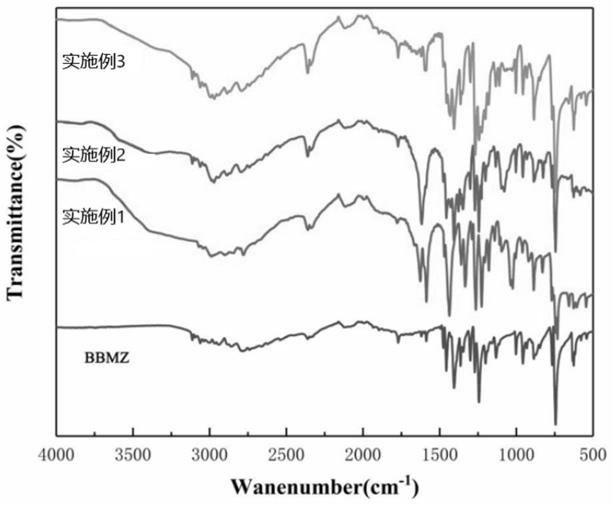
1.本发明属于催化剂技术领域,具体属于离子液体催化剂技术领域,涉及离子液体催化剂的制备及其应用。
背景技术:2.碳酸二乙酯(dec)是一种重要的有机合成中间体,含有乙基、乙氧基、羰基和羰乙氧基,可以通过与醇、酚、胺、酯和其他化合物的反应生成一系列重要的化学产品;又因其为非毒性,释放到环境中可缓慢分解成co2和乙醇,表现出良好的环保特性,被公认为是一种具有很高工业应用价值的绿色化学品。
3.碳酸甲乙酯(emc)是一种简单的不对称碳酸酯,分子中同时拥有甲基和乙基,因此兼有碳酸二甲酯和碳酸二乙酯的特性,可以在有机合成中作特殊试剂。近些年发现碳酸甲乙酯是性能优良的锂离子电池电解液,能有效提高电池的充放电量和电容量密度的能力,大大增强电池的安全性能和使用寿命。
4.由于碳酸甲乙酯和碳酸二乙酯都是非常具有发展前景的化工产品和锂电池电解液,因此其制备受到广泛的关注。
5.碳酸甲乙酯和碳酸二乙酯酯交换合成法具有反应条件温和、绿色无污染和经济发展优势等特点。长期以来工业上以醇钠作为酯交换合成碳酸甲乙酯和碳酸二乙酯的催化剂,但在生产过程中醇钠易失活,不能循环使用,且生成的烷基钠等副产物堵塞管道。
6.离子液体具有结构可设计和性能可调节等特点被应用于催化合成碳酸酯,并具有较好的催化性能,但其自身的液相态和黏度大等性能在分离与纯化方面存在缺陷,所以采用硅胶、分子筛、聚合物等载体固载离子液体的文献也层出不穷,但在催化过程中容易脱载。因此,寻求新的方法设计并制备高效的固态离子液体催化剂一直备受专家学者的关注。
技术实现要素:7.为了克服上述问题,本发明人进行了锐意研究,研究出用于酯交换催化合成碳酸甲乙酯和碳酸二乙酯的碱性离子液体催化剂,其中含有苯并咪唑阴离子和碱金属阳离子,将其用于以碳酸二甲酯和乙醇为原料,催化合成碳酸甲乙酯和碳酸二乙酯时,由于苯并咪唑阴离子具有更强的配位和亲核能力,碱金属阳离子增加了活性位点,使得催化剂具有优异的化学稳定性,与传统醇钠催化剂相比,碳酸二甲酯的转化率以及产物的收率都得到了显著的提高,且所述催化剂为固体,反应结束易分离,高效环保,在工业生产中具有广阔的应用前景,从而完成了本发明。
8.具体来说,本发明的目的在于提供以下方面:
9.第一方面,提供一种用于酯交换催化合成碳酸甲乙酯和碳酸二乙酯的催化剂,所述催化剂为金属咪唑类碱性离子液体催化剂,包括咪唑类阴离子和金属阳离子。
10.第二方面,提供第一方面所述的催化剂的应用,用于酯交换催化合成碳酸甲乙酯和碳酸二乙酯。
11.第三方面,提供一种合成碳酸甲乙酯和碳酸二乙酯的方法,所述方法包括以下步骤:
12.步骤一,制备催化剂;
13.步骤二、以碳酸二甲酯和乙醇为原料,加入所述催化剂,进行反应,制得碳酸甲乙酯和碳酸二乙酯。
14.本发明所具有的有益效果包括:
15.(1)本发明提供的催化剂具有更强的配位和亲核能力,其中含有的苯并咪唑阴离子与碱金属阳离子之间产生协同催化效应,用于酯交换反应时,与传统的杂环含氮类催化剂以及醇钠催化剂相比,提高了反应物的转化率和产物的收率。
16.(2)本发明提供的催化剂具有较好的热稳定性和化学稳定性,反应结束后易分离回收,并可循环使用,使催化过程更环保。
17.(3)使用本发明的催化剂催化合成碳酸甲乙酯和碳酸二乙酯时,有效解决了使用传统醇钠催化剂时所生成的烷基钠副产物堵塞管道的问题。
18.(4)本发明提供的制备碳酸甲乙酯和碳酸二乙酯的方法,采用本发明的催化剂与使用传统醇钠催化剂相比,反应物碳酸二甲酯的转化率和产物碳酸二乙酯的收率得到明显提高。
19.(5)本发明提供的制备碳酸甲乙酯和碳酸二乙酯的方法,高效环保,本发明的催化剂也为离子液体催化酯交换反应合成碳酸酯提供了新的发展思路。
附图说明
20.图1示出实施例1-3制得的催化剂与苯并咪唑红外光谱图;
21.图2示出实施例1-3制得的催化剂与苯并咪唑xrd谱图;
22.图3示出实施例6中所述馏出液的气相色谱图;
23.图4示出实施例6中所述釜液蒸馏物的气相色谱图。
具体实施方式
24.下面通过附图和实施例对本发明进一步详细说明。通过这些说明,本发明的特点和优点将变得更为清楚明确。
25.在这里专用的词“示例性”意为“用作例子、实施例或说明性”。这里作为“示例性”所说明的任何实施例不必解释为优于或好于其它实施例。尽管在附图中示出了实施例的各种方面,但是除非特别指出,不必按比例绘制附图。
26.本发明第一方面,提供一种用于酯交换催化合成碳酸甲乙酯和碳酸二乙酯的催化剂,所述催化剂为金属咪唑类离子液体催化剂,包括咪唑类阴离子和金属阳离子。
27.在本发明中,所述催化剂属于碱性离子液体催化剂,碱催化是当代化学的一个重要组成部分,但是,传统的碱性催化剂大多有毒有害且催化效率比较低。为了保护人类的身体健康和经济社会的可持续发展,开发绿色、高效、有潜力的碱性催化剂势在必行。作为绿色化学背景下发展起来的兼有溶剂和催化剂性质的碱性离子液体,由于其具备高催化活性、可重复使用性、不易挥发性、不可燃性等优点,具有良好的应用前景。
28.进一步地,所述咪唑类阴离子优选为取代或未取代的咪唑或苯并咪唑阴离子,更
优选为苯并咪唑阴离子,所述金属阳离子优选为碱金属阳离子。
29.本发明人发现,苯并咪唑阴离子对酯交换反应具有更高的选择性,可以有效提高产物的收率,特别是用于催化碳酸二甲酯与乙醇合成碳酸甲乙酯和碳酸二乙酯时,能增强催化活性,提高反应转化率,不受任何理论的束缚,这可能是因为苯并咪唑阴离子具有更强的配位和亲核能力导致的;碱金属阳离子增加了催化剂的活性位点,苯并咪唑阴离子与碱金属阳离子之间产生协同催化效应,进一步提高反应原料的转化率和目标产物的收率。
30.此外,所述催化剂常温如25℃下为固体,易溶于水、乙醇等溶剂,不易燃烧、不爆炸、不氧化,具有较好的热稳定性和化学稳定性,同时具有易存放、绿色无污染的特性。
31.根据本发明,所述催化剂具有如下结构式:
[0032][0033]
其中,m为碱金属,优选为钠、钾或锂,最优选为锂。
[0034]
通过红外光谱可以看到,所述催化剂化合物在约3063cm-1
处出现弱吸收峰,为苯环上c-h的伸缩振动吸收峰,在约1586cm-1
、1629cm-1
、1479cm-1
、1454cm-1
处出现多峰,为苯环的c=c骨架振动峰;在约1767cm-1
处出现吸收峰,此峰为咪唑环上的c=c的伸缩振动吸收峰,在约1361cm-1
处出现c=n的吸收峰,在约2373cm-1
处为n-h的伸缩振动吸收峰,在约751cm-1
处出现咪唑环弯曲振动峰。当m为不同碱金属时,各峰位置和强弱有细微差别(具体可参见其红外光谱图)。
[0035]
此外,由于所述催化剂化合物常温下为固体,可进行粉末衍射光谱分析,xrd谱图表明,分别在2θ大约为13.24
°
、14.56
°
、18.29
°
、19.45
°
、22.56
°
、23.73
°
、25.67
°
、26.37
°
、27.07
°
、28.93
°
、29.71
°
、30.02
°
、35.23
°
、37.01
°
、37.72
°
、39.51
°
、41.21
°
、42.30
°
、45.96
°
、46.74
°
、48.21
°
、49.61
°
、50.47
°
、52.72
°
、53.97
°
、56.21
°
和58.62
°
处出现不同的衍射峰,与苯并咪唑的衍射峰相对应,当m为不同碱金属如锂、钾、钠时,在2θ大约介于23
°
和78
°
之间区域,出现不同的衍射峰。
[0036]
在本发明中,所述活性元素金属钠、钾或锂有效增加了催化剂表面的活性位点,进而提高催化性能,有助于提高催化反应的选择性和稳定性。
[0037]
在本发明中,所述催化剂用于酯交换催化合成碳酸甲乙酯和碳酸二乙酯时可以循环使用,例如,其循环使用5次以上,仍保持较好的催化效果。
[0038]
本发明第二方面,提供第一方面所述的催化剂的应用,用于酯交换催化合成碳酸甲乙酯和碳酸二乙酯。
[0039]
本发明第三方面,提供一种合成碳酸甲乙酯和碳酸二乙酯的方法,所述方法包括以下步骤:
[0040]
步骤一,制备本发明所述的催化剂;
[0041]
步骤二、以碳酸二甲酯和乙醇为原料,加入所述催化剂,进行反应,制得碳酸甲乙酯和碳酸二乙酯。
[0042]
以下详述合成碳酸甲乙酯和碳酸二乙酯的方法。
[0043]
步骤一,制备本发明所述的催化剂。
[0044]
根据优选的实施方式,将咪唑类化合物和金属化合物溶于溶剂中,加热进行反应,反应结束后对产物进行处理,得到所述催化剂。
[0045]
其中,所述咪唑类化合物为取代或未取代的咪唑或苯并咪唑化合物,优选为苯并咪唑;
[0046]
所述金属化合物选自一种或多种水溶性金属化合物,优选金属氢氧化物,如氢氧化钠、氢氧化钾、氢氧化锂、氢氧化钡等,金属氧化物,如氧化钠,金属盐,如氯化钾、硝酸钠、氯化钠等;优选为金属氢氧化物,更优选为氢氧化钠、氢氧化钾或氢氧化锂,最优选为氢氧化锂。
[0047]
在本发明中,咪唑类化合物为催化剂提供咪唑类阴离子,金属化合物为催化剂提供金属阳离子,以咪唑类化合物和金属化合物制得的催化剂化学性质稳定。特别是以苯并咪唑和金属氢氧化物制得的催化剂中,苯并咪唑阴离子具有更强的配位和亲核能力,提高了酯交换反应的选择性和转化率,金属氢氧化物如氢氧化钠、氢氧化钾、氢氧化锂等不仅增加了催化剂的活性位点,同时氢氧化钠、氢氧化钾和氢氧化锂的碱性强,易与苯并咪唑反应脱水结合,反应过程无三废产生,易制得性质稳定的催化剂。
[0048]
在本发明中,所述咪唑类化合物和金属化合物摩尔比为1:(0.5~3),优选为1:(0.8~2),更优选为1:(0.9~1.2),例如1:1。
[0049]
根据本发明,随着金属化合物摩尔量的增加,催化剂表面的活性位点数目增多,但是过多的活性位点不仅不会增加催化剂的活性,反而会导致副产物的产生。
[0050]
根据本发明,所述溶剂选自水,醇类如乙醇、甲醇,酮类如丙酮等,优选为水。
[0051]
在本发明中,以水作为溶剂,就能将制备催化剂的反应原料溶解,且具有来源广泛、成本低的优势。
[0052]
在本发明中,溶剂的使用量仅需满足能将咪唑类化合物和金属化合物溶解,且加热反应状态呈均相即可,过量的溶剂会增加后处理负担。
[0053]
根据优选实施方式,所述咪唑类化合物和金属化合物混合物摩尔量与溶剂体积之比为0.2mol:(40~90)ml,优选为0.2mol:(50~80)ml,例如0.2mol:60ml。
[0054]
根据本发明,所述反应温度为50~100℃,优选为60~90℃,更优选为70~80℃。
[0055]
在本发明中,将反应加热,不仅可以加快反应速率,还可以提高催化剂的活性,但是过高的温度,催化剂上的活性位点反而会降低,当反应温度为50~100℃,特别是70~80℃时,制得的催化剂上具有较高的活性位点。
[0056]
进一步地,加热反应的时间为6~36h,优选为10~28h,更优选为12~24h,例如16~18h。
[0057]
其中,随着反应时间的延长,反应越充分,催化剂目标产物的收率越高,但是过长的时间不会对催化剂的收率产生显著的影响,从经济角度出发,在上述加热反应时间范围内,反应状态和催化剂收率达到最佳。
[0058]
任选地,加热反应在惰性气体保护气氛下进行,所述惰性气体为氮气或氩气、氦气等稀有气体,优选氮气。
[0059]
根据本发明,所述后处理包括:去除溶剂、洗涤、过滤和干燥。
[0060]
根据优选实施方式,所述去除溶剂是将反应后的液体产物进行真空旋蒸,例如采用旋转蒸发仪以去除溶剂。
[0061]
为进一步在短时间内去除溶剂,去除溶剂的温度与加热反应的温度大致相当,此时不会对反应产生任何影响,所述温度为60~100℃,优选为70~90℃,更优选为75~80℃;在此温度下,仅需25~50min就可达到去除溶剂的目的,优选地,去除溶剂的时间为30~45min,更优选地,去除溶剂的时间为35~40min。
[0062]
在本发明中,洗涤时选取的洗涤剂不仅不能和催化剂之间发生反应,同时还需保证催化剂在洗涤剂中有较大的溶解度,以及易于去除。
[0063]
优选地,所述洗涤剂选自甲醇或丙酮,优选地,所述洗涤剂为甲醇。
[0064]
本发明人发现,以甲醇作为洗涤剂,制得的催化剂易溶于甲醇,而微溶于未反应的原料如金属化合物,更容易得到高纯度催化剂。
[0065]
任选地,将过滤后所得溶液在40~60℃下旋蒸15~30min,去除其中的大部分洗涤剂,减少干燥时间。
[0066]
进一步,将过滤后所得溶液在45~55℃下旋蒸18~25min。
[0067]
更进一步,将过滤后所得溶液在50℃下旋蒸15~20min。
[0068]
在本发明中,所述干燥温度为50~90℃,优选为60~85℃,更优选为75~80℃;所述干燥时间为12~36h,优选为18~30h,优选为24h。
[0069]
根据本发明,最终获得的催化剂为固体,反应结束后易分离回收,大大减少了酯交换反应的后续处理操作。
[0070]
步骤二、以碳酸二甲酯和乙醇为原料,加入所述催化剂,进行反应,制得碳酸甲乙酯和碳酸二乙酯。
[0071]
本发明人经大量研究发现,和传统催化剂如乙醇钠催化制备碳酸甲乙酯和碳酸二乙酯相比,本发明所述的催化剂催化合成碳酸甲乙酯和碳酸二乙酯时,几乎不会产生醚类等副产物,解决了使用传统催化剂如乙醇钠催化制备碳酸甲乙酯和碳酸二乙酯时,由于变质生成的烷基钠副产物导致堵塞管道的技术难题;同时,反应过程中,碳酸二甲酯的转化率可提高8%以上,甚至最高可提高至约21%;碳酸甲乙酯和碳酸二乙酯的总收率可提高10%以上,甚至可提高至约20%,其中,碳酸二乙酯的收率提高更为明显,例如碳酸甲乙酯的收率可提高1%~5%,而碳酸二乙酯的收率可提高8%~15%。
[0072]
根据本发明,催化剂的使用重量占碳酸二甲酯和乙醇混合物总重量的百分比为0.1~1%,优选为0.3~0.8%,更优选为0.4~0.7%,例如0.5%。
[0073]
其中,随着催化剂加入量的增多,催化剂上的活性位点越多,催化反应越激烈,反应速率加快,碳酸二甲酯的转化率提高,过量的催化剂使得反应过于激烈,无法控制反应速率,对反应不利。
[0074]
根据本发明,碳酸二甲酯和乙醇反应的摩尔比为1:(2~5),优选为1:(3~4),更优选为1:4。
[0075]
本发明人发现,随着乙醇加入量的增加,碳酸二甲酯的转化率先增大后减小,追其原因,可能是因为过量的乙醇与原料碳酸二甲酯及反应生成的甲醇形成三元共沸物,降低了产物碳酸甲乙酯和碳酸二乙酯的收率。
[0076]
根据本发明,酯交换反应的温度为50~80℃,优选为60~70℃,更优选为63~64
℃。
[0077]
本发明人发现,随着反应温度的升高,碳酸二甲酯的转化率、碳酸甲乙酯和碳酸二乙酯的收率逐渐增加,而且反应时间明显缩短,因而反应温度尽量保持较高的温度;又由于碳酸二甲酯和反应生成的甲醇共沸物沸点为63.7℃,如果反应温度过高,特别是高于80℃时,更多的乙醇会与碳酸二甲酯、及反应生成的甲醇形成三元共沸物,降低碳酸甲乙酯和碳酸二乙酯的收率,当温度保持在50~80℃,特别是63~64℃时,反应生成的碳酸甲乙酯和碳酸二乙酯的收率最高。
[0078]
在一种优选实施方式中,反应时,为了保持反应温度控制在上述温度范围内,且使得反应平稳有序、呈均相反应状态进行,控制反应体系的外源温度为100℃左右,同时以80~90r/min的转速搅拌反应物。例如,反应时,油浴加热至100℃,通过搅拌器调节搅拌转速为80~90r/min,当反应体系中酯交换反应温度为50~80℃时,开始收集组分。
[0079]
根据本发明,反应过程中以(2~4):1的回流比采集馏出液,优选以3:1的回流比采集馏出液。此时,可以将更多的轻组分如反应物乙醇和产物甲醇从反应体系中采出,更多的重组分如反应物碳酸二甲酯、产物碳酸甲乙酯和碳酸二乙酯作为釜液依然保留在反应体系中,有利于提高碳酸二甲酯的转化率。
[0080]
根据本发明,反应结束后,获得的物质中含有催化剂、产物碳酸甲乙酯和碳酸二乙酯以及少量的反应物乙醇、碳酸二甲酯和产物甲醇,经常压蒸馏和减压蒸馏,最终获得碳酸甲乙酯和碳酸二乙酯。
[0081]
根据本发明优选地实施方式,通过常压蒸馏采出反应物乙醇、碳酸二甲酯和产物甲醇,此时体系中含有催化剂和产物碳酸甲乙酯、碳酸二乙酯,优选通过减压蒸馏的方式将碳酸甲乙酯和碳酸二乙酯的共沸物采出,这样,既能够获得纯净的碳酸甲乙酯和碳酸二乙酯共沸物,而且还实现了体系中催化剂与碳酸甲乙酯和碳酸二乙酯的分离,进而不但避免了催化剂对碳酸甲乙酯和碳酸二乙酯的纯度产生影响,更便于催化剂回收和重新利用。
[0082]
其中,常压蒸馏的温度为80~100℃,优选为95℃,减压蒸馏的压力为-0.06~-0.1mpa,优选为-0.08~-0.09mpa,温度为90~110℃,优选为95℃。
[0083]
工业上,通常将碳酸甲乙酯和碳酸二乙酯同时应用于锂离子电池电解液,因此无需将制得的碳酸甲乙酯和碳酸二乙酯进一步分离,具有节能减耗的优势。当然本发明也可以根据市场需求,通过调节碳酸二甲酯和乙醇的摩尔比,控制碳酸二甲酯和碳酸二乙酯的组分比例。
[0084]
根据本发明,以碳酸二甲酯和乙醇为原料,催化酯化反应制备碳酸甲乙酯和碳酸二乙酯,所述催化剂为碱性离子液体催化剂,其中含有苯并咪唑阴离子和碱金属阳离子,苯并咪唑阴离子具有更强的配位和亲核能力,与提供活性位点的锂离子、钠离子或钾离子之间相互作用,不仅提高了反应的稳定性,同时提高了反应物碳酸二甲酯的转化率、产物碳酸甲乙酯和碳酸二乙酯的收率,反应过程中,几乎没有环己醇、醚类等副产物的产生。
[0085]
本发明中,由于反应结束采集得到的馏出物中含有轻组分甲醇和乙醇,以及微量的未反应完全的碳酸二甲酯、产物碳酸甲乙酯和碳酸二乙酯,反应体系中除了催化剂外,含有大量的产物碳酸甲乙酯和碳酸二乙酯,以及少量未反应完全的碳酸二甲酯、少量的轻组分甲醇和乙醇,为了测定本发明产物中各组分的含量,可按照常规方式测试方法如面积归一化法进行测定和计算。
[0086]
进一步地,本发明中所述面积归一化法具体为:反应结束后,称量馏出液的质量,记为m1,获得馏出液的气相色谱图,并在上述条件下从反应后体系,即釜液中蒸馏采出甲醇、乙醇和碳酸二甲酯,之后在上述条件下继续蒸馏采出碳酸甲乙酯和碳酸二乙酯共沸产物,称量所述釜液蒸馏物,即碳酸甲乙酯和碳酸二乙酯共沸产物、甲醇、乙醇和碳酸二甲酯的质量,记为m2,获得该釜液蒸馏物的气相色谱图。根据m1、m2以及上述两张气相色谱图,通过面积归一化法测定产物中含有的组分含量,并计算碳酸二甲酯的转化率以及产物碳酸甲乙酯和碳酸二乙酯的收率。
[0087]
根据本发明,碳酸二甲酯的转化率可达到48%以上,甚至高至60%,产物碳酸甲乙酯和碳酸二乙酯的总收率可达到45%以上,甚至高至60%,特别地,碳酸甲乙酯的收率可达到17%以上,甚至高至22%,碳酸二乙酯的收率可达到30%以上,甚至高至45%。
[0088]
进一步地,所述碱性离子液体催化剂为固体,反应结束易分离,分离后的催化剂直接套用于下一批次碳酸甲乙酯和碳酸二乙酯的制备,循环使用5次以上,仍保持较好的催化效果,例如循环使用5次后,碳酸二甲酯的转化率可达到50%以上,而碳酸甲乙酯的收率可达到20%以上,和/或,碳酸二乙酯的收率可达到30%以上。
[0089]
实施例
[0090]
以下通过具体实例进一步描述本发明,不过这些实例仅仅是范例性的,并不对本发明的保护范围构成任何限制。
[0091]
实施例1
[0092]
催化剂bbmz-na的制备
[0093]
将0.1mol苯并咪唑、0.1mol氢氧化钠和60ml蒸馏水加入至三口烧瓶中,再加入磁力搅拌子,将三口烧瓶与冷凝管连接,之后在氮气保护下、于75℃回流反应12h,反应结束后,将反应后的液体产物立刻采用旋转蒸发仪于80℃真空旋蒸30min除去蒸馏水,然后加入20ml甲醇洗涤并过滤,再次采用旋转蒸发仪于50℃真空旋蒸15min去除甲醇,将旋蒸后的产物于80℃下真空干燥24h,得到白色固体颗粒,即为目标产物催化剂苯并咪唑钠,记为bbmz-na,其红外光谱图和xrd谱图分别示于图1和图2中。
[0094]
实施例2
[0095]
催化剂bbmz-li的制备
[0096]
将0.1mol苯并咪唑、0.1mol氢氧化锂和50ml蒸馏水加入至三口烧瓶中,再加入磁力搅拌子,将三口烧瓶与冷凝管连接,之后在氮气保护下、于80℃回流反应16h,反应结束后,将反应后的液体产物立刻采用旋转蒸发仪于75℃真空旋蒸40min除去蒸馏水,然后加入25ml甲醇洗涤并过滤,再次采用旋转蒸发仪于50℃真空旋蒸15min去除甲醇,将旋蒸后的产物于75℃下真空干燥24h,得到黄色固体颗粒,即为目标产物催化剂苯并咪唑锂,记为bbmz-li,其红外光谱图和xrd谱图分别示于图1和图2中。
[0097]
实施例3
[0098]
催化剂bbmz-k的制备
[0099]
将0.1mol苯并咪唑、0.1mol氢氧化钾和80ml蒸馏水加入至三口烧瓶中,再加入磁力搅拌子,将三口烧瓶与冷凝管连接,之后在氮气保护下、于70℃回流反应24h,反应结束后,将反应后的液体产物立刻采用旋转蒸发仪于80℃真空旋蒸35min除去蒸馏水,然后加入20ml甲醇洗涤并过滤,再次采用旋转蒸发仪于50℃真空旋蒸20min去除甲醇,将旋蒸后的产
物于80℃下真空干燥24h,得到白色固体颗粒,即为目标产物催化剂苯并咪唑钾,记为bbmz-k,其红外光谱图和xrd谱图分别示于图1和图2中。
[0100]
实施例1-3制得的催化剂与苯并咪唑(bbmz)的红外光谱图如图1所示,图中可以看出:在约3063cm-1
处出现弱吸收峰,此峰为苯环上c-h的伸缩振动吸收峰,在约1586cm-1
、1629cm-1
、1479cm-1
、1454cm-1
处出现苯环的c=c骨架振动峰,说明苯环的结构并未被破环;在约1767cm-1
处出现吸收峰,为咪唑环上的c=c的伸缩振动吸收峰,在约1361cm-1
处,为c=n的吸收峰,在约2373cm-1
处为n-h的伸缩振动吸收峰,在约751cm-1
处出现咪唑环弯曲振动峰,说明咪唑结构未被破环,由此表明各实施例所制得的催化剂中均含有苯并咪唑结构。
[0101]
实施例1-3制得的催化剂与苯并咪唑的xrd谱图如图2所示,其中,在约13.24
°
、14.56
°
、18.29
°
、19.45
°
、22.56
°
、23.73
°
、25.67
°
、26.37
°
、27.07
°
、28.93
°
、29.71
°
、30.02
°
、35.23
°
、37.01
°
、37.72
°
、39.51
°
、41.21
°
、42.30
°
、45.96
°
、46.74
°
、48.21
°
、49.61
°
、50.47
°
、52.72
°
、53.97
°
、56.21
°
和58.62
°
处出现衍射峰(2θ),与苯并咪唑的衍射峰相对应;此外,当金属分别为锂、钾、钠时,在2θ约35.85
°
、44.79
°
、52.17
°
和65.15
°
处,约23.81
°
、33.52
°
、41.76
°
、49.77
°
、60.80
°
、63.67
°
、66.71
°
和68.42
°
处,约27.38
°
、29.01
°
、32.35
°
、48.11
°
、52.25
°
、52.37
°
、57.30
°
、60.10
°
和77.28
°
处,出现相应的衍射峰。
[0102]
实施例4
[0103]
将18g碳酸二甲酯和27.6g乙醇加入三口烧瓶中,同时加入0.23g实施例2制得的催化剂bbmz-li,将三口烧瓶与回流冷凝装置连接,用100℃油浴加热三口烧瓶,同时开启搅拌器和回流冷凝装置中的冷却水,调节搅拌转速为80r/min,当三口烧瓶顶部温度稳定在63.7℃时,以回流比为3:1采集馏出液,体系中的液体为釜液。
[0104]
2.5h后结束反应,称量获得的馏出液的质量为m1,利用气相色谱仪获得该馏出液的气相色谱图,并于常压、95℃条件下从釜液中蒸馏采出甲醇、乙醇和碳酸二甲酯,之后于-0.08mpa、95℃条件下继续蒸馏采出碳酸甲乙酯和碳酸二乙酯共沸产物,称量釜液蒸馏物的质量,记为m2,利用气相色谱仪获得该釜液蒸馏物的气相色谱图。根据所述m1、m2以及两张气相色谱图,通过面积归一化法测定产物中含有的组分含量,并计算碳酸二甲酯的转化率以及产物碳酸甲乙酯和碳酸二乙酯的收率。
[0105]
经以上检测和计算,碳酸二甲酯的转化率为55.69%,碳酸甲乙酯的收率为21.46%,碳酸二乙酯的收率为34.23%。
[0106]
最后,将催化剂直接回收,进行下一批次的反应,连续进行上述反应5批次,经检测和计算,最后批次反应的碳酸二甲酯转化率可达到51.12%,碳酸甲乙酯的收率为20.36%,碳酸二乙酯的收率为30.76%。
[0107]
实施例5
[0108]
将18g碳酸二甲酯和18.4g乙醇加入三口烧瓶中,同时加入0.23g实施例2制得的催化剂bbmz-li,将三口烧瓶与回流冷凝装置连接,用100℃油浴加热三口烧瓶,同时开启搅拌器和回流冷凝装置中的冷却水,调节搅拌转速为80r/min,当三口烧瓶顶部温度稳定在63.7℃时,以回流比为3:1采集馏出液,体系中的液体为釜液。
[0109]
2.5h后结束反应,称量获得的馏出液的质量为m1,利用气相色谱仪获得该馏出液的气相色谱图,并于常压、95℃条件下从釜液中蒸馏采出甲醇、乙醇和碳酸二甲酯,之后于-0.08mpa、95℃条件下继续蒸馏采出碳酸甲乙酯和碳酸二乙酯共沸产物,称量釜液蒸馏物的
质量,记为m2,利用气相色谱仪获得该釜液蒸馏物的气相色谱图。根据所述m1、m2以及两张气相色谱图,通过面积归一化法测定产物中含有的组分含量,并计算碳酸二甲酯的转化率以及产物碳酸甲乙酯和碳酸二乙酯的收率。
[0110]
经以上检测和计算,碳酸二甲酯的转化率为52.32%,碳酸甲乙酯的收率为29.11%,碳酸二乙酯的收率为23.21%。
[0111]
实施例6
[0112]
将18g碳酸二甲酯和36.8g乙醇加入三口烧瓶中,同时加入0.23g实施例2制得的催化剂bbmz-li,将三口烧瓶与回流冷凝装置连接,用100℃油浴加热三口烧瓶,同时开启搅拌器和回流冷凝装置中的冷却水,调节搅拌转速为80r/min,当三口烧瓶顶部温度稳定在63.7℃时,以回流比为3:1采集馏出液,体系中的液体为釜液。
[0113]
2.5h后结束反应,称量获得的馏出液的质量(m1)为24.25g,利用气相色谱仪获得该馏出液的气相色谱图(如图3所示,可以看出谱图中含有4个峰,从左到右对应的物质依次为甲醇和乙醇、碳酸二甲酯、碳酸甲乙酯和碳酸二乙酯);并于常压、95℃条件下从釜液中蒸馏采出甲醇、乙醇和碳酸二甲酯,之后于-0.08mpa、95℃条件下继续蒸馏采出碳酸甲乙酯和碳酸二乙酯共沸产物,称量釜液蒸馏物的质量(m2)为30.55g,利用气相色谱仪获得该釜液蒸馏物的气相色谱图(如图4所示,可以看出谱图中含有5个峰,从左到右对应的物质依次为甲醇、乙醇、碳酸二甲酯、碳酸甲乙酯和碳酸二乙酯)。根据m1、m2以及上述两张气相色谱图通过面积归一化法测定产物中含有的组分含量,并计算碳酸二甲酯的转化率以及产物碳酸甲乙酯和碳酸二乙酯的收率,结果如下:
[0114]
未反应的碳酸二甲酯的质量为7.12g(24.25g
×
0.57%+30.55g
×
22.86%);反应得到的碳酸甲乙酯的质量为3.79g(24.25g
×
15.10%+30.55g
×
0.43%);反应得到的碳酸二乙酯的质量为9.92g(24.25g
×
40.91%+30.55g
×
0.01%);进而计算可得:碳酸二甲酯的转化率为60.45%(1-7.12g
÷
18g);碳酸甲乙酯收率为18.22%(3.79g
÷
104g/mol
÷
0.2mol);碳酸二乙酯收率为42.02%(9.92g
÷
118g/mol
÷
0.2g/mol)。
[0115]
实施例7
[0116]
以与实施例4相似的方式合成碳酸甲乙酯和碳酸二乙酯,区别在于:将18g碳酸二甲酯和46g乙醇(此时碳酸二甲酯和乙醇的摩尔比为1:5)加入三口烧瓶中。
[0117]
反应结束后,经检测和计算,碳酸二甲酯的转化率为54.23%,碳酸甲乙酯的收率为11.02%,碳酸二乙酯的收率为43.21%。
[0118]
实施例8
[0119]
以与实施例5相似的方式合成碳酸甲乙酯和碳酸二乙酯,区别在于:加入0.23g实施例1制得的催化剂bbmz-na。
[0120]
反应结束后,经检测和计算,碳酸二甲酯的转化率为52.23%,碳酸甲乙酯的收率为19.58%,碳酸二乙酯的收率为32.65%。
[0121]
实施例9
[0122]
以与实施例5相似的方式合成碳酸甲乙酯和碳酸二乙酯,区别在于:加入0.23g实施例3制得的催化剂bbmz-k。
[0123]
反应结束后,经检测和计算,碳酸二甲酯的转化率为48.62%,碳酸甲乙酯的收率为18.62%,碳酸二乙酯的收率为29.98%。
[0124]
对比例
[0125]
对比例1
[0126]
以与实施例5相似的方式合成碳酸甲乙酯和碳酸二乙酯,区别在于:加入0.23g催化剂乙醇钠。
[0127]
反应结束后,经检测和计算,碳酸二甲酯的转化率为38.23%,碳酸甲乙酯的收率为16.25%,碳酸二乙酯的收率为21.46%。
[0128]
结合对比例1、实施例5和实施例8-9可知,实施例5和实施例8-9使用的催化剂的催化效果明显优于传统催化剂乙醇钠,以实施例5为例,反应转化率由传统催化剂乙醇钠的38.23%提高到52.32%,碳酸甲乙酯和碳酸二乙酯的收率分别为29.11%和23.21%。
[0129]
结合实施例4-7可知,随着乙醇加入量的逐渐增加,碳酸二甲酯转化率先增大再降低,当碳酸二甲酯和乙醇摩尔比为1:4(对应实施例6)时,碳酸二甲酯转化率达到60.45%,此时对应的碳酸甲乙酯和碳酸二乙酯的收率分别为18.22%和42.02%。
[0130]
以上结合优选实施方式和范例性实例对本发明进行了详细说明。不过需要声明的是,这些具体实施方式仅是对本发明的阐述性解释,并不对本发明的保护范围构成任何限制。在不超出本发明精神和保护范围的情况下,可以对本发明技术内容及其实施方式进行各种改进、等价替换或修饰,这些均落入本发明的保护范围内。本发明的保护范围以所附权利要求为准。