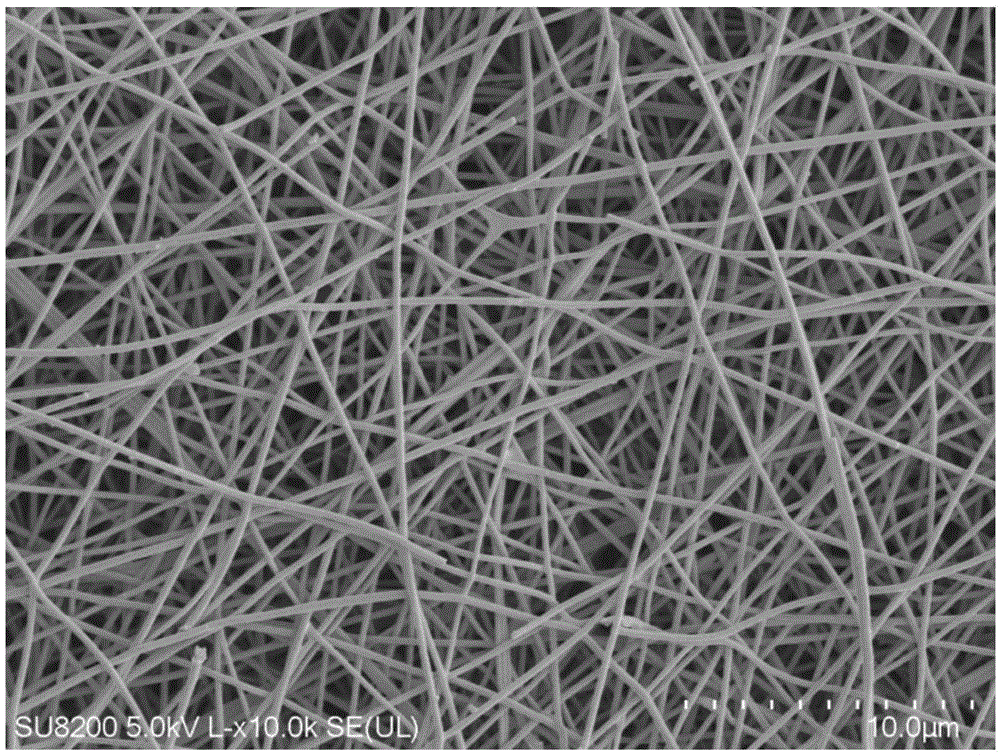
本发明属于催化剂领域,特别涉及用于炔丙基醇部分加氢制备烯丙基醇的催化剂及其制法。
背景技术:
:炔丙基醇选择性加氢制备烯丙基醇是精细化工领域的一项重要工艺。而烯丙基醇作为重要的化学合成中间体,广泛应用于农药、医药和新材料等领域。专利cn1966480a公开了一种以铅毒化的pd/c作为催化1,4-丁炔二醇部分加氢的催化剂,在35-45℃和0.6-1.7mpa下合成1,4丁烯二醇,此催化剂含有重金属铅,对环境产生不利影响,不适合大规模工业化推广。reimer等介绍了一种适用于单取代长碳链炔选择性加氢的贵金属催化剂。该催化剂以金属织物为载体,通过气相沉淀法或浸渍法将pd、bi、ag负载在金属织物上。他们通过气相沉淀法制备出pd-bi/金属织物催化剂,通过浸渍法制备出pd-ag/金属织物催化剂。这款催化剂的选择性不高,副产物大量产生。工业上,炔丙基醇选择性加氢制备烯丙基醇的反应多采用lindlar催化剂,即通过一定量的醋酸铅毒化5%的pd/caco3,并在釜式反应器中加入喹啉。lindlar催化剂为粉末状催化剂,反应结束后需进行过滤操作;并且重金属铅、喹啉的引入具有环境不友好、分离工艺复杂等缺点。因此,如何制备绿色环保、高转化率、高选择性、使用寿命长的催化剂成为制约炔丙基醇选择性加氢制备烯丙基醇工艺发展的关键因素。技术实现要素:本发明的目的在于提供一种用于炔丙基醇部分加氢制备烯丙基醇的催化剂及其制法。制法简单;制得的该催化剂绿色环保、具有高转换率和高选择性、使用寿命长,能够促进炔丙基醇选择性加氢制备烯丙基醇工艺的健康发展。本发明的另一个目的在于提供一种利用前述的催化剂进行炔丙基醇部分加氢制备烯丙基醇的方法。为实现上述目的,本发明采用以下技术方案:一种用于炔丙基醇部分加氢制备烯丙基醇的催化剂的制法,包括如下步骤:(1)以含氮或硫小分子芳环化合物为原料,以路易斯酸为催化剂,进行缩聚反应得到低聚体,所得低聚体依次进行研磨、洗涤和干燥处理得低聚体粉末;所述含氮或硫小分子芳环化合物中,含有1-3个苯环,且至少一个苯环上含有氮或硫;所述洗涤可以为碱洗、水洗或者二者相结合;(2)将所述步骤(1)得到的低聚体粉末和助纺剂加入溶剂中混合均匀得到纺丝溶液,然后采用静电纺丝技术将所述纺丝溶液纺制成纳米纤维膜;(3)将所述步骤(2)得到的纳米纤维膜置于炭化炉中依次进行预氧化、炭化和活化处理,得到碳纳米纤维膜载体;(4)将所述步骤(3)得到的碳纳米纤维膜载体在反应器(比如反应釜)与可溶性金属硫酸盐、硫脲、表面活性剂和水热反应所需的去离子水混合,并进行水热反应以在所述碳纳米纤维膜载体上进行助催化剂组分的负载,然后固液分离得到负载后的碳纳米纤维膜载体;(5)将所述步骤(4)得到的负载后的碳纳米纤维膜载体浸渍于含钯活性组分的盐溶液中进行催化剂活性组分的负载,然后固液分离得到含钯活性组分的催化剂产品。本发明步骤(1)中,所述低聚体通常是指平均聚合度不大于6的聚合体,比如为2.5、3、4或5.5。水热反应是指在密封的压力容器中,在一定的温度和压力下,在水、水溶液或蒸汽等流体中所进行有关化学反应的总称。水热法又称热液法。利用本发明的制法得到的催化剂中含有n和/或s,将其用于炔丙基醇部分加氢制备烯丙基醇的反应中时,起到了毒化剂/抑制剂的作用,能够在炔基加氢时,抑制双键加氢生成单键的反应,只促进三键加氢生成双键的反应,从而提高加氢反应的转化率和选择性。采用本发明催化剂的制法制备催化剂过程中,采用静电纺丝技术制备出的纳米纤维膜,以及该纳米纤维膜依次经预氧化、炭化和活化处理后得到的碳纳米纤维膜载体均为整体结构,无需其他成型工艺;并且碳纳米纤维膜载体的中空结构使活性位点最大程度暴露,从而使得制得的催化剂能够对炔丙基醇部分加氢制备烯丙基醇的反应起到较好的催化作用,提高反应的转化率和加氢选择性。助催化剂组分以及活性组分的负载,有利于提高催化剂的催化效果,从而进一步提高加氢反应的转化率和加氢选择性。优选地,所述步骤(1)中,路易斯酸催化剂选自alcl3、bf2、ticl4、sncl4、fecl3、sbcl5和febr3中的一种或多种。优选地,所述步骤(1)中,路易斯酸催化剂与所述含氮或硫小分子芳环化合物的质量比为1:(2-20),进一步优选1:(5-10),比如1:8。缩聚反应是可逆反应,反应速率及聚合度与反应的平衡之间有密切的关系。催化剂能够通过改变缩聚反应的活化能而影响其反应方向和反应速率,从而影响其聚合度。催化剂与所述含氮或硫小分子芳环化合物的质量比能够影响缩聚反应的反应方向、反应速率及聚合度,当该摩尔比为1:(2-20),特别是1:(5-10)时,能够在保证缩聚反应正向进行的基础上,使其能够快速反应得到低聚物,且能使低聚物产品的聚合度达到适合纺丝的要求,从而获得性能优良的纳米纤维膜及碳纳米纤维膜载体,以便于得到具有较高活性和加氢选择性的催化剂以用于炔丙基醇部分加氢制备烯丙基醇反应中。优选地,所述步骤(1)中,所述含氮或硫小分子芳环化合物选自喹啉、吡啶、异喹啉、噻吩、苯并喹啉、苯并异喹啉和苯并噻吩中的一种或多种。优选地,所述步骤(1)中,缩聚反应的反应温度为100-400℃,反应时间为1-20h;进一步优选反应温度为200-300℃,反应时间为4-10h。缩聚反应的反应温度和反应时间能够影响其反应速率和产物的聚合度,当缩聚反应的反应温度为100-400℃,反应时间为1-20h,特别是反应温度为200-300℃,反应时间为4-10h时,能够进一步保证反应快速进行得到低聚物,且能使低聚物产品的聚合度达到适合纺丝的要求,从而获得性能优良的纳米纤维膜及碳纳米纤维膜载体,以便于得到具有较高活性和加氢选择性的催化剂以用于炔丙基醇部分加氢制备烯丙基醇反应中。本发明所用静电纺丝技术为本领域所熟知,其通常是将纺丝溶液或熔体通过针头(针头的内径可以为0.2-2.0mm,比如0.2mm、0.4mm、0.5mm、1.0mm、1.6mm或2.0mm)输出为纺丝液滴,然后通过施加在针头上的电压(电压可以为10-30kv,比如15kv、10kv、25kv或30kv)使纺丝液滴在针头处被加速而纺制成丝,并经旋转的接收装置(接收装置可以为金属滚筒收集器,转速可以为100-1000rpm,比如100rpm、200rpm、300rpm、600rpm、800rpm或1000rpm)收集,从而得到纳米纤维。为了提高纺丝溶液的性能以得到性能更好的纳米纤维膜及碳纳米纤维膜载体,优选地,所述步骤(2)中,所述助纺剂选自聚乙烯吡咯烷酮、聚苯胺、聚丙烯腈、碳纳米管和酚醛树脂中的一种或多种。进一步优选地,所述步骤(2)中,所述低聚体粉末与所述助纺剂的质量比为1:(0.5-10),进一步优选为1:(1-7),再进一步优选为1:(2-4)。助纺剂的选择及低聚体粉末与助纺剂的质量比均能影响纺丝溶液的性能,从而影响纳米纤维膜的纺制及性能,进一步影响碳纳米纤维膜载体的性能。低聚体粉末与助纺剂的质量比为1:(0.5-10),优选1:(1-7),进一步优选1:(2-4)时,有助于进一步提高纺丝溶液的性能,从而进一步提高纳米纤维膜及碳纳米纤维膜载体的性能,进而得到具有较高活性和加氢选择性的催化剂以用于炔丙基醇部分加氢制备烯丙基醇反应中。优选地,所述步骤(2)中,所述溶剂选自n,n-二甲基甲酰胺、二甲基亚砜、n,n-二甲基乙酰胺和n-甲基吡咯烷酮中的一种或多种,从而一方面对低聚体粉末和助纺剂具有较好的溶解性能,另一方面能够提高纺丝溶液的纺丝性能。优选地,所述步骤(2)中,所述低聚体粉末与所述助纺剂在溶剂中的混合温度为20-120℃,进一步优选为60-100℃。所述低聚体粉末与所述助纺剂在溶剂中的混合温度为20-120℃,优选60-100℃时,能够提高纺丝溶液的纺丝性能,从而提高纳米纤维膜及碳纳米纤维膜载体的性能,进而得到具有较高活性和加氢选择性的催化剂以用于炔丙基醇部分加氢制备烯丙基醇反应中。优选地,所述步骤(3)中,预氧化温度为150-300℃,预氧化时间为1-3h,所述预氧化处理的气体氛围为空气;优选预氧化温度为200-250℃,预氧化时间为1.5-2.5h;进一步优选从室温升温至所述预氧化温度的升温速率为0.5-2℃/min,优选1-1.5℃/min。预氧化温度和预氧化时间的上述设置,能够提高预氧化处理的处理效果;从室温升温至所述预氧化温度的升温速率的上述设置,能够进一步提高预氧化处理的处理效果;从而为后续的炭化处理和活化处理步骤打好基础,以得到性能优良的碳纳米纤维膜载体,从而进一步提高后续步骤对助催化剂组分和活性组分的负载效果,得到具有较高活性和加氢选择性的催化剂以用于炔丙基醇部分加氢制备烯丙基醇反应中。优选地,所述步骤(3)中,所述预氧化处理在流动空气下进行,所述空气的流量为50-500ml/g纳米纤维膜/min,进一步优选100-400ml/g纳米纤维膜/min,再进一步优选150-250ml/g纳米纤维膜/min。预氧化处理的气体氛围及流量的上述设置,能够进一步提高预氧化处理的处理效果;从而为后续的炭化处理和活化处理步骤打好基础,以得到性能优良的碳纳米纤维膜载体,从而进一步提高后续步骤对助催化剂组分和活性组分的负载效果,得到具有较高活性和加氢选择性的催化剂以用于炔丙基醇部分加氢制备烯丙基醇反应中。优选地,所述步骤(3)中,炭化温度为600-800℃,炭化时间为1-3h,所述炭化处理的气体氛围为氮气;进一步优选从所述预氧化温度升温至所述炭化温度的升温速率为2-5℃/min,优选3-4℃/min。炭化温度和炭化时间的上述设置,能够提高炭化处理的处理效果;从预氧化温度升温至炭化温度的升温速率的上述设置,能够进一步提高炭化处理的处理效果;从而为后续的活化处理步骤打好基础,以得到性能优良的碳纳米纤维膜载体,从而进一步提高后续步骤对助催化剂组分和活性组分的负载效果,得到具有较高活性和加氢选择性的催化剂以用于炔丙基醇部分加氢制备烯丙基醇反应中。优选地,所述步骤(3)中,所述炭化处理在流动氮气下进行,所述氮气的流量为50-500ml/g纳米纤维膜/min,进一步优选100-400ml/g纳米纤维膜/min,再进一步优选150-250ml/g纳米纤维膜/min。炭化处理的气体氛围及流量的上述设置,能够进一步提高炭化处理的处理效果;从而为后续的活化处理步骤打好基础,以得到性能优良的碳纳米纤维膜载体,从而进一步提高后续步骤对助催化剂组分和活性组分的负载效果,得到具有较高活性和加氢选择性的催化剂以用于炔丙基醇部分加氢制备烯丙基醇反应中。优选地,所述步骤(3)中,活化温度为1000-1200℃,活化时间为1-3h,所述活化处理的气体氛围为氨气;进一步优选从所述炭化温度升温至所述活化温度的升温速率为0.5-2℃/min,优选1-1.5℃/min。活化温度和活化时间的上述设置,能够提高活化处理的处理效果;从炭化温度升温至活化温度的升温速率的上述设置,能够进一步提高活化处理的处理效果,从而得到性能优良的碳纳米纤维膜载体;从而进一步提高后续步骤对助催化剂组分和活性组分的负载效果,得到具有较高活性和加氢选择性的催化剂以用于炔丙基醇部分加氢制备烯丙基醇反应中。优选地,所述步骤(3)中,所述活化处理在流动氨气下进行,所述氨气的流量为50-500ml/g纳米纤维膜/min,进一步优选100-400ml/g纳米纤维膜/min,再进一步优选150-250ml/g纳米纤维膜/min。活化处理的气体氛围及流量的上述设置,能够进一步提高活化处理的处理效果,从而得到性能优良的碳纳米纤维膜载体;从而进一步提高后续步骤对助催化剂组分和活性组分的负载效果,得到具有较高活性和加氢选择性的催化剂以用于炔丙基醇部分加氢制备烯丙基醇反应中。优选地,所述可溶性金属硫酸盐中的金属元素选自铜、铁、锌和钠中的一种或多种。进一步优选地,所述步骤(4)中,所述可溶性金属硫酸盐选自硫酸铜、硫酸铁、硫酸锌、硫酸亚铁和硫酸钠中的一种或多种。优选地,所述步骤(4)中,所述表面活性剂选自柠檬酸、乙二胺四乙酸、溴化十六烷三甲基铵和十二烷基硫酸钠中的一种或多种。优选地,所述步骤(4)中,所述可溶性金属硫酸盐、硫脲、表面活性剂与碳纳米纤维膜载体的质量比为1:(1-5):(0.1-0.5):(50-100),优选为1:(2-4):(0.2-0.4):(65-85)。比如,所述硫脲的用量可以是可溶性金属硫酸盐质量的2.5倍、3倍或3.5倍;所述表面活性剂的用量可以是可溶性金属硫酸盐质量的0.25倍、0.3倍或0.35倍;所述碳纳米纤维膜载体的用量可以是可溶性金属硫酸盐质量的70倍、75或80倍。为顺利实施例水热反应,所述去离子水的用量为本领域技术人员所熟知,例如所述去离子水的用量可以是所述碳纳米纤维膜载体质量的至少8倍,比如10倍、20倍、30倍、50倍、100倍等等。通过加入足够的去离子水可以使碳纳米纤维膜载体均匀分布于反应容器的底部。上述四种组分的质量比在上述范围内,尤其是优选范围内时,能够提高助催化剂组分在碳纳米纤维膜载体上的负载效果,从而提高活性组分的活性,进而提高所制得催化剂的催化活性和加氢选择性。优选地,所述步骤(4)中,所述水热反应的反应温度为100-300℃,反应时间为5-20h;进一步优选反应温度为150-250℃,比如200℃,反应时间为8-15h,比如11h。水热反应的反应温度和反应时间设置在上述范围内,尤其是优选范围内时,有助于提高催化剂组分在碳纳米纤维膜载体上的负载效果,从而提高活性组分的活性,进而提高所制得催化剂的催化活性和加氢选择性。优选地,所述步骤(5)中,含钯活性组分的盐溶液选自氯化钯溶液、硝酸钯溶液和硫酸钯溶液中的任一种。优选地,所述步骤(5)中,含钯活性组分的盐溶液的浓度为0.5-2.5mol/l,优选1.0-2.0mol/l。含钯活性组分的盐溶液的浓度在上述范围内,尤其是优选范围内时,有助于提高活性组分在负载后的碳纳米纤维膜载体上的负载效果,使其负载均匀,从而提高所制得催化剂的催化活性和加氢选择性。优选地,所述步骤(5)中,负载后的碳纳米纤维膜载体与含钯活性组分的盐溶液中盐的质量比为(20-30):1,优选(23-27):1。负载后的碳纳米纤维膜载体与含钯活性组分的盐溶液中盐的质量比为(20-30):1,优选是(23-27):1时,有助于提高活性组分在负载后的碳纳米纤维膜载体上的负载效果,使其负载量合适,从而使活性组分能够与助催化剂组分相互促进,共同作用,进而提高所制得催化剂的催化活性和加氢选择性。优选地,所述步骤(5)中,浸渍时间为5-20h,进一步优选10-15h。浸渍时间为5-20h,尤其是10-15h时,能够进一步提高活性组分在负载后的碳纳米纤维膜载体上的负载效果,提高所制得催化剂的催化活性和加氢选择性。本发明还提供一种利用前述的制法制备得到的催化剂。优选地,所述催化剂中,活性组分的含量为2.8-3.6wt%,优选3.0-3.4wt%,比如3.2wt%。优选地,所述催化剂中,助催化剂组分的含量为0.4-1.2wt%,比如0.6wt%、0.8wt%、1.0wt%。本发明还提供一种炔丙基醇部分加氢制备烯丙基醇的方法,所述方法是,在前述催化剂的作用下,炔丙基醇在氢气中进行加氢反应得到烯丙基醇。炔丙基醇部分加氢制备烯丙基醇的反应通式如下:其中,r1、r2为氢或者烃基。催化剂对该加氢反应的转化率及加氢选择性影响很大,本发明利用前述制法制备的催化剂,一方面催化剂的活性位点暴露得比较多,另一方面能够毒化抑制剂,因此能够对该反应起到很好的催化作用,使得炔丙基醇能够选择性加氢得到烯丙基醇,且能够提高反应的转化率及加氢选择性。本发明采用固定床反应器进行炔丙基醇部分加氢反应,通过调控反应的温度、压力、原料/溶剂的比例、液时空速等条件来实现对反应转化率和选择性的调控。与釜式反应器相比,固定床反应器避免了原料的长时间停留,减少了反应副产物的产生,从而提升部分加氢反应的选择性。优选地,所述方法中,加氢反应的反应温度为15-120℃,反应压力为0-3.0mpa;进一步优选反应温度为25-60℃,比如35℃、45℃,反应压力为0.1-1.0mpa,比如0.4mpa、0.7mpa。优选地,所述方法中,所述炔丙基醇选自去氢异植物醇、四氢去氢橙花叔醇、去氢橙花叔醇中的一种或多种。优选地,所述方法中,炔丙基醇经溶剂溶解后再进行加氢反应,溶解炔丙基醇所用的溶剂选自正己烷、乙醇、二氯甲烷、乙酸乙酯、甲苯、四氢呋喃中的一种或几种。为了提高炔丙基醇的溶解性能,优选地,加氢反应中,炔丙基醇与溶剂的摩尔比为0.5-5.0,进一步优选1.0-2.0,比如1.5。优选地,所述方法中,所述加氢反应在固定床反应器中进行,所述固定床反应器进料的液时空速为0.1-10h-1,优选0.3-5h-1,比如1.0h-1、3.0h-1。与现有技术相比,本发明具有以下有益效果:1)采用本发明催化剂的制法制备催化剂过程中所得到的碳纳米纤维膜载体,一方面起到了催化剂载体的作用,另一方面由于其中n和/或s的存在,还能起到毒化剂/抑制剂的作用,能够在炔基加氢时,抑制双键加氢生成单键的反应,只促进三键加氢生成双键的反应,从而能够与助催化剂组分和活性组分共同作用来提升加氢反应的选择性;2)采用静电纺丝技术制备出的纳米纤维膜,以及该纳米纤维膜依次经预氧化、炭化和活化处理后得到的碳纳米纤维膜载体均为整体结构,无需其他成型工艺;并且碳纳米纤维膜载体的中空结构使活性位点最大程度暴露,从而使得制得的催化剂能够对炔丙基醇部分加氢制备烯丙基醇的反应起到较好的催化作用,提高反应的转化率和加氢选择性;3)使用本发明的催化剂对炔丙基醇部分加氢制备烯丙基醇的反应进行催化时,加氢反应的转化率达到99.5-100%,加氢选择性达到99.0-99.5%,所得产品的纯度可达到98%以上;而且加氢反应完成后只需将溶剂闪蒸分离即可得到产品,而无需对原料和反应过程中产生的过氢副产物进行分离;4)将本发明的催化剂用于炔丙基醇部分加氢制备烯丙基醇的反应中时,能够避免lindlar催化剂中引入重金属铅,并且无需使用喹啉等液体毒化剂,使得炔丙基醇部分加氢制备烯丙基醇的工艺具有绿色环保、能够简化分离工艺等优势;5)将本发明的催化剂用于炔丙基醇部分加氢制备烯丙基醇的反应中时,使用了固定床反应器,与将粉末状lindlar催化剂应用于釜式反应器中进行炔丙基醇部分加氢制备烯丙基醇的反应相比,本发明方法简化了过滤工艺。附图说明图1为实施例1中碳纳米纤维膜载体的sem图。具体实施方式以下通过具体实施例对本发明的技术方案及其效果做进一步说明。以下实施例仅用于说明本发明的内容,本发明并不仅限于这些实施例。应用本发明的构思对本发明进行的简单改变都在本发明要求保护的范围内。以下实施例中,所有原料均通过商业途径购买得到,所有试剂如未特别说明均为分析纯;且,1、气相色谱分析条件如下:(1)色谱柱:非极性柱,db-5;(2)进样口温度:40℃;(3)分流比:1:20;(4)升温程序:40℃保持0.33min,然后以15℃/min的升温速率升温至200℃,保持1min;再以10℃/min的升温速率升温至280℃,保持3min;气相检测器温度:220℃。2、采用物理吸附分析仪测量催化剂产品的比表面积;物理吸附分析仪的型号:美国micromeritics公司的asap2020型。3、采用扫描电子显微镜(sem)观测碳纳米纤维膜载体的微观形貌;扫描电子显微镜(sem)的型号:jeol公司jbm-6700f型。实施例(简称s)1-5及对比例(简称d)1-3利用本发明的制法制备用于炔丙基醇部分加氢制备烯丙基醇的催化剂,制备过程包括如下步骤:(1)以含氮或硫小分子芳环化合物为原料,以路易斯酸为催化剂,进行缩聚反应得到低聚体,所得低聚体依次进行研磨、碱洗、水洗和干燥处理得低聚体粉末;(2)将所述步骤(1)得到的低聚体粉末和助纺剂加入溶剂中混合均匀得到纺丝溶液,然后采用静电纺丝技术将所述纺丝溶液纺制成纳米纤维膜;在静电纺丝过程中,控制所使用针头的内径、金属滚筒收集器的转速及施加在针头的电压;(3)将所述步骤(2)得到的纳米纤维膜置于炭化炉中依次进行预氧化、炭化和活化处理,得到碳纳米纤维膜载体;在预氧化处理过程中,控制预氧化温度、预氧化时间以及从室温升温至预氧化温度的升温速率;在炭化处理过程中,控制炭化温度、炭化时间以及从预氧化温度升温至炭化温度的升温速率;在活化处理过程中,控制活化温度、活化时间以及从炭化温度升温至活化温度的升温速率;(4)将所述步骤(3)得到的碳纳米纤维膜载体置于装有去离子水的水热釜中,然后加入金属硫酸盐溶液、硫脲和表面活性剂,利用水热反应在所述碳纳米纤维膜载体上进行助催化剂组分的负载,得到催化剂产品初产品;其中,水热釜的体积为100ml;(5)将所述步骤(4)得到的负载后的碳纳米纤维膜载体浸渍于含钯活性组分的盐溶液中进行催化剂活性组分的负载,得到催化剂产品。s1-5及d1-3制得的催化剂产品依次为a、b、c、d、e、f、g、h。制备催化剂产品的工艺条件如表1-7所示。制备得到的各催化剂产品的结构和性质如表8所示。表1s1-5及d1-3中步骤(1)的工艺条件原料路易斯酸催化剂n1:n2反应温度(℃)反应时间(h)s1苯并喹啉fecl31:23004s2喹啉febr31:525020s3噻吩bf21:204001s4异喹啉alcl31:830010s5苯并异喹啉ticl41:101008d1苯并喹啉fecl31:23004d2苯并喹啉fecl31:23004d3苯并喹啉fecl31:23004注:n1:n2是指步骤(1)中路易斯酸催化剂与原料的摩尔比。表2s1-5及d1-3中步骤(2)的工艺条件注:m1:m2是指步骤(2)中低聚体粉末与助纺剂的质量比;针头内径是指静电纺丝过程中所使用针头的内径;转速是指静电纺丝过程中金属滚筒收集器的转速;电压是指指静电纺丝过程中施加在针头的电压。d1和d3中,无步骤(2),其步骤(3)的处理对象为步骤(1)得到的低聚体粉末。表3s1-5及d1-3中步骤(3)中预氧化处理的工艺条件注:表3中升温速率是指步骤(3)中从室温升温至所述预氧化温度的升温速率。表4s1-5及d1-3中步骤(3)中炭化处理的工艺条件注:表4中升温速率是指步骤(3)中从预氧化温度升温至炭化温度的升温速率。表5s1-5及d1-3中步骤(3)中活化处理的工艺条件注:表4中升温速率是指步骤(3)中从炭化温度升温至活化温度的升温速率。表6s1-5及d1-3中步骤(4)的工艺条件注:m3:m4:m5:m6:m7是指步骤(4)中金属硫酸盐、硫脲、表面活性剂、碳纳米纤维膜载体、去离子水的质量比;d2和d3无步骤(4),是指步骤(3)得到的载体不进行助催化剂组分的负载(即步骤(4)),直接进行活性组分的负载(即步骤(5))。表7s1-5及d1-3中步骤(5)的工艺条件注:m8:m9是指步骤(5)中负载后的碳纳米纤维膜载体与含钯活性组分的盐溶液中盐的质量比。表8s1-5及d1-3中所得催化剂产品的结构和性质根据表1-8可知,s1-s5均可制备出具有大比表面积、含n和/或s,并具备助催化剂组分和活性组分的催化剂,从而应用于炔丙基醇部分加氢反应。由s1-s5与d1、d3的对比可以发现,利用静电纺丝技术将催化剂的载体制备成纤维膜可以有效提升催化剂载体的比表面积,从而促进催化活性位点的充分暴露;由s1-s5与d2、d3的对比可以发现,利用水热反应可有效实现助催化剂组分在载体上的负载,从而达到促进提升加氢选择性的作用。由图1可看出,s1成功制备了炭纳米纤维膜载体,而根据表8中s1-s5与d1、d3的比较可知,炭纳米纤维膜载体的制备对活性位点的暴漏起到了促进作用。实施例(简称s)6-10及对比例(简称d)4-6在一定温度和压力,以及氢气氛围下,炔丙基醇溶液在固定床反应器(固定床内径为40mm,催化剂填充高度为150mm)上进行选择性加氢反应,所采用的催化剂分别为实施例1-5及对比例1-3制得的催化剂产品a、b、c、d、e、f、g、h,分别得到反应产品液。将反应产品液闪蒸即可得到烯丙基醇产品。各加氢反应的工艺条件详见表9,反应结果如表10所示。表9s6-10及d4-6中各加氢反应的工艺条件表10s6-10及d4-6中各加氢反应的反应结果产品选择性(%)转化率(%)产品纯度(%)s699.399.999.0s799.499.598.7s899.199.698.5s999.299.798.7s1099.210099.0d498.586.284.7d596.290.586.9d694.183.978.8根据表9-10,由实施例s6-10的数据比较可知,使用本发明所制备的催化剂进行炔丙基醇部分加氢反应,反应转化率和选择性高,显示出优良的催化性能。由s6-10与d4的对比可知,使用催化剂f的d4相对于使用催化剂a-e的s6-10,其加氢反应的加氢选择性、转化率以及产品纯度均有下降,且转化率及产品纯度下降幅度较大,这说明利用静电纺丝工艺间接将载体制备成纤维膜,能够有效提升加氢反应的转化率以及产品纯度。由s6-10与d5的对比可知,使用催化剂g的d5相对于使用催化剂a-e的s6-10,其加氢反应的加氢选择性、转化率以及产品纯度均有下降,且转化率及产品纯度下降幅度较大,这说明助催化剂组分的存在可有效促进加氢反应的加氢选择性、转化率以及产品纯度的提升。由s6-10与d6的对比可知,使用催化剂h的d6相对于使用催化剂a-e的s6-10,其加氢反应的加氢选择性、转化率以及产品纯度均有下降,且转化率及产品纯度下降幅度较大;而由d4-6之间的对比可知,使用催化剂h的d6相对于使用催化剂f和g的d4和d5,其加氢反应的加氢选择性、转化率以及产品纯度的下降幅度均较大;这说明利用静电纺丝工艺间接将载体制备成纤维膜和助催化剂组分的负载能够共同作用以提升加氢反应的转化率和加氢选择性,从而使所得到的烯丙基醇产品的纯度提升。当前第1页12