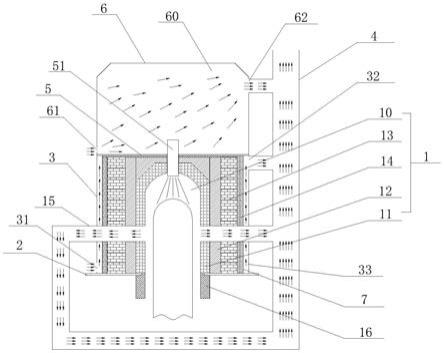
一种用于高纯合成石英生产的集成式反应釜
【技术领域】
1.本发明属于反应釜的技术领域,尤其涉及一种用于高纯合成石英生产的集成式反应釜。
背景技术:2.目前国内主要有直接法及间接法制造高纯合成石英产品,直接法主要是以高纯四氯化硅为原料,在1400
‑
2000℃的反应釜内发生物理及化学反应,直接熔制为高纯合成石英。在反应过程中会产生的大量的有害物质氯化氢及二氧化硅粉尘,需要排放至废气处理系统进行处理。但是由于反应釜内需要保持高温环境,目前国内生产厂家一般是降低反应釜内排气量来保障,这就会使部分氯化氢及二氧化硅溢出至车间内,影响车间环境及生产。
3.直接法制造的高纯合成石英产品一般在反应釜底部不断生长,因此底部需要安装支撑产品用的塔体装备。反应釜使用时需要先进行塔体装备安装,然后在顶部水泥平台上现场搭建反应釜,致使设备结构有差异、不统一,使得反应釜与塔体平台之间安装较为麻烦,装备无法进行统一替换,同时安装周期长,影响附近机台的正常生产。
4.目前制造高纯合成石英产品用的反应釜皆为保温材料直接裸露式或者单层金属包裹式结构,反应釜表面温度比较高,容易烫伤操作人员,同时高温产生反应釜表面变色,不美观,反应釜底部密封不足,光辐射严重,耗能高,有害气体容易泄露。
技术实现要素:5.本发明的目的就是解决背景技术中的问题,提出一种用于高纯合成石英生产的集成式反应釜,能够在保证炉膛高温环境的同时有效降低反应釜表面温度,防止操作人员被烫伤和反应釜表面因高温而变色,防止反应釜内的有害物质溢出,反应釜的结构统一便于维护更换,安装使用过程中炉体不易发生破裂。
6.为实现上述目的,本发明提出了一种用于高纯合成石英生产的集成式反应釜,包括炉体、安装座、下炉罩和排废管,炉体内部设有炉膛,所述炉体包括由内到外依次设置的耐火层、隔热层、保温层和缓冲层,所述保温层的外侧壁、隔热层和保温层的上端用缓冲层包裹住,所述下炉罩套设在炉体的外侧,下炉罩和炉体的上、下端分别与隔板、安装座相连并形成有隔热腔,所述下炉罩上设有隔热腔进风口和隔热腔排气口,所述隔板上安装有燃烧器和上炉罩,上炉罩与隔板之间形成有上炉腔,上炉罩上设有上炉腔进风口、位于上炉腔进风口斜上方的上炉腔排气口,所述燃烧器的喷火端穿过炉体插入炉膛内,所述炉膛外接有排气管,所述排废管与隔热腔排气口、上炉腔排气口、排气管相连。
7.作为优选,所述炉膛底部设有炉体保温层,炉体保温层的上端与耐火层相连,炉体保温层外侧壁与安装座相连,炉体保温层的设计能有效减少炉膛对外的光辐射,减少热量散失,降低能耗,避免安装座与炉膛直接接触,进而有效降低安装座的温度,防止其变形,确保反应釜能正常使用。
8.作为优选,所述耐火层由耐高温材料制成,耐高温材料包括刚玉或碳化硅,所述耐
火层内壁光滑,可耐极高温度,表面光滑可防止积灰,防止生产时杂质掉落至炉膛内的产品上影响产品的品质,可保障炉膛容积及流场,稳定生产。
9.作为优选,所述隔热层由高纯氧化铝空心球件制成,耐高温隔热,安装方便。
10.作为优选,所述保温层由聚轻砖制成,保温效果好,可耐温隔热,使用成本低。
11.作为优选,所述缓冲层由软毡制成,缓冲层的外沿用内罩压紧,内罩下端安装在安装座上,通过内罩压紧把内部硬质的耐火层、隔热层、保温层与软毡紧紧安装于一体,软毡具有一定柔度,可防止耐火层、隔热层、保温层安装时开裂,同时又能使耐火层、隔热层、保温层有一定膨胀空间,防止热胀冷缩时开裂。
12.作为优选,所述内罩、下炉罩、上炉罩和隔板均为硬质构件,保证内罩、下炉罩、上炉罩和隔板具有一定的硬度,减少反应釜的调试安装时间。
13.作为优选,所述硬质构件为不锈钢构件、耐高温喷涂件、钛制或哈氏合金件,具有良好的硬度和耐腐蚀性能,使用寿命相对较长。
14.作为优选,所述排气管、隔热腔排气口高于隔热腔进风口,能够使得炉膛内有害物质及时排出炉膛,保障反应釜生产的高效进行,防止有害物质溢出反应釜影响车间环境,保障生产安全。
15.作为优选,所述耐火层的厚度为60~120mm,所述保温层的厚度为200~300mm,所述隔热层厚度为100~250mm,所述耐火层的耐火温度为1800~2000℃,所述保温层的耐火温度为800~1200℃,所述隔热层的耐火温度为1500~1700℃,耐火层、隔热层、保温层之间采用不同耐火温度设置可保证炉膛内高温及隔热效果,降低材料成本,耐火层、隔热层、保温层的厚度可确保炉膛内具有1400~2000℃的高温。
16.本发明的有益效果:本发明通过隔热腔和上炉腔内形成有流动的风场作用,炉体包括耐火层、隔热层、保温层和缓冲层,使得炉膛内溢出的有害物质可被吹至排废管,防止反应釜内有害物质溢出,可对反应釜表面进行降温使得其保持在40~70℃的低温状态,结合炉体采用多层结构使得炉膛保持在高温状态,保证炉膛高温环境的同时有效降低反应釜表面温度,防止操作人员被烫伤和反应釜表面因高温而变色;将炉体、下炉罩安装在安装座上,隔板安装在炉体及下炉罩上,下炉罩安装在隔板上,使得反应釜整体安装方便,结构统一便于更换维护;将保温层的外侧壁、隔热层和保温层的上端用缓冲层包裹住,缓冲层可起到一定缓冲作用,缓冲层可将耐火层、隔热层、保温层安装于一体,防止耐火层、隔热层、保温层安装时开裂,同时又能使耐火层、隔热层、保温层有一些膨胀空间,防止热胀冷缩时开裂;将排废管与隔热腔排气口、上炉腔排气口、排气管相连,排气管与炉膛相连,排废管末端与废气处理装置装置,可对废气中的有害物质进行无害化处理。
17.本发明的特征及优点将通过实施例结合附图进行详细说明。
【附图说明】
18.图1是本发明一种实施例的主视图结构示意图。
19.图中:1
‑
炉体、2
‑
安装座、3
‑
下炉罩、4
‑
排废管、5
‑
隔板、6
‑
上炉罩、7
‑
内罩、10
‑
炉膛、11
‑
耐火层、12
‑
隔热层、13
‑
保温层、14
‑
缓冲层、15
‑
排气管、16
‑
炉体保温层、31
‑
隔热腔进风口、32
‑
隔热腔排气口、33
‑
隔热腔、51
‑
燃烧器、60
‑
上炉腔、61
‑
上炉腔进风口、62
‑
上炉腔排气口。
【具体实施方式】
20.参阅图1,本技术提供了一种用于高纯合成石英生产的集成式反应釜,包括炉体1、安装座2、下炉罩3和排废管4,炉体1内部中间位置设有贯穿炉体1底部的炉膛10,位于炉膛10侧面的炉体1部分包括沿炉膛10的径向由内到外依次设置的耐火层11、隔热层12、保温层13和缓冲层14,位于炉膛10上端的炉体1部分包括沿炉膛10轴向自下而上依次设置有耐火层11、隔热层12和缓冲层14,保温层13的外侧壁、隔热层12和保温层13的上端用缓冲层14包裹住,下炉罩3套设在炉体1的外侧,下炉罩3和炉体1的上、下端分别与隔板5、安装座2相连并形成有隔热腔33,下炉罩3上设有与隔热腔33相连通的隔热腔进风口31和隔热腔排气口32,隔热腔排气口32位于隔热腔进风口31的斜对面且高于隔热腔进风口31,隔板5上安装有燃烧器51和上炉罩6,上炉罩6与隔板5之间形成有上炉腔60,上炉罩6上设有上炉腔进风口61、位于上炉腔进风口61斜上方的上炉腔排气口62,上炉腔进风口61、上炉腔排气口62均与上炉腔60相连通,燃烧器51的喷火端穿过炉体1插入炉膛10内,炉膛10外接有排气管15,排废管4与隔热腔排气口32、上炉腔排气口62、排气管15相连,其中,排废管4末端连接有废气处理装置,风由上炉腔进风口61吹入并由上炉腔排气口62排出可在上炉罩6内部形成有一个稳定的上风场,通过隔热腔进风口31的进风和隔热腔排气口32的排气可在隔热腔33内形成一个稳定的下风场,燃烧器51的另一端通入高纯氢气、氧气及高纯原料气四氯化硅,下风场与耐火层11、隔热层12、保温层13共同作用可保证下炉罩3保持在40~70℃的低温状态,避免烫伤工作人员以保证反应釜的安全使用,反应釜的外径尺寸小。
21.进一步地,炉膛10底部设有炉体保温层16,炉体保温层16的上端与耐火层11相连,炉体保温层16外侧壁与安装座2相连。
22.进一步地,耐火层11由耐高温材料制成,耐高温材料包括刚玉或碳化硅,耐火层11内壁光滑。
23.进一步地,隔热层12由纯度90%以上的高纯氧化铝空心球件制成。
24.进一步地,保温层13由聚轻砖制成。
25.进一步地,缓冲层14由软毡制成,纵向的缓冲层14外侧用内罩7压紧,内罩7下端安装在安装座2上,用内罩7压紧后内罩7外壁、隔板5下端、安装座2上端和下炉罩3内壁之间围合形成有隔热腔33。
26.进一步地,内罩7、下炉罩3、上炉罩6和隔板5均为硬质构件,硬质构件可选用不锈钢构件、耐高温喷涂件、钛制或哈氏合金件。
27.进一步地,排气管15、隔热腔排气口32高于隔热腔进风口31。
28.进一步地,耐火层11的厚度为60~120mm,保温层13的厚度为200~300mm,隔热层12厚度为100~250mm,耐火层11的耐火温度为1800~2000℃,保温层13的耐火温度为800~1200℃,隔热层12的耐火温度为1500~1700℃。
29.为了进一步说明本技术的技术方案,以下为本技术中耐火层11、保温层13和隔热层12设置的具体实施例。
30.实施例1:耐火层11的厚度为80mm,保温层13的厚度为230mm,隔热层12厚度为160mm,耐火层11的耐火温度为1900℃,保温层13的耐火温度为1100℃,隔热层12的耐火温度为1700℃,该厚度设计可使得炉膛10内的温度保持在1800℃,下炉罩3外表面温度66℃。
31.实施例2:耐火层11的厚度为100mm,保温层13的厚度为280mm,隔热层12厚度为
180mm,耐火层11的耐火温度为1800℃,保温层13的耐火温度为900℃,隔热层12的耐火温度为1500℃,该厚度设计可使得炉膛10内的温度保持在1800℃,下炉罩3外表面温度51℃。
32.实施例3:耐火层11的厚度为60mm,保温层13的厚度为250mm,隔热层12厚度为220mm,耐火层11的耐火温度为2000℃,保温层13的耐火温度为1000℃,隔热层12的耐火温度为1600℃,该厚度设计可使得炉膛10内的温度保持在1800℃,下炉罩3外表面温度50℃。
33.本发明工作过程:
34.本反应釜在工作过程中,将安装座2下端安装在塔体装备上,炉体1、内罩7和下炉罩3下端安装在安装座2上,隔板5安装在内罩7和下炉罩3上,上炉罩6安装在隔板5上,隔板5下端与炉体1顶部水平方向设置的缓冲层14相接触,炉体保温层16插入塔体设备内,工作时,燃烧器51一端通入高纯氢气、氧气及高纯原料气四氯化硅后点火使得炉膛10内温度升高至反应温度,原料和气体在炉膛10内反应生成石英产品,使用过程中,风分别从隔热腔进风口31和上炉腔进风口61吹入隔热腔33和上炉腔60内,隔热腔33内的风可将炉体1的部分热量及有害物质吹向隔热腔排气口32并从隔热腔排气口32吹向排废管4,上炉腔60内的风可将从炉膛10溢出的有害物质氯化氢及二氧化硅吹向上炉腔排气口62并从上炉腔排气口62吹向排废管4,炉膛10内的有害物质可由排气管15排至排废管4,排废管4末端的废气处理装置对其内部的有害物质进行无害化处理后排放至环境中,隔热腔33内风流动形成的风场可对炉体1进行一定降温处理,上炉腔60内风流动形成的风场可对隔板5和燃烧器51进行一定降温作用且可提供一定的氧气保证燃烧器51的正常使用。
35.上述实施例是对本发明的说明,不是对本发明的限定,任何对本发明简单变换后的方案均属于本发明的保护范围。