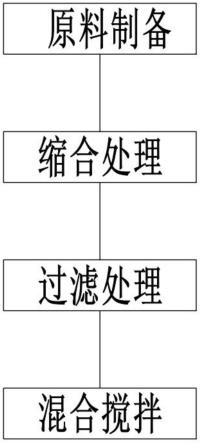
1.本发明涉及缓蚀剂技术领域,具体涉及一种污水汽提塔缓蚀剂的制备方法。
背景技术:2.污水缓蚀剂,污水缓蚀剂即高碱高硬水用缓蚀阻垢剂。采用大分子有机膦、多元共聚物和高分子聚合物等组成。
3.如授权公告号为cn107641811b,授权公告日为20190712的一种聚合物型高效复配缓蚀剂及其制备方法与应用。所述缓蚀剂为三元复配型缓蚀剂,缓蚀剂包括主缓蚀剂、辅缓蚀剂、表面活性剂和去离子水;其中,主缓蚀剂、辅缓蚀剂和表面活性剂的质量之比为(6-10):(5-20):(4-8);主缓蚀剂为聚乙二醇-聚丙二醇-聚乙二醇三嵌段共聚物;辅缓蚀剂为聚乙二醇辛基苯基醚;表面活性剂为十六烷基三甲基溴化铵。复配型缓蚀剂的制备方法包括将所述主缓蚀剂、辅缓蚀剂和表面活性剂加入去离子水中,溶解均匀,得到缓蚀剂。聚合物型高效复配缓蚀剂能够在抑制碳钢在酸液中的腐蚀中应用。本发明提供的复配型缓蚀剂具有应用广泛、作用高效、效果稳定、协同效应好,且用量少和制备方法简单等一系列优点。
4.上述以及在现有技术中的缓蚀剂原料成本较高,导致缓蚀剂生产成本较高,而且现有缓蚀剂制备过程较为复杂,因此,亟需设计一种污水汽提塔缓蚀剂的制备方法解决上述问题。
技术实现要素:5.本发明的目的是提供一种污水汽提塔缓蚀剂的制备方法,以解决现有技术中的上述不足之处。
6.为了实现上述目的,本发明提供如下技术方案:
7.一种污水汽提塔缓蚀剂的制备方法,包括以下步骤:
8.s1.原料制备:
9.s1.1:
10.s1.1.1粉末制备:选取合适的植物原材料,而后对原材料进行水洗浸泡处理,而后进行晾晒,之后进行切割与粉碎处理,最后再将切碎的物料倒入粉碎研磨设备中进行粉碎研磨处理,而后在进行过筛处理,从而得到物料粉末;
11.s1.1.2加料搅拌:将称量好的粉末倒入微波萃取设备中,而后在加入溶剂,随后在启动搅拌器对物料进行搅拌,再启动微波萃取设备,从而对混合的溶液进行提取处理;
12.s1.1.3浓缩提取:在上述步骤完成后,使用抽滤设备对溶液进行抽滤处理,同时将抽滤的溶液倒入浓缩罐内部进行浓缩处理,之后在将浓缩处理好的溶液倒入存储罐内部存储;
13.s1.1.4甲酯化预处理:称取合适的上述浓缩好的溶液,而后将溶液倒入罐体内部,同时在加入一定量的硫酸、蒸馏水,之后启动罐体上的加热结构进行加热,使得溶液分层,而后用分液设备进行分液处理,而后在用热水进行洗涤,而后在将上清液进行抽取,从而得
到脂肪酸;
14.s1.2研磨处理:将选取的原料倒入粉碎研磨设备中,而后启动设备,从而对原材料进行粉碎研磨处理,从而得到粉末;
15.s2.缩合处理:将s1.1中得到脂肪酸与一定量的乙二胺倒入缩合设备中,而后在加入缩合剂,之后在启动缩合设备,使得脂肪酸与乙二胺进行缩合反应,从而得到咪唑啉;
16.s3.过滤处理:将上述得到的咪唑啉倒入过滤设备,而后启动压滤结构,从而进行压滤处理,得到无杂质的咪唑啉;
17.s4.混合搅拌:将s3得到的咪唑啉与一定量的s1.2得到的粉末及添加剂倒入搅拌设备中,而后启动搅拌器,对搅拌设备中的物料进行搅拌,得到缓蚀剂,之后在将缓蚀剂存入存储罐中进行存储。
18.进一步地,所述s1.1.1中植物原材料为海带、豆科植物根茎叶等,所述s1.1.2中溶剂为石油醚。
19.进一步地,所述s1.1.2中粉末与溶剂比为:1:6-10,所述s1.1.2中微波萃取设备微波功率400-600w,温度30-70℃,时间为3-8min。
20.进一步地,所述s1.1.3中抽滤时产生滤渣继续提取,且滤渣提取次数为1-3次。
21.进一步地,所述s1.1.4中浓缩溶液:硫酸:蒸馏水固液比例为:1:2:2,且硫酸的浓度为:0.5mol/l。
22.进一步地,所述s1.1.4中加热时间为45-80min,所述s1.1.4中热水洗涤次数为三次。
23.进一步地,所述s1.2中原材料为活性炭、沸石、竹炭中的一种。
24.进一步地,所述s2中缩合剂为碱或者醇钠。
25.进一步地,所述s4中添加剂为醛类化合物、羟乙基六氢均三嗪、降凝剂、适量去离子水及表面活性剂、钠盐。
26.在上述技术方案中,本发明提供的一种污水汽提塔缓蚀剂的制备方法,(1)本发明设计的粉末制备方法,在生产该缓蚀剂时,粉末制备方法制备的脂肪酸可以降低该缓蚀剂原料的成本,实现对植物根茎叶的资源再利用,降低生产成本;(2)本发明所设计的缓蚀剂产品生产工艺简单环保,性价比高,可以有效解决污水介质对金属设备管线的腐蚀问题,且产品不含磷、硫化合物,可以避免对后续装置催化剂中毒即高温部位设备管线腐蚀的问题;(3)本发明所设计的添加剂、活性炭粉末,在使用该缓蚀剂对污水处理时,添加剂可以提高缓蚀剂的性能,同时易生产,毒性小,环境污染小,经济效益高,符合节能减排与清洁生产的要求,而且活性炭粉末可以吸附污水中的颗粒物质,使得污水沉降效果提高,有利于提高缓蚀剂性能。
附图说明
27.为了更清楚地说明本技术实施例或现有技术中的技术方案,下面将对实施例中所需要使用的附图作简单地介绍,显而易见地,下面描述中的附图仅仅是本发明中记载的一些实施例,对于本领域普通技术人员来讲,还可以根据这些附图获得其他的附图。
28.图1为本发明一种污水汽提塔缓蚀剂的制备方法实施例提供的制备方法流程图。
29.图2为本发明一种污水汽提塔缓蚀剂的制备方法实施例提供的原料制备流程图。
30.图3为本发明一种污水汽提塔缓蚀剂的制备方法实施例提供的用途流程图。
具体实施方式
31.为了使本领域的技术人员更好地理解本发明的技术方案,下面将结合附图对本发明作进一步的详细介绍。
32.如图1-2所示,本发明实施例提供的一种污水汽提塔缓蚀剂的制备方法,包括以下步骤:
33.s1.原料制备:
34.s1.1.1粉末制备:选取合适的植物原材料,而后对原材料进行水洗浸泡处理,而后进行晾晒,之后进行切割与粉碎处理,最后再将切碎的物料倒入粉碎研磨设备中进行粉碎研磨处理,而后在进行过筛处理,从而得到物料粉末;
35.s1.1.2加料搅拌:将称量好的粉末倒入微波萃取设备中,而后在加入溶剂,随后在启动搅拌器对物料进行搅拌,再启动微波萃取设备,从而对混合的溶液进行提取处理;
36.s1.1.3浓缩提取:在上述步骤完成后,使用抽滤设备对溶液进行抽滤处理,同时将抽滤的溶液倒入浓缩罐内部进行浓缩处理,之后在将浓缩处理好的溶液倒入存储罐内部存储;
37.s1.1.4甲酯化预处理:称取合适的上述浓缩好的溶液,而后将溶液倒入罐体内部,同时在加入一定量的硫酸、蒸馏水,之后启动罐体上的加热结构进行加热,使得溶液分层,而后用分液设备进行分液处理,而后在用热水进行洗涤,而后在将上清液进行抽取,从而得到脂肪酸;
38.s1.2研磨处理:将选取的原料倒入粉碎研磨设备中,而后启动设备,从而对原材料进行粉碎研磨处理,从而得到粉末;
39.s2.缩合处理:将s1.1中得到脂肪酸与一定量的乙二胺倒入缩合设备中,而后在加入缩合剂,之后在启动缩合设备,使得脂肪酸与乙二胺进行缩合反应,从而得到咪唑啉;
40.s3.过滤处理:将上述得到的咪唑啉倒入过滤设备,而后启动压滤结构,从而进行压滤处理,得到无杂质的咪唑啉;
41.s4.混合搅拌:将s3得到的咪唑啉与一定量的s1.2得到的粉末及添加剂倒入搅拌设备中,而后启动搅拌器,对搅拌设备中的物料进行搅拌,得到缓蚀剂,之后在将缓蚀剂存入存储罐中进行存储。
42.具体的,本实施例中,包括以下步骤:
43.s1.原料制备:
44.s1.1.1粉末制备:选取海带、豆科植物根茎叶,而后对原材料进行水洗浸泡处理,而后进行晾晒,之后进行切割与粉碎处理,最后再将切碎的物料倒入粉碎研磨设备中进行粉碎研磨处理,而后在进行过筛处理,从而得到物料粉末;
45.s1.1.2加料搅拌:将称量好的粉末倒入微波萃取设备中,而后在加入石油醚溶剂,粉末与溶剂比为:1:8,随后在启动搅拌器对物料进行搅拌,再启动微波萃取设备,此时微波萃取设备微波功率500w,温度50℃,时间为5min从而对混合的溶液进行提取处理;
46.s1.1.3浓缩提取:在上述步骤完成后,使用抽滤设备对溶液进行抽滤处理,抽滤时产生滤渣继续提取,且滤渣提取次数为3次,同时将抽滤的溶液倒入浓缩罐内部进行浓缩处
理,之后在将浓缩处理好的溶液倒入存储罐内部存储;
47.s1.1.4甲酯化预处理:称取合适的上述浓缩好的溶液,而后将溶液倒入罐体内部,同时在加入一定量的0.5mol/l硫酸、蒸馏水,浓缩溶液:硫酸:蒸馏水固液比例为:1:2:2,之后启动罐体上的加热结构进行加热,使得溶液分层,而后用分液设备进行分液处理,而后在用热水进行洗涤,而后在将上清液进行抽取,从而得到脂肪酸;
48.s1.2研磨处理:将选取的活性炭原料倒入粉碎研磨设备中,而后启动设备,从而对原材料进行粉碎研磨处理,从而得到粉末;
49.s2.缩合处理:将s1.1中得到脂肪酸与一定量的乙二胺倒入缩合设备中,而后在加入缩合剂,之后在启动缩合设备,使得脂肪酸与乙二胺进行缩合反应,从而得到咪唑啉;
50.s3.过滤处理:将上述得到的咪唑啉倒入过滤设备,而后启动压滤结构,从而进行压滤处理,得到无杂质的咪唑啉;
51.s4.混合搅拌:将s3得到的咪唑啉与一定量的s1.2得到的粉末及醛类化合物、羟乙基六氢均三嗪、降凝剂、适量去离子水及表面活性剂、钠盐倒入搅拌设备中,而后启动搅拌器,对搅拌设备中的物料进行搅拌,得到缓蚀剂,之后在将缓蚀剂存入存储罐中进行存储。
52.本发明提供的一种污水汽提塔缓蚀剂的制备方法,在生产该缓蚀剂时,粉末制备方法制备的脂肪酸可以降低该缓蚀剂原料的成本,实现对植物根茎叶的资源再利用,降低生产成本。
53.本发明提供的另一个实施例中,如图2所示的,s1.1.1中植物原材料为海带、豆科植物根茎叶等,s1.1.2中溶剂为石油醚。
54.本发明提供的另一个实施例中,如图2所示的,s1.1.2中粉末与溶剂比为:1:8,s1.1.2中微波萃取设备微波功率500w,温度50℃,时间为5min。
55.本发明提供的另一个实施例中,如图2所示的,s1.1.3中抽滤时产生滤渣继续提取,且滤渣提取次数为3次。
56.本发明提供的另一个实施例中,如图2所示的,s1.1.4中浓缩溶液:硫酸:蒸馏水固液比例为:1:2:2,且硫酸的浓度为:0.5mol/l。
57.本发明提供的另一个实施例中,如图2所示的,s1.1.4中加热时间为60min,s1.1.4中热水洗涤次数为三次。
58.本发明提供的另一个实施例中,如图2所示的,s1.2中原材料为活性炭、沸石、竹炭中的一种。
59.本发明提供的另一个实施例中,如图1所示的,s2中缩合剂为碱或者醇钠。
60.本发明提供的另一个实施例中,如图1所示的,s4中添加剂为醛类化合物、羟乙基六氢均三嗪、降凝剂、适量去离子水及表面活性剂、钠盐。
61.一种污水汽提塔缓蚀剂的用途,如图3所示,包括以下步骤:
62.s1.倒入池体:将上述制备的缓蚀剂按一定量进行称量,而后在将缓蚀剂倒入废水池中;
63.s2.搅拌处理:在上述缓蚀剂进入废水池中时,可以启动搅拌器,使得废水池中的废水与缓蚀剂混合均匀;
64.s3.反应沉降:在上述缓蚀剂与废水混合均匀后,缓蚀剂内部的颗粒成分会吸附污水中颗粒,使得污水出现沉降,同时缓蚀剂中碱或酸会与废水进行反应,中和废水;
65.s4.排出污水:而后将上述处理好的废水用泵抽入其他设备中进行处理,之后在将处理好的废水排放出去。
66.实施例一
67.一种污水汽提塔缓蚀剂的制备方法,包括以下步骤:
68.s1.原料制备:
69.s1.1.1粉末制备:选取海带、豆科植物根茎叶,而后对原材料进行水洗浸泡处理,而后进行晾晒,之后进行切割与粉碎处理,最后再将切碎的物料倒入粉碎研磨设备中进行粉碎研磨处理,而后在进行过筛处理,从而得到物料粉末;
70.s1.1.2加料搅拌:将称量好的粉末倒入微波萃取设备中,而后在加入石油醚溶剂,粉末与溶剂比为:1:6,随后在启动搅拌器对物料进行搅拌,再启动微波萃取设备,此时微波萃取设备微波功率500w,温度50℃,时间为5min从而对混合的溶液进行提取处理;
71.s1.1.3浓缩提取:在上述步骤完成后,使用抽滤设备对溶液进行抽滤处理,抽滤时产生滤渣继续提取,且滤渣提取次数为3次,同时将抽滤的溶液倒入浓缩罐内部进行浓缩处理,之后在将浓缩处理好的溶液倒入存储罐内部存储;
72.s1.1.4甲酯化预处理:称取合适的上述浓缩好的溶液,而后将溶液倒入罐体内部,同时在加入一定量的0.5mol/l硫酸、蒸馏水,浓缩溶液:硫酸:蒸馏水固液比例为:1:2:2,之后启动罐体上的加热结构进行加热,使得溶液分层,而后用分液设备进行分液处理,而后在用热水进行洗涤,而后在将上清液进行抽取,从而得到脂肪酸;
73.s1.2研磨处理:将选取的活性炭原料倒入粉碎研磨设备中,而后启动设备,从而对原材料进行粉碎研磨处理,从而得到粉末;
74.s2.缩合处理:将s1.1中得到脂肪酸与一定量的乙二胺倒入缩合设备中,而后在加入缩合剂,之后在启动缩合设备,使得脂肪酸与乙二胺进行缩合反应,从而得到咪唑啉;
75.s3.过滤处理:将上述得到的咪唑啉倒入过滤设备,而后启动压滤结构,从而进行压滤处理,得到无杂质的咪唑啉;
76.s4.混合搅拌:将s3得到的咪唑啉与一定量的s1.2得到的粉末及醛类化合物、羟乙基六氢均三嗪、降凝剂、适量去离子水及表面活性剂、钠盐倒入搅拌设备中,而后启动搅拌器,对搅拌设备中的物料进行搅拌,得到缓蚀剂,之后在将缓蚀剂存入存储罐中进行存储。
77.实施例二
78.一种污水汽提塔缓蚀剂的制备方法,包括以下步骤:
79.s1.原料制备:
80.s1.1.1粉末制备:选取海带、豆科植物根茎叶,而后对原材料进行水洗浸泡处理,而后进行晾晒,之后进行切割与粉碎处理,最后再将切碎的物料倒入粉碎研磨设备中进行粉碎研磨处理,而后在进行过筛处理,从而得到物料粉末;
81.s1.1.2加料搅拌:将称量好的粉末倒入微波萃取设备中,而后在加入石油醚溶剂,粉末与溶剂比为:1:8,随后在启动搅拌器对物料进行搅拌,再启动微波萃取设备,此时微波萃取设备微波功率500w,温度50℃,时间为5min从而对混合的溶液进行提取处理;
82.s1.1.3浓缩提取:在上述步骤完成后,使用抽滤设备对溶液进行抽滤处理,抽滤时产生滤渣继续提取,且滤渣提取次数为3次,同时将抽滤的溶液倒入浓缩罐内部进行浓缩处理,之后在将浓缩处理好的溶液倒入存储罐内部存储;
83.s1.1.4甲酯化预处理:称取合适的上述浓缩好的溶液,而后将溶液倒入罐体内部,同时在加入一定量的0.5mol/l硫酸、蒸馏水,浓缩溶液:硫酸:蒸馏水固液比例为:1:2:2,之后启动罐体上的加热结构进行加热,使得溶液分层,而后用分液设备进行分液处理,而后在用热水进行洗涤,而后在将上清液进行抽取,从而得到脂肪酸;
84.s1.2研磨处理:将选取的活性炭原料倒入粉碎研磨设备中,而后启动设备,从而对原材料进行粉碎研磨处理,从而得到粉末;
85.s2.缩合处理:将s1.1中得到脂肪酸与一定量的乙二胺倒入缩合设备中,而后在加入缩合剂,之后在启动缩合设备,使得脂肪酸与乙二胺进行缩合反应,从而得到咪唑啉;
86.s3.过滤处理:将上述得到的咪唑啉倒入过滤设备,而后启动压滤结构,从而进行压滤处理,得到无杂质的咪唑啉;
87.s4.混合搅拌:将s3得到的咪唑啉与一定量的s1.2得到的粉末及醛类化合物、羟乙基六氢均三嗪、降凝剂、适量去离子水及表面活性剂、钠盐倒入搅拌设备中,而后启动搅拌器,对搅拌设备中的物料进行搅拌,得到缓蚀剂,之后在将缓蚀剂存入存储罐中进行存储。
88.实施例三
89.一种污水汽提塔缓蚀剂的制备方法,包括以下步骤:
90.s1.原料制备:
91.s1.1.1粉末制备:选取海带、豆科植物根茎叶,而后对原材料进行水洗浸泡处理,而后进行晾晒,之后进行切割与粉碎处理,最后再将切碎的物料倒入粉碎研磨设备中进行粉碎研磨处理,而后在进行过筛处理,从而得到物料粉末;
92.s1.1.2加料搅拌:将称量好的粉末倒入微波萃取设备中,而后在加入石油醚溶剂,粉末与溶剂比为:1:10,随后在启动搅拌器对物料进行搅拌,再启动微波萃取设备,此时微波萃取设备微波功率500w,温度50℃,时间为5min从而对混合的溶液进行提取处理;
93.s1.1.3浓缩提取:在上述步骤完成后,使用抽滤设备对溶液进行抽滤处理,抽滤时产生滤渣继续提取,且滤渣提取次数为3次,同时将抽滤的溶液倒入浓缩罐内部进行浓缩处理,之后在将浓缩处理好的溶液倒入存储罐内部存储;
94.s1.1.4甲酯化预处理:称取合适的上述浓缩好的溶液,而后将溶液倒入罐体内部,同时在加入一定量的0.5mol/l硫酸、蒸馏水,浓缩溶液:硫酸:蒸馏水固液比例为:1:2:2,之后启动罐体上的加热结构进行加热,使得溶液分层,而后用分液设备进行分液处理,而后在用热水进行洗涤,而后在将上清液进行抽取,从而得到脂肪酸;
95.s1.2研磨处理:将选取的活性炭原料倒入粉碎研磨设备中,而后启动设备,从而对原材料进行粉碎研磨处理,从而得到粉末;
96.s2.缩合处理:将s1.1中得到脂肪酸与一定量的乙二胺倒入缩合设备中,而后在加入缩合剂,之后在启动缩合设备,使得脂肪酸与乙二胺进行缩合反应,从而得到咪唑啉;
97.s3.过滤处理:将上述得到的咪唑啉倒入过滤设备,而后启动压滤结构,从而进行压滤处理,得到无杂质的咪唑啉;
98.s4.混合搅拌:将s3得到的咪唑啉与一定量的s1.2得到的粉末及醛类化合物、羟乙基六氢均三嗪、降凝剂、适量去离子水及表面活性剂、钠盐倒入搅拌设备中,而后启动搅拌器,对搅拌设备中的物料进行搅拌,得到缓蚀剂,之后在将缓蚀剂存入存储罐中进行存储。
99.实施例一、实施例二和实施例三中采用的石油醚溶剂质量不同,通过对最终得到
的锰酸锂进行实验比对,实施例二中萃取脂肪酸的效果最佳。
100.工作原理:s1.倒入池体:将上述制备的缓蚀剂按一定量进行称量,而后在将缓蚀剂倒入废水池中;s2.搅拌处理:在上述缓蚀剂进入废水池中时,可以启动搅拌器,使得废水池中的废水与缓蚀剂混合均匀;s3.反应沉降:在上述缓蚀剂与废水混合均匀后,缓蚀剂内部的颗粒成分会吸附污水中颗粒,使得污水出现沉降,同时缓蚀剂中碱或酸会与废水进行反应,中和废水;s4.排出污水:而后将上述处理好的废水用泵抽入其他设备中进行处理,之后在将处理好的废水排放出去。
101.以上只通过说明的方式描述了本发明的某些示范性实施例,毋庸置疑,对于本领域的普通技术人员,在不偏离本发明的精神和范围的情况下,可以用各种不同的方式对所描述的实施例进行修正。因此,上述附图和描述在本质上是说明性的,不应理解为对本发明权利要求保护范围的限制。