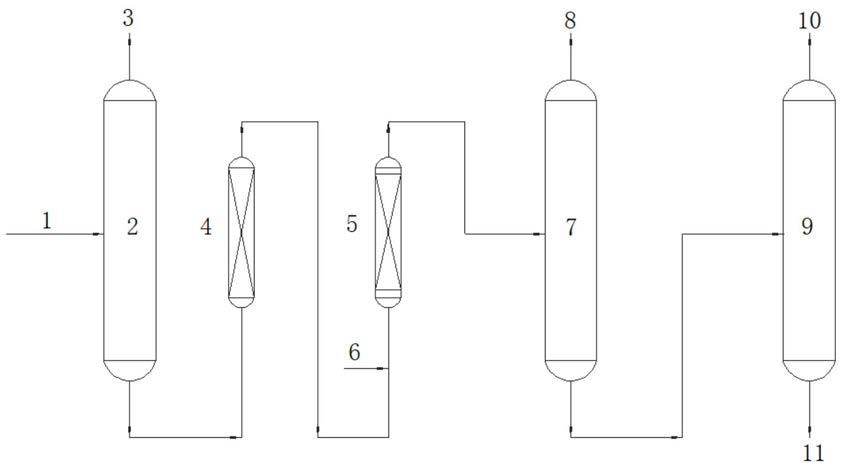
1.本发明属于催化剂材料技术领域,具体涉及一种用于选择加氢脱除二烯烃和炔烃的非钯贵金属加氢催化剂,并进一步公开其制备方法与应用。
背景技术:2.碳四轻烃是主要来源于乙烯装置热裂解、炼油催化裂化及煤制烯烃工艺的组分,主要含有丁烷、正丁烯(直链丁烯)和异丁烯等,是一种重要的有机化工原料。由于不同来源的轻烃原料中含有不同含量的丁二烯和炔烃,在进行下游综合利用时必须要将其脱除,目前,通常采用的脱除工艺一般是选择加氢的方法。
3.传统的轻烃加氢工艺通常采用的是vⅲ族的金属催化剂,经研究及实践发现,贵金属对加氢反应有很高的本征活性,其中的贵金属pt、pd、ru、rh催化剂由于其活性高,处理量大,催化剂稳定性好,使用寿命长,操作条件缓和等优点,相比其它催化剂更适用于选择性加氢反应。但却也存在催化剂的价格昂贵,一次投资高的劣势。因此,选择不同种类的金属作为活性组分,根据不同时期金属价格的差异,选择不同种类进行制备加氢催化剂,具有更为现实的意义。
4.如中国专利cn106475092a公开了一种用氧化铝基铂催化剂的制备方法,通过先制备出含水率40-50%的湿料,然后加入粘合剂造粒成型、马弗炉中烧结、制备出氧化铝载铂颗粒,最后还原反应制备出氧化铝基铂催化剂。该催化剂可用于氨氧化、石油烃重整、不饱和化合物氧化及加氢、气体中一氧化碳、氮氧化物的脱除等过程,但对于轻烃中双烯烃加氢效果则并不理想。
5.又如中国专利cn 104220163a公开了一种在沸石载体材料上制备了含有钯和铂的双金属催化剂的方法,但该催化剂通常用于氧化催化工艺中同样对于轻烃中双烯烃加氢效果则并不理想。
6.又如中国专利cn110563536a公开了一种用cupdpt催化剂催化1,3-丁二烯选择性加氢的方法,其通过调节催化剂中金属铜、钯、铂的含量及tio2@c含量就可以制得用于1,3-丁二烯选择性加氢的高活性、高稳定性负载型cupdpt催化剂。使用该催化剂进行1,3-丁二烯选择性加氢反应,其中产物中1,3-丁二烯含量低于670ppb,丁烷含量低于1.5%,催化剂连续运行150h后仍保持良好的催化活性。但其制备过程过于复杂,且所用原料具有高度高危险性,环保性较差。
7.又如中国专利cn111230141a公开了一种絮球形貌ptrucos合金纳米晶的制备方法,以氯铂酸,氯化钴和亚硫酸钠以及氯化钌为原料,以pvp和乙二醇为还原剂为形貌调控剂,通过两步还原方法制备得到絮团形貌的ptrucos合金纳米粒子。得到的絮团形貌的ptrucos合金纳米粒子表现出的丁二烯选择加氢性能,随着反应温度的提高而不断深度加氢,在25℃下进行催化反应,丁二烯转化率仅为5.1%,当反应温度升高到40℃时,丁二烯转化率为30%,产物中生成1-丁烯选择性为52.1%,2-丁烯选择性为39.6%,且一部分产物为正丁烷;而当反应温度为70℃时,丁二烯加氢转化率为100%,产物中没有2-丁烯而大部分
产物为丁烷。
8.又如中国专利cn109485536a公开了一种碳四馏分中炔烃和/或二烯烃的选择加氢方法,所选用负载型加氢催化剂活性金属组分为钯0.01-0.5重量%,助剂为银0-15重量%,载体为氧化铝。所述催化剂的堆密度可以为0.5-1.5g/cm3,比表面积可以为5-350m2/g,通过一段或多段加氢反应器,可以将丁二烯加氢至10ppm以下。
9.又如中国专利cn1238239a公开了一种催化碳四馏分中双烯烃选择加氢催化剂的制备方法,其主要技术特点是在δ、θ、α混相氧化铝载体上负载钯或钯和金组成,活性组分钯在载体上的含量0.05-0.5%m/m,金在载体上的含量为0.005-0.05%,制备的催化剂具有抗硫中毒能力、活性高、选择性好的优势,且在液空速10h-1
、温度50℃、压力1.5mpa、氢二烯比2.0mol/mol条件下,加氢转化率99.11%,烯烃收率100.82%。
10.综上所述,传统的贵金属加氢催化剂,涉及的催化剂主要为钯基催化剂,其他诸如铂、钌催化剂在进行加氢反应时则会存在烯烃加氢损失较高、丁烯得率低的缺陷,且低温加氢活性及选择性远低于钯为主的金属催化剂。因此,需要开发一种新型贵金属铂催化剂,期待其既具有较高的丁二烯加氢活性,以及较高的烯烃收率,更适宜于轻烃的加氢处理。
技术实现要素:11.为此,本发明所要解决的技术问题在于提供一种贵金属加氢催化剂,所述催化剂在临氢状态下,具有较高的加氢活性,可有效解决现有技术中铂金属催化剂在进行加氢反应时,加氢活性不高、丁二烯转化率低、烯烃损失率高的问题;
12.本发明所要解决的第二个技术问题在于提供一种二烯烃加氢反应工艺,主要适用于以石油化工炼油、裂解及煤化工甲醇制烯烃(mto)等工艺产生的c2-c8轻烃馏分,在临氢与缓和条件下,与所述贵金属催化剂接触,使物料中的二烯烃和炔烃转化为单烯,极少部分转化为烷烃,并具有丁二烯转化率高、烯烃加氢损失率低的特点。
13.为解决上述技术问题,本发明所述的一种贵金属加氢催化剂,所述催化剂包括载体和负载与所述载体上的加氢活性组分和助活性组分;
14.所述载体包括氧化铝或氧化硅;
15.所述载体的比表面积为20-300
㎡
/g,优选为50-150
㎡
/g,比孔容0.2-0.8ml/g,孔半径在5.0-15nm(氮吸附法);
16.所述加氢活性组分包括第
ⅷ
族金属元素中的至少一种,如pt和ru,最好采用pt;
17.所述助活性组分包括第ⅲb族金属元素中的至少一种,最好采用la或ce。
18.具体的,所述氧化铝为以δ相为主相,并选择性含有少量θ相的混相氧化铝。
19.具体的,所述混相氧化铝载体中,所述δ相氧化铝所占质量比为80-95wt%,所述θ相氧化铝所占质量比为5-20wt%。
20.具体的,所述的贵金属加氢催化剂:
21.所述加氢活性组分基于所述载体的负载量为0.05-0.5wt%,优选为0.1-0.3wt%;
22.所述助活性组分基于所述载体的负载量为0.05-3.0wt%,优选为0.1-2.0wt%。
23.本发明还提供了一种制备所述贵金属加氢催化剂的方法,包括如下步骤:
24.(1)取选定的所述载体与选定助活性组分的水溶液,按照选定的负载量比例充分混匀,经捏合、成型、干燥及焙烧处理后,备用;
25.或者,
26.在制备选定的所述载体时,按照选定的负载量比例,加入选定的活性组分,经捏合、成型、干燥及焙烧处理后,备用;
27.(2)将上述处理后的载体,按照选定的负载量,浸渍于选定加氢活性组分的水溶液中,经干燥机焙烧处理后,即得。
28.具体的,所述步骤(1)中,所述助活性组分的水溶液包括所述助活性组分的盐溶液,优选为硝酸盐或氯化盐溶液。
29.具体的,所述步骤(1)中,所述成型步骤中还添加有扩孔剂和/或粘结剂。所用粘结剂和扩孔剂为公知物质,加入量以载体重量为基准,扩孔剂1-4wt%,粘结剂1-2wt%。
30.具体的,所述步骤(1)中,载体可以可按要求加工成条形、三叶草形、球形、圆柱形或其他任意形状,以满足不同工艺的要求。
31.具体的,所述步骤(1)中,载体是以薄水铝石粉末或其为主要成分的混合体,与助活性组分制成的水溶液混合后,经捏合、成型、干燥后在400-1200℃下焙烧2-16小时而成。
32.具体的,所述步骤(2)中,所述加氢活性组分的水溶液包括所述加氢活性组分的盐溶液,优选为硝酸盐或氯化盐溶液。
33.具体的,所述步骤(2)中,所述浸渍步骤中,还添加有可以使溶液体系呈酸性的竞争吸附剂,所述竞争吸附剂的添加量占所述载体量的1.0-10.0wt%,可以是有机酸(甲酸、乙酸、草酸)或无机酸中的硝酸、盐酸,使溶液呈酸性。
34.具体的,所述步骤(2)中,所述浸渍步骤在常温-100℃浸渍,也可以在超声波40khz下震荡3-30min后浸渍。当一种以上选定的加氢活性组分金属时,可以采用共浸,也可采用分浸。
35.具体的,所述步骤(2)中,载体浸渍后在100-300℃干燥,最好是300-600℃下焙烧3-6小时。
36.本发明还公开了一种二烯烃加氢反应工艺,所述加氢处理步骤使用的催化剂包括所述的贵金属加氢催化剂。
37.本发明所述贵金属加氢催化剂,以含有δ相和θ相混相氧化铝为载体,以第
ⅷ
族金属元素为加氢活性组分,以第ⅲb族金属元素为助活性组分,通过控制所述载体的结构和参数等性能,制得催化剂具有较好的加氢催化性能,可以高效的将碳四中的二烯烃和炔烃选择性加氢脱除,同时保持较高的烯烃收率,适宜于轻烃综合利用工艺中的二烯烃脱除处理。
38.本发明所述二烯烃加氢脱除工艺,以所述贵金属加氢催化剂进行催化加氢反应,同时结合现有工艺,针对于一般性的fcc轻烃原料或者mto/mtp等不含硫化物的物料的加氢处理,可以在不进行装置及系统改动的前提下,即可将物料中的二烯烃、炔烃脱除,又可将反应热进行回收,降低装置的综合能耗,提高选择加氢装置的经济性。
附图说明
39.为了使本发明的内容更容易被清楚的理解,下面根据本发明的具体实施例并结合附图,对本发明作进一步详细的说明,其中,
40.图1为以fcc轻烃物料的加氢工艺流程示意图;
41.图2为其他不含硫化物轻烃物料的加氢工艺流程示意图;
42.图中附图标记表示为:1-轻烃物料,2-c3、c4分离塔,3-c3物料,4-脱硫塔,5-加氢反应器,6-h2物料,7-轻c4塔,8-轻c4物料,9-重c4塔,10-重c4物料,11-c5物料。
具体实施方式
43.下面通过实施例和比较例进一步描述本发明的技术方案,但本发明的保护范围不受实施例的限制。
44.本发明下述实施例中,以xrd(x射线衍射)法分析催化剂物相结构;n2吸附法测定比表面积和孔径分布。
45.实施例1
46.本实施例所述贵金属载体的制备方法,包括如下步骤:
47.(1)取薄水铝石粉末中加入5%田菁粉混合均匀,并加入含2wt%柠檬酸的水溶液,la的硝酸盐按2.3wt%(以氧化镧计)添加,配置成水溶液,充分混匀,经捏合、挤条成型制成直径1.5-3mm条形或2-4mm球形;按下列温度程序进行烧结,制得载体:a、室温下干燥24小时,b、140℃干燥4小时,c、140-500℃恒温1小时,d、500-1000℃恒温4小时,e、自然降温;
48.本步骤中制得的载体晶相为以δ相为主相(≥90%以上),比孔容为0.3-0.5ml/g,比表面为100-150m2/g;
49.(2)按催化剂pt负载含量要求,称取含量不少于37.6%的氯铂酸粉末,溶于蒸馏水中,配制成cl6h2pt水溶液;于室温-100℃条件下将上述方法制备的载体浸渍在pt溶液中,在浸渍溶液中同时加入10wt%的竞争吸附剂甲酸,均匀搅动,使活性组分均匀分布在载体的表面,待溶液无色变清透明后滤除余液,在120℃下干燥2小时,并在400℃焙烧6小时,即得所需催化剂,记为1#催化剂,经测试,pt在所述载体上的负载含量为0.3%(m/m)。
50.实施例2:
51.本实施例所述贵金属载体的制备方法,包括如下步骤:
52.(1)取薄水铝石粉末中加入2%田菁粉混合均匀,并加入含1wt%柠檬酸的水溶液,经捏合、挤条成型制成直径1.5-3mm条形或2-4mm球形;另取ce的硝酸盐按0.5%(以氧化铈计)添加配置成水溶液,将上述成型后的载体浸渍于上述硝酸ce盐溶液中,并按实施例1温度烧结,制得载体;
53.本步骤中制得的载体晶相为以δ相为主(≥90%以上)的晶相。
54.(2)按催化剂pt含量要求为0.3%,配制cl6h2pt水溶液,使用40khz超声处理30min,在加热85℃条件下将上述方法制备的载体浸渍在cl6h2pt水溶液中,在浸渍溶液中同时加入1wt%的竞争吸附剂硝酸,使活性组分均匀分布在载体的表面,待溶液无色变清透明后滤除余液,在120℃下干燥2小时,并在400℃焙烧6小时,即得所需催化剂,记为2#催化剂。
55.实施例3
56.本实施例所述贵金属载体的制备方法,包括如下步骤:
57.(1)取薄水铝石粉末中加入5%田菁粉混合均匀,并加入含2wt%柠檬酸的水溶液,la的硝酸盐按2.3wt%(以氧化镧计)添加,配置成水溶液,充分混匀,经捏合、挤条成型制成直径1.5-3mm条形或2-4mm球形;按下列温度程序进行烧结,制得载体:a、室温下干燥24小时,b、140℃干燥4小时,c、140-500℃恒温1小时,d、500-1000℃恒温4小时,e、自然降温;
58.(2)按催化剂ru负载含量(0.3%(m/m))要求,称取硝酸ru粉末,溶于蒸馏水中,配
制成水溶液;于室温-100℃条件下将上述方法制备的载体浸渍在ru溶液中,在浸渍溶液中同时加入10wt%的竞争吸附剂甲酸,均匀搅动,使活性组分均匀分布在载体的表面,待溶液无色变清透明后滤除余液,在120℃下干燥2小时,并在400℃焙烧6小时,即得所需催化剂。
59.实施例2:
60.本实施例所述贵金属载体的制备方法,包括如下步骤:
61.(1)取薄水铝石粉末中加入2%田菁粉混合均匀,并加入含1wt%柠檬酸的水溶液,经捏合、挤条成型制成直径1.5-3mm条形或2-4mm球形;另取ce的硝酸盐按0.5%(以氧化铈计)添加配置成水溶液,将上述成型后的载体浸渍于上述硝酸ce盐溶液中,并按实施例1温度烧结,制得载体;
62.(2)按催化剂ru含量要求为0.3%,配制硝酸ru水溶液,使用40khz超声处理30min,在加热85℃条件下将上述方法制备的载体浸渍在cl6h2pt水溶液中,在浸渍溶液中同时加入1wt%的竞争吸附剂硝酸,使活性组分均匀分布在载体的表面,待溶液无色变清透明后滤除余液,在120℃下干燥2小时,并在400℃焙烧6小时,即得所需催化剂。
63.对比例1
64.本对比例所述催化剂参考中国专利cn106475092a中方法制备。
65.称取200g纳米氧化铝粉,加入10倍纯净水,搅拌均匀;向浓度1%氯铂酸溶液中加入分散剂聚乙烯吡咯烷酮0.2g/l,将氯铂酸溶液加入到纳米氧化铝粉溶液,80℃搅拌1h,降至常温,继续加入纳米氧化铝粉,搅拌均匀,调节为含水率40%的湿料,继续加入0.04%的粘合剂高岭土,投入挤条机中挤条成型,马弗炉中700℃焙烧3h。再置于5%盐酸溶液中洗涤,去除纳米铝粉,在反应器中100℃通h2还原5h,即得所需催化剂,记为3#催化剂,经测试,最终pt含量为载体重量的0.3%。
66.对比例2
67.本对比例所述催化剂参考中国专利cn 111230141a中方法制备,具体步骤包括:
68.(1)将100μl h2ptcl6(0.1m)、100μl cocl2(0.1m)和240μlnaoh(0.2m)、3mlna2so3(0.02m)加入到4.56ml去离子水中,制备生长溶液,静置陈化一夜;
69.(2)在磁力搅拌下,将800μl去离子水,1ml pvp(5wt%)、200μl hcooh加到生长溶液中,搅拌10min;
70.(3)将步骤(2)得到的溶液转移到20ml的反应釜中,置于烘箱中200℃保持8h;
71.(4)将步骤(3)反应后溶液离心,然后用去离子水:乙醇=1:1洗涤3次,得到ptcos纳米线;
72.(5)将步骤(4)得到的ptcos在烘箱中80℃干燥,称取得到的ptcos纳米线的质量;
73.(6)取1mg干燥后得到ptcos,分散在6ml乙二醇中在40khz下超声20min,将ptcos-eg混合溶液在磁力搅拌下55℃预热30min,然后用注射器将0.4ml rucl3(5mm)缓慢加入ptcos-eg混合溶液中,在水浴55℃下继续保持10h;(即按1mgptcos对应6ml乙二醇对应0.4ml rucl3(5mm)引入ru);
74.(7)将步骤(6)反应后溶液离心,用乙醇:丙酮=2:1洗涤2次,用水洗涤2次,得到絮团形貌ptrucos合金,记为4#催化剂。
75.实验例
76.在相同工艺条件下,将上述实施例及对比例中制备的催化剂1#、2#、3#、4#,分别在
固定床装置上进行c4馏分选择加氢反应。反应器为内径20mm管式反应器,催化剂床层两端用惰性瓷球填充,在使用前用氢气还原10个小时后进行评价,不同的工艺条件如表1所示,待处理的c4原料分析见表2所示,经加氢处理后的催化剂的评价结果见表3所示。
77.丁烯收率:
[0078][0079]
表1实验例不同加氢工艺条件
[0080]
序号催化剂反应压力mpa液相空速h-1
反应温度℃氢二烯比mol/mol11#1.55852.522#1.55852.533#1.55852.544#1.5 60 51#1.551102.562#1.551102.573#1.551102.584#1.5 70 [0081]
表2待处理的c4原料成分
[0082]
组成ic4°
nc4°
tc
4=
1-c
4≡
ic
4≡
cc
4≡c4==
其他m,%45.4710.1712.1912.8712.077.060.160.01
[0083]
表3丁烯加氢结果
[0084]
序号二烯转化率,%c
4==
残余量丁烷收率,%丁烯收率,%179.380.0318101.4699.36280.480.0301101.8899.36334.950.1003101.4499.344*87.4 113.886.2591.890.0125103.4297.87691.440.0132103.3897.56765.760.0528104.5598.548*100.0 175.224.8
[0085]
注:8*数据为根据该专利文献记载。
[0086]
由表3数据可以看出,本发明制备催化剂(1#、2#)在进行二烯烃的加氢处理时,其1-丁烯收率优于对比催化剂3#,丁烯收率优于对比催化剂4#。经加氢反应后的产物中,二烯烃随着温度的升高,反应转化率逐步提高,但烯烃收率略有降低,烷烃收率增加。与对比例制得催化剂相比较,本发明方案不仅丁烯收率高,丁二烯脱除率高,且丁烯选择性好。
[0087]
应用例1
[0088]
如图1所示的工艺流程图,来自fcc装置的轻烃物料1进入c3、c4分离塔2进行c3、c4物料分离,,顶部分出的c3物料3去至其他丙烯分离装置;而分离塔2底部采出的c4、c5烃则可以不经减温直接进入脱硫塔4,所述脱硫塔4内净化剂采用cu、fe、zn、na为主要金属的单金
属或复合金属的化合物制备的脱硫剂进行轻烃吸附脱硫,使得进入本加氢反应器中的总硫含量<3ppm,通过将物料中的总硫含量控制在一定水平,再与h2物料6混合,一并进入加氢反应器5,所示加氢反应器5内装填有实施例1中制备的铂金属催化剂,反应器为筒式结构,催化剂装在反应器中部,上下两端装有惰性瓷球或玻璃球填充,氢气经质量流量计精确控制,与物料混合后进入反应器催化剂床层。
[0089]
物料中的丁二烯与h2在较高温度下反应,生成丁烯和少量丁烷,加氢反应放热使液体物料进一步增高,随物料中丁二烯含量的不同温升也不同,反应后的物料依次直接进入轻c4塔7和重c4塔9,热量在塔内得以回收,分离出轻c4物料8去至烷基化装置,重c4物料10及c5物料11则排出所述装置。
[0090]
应用例2
[0091]
如图2所示的工艺流程图,来自mto/mtp装置的不含硫化物的轻烃物料1在进入气分流程之后先进入c3、c4分离塔2进行c3、c4物料分离,顶部分出的c3物料3去丙烯分离装置;分离塔2底部采出的c4、c5烃则不经减温直接进入加氢反应器5,与h2物料6混合反应,所述加氢反应器5内装填有实施例1制备的铂金属催化剂,反应器为筒式结构,催化剂装在反应器中部,上下两端装有惰性瓷球或玻璃球填充,氢气经质量流量计精确控制,与物料混合后进入反应器催化剂床层。
[0092]
物料中的二烯烃(丁二烯)、炔烃与h2在较高温度下反应,生成丁烯和少量丁烷,加氢反应放热使液体物料进一步增高,随物料中丁二烯含量的不同温升也不同,反应后的物料直接进入轻c4塔7,热量在塔内得以回收,分离出轻c4物料8去及c5物料11则排出装置。
[0093]
本方法所述二烯烃加氢脱除工艺,以20万吨/年c4规模装置为基准,采用本发明催化剂及工艺,经选择加氢后的丁烯物料不但可以完全脱除丁二烯,并且分离后的物料可直接进入下游加以利用,同时,本方法工艺对加氢后的产物部分热量进行利用,流程简单,易于实施,经计算可使气分装置蒸汽消耗降低约1%。
[0094]
显然,上述实施例仅仅是为清楚地说明所作的举例,而并非对实施方式的限定。对于所属领域的普通技术人员来说,在上述说明的基础上还可以做出其它不同形式的变化或变动。这里无需也无法对所有的实施方式予以穷举。而由此所引伸出的显而易见的变化或变动仍处于本发明创造的保护范围之中。