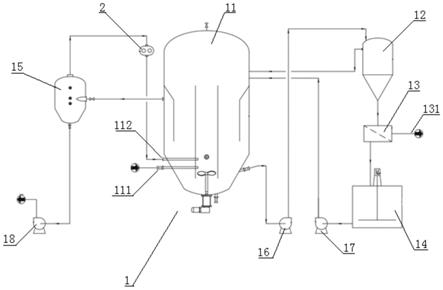
[0001]
本发明涉及结晶工艺技术领域,具体而言,特别涉及一种热泵型升温结晶工艺。
背景技术:[0002]
对于逆溶解度(即溶解度随温度升高而降低)物料结晶,目前多为多效或者mvr蒸发结晶工艺。但该类蒸发结晶工艺在其使用过程中还存在以下不足:
[0003]
1、蒸发结晶,物料与加热介质间壁换热会导致换热管内结垢堵塞;
[0004]
2、换热面积大,配套设备多且昂贵,设备投资高;
[0005]
3、强制循环泵流量大,对晶体损伤破坏严重,产品粒度小;
[0006]
4、系统热负荷高,动力消耗大,运行成本高。
技术实现要素:[0007]
本发明旨在至少在一定程度上解决现有技术中的上述技术问题之一。有鉴于此,本发明提供一种适用于热泵型蒸汽直接接触加热形式的升温结晶工艺,加热过程无换热面、无结垢、无需外置循环泵,易于培养晶体,热量回收重复利用,具有工艺简单、流程短、投资低且能耗低的优点。
[0008]
本发明提供一种热泵型升温结晶工艺,包括以下步骤:
[0009]
s1、设置升温结晶装置中的流量计、液位计、压力表、温度计、调节阀等自控仪表和plc或dcs系统,完成装置的自动化控制;
[0010]
s2、将待结晶原液通入升温结晶装置中,再接入初始蒸汽,所述原液与所述初始蒸汽接触后析出晶体,含有所述晶体的晶浆经过固液分离,得到的固体为结晶产品,得到的母液重新送回所述升温结晶装置;
[0011]
s3、结晶完成液从所述升温结晶装置中取出,并经过降压后沸腾蒸发出二次蒸汽,降温后送至界外,供前端生产套用;
[0012]
s4、步骤s3中的二次蒸汽经由蒸汽压缩机回收,并再次压缩后供给所述升温结晶装置使用。
[0013]
根据本发明的一个实施例,所述升温结晶装置包括通过管道顺序连通的升温结晶器、增稠器、离心机和母液罐,所述升温结晶器上设有高浓度原液入料口和蒸汽入口,所述升温结晶器与所述母液罐之间通过管道连通,所述升温结晶器上设有通过管道连通且供所述清液汽化降温使用的低压闪蒸器,所述低压闪蒸器上设有二次蒸汽出口和清液出口,所述离心机上设有固体出口。
[0014]
根据本发明的一个实施例,所述升温结晶器与所述增稠器之间连通的管道上设有结晶出料泵,所述母液罐与所述升温结晶器之间连通的管道上设有母液泵。
[0015]
根据本发明的一个实施例,所述低压闪蒸器上的所述二次蒸汽出口通过管道与蒸汽压缩机连接,其中所述蒸汽压缩机的蒸汽出口端与所述升温结晶器的所述蒸汽入口连通。
[0016]
根据本发明的一个实施例,所述低压闪蒸器的所述清液出口连接有出液管道,该出液管道上设有低浓液出料泵。
[0017]
根据本发明的一个实施例,所述原液为逆溶解度的结晶物料。
[0018]
本发明的热泵型升温结晶工艺,待结晶原液与高温初始蒸汽在升温结晶器中直接接触并加热升温,原液溶解度下降而析出晶体,含有晶体的晶浆通过结晶出料泵进入增稠器中增稠后送入离心机内进行固液分离,固体即为结晶产品,离心后晶浆中的母液经母液罐缓存后通过母液泵返回升温结晶器中,同时升温结晶器中的清液进入低压闪蒸器中,经过低压汽化降温后送至界外,而低压闪蒸器中的二次蒸汽由蒸汽压缩机回收再压缩后送至升温结晶器中使用,上述工艺过程适用于逆溶解度结晶物料,如硫酸锰、硫酸锌、硫酸镁等,且采用热泵将系统内部热量以回收蒸汽的形式进行循环利用,极大的降低新鲜蒸汽的消耗,甚至还可对外供给少量蒸汽,尤其适用于蒸汽直接接触加热形式的升温结晶过程,加热过程中无换热面、无结垢弊端、无需外置循环泵,易于培养晶体,具有工艺简单、流程短、投资低、能耗低的优点。
附图说明
[0019]
图1是根据本发明的一种热泵型升温结晶工艺中装置的结构示意图。
[0020]
图2是根据本发明的一种热泵型升温结晶工艺的步骤流程图。
[0021]
附图标记:1-升温结晶装置;2-蒸汽压缩机;11-升温结晶器;12-增稠器;13-离心机;14-母液罐;15-低压闪蒸器;16-结晶出料泵;17-母液泵;18-低浓液出料泵;111-高浓度原液入料口;112-蒸汽入口;131-固体出口;151-二次蒸汽出口;152-清液出口。
具体实施方式
[0022]
下面详细描述本发明的实施例,所述实施例的示例在附图中示出,其中自始至终相同或类似的标号表示相同或类似的元件或具有相同或类似功能的元件。下面通过参考附图描述的实施例是示例性的,旨在用于解释本发明,而不能理解为对本发明的限制。
[0023]
如图1和图2所示,一种热泵型升温结晶工艺,包括以下步骤:
[0024]
s100、设置升温结晶装置1中的流量计、液位计、压力表、温度计、调节阀等自控仪表和plc或dcs系统,完成装置的自动化控制;
[0025]
s200、将待结晶原液通入升温结晶装置1中,再接入初始蒸汽,原液与初始蒸汽接触后析出晶体,含有晶体的晶浆经过固液分离,得到的固体为结晶产品,得到的母液重新送回所述升温结晶装置;
[0026]
s300、结晶完成液从升温结晶装置1中取出,并经过降压后沸腾蒸发出二次蒸汽,降温后送至界外,供前端生产套用;
[0027]
s400、步骤s300中的二次蒸汽经由蒸汽压缩机2回收,并再次压缩后供给升温结晶装置1使用。
[0028]
本发明的热泵型升温结晶工艺,待结晶原液与高温初始蒸汽在升温结晶器11中直接接触并加热升温,原液溶解度下降而析出晶体,含有晶体的晶浆通过结晶出料泵进入增稠器12中增稠后送入离心机13内进行固液分离,固体即为结晶产品,离心后晶浆中的母液经母液罐14缓存后通过母液泵17返回升温结晶器11中,同时升温结晶器11中的清液进入低
压闪蒸器15中,经过低压汽化降温后送至界外,而低压闪蒸器15中的二次蒸汽由蒸汽压缩机2回收再压缩后送至升温结晶器1中使用,上述工艺过程适用于逆溶解度结晶物料,如硫酸锰、硫酸锌、硫酸镁等,且采用热泵将系统内部热量以回收蒸汽的形式进行循环利用,极大的降低新鲜蒸汽的消耗,甚至还可对外供给少量蒸汽,尤其适用于蒸汽直接接触加热形式的升温结晶过程,加热过程中无换热面、无结垢弊端、无需外置循环泵,易于培养晶体,具有工艺简单、流程短、投资低、能耗低的优点。
[0029]
如图2所示,升温结晶装置1包括通过管道顺序连通的升温结晶器11、增稠器12、离心机13和母液罐14,升温结晶器11上设有高浓度原液入料口111和蒸汽入口112,升温结晶器1与母液罐14之间通过管道连通,升温结晶器1上设有通过管道连通且供清液汽化降温使用的低压闪蒸器15,低压闪蒸器15上设有二次蒸汽出口151和清液出口152,其中增稠器12与低压闪蒸器15之间连通有供清液输送的管道,离心机13上设有固体出口131,其中,升温结晶器11与增稠器12之间连通的管道上设有结晶出料泵16,母液罐14与升温结晶器11之间连通的管道上设有母液泵17;低压闪蒸器15上的二次蒸汽出口151通过管道与蒸汽压缩机2连接,其中蒸汽压缩机2的蒸汽出口端与升温结晶器1的蒸汽入口112连通;低压闪蒸器15的清液出口连接有出液管道,该出液管道上设有低浓液出料泵18。
[0030]
如图1和图2所示,原液为逆溶解度的结晶物料,例如硫酸锰、硫酸锌、硫酸镁等其中的一种。
[0031]
如图1和图2所示,以下为本发明的热泵型升温结晶工艺使用的实施例:
[0032]
首先设置流量计、液位计、压力表、温度计、调节阀等自控仪表和plc或dcs系统,实现工艺过程稳定和自动化控制;
[0033]
将80℃,浓度为22%的硫酸锰溶液通过本工艺得到一水硫酸锰,其中升温结晶器11内温度设定为140℃,低压闪蒸器15内温度设定为90℃,硫酸锰溶液进入升温结晶器11与初始蒸汽直接接触升温结晶,析出一水硫酸锰晶体,升温结晶器11内的清液进入低压闪蒸器15,含有晶体的晶浆进入增稠器14,增稠器14内的清液返回低压闪蒸器15,较浓的晶浆进入离心机13固液分离得到固体一水硫酸锰;离心后的晶浆母液进入母液罐14后返回升温结晶器11中,同时高温清液在低压闪蒸器15内发生低压汽化降温,闪蒸出的二次蒸汽经蒸汽压缩机2压缩后再进入升温结晶器11加热原液,闪蒸后的低温溶液可返回此工艺前段浓缩或者套用,综上使用本发明的升温结晶工艺生产1吨固体蒸汽耗用量为238kg,电耗为80kw,若采用目前mvr蒸发结晶工艺生产1吨产品蒸汽耗用量为155kg,电耗为144kw,可见,本工艺运行成本较低,且没有换热器、轴流泵等主要设备,设备投资远小于mvr蒸发结晶。
[0034]
尽管上面已经示出和描述了本发明的实施例,可以理解的是,上述实施例是示例性的,不能理解为对本发明的限制,本领域的普通技术人员在本发明的范围内可以对上述实施例进行变化、修改、替换和变型。