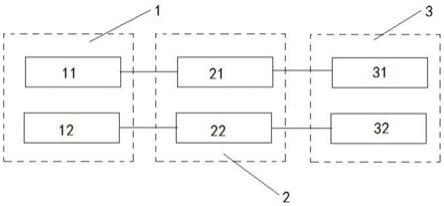
1.本发明涉及水处理领域,特别是涉及一种热力杀菌釜水处理自动控制系统及方法。
背景技术:2.罐装密封(马口铁罐、铝罐、玻璃管、软包)食品(如各种罐头、饮品、肉类等)在进入市场前需经历杀菌处理达到食品的商业无菌状态,从而提高食品的保质期。工业上杀菌方式主要以热力杀菌为主。将食品罐装密封好送入热杀菌设备中,通过水或蒸汽为介质,在高温条件下,将食物中的各种致病菌、腐败菌等杀死,达到食物的商业无菌状态。
3.热力杀菌设备有很多种,从生产的连续性上分类,主要有两大类,可分为连续式和非连续式杀菌釜。连续式杀菌釜典型的代表有静水压式杀菌釜、轨道式旋转杀菌釜,非连续式杀菌釜的典型代表有非连续式立式、卧式杀菌釜。我国使用较多的是静水压式杀菌釜、非连续式的卧式杀菌釜。
4.采用热力设备进行杀菌,其基本原理是利用高温条件将食物中的各种致病菌、腐败菌等杀灭,整个杀菌过程基本一致。其过程主要经历三个阶段:
5.预热:食品包装容器在杀菌釜中与预热水充分接触,提升封装食物的温度以达到逐渐接近杀菌温度的目的,此外还能达到降低蒸汽用量、降低能耗的目的。热水温度取决于采用的杀菌设备的类型,如果是非连续卧式杀菌釜,通常在杀菌釜中通入一定温度(温度一般在50-90℃之间)的热水;如果采用连续式静水压式杀菌设备,其热水预热区是一个随着水柱的下降而温度逐渐升高的温区,以此更接近随后的杀菌温度。
6.杀菌:在预热完成后,封装食物容器在高温蒸汽或水中进行杀菌处理,此期间的温度一般在100-130℃。以此杀灭各种致病菌、腐败菌等。
7.冷却:杀菌结束后进入冷却阶段,使食物容器充分与冷却水接触,以此降低食品温度。基于杀菌釜的种类不同,冷却方式及过程有存在差异,但其目的是将封装食物温度降低。静水压式连续杀菌釜的降温首先是进入带压冷却区,该冷却区水温较高,基本与预热区的温度保持对称,机内带压冷却区后温度随着水柱的升高不断降低,然后进入常压冷却;如果采用的非连续式的卧式杀菌釜,在杀菌结束后杀菌釜通入冷却水并循环,逐渐对杀菌釜和封装食物降温。
8.预热和冷却过程中,热水和冷水在杀菌釜中与杀菌釜本体和封装食物容器进行充分接触,并进行相应的的水循环,逐渐与杀菌釜本体以及封装食物进行换热从而达到预热和冷却的目的,杀菌釜和封装食物容器在热水和冷却水中有一定的停留时间,热水和冷却水会对杀菌釜本体金属和食物封装容器会产生严重的腐蚀。而考虑到热力杀菌生产条件的特殊性:(1)杀菌釜的主要制备材料是碳钢,还有少数部件采用不锈钢、铜等金。食物封装容器材料通常为玻璃、马口铁、铝合金、软包装等材料,在杀菌釜中包含多种金属材料,因此存在巨大的电偶腐蚀趋势;(2)杀菌釜的热水和冷却水相对于传统的敞开式循环冷却水的温度要高很多,热水可能高至90℃,甚至更高,冷却水温度也可能高至70℃,甚至更高,而高温
具有更高的腐蚀倾向;(3)冷却过程中,出水国标要求的余氯含量需要大于0.5ppm,高余氯会极大的加剧金属腐蚀。
9.考虑到热力杀菌生产的特殊性,相对于传统的循环冷却水,其腐蚀问题对设备和生产的影响会更严重、更难解决。该问题对热力杀菌与封装食物产品可能造成的巨大的影响:严重的腐蚀导致设备经常停机检修,增加维修成本,降低生产率,因停产产生的隐性损失更是不可估量;腐蚀还导致设备使用寿命大幅下降,国内一般在3年左右,甚至短则1年就报废了,杀菌釜属于高投入的重资产设备,无形中增加生产成本;更严重的问题是腐蚀产物易附着在封装食物容器表面,大大提高封装食物产品的次品率。
10.为了进行设备保护、降低维修频率、提高生产率、提高成品率、降低成本,需要对热力杀菌过程中的水处理进行一定的化学处理以抑制严重的腐蚀,而一套卓越的、完整的水处理控制系统是关键。目前在国内热力杀菌过程中,由于水处理条件相对苛刻,难度较大,基本没有进行完整的水处理的系统和方法。
技术实现要素:11.本发明的目的是提供一种热力杀菌釜水处理自动控制系统及方法,通过监测杀菌釜预热水和冷却水的一些特征参数,实现对杀菌釜水处理的控制,帮助使用杀菌釜的食品生产企业提高设备使用寿命、降低维修频率、提高生产率、提高成品率、降低成本。
12.为实现上述目的,本发明提供了如下方案:
13.一种热力杀菌釜水处理自动控制系统,所述系统包括:取样模块,监测模块和控制模块;
14.所述取样模块包括热取样管路和冷取样管路,所述热取样管路和所述冷取样管路分别用于从热水区获得热取样水和从冷水区获得冷取样水;
15.所述监测模块包括热水监测子模块和冷水监测子模块,所述热水监测子模块用于对所述热取样水的在线荧光进行监测;所述冷水监测子模块用于对所述冷取样水的在线荧光和在线余氯进行监测;
16.所述控制模块包括热水控制子模块和冷水控制子模块;所述热水控制子模块,与所述热水监测子模块连接,用于根据所述热取样水的在线荧光信号控制是否向所述热水区中投加复合型药剂;所述冷水控制子模块,与所述冷水监测子模块连接,用于根据所述冷取样水的在线荧光信号控制是否向所述冷水区中投加复合型药剂以及根据所述冷取样水的余氯信号控制是否向所述冷水区中投加氧化性杀菌剂。
17.本发明还提供一种热力杀菌釜水处理自动控制方法,应用于上述控制系统,所述方法包括:
18.对热水区和冷水区分别取样,得到热取样水和冷取样水;
19.分别对所述热取样水和所述冷取样水进行在线荧光监测,获得热取样水的在线荧光信号和冷取样水的在线荧光信号;
20.根据所述热取样水的在线荧光信号控制是否向所述热水区投放复合型药剂,根据所述冷取样水的在线荧光信号控制是否向所述冷水区投放复合型药剂;
21.对所述冷取样水进行在线余氯监测,获得冷取样水的在线余氯信号;
22.根据所述冷取样水的在线余氯信号控制是否向所述冷水区投放氧化性杀菌剂。
23.根据本发明提供的具体实施例,本发明公开了以下技术效果:
24.本发明提供的热力杀菌釜水处理自动控制系统及方法,设置热取样管路和冷取样管路分别进行热水和冷水取样,并设置热水监测子模块和冷水监测子模块同时对取样热水和取样冷水中的在线荧光信号进行监测。由于本发明的药剂中复配了一定比例的荧光示踪剂,通过在线荧光信号的强度可以获得药剂浓度的在线实时值,当热水或冷水中的药剂浓度值低于预设药剂浓度阈值时,分别通过热水控制子模块向热水区投放复合型药剂,以及通过冷水控制子模块向冷水区投放复合型药剂,通过投放该药剂可以缓解杀菌釜中热水区和冷水区的腐蚀。同时,本发明还通过冷水监测子模块对冷取样水的在线余氯进行监测,如当在线余氯值低于预设余氯阈值时,通过冷水控制子模块向冷水区投加氧化性杀菌剂,以使得冷水中的余氯值高于预设余氯阈值,进而达到余氯出水标准。本发明上述方案中通过对杀菌釜的热水和冷水同时监测,无论热水或冷水任何一方的水质出现加剧腐蚀的情况时,均采取投放药剂等方式来缓解,进而大幅提高杀菌釜水处理效果,提升杀菌釜使用寿命,降低维修频率,降低成本。
附图说明
25.为了更清楚地说明本发明实施例或现有技术中的技术方案,下面将对实施例中所需要使用的附图作简单地介绍,显而易见地,下面描述中的附图仅仅是本发明的一些实施例,对于本领域普通技术人员来讲,在不付出创造性劳动的前提下,还可以根据这些附图获得其他的附图。
26.图1为本发明实施例1提供的热力杀菌釜水处理自动控制系统结构图;
27.图2为本发明实施例2提供的热力杀菌釜水处理自动控制方法流程图。
28.符号说明:
29.1-取样模块;2-监测模块;3-控制模块;4-数字化管理模块;11-热取样管路;12-冷取样管路;21-热水监测子模块;22-冷水监测子模块;211-第一液位传感器;212-第一微型冷却器;213-第一温度探测器;214-第二温度探测器;221-第二液位传感器;222-第二微型冷却器;223-第三温度探测器;224-第四温度探测器;31-热水控制子模块;32-冷水控制子模块。
具体实施方式
30.下面将结合本发明实施例中的附图,对本发明实施例中的技术方案进行清楚、完整地描述,显然,所描述的实施例仅仅是本发明一部分实施例,而不是全部的实施例。基于本发明中的实施例,本领域普通技术人员在没有做出创造性劳动前提下所获得的所有其他实施例,都属于本发明保护的范围。
31.本发明的目的是提供一种热力杀菌釜水处理自动控制系统及方法,对杀菌釜的热水和冷水同时监测和控制,大大提升杀菌釜水处理的处理效果,帮助使用杀菌釜的食品生产企业提高设备使用寿命,降低维修频率,提升生产连续性及生产效率,提高成品率,降低成本、提升企业竞争力。
32.为使本发明的上述目的、特征和优点能够更加明显易懂,下面结合附图和具体实施方式对本发明作进一步详细的说明。
33.实施例1
34.本实施例提供一种热力杀菌釜水处理自动控制系统,请参阅图1,所述系统包括:取样模块1,监测模块2和控制模块3。
35.取样模块1包括热取样管路11和冷取样管路12,热取样管路11和冷取样管路12分别用于从热水区获得热取样水和从冷水区获得冷取样水。
36.监测模块2包括热水监测子模块21和冷水监测子模块22,热水监测子模块21用于对热取样水的在线荧光进行监测;冷水监测子模块22用于对冷取样水的在线荧光和在线余氯进行监测。
37.需要说明的是,本实施例可以根据需要监测的信息对应设置传感器,例如上述对取样水中的在线荧光进行监测,则可以设置热水监测子模块21和冷水监测子模块22均包括在线荧光传感器,需要对冷取样水的在线余氯进行监测,则可以设置冷水监测子模块22中还包含在线余氯传感器。
38.控制模块3包括热水控制子模块31和冷水控制子模块32;热水控制子模块31,与热水监测子模块21连接,用于根据热取样水的在线荧光信号控制是否向热水区中投加复合型药剂;冷水控制子模块32,与冷水监测子模块22连接,用于根据冷取样水的在线荧光信号控制是否向冷水区中投加复合型药剂。
39.上述复合型药剂包括分散剂、缓蚀剂、阻垢剂等药剂,通过在使用的药剂中复配一定比例的荧光示踪剂,并通过在线荧光传感器监测荧光强度以获得药剂浓度的在线实时值。通过设置药剂浓度的控制范围来投加药剂。如药剂浓度控制在10
±
1ppm,那么当药剂浓度低于9ppm时,通过控制模块3开启加药泵投加药剂,当检测到浓度高于11ppm时,通过控制模块3关闭加药泵停止投加药剂。
40.现实中杀菌釜的预热水和冷却水的温度超过50℃时有发生,这给药剂浓度的监测带来了挑战,因为在相对高的温度下,对荧光信号的监测将会发生偏差,检测不再准确,这给水处理控制带来了较大的挑战,在一定程度上影响了水处理效果。
41.作为一种可选的实施方式,本实施例中,热水监测子模块21还包括第一微型冷却器212,第一温度探测器213和第二温度探测器214;第一微型冷却器212设置于热取样管路11上,第一温度探测器213和第二温度探测器214分别设置于第一微型冷却器212前后,并分别用于探测进入第一微型冷却器212前的水温以及经过第一微型冷却器212之后的水温,热水控制子模块31还用于根据第一温度探测器213探测的水温控制第一微型冷却器212的启停;
42.冷水监测子模块22还包括第二微型冷却器222,第三温度探测器223和第四温度探测器224;第二微型冷却器222设置于冷取样管路12上,第三温度探测器223和第四温度探测器224分别设置于第二微型冷却器222前后,并分别用于探测进入第二微型冷却器222前的水温以及经过第二微型冷却器222之后的水温,冷水控制子模块32还用于根据第三温度探测器223探测的水温控制第二微型冷却器222的启停。
43.通过在热水和冷却水的取样水管路各安装微型冷却器以使得进入在线荧光传感器的水温低于45℃,提升在线荧光信号检测准确性。在冷却器前后安装温度传感器,通过温度信号,以控制微型冷却器的冷水的启停。
44.现有的水处理,大多是根据国家标准要求在冷却水中投入大量的氧化型杀菌剂以
达到大于0.5ppm的出水余氯标准,而余氯信号基本是通过定时人工检测,然后再手动投加氧化性杀菌剂至冷却水中,或者是通过定时器连续的投加至冷却水中,常常导致冷却水余氯值长期远高于0.5ppm,引起的腐蚀问题十分严重。
45.本实施例中,冷水监测子模块22还对冷取样水的在线余氯(或氧化还原电位orp)进行监测,冷水控制子模块32还用于根据冷取样水的余氯信号(或氧化还原电位orp)控制是否向冷水区中投加氧化性杀菌剂。如余氯控制范围在0.6
±
0.1ppm,那么当余氯低于0.5ppm时,通过冷水控制子模块32开启加药泵投加氧化性杀菌剂,当余氯大于0.7ppm时,通过冷水控制子模块32关闭加药泵停止投加氧化性杀菌剂,这样可以将冷却水的余氯值精确控制在大于0.5ppm以满足标准,但同时小于0.7ppm,以最大限度的降低余氯对腐蚀的影响。也可通过orp信号控制是否投加氧化性杀菌剂,余氯值与氧化还原电位有一定的对应值,这取决于每个现场的水质情况,首先确定对应关系,如已确定某水质余氯0.5ppm时,对应的orp值为500mv,那么可以将orp范围设置在550
±
50mv,当低于500mv时,开始控制氧化性杀菌剂的投加,而当高于氧化还原电位高于600mv时停止氧化性杀菌剂的投加。
46.杀菌釜中的热水和冷水除了会对釜体金属和封装食物容器产生腐蚀危害外,还易产生结垢及沉积、微生物污垢等危害。由于在生产过程中对某些部件局部要涂抹润滑油以增强部件衔接或转动的润滑性,而润滑油会滋生微生物问题,因此水体有巨大的微生物滋生倾向,容易形成污垢。同时,生产过程还可能存在爆罐现象,食物从容器中泄露到水中,增加水中的有机物含量,促进微生物滋生及繁殖,容易形成污垢。结垢沉积、微生物污垢的影响除了降低换热效率外,其主要的影响在食物罐体,一旦在食物罐体发生结垢沉积附着在外表面,严重影响食品安全、降低成品率。因此,解决结垢与沉积、微生物污染等对确保食品安全、设备保护、提高生产率、降低成本等同样至关重要。
47.基于上述情况,本实施例的热水监测子模块21还用于对热取样水的电导率、总铁、浊度以及化学需氧量进行监测,热水控制子模块31还用于根据热取样水的电导率、总铁、浊度以及化学需氧量信号实现热水区的热水排污控制;
48.冷水监测子模块22还用于对冷取样水的电导率、总铁、浊度以及化学需氧量进行监测,冷水控制子模块32还用于根据冷取样水的电导率、总铁、浊度以及化学需氧量信号实现冷水区的冷水排污控制。
49.通常情况下,本实施例采用电导率的设置范围进行排污控制,如电导率控制在500
±
20μs/cm,那么当电导率高于520μs/cm时,控制模块3开启排污泵进行排污直至电导率降低到480μs/cm以下控制模块3关闭排污泵停止排污。
50.杀菌釜的热水和冷却水的具体状况与传统的敞开式循环冷却水略有不同,有其特殊性如总铁高,余氯高,高cod(化学需氧量)等,这些参数都无法体现在传统的循环冷却水控制系统中,对热水和冷却水的排污也不能完全按照传统的电导率的设置范围模式进行排污。
51.本实施例提供的上述方案,当热水和冷却水遭遇苛刻的水质环境时,同样可以进行排污,例如出现腐蚀加剧,当总铁、浊度、或在线cod含量超过其临界值,均可以通过控制模块3启动排污泵强行进行排污,直到其相应的值达到合理范围,如设置可容忍的总铁范围为0.5-2ppm,那么当总铁大于2ppm时,可启动排污泵强行排污直到总铁小于0.5ppm为止关闭排污泵停止排污,即使此时热水系统的电导率还未达到排污标准。
52.需要说的是,本领域技术人员还可根据需要,设置监测模块2包含其他相应的传感器,例如当需要监测热水区和冷水区的ph值时,则可设置热水监测子模块21和冷水监测子模块22均包含ph传感器,从而分别监测热取样管路11和冷取样管路12中水的ph值;当需要监测热水区和冷水区的腐蚀率时,可以设置热水监测子模块21和冷水监测子模块22均包含在线腐蚀率传感器或腐蚀挂片,从而分别监测热取样管路11和冷取样管路12中的腐蚀,本实施例并不对此进行限制。
53.经过排污有效降低了热水或冷水中的总铁、cod、浊度等,但同样也会使得热水区或冷水区的水位下降,基于此,本实施例设置的热水监测子模块21还包括第一液位传感器211,第一液位传感器211设置于热水区,用于获取热水区的液位信号;冷水监测子模块22包括第二液位传感器221,第二液位传感器221设置于冷水区,用于获取冷水区的液位信号;
54.热水控制子模块31还用于根据热水区的液位信号控制向热水区补水,冷水控制子模块32还用于根据冷水区的液位信号控制向冷水区补水。
55.考虑到杀菌釜水处理过程中的数据记录问题,以及为方便用户进行数字化管理,提高杀菌釜水处理效率,本实施例提供的水处理控制系统还包括数字化管理模块4,数字化管理模块4与取样模块1、监测模块2和控制模块3均连接,用于对系统各模块的数据进行记录并存储到云端。
56.实施例2
57.本实施例提供一种热力杀菌釜水处理自动控制方法,本实施例提供的方法应用于实施例1所述的系统,请参阅图2,所述方法包括:
58.对热水区和冷水区分别取样,得到热取样水和冷取样水;
59.分别对所述热取样水和所述冷取样水进行在线荧光监测,获得热取样水的在线荧光信号和冷取样水的在线荧光信号;
60.根据所述热取样水的在线荧光信号控制是否向所述热水区投放复合型药剂,根据所述冷取样水的在线荧光信号控制是否向所述冷水区投放复合型药剂;
61.对所述冷取样水进行在线余氯监测,获得冷取样水的在线余氯信号;
62.根据所述冷取样水的在线余氯信号控制是否向所述冷水区投放氧化性杀菌剂。
63.作为一种可选的实施方式,所述方法还包括:
64.分别对所述热取样水和所述冷取样水的电导率、总铁、浊度以及化学需氧量进行监测;
65.根据所述冷取样水的电导率、总铁、浊度以及化学需氧量信号控制是否对所述冷水区的冷水排污;
66.根据所述热取样水的电导率、总铁、浊度以及化学需氧量信号控制是否对所述热水区的热水排污。
67.作为一种可选的实施方式,所述方法还包括:
68.通过第一液位传感器211获取所述热水区的液位信号,通过第二液位传感器221获取所述冷水区的液位信号;
69.根据所述热水区的液位信号控制是否向所述热水区补水,根据所述冷水区的液位信号控制是否向所述冷水区补水。
70.可选的,热取样管路上设置第一微型冷却器,冷取样管路上设置第二微型冷却器;
所述方法还包括:
71.利用第一温度探测器213对进入第一微型冷却器212前的水温进行监测,利用第二温度探测器214对通过第一微型冷却器212后的水温进行监测;
72.根据所述第一温度探测器213监测的水温和所述第二温度探测器214监测的水温控制所述第一微型冷却器212的启停;
73.利用第三温度探测器223对进入第二微型冷却器222前的水温进行监测,利用第四温度探测器224对通过第二微型冷却器222后的水温进行监测;
74.根据所述第三温度探测器223监测的水温和所述第四温度探测器224监测的水温控制所述第二微型冷却器222的启停。
75.作为一种可选的实施方式,所述方法还包括:
76.通过数字化模块4对所述杀菌釜水处理自动控制过程中的数据进行记录并存储到云端。
77.本发明提供的杀菌釜水处理自动控制系统及方法,可同时提供杀菌釜热水、冷却水精确的监控,大幅提升杀菌釜水处理效果,提升杀菌釜使用寿命,降低维修频率、提高生产率、降低成本、提升企业竞争力。
78.通过引入更多的水质处理结果窗口参数传感器如总铁、腐蚀率、浊度、cod等,可能基于结果导向(如总铁、浊度、在线cod)调控排污方式,避免单一电导率控制引起的弊端(如高总铁、浊度、cod导致的各种腐蚀、沉积污垢等问题),提升水处理效果。
79.通过在热水、冷却水取样水均安装微型冷却器,可实现在高温条件下的精准检测在线荧光信号,药剂浓度监控更精确,水处理效果更好。
80.通过数字化管理提升杀菌釜水处理效率。
81.本说明书中各个实施例采用递进的方式描述,每个实施例重点说明的都是与其他实施例的不同之处,各个实施例之间相同相似部分互相参见即可。
82.本文中应用了具体个例对本发明的原理及实施方式进行了阐述,以上实施例的说明只是用于帮助理解本发明的方法及其核心思想;同时,对于本领域的一般技术人员,依据本发明的思想,在具体实施方式及应用范围上均会有改变之处。综上所述,本说明书内容不应理解为对本发明的限制。