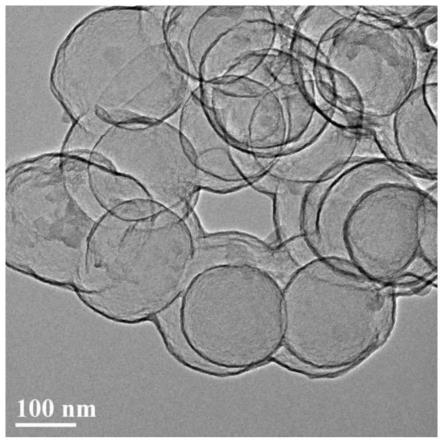
1.本发明属于碳材料控制合成领域,具体涉及一种双层核壳结构的金属单原子氮碳材料及其制备方法和用途。
技术背景
2.掺杂碳材料,因其组分、形貌及孔结构高度可调,已经在能源相关领域如电化学催化、电化学储能、吸附等领域广泛应用。如将丰富的介孔和微孔引入到掺杂碳中,可以极大的提升材料的电容容量。再如使用钴单原子负载的氮掺杂纳米碳材料可以显著提高对于多硫化物的催化转化能力,进而提升锂硫储能电池的容量。目前已经有很多不同金属单原子负载的掺杂碳材料,但大部分只具有简单的形貌结构和一种金属单原子的负载,难以应对目前复杂的催化需求。
3.为了解决上述问题,提出本发明。
技术实现要素:4.本发明第一方面提供一种双层核壳结构的金属单原子氮碳材料,所述金属单原子氮碳材料包括双层球壳状结构,所述双层球壳状结构包括内层、外层和内层外层之间的间隙区域,
5.所述内层为负载有第一金属单原子的氮掺杂碳材料,所述外层为负载有第二金属单原子的氮掺杂碳材料;
6.所述第一金属单原子和第二金属单原子相同或者不同。
7.优选地,所述内层和外层的厚度均为5~20nm,所述外层的尺寸为200~400nm,所述内层的尺寸为80~200nm。
8.优选地,所述第一金属单原子选自铁单原子、镍单原子、铜单原子、钴单原子、锰单原子、钌单原子、钒单原子、锌单原子、钼单原子中的一种;
9.所述第二金属单原子选自铁单原子、镍单原子、铜单原子、钴单原子、锰单原子、钌单原子、钒单原子、锌单原子、钼单原子中的一种。
10.优选地,上述内层和/或外层中,所述氮掺杂碳材料中还掺杂有其他非金属元素,例如硫和/或磷等。
11.上述材料中,第一金属单原子和第二金属单原子作为催化反应的活性位点。优选的,第一金属单原子为铁单原子,所述第二金属单原子为铜单原子;或者第一金属单原子为镍单原子,所述第二金属单原子为钒单原子;或者第一金属单原子为铜单原子,所述第二金属单原子为镍单原子;或者第一金属单原子为钴单原子,所述第二金属单原子为锌单原子;或者第一金属单原子为锰单原子,所述第二金属单原子为钌单原子;或者第一金属单原子为钌单原子,所述第二金属单原子为铁单原子;或者第一金属单原子为钒单原子,所述第二金属单原子为镍单原子;或者第一金属单原子为锌单原子,所述第二金属单原子为钴单原
子;或者第一金属单原子为钼单原子,所述第二金属单原子为锰单原子。
12.本发明中,所述金属单原子氮碳材料的双层球壳状结构中,内层形成内层球,单个或多个内层球或外层包裹。
13.优选地,所述金属单原子氮碳材料还包括包裹双层球壳状结构且从内到外依次排列的第三层到第n层,n大于或等于3。所述第n层为负载有第n金属单原子的氮掺杂碳材料。所述第一金属单原子和第n金属单原子相同或者不同,n大于或等于3。
14.例如,所述金属单原子氮碳材料还包括包裹双层球壳状结构的第三层。所述第三层为负载有第三金属单原子的氮掺杂碳材料。
15.例如,所述金属单原子氮碳材料还包括包裹双层球壳状结构且从内到外依次排列的第三层到第四层。所述第三层为负载有第三金属单原子的氮掺杂碳材料。所述第四层为负载有第四金属单原子的氮掺杂碳材料。
16.例如,所述金属单原子氮碳材料还包括包裹双层球壳状结构且从内到外依次排列的第三层、第四层到第五层。所述第三层为负载有第三金属单原子的氮掺杂碳材料。所述第四层为负载有第四金属单原子的氮掺杂碳材料。所述第五层为负载有第五金属单原子的氮掺杂碳材料。
17.优选地,所述第三金属单原子、第四金属单原子、第五金属单原子、第n金属单原子分别彼此独立的选自铁单原子、镍单原子、铜单原子、钴单原子、锰单原子、钌单原子、钒单原子、锌单原子、钼单原子中的一种,n大于或等于3。
18.本发明第二方面提供第一方面所述的双层核壳结构的金属单原子氮碳材料的制备方法,所述制备方法包括以下步骤:
19.步骤1:将二氧化硅颗粒分散在第一金属盐的甲酰胺溶液中,置于可加热容器中,升温至100~300℃,保持8~24h,反应结束后,固液分离,将得到的固体产物进行干燥,在600~1000℃下煅烧1~5h,得到第一产物;
20.步骤2:取步骤1得到的第一产物分散在氨水的醇水溶液中,在搅拌下和常温下,缓慢滴入正硅酸乙酯的醇水溶液,反应结束后,固液分离,将得到的固体产物干燥后得到第二产物;
21.步骤3:将步骤2得到的第二产物分散到第二金属盐的甲酰胺溶液,然后置于可加热容器中,升温到100~300℃,保持8~48h,反应结束后,固液分离,将得到的固体产物进行干燥,在600~1000℃下煅烧1~5h,得到第三产物;
22.步骤4:将步骤3得到的第三产物与热的碱性溶液混合,除去二氧化硅,固液分离,得到的固体产物干燥后即得到所述双层核壳结构的金属单原子氮碳材料;
23.其中,步骤1和步骤3中,所述甲酰胺溶液彼此独立地为纯甲酰胺的溶液、甲酰胺的硫脲溶液或者甲酰胺的红磷溶液。甲酰胺的硫脲溶液中,硫脲的浓度为0.001-0.05m
24.甲酰胺的红磷溶液中,红磷的浓度为0.001-0.05m。
25.在步骤1和步骤2中,若将一定浓度的金属盐加入到甲酰胺的硫脲或红磷溶液中,则可得到硫或磷掺杂的双层核壳材料。
26.优选地,所述步骤1中,所述第一金属盐的甲酰胺溶液中,第一金属盐的浓度为0.001-0.05m。
27.所述二氧化硅颗粒和第一金属盐的甲酰胺溶液的比例不限,例如为0.1g:30ml。
28.优选地,所述二氧化硅颗粒为球形二氧化硅颗粒。
29.优选地,所述步骤2中,其中,所述正硅酸乙酯的醇水溶液中,正硅酸乙酯的浓度为0.01-0.5ml/l。醇水溶液中,醇和水体积比不限,例如为3:1;
30.所述正硅酸乙酯的滴入时间为1-12h。本发明中,控制正硅酸乙酯的醇水溶液中正硅酸乙酯的浓度以及正硅酸乙酯的醇水溶液的滴入时间以控制二氧化硅可以成功的包覆在内层上。
31.步骤1得到的第一产物与氨水的醇水溶液的比例不限,例如为0.1g:50ml。
32.优选地,所述步骤3中,所述第二金属盐的甲酰胺溶液中,第二金属盐的浓度为0.001-0.05m。
33.步骤2得到的第二产物与第二金属盐的甲酰胺溶液的比例不限,例如为0.1g:30ml。
34.优选地,所述步骤3中,所述第一金属盐为硝酸盐或氯化盐;所述第二金属盐为硝酸盐或氯化盐;所述第一金属盐中的第一金属选自铁、镍、铜、钴、锰、钌、钒、锌、钼中的一种;所述第二金属盐中的第二金属选自铁、镍、铜、钴、锰、钌、钒、锌、钼中的一种。
35.所述步骤1和3中的升温至100~300℃,保持8~48h;更优选为升温至160~200℃,保持8~24h。
36.本发明中,通过控制第一金属盐浓度以控制内层的厚度,通过控制第二金属盐浓度以控制外层的厚度。
37.优选地,所述步骤1、步骤2、步骤3中分散的手段包括手动振荡、机械振荡、超声、搅拌等;更优选方案为超声。
38.优选地,所述步骤1、步骤3中,所述可加热容器为耐热性较好的安全容器,如烧瓶、聚四氟乙烯反应釜等。更优选方案中使用聚四氟乙烯反应釜承载反应。
39.优选地,所述步骤1、步骤2、步骤3、步骤4中,所述固液分离的手段包括离心、过滤、静置沉降等。更优选方案使用离心,以提高时间效率。
40.优选地,所述金属单原子氮碳材料还包括包裹双层球壳状结构且从内到外依次排列的第三层到第n层,n大于或等于3时,所述制备方法包括以下步骤:
41.步骤1:将二氧化硅颗粒分散在第一金属盐的甲酰胺溶液中,置于可加热容器中,升温至100~300℃,保持8~48h,反应结束后,固液分离,将得到的固体产物进行干燥,在600~1000℃下煅烧1~5h,得到第一产物;
42.步骤2:取步骤1得到的第一产物分散在氨水的醇水溶液中,在搅拌下和常温下,缓慢滴入正硅酸乙酯的醇水溶液,反应结束后,固液分离,将得到的固体产物干燥后得到第二产物;
43.步骤3:将步骤2得到的第二产物分散到第二金属盐的甲酰胺溶液,然后置于可加热容器中,升温到100~300℃,保持8~48h,反应结束后,固液分离,将得到的固体产物进行干燥,在600~1000℃下煅烧1~5h,得到第三产物;
44.步骤4:重复所述步骤2和步骤3n-3次;
45.步骤5:将步骤4得到的产物与碱性溶液混合,除去二氧化硅,固液分离,得到的固体产物干燥后即得到所述双层核壳结构的金属单原子氮碳材料;
46.其中,步骤1、步骤3和步骤4中,所述甲酰胺溶液彼此独立地为纯甲酰胺的溶液、甲
酰胺的硫脲溶液或者甲酰胺的红磷溶液。
47.例如,步骤4:重复所述步骤2和步骤3一次,得到第四产物。上述重复所述步骤2和步骤3一次的具体方法是:
48.取上述步骤3得到的第三产物分散在氨水的醇水溶液中,在搅拌下和常温下,缓慢滴入正硅酸乙酯的醇水溶液,反应结束后,固液分离,将得到的固体产物干燥后得到第四产物;
49.将得到的第四产物分散到第三金属盐的甲酰胺溶液,然后置于可加热容器中,升温到100~300℃,保持8~48h,反应结束后,固液分离,将得到的固体产物进行干燥,在600~1000℃下煅烧1~5h,得到第五产物;
50.将第五产物与碱性溶液混合,除去二氧化硅,固液分离,得到的固体产物干燥后即得到所述双层核壳结构的金属单原子氮碳材料。此时,所述金属单原子氮碳材料还包括包裹双层球壳状结构的第三层。所述第三层为负载有第三金属单原子的氮掺杂碳材料。
51.本发明的有益效果如下:
52.1、本发明的材料具有明确双层结构,且具有不同金属单原子活性位点的催化剂为具有多种中间体的多步催化反应提供了更好的解决方案。
53.具体表现为,在多步催化反应中,各个步骤的反应中间体常常需要适配不同的金属单原子活性位点才能实现最大化的催化性能,而本发明开发的材料第一次实现了在一个连续催化反应中对不同中间体在活性位点上的吸附行为的分别优化,以达到最佳的整体催化性能。
54.2、本发明的制备策略为,利用二氧化硅作为硬模板,基于甲酰胺的席夫碱反应即甲酰胺中的亲核基团(-nh2)对于亲电基团(c=o)的指向性进攻,完成c=n偶联,在二氧化硅表面形成碳氮材料的包覆层,并在反应中利用其较高的氮含量耦合金属并煅烧使其稳定锚定,再在该包覆层上生长二氧化硅作为新的模板和隔离层并再次包覆,煅烧,洗去二氧化硅后即可得到双层核壳结构的金属单原子氮碳材料。
55.其具体的优势为,所得到的具有较高氮含量的金属氮碳表面解决了传统纯碳表面疏水且无法再次实现二氧化硅生长的问题,再次生长的二氧化硅作为致密隔断,阻隔了外层金属氮碳材料的合成中对内层的干扰,实现了内外层金属单原子负载的独立性。该方法所需设备简单,低毒,适合实验室研究及工业生产。
56.3、本发明的方法可以对掺杂碳材料进行形貌、负载金属元素方面的控制。本发明的材料在锂硫电池领域中具有重要的应用。
附图说明
57.图1为实施例1制备的cu-nc@fe-nsc双层核壳材料的x射线粉晶衍射图样(纵坐标ir:相对衍射强度)。
58.图2为实施例1制备的cu-nc@fe-nsc双层核壳材料的透射电子显微镜照片。
59.图3为实施例1制备的cu-nc@fe-nsc双层核壳材料的x射线能谱,插图为其元素含量。
60.图4为实施例2制备的v-nc@ni-nc双层核壳材料的x射线粉晶衍射图样(纵坐标ir:相对衍射强度)。
61.图5为实施例2制备的v-nc@ni-nc双层核壳材料的透射电子显微镜照片。
62.图6为实施例2制备的v-nc@ni-nc双层核壳材料的x射线能谱,插图为其元素含量。
63.图7为实施例3制备的ni-npc@cu-nc双层核壳材料的x射线粉晶衍射图样(纵坐标ir:相对衍射强度)。
64.图8为实施例3制备的ni-npc@cu-nc双层核壳材料的透射电子显微镜照片。
65.图9为实施例3制备的ni-npc@cu-nc双层核壳材料的x射线能谱,插图为其元素含量。
66.图10为实施例4制备的zn-nc@co-nc双层核壳材料的x射线粉晶衍射图样(纵坐标ir:相对衍射强度)。
67.图11为实施例4制备的zn-nc@co-nc双层核壳材料的透射电子显微镜照片。
68.图12为实施例4制备的zn-nc@co-nc双层核壳材料的x射线能谱,插图为其元素含量。
69.图13为实施例4制备的zn-nc@co-nc双层核壳材料的透射电子显微镜元素分布图照片。
70.图14为实施例4制备的zn-nc@co-nc双层核壳材料中co元素的x射线吸收近边结构谱。
71.图15为实施例4制备的zn-nc@co-nc双层核壳材料中co元素的傅里叶变换扩展x射线精细结构谱。
72.图16为实施例4制备的zn-nc@co-nc双层核壳材料中co元素的傅里叶变换扩展x射线精细结构拟合谱,插图为其精细结构示意图。
73.图17为实施例4制备的zn-nc@co-nc双层核壳材料中zn元素的x射线吸收近边结构谱。
74.图18为实施例4制备的zn-nc@co-nc双层核壳材料中zn元素的傅里叶变换扩展x射线精细结构谱。
75.图19为实施例4制备的zn-nc@co-nc双层核壳材料中zn元素的傅里叶变换扩展x射线精细结构拟合谱,插图为其精细结构示意图。
76.图20为实施例5制备的ru-nc@mn-nc双层核壳材料的x射线粉晶衍射图样(纵坐标ir:相对衍射强度)。
77.图21为实施例5制备的ru-nc@mn-nc双层核壳材料的透射电子显微镜照片。
78.图22为实施例5制备的ru-nc@mn-nc双层核壳材料的x射线能谱,插图为其元素含量。
79.图23为实施例6制备的fe-nc@ru-nc双层核壳材料的x射线粉晶衍射图样(纵坐标ir:相对衍射强度)。
80.图24为实施例6制备的fe-nc@ru-nc双层核壳材料的透射电子显微镜照片。
81.图25为实施例6制备的fe-nc@ru-nc双层核壳材料的x射线能谱,插图为其元素含量。
82.图26为实施例7制备的ni-nc@v-npc双层核壳材料的x射线粉晶衍射图样(纵坐标ir:相对衍射强度)。
83.图27为实施例7制备的ni-nc@v-npc双层核壳材料的透射电子显微镜照片。
84.图28为实施例7制备的ni-nc@v-npc双层核壳材料的x射线能谱,插图为其元素含量。
85.图29为实施例8制备的co-nc@zn-nc双层核壳材料的x射线粉晶衍射图样(纵坐标ir:相对衍射强度)。
86.图30为实施例8制备的co-nc@zn-nc双层核壳材料的透射电子显微镜照片。
87.图31为实施例7制备的co-nc@zn-nc双层核壳材料的x射线能谱,插图为其元素含量。
88.图32为实施例8制备的co-nc@zn-nc双层核壳材料的透射电子显微镜元素分布图照片。
89.图33为实施例9制备的mn-nsc@mo-nc双层核壳材料的x射线粉晶衍射图样(纵坐标ir:相对衍射强度)。
90.图34为实施例9制备的mn-nsc@mo-nc双层核壳材料的透射电子显微镜照片。
91.图35为实施例7制备的mn-nsc@mo-nc双层核壳材料的x射线能谱,插图为其元素含量。
92.图36为以金属锂作为负极,以实施例4所得样品zn-nc@co-nc作为正极装配扣式电池的循环伏安曲线。
93.图37为以金属锂作为负极,以实施例4所得样品zn-nc@co-nc作为正极装配扣式电池的倍率性能
94.图38为以金属锂作为负极,以实施例4所得样品zn-nc@co-nc作为正极装配扣式电池的长循环性能以及库伦效率。
95.图39为根据密度泛函理论计算得到的多硫化物分别在拟合的co-n4和zn-n4位点上的结合能。
96.图40为以金属锂作为负极,以实施例8所得样品co-nc@zn-nc作为正极装配扣式电池的循环伏安曲线。
97.图41为以金属锂作为负极,以实施例8所得样品co-nc@zn-nc作为正极装配扣式电池的倍率性能。
98.图42为以金属锂作为负极,以实施例8所得样品co-nc@zn-nc作为正极装配扣式电池的长循环性能以及库伦效率。
99.图43为以金属锂作为负极,以对比例1样品co-nc作为正极装配扣式电池的循环伏安曲线。
100.图44为以金属锂作为负极,以对比例1样品co-nc作为正极装配扣式电池的倍率性能。
101.图45为以金属锂作为负极,以对比例1样品co-nc作为正极装配扣式电池的长循环性能以及库伦效率。
102.图46为以金属锂作为负极,以对比例2样品zn-nc作为正极装配扣式电池的循环伏安曲线。
103.图47为以金属锂作为负极,以对比例2样品zn-nc作为正极装配扣式电池的倍率性能。
104.图48为以金属锂作为负极,以对比例2样品zn-nc作为正极装配扣式电池的长循环
性能以及库伦效率。
具体实施方式
105.实施例中球形二氧化硅颗粒尺寸约100nm。
106.实施例1
107.一种双层核壳结构的金属单原子氮碳材料的制备步骤如下:
108.步骤1:将0.1g球形二氧化硅颗粒超声分散在30毫升,浓度为0.01m的硝酸铁的甲酰胺硫脲溶液中(硫脲浓度为0.001m),置于聚四氟乙烯反应釜中,升温至160℃,保持24小时,反应结束后,通过离心将固液分离,将固体产物进行干燥,在800℃下煅烧3小时,产物记为fe-nsc@sio2。
109.步骤2:取0.1g的fe-nsc@sio2超声分散在50毫升、20ml/l的氨水的醇水(醇水体积比为3:1)溶液中,在常温下,在3小时内匀速缓慢滴入10毫升、0.1ml/l的正硅酸乙酯的醇水(醇水体积比为3:1)溶液,反应结束后,通过离心分离固体产物,干燥后得到产物记为sio2@fe-nsc@sio2。
110.步骤3:将0.1gsio2@fe-nsc@sio2超声分散在30毫升、浓度为0.01m的硝酸铜的甲酰胺溶液中,置于聚四氟乙烯反应釜中,升温至180℃,保持12小时,反应结束后,通过离心将固液分离,将固体产物进行干燥,在600℃下煅烧5小时得到产物cu-nc@sio2@fe-nsc@sio2;
111.步骤4:将步骤三所得产物0.2gcu-nc@sio2@fe-nsc@sio2与100ml浓碱溶液(6m的氢氧化钠溶液)混合反应12小时,除去二氧化硅。通过离心分离固体产物,干燥后即得到最终产物,记为cu-nc@fe-nsc。
112.实施例2
113.一种双层核壳结构的金属单原子氮碳材料的制备步骤如下:
114.步骤1:将0.1g球形二氧化硅颗粒超声分散在30毫升、浓度为0.01m的硝酸镍的甲酰胺溶液中,置于聚四氟乙烯反应釜中,升温至180℃,保持12小时,反应结束后,通过离心将固液分离,将固体产物进行干燥,在800℃下煅烧3小时,产物记为ni-nc@sio2;
115.步骤2:取0.1gni-nc@sio2超声分散在50毫升、20ml/l的氨水的醇水(醇水体积比为3:1)溶液中,在常温下,在3小时内匀速缓慢滴入10毫升,0.1ml/l的正硅酸乙酯的醇水(醇水体积比为3:1)溶液,反应结束后,通过离心分离固体产物,干燥后得到产物记为sio2@ni-nc@sio2;
116.步骤3:将0.1gsio2@ni-nc@sio2超声分散在30毫升、浓度为0.01m的氯化钒的甲酰胺溶液中,置于聚四氟乙烯反应釜中,升温至180℃,保持12小时,反应结束后,通过离心将固液分离,将固体产物进行干燥,在800℃下煅烧3小时得到产物v-nc@sio2@ni-nc@sio2;
117.步骤4:将步骤三所得产物0.2gv-nc@sio2@ni-nc@sio2与100ml浓碱溶液(6m的氢氧化钠溶液)混合反应12小时除去二氧化硅。通过离心分离固体产物,干燥后即得到最终产物记为v-nc@ni-nc。
118.实施例3
119.一种双层核壳结构的金属单原子氮碳材料的制备步骤如下:
120.步骤1:将0.1g球形二氧化硅颗粒超声分散在30毫升,浓度为0.05m的硝酸铜的甲酰胺溶液中,置于聚四氟乙烯反应釜中,升温至200℃,保持8小时,反应结束后,通过离心将
固液分离,将固体产物进行干燥,在800℃下煅烧3小时,产物记为cu-nc@sio2;
121.步骤2:取0.1gcu-nc@sio2超声分散在50毫升,20ml/l的氨水的醇水(醇水体积比为3:1)溶液中,在常温下,在3小时内匀速缓慢滴入10毫升,0.01ml/l的正硅酸乙酯的醇水(醇水体积比为3:1)溶液,反应结束后,通过离心分离固体产物,干燥后得到产物记为sio2@cu-nc@sio2;
122.步骤3:将0.1gsio2@cu-nc@sio2超声分散在30毫升,浓度为0.01m(硝酸镍的浓度为0.01m)的硝酸镍的甲酰胺红磷溶液中(红磷浓度为0.001m),置于聚四氟乙烯反应釜中,升温至180℃,保持12小时,反应结束后,通过离心将固液分离,将固体产物进行干燥,在1000℃下煅烧1小时得到产物ni-npc@sio2@cu-nc@sio2;
123.步骤4:将步骤三所得产物0.2gni-npc@sio2@cu-nc@sio2与100ml浓碱(6m的氢氧化钠溶液)混合反应12小时,除去二氧化硅。通过离心分离固体产物,干燥后即得到最终产物记为ni-npc@cu-nc。
124.实施例4
125.一种双层核壳结构的金属单原子氮碳材料的制备步骤如下:
126.步骤1:将0.1g球形二氧化硅颗粒超声分散在30毫升、浓度为0.01m的硝酸钴的甲酰胺溶液中,置于聚四氟乙烯反应釜中,升温至180℃,保持12小时,反应结束后,通过离心将固液分离,将固体产物进行干燥,在800℃下煅烧3小时,产物记为co-nc@sio2。
127.步骤2:取0.1gco-nc@sio2超声分散在50毫升、20ml/l的氨水的醇水(醇水体积比为3:1)溶液中,在常温下,在3小时内匀速缓慢滴入10毫升,0.1ml/l的正硅酸乙酯的醇水(醇水体积比为3:1)溶液,反应结束后,通过离心分离固体产物,干燥后得到产物记为sio2@co-nc@sio2。
128.步骤3:将0.1gsio2@co-nc@sio2超声分散在30毫升、浓度为0.01m的硝酸锌的甲酰胺溶液中,置于聚四氟乙烯反应釜中,升温至180℃,保持12小时,反应结束后,通过离心将固液分离,将固体产物进行干燥,在800℃下煅烧3小时得到产物zn-nc@sio2@co-nc@sio2;
129.步骤4:将步骤三所得产物0.2gzn-nc@sio2@co-nc@sio2与100ml浓碱溶液(6m的氢氧化钾溶液)混合反应12小时,除去二氧化硅。通过离心分离固体产物,干燥后即得到最终产物记为zn-nc@co-nc。
130.实施例5
131.一种双层核壳结构的金属单原子氮碳材料的制备步骤如下:
132.步骤1:将0.1g球形二氧化硅颗粒超声分散在30毫升、浓度为0.01m的硝酸锰的甲酰胺溶液中,置于聚四氟乙烯反应釜中,升温至180℃,保持12小时,反应结束后,通过离心将固液分离,将固体产物进行干燥,在600℃下煅烧5小时,产物记为mn-nc@sio2。
133.步骤2:取0.1.gmn-nc@sio2超声分散在50毫升、20ml/l的氨水的醇水(醇水体积比为3:1)溶液中,在常温下,在1小时内匀速缓慢滴入10毫升、0.1ml/l的正硅酸乙酯的醇水(醇水体积比为3:1)溶液,反应结束后,通过离心分离固体产物,干燥后得到产物记为sio2@mn-nc@sio2。
134.步骤3:将0.1gsio2@mn-nc@sio2超声分散在30毫升、浓度为0.001m的氯化钌的甲酰胺溶液中,置于聚四氟乙烯反应釜中,升温至180℃,保持12小时,反应结束后,通过离心将固液分离,将固体产物进行干燥,在800℃下煅烧3小时得到产物ru-nc@sio2@mn-nc@sio2;
135.步骤4:将步骤三所得产物0.2gru-nc@sio2@mn-nc@sio2与100ml浓碱溶液(6m的氢氧化钾溶液)混合反应12小时,除去二氧化硅。通过离心分离固体产物,干燥后即得到最终产物记为ru-nc@mn-nc。
136.实施例6
137.一种双层核壳结构的金属单原子氮碳材料的制备步骤如下:
138.步骤1:将0.1g球形二氧化硅颗粒超声分散在30毫升,浓度为0.01m的氯化钌的甲酰胺溶液中,置于聚四氟乙烯反应釜中,升温至180℃,保持12小时,反应结束后,通过离心将固液分离,将固体产物进行干燥,在800℃下煅烧3小时,产物记为ru-nc@sio2;
139.步骤2:取0.1gru-nc@sio2超声分散在50毫升、20ml/l的氨水的醇水(醇水体积比为3:1)溶液中,在常温下,在3小时内匀速缓慢滴入10毫升,0.5ml/l的正硅酸乙酯的醇水(醇水体积比为3:1)溶液,反应结束后,通过离心分离固体产物,干燥后得到产物记为sio2@ru-nc@sio2;
140.步骤3:将0.1gsio2@ru-nc@sio2超声分散在30毫升、浓度为0.01m的硝酸铁的甲酰胺溶液中,置于聚四氟乙烯反应釜中,升温至180℃,保持12小时,反应结束后,通过离心将固液分离,将固体产物进行干燥,在800℃下煅烧3小时得到产物fe-nc@sio2@ru-nc@sio2;
141.步骤4:将步骤三所得产物0.2gfe-nc@sio2@ru-nc@sio2与100ml浓碱溶液(6m的氢氧化钾溶液)混合反应12小时,除去二氧化硅。通过离心分离固体产物,干燥后即得到最终产物记为fe-nc@ru-nc。
142.实施例7
143.一种双层核壳结构的金属单原子氮碳材料的制备步骤如下:
144.步骤1:将0.1g球形二氧化硅颗粒超声分散在30毫升、浓度为0.01m的氯化钒的甲酰胺红磷溶液中(红磷浓度为0.01m),置于聚四氟乙烯反应釜中,升温至180℃,保持12小时,反应结束后,通过离心将固液分离,将固体产物进行干燥,在1000℃下煅烧1小时,产物记为v-npc@sio2;
145.步骤2:取0.1gv-npc@sio2超声分散在50毫升、20ml/l的氨水的醇水(醇水体积比为3:1)溶液中,在常温下,在12小时内匀速缓慢滴入10毫升,0.1ml/l的正硅酸乙酯的醇水(醇水体积比为3:1)溶液,反应结束后,通过离心分离固体产物,干燥后得到产物记为sio2@v-npc@sio2;
146.步骤3:将0.1gsio2@v-npc@sio2超声分散在30毫升、浓度为0.05m的硝酸镍的甲酰胺溶液中,置于聚四氟乙烯反应釜中,升温至160℃,保持24小时,反应结束后,通过离心将固液分离,将固体产物进行干燥,在800℃下煅烧3小时得到产物ni-nc@sio2@v-npc@sio2;
147.步骤4:将步骤三所得产物0.2gni-nc@sio2@v-npc@sio2与100ml浓碱溶液(6m的氢氧化钾溶液)混合反应12小时,除去二氧化硅。通过离心分离固体产物,干燥后即得到最终产物记为ni-nc@v-npc。
148.实施例8
149.一种双层核壳结构的金属单原子氮碳材料的制备步骤如下:
150.步骤1:将0.1g球形二氧化硅颗粒超声分散在30毫升、浓度为0.01m的硝酸锌的甲酰胺溶液中,置于聚四氟乙烯反应釜中,升温至180℃,保持12小时,反应结束后,通过离心将固液分离,将固体产物进行干燥,在800℃下煅烧3小时,产物记为zn-nc@sio2;
20nm,因此综合,内层和外层的厚度约为5-20nm。
164.其中实施例4和8的以co在内层zn在外层和zn在内层co在外层的透射电子显微镜元素分布图照片说明了内外层金属元素的独立分布性,即内层只有co单原子且外层只有zn单原子(实施例4,附图13),和内层只有zn单原子且外层只有co单原子(实施例8,附图32)。
165.进一步地,附图14说明了实施例4所合成的样品与作为标准样的肽箐钴(copc)类似,co处于氧化态,且价态处于零价的标准样钴单质(co-foil)与标准样四氧化三钴(co3o4)之间。与之相邻的第一壳层的氮原子与钴原子间距约为0.19nm(附图15)与标准样的肽箐钴和四氧化三钴接近,小于标准样钴单质,附图16中插图的结构与所测样品结构拟合较好,进一步说明实施例4所合成的样品中co原子为单分散形式存在。附图17说明了实施例4所合成的样品中与作为标准样的肽箐锌(znpc)类似,zn处于氧化态,且价态处于零价的标准样锌单质(zn-foil)与标准样氧化锌(zno)之间。与之相邻的第一壳层的氮原子与钴原子间距约为0.17nm(附图18)与标准样的肽箐锌和氧化锌接近,小于标准样锌单质,附图19中插图的结构与所测样品结构拟合较好,进一步说明实施例4所合成的样品中zn原子为单分散形式存在。
166.应用例1
167.以金属锂作为负极,以实施例4所得的zn-nc@co-nc双层核壳材料作为正极装配扣式电池,在电池测试仪上进行反复充放电循环,实验中采取的正极片上硫的担载量为2mg cm-2
。循环伏安曲线是在电压范围为1.7-2.8v,扫速为0.1mvs-1
的条件下测得。
168.如附图36所示,在放电/还原阶段出现的峰(2.02v)说明了硫向短链多硫化物的转化,在氧化反应阶段,出现在2.32v和2.4v的两个峰对应了硫化锂和多硫化锂的脱锂化过程。氧化和还原之间的较窄的电位窗口说明了zn-nc@co-nc材料对于多硫化物催化转化优异的性能。
169.附图37展示了不同倍率下zn-nc@co-nc的性能测试。在此,我们定义1c为1675mah g-1
,其含义为锂硫电池中单质硫在1小时完全放电/锂化形成硫化锂的放电倍率。在0.2c下,zn-nc@co-nc电极能够放出超过1075mahg-1
的超高容量,在2c和4c的放电条件下,也依然存有约846mahg-1
和766mahg-1
的实际比容量,这表明了以双层核壳zn-nc@co-nc材料作为正极装配的锂硫电池具有优异的倍率性能。
170.附图38为以zn-nc@co-nc材料作为正极装配的锂硫电池的循环测试性能,其具有超高的初始放电比容量,为1185mahg-1
,在500次循环中,每个循环只有0.063%的超低的容量衰减率,再一次说明了以双层核壳zn-nc@co-nc材料作为锂硫电池正极优越的性能。
171.附图39为根据密度泛函理论计算得到的多硫化物分别在拟合的co-n4和zn-n4位点上的结合能。如图所示,对于长链多硫化物如s8,li2s8,li2s6,co-nc位点具有比zn-nc更高的结合能,更容易发生催化反应。相反,zn-nc比co-nc对于短链多硫化物,即li2s4,li2s2和li2s,有更好的吸附作用,所以将co-nc置于内层,zn-nc置于外层是符合锂硫电池中单质硫由内向外逐层催化转化的规律的,即被封装于双层核壳结构最内层的硫单质先经过co-nc位点被催化转化为li2s6,再扩散迁移到zn-nc位点上被催化转化为li2s进而完成整个催化转化反应。
172.应用例2
173.以金属锂作为负极,以实施例8所得样品co-nc@zn-nc作为正极装配扣式电池,在
电池测试仪上进行反复充放电循环,实验中采取的正极片上硫的担载量为2mgcm-2
。。循环伏安曲线是在电压范围为1.7-2.8v,扫速为0.1mvs-1
的条件下测得。
174.如附图40所示,在放电/还原阶段出现的峰(2.02v)说明了硫向短链多硫化物的转化,在氧化反应阶段,出现在2.36v和2.42v的两个峰对应了硫化锂和多硫化锂的脱锂化过程。氧化和还原之间的电位窗口说明了co-nc@zn-nc材料对于多硫化物催化转化优异的性能,相比较于实施例4的zn-nc@co-nc材料,该窗口更宽,说明了co单原子催化剂在内层zn单原子催化剂在外层的排布更有利于多硫化物由长链向短链直到变为li2s的整个催化转化过程。
175.附图41展示了不同倍率下co-nc@zn-nc的性能测试。在0.2c下,co-nc@zn-nc电极能够放出超过1004mahg-1
的容量,在2c和4c的放电条件下,也依然存有约774mahg-1
和694mahg-1
的实际比容量,这表明了以双层核壳co-nc@zn-nc材料作为正极装配的锂硫电池也具有优异的倍率性能,与实施例4的zn-nc@co-nc材料相比较低,这说明了co在内层,zn在外层的重要性。
176.附图42为以双层核壳co-nc@zn-nc材料作为正极装配的锂硫电池的循环测试性能,其具有超高的初始放电比容量,为1155mahg-1
,在500次循环中,每个循环有0.072%的较低的容量衰减率,再一次说明了co在内层zn在外层结构对于多硫化物连续催化转化的重要性。
177.对比例1
178.实施例4中,跳过步骤3,直接将步骤2所得产品进行步骤4的碱洗过程,可得到co-nc单层核壳材料。以金属锂作为负极,以co-nc单层核壳材料作为正极装配扣式电池,在电池测试仪上进行反复充放电循环,实验中采取的正极片上硫的担载量为2mgcm-2
。循环伏安曲线是在电压范围为1.7-2.8v,扫速为0.1mvs-1
的条件下测得。
179.如附图43所示,在放电/还原阶段出现的峰(2.00v)说明了硫向短链多硫化物的转化,在氧化反应阶段,出现在2.44v的氧化峰对应了多硫化锂的脱锂化过程。氧化和还原之间的电位窗口说明了co-nc材料可以实现多硫化物的催化转化,相比较于实施例4和实施例8中的双层材料,该窗口更宽,说明了单层co-nc材料虽然可以实现多硫化物的催化转化,但是性能并不够好。
180.附图44展示了不同倍率下co-nc的性能测试。在0.2c下,co-nc电极能够放出超过875mah g-1
的容量,在2c和4c的放电条件下,也依然存有约600mah g-1
和510mah g-1
的实际比容量,这表明了以单层核壳co-nc材料作为正极装配的锂硫电池也具有较好的倍率性能,但是大幅低于实施例4和实施例8中材料的倍率性能,这说明了双层核壳结构在对硫化物催化转化中的重要作用。
181.附图45为以单层核壳co-nc材料作为正极装配的锂硫电池的循环测试性能,其较好的初始放电比容量,为900mah g-1
,在500次循环中,每个循环有0.104%的容量衰减率,再一次说明了双层核壳结构对于多硫化物连续催化转化的重要性。
182.对比例2
183.实施例8中,跳过步骤3,直接将步骤2所得产品进行步骤4的碱洗过程,可得到zn-nc单层核壳材料。以金属锂作为负极,以zn-nc单层核壳材料作为正极装配扣式电池,在电池测试仪上进行反复充放电循环,实验中采取的正极片上硫的担载量为2mg cm-2
。循环伏安
曲线是在电压范围为1.7-2.8v,扫速为0.1mvs-1
的条件下测得。
184.如附图46所示,在放电/还原阶段出现的峰(1.98v)说明了硫向短链多硫化物的转化,在氧化反应阶段,出现在2.44v的氧化峰对应了多硫化锂的脱锂化过程。氧化和还原之间的电位窗口说明了zn-nc材料可以实现多硫化物的催化转化,相比较于实施例4和实施例8中的双层材料,该窗口更宽,说明了单层zn-nc材料虽然可以实现多硫化物的催化转化,但是性能并不够好。
185.附图47展示了不同倍率下zn-nc的性能测试。在0.2c下,zn-nc电极能够放出超过777mah g-1
的容量,在2c和4c的放电条件下,也依然存有约538mah g-1
和456mah g-1
的实际比容量,这表明了以单层核壳zn-nc材料作为正极装配的锂硫电池也具有较好的倍率性能,但是大幅低于实施例4和实施例8中材料的倍率性能,这说明了双层核壳结构在对硫化物催化转化中的重要作用。
186.附图48为以单层核壳zn-nc材料作为正极装配的锂硫电池的循环测试性能,其较好的初始放电比容量,为832mah g-1
,在500次循环中,每个循环有0.118%的容量衰减率,再一次说明了双层核壳结构对于多硫化物连续催化转化的重要性。