨胀机降压后进入第五级换热器,第三级换热器、第六级换热器提供冷能;最后两股制冷剂返回所述氢气制冷剂压缩模块完成制冷循环。
57.与现有技术相比,本发明具有如下的有益效果:
58.本发明提出一种基于混合制冷剂循环预冷的氢液化系统和氢液化工艺,使用高效的混合制冷循环和氢制冷剂循环为液化进料氢气提供冷能,其中,预冷段使用混合制冷剂循环,过冷段使用氢气低温膨胀制冷循环,制冷剂的流量和压力经过优化,有效降低了能
耗,改善了液化过程的换热特性,提高了换热效率;相比于采用液氮进行预冷的方式(生产液氮需要额外的能耗),采用氢制冷剂能够节约能耗;
59.本发明通过将每个制冷循环分成两个制冷支路,有效提高了制冷循环的制冷效率;其中:
60.混合制冷剂循环被分成两个支路(例如第一出口支路、第二出口支路)为预冷冷箱(例如第一换热器、第二换热器)提供冷能,每个支路的制冷剂分别在不同压力制冷,提高了制冷循环的效率。此外,为了充分利用两个支路不同的冷凝压力(低压) 降低预冷循环的能耗,分别使用不同的压缩机组(例如第一级混合制冷剂压缩机+第二级混合制冷剂压缩机、第三级混合制冷剂压缩机)对低压制冷剂进行增压,并使用压缩机(例如第四级混合制冷剂压缩机)和泵(例如第一级混合制冷剂泵)分别将中压气相制冷剂和液相制冷剂增压到相同的蒸发压力(制冷剂的高压),这样的结构设置不仅保证了压缩机能够高效和安全的运行,而且也有效降低了工艺的能耗;
61.氢制冷剂循环同样被分成多个子回路为过冷冷箱(例如第三换热器、第四换热器、第五换热器)提供冷能;与混合制冷剂循环一样,每个子制冷回路均在不同的压力水平下工作;如果氢制冷循回路采用多个回路,而每个回路连续为多个换热器提供冷能,将会导致一些换热器具有较大的温差,这样不仅会造成冷能的浪费,而且也会导致换热器较低的换热效率,同时也会导致各换热器之间产生较高程度的相互影响;而本发明中的每个换热器均连接一支制冷剂回路,最大程度降低了各换热器之间的相互影响程度,因此,可以通过调整与每个换热器相连接的制冷剂流量和压力提供与热流匹配的冷能,从而有效降低换热器的温差;
62.同时,本发明的混合制冷剂循环和氢制冷剂循环分别独立运行,简化了工艺的结构,避免了两个制冷剂循环之间的相互影响,方便了后续优化每个制冷循环的制冷剂的流量和压力;
63.本发明的技术方案涉及混合制冷剂预冷、混合制冷剂双压的两个支路、压缩机组配置、过冷循环多个子回路、多级正仲氢转化以及混合冷剂组分控制、制冷工艺参数控制等措施,这些措施不是简单叠加,而是相互协调搭配形成了一个有机整体,由此使得本发明的液化工艺具有能耗低,液化率高的优势,产品液氢中的仲氢浓度≥95%。
附图说明
64.图1为实施例1提供的基于混合制冷剂预冷的氢液化系统的示意图。
65.图2a-图2h为过冷换热器的thcc曲线。
66.主要附图标号说明:
67.c1 第一级混合制冷剂压缩机
ꢀꢀꢀꢀꢀ
c5 第一级氢气制冷剂压缩机
68.e1 第一级混合制冷剂冷却器
ꢀꢀꢀꢀꢀ
e5 第一级氢气制冷剂冷却器
69.c2 第二级混合制冷剂压缩机
ꢀꢀꢀꢀꢀ
c6 第二级氢气制冷剂压缩机
70.e2 第二级混合制冷剂冷却器
ꢀꢀꢀꢀꢀ
e6 第二级氢气制冷剂冷却器
71.c3 第三级混合制冷剂压缩机
ꢀꢀꢀꢀꢀ
c7 第三级氢气制冷剂压缩机
72.e3 第三级混合制冷剂冷却器
ꢀꢀꢀꢀꢀ
e7 第三级氢气制冷剂冷却器
73.c4 第四级混合制冷剂压缩机
ꢀꢀꢀꢀꢀ
c8 第四级氢气制冷剂压缩机
74.p1 第一级混合制冷剂泵
ꢀꢀꢀꢀꢀꢀꢀꢀꢀ
e8 第四级氢气制冷剂冷却器
75.e2 第四级混合制冷剂冷却器
ꢀꢀꢀꢀꢀ
hx6 第六级换热器
76.m1 第一混合制冷剂混合器
ꢀꢀꢀꢀꢀꢀꢀ
t1 第一氢气分配器
77.s1 第一混合制冷剂相分离器
ꢀꢀꢀꢀꢀ
ex3 第三级膨胀机
78.m2 第二混合制冷剂混合器
ꢀꢀꢀꢀꢀꢀꢀ
ex4 第四级膨胀机
79.s2 第二混合制冷剂相分离器
ꢀꢀꢀꢀꢀ
m3 第一氢气制冷剂混合器
80.hx1 第一级换热器
ꢀꢀꢀꢀꢀꢀꢀꢀꢀꢀꢀꢀꢀꢀ
m4 第二氢气制冷剂混合器
81.ex1 第一级膨胀机
ꢀꢀꢀꢀꢀꢀꢀꢀꢀꢀꢀꢀꢀꢀ
hx3 第三级换热器
82.hx2 第二级换热器
ꢀꢀꢀꢀꢀꢀꢀꢀꢀꢀꢀꢀꢀꢀ
ex5 第五级膨胀机
83.ex2 第二级膨胀机
ꢀꢀꢀꢀꢀꢀꢀꢀꢀꢀꢀꢀꢀꢀ
t2 第二氢气分配器
84.r1 第一级正仲氢转化器
ꢀꢀꢀꢀꢀꢀꢀꢀꢀ
ex6 第六级膨胀机
85.r2 第二级正仲氢转化器
ꢀꢀꢀꢀꢀꢀꢀꢀꢀ
hx4 第四级换热器
86.r3 第三级正仲氢转化器
ꢀꢀꢀꢀꢀꢀꢀꢀꢀ
hx5 第五级换热器
87.ex7 第七级膨胀机
ꢀꢀꢀꢀꢀꢀꢀꢀꢀꢀꢀꢀꢀꢀ
tank 液氢储罐
88.1 第一原料氢气管道
ꢀꢀ
2 第二原料氢气管道
ꢀꢀ
3 第三原料氢气管道
89.4 第四原料氢气管道
ꢀꢀ
5 第五原料氢气管道
ꢀꢀ
6 第六原料氢气管道
90.7 第七原料氢气管道
ꢀꢀ
8 第八原料氢气管道
ꢀꢀ
9 第九原料氢气管道
91.10 第十原料氢气管道 11,13-14,16-17,19-21,23-59 管道
92.12 第一出口支路
ꢀꢀ
18 第二出口支路
ꢀꢀ
15 第一出口回路
ꢀꢀ
22 第二出口回路
具体实施方式
93.为了对本发明的技术特征、目的和有益效果有更加清楚的理解,现对本发明的技术方案进行以下详细说明,但不能理解为对本发明的可实施范围的限定。
94.实施例1
95.本实施例提供了一种基于混合制冷剂循环预冷的氢气液化系统,其组成如图1 所示,该氢气液化系统包括:
96.氢气液化管路、预冷冷箱模块、正仲氢转换模块、过冷冷箱模块、液氢储存模块、混合制冷剂压缩模块、氢气制冷剂压缩模块;其中:
97.氢气液化管路用于将原料氢气预冷到80k和过冷到20k,其包括第一原料氢气管道1、第二原料氢气管道2、第三原料氢气管道3、第四原料氢气管道4、第五原料氢气管道5、第六原料氢气管道6、第七原料氢气管道7、第八原料氢气管道8、第九原料氢气管道9、第十原料氢气管道10;
98.预冷冷箱模块包括第一级换热器hx1、第一级两相膨胀机ex1、第二级换热器 hx2和第二级两相膨胀机ex2;
99.正仲氢转换模块包括第一级正仲氢转化器r1、第二级正仲氢转化器r2和第三级正仲氢转化器r3;
100.过冷冷箱模块用于过冷原料氢气到20k,其包括第三级换热器hx3、第四级换热器hx4、第五级换热器hx5、第六级换热器hx6、第三级两相膨胀机ex3、第四级两相膨胀机ex4、第五级两相膨胀机ex5、第六级两相膨胀机ex6、第七级两相膨胀机ex7、第一氢气分配器t1、
第二氢气分配器t2和第二级氢气制冷剂混合器 m4;
101.液氢储存模块为液氢储罐tank;
102.混合制冷剂压缩模块用于向预冷冷箱模块输送混合制冷剂,以提供冷能,其包括第一级混合制冷剂压缩机c1、第一级混合制冷剂冷却器e1、第二级混合制冷剂压缩机c2、第二级混合制冷剂冷却器e2、第三级混合制冷剂压缩机c3、第三级混合制冷剂冷却器e3、第一混合制冷剂混合器m1、第一混合制冷剂相分离器s1、第四级混合制冷剂压缩机c4、第一级混合制冷剂泵p1、第二混合制冷剂混合器m2、第四级混合制冷剂冷却器e4和第二混合制冷剂相分离器s2;
103.氢气制冷剂压缩模块用于向过冷冷箱模块输送氢气制冷剂以提供冷能,其包括第一级氢气制冷剂压缩机c5、第一级氢气制冷剂冷却器e5、第一氢气制冷剂混合器 m3、第二级氢气制冷剂压缩机c6、第二级氢气制冷剂冷却器e6、第三级氢气制冷剂压缩机c7、第三级氢气制冷剂冷却器e7、第四级氢气制冷剂压缩机c8和第四级氢气制冷剂冷却器e8;
104.其中:第一原料氢气管道1与第一级换热器hx1的第一流道的入口连接,用于输入原料氢气,第一级换热器hx1的第一流道的出口通过第二原料氢气管道2连接至第二级换热器hx2的第一流道的入口,第二级换热器hx2的第一流道的出口通过第三原料氢气管道3连接至第一级正仲氢转化器r1的入口,第一级正仲氢转化器r1 的出口通过第四原料氢气管道4连接至第三级换热器hx3的第一流道的入口,第三级换热器hx3的第一流道的出口通过第五原料氢气管道5连接至第二级正仲氢转化器r2的入口,第二级正仲氢转化器r2的出口通过第六原料氢气管道6连接至第四级换热器hx4的第一流道的入口,第四级换热器hx4的第一流道的出口通过第七原料氢气管道7连接至第三级正仲氢转化器r3的入口,第三级正仲氢转化器r3的出口通过第八原料氢气管道8连接至第五级换热器hx5的第一流道的入口,第五级换热器hx5的第一流道的出口通过第九原料氢气管道9连接至第七级两相膨胀机ex7 的入口,第七级两相膨胀机ex7的出口通过第十原料氢气管道10连接至氢气储罐 tank;
105.混合制冷剂压缩模块设有第一出口支路12、第二出口支路18、第一出口回路15、第二出口回路22,第一出口支路12、第二出口支路18分别与第一级换热器hx1的第二流道的入口、第三流道的入口连接,第一出口回路15、第二出口回路22分别与第一级换热器hx1的第四流道的出口、第二级换热器hx2的第三流道的出口连接;
106.第一级混合制冷剂压缩机c1、第一级混合制冷剂冷却器e1、第二级混合制冷剂压缩机c2、第二级混合制冷剂冷却器e2通过管路23,24,25依次连接,第二级混合制冷剂冷却器e2的出口通过管路26与第一混合制冷剂混合器m1的入口连接;第三级混合制冷剂压缩机c3与第三级混合制冷剂冷却器e3通过管路16连接,第三级混合制冷剂冷却器e3的出口与第一混合制冷剂混合器m1的入口连接;
107.第一混合制冷剂混合器m1的出口通过管路27与第一混合制冷剂相分离器s1的入口连接;第一混合制冷剂相分离器s1的气体出口、液体出口分别通过管路28,30 与第四级混合制冷剂压缩机c4的入口、第一级混合制冷剂泵p1的入口连接;第四级混合制冷剂压缩机c4的出口、第一级混合制冷剂泵p1的出口分别通过管路29,31 与第二混合制冷剂混合器m2的入口连接;
108.第二混合制冷剂混合器m2的出口通过管路32与第四级混合制冷剂冷却器e4 的入口连接;第四级混合制冷剂冷却器e4的出口通过管路11和第二混合制冷剂相分离器s2的入
口连接;第二混合制冷剂相分离器s2的液体出口、气体出口分别与第一出口支路12、第二出口支路18连接;第三级混合制冷剂压缩机c3的入口与第一出口回路15连接,第一级混合制冷剂压缩机c1的入口与第二出口回路22连接;
109.第二出口支路18与第一级换热器hx1的第二流道的入口连接,第一级换热器 hx1的第二流道的出口通过管路19与第二级换热器hx2的第二流道的入口连接,第二级换热器hx2的第二流道的出口通过管路20与第二级两相膨胀机ex2的入口连接,第二级两相膨胀机ex2的出口通过管路21与第二级换热器hx2的第四流道的入口连接;
110.第一出口支路12与第一级换热器hx1的第三流道的入口连接,第一级换热器 hx1的第三流道的出口通过管路13与第一级两相膨胀机ex1的入口连接,第一级两相膨胀机ex1的出口通过管路14与第一级换热器hx1的第四流道的入口连接;
111.第三级换热器hx3的第二流道的出口通过管路49与第五级两相膨胀机ex5的入口连接,第五级两相膨胀机ex5的出口通过管路50与第二氢气分配器t2的入口连接,第二氢气分配器t2的两个出口分别通过管路51,52与第四级换热器hx4的第三流道的入口、第六级两相膨胀机ex6的入口连接,第四级换热器hx4的第三流道的出口通过管路57与第三级换热器hx3的第四流道的入口连接,第三级换热器hx3 的第四流道的出口通过管路59与第六级换热器hx6的第一流道的入口连接;
112.第六级换热器hx6的第三流道的出口通过管路44与第一氢气分配器t1的入口连接,第一氢气分配器t1的两个出口分别通过管路45,48与第三级两相膨胀机ex3 的入口、第三级换热器hx3的第二流道的入口连接;
113.第三级两相膨胀机ex3的出口通过管路46与第四级两相膨胀机ex4的入口连接,第四级两相膨胀机ex4的出口通过管路47与第二级氢气制冷剂混合器m4的入口连接;
114.第六级两相膨胀机ex6的出口通过管路53与第五级换热器hx5的第二流道的入口连接,第五级换热器hx5的第二流道的出口通过管路54与第四级换热器hx4 的第二流道的入口连接,第四级换热器hx4的第二流道的出口通过管路55与第二级氢气制冷剂混合器m4的入口连接;
115.第二级氢气制冷剂混合器m4的出口通过管路56与第三级换热器hx3的第三流道的入口连接,第三级换热器hx3的第三流道的出口通过管路58与第六级换热器 hx6的第二流道的入口连接;
116.第六级换热器hx6的第一流道的出口通过管路33与第一氢气制冷剂混合器m3 的入口连接;第六级换热器hx6的第二流道的出口通过管路34与第一级氢气制冷剂压缩机c5的入口连接;第一级氢气制冷剂压缩机c5的出口通过管路35与第一级氢气制冷剂冷却器e5的入口连接,第一级氢气制冷剂冷却器e5的出口通过管路36与第一氢气制冷剂混合器m3的入口连接;
117.第一氢气制冷剂混合器m3、第二级氢气制冷剂压缩机c6、第二级氢气制冷剂冷却器e6、第三级氢气制冷剂压缩机c7、第三级氢气制冷剂冷却器e7、第四级氢气制冷剂压缩机c8和第四级氢气制冷剂冷却器e8通过管路37,38,39,40,41,42依次连接;第四级氢气制冷剂冷却器e8的出口通过管路43与第六级换热器hx6的第三流道的入口连接;
118.在图1中,第一级换热器hx1至第五级换热器hx5的流道命名按照由下向上的顺序进行,即最下方的流道为第一流道,第六级换热器hx6的流道命名按照由左向右的顺序进
行,即最左侧的流道为第一流道。
119.实施例2
120.本实施例提供了一种氢气液化工艺,其是采用实施例1的氢气液化系统进行的,其中,原料氢气的压力为2100kpa,温度为25℃,流量为3.5kg/s。
121.氢气液化的具体步骤如下:
122.预冷段:混合制冷剂包括摩尔百分比为26.86%甲烷、22.23%乙烷、22.45%丙烷、 13.65%异丁烷、12.85%氮气和1.96%氢气,制冷剂总质量流量为273254.7kg/h,混合制冷剂增至4812.25kpa并冷却至25℃后进入第二混合制冷剂相分离器s2进行气液分离;
123.分离后,气相制冷剂通过第二出口支路18依次进入第一级换热器hx1和第二级换热器hx2,它的温度被冷却到-193℃,然后,制冷剂通过管路20进入第二级两相膨胀机ex2降压到228.99kpa,随后,制冷剂通过管路21返回到第二级换热器hx2 与热流进行充分的换热,最后,制冷剂通过第二出口回路22进入压缩单位完成一次循环。来自s2的液相制冷剂通过第一出口支路12流入第一级换热器hx1被冷却到
ꢀ‑
30℃,然后,制冷剂通过管路13通过第一级两相膨胀机ex1降压到717.96kpa,之后,制冷剂通过管路14返回到第一级换热器hx1为冷却原料氢气和制冷剂提供冷能,最后,低压高温制冷剂通过第一出口回路15进入压缩单元完成一次循环。
124.过冷段:氢气制冷剂的质量流量为50770.74kg/h。氢气制冷剂首先被增压到 3297.08kpa,并降温到25℃后进入第六级换热器hx6内被回流氢气制冷剂降温到
ꢀ‑
167℃,随后,氢气制冷剂通过管路44在第一氢气分配器t1内分成两股制冷剂,即第一氢气制冷剂和第二氢气制冷剂,并以不同的制冷支路工作。在第一个制冷支路,第二氢气制冷剂通过管路45依次进入第三级两相膨胀机ex3和第四级两相膨胀机 ex4,它的压力被降到113.63kpa,随后,第二氢气制冷剂通过管路47与另一股来自管路55的第四氢气制冷剂进入第一氢气制冷剂混合器m4混合后进入第三级换热器 hx3提供冷能,在另一条制冷支路,第一氢气制冷剂通过管路48进入第三级换热器 hx3,温度被冷却到-221℃,然后,第一氢气制冷剂通过管路49进入第五级两相膨胀机ex5,其压力降到352.29kpa,随后,第一氢气制冷剂通过管路50进入第二氢气分配器t2并分成两股制冷剂,即第三氢气制冷剂和第四氢气制冷剂,其中,第三制冷剂通过管路51直接流入第四级换热器hx4提供冷能,第四氢气制冷剂通过管路 52进入第六级两相膨胀机ex6降压到113.63kpa后依次进入第五级换热器hx5、第四级换热器hx4、第三级换热器hx2和第六级换热器hx6提供冷能。
125.经压缩净化处理后的原料氢气1经过第一级换热器hx1和第二级换热器hx2预冷到-193℃,经过第一级正仲氢转换器r1进行第一次氢的正仲氢转化至组分变为摩尔百分比为48.09%仲氢(para-hydrogen)、51.91%正氢(ortho-hydrogen);经第一次转换后的原料氢气4经过第三级换热器hx3冷却到-221℃,然后进入第二级正仲氢转换器r2进行第二次氢的正仲氢转化至组分变为摩尔百分比为73.38%仲氢 (para-hydrogen)、26.62%正氢(ortho-hydrogen);经第二次转换后的原料氢气6进入第四级换热器hx4冷却到-242℃后进入第三级正仲氢转换器r3进行第三次氢的正仲氢转化至组分变为摩尔百分比为96.48%仲氢(para-hydrogen)、3.52%正氢 (ortho-hydrogen);最后,原料氢气8经过第五级换热器hx5过冷到-253℃后进入第七级两相膨胀机ex7降压到110kpa后进入液化氢气存储罐tank。
126.通过采用的hysys软件的模拟计算得出,该基于混合制冷剂循环预冷的氢气液化
系统的能耗为5.96kwh/kg。经过三级正仲氢转化器(第一级正仲氢转化器r1、第二级正仲氢转化器r2和第三级正仲氢转换器r3)后,液氢中的仲氢的摩尔百分比为 96.48%,液化率达到100%。
127.为说明本发明的过冷换热器具有较高的换热效率,本发明对过冷换热器的主要设计参数进行了评价。换热器的主要设计参数有最小换热温差(mita)和对数平均温差(lmtd)。在满足约束条件下,mita和lmtd值越小,其换热器的换热效率越高。表1为本发明和cn 216204684 u的过冷换热器的设计参数。
128.表1过冷换热器的mita和lmtd
[0129][0130]
从表1可知,本发明的过冷换热器的mita和lmtd均小于cn 216204684 u中的过冷换热器,特别是lmtd,这表明本发明的过冷换热器具有较高的换热效率。
[0131]
此外,为了更加清楚的说明本发明的过冷换热器的换热性能,这里给出过冷换热器的温度热流复合曲线(thcc),如图2a-图2h所示,其中,图2a、图2c、图2e、图2g是本发明的过冷换热器对应的曲线,图2b、图2d、图2f、图2h是cn 216204684u的过冷换热器对应的曲线。thcc反映了换热器内部热流和冷流的温度相对于热流的变化情况,它的间隔可以评估换热器的损失,其间隔越小,损失越小,换热效率越高。从图2a-图2h可知,本发明的过冷换热器的thcc曲线的间隔小于cn216204684 u,这说明本发明的过冷换热器的换热效率优于cn 216204684 u的过冷换热器,本发明的氢气液化系统和氢气液化工艺的换热效率优于cn 216204684 u。