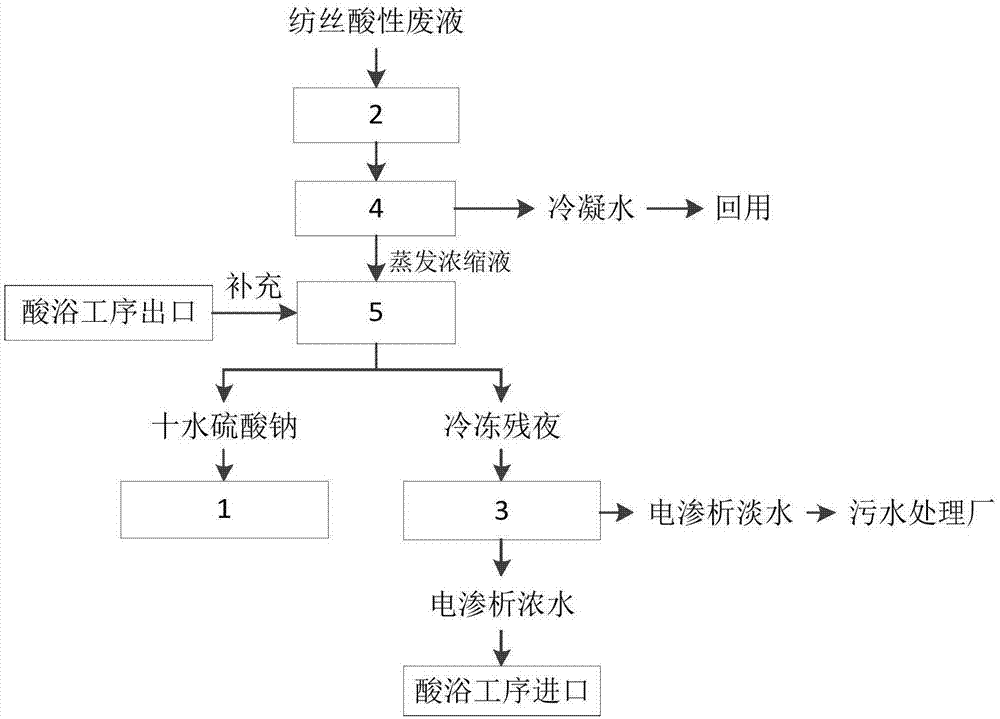
本发明涉及一种粘胶纤维行业纺丝废液中有价元素的分阶资源化回收方法,能够实现废水的近零排放,属于废水资源化利用领域。
背景技术:
:粘胶纤维生产主要有两个工序,一是制胶工序,二是纺丝工序。从粘胶变成具有一定品质的再生纤维素丝条的过程,是通过酸性的凝固酸浴完成的。粘胶纤维凝固的组分主要有硫酸、硫酸钠、硫酸锌,为了某些工艺目的和提高纤维的物理机械性能,常在凝固浴中加入少量含铝助剂。因此,这股废水是一种强酸性高盐废水,含有大量硫酸、硫酸钠、硫酸锌,同时含有一定量的有机物,其水质指标如表1所示。表1废水水质指标由表1中的数据可以看出,废水中硫酸的含量达到了15000mg/l,约1.5%;硫酸钠含量为45000mg/l,约4.5%,其次还有少量的硫酸锌和硫酸铝,废水中的总盐分为6.8%,属于高含盐废水。此外,废水中还有一定量的有机物(主要成份为纤维素磺酸酯),会对后续的处理过程产生较大影响。目前,粘胶纤维纺丝废水的处理工艺是将制胶工序中产生的碱性水混合,采用一级物化+二级生化的处理工艺,一级物化措施主要有中和、曝气吹脱、除重等工序,二级生化主要是利用微生物的作用将有机物及其他杂质元素去除。但是现有工艺主要存在以下几个问题:(1)浪费大量的硫酸资源,并消耗大量碱,处理工艺粗犷。纺丝废水中酸性废水与制胶工艺的碱性废水混合后,废水仍然是酸性废水,ph约为2-3,需要消耗大量的碱将废水的ph调节至碱性,达到去除重金属的碱度。在中和调碱的过程中,将纺丝废水中的大量硫酸浪费,消耗大量的碱,由此造成了资源的浪费以及药剂成本的增加,是一种粗狂的环保处理工艺。(2)产生大量的废渣,增加危废处置成本。在除重阶段,主要是去除废水中的锌和铝,再利用碱沉淀的过程中会产生大量的废渣,产生的废渣是一种危险废弃物,需要按照危险废弃物的处理标准去处置,费用很高,大大增加了企业的环保成本。(3)废水中的盐分超标,生化工艺不稳定。纺丝废水中含有大量的盐分,在两股废水混合后盐分也较高,会对微生物的影响很大,且微生物对盐分的处理效果较差,国家对排放废水中的盐分指标控制的越来越严,致使出水中的盐分不达标。(4)造成废水中硫酸钠资源的浪费。纺丝废水中含有大量的硫酸钠,其含量高达4.5%,将废水混合生化处理会造成了大量的资源浪费,也会生化处理产生很大的负面影响。(5)废水中的热量没有利用,造成浪费。纺丝废水的温度在70-80℃范围内,而生化处理的温度需要在常温条件,这部分热量没有充分利用,造成了资源浪费。(6)在除重金属的过程中,由于锌的沉淀ph范围比较窄(ph8-9),条件很难控制,且干扰因素较多,往往出水中的锌不能达标。技术实现要素:技术问题:本发明提供了一种实现酸性废液的低能耗高回收处置,满足了硫酸钠盐的平衡,避免了硫酸钠盐在系统中的累积,建立了废酸处置与生产工艺的新平衡的在粘胶纤维生产工艺中协同处置酸性废液的方法,废酸处置工艺中只有电渗析淡水排放,大大降低了系统能耗,实现废水近零排放。本发明同时提供一种实现上述方法的一种在粘胶纤维生产工艺中协同处置酸性废液的装置。技术方案:本发明的在粘胶纤维生产工艺中协同处置酸性废液的方法,包括以下步骤:(1)将粘胶纤维行业纺丝酸性废液输送进入过滤装置(2)去除废液中的固体不溶物;(2)对步骤(1)处理后的废液进行蒸发浓缩处理,得到体积为原废液体积10%~50%的浓缩液;(3)将步骤(2)得到的浓缩液与从纺丝生产工艺中的酸浴生产工序出口调出的酸浴溶液混合,采用冷冻结晶的方式回收混合液中的十水硫酸钠晶体,同时产生冷冻残液;(4)对步骤(3)冷冻结晶产生的冷冻残液进行电渗析,去除冷冻残液中的有机物,同时对步骤(3)回收的十水硫酸钠晶体进行精制得到无水硫酸钠;(5)将步骤(4)电渗析处理后得到的浓水回用至纺丝生产工艺中的酸浴装置。进一步的,本发明方法中,步骤(4)的电渗析中,采用纯水作为电渗析淡水的接收液,冷冻残液与纯水接收液的体积比为1:(2~5),当电渗析装置产生的淡水与浓水中盐分的比值为1:(5~15)时,完成电渗析去除有机物的工作。进一步的,本发明方法中,所述步骤(3)中,从酸浴生产工序出口调出的酸浴溶液水量为冷冻残液水量的10~30%。进一步的,本发明方法中,所述酸浴装置中的酸浴溶液质量为冷冻残液质量的20%。进一步的,本发明方法中,所述步骤(2)中得到体积为原废液体积15%~30%的浓缩液。进一步的,本发明方法中,所述步骤(3)中的冷冻结晶采用两级降温冷冻:第一级冷冻结晶将浓缩液的温度由75~100摄氏度降低至40~50摄氏度,并在该温度条件下稳定20~60min;第二级冷冻结晶将温度由40~50摄氏度降低至-10~0摄氏度,并在该温度条件下稳定20~60min,通过固液分离,得到十水硫酸钠晶体。进一步的,本发明方法中,所述步骤(3)中回用至纺丝生产工艺中的酸浴装置的冷冻残液满足以下回用标准:硫酸(g/l)硫酸锌(g/l)硫酸铝(g/l)115-120≥7.5≥2.5进一步的,本发明方法中,所述步骤(1)中的过滤装置(2)采用精密过滤器。本发明的一种在粘胶纤维生产工艺中协同处置酸性废液的装置,包括依次连接的过滤装置(2)、蒸发浓缩装置(4)、冷冻结晶装置(5),分别与所述冷冻结晶装置(5)连接的电渗析系统(3)和精制系统(1),冷冻结晶装置(5)的进口与纺丝生产工艺中的酸浴生产工序出口连接,所述电渗析系统(3)的浓水出口与纺丝生产工艺中的酸浴生产工序进口连接。进一步的,本发明装置中,所述电渗析装置(3)串联设置两级或两级以上。本发明方法的一种实施例中,包括以下步骤:步骤(1)粘胶纤维行业纺丝废液温度在70~80℃范围内,废液进入精密过滤器,去除废液中的固体不溶物;优选的实施例中,精密过滤器的过滤精度为5μm;步骤(2)取步骤(1)精密过滤器出水进入蒸发浓缩装置,蒸发浓缩的温度控制在75-100摄氏度,当蒸发浓缩液的体积为原废液体积的10%~50%时,进入下一工序;优选的实施例中,蒸发浓缩液的体积为原废液体积的15%~30%;步骤(3)取步骤(2)的蒸发浓缩液进入冷冻结晶装置,蒸发浓缩液分为两级降温冷冻回收晶体,避免造成设备堵塞。第一级冷冻结晶将浓缩液的温度由75~100摄氏度降低至40~50摄氏度,并在该温度条件下稳定20~60min;第二级冷冻结晶将温度由40~50摄氏度降低至-10~0摄氏度,并在该温度条件下稳定20~60min,通过固液分离,得到十水硫酸钠晶体和冷冻残液;优选的实施例中,固液分离方式为离心分离;优选的实施例中,收集冷冻结晶过程中热量换热至蒸发浓缩装置或(和)硫酸钠精制装置;步骤(4)取步骤(3)冷冻结晶装置产生的冷冻残液进入电渗析装置,电渗析装置的主要作用是去除冷冻残液中的有机物,避免冷冻残液回用到生产工艺后造成生产工艺中有机物的富集,最终导致生产工艺的瘫痪。冷冻残液中在经过电渗析装置时,采用纯水为电渗析淡水的接收液,冷冻残液与纯水接收液的体积比为1:(2~5),当电渗析装置产生的淡水与浓水中盐分的比值为1:(5~15)时(可以以电导率表征),完成电渗析分离有机物的工作。电渗析装置处理后淡水(富含有机物)输送至厂区内的污水处理站处理,浓水(富含硫酸、硫酸钠、硫酸锌等盐分)循环套用至酸浴装置的进口,在酸浴装置中充分利用浓水中的硫酸、硫酸钠、硫酸锌等资源,实现废液中资源化利用的目的;优选的实施例中,电渗析装置设置两级及以上;优选的实施例中,电渗析装置的产生的淡水经污水处理站处理后进行中水回用;步骤(5)取步骤(3)冷冻结晶装置产生的十水硫酸钠晶体,采用50-70摄氏度温度下的硫酸钠饱和溶液清洗,按照十水硫酸钠晶体(含水率在70~90%)和饱和硫酸钠溶液的质量体积比为1:(1~5)混合,加入氢氧化钠将溶液调节至中性,搅拌清洗30~60min,固液分离,晶体经过烘干工序得到产品级(达到一类一等品纯度)的无水硫酸钠,饱和清洗液回用至冷冻结晶工序;优选的实施例中,硫酸钠精制工艺采用两级清洗工艺,按照同样的清洗方式清洗两次;优选的实施例中,清洗后的饱和硫酸钠晶体可分批次重复利用;优选的实施例中,硫酸钠精制工艺也可采用纯水溶解+中和沉淀+蒸发结晶的方式得到无水硫酸钠;步骤(6)取酸浴装置出口处的酸浴溶液调用至冷冻结晶装置,调用酸浴出口处酸浴溶液水量为冷冻残液的10-30%,以实现整个系统中的硫酸钠盐平衡,确保整个系统的稳定运行。本发明针对粘胶纤维行业中的酸性废液的特点,以资源化利用为原则,协同其生产工艺,充分利用废液中的硫酸、硫酸钠、硫酸锌物质,同时建立系统中新的物料平衡,充分考虑废水中的热量,实现酸性废液的低能耗高回收处置,废酸处置工艺中只有电渗析淡水排放至污水处理厂,实现了废水的近零排放。有益效果:本发明与现有技术相比,具有以下优点:1、本发明的处理技术充分利用废水特性,大大降低了系统能耗。酸性废液的出水温度为70~80摄氏度,蒸发结晶的温度通常在70~100摄氏度之间,本发明技术充分利用出水的热量,直接进入蒸发系统,几乎可以实现蒸发过程中的零热量供给,大大降低处理成本,实现真正意义上的节能处置。2、本发明结合生产工艺,协同实现资源的最大化利用。在粘胶纤维生产工艺中,酸浴工序是很重要的一个工序,在酸浴工序中需要加入大量的硫酸、硫酸钠、硫酸锌及硫酸铝药剂,来实现酸浴的目的。在本发明中,冷冻残液经过电渗析装置去除有机物后,硫酸、硫酸锌、硫酸铝的浓度均达到了生产工艺中酸浴工序的回用标准。有机物对于酸浴工序是一种不必要的物质,若在冷冻残液中带入有机物会造成酸浴工序有机物的富集,有机物长期累积会对生产工艺产生不可逆的影响。因此,冷冻残夜经过电渗析去除有机物后可直接回用至酸浴工序,实现资源化的最大化利用。3、本发明技术建立了废酸处置与生产工艺的物料新平衡。本发明中,冷冻残液回用到生产工艺中的酸浴工序中,会将冷冻残液中的少部分硫酸钠带回,为了保证废酸液处理过程中硫酸钠盐的平衡,需要从酸浴工序出口处调出一部分酸浴溶液至冷冻结晶系统,以满足硫酸钠盐的平衡,同时也避免了硫酸钠盐在系统中的累积,建立了废酸处置与生产工艺的新平衡,具有显著创新性。4、本发明创新性的采用电渗析装置去除废水中有机物,避免了有机物在系统内富集。现有膜装置中,超滤膜、反渗透膜利用拦截的原理分离淡水和浓水,因此浓水中含有离子盐分和有机物均很高,淡水可中水回用,盐分和有机物没有分离;而电渗析膜利用的电荷移动原理分离盐分和有机物,产生的淡水中盐分低有机物高,满足了生化处理的进水条件,浓水中盐分高有机物浓度低,实现了盐分和有机物的分离。5、本发明工艺采用冷冻结晶工艺回收钠盐晶体。在粘胶纤维行业,回收钠盐一般采用直接蒸发结晶的方式,这种方式大大降低回收钠盐的纯度,因为废水中的有机物含量较多,直接蒸发会造成绝大部分的有机物夹带钠盐晶体中,给钠盐的纯度和品质均产生很大影响,且蒸发的水量较大。而在本发明中采用冷冻结晶的方式回收钠盐,可有效屏蔽有机物的干扰,在浓缩倍数较小的情况下降温结晶,显著降低有机物的夹带,提高钠盐的品质。同时,由于降温结晶析出的十水硫酸钠,带出10个结晶水,可大幅度降低了蒸发结晶的水量。因此,本发明工艺中通过工艺的创新性,在通过降低蒸发结晶的水量的同时提高了晶体纯度,创新性十分显著。附图说明图1为本发明方法的工艺流程图。图中有:1—精制系统;2—过滤装置;3—电渗析系统;4—蒸发浓缩装置;5—冷冻结晶装置。具体实施方式下面结合实施例和说明书附图对本发明作进一步的说明。实施例1(1)取某粘胶纤维公司的纺丝酸性废液进行实验,其酸性废液的初始指标如表1-1所示。表1-1原废液指标数据由表中的数据可以看出,废液中硫酸钠含量最高,浓度高达为5%,其次是硫酸,浓度达到了1.5%,硫酸锌和硫酸铝含量较低,两者之和的浓度达到0.13%,有机物的浓度较高,为2000ppm,长期富集会对酸性处理和生产工艺产生不可逆的影响。(2)取5000ml酸性废液进入精密过滤器,去除废液中的固体物质;(3)取5000ml精密过滤器出水进入旋转蒸发仪,蒸发温度为85摄氏度,当蒸发浓缩液的体积为500ml时(浓缩液的体积为原废液体积的10%),停止蒸发;(4)取蒸发浓缩液500ml和生产工艺中酸浴工序出口溶液50ml(为回用冷冻残液水量的20%)混合,混合液共550ml,进行冷冻结晶,第一阶段降温至40摄氏度,并在40摄氏度的温度下维持20min;第二阶段降温至0摄氏度,并维持该温度20min,将固液混合离心分离,得到十水硫酸钠晶体和冷冻残液;(5)取步骤(4)的冷冻残液500ml进入电渗析装置,采用1000ml纯水作为吸收液(冷冻残液与纯水接收液的体积比为1:2),当淡水中的电导率与浓水中的电导率比值为1:5时,完成该工序。电渗析淡水(约1250ml)排入厂区污水处理厂处理,电渗析浓水(约250ml)回用至生产工艺中的酸浴工序;(6)取步骤(4)中的十水硫酸钠晶体25g(湿重,含水率为80%)溶解于50ml饱和硫酸钠中,溶液温度维持在60摄氏度,并加入氢氧化钠溶液调节固液混合物的ph至8.23左右,搅拌30min,离心分离,将固体重新用50ml饱和硫酸钠中,溶液温度维持在60摄氏度,再次搅拌30min,离心分离,固体经过烘干得到无水硫酸钠工业品标准中的一类一等品的纯度。实验步骤中的检测数据如表1-2所示。表1-2各处理步骤中水样的指标浓度回收的无水硫酸钠晶体的纯度检测指标如表1-3所示。表1-3无水硫酸钠晶体纯度指标数据及相关标准单位:%,ph无量纲实施例2(1)取某粘胶纤维公司的纺丝酸性废液进行实验,其酸性废液的初始指标如表2-1所示。表2-1原废液指标数据由表中的数据可以看出,废液中硫酸钠含量最高,浓度高达为5%,其次是硫酸,浓度达到了1.5%,硫酸锌和硫酸铝含量较低,两者之和的浓度达到0.13%,有机物的浓度较高,为2000ppm,长期富集会对酸性处理和生产工艺产生不可逆的影响。(2)取5000ml酸性废液进入精密过滤器,去除废液中的固体物质;(3)取5000ml精密过滤器出水进入旋转蒸发仪,蒸发温度为95摄氏度,当蒸发浓缩液的体积为750ml时(浓缩液的体积为原废液体积的15%),停止蒸发;(4)取蒸发浓缩液750ml和生产工艺中酸浴工序出口溶液70ml(为回用冷冻残液水量的20%)混合,混合液共820ml,进行冷冻结晶,第一阶段降温至50摄氏度,并在50摄氏度的温度下维持60min;第二阶段降温至-5摄氏度,并维持该温度60min,将固液混合离心分离,得到十水硫酸钠晶体和冷冻残液;(5)取步骤(4)的冷冻残液700ml进入电渗析装置,采用2100ml纯水作为吸收液(冷冻残液与纯水接收液的体积比为1:3),当淡水中的电导率与浓水中的电导率比值为1:7时,完成该工序。电渗析淡水(约2450ml)排入厂区污水处理厂处理,电渗析浓水(约350ml)回用至生产工艺中的酸浴工序;(6)取步骤(4)中的十水硫酸钠晶体50g(湿重,含水率为80%)溶解于75ml饱和硫酸钠中,溶液温度维持在70摄氏度,并加入氢氧化钠溶液调节固液混合物的ph至7.86,搅拌60min,离心分离,将固体重新用75ml饱和硫酸钠中,溶液温度维持在70摄氏度,再次搅拌60min,离心分离,固体经过烘干得到无水硫酸钠工业品标准中的一类一等品的纯度。实验步骤中的检测数据如表2-2所示。表2-2各处理步骤中水样的指标浓度回收的无水硫酸钠晶体的纯度检测指标如表2-3所示。表2-3无水硫酸钠晶体纯度指标数据及相关标准单位:%,ph无量纲实施例3(1)取某粘胶纤维公司的纺丝酸性废液进行实验,其酸性废液的初始指标如表3-1所示。表3-1原废液指标数据由表中的数据可以看出,废液中硫酸钠含量最高,浓度高达为5%,其次是硫酸,浓度达到了1.5%,硫酸锌和硫酸铝含量较低,两者之和的浓度达到0.13%,有机物的浓度较高,为2000ppm,长期富集会对酸性处理和生产工艺产生不可逆的影响。(2)取5000ml酸性废液进入精密过滤器,去除废液中的固体物质;(3)取5000ml精密过滤器出水进入旋转蒸发仪,蒸发温度为100摄氏度,当蒸发浓缩液的体积为1500ml时(浓缩液的体积为原废液体积的30%),停止蒸发;(4)取蒸发浓缩液1500ml和生产工艺中酸浴工序出口溶液80ml(为回用冷冻残液水量的30%)混合,混合液共1580ml,进行冷冻结晶,第一阶段降温至45摄氏度,并在45摄氏度的温度下维持45min;第二阶段降温至-10摄氏度,并维持该温度20min,将固液混合离心分离,得到十水硫酸钠晶体和冷冻残液;(5)取步骤(4)的冷冻残液700ml进入电渗析装置,采用3500ml纯水作为吸收液(冷冻残液与纯水接收液的体积比为1:5),当淡水中的电导率与浓水中的电导率比值为1:15时,完成该工序。电渗析淡水(约3935ml)排入厂区污水处理厂处理,电渗析浓水(约265ml)回用至生产工艺中的酸浴工序;(6)取步骤(4)中的十水硫酸钠晶体50g(湿重)溶解于50ml饱和硫酸钠中,溶液温度维持在50摄氏度,并加入氢氧化钠溶液调节固液混合物的ph至7.86,搅拌60min,离心分离,将固体重新用50ml饱和硫酸钠中,溶液温度维持在60摄氏度,再次搅拌30min,离心分离,固体经过烘干得到无水硫酸钠工业品标准中的一类一等品的纯度。实验步骤中的检测数据如表3-2所示。表3-2各处理步骤中水样的指标浓度回收的无水硫酸钠晶体的纯度检测指标如表3-3所示。表3-3无水硫酸钠晶体纯度指标数据及相关标准单位:%,ph无量纲实施例4(1)取某粘胶纤维公司的纺丝酸性废液进行实验,其酸性废液的初始指标如表4-1所示。表4-1原废液指标数据由表中的数据可以看出,废液中硫酸钠含量最高,浓度高达为5%,其次是硫酸,浓度达到了1.5%,硫酸锌和硫酸铝含量较低,两者之和的浓度达到0.13%,有机物的浓度较高,为2000ppm,长期富集会对酸性处理和生产工艺产生不可逆的影响。(2)取5000ml酸性废液进入精密过滤器,去除废液中的固体物质;(3)取5000ml精密过滤器出水进入旋转蒸发仪,蒸发温度为75摄氏度,当蒸发浓缩液的体积为2500ml时(浓缩液的体积为原废液体积的50%),停止蒸发;(4)取蒸发浓缩液2500ml和生产工艺中酸浴工序出口溶液60ml(为回用冷冻残液水量的10%)混合,混合液共2560ml,进行冷冻结晶,第一阶段降温至48摄氏度,并在48摄氏度的温度下维持50min;第二阶段降温至-3摄氏度,并维持该温度30min,将固液混合离心分离,得到十水硫酸钠晶体和冷冻残液;(5)取步骤(4)的冷冻残液700ml进入电渗析装置,采用2800ml纯水作为吸收液(冷冻残液与纯水接收液的体积比为1:4),当淡水中的电导率与浓水中的电导率比值为1:5时,完成该工序。电渗析淡水(约2920ml)排入厂区污水处理厂处理,电渗析浓水(约580ml)回用至生产工艺中的酸浴工序;(6)取步骤(4)中的十水硫酸钠晶体50g(湿重)溶解于100ml纯水中,溶液温度维持在65摄氏度,并加入氢氧化钠溶液调节固液混合物的ph至7.86,搅拌45min,过滤去除中和后溶液中的固体杂质,滤液经过蒸发结晶得到较为浓稠的固液混合物,离心分离,固体经过烘干得到无水硫酸钠工业品标准中的一类一等品的纯度。实验步骤中的检测数据如表4-2所示。表4-2各处理步骤中水样的指标浓度回收的无水硫酸钠晶体的纯度检测指标如表4-3所示。表4-3无水硫酸钠晶体纯度指标数据及相关标准单位:%,ph无量纲当前第1页12