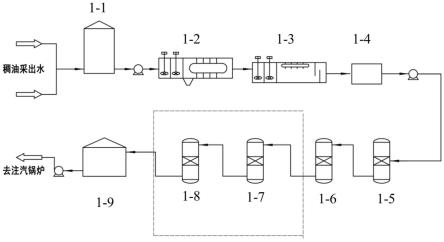
1.本发明涉及稠油采出水回用注汽锅炉技术领域,尤其涉及一种不除硅稠油采出水回用注汽锅炉的方法及系统。
背景技术:2.稠油资源分布很广,储量丰富,占石油总资源量的25%-30%以上,已成为我国重要能源保障之一。我国稠油开采以注蒸汽热力采油为主,稠油热采伴随着产生大量的高温、高含盐、高含硅、高含有机物的稠油采出水,稠油采出水经过除油、除悬浮物、除二氧化硅、除硬度后回用注汽锅炉使之循环利用,一方面可节省大量的宝贵的清水资源,另一方面可大幅降低稠油污水外排对环境的影响,同时可以充分利用稠油污水的温度(80-90℃)节约注汽锅炉的燃料,具有显著的经济、环境和社会效益。
3.我国稠油采出水中二氧化硅含量一般为100-300mg/l,而且随着稠油不断热力开采,稠油采出水中二氧化硅含量在逐渐升高。sy/t6086-2012热力采油蒸汽发生器运行技术规程水质指标要求稠油采出水的二氧化硅含量降低至50mg/l以下才能回用到注汽锅炉。国内外常以温石灰、热石灰和氢氧化钠等化学去除方法除硅,这些方法的共同特点是镁剂除硅,所谓的镁剂除硅是指在一定的ph条件下(比如9-11,通常采用石灰或者氢氧化钠进行ph调节),在水中投加氧化镁或氯化镁进行化学反应,形成碳酸镁或氢氧化镁等絮状物,利用碳酸镁或氢氧化镁絮状物吸附水中的溶解性硅酸化合物,生成硅酸镁沉淀,通过沉淀排泥使得硅酸化合物(俗称二氧化硅)得以去除。由于碳酸镁、氢氧化镁和硅酸镁等絮状物颗粒比较细小、轻飘,为了提高沉淀效果,通常需要额外投加聚铝和聚丙烯酰胺,通过吸附架桥的作用,增加絮状物颗粒粒径,有利于重力沉降,缩短沉淀时间。
4.在目前的稠油采出水回用注汽锅炉技术中,镁剂除硅存在以下不足:1、加药种类比较多。需要投加大量的氢氧化钠或石灰,氧化镁或氯化镁,聚铝和聚丙酰胺等化学药剂。2、加药量比较大,除硅成本比较高,每方稠油采出水需除硅药剂费约4-6元,给企业带来沉重的经济压力。3、由于投加的药剂种类较多,加药量较大,因此产生的硅泥量比较大,大约占处理水量的10%。这些硅泥由于含有一定的原油,属于危险废物,每吨危险废物的处理费至少1500元,给企业带来沉重的经济负担和生产经营压力。4、由于投加氢氧化钠或石灰,水中的ph由7左右上升到9-11,由中性变为强碱性,水质性质发生了明显的变化,而硅泥絮状物颗粒较小,很容易随水流入到后续的过滤系统、软化系统,导致滤料和树脂板结和结垢,影响过滤系统和软化系统的正常运行。
5.因此,亟需研究开发一种针对高含硅的稠油采出水的不除硅直接回用注汽锅炉的新技术。
技术实现要素:6.为了解决上述问题,本发明的目的在于提供一种无需除硅的稠油采出水回用注汽锅炉的方法及系统。该方法能够在不降温、不除硅、不除盐、不除有机物的情况下将高含硅
稠油采出水中二价三价结垢离子浓度降低至50μg/l以下,在不降低给水的二氧化硅浓度的情况下也可完全避免锅炉结垢问题的发生。
7.为了达到上述目的,本发明提供了一种不除硅稠油采出水回用注汽锅炉的方法,包括:对稠油采出水依次进行预处理、过滤处理和二价三价结垢离子深度处理,所述深度处理所用的处理剂包括大孔弱酸树脂,所述大孔弱酸树脂的原料包括质量比为(25-35):(32-50):(1-3):(0.8-1.2):(6-9)的基体材料、致孔剂、增强剂、引发剂、分散剂。
8.在本发明的具体实施方案中,上述方法不包括对稠油采出水进行除硅处理、即在整个处理过程中不添加除硅剂。在常规采出水回用注汽锅炉方法中,一般是在预处理后、软化处理前利用氧化镁氯化镁等除硅剂对采出水进行除硅处理,降低二氧化硅含量以避免二氧化硅与钙镁离子形成硅垢导致采出水在锅炉炉管中结垢。本发明研究发现,锅炉炉管结垢的发生主要与注汽锅炉本身的运行压力、温度以及产生的蒸汽的干度、水中二价三价结垢离子(ca
2+
、mg
2+
、fe
2+
、fe
3+
、al
3+
、ba
2+
、sr
3+
等)、以及水中二氧化硅浓度密切相关,而不是仅仅与硬度(ca
2+
、mg
2+
)和二氧化硅浓度有关。在保证锅炉运行的压力、温度和干度稳定的情况下,锅炉结垢与否主要是与二氧化硅和二价三价结垢离子(ca
2+
、mg
2+
、fe
2+
、fe
3+
、al
3+
、ba
2+
、sr
3+
等)浓度有关。对锅炉结垢物成分进一步分析发现,炉管结垢物主要为锥辉石(nabafealsi2o6)、钙铁榴石(ca3srfe2si3o
12
)和透闪石(ca2mg5si8o
22
(oh)2)。不论在何种水质条件下,垢样中都不会存在单独的二氧化硅垢,这说明二氧化硅如果不与其他结垢离子如ca
2+
、mg
2+
、fe
2+
、fe
3+
、al
3+
、ba
2+
、sr
3+
等结合,二氧化硅即不会结垢,这是在锅炉结垢机理认识上取得的重大突破,对此,本发明通过实施“高含硅稠油采出水回用注汽锅炉先导试验”表明:只要将二价三价结垢离子浓度深度去除至50μg/l以下,二氧化硅浓度即使由50mg/l提升至300mg/l也不会发生注汽锅炉炉管结垢的问题,也就是可以只进行二价三价结垢离子深度去除、同时取消除硅工艺。将本发明的上述方法应用于油田,能够取得显著的经济、环境、社会效益。
9.在上述方法中,所述预处理不包括除硅处理。经过深度处理的稠油采出水中二氧化硅含量小于300mg/l,基本与稠油采出水的典型水质中二氧化硅含量(100-300mg/l)持平,也就是可以不进行除硅。由于经过深度处理的稠油采出水的二价三价结垢离子浓度降低至50μg/l以下,也就是将稠油采出水中容易与二氧化硅结垢的ca
2+
、mg
2+
、fe
2+
、fe
3+
、al
3+
、ba
2+
、sr
3+
等二价三价离子的浓度处理到微量水平,因此经过上述方法处理后的稠油采出水虽然二氧化硅含量高,但不会在锅炉中生成硅垢,进而可以将锅炉给水中二氧化硅浓度低于50mg/l的标准提高至低于300mg/l,突破当前稠油采出水回用注汽锅炉的技术标准界限。
10.相比于常规强酸树脂只能将稠油采出水硬度(ca
2+
、mg
2+
)降低至0.3-0.5mg/l,本发明提供的大孔弱酸树脂可以彻底吸附稠油采出水中所有的二价三价结垢离子,将该大孔弱酸树脂作为深度处理剂应用于上述稠油采出水回用注汽锅炉方法时可以将稠油采出水的二价三价结垢离子(ca
2+
、mg
2+
、fe
2+
、fe
3+
、al
3+
、ba
2+
、sr
3+
等)浓度降低至50μg/l以下,在该二价三价结垢离子浓度条件下,即使二氧化硅的浓度稍高(例如二氧化硅含量高于100mg/l、小于300mg/l),也不会发生锅炉结垢的情况、或者结垢速度也会等同或低于除硅后的结垢速度。因此,本发明提供的稠油采出水回用注汽锅炉方法可以省略除硅处理,进而无需添加镁剂等除硅剂,节约投加药剂的成本和处理硅泥的成本,避免由于添加镁剂引起的过滤处理和软化处理过程中系统结垢的问题,提高生产效率、降低生产维修费用。
11.根据本发明的具体实施方案,在上述方法中,经过深度处理的稠油采出水的油含量一般小于2mg/l,悬浮物含量一般小于2mg/l,二氧化硅含量一般小于300mg/l,总溶解性固体含量一般小于7000mg/l,二价三价结垢离子浓度一般为50μg/l以下。
12.根据本发明的具体实施方案,在上述方法中,所述深度处理一般包括依次进行的一级深度处理和二级深度处理,经过一级深度处理的稠油采出水的硬度小于5mg/l,经过二级深度处理的稠油采出水中二价三价结垢离子浓度(ca
2+
、mg
2+
、fe
2+
、fe
3+
、al
3+
、ba
2+
、sr
3+
等)为50μg/l以下。所述一级深度处理和二级深度处理一般是分别以上述大孔弱酸树脂为深度处理剂进行。
13.根据本发明的具体实施方案,在上述方法中,在深度处理的过程中,所述大孔弱酸树脂在深度处理器中的工作滤速可以是20-30m/h、例如20-25m/h。所述大孔弱酸树脂在深度处理器中的装填高度可以是1-1.6m、例如1.4-1.6m。
14.根据本发明的具体实施方案,在上述方法中,所述预处理一般包括依次进行的除油缓冲处理、斜板除油处理、浮选处理。
15.根据本发明的具体实施方案,在上述方法中,所述除油缓冲处理的处理温度一般控制为60-90℃、时间一般为12小时。经过除油缓冲处理的稠油采出水的油含量一般小于500mg/l,悬浮物含量一般小于300mg/l。
16.根据本发明的具体实施方案,在上述方法中,所述斜板除油可以包括快速混合、慢速反应和斜板沉淀的操作。在快速混合的过程中,搅拌采用的搅拌桨的gt值可以为大于或等于1.5
×
104,破乳剂可以采用聚合氯化铝等除油剂,破乳剂的加药量可以为大于或等于150mg/l;在慢速反应的过程中,所述慢速反应的时间为15分钟,搅拌采用的搅拌桨的gt值可以为大于或等于1
×
104,助凝剂可以采用聚丙烯酰胺等,助凝剂的加药量可以为2-3mg/l;在斜板沉淀的过程中,所述斜板沉淀的时间一般为1.5小时。
17.根据本发明的具体实施方案,在上述方法中,经过斜板除油处理的稠油采出水的油含量一般小于50mg/l,悬浮物含量一般小于100mg/l。
18.根据本发明的具体实施方案,在上述方法中,所述浮选处理可以包括快速混合、慢速反应和浮选除杂的操作。在快速混合的过程中,所述快速混合的时间可以为1分钟,快速混合采用的搅拌桨的gt值可以为1.5
×
104,破乳剂可以采用聚合氯化铝等除油剂,破乳剂的加药量为20mg/l;在慢速反应的过程中,所述慢速反应的时间可以为3分钟,慢速反应采用的搅拌桨的gt值可以为1
×
104,助凝剂可以采用聚丙烯酰胺等,助凝剂的加药量可以控制为1-2mg/l;在浮选除杂的过程中,所述浮选除杂的时间可以为0.5小时。
19.根据本发明的具体实施方案,在上述方法中,经过浮选处理的稠油采出水的油含量一般小于10mg/l,悬浮物含量一般小于20mg/l,二氧化硅含量一般小于300mg/l,总硬度一般小于200mg/l。
20.根据本发明的具体实施方案,在上述方法中,经过过滤处理的稠油采出水的总硬度一般小于200mg/l,油含量一般小于2mg/l,悬浮物含量一般小于2mg/l,二氧化硅含量一般小于300mg/l,总溶解性固体含量一般小于7000mg/l。
21.根据本发明的具体实施方案,在上述方法中,所述过滤处理可以包括依次进行的一级过滤处理和二级过滤处理,经过一次过滤处理的稠油采出水的总硬度一般小于200mg/l,油含量一般小于5mg/l,悬浮物含量一般小于5mg/l,二氧化硅含量一般小于300mg/l,总
溶解性固体含量一般小于7000mg/l。
22.根据本发明的具体实施方案,所述过滤处理还可以包括在一级过滤处理之前进行过滤吸水处理的操作,所述过滤吸水的时间一般控制为0.5小时。
23.根据本发明的具体实施方案,在一级过滤处理的过程中,采用的滤料可以采用无烟煤等,正常滤速可以控制为13m/h,校核滤速可以控制为15.6m/h,工作周期可以控制为12小时。所述一级过滤处理可以包括采用气水联合等方式进行洗涤,水洗强度可以控制为13l/s.m2,水洗时间可以控制为10min,气洗强度可以控制为16nl/s
·
m2,气洗时间可以控制为5min。
24.根据本发明的具体实施方案,在二级过滤处理的过程中,采用的滤料可以采用无烟煤和金刚砂等,正常滤速可以控制为7.8m/h,校核滤速可以控制为8.7m/h,工作周期可以控制为24小时,所述一级过滤处理可以包括采用气水联合等方式进行洗涤,水洗强度可以控制为13l/s
·
m2,水洗时间可以控制为10min,气洗强度可以控制为16nl/s
·
m2,气洗时间可以控制为5min。
25.在本发明的具体实施方案中,用于二价三价结垢离子深度处理的大孔弱酸树脂具有以下特点:
26.1、能够耐受95℃以上(优选95-120℃)的高温,在高温条件下能够保持结构完整不破碎,在进行深度处理时无需降温,使用寿命长;
27.2、兼具较高的机械强度(290-310n/mm2)和较大的孔径(800nm-900nm)及孔道面积(800-1200m2/g),直径较大的有机物分子能够通过大孔弱酸树脂的孔道、便于有机物的吸附和脱附,从而有效防止有机物污染。
28.3、交换容量大(3.9-4.1mmol/ml),能够同时吸附大量的二价三价结垢离子(ca
2+
、mg
2+
、fe
2+
、fe
3+
、al
3+
、ba
2+
、sr
3+
)和少量有机物,不仅可以使稠油采出水的二价三价结垢离子浓度降低至50μg/l以下,还可以节约有机物去除剂的使用,能够不提前除盐、除有机物的前提下实现对稠油采出水中所有二价三价结垢离子(ca
2+
、mg
2+
、fe
2+
、fe
3+
、al
3+
、ba
2+
、sr
3+
)的深度处理;
29.4、树脂饱和或中毒后可再生,可通过酸再生、碱转型的方法使吸附在树脂中的无机盐离子(ca
2+
、mg
2+
、fe
2+
、fe
3+
、al
3+
、ba
2+
、sr
3+
等)和大分子有机物脱附,从而维持大孔弱酸树脂的交换容量、去除孔隙中的污染物,恢复其活性,具有可再生、可循环使用的特点。
30.根据本发明的具体实施方案,在上述大孔弱酸树脂中,所述致孔剂能够在所述大孔弱酸树脂内部形成大量毛细孔道、将基体材料形成的高分子分割为非均相凝胶结构,进而在树脂内部形成凝胶孔和毛细孔、扩大大孔弱酸树脂的孔径,提高孔道面积,加快离子交换反应速度、提高交换容量,不仅能够提高对二价三价结垢离子(ca
2+
、mg
2+
、fe
2+
、fe
3+
、al
3+
、ba
2+
、sr
3+
))的吸附能力,并且大孔弱酸树脂较大的孔径结构使直径较大的有机物分子也能够通过。在吸附过程中,大孔弱酸树脂对水中ca
2+
、mg
2+
、fe
2+
、fe
3+
、al
3+
、ba
2+
、sr
3+
的吸附能力远大于对有机物的吸附能力,因此对二价三价结垢离子的吸附过程不会受到有机物吸附过程的干扰。此外,所述大孔弱酸树脂在酸液和碱液中表现出一定的收缩膨胀能力,为二价三价结垢离子和有机物分子在大孔弱酸树脂中的吸附与脱附提供条件、提高大孔弱酸树脂的抗污染能力。在一些具体实施方案中,所述致孔剂可以是甲苯、二甲苯、聚乙二醇和羟丙基纤维素中的一种或两种以上的组合。
31.根据本发明的具体实施方案,在上述大孔弱酸树脂中,所述增强剂能够提高上述大孔弱酸树脂的交联度,进而所述大孔弱酸树脂的机械强度与耐高温性能大幅度提高。在一些实施方案中,所述大孔弱酸树脂的机械强度为290-310n/mm2,并能够耐受95℃以上的高温(一些具体实施方案中耐高温能力可达95-120℃),远远优于常规树脂。在一些具体实施方案中,所述增强剂可以包括丙烯腈和/或异丁腈等。
32.本发明通过研究发现,大孔弱酸树脂的孔径过小会导致其交换容量过小、深度处理效果不明显;大孔弱酸树脂的孔径过大则会破坏其机械性能,导致树脂易破碎。本发明通过将致孔剂与增强剂的用量控制在合适的范围内,能够在扩大大孔弱酸树脂的孔径、获得较大的交换容量和抗污染能力的同时兼顾较高的机械性质、提高其耐温能力。所述致孔剂与增强剂的质量比一般控制在(32-50):(1-3),例如控制为40:2。在一些具体实施方案中,致孔剂和增强剂在大孔弱酸树脂中原料的添加量可以控制为以下比例:所述基体材料、致孔剂、增强剂、引发剂、分散剂的质量比为30:(40-50):(1-2):1:(7-8)。
33.根据本发明的具体实施方案,在上述大孔弱酸树脂中,所述基体材料可以包括丙烯酸酯类化合物。所述丙烯酸酯类化合物可以包括丙烯酸甲酯、丙烯酸乙酯、2-甲基丙烯酸甲酯和2-甲基丙烯酸乙酯等中的一种或两种以上的组合。
34.根据本发明的具体实施方案,在上述大孔弱酸树脂中,所述引发剂可以包括明胶和/或聚乙烯醇等。
35.根据本发明的具体实施方案,在上述大孔弱酸树脂中,所述分散剂可以包括聚乙烯醇、明胶、羧甲基纤维素等中的一种或两种以上的组合。
36.在本发明的具体实施方案中,所述大孔弱酸树脂的原料还可以包括交联剂。
37.根据本发明的具体实施方案,在上述大孔弱酸树脂中,所述交联剂可以包括二乙烯基苯等。
38.在本发明的具体实施方案中,所述基体材料、交联剂的质量比一般为25-35:15-25,例如可以是30:20。
39.在一些具体实施方案中,所述基体材料、致孔剂、增强剂、交联剂、引发剂、分散剂的质量比可以为30:(40-50):(1-2):20:1:(7-8)。
40.在本发明的具体实施方案中,以质量份计,上述大孔弱酸树脂的原料可以包括:25-35份基体材料(一般为丙烯酸酯类化合物,例如丙烯酸甲酯、丙烯酸乙酯、2-甲基丙烯酸甲酯和2-甲基丙烯酸乙酯中的一种或两种以上的组合)、32-50份致孔剂(例如甲苯、二甲苯、聚乙二醇和羟丙基纤维素中的一种或两种以上的组合)、1-3份增强剂(丙烯腈和/或异丁腈等)、15-25份交联剂(二乙烯基苯等)、0.8-1.2份引发剂(明胶和/或聚乙烯醇等)、6-9份分散剂。优选地,以质量份计,所述大孔弱酸树脂的原料包括:30份基体材料、32-46份或30份-40份(优选40份)致孔剂、1-2份增强剂、20份交联剂、1份引发剂、7-8份分散剂。
41.根据本发明的具体实施方案,上述大孔弱酸树脂的制备方法一般包括:将上述大孔弱酸树脂的原料(包括基体材料、致孔剂、增强剂、分散剂、引发剂,进一步还可以包括交联剂等)混合后进行悬浮聚合、得到树脂珠体;将树脂珠体水解,得到所述大孔弱酸树脂。
42.根据本发明的具体实施方案,在上述大孔弱酸树脂的制备方法中,所述悬浮聚合的反应温度一般控制为70-95℃(例如85℃、90℃),反应时间一般控制为7-10小时(优选7-9小时,例如8小时),反应压力一般是常压。
43.根据本发明的具体实施方案,在上述大孔弱酸树脂的制备方法中,在所述水解过程中,所述致孔剂能够随水蒸发,从而在树脂珠体内形成大量毛细孔道,扩大所述大孔弱酸树脂的孔径和孔道面积。所述水解的温度一般是100℃、水解的时间一般是1小时。
44.在本发明的具体实施方案中,上述大孔弱酸树脂的制备方法可以包括:将基体材料、致孔剂、增强剂混合,然后加入交联剂、引发剂和分散剂,在70-95℃、常压条件下悬浮聚合7-10小时,得到树脂珠体;再将树脂珠体以100℃条件下水解1小时,得到所述大孔弱酸树脂。
45.相比于强酸树脂等常用的水处理剂,本发明采用的大孔弱酸树脂可以在饱和、中毒之后通过再生过程脱附其孔隙内的无机杂质和有机杂质、避免有机杂质污染,该再生过程可以使大孔弱酸树脂的交换容量完全恢复。
46.根据本发明的具体实施方案,在上述方法中,当经过一级深度处理稠油采出水的硬度大于5mg/l、或者经过所述二级深度处理稠油采出水二价三价结垢离子浓度大于50μg/l时(这两种情况下认为大孔弱酸树脂因饱和或中毒而失效),相应地,上述方法还可以包括将一级深度处理或二级深度处理采用的大孔弱酸树脂进行再生的操作,所述大孔弱酸树脂的再生过程一般包括:将大孔弱酸树脂依次在酸液、碱液中浸泡,直至稠油采出水经过再生的大孔弱酸树脂后二价三价结垢离子浓度达到50μg/l以下为止。
47.在上述再生过程中,所述大孔弱酸树脂在酸液、碱液中的浸泡时间一般根据树脂的收缩膨胀情况决定。具体来说,大孔弱酸树脂一般在酸液中浸泡至树脂高度降低程度达到30%,例如大孔弱酸树脂在酸液中浸泡的时间一般控制为≥1小时;在碱液中浸泡至树脂高度上升幅度达到65%,例如在碱液中浸泡的时间一般控制为≥1.5小时。
48.在本发明的具体实施方案中,当一级深度处理或二级深度处理采用的大孔弱酸树脂发生中毒或饱和时,在对失效的大孔弱酸树脂进行再生处理之后,可以以未失效的大孔弱酸树脂所填充的深度处理器作为一级深度处理装置,以失效后再生的大孔弱酸树脂所填充的深度处理器作为二级深度处理装置。
49.根据本发明的具体实施方案,在上述再生过程中,酸液浸泡大孔弱酸树脂能够将该树脂吸附的二价三价结垢离子置换出来,此时大孔弱酸树脂由na型转换为h型;而碱液浸泡树脂层能够重新将大孔弱酸树脂由h型转换为na型,避免对大孔弱酸树脂处理的稠油采出水水质的影响。此外,以酸液浸泡树脂层能够使大孔弱酸树脂收缩、以碱液浸泡树脂层能够使大孔弱酸树脂膨胀,收缩和膨胀的过程能够有利于大孔弱酸树脂吸附的二价三价结垢离子和有机物的脱出、从而维持树脂的交换效果、延长树脂的使用寿命。
50.根据本发明的具体实施方案,上述再生过程还可以包括在酸液浸泡前和/或在碱液浸泡后利用软化水(二价三价结垢离子浓度为50μg/l以下的水)进行洗涤的操作,用于去除大孔弱酸树脂中吸附的悬浮物等杂质。
51.根据本发明的具体实施方案,大孔弱酸树脂的再生程度一般通过稠油采出水检测,具体是利用大孔弱酸树脂对未经处理的稠油采出水进行深度处理,当处理后的稠油采出水中二价三价结垢离子的浓度达到50μg/l以下时,证明大孔弱酸树脂的交换容量完全恢复,再生过程完成。
52.在上述再生过程中,优选地,所述酸液的ph≤2,所述碱液的ph≥13。所述酸液可以是质量浓度为3-5%的盐酸等;所述碱液可以是质量浓度为3-5%的氢氧化钠溶液等。
53.本发明还提供了一种不除硅稠油采出水回用注汽锅炉系统,其包括依次连通的预处理系统、过滤系统和深度处理系统,该稠油采出水回用注汽锅炉系统能够实现上述不除硅稠油采出水回用注汽锅炉的方法。
54.在本发明的具体实施方案中,所述深度处理系统一般装填有大孔弱酸树脂、用于去除稠油采出水中的二价三价结垢离子,例如上述方法中采用的大孔弱酸树脂。
55.根据本发明的具体实施方案,所述不除硅稠油采出水回用注汽锅炉系统能够实现上述不除硅稠油采出水回用注汽锅炉方法。
56.根据本发明的具体实施方案,所述预处理系统用于首先对稠油采出水进行预处理。在具体实施方案中,所述预处理系统可以包括依次连通的除油缓冲水罐、斜板除油池、daf浮选机,分别用于进行除油缓冲处理、斜板除油处理、浮选处理。所述斜板除油池可以进一步包括快速混合池、慢速反应池和斜板沉淀池;所述daf浮选机可以进一步包括快速混合池、慢速反应池和和浮选机。在一些具体实施方案中,所述浮选机可以包括空压机、压力溶气罐、释放器、浮选区、浮渣刮板等,空压机用于空气压缩进入压力溶气罐中的水混合形成一定压力的溶气水,所述压力一般控制在0.3-0.5mpa;释放器用于将溶解在溶气水中的空气在浮选机中释放出来,形成直径为30微米左右的呈乳状液的气泡,这些数量巨大的直径非常细小的气泡与稠油采出水中的油和悬浮物结合在一起,在浮力的作用下一起上浮形成浮渣,通过刮板将浮渣去除,使进入浮选机中的稠油采出水得到进一步净化。
57.根据本发明的具体实施方案,所述预处理系统还可以包括过滤吸水池。在具体实施方案中,所述过滤吸水池的入口一般与daf浮选机的出口连接。
58.根据本发明的具体实施方案,所述过滤系统用于在预处理后对稠油采出水进行过滤处理。在具体实施方案中,所述过滤系统一般包括相互连接的一级过滤器和二级过滤器、分别用于进行一级过滤处理和二级过滤处理。所述一级过滤器的入口一般与预处理系统的出口连接,当所述预处理系统由依次连通的除油缓冲水罐、斜板除油池、daf浮选机组成时,所述一级过滤器的入口可以与daf浮选机的出口连接;当所述预处理系统进一步包括过滤吸水池时,所述过滤吸水池的出口可以与一级过滤器的入口连接。
59.根据本发明的具体实施方案,所述深度处理系统用于对稠油采出水进行二价三价结垢离子的深度处理。在具体实施方案中,所述深度处理一般包括一级深度处理器和二级深度处理器、分别用于进行一级深度处理和二级深度处理。所述一级深度处理器的入口一般与过滤系统的出口连接,当所述过滤系统包括上述一级过滤器和二级过滤器时,所述一级深度处理器的入口一般与二级过滤器的出口连接。
60.根据本发明的具体实施方案,所述深度处理系统的出口(二级深度处理器的出口)可以通过连接外输水罐,通过泵外输将处理后的稠油采出水输送至蒸汽锅炉。
61.本发明的有益效果在于:
62.1、本发明提供的稠油采出水回用注汽锅炉方法无需添加除硅剂,仅通过将稠油采出水中的二价三价结垢离子(ca
2+
、mg
2+
、fe
2+
、fe
3+
、al
3+
、ba
2+
、sr
3+
等)浓度降低至50μg/l以下,就能保证在稠油采出水含硅量高的情况下在回用注汽锅炉中时不发生结垢问题、保证锅炉安全运行。
63.2、由于无需添加除硅剂,本发明提供的上述方法既能够有效避免锅炉结垢的问题,还能够解决因添加镁剂除硅导致的加药量大、药剂添加、硅泥处理和除硅池及其配套设
施(加药系统和硅泥处理系统)等投资成本高、后续过滤系统和软化系统结垢严重等问题。
64.3、本发明提供的上述方法显著降低注汽锅炉对回用采出水中二氧化硅的含量要求、突破现有技术的限制,实现高含硅稠油采出水回用注汽锅炉,具有显著的经济、环境和社会效益。
附图说明
65.图1为实施例1的稠油采出水回用注汽锅炉系统的结构图。
66.图2为实施例2的注汽锅炉系统的工作流程图。
67.图3为对比例1的稠油采出水回用注汽锅炉系统的结构图。
68.图4为对比例1中除硅处理的流程图。
69.图5为测试例1中高含硅污水回用热注锅炉和除硅污水回用热注锅炉的管壁照片。
70.符号说明
71.除油缓冲水罐1-1,斜板除油池1-2,daf浮选机1-3,过滤吸水池1-4,一级过滤器1-5,二级过滤器1-6,一级深度处理器1-7,二级深度处理器1-8,一级软化处理器1-7a,二级软化处理器1-8a,外输水罐1-9,除硅池1-10;柱塞泵2-1,换热器2-2,对流段2-3,辐射段2-4,燃烧器2-5。
具体实施方式
72.为了对本发明的技术特征、目的和有益效果有更加清楚的理解,现对本发明的技术方案进行以下详细说明,但不能理解为对本发明的可实施范围的限定。
73.实施例1
74.本实施例提供了一种不除硅稠油采出水回用注汽锅炉系统,图1为该系统的结构连接示意图。具体地,该系统包括依次连接的除油缓冲水罐1-1,斜板除油池1-2,daf浮选机1-3,过滤吸水池1-4,一级过滤器1-5,二级过滤器1-6,一级深度处理器1-7,二级深度处理器1-8和外输水罐1-9。
75.其中,斜板除油池1-2包括依次连通的快速混合池、慢速反应池和斜板沉淀池。快速混合池和慢速反应池分别设有搅拌桨。
76.daf浮选机1-3包括依次连通的快速混合池、慢速反应池和浮选机。快速混合池和慢速反应池分别设有搅拌桨。浮选机包括空压机、压力溶气罐、释放器、浮选区、浮渣刮板。空压机用于将空气压缩进入压力溶气罐中的水混合形成一定压力的溶气水;释放器用于将溶气水中溶解的空气向浮选机中的稠油采出水释放,在稠油采出水中形成大量且细小的乳状液气泡;浮渣刮板用于将气泡与稠油采出水中的油、悬浮物结合形成的浮渣去除,净化稠油采出水。
77.一级深度处理器1-7与二级深度处理器1-8中分别填充为1.4m高的大孔弱酸树脂。外输水罐1-9用于收集处理后的稠油采出水并将其输送至注汽锅炉。
78.除油缓冲水罐1-1的出口与斜板除油池1-2中的快速混合池的入口连接,斜板除油池1-2中的斜板沉淀池的出口与daf浮选机1-3中的快速混合池的入口连接,daf浮选机1-3中的斜板沉淀池的出口与过滤吸水池1-4的入口连接,过滤吸水池1-4的出口与一级过滤器1-5的入口连接、一级过滤器1-5的出口与二级过滤器1-6的入口连接,二级过滤器1-6的出
口与一级深度处理器1-7的入口连接,一级深度处理器1-7的出口与二级深度处理器1-8的入口连接,二级深度处理器1-8的出口与外输水罐1-9的入口连接。外输水罐1-9与注汽锅炉入口相连。
79.本实施例中一级深度处理器1-7和二级深度处理器1-8中填充的大孔弱酸树脂制备方法如下:
80.以质量份计,先混合30份质量比为2:1的丙烯酸甲酯与丙烯酸乙酯(作为基体材料)、40份质量比为1:1的甲苯和二甲苯(作为致孔剂)、2份质量比为10:1的丙烯腈和异丁腈(作为增强剂)、然后加入20份二乙烯基苯(交联剂)、1份质量比为20:1明胶和聚乙烯醇(引发剂),7份羧甲基纤维素(作为分散剂),混合,得到大孔弱酸树脂原料。将大孔弱酸树脂原料在常压90℃悬浮聚合反应9小时,得到所述树脂珠体;将树脂珠体100℃水解1小时,得到大孔弱酸树脂。
81.实施例2
82.本实施例提供了一种不除硅稠油采出水回用注汽锅炉方法,该方法在实施例1提供的系统中进行,包括采用实施例1制备的大孔弱酸树脂进行二价三价结垢离子深度去除。
83.本实施例提供的稠油采出水回用注汽锅炉方法具体包括以下过程:
84.一、预处理:
85.1、除油缓冲处理:将稠油采出水进行水质水量调节,温度为60-90℃,处理时间为12小时,通过控制液位,可以将上浮的稠油回收后脱水。处理后的稠油采出水的油含量控制为500mg/l以下,悬浮物含量控制在300mg/l以下。
86.以上除油缓冲处理在除油缓冲罐1-1中进行。
87.2、斜板除油处理:
88.(1)快速混合处理:将经过除油缓冲处理的稠油采出水进行快速混合处理,处理时间为5分钟。处理过程中将聚合氯化铝等除油剂作为破乳剂加入稠油采出水,加药量控制在150mg/l;同时采用搅拌桨对稠油采出水进行搅拌,搅拌桨的gt值控制在1.5
×
104。
89.在一些具体实施方案中,以上快速混合处理在斜板除油池1-2中的快速混合池中进行。
90.(2)慢速反应处理:将经过快速混合处理的稠油采出水进行慢速反应处理,处理时间为15分钟。处理过程中将聚丙烯酰胺等作为助凝剂加入稠油采出水,加药量控制在2-3mg/l;同时采用搅拌桨对稠油采出水进行搅拌,搅拌桨的搅拌桨的gt值控制在1
×
104。
91.以上慢速反应处理在斜板除油池1-2中的慢速反应池中进行。
92.(3)斜板沉淀处理:将经过慢速反应处理的稠油采出水进行斜板沉淀处理,处理时间为1.5h。
93.以上斜板沉淀处理在斜板除油池1-2中的斜板沉淀池中进行。
94.经过斜板沉淀处理的稠油采出水的油含量控制在50mg/l以下,悬浮物含量控制在100mg/l以下。
95.3、浮选处理:
96.(1)快速混合处理:将经过斜板沉淀处理的稠油采出水进行快速混合处理,处理时间为1分钟。处理过程中将聚合氯化铝等除油剂作为破乳剂加入稠油采出水,加药量控制在20mg/l;同时采用搅拌桨对稠油采出水进行搅拌,搅拌桨的搅拌桨的gt值控制在1.5
×
104。
97.以上快速混合处理可以在daf浮选机1-3中的快速混合池中进行。
98.(2)慢速反应处理:将经过快速混合处理的稠油采出水进行慢速反应处理,处理时间为3分钟。处理过程中将聚丙烯酰胺等作为助凝剂加入稠油采出水,加药量控制在1-2mg/l;同时采用搅拌桨对稠油采出水进行搅拌,搅拌桨的搅拌桨的gt值控制在1
×
104。
99.以上慢速反应处理可以在daf浮选机1-3中的慢速反应池中进行。
100.(3)浮选除杂处理:将经过慢速反应处理的稠油采出水进行浮选除杂处理,处理时间为0.5小时。将压缩空气与水混合形成一定压力(一般为0.3-0.5mpa)的溶气水,将该溶气水中溶解的空气在稠油采出水中释放,在稠油采出水中形成直径为30微米左右的呈乳状液的大量气泡,气泡与水中的油和悬浮物结合在一起,在浮力的作用下一起上浮形成浮渣,去除浮渣,从而净化稠油采出水。
101.经过浮选除杂处理的稠油采出水的油的含量控制在10mg/l以下,悬浮物的含量控制在20mg/l以下,总硬度为200mg/l以下,二氧化硅的含量控制在300mg/l以下。
102.以上浮选处理可以在daf浮选机1-3中的浮选机中进行。
103.二、过滤处理:
104.4、过滤吸水处理:将浮选处理后的稠油采出水进行过滤吸水处理,处理的时间为0.5小时。该过滤吸水处理可以在过滤吸水池1-4中进行。
105.5、一级过滤处理:对经过过滤吸水处理的稠油采出水进行一级过滤处理,采用无烟煤作为滤料,正常滤速为13m/h,校核滤速为15.6m/h,工作周期为12小时。反洗方式采用气水联合反洗,水洗强度为13l/s.m2,水洗时间为10min,气洗强度为16nl/s.m2,气洗时间为5min。
106.经过一级过滤处理的稠油采出水的油含量小于5mg/l,悬浮物的含量小于5mg/l,二氧化硅的含量小于300mg/l,总硬度小于200mg/l,总溶解性固体的含量小于7000mg/l。
107.6、二级过滤处理:对经过二级过滤处理的稠油采出水进行二级过滤处理,采用无烟煤和金刚砂作为滤料,正常滤速为7.8m/h,校核滤速为8.7m/h,工作周期为24小时。反洗方式采用气水联合反洗,水洗强度为13l/s.m2,水洗时间为10min,气洗强度为16nl/s.m2,气洗时间为5min。
108.经过二级过滤处理的稠油采出水的油含量小于2mg/l,悬浮物含量小于2mg/l,二氧化硅含量小于300mg/l,总硬度小于200mg/l,总溶解性固体含量小于7000mg/l。
109.上述一级过滤处理、二级过滤处理可以分别在一级过滤器1-5、二级过滤器1-6中进行。
110.三、深度处理
111.7、一级深度处理:对经过二级过滤处理的稠油采出水采用实施例1中制备的大孔弱酸树脂进行一级深度处理。大孔弱酸树脂的装填高度为1.4m,工作滤速为20m/h。
112.经过一级深度处理的稠油采出水总硬度控制在5mg/l以下,油含量小于2mg/l,悬浮物含量小于2mg/l,二氧化硅含量小于300mg/l,总溶解性固体含量小于7000mg/l。
113.8、二级深度处理:对经过一级深度处理的稠油采出水采用实施例1中制备的大孔弱酸树脂进行二级深度处理。大孔弱酸树脂的装填高度为1m,工作滤速为30m/h。
114.经过二级深度处理的稠油采出水的所有二价三价结垢离子浓度之和控制在50μg/l以下,油含量小于2mg/l,悬浮物含量小于2mg/l,二氧化硅含量小于300mg/l,总溶解性固
体含量小于7000mg/l。
115.上述一级深度处理、二级深度处理可以分别在一级深度处理器1-7、二级深度处理器1-8中进行。
116.二级深度处理的出水即为回用注汽锅炉的稠油采出水,一般将出水收集在外输水罐1-9、然后向注汽锅炉输送。
117.四、再生处理
118.在上述方法中,当经过一级深度处理稠油采出水总硬度大于5mg/l、或者经过二级深度处理的稠油采出水的二价三价结垢离子浓度大于50μg/l时,说明一级深度处理器或者二级深度处理器中的大孔弱酸树脂已失效(即中毒或饱和)。这种情况下上述方法还包括将失效的大孔弱酸树脂进行原位再生处理,再生处理过程包括:
119.用深度处理后的水(二价三价结垢离子浓度在50μg/l以下的水)对大孔弱酸树脂进行反洗,再将大孔弱酸树脂在质量浓度为5%的盐酸溶液中浸泡至树脂的高度降低幅度达到30%(一般至少需要1小时),然后将大孔弱酸树脂在质量浓度为5%的氢氧化钠溶液中浸泡至树脂的高度上升幅度达到65%(一般至少需要1.5小时),再用深度处理后的水(即软水)洗涤大孔弱酸树脂、然后向大孔弱酸树脂中注入未经过处理的稠油采出水,测试大孔弱酸树脂对稠油采出水的处理效果。当经过处理的稠油采出水的二价三价结垢离子浓度为50μg/l以下时,树脂再生处理完毕;当经过处理的水二价三价结垢离子浓度大于50μg/l时,重复以上再生过程,直至经深度处理的稠油采出水的二价三价结垢离子浓度在50μg/l以下。
120.观察再生大孔弱酸树脂对有机物吸附能力的恢复情况:利用再生后的大孔弱酸树脂(实施例1中装填的大孔弱酸树脂失效后再生)对稠油采出水进行处理,水中的cod由350mg/l下降至300mg/l、与新制的大孔弱酸树脂对cod的降低程度相同,说明再生后的大孔弱酸树脂对有机物的吸附能力可基本恢复至新制大孔弱酸树脂的水平。上述结果说明大孔弱酸树脂中与其吸附的有机物之间结合能力较弱,再生过程可以使大孔弱酸树脂收缩和膨胀、利于树脂中有机物的脱附,因而能够基本恢复大孔弱酸树脂对有机物吸附的能力。
121.在一些实施方案中,当一级深度处理器或二级深度处理器中的大孔弱酸树脂经过再生处理后,可以将再生大孔弱酸树脂装填的深度处理器作为二级深度处理器,将没有经过再生处理、且没有出现失效的大孔弱酸树脂的深度处理器作为一级深度处理器,以保证对稠油采出水的深度处理效果,保持处理后的稠油采出水二价三价结垢离子浓度在50μg/l以下。
122.在具体实施方案中,经过上述不除硅稠油采出水回用注汽锅炉方法处理的稠油采出水一般由二级深度处理器出水进入外输水罐1-9,通过泵外输至注汽锅炉进水箱,经柱塞泵2-1强制升压进入注汽锅炉,注汽锅炉工作流程见图2。经过深度处理的稠油采出水首先进入换热器2-2外管,与换热器2-2内管的热水(260℃)换热至140℃,并通过旁路管线调节进入对流段2-3入口,与烟气(800-900℃)换热至260℃。然后进入换热器2-2内管,经与换热器2-2外管水换热降温至200℃。最后进入辐射段2-4,通过燃烧器2-5加热(900-1000℃),产生干度为80%,温度为280-300℃的饱和蒸汽,通过注汽管线注入油层,实现蒸汽采油。
123.对比例1
124.本对比例提供了一种包括除硅处理的稠油采出水回用注汽锅炉方法,其是在图3所示的稠油采出水回用注汽锅炉系统中进行的。该系统是在实施例1提供的系统的基础上
增加了除硅池1-10及其配套设施(加药系统和硅泥处理系统);除硅池1-10中投加氢氧化钠、镁盐(氯化镁和/或氧化镁)、聚铝和聚丙烯酰胺等,并分别用一级软化处理器1-7a、二级软化处理器1-8a代替一级深度处理器7、二级深度处理器8;一级软化处理器1-7a与二级软化处理器1-8a中装填的是常规大孔弱酸树脂(厂家为罗蒙哈斯,型号为d113)、而非实施例1中制备的大孔弱酸树脂。
125.本对比例提供的方法也与实施例2的方法基本相似,区别仅在于:
126.以常规大孔弱酸树脂进行的软化处理替代实施例2所用的大孔弱酸树脂进行的深度去除处理,并且在浮选除杂处理和过滤处理之间依次增加除硅处理的步骤,具体是将浮选除杂处理后的稠油采出水送入ph为11-13、含有氧化镁除硅剂(型号为hf-1)的除硅池中进行处理,除硅的过程如图4所示。再将除硅处理后的稠油采出水送入过滤吸水池按照实施例2中的流程进行之后的过滤吸水、过滤、软化处理等步骤。
127.以与实施例2相同的稠油采出水作为处理对象、进行上述稠油采出水回用注汽锅炉方法。稠油采出水原水、实施例2最终出水与本对比例最终出水的二氧化硅浓度以及二价三价结垢离子浓度检测结果总结在表1中(表1中的合计是指二价三价结垢离子浓度之和,不包括二氧化硅浓度)。
128.表1
[0129][0130]
实施例2的出水没有经过除硅处理、以下称为不除硅稠油污水,对比例1的出水经过除硅处理,以下称为除硅稠油污水,由表1可以看出,两种出水的水质主要存在以下不同点:1、二氧化硅浓度不同,不除硅稠油污水中二氧化硅浓度为298mg/l、是一种高含硅污水,除硅稠油污水中二氧化硅浓度为100mg/l、是一种除硅污水,不除硅稠油污水的二氧化硅含量是除硅稠油污水二氧化硅含量的近3倍;2、二价三价结垢离子浓度不同,不除硅稠油污水中的二价三价结垢离子浓度为23.5μg/l,而除硅稠油污水中二价三价结垢离子浓度高达462μg/l,是不除硅稠油污水的20倍。
[0131]
测试例1
[0132]
为了验证对比例1与实施例2处理得到的稠油采出水是否能够回用锅炉,采用两台注汽锅炉进行了不除硅稠油污水回用热注锅炉和除硅稠油污水回用热注锅炉试验对比试验,一台锅炉为不除硅稠油污水回用,蒸汽量为10t/h,也就是实施例2处理后的稠油采出水;另一台锅炉为除硅稠油污水回用,蒸汽量为10t/h,也就是对比例1处理后的稠油采出水。试验开始于2010年5月2日,整个试验分为两个阶段进行:
[0133]
第一阶段:2010年5月2日-6月30日,计划注汽10000方,实际注汽11374方。
[0134]
第二阶段:2010年7月10日-2011年5月6日,计划注汽50000方,实际注汽量57000方。
[0135]
试验结束后,对高含硅稠油污水回用锅炉和除硅稠油污水回用锅炉的炉管进行了
切割,图5为两个锅炉的炉管管壁照片,a图对应高含硅稠油污水回用锅炉、b图对应除硅稠油污水回用锅炉。
[0136]
从图5可以看出,高含硅稠油污水回用锅炉的结垢情况与除硅稠油污水回用锅炉的结垢情况相当、均是较为轻微的程度。这一结果说明,只要将二价三价结垢离子控制在微量浓度下,就可以在不除硅的情况下得到不结垢的稠油采出水,实现不除硅稠油污水回用锅炉的目的,具有显著的经济、环境和社会效益。
[0137]
测试例2
[0138]
本测试例提供了实施例2的不除硅稠油采出水回用注汽锅炉方法现的场试验结果。将实施例2的不除硅稠油采出水回用注汽锅炉方法在室内研究和现场中试成功的基础上进行了工程推广应用,具体是在我国辽河油田和新疆油田等稠油油田进行应用。应用后,所有高含硅(二氧化硅含量低于300mg/l)的稠油采出水的回用注汽锅炉工程全部停运除硅工艺,目前锅炉运行平稳,经济效益显著。
[0139]
在应用中,本发明提供的不除硅稠油采出水回用注汽锅炉方法具有以下优点:
[0140]
1、缩短工艺流程,由于取消除硅池和配套由于取消除硅池及配套设施(加药系统和硅泥处理系统),因此可节约基建投资15%以上;
[0141]
2、大幅降低运行成本,每方稠油采出水可节约除硅药剂费用4-6元,辽河油田利用该技术每年可以节约1亿元以上;
[0142]
3、大幅降低污泥处理成本,由于取消除硅系统、不产生硅泥,因此节省硅泥处理费1500元/方,辽河油田采用该技术每年可节约污泥处理费用1亿元以上;
[0143]
4、避免过滤和软化系统结垢,大幅度提高生产效率,大幅度降低生产维修费用。