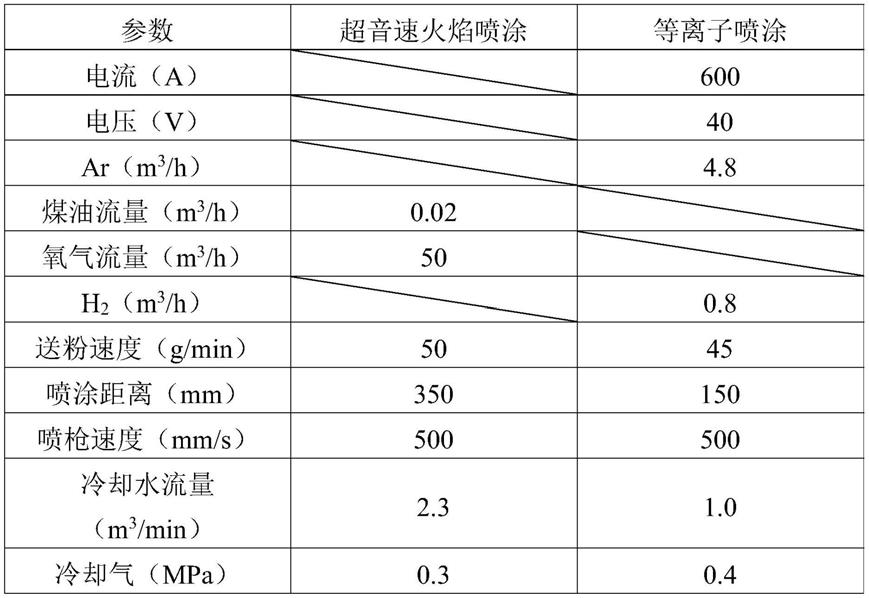
1.本发明涉及电解水领域,特别是涉及一种金属催化剂、制备方法及在电解水中的应用。
背景技术:2.随着氢能行业、绿色经济及“低碳化”要求的发展,氢气正式作为能源或能源载体进入民用、工业化生产中。目前工业制氢仍主要来自化石资源,并未从源头上解决绿色可持续的问题,也无法解决大气污染和雾霾等环境生态问题。由太阳能等可再生能源出发,通过水电解制氢,有望根本上解决目前的能源供给和环境问题。
3.目前水电解制氢是一种较为方便、相对高效的制取氢气的方法。当前碱性电解水制氢工业一般采用过渡金属基催化剂(金属镍、不锈钢等)作为电极材料。为了实现一定的氢气产量和能量利用效率,工业上碱性电解水制氢操作电压通常高达2-2.2v,远大于其热平衡理论最低值1.48v,导致电解效率较低(59~70%),单位制氢能耗较大(5.0~6.6kwh
·
nm-3
)。主要原因是目前商业化电解水电极催化活性较低,析氢、析氧反应过电位过高。因此,需要尽可能地减少电解槽工作电压,增大工作电流,从而提高电解槽能量效率及降低能耗。
4.从目前电解水催化剂的发展来看,多孔金属基底由于较大的比表面积、适中的孔结构以及足够的机械强度,常被用做电极骨架来支撑催化反应活性中心。通过在骨架上引入过渡金属元素构筑新一代电催化剂。例如专利cn201810487534、cn201510303542引入过渡金属氧化物、氢氧化物构建活性中心,专利cn201510607936、cn201510295130、cn201610043831、cn201510334080引入氮化物、硫化物、硒化物、磷化物等来构筑活性中心,这些电解水催化剂表现出接近或与贵金属相当的催化活性。但这些材料中催化活性中心是通过较大的纳米颗粒形式引入和构建的,一方面很多催化活性位点是包裹在颗粒内部,不能有效地得到利用;另一方面增加了原料的成本。
5.近年来的发展显示,通过理性构筑活性中心结构,缩小颗粒尺寸至几个纳米、亚纳米团簇、甚至原子尺度分散时,材料可展示出特异的优于贵金属的催化水分解活性。专利cn201811375698公开了一种钌呈原子级分散的复合材料的制备方法;先以溶液法合成水滑石材料作为载体,然后在含钌的碱性溶液中处理载体,再经分离、真空干燥等处理得到原子级分散在水滑石上的钌催化剂。cn201910517151公开了一种在特定的反应腔室内、一定真空度下,在等离子体气氛中处理前驱物,得到单原子材料的方法。
6.目前催化活性中心小尺度、高度分散的材料的制备和研究取得了一定的进展,但是制备过程条件苛刻,元素种类受限、催化剂粉末需二次成型等问题。在实际工业应用中无法快速、高重复性、工业级放大生产。因此,如何开发一种具有普适性、易于调节负载量、适合工业大量及快速生产的活性中心高分散、甚至原子级分散电极极板的制备方法已成为目前亟待解决的问题。
技术实现要素:7.根据本技术的第一个方面,提供了一种金属催化剂的制备方法,该方法步骤简单,且不局限特定的金属和基底材料,具有一定的普适性;采用该方法便于控制最终活性金属颗粒在导电基底上的尺寸大小,可以制备出原子级分散、金属原子团簇及纳米金属粒子,确保活性金属颗粒的高分散性。
8.所述金属催化剂的制备方法,包括以下步骤:
9.将含有金属前驱体及金属粉末的混合物高温喷涂至导电基底上,得到金属催化剂。
10.可选地,所述金属前驱体为金属无机盐或金属有机配合物;
11.可选地,所述金属无机盐选自氯铂酸钾、硝酸镍、硝酸钴、硝酸铬、硝酸铁、钼酸钠、钨酸钠、氯化亚锡中的至少一种。
12.所述金属前驱体中的金属元素为过渡金属元素和/或后过渡金属元素;
13.所述过渡金属元素选自铂元素、镍元素、钴元素、铬元素、钼元素、钨元素、铁元素中的至少一种;
14.所述后过渡金属元素为锡元素、铅元素、铋元素中的至少一种。
15.可选地,所述金属前驱体为金属有机配合物;
16.所述金属有机配合物中的有机配体选自乙烯基硅氧烷、乙二胺四乙酸钠、乙二胺四乙酸、甘氨酸、邻苯二甲酸、三乙烯二胺、n,n-二甲基甲酰胺、乙酸、葡萄糖中的至少一种,优选乙烯基硅氧烷。
17.可选地,所述金属前驱体为金属有机配合物,所述金属有机配合物的制备方法包括:
18.对含有金属源、所述有机配体的混合液反应,得到所述金属前驱体。
19.在一具体实施例中,所述金属有机配合物的制备方法包括:
20.对含有金属源、所述有机配体、碱源的混合液反应,洗涤、干燥,得到所述金属前驱体。
21.其中,所述碱源选自碳酸氢钠、碳酸钠、碳酸氢钾、碳酸钾中的至少一种;所述混合液中还含有溶剂,所述溶剂可选自水、乙醇、丙酮、异丙醇等常规溶剂;所述金属源为含有过渡金属元素和/或后过渡金属元素的化合物,所述金属源优选氯铂酸钾。
22.可选地,所述反应的反应温度为70~80℃,反应时间为30~300min;可选地,所述有机配体与金属源的摩尔比为1~200:1;
23.可选地,所述金属粉末为金属单质粉末和/或金属合金粉末;
24.所述金属粉末中的金属元素为过渡金属元素和/或主族金属元素;
25.所述过渡金属元素选自镍元素、铁元素、钴元素、锰元素、钛元素、铜元素、锌元素、钨元素、钼元素中的至少一种;
26.所述主族金属元素选自铝元素、铟元素中的至少一种;
27.所述金属粉末为20~600目。
28.可选地,所述金属前驱体中的金属元素与所述金属粉末的金属元素不同。
29.可选地,所述金属前驱体的质量为所述金属粉末质量的10-4
~5%,其中,所述金属前驱体的质量以具有催化活性的金属的质量计。优选地,所述金属前驱体的质量为所述金
属粉末质量的0.0001~0.4%,更优选0.0001~0.02%,以确保达到原子级分散。
30.可选地,所述金属前驱体的质量为所述金属粉末质量百分比的下限可选自0.0001%、0.0015%、0.0020%、0.0025%、0.0030%、0.0035%、0.0040%、0.0047%、0.0050%、0.0055%、0.0060%、0.0065%、0.0070%、0.0075%、0.0077%、0.031%、0.11%、0.15%、0.16%、0.17%、0.18%、0.19%、0.20%、0.21%、0.22%、0.23%、0.24%、0.25%、0.26%、0.27%、0.28%、0.29%、0.30%、0.31%、0.32%、0.33%、0.34%、0.35%、0.36%或0.37%,上限可选自0.0015%、0.0020%、0.0025%、0.0030%、0.0035%、0.0040%、0.0047%、0.0050%、0.0055%、0.0060%、0.0065%、0.0070%、0.0075%、0.0077%、0.031%、0.11%、0.15%、0.16%、0.17%、0.18%、0.19%、0.20%、0.21%、0.22%、0.23%、0.24%、0.25%、0.26%、0.27%、0.28%、0.29%、0.30%、0.31%、0.32%、0.33%、0.34%、0.35%、0.36%、0.37%或0.4%。
31.可选地,所述混合物中还包括粘结剂;所述粘结剂选自全氟磺酸树脂、羧甲基纤维素、糊精、乙烯-丙烯酸共聚物、聚乙烯醇、聚氨酯、聚苯乙烯、聚氧乙烯-聚氧丙烯-聚氧乙烯、聚氧丙烯-聚氧乙烯-聚氧丙烯、聚苯乙烯-聚氧乙烯中的至少一种;
32.优选地,所述粘结剂选自全氟磺酸树脂、羧甲基纤维素、聚乙烯醇、聚氨酯中的至少一种。
33.可选地,所述粘结剂为所述金属粉末的质量的0.05%~10%。
34.可选地,所述导电基底为镍基底、不锈钢基底、铜基底或钛基底;
35.所述导电基底的形状为板状、片状、网状或泡沫状。
36.可选地,所述高温喷涂为燃烧火焰喷涂、电弧喷涂、超音速喷涂或等离子体喷涂。
37.可选地,所述高温喷涂的送粉速度为45~80g/min,喷涂距离为150~380mm,喷枪水平移动速度为10~600mm/s。
38.可选地,含有所述金属前驱体、粘结剂及金属粉末的混合物通过以下方式获得:将金属前驱体加入溶剂中,得到混合液,将粘结剂、金属粉末加入所述混合液中,去除所述溶剂,得到所述混合物;
39.可选地,以金属摩尔计,所述金属前驱体在所述混合液中的摩尔浓度为0.2~10mmol
·
l-1
;优选地,以金属摩尔计,所述金属前驱体在所述混合液中的摩尔浓度为0.2~5mmol
·
l-1
;
40.在一具体实施例中,含有所述金属前驱体、粘结剂及金属粉末的混合物通过以下方式获得:
41.取一定量的金属前驱体溶于定量溶剂中,然后加入定量粘结剂和定量金属粉末搅拌一定时间后干燥去除溶剂得到混合物。其中,混合方式可选自机械搅拌和/或球磨混合;
42.可选地,所述去除溶剂,具体包括:
43.通过旋风干燥或冷冻干燥去除所述溶剂;
44.所述旋风干燥的具体条件包括:
45.进口热空气温度130~150℃,干燥压力为常压,热气体滞留时间2~8s,物料平均滞留时间为15~60min;
46.所述冷冻干燥的具体条件包括:干燥压力为真空干燥(<30pa),冷阱温度为-40~-70℃,干燥时间为48~120h。
47.可选地,将金属前驱体、粘结剂及金属粉末的混合物高温喷涂至导电基底上之后,还包括:
48.采用碱或酸溶液进行洗涤,所述碱或酸溶液的摩尔浓度为0.1~10m。所述碱溶液可以为氢氧化钠溶液、氢氧化钾溶液等;所述酸溶液可以为盐酸溶液、硝酸溶液、硫酸溶液等。
49.在一具体实施例中,所述的制备方法,包括以下步骤:
50.(1)制备金属前驱体i;
51.(2)将制备的金属前驱体i与金属粉末、粘结剂混合,干燥,得到前驱体ii;
52.(3)将所述前驱体ii高温喷涂至导电基底上,得到iii,洗涤、干燥,得到金属催化剂。该实施例中,金属前驱体i即为所述金属前驱体,前驱体ii即为所述含有金属前驱体及金属粉末的混合物,ⅲ即为喷涂有前驱体ⅱ的导电基底。
53.优选地,(1)所述金属前驱体中的金属元素为过渡金属元素和/或后过渡金属元素;所述过渡金属元素选自铂元素、镍元素、钴元素、铬元素、钼元素、铁元素、钨元素中的至少一种;所述后过渡金属元素为锡元素、铅元素、铋元素中的至少一种
54.优选地,(1)中所述金属前驱体i包括金属有机配合物、金属硝酸盐、氯化物、硫酸盐、钼酸盐、含有特定金属元素的化合物等。所述金属有机配合物的制备方法如下:将有机配体与金属盐在溶液中混合均匀,去除溶剂,洗涤,干燥。所用有机配体可以是乙烯基硅氧烷,乙二胺四乙酸钠,甘氨酸,邻苯二甲酸、三乙烯二胺,n,n-二甲基甲酰胺,乙酸、葡萄糖。
55.优选地,(2)中所述金属粉末为镍、铁、钴、锰、钛、铝、铜、锌、铟、钨、钼粉末中的一种或几种的合金粉末或混合粉末,尺度范围为20~600目。
56.优选地,(2)中所述金属粉末为镍铝合金粉末。
57.优选地,(2)中所述粘结剂选自全氟磺酸树脂、羧甲基纤维素、糊精、乙烯-丙烯酸共聚物、聚乙烯醇、聚氨酯、聚苯乙烯、聚氧乙烯-聚氧丙烯-聚氧乙烯、聚氧丙烯-聚氧乙烯-聚氧丙烯、聚苯乙烯-聚氧乙烯中的一种中的至少一种或几种。
58.优选地,(2)中所述粘结剂为全氟磺酸树脂、羧甲基纤维素、聚乙烯醇、聚氨酯。
59.优选地,(2)中所述混合,混合方式可以是机械搅拌、球磨混合,干燥可以是旋风干燥、冷冻干燥等。
60.优选地,(2)中所述的干燥为真空冷冻干燥,干燥时间为2~5天。
61.优选地,(3)中所述高温喷涂选自燃烧火焰喷涂、电弧喷涂、超音速喷涂和等离子体喷涂中的一种。
62.优选地,(3)种所述导电基底的形式是镍、钛、铜、不锈钢等的板、片、网、泡沫等。
63.优选地,(3)所述导电基底指的是镍网、镍片和泡沫镍。
64.优选地,(3)所述洗涤处理指的是将iii浸泡在碱性溶液中一定时间。其中碱性溶液指氢氧化钠,氢氧化钾的水溶液,浓度为2~40wt.%。
65.根据本技术的第二个方面,提供了上述任一项所述的制备方法制备的金属催化剂。
66.根据本技术的第三个方面,提供了上述任一项所述制备方法制备的金属催化剂在碱性电解水析氢和产氧反应中的应用。
67.本技术中,所述高温喷涂是指喷涂温度在500摄氏度以上。
68.本技术能产生的有益效果包括:
69.(1)本发明通过将金属前驱体与金属粉末结合得到待喷涂材料,经高温喷涂后,金属粉末形成的基底层,金属前驱体经高温分解形成的金属或金属氧化物颗粒分散嵌在基底层中,实现了有效地分散;
70.(2)本发明采用方法不局限特定的金属和基底材料,具有一定的普适性;
71.(3)本发明采用方法,通过控制金属前驱体、粉末的量,以及喷涂工艺条件,可以方便的控制最终活性金属颗粒在导电基底上的尺寸大小,可以得到原子级分散、金属原子团簇、纳米金属粒子活性金属颗粒;
72.(4)本发明提供的制备高分散金属催化剂的方法便于大规模生产;
73.(5)本技术提供的金属催化剂应用于碱性电解水析氢和产氧反应中时具有较高的能量转化效率。
附图说明
74.图1为实施例1的催化剂颗粒尺寸统计分布图。
75.图2为实施例2的催化剂颗粒尺寸统计分布图。
76.图3为实施例3的催化剂颗粒尺寸统计分布图。
77.图4为实施例4的催化剂颗粒尺寸统计分布图。
78.图5为实施例5的催化剂颗粒高分辨球差电镜图。
79.图6为实施例7和对比例的析氢反应极化曲线图。
80.图7为实施例7的产氢稳定性曲线图。
81.图8为实施例15和对比例的析氧反应极化曲线图。
82.图9为实施例15的产氧稳定性曲线图。
具体实施方式
83.下面结合实施例详述本技术,但本技术并不局限于这些实施例。
84.未做特别说明的情况下,本技术中所述原料均为市售产品。
85.其中,双封头(乙烯基硅氧烷)购买自上海迈瑞尔化学技术有限公司的gel-siv9097.5-25g型号;
86.全氟磺酸树脂购买自杜邦公司的d520型号
87.聚乙烯醇购买自上海迈瑞尔化学技术有限公司的m29057-1kg型号;
88.所用金属盐、甘氨酸、乙二胺四乙酸钠、邻苯二甲酸和有机溶剂均购买自国药化学试剂有限公司,均为分析纯。镍网为购买自安平县康威金属丝网制品有限公司,规格为60目。
89.所用超音速喷涂系统为美国普莱克斯表面技术公司的jp8000型超音速火焰喷涂(hp/hvof)系统,各实施例具体工艺参数参见表a。
90.所用等离子体喷涂系统为美国普莱克斯表面技术公司的7700型等离子喷涂系统,各实施例具体工艺参数参见表a。
91.采用jem-2100f透射电子显微镜对催化剂中活性金属粒子的粒径进行测量。
92.表a各实施例喷涂工艺参数表
[0093][0094]
以下通过实施例对高分散金属催化剂的制备及其应用进一步的详细说明:
[0095]
实施例1
[0096]
将40ml氯铂酸钾异丙醇溶液(120mmol
·
l-1
)与双封头(乙烯基硅氧烷)(1g)混合,然后加入nahco3(1g)得到悬乳液,将得到的悬乳液在70~80℃搅拌30min,除去异丙醇,得到前体i。将得到的前体i、镍铝合金粉(250g,180~250目,ni:al=4:1,摩尔比)、3ml5 wt.%全氟磺酸树脂的乙醇溶液及50ml乙醇机械搅拌3小时,然后在-60℃冷冻干燥72小时,得到前体ii。前体ii通过超音速喷涂系统负载在镍网上得到iii。把iii在10wt.%氢氧化钾溶液中浸泡12小时洗去可溶于碱的物质,然后用水清洗,干燥,得到催化剂。
[0097]
实施例2
[0098]
与实施例1制备方法相同,唯一不同的是氯铂酸钾浓度为50mmol
·
l-1
,得到催化剂。
[0099]
实施例3
[0100]
与实施例1制备方法相同,唯一不同的是氯铂酸钾浓度为36mmol
·
l-1
,得到催化剂。
[0101]
实施例4
[0102]
与实施例1制备方法相同,唯一不同的是氯铂酸钾浓度为10.0mmol
·
l-1
,得到催化剂。
[0103]
实施例5
[0104]
与实施例1制备方法相同,唯一不同的是氯铂酸钾浓度为0.5mmol
·
l-1
,得到催化剂。
[0105]
表1、实施例1-5提供的催化剂中铂纳米离子的平均直径
[0106][0107]
如图1~5所示,随着氯铂酸钾的浓度逐渐降低,所制备的铂纳米粒子的粒径逐渐减小,尤其是在0.5mmol
·
l-1
浓度的时候,所制备的铂纳米粒子为0.35nm,通常粒子粒径达到1~2个原子半径范围即可认为是原子级分散,因此,该浓度下制备的催化剂相当于原子级分散的催化剂。
[0108]
实施例6
[0109]
取粒径尺寸约为180~250目的镍铝合金粉250g(ni:al摩尔比=4:1),加入至40ml的120mmol
·
l-1
氯铂酸钾水溶液中,再加入1g聚乙烯醇,机械搅拌4小时,在-60℃下冷冻干燥96小时,得到混合物。通过超音速喷涂方式将得到的混合物引至镍网载体上。将所得材料放入10wt.%的koh中洗涤处理20小时,然后用水清洗,干燥,得到最后的催化剂。
[0110]
实施例7
[0111]
取粒径尺寸约为180~250目的镍铝合金粉250g(ni:al摩尔比=4:1),加入至40ml的0.5mmol
·
l-1
氯铂酸钾水溶液中,再加入1g聚乙烯醇,机械搅拌4小时,在-60℃下冷冻干燥5天,得到混合物。通过超音速喷涂方式将得到的混合物引至镍网载体上。将所得材料放入10wt.%的koh中洗涤处理20小时,然后用水清洗,干燥,得到最后的催化剂。
[0112]
实施例8
[0113]
与实施例6制备方法相同,唯一不同的是金属盐为硝酸钴,其水溶液浓度为120mmol
·
l-1
,得到催化剂。
[0114]
实施例9
[0115]
与实施例7制备方法相同,唯一不同的是金属盐为硝酸钴,其水溶液浓度为0.5mmol
·
l-1
,得到催化剂。
[0116]
实施例10
[0117]
与实施例6制备方法相同,唯一不同的是金属盐为钼酸钠,其水溶液浓度为120mmol
·
l-1
,得到催化剂。
[0118]
实施例11
[0119]
与实施例7制备方法相同,唯一不同的是金属盐为钼酸钠,其水溶液浓度为0.5mmol
·
l-1
,得到催化剂。
[0120]
实施例12
[0121]
与实施例6制备方法相同,唯一不同的是金属盐为硝酸铬,其水溶液浓度为
120mmol
·
l-1
,得到催化剂。
[0122]
实施例13
[0123]
与实施例7制备方法相同,唯一不同的是金属盐为硝酸铬,其水溶液浓度为0.5mmol
·
l-1
,得到催化剂。
[0124]
实施例14
[0125]
与实施例6制备方法相同,唯一不同的是金属盐为硝酸铁,其水溶液浓度为120mmol
·
l-1
,得到催化剂。
[0126]
实施例15
[0127]
与实施例7制备方法相同,唯一不同的是金属盐为硝酸铁,其水溶液浓度为0.5mmol
·
l-1
,得到催化剂。
[0128]
实施例16
[0129]
与实施例6制备方法相同,唯一不同的是金属盐为钨酸钠,其水溶液浓度为120mmol
·
l-1
,得到催化剂。
[0130]
实施例17
[0131]
与实施例7制备方法相同,唯一不同的是金属盐为钨酸钠,其水溶液浓度为0.5mmol
·
l-1
,得到催化剂。
[0132]
实施例18
[0133]
与实施例6制备方法相同,唯一不同的是金属盐为氯化亚锡,其水溶液浓度为120mmol
·
l-1
,得到催化剂。
[0134]
实施例19
[0135]
与实施例7制备方法相同,唯一不同的是金属盐为氯化亚锡,其水溶液浓度为0.5mmol
·
l-1
,得到催化剂。
[0136]
表2、实施例6~19提供的催化剂中的金属纳米粒子的平均粒径
[0137]
[0138][0139]
表2所示,采用不同的金属前驱体,都可以有效的制备金属纳米粒子,尤其是采用低浓度的金属前驱体时,所制备纳米粒子为相应金属的原子级分散的尺度。
[0140]
实施例20
[0141]
与实施例5制备方法相同,唯一不同的是金属粉组成为400~450目钴粉50g、180~250目镍粉100g、180~250目铝粉50g。
[0142]
实施例21
[0143]
与实施例5制备方法相同,唯一不同的是金属粉组成为:200~280目钛铝合金粉80g(钛:铝摩尔比=1:3),180~250目镍粉150g。
[0144]
实施例22
[0145]
与实施例5制备方法相同,唯一不同的是金属组成为:180~250目铁铝合金粉250g(铁:铝摩尔比=3:1)。
[0146]
表3实施例20~22提供的催化剂中的铂纳米粒子平均粒径
[0147][0148]
由表3可知,在不同的金属纳米粉末组成下,均可以制备出原子级分散的铂金属粒子,直径在0.34~0.37nm范围。
[0149]
实施例23
[0150]
与实施例5制备方法相同,唯一不同的是有机配体,这里使用的有机配体是乙二胺四乙酸钠,质量为12mg。
[0151]
实施例24
[0152]
与实施例5制备方法相同,唯一不同的是有机配体,这里使用的有机配体是甘氨酸,质量为15mg。
[0153]
实施例25
[0154]
与实施例5制备方法相同,唯一不同的是有机配体,这里使用的有机配体是邻苯二
甲酸,质量为20mg。
[0155]
表4使用不同有机配体制备铂纳米金属粒子的粒径
[0156][0157]
实施例26
[0158]
与实施例7制备方法相同,唯一不同的是喷涂方法改为高温等离子喷涂得到催化剂。
[0159]
实施例27
[0160]
与实施例9制备方法相同,唯一不同的是喷涂方法改为高温等离子喷涂得到催化剂。
[0161]
实施例28
[0162]
与实施例11制备方法相同,唯一不同的是喷涂方法改为高温等离子喷涂得到催化剂。
[0163]
实施例29
[0164]
与实施例13制备方法相同,唯一不同的是喷涂方法改为高温等离子喷涂得到催化剂。
[0165]
表5、不同金属在超音速喷涂和高温等离子喷涂条件下金属纳米粒子粒径
[0166]
[0167]
由表5可知,利用超音速喷涂和高温等离子喷涂针对不同金属均可以制备原子级分散的纳米粒子。
[0168]
对比例30
[0169]
对比例采用碱性电解水市售镍商业催化剂,从考克利尔竞立苏州氢能设备有限公司购入。
[0170]
实施例31
[0171]
催化活性评估:通过chi 760d电化学工作站在标准的三电极配置中测量催化剂产氢或产氧催化活性。测量时直接把制备的催化剂作为工作电极,汞/氧化汞为参比电极,镍网为对电极,浓度30wt.%的氢氧化钾水溶液为电解质,以线性扫描伏安法或循环伏安法,扫描速度5mv/s来测试析氢反应(her)和/或析氧反应(oer)活性,欧姆补偿为90%。
[0172]
其中,产氢催化活性以实施例7提供的催化剂作为典型代表,如图6所示,实施例7制备的催化剂均具有很高的电解水产氢催化活性,相同条件下其产氢催化活性远比对比例30的商业催化剂高。
[0173]
实施例32
[0174]
产氧催化活性以实施例15提供的催化剂作为典型代表,如图8所示,实施例15制备的催化剂均具有很高的电解水产氧催化活性,相同条件下其产氧催化活性远比对比例30的商业催化剂高。
[0175]
实施例33
[0176]
催化稳定性评估:通过chi760d工作站在标准的两电极配置中测量各实施例及对比例提供的催化剂的电解水产氢或产氧催化稳定性。测试时把制备的对比例30商业催化剂作为对电极,各实施例提供的催化剂分别做为析氢阴极,浓度30wt.%的氢氧化钾水溶液为电解质,工作温度为80度,在400ma cm-2
电流下恒电流测试,欧姆补偿比例为90%。
[0177]
以实施例7提供的催化剂作为典型代表,如图7所示,实施例7所制备镍铂催化剂具有很高的电解水产氢稳定性。其他各实施例也均具有较高的电解水产氢稳定性。
[0178]
实施例34
[0179]
同实施例33相同,将各实施例提供的催化剂分别作为析氧阳极,把制备的对比例30商业催化剂作为对电极,在500ma cm-2
电流下恒电流测试,欧姆补偿比例为90%。
[0180]
以实施例15提供的催化剂作为典型代表,如图9所示,实施例15所制备镍铁催化剂具有很高的电解水产氧稳定性。其他各实施例也均具有较高的电解水产氧稳定性。
[0181]
实施例35
[0182]
本发明实施例中电解效率=1.48/电解电压;
[0183]
单位制氢能耗指的是每电解产生一立方米氢气时整个系统所消耗的总电能。
[0184]
根据gb32311-2015方法确定本发明各实施例及对比例提供的催化剂的电解效率及单位制氢能耗,具体参数参见表6。
[0185]
表6各实施例及对比例所得催化剂催化性能
[0186][0187][0188]
由表6可知,本技术提供的催化剂具有更好的电解效率和低的单位制氢能耗。
[0189]
以上所述,仅是本技术的几个实施例,并非对本技术做任何形式的限制,虽然本技术以较佳实施例揭示如上,然而并非用以限制本技术,任何熟悉本专业的技术人员,在不脱离本技术技术方案的范围内,利用上述揭示的技术内容做出些许的变动或修饰均等同于等效实施案例,均属于技术方案范围内。