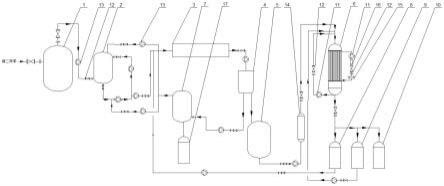
1.本实用新型涉及化工技术领域,特别涉及一种间苯二甲胺生产系统。
背景技术:2.间苯二甲胺又称1,3-苯二甲胺、间二甲氨基苯、1,3-二甲氨基苯等,分子式为c8h
12
n2,密度为1.032g/cm3,熔点为14℃(lit.),沸点为247.0
±
0.0℃ at 760mmhg,常温下为无色至黄色液体。间苯二甲胺是一种重要的化工原料,主要用作环氧树脂固化剂,间苯二甲胺还可以作为光敏塑料、橡胶助剂、聚氨酯树脂、涂料生产原料及尼龙改性用聚合物单体。间苯二甲胺制得的环氧树脂固化剂固化性能优异,耐热性、耐水性和耐化学腐蚀性好,能够得到透明且表面极光滑的固化树脂。以间苯二甲胺为改性单体制得的新型尼龙树脂-间二甲苯尼龙树脂具有良好的抗透氧性和抗二氧化碳流失性。间苯二甲胺还可以用来合成聚氨酯的单体-间二甲苯二氰酸酯。与目前常用的二苯基甲烷二异氰酸酯相比,以间苯二甲胺为原料合成的间二甲苯二氰酸酯产品不易泛黄,干燥时间短,可得到硬度高、稳定性好的漆膜。此外,间苯二甲胺在橡胶制品、农药、纤维整理剂、防锈剂、螯合剂、润滑剂、纸张及电子产品行业均有广泛的应用,是目前国内需重点发展的精细石油化学品。
3.间苯二甲胺制取主要采用以间苯二甲腈为原料,经催化加氢制得。然而,采用现有的设备生产高纯度间苯二甲胺,存在生产能耗高、三废产生量大、萃取剂分离不彻底、操作复杂等缺陷。
技术实现要素:4.有鉴于此,本实用新型的目的在于提供一种间苯二甲胺生产系统,用于解决采用现有设备生产高纯度间苯二甲胺,存在生产能耗高、三废产生量大、萃取剂分离不彻底、操作复杂等缺陷的技术问题。
5.为解决上述技术问题,本技术提供一种间苯二甲胺生产系统,包括依次连通的氨氧化反应器、吸收塔、悬浮结晶器和固液分离机构,所述固液分离机构底部设置有固相出口和液相出口,所述固相出口连通有加氢反应器,所述加氢反应器位于所述固液分离机构下方,所述加氢反应器的出液端连通有熔融结晶器。
6.本技术的生产系统的工作原理为:通过悬浮结晶器对中间产品间苯二甲腈进行提纯,并通过熔融结晶器对间苯二甲胺进行提纯,能够将间苯二甲胺的纯度提高至99.9%以上,满足医药级、食品级的应用需求,且降低能耗,缩短时间。
7.可选地,所述间苯二甲胺生产系统还包括脱溶塔,所述脱溶塔的进液端连通所述液相出口,所述脱溶塔的气相出口连通所述吸收。
8.本技术通过增设脱溶塔,并将脱溶塔的进液端连通液相出口,将脱溶塔的气相出口连通吸收塔,能够回收经固液分离机构固液分离后得到的液体中的溶剂,并将回收得到的溶剂送入吸收塔中进行重复利用,提高溶剂的利用效率,降低生产成本。
9.可选地,所述熔融结晶器采用降膜结晶器。
10.可选地,所述熔融结晶器设置有物料进口、物料出口、冷热媒进口和冷热媒出口,所述物料进口连通所述加氢反应器的出液端,所述物料出口经物料循环管道连通所述物料进口,所述物料循环管道上设置有循环泵。
11.本技术通过将熔融结晶器的物料进口经物料循环管道连通熔融结晶器的物料进口,能够将含间苯二甲胺的溶液中未结晶物料再次送入熔融结晶器中,以使含间苯二甲胺的溶液中未结晶物料作为下一次结晶原料,进而提高间苯二甲胺的收率。
12.可选地,所述物料出口连通有母液罐,所述母液罐经管道连通所述悬浮结晶器的进料口。
13.本技术通过将物料出口连通母液罐,并将母液罐通悬浮结晶器的进料口,能够将结晶过程中得到的母液(结晶后残余溶液,母液中含少量间苯二甲胺),进而将熔融结晶器的物料出口排出的母液送入悬浮结晶器中进行结晶,以回收母液中的间苯二甲胺,提高间苯二甲胺的收率。
14.可选地,所述物料出口连通有汗液罐,所述汗液罐经管道连通所述物料进口。
15.本技术通过将物料出口连通汗液罐,并将汗液罐连通物料进口,能够将结晶过程中得到的汗液送入熔融结晶器中进行结晶,以回收汗中的间苯二甲胺,提高间苯二甲胺的收率。
16.可选地,所述生产系统还包括冷却器,所述冷却器位于加氢反应器与熔融结晶器之间的连通管道上。
17.可选地,所述冷热媒出口经冷热媒循环管道连通冷热媒进口,冷热媒循环管道上设置有循环泵、冷媒冷却器和热媒换热器。
18.本技术通过将冷热媒出口经冷热媒循环管道连通冷热媒进口,并在冷热媒循环管道上设置循环泵、冷媒冷却器和热媒换热器,能够实现冷热媒的循环利用,提高冷热媒利用率,降低生产成本。
附图说明
19.图1为实施例的间苯二甲胺生产系统的结构示意图。
20.附图标记
21.1-氨氧化反应器;
22.2-吸收塔;
23.3-悬浮结晶器;
24.4-固液分离机构;
25.5-加氢反应器;
26.6-熔融结晶器;
27.7-脱溶塔;
28.8-母液罐;
29.9-汗液罐;
30.10-产品罐;
31.11-循环泵;
32.12-开关阀;
33.13-离心泵;
34.14-冷却器;
35.15-冷媒冷却器;
36.16-热媒换热器;
37.17-废液罐。
具体实施方式
38.以下通过特定的具体实例说明本实用新型的实施方式,本领域技术人员可由本说明书所揭露的内容轻易地了解本实用新型的其他优点与功效。本实用新型还可以通过另外不同的具体实施方式加以实施或应用,本说明书中的各项细节也可以基于不同观点与应用,在没有背离本实用新型的精神下进行各种修饰或改变。
39.需要说明的是,本实施例中所提供的图示仅以示意方式说明本实用新型的基本构想,遂图式中仅显示与本实用新型中有关的组件而非按照实际实施时的组件数目、形状及尺寸绘制其实际实施时各组件的型态、数量及比例可为一种随意的改变,且其组件布局型态也可能更为复杂。本说明书所附图式所绘示的结构、比例、大小等,均仅用以配合说明书所揭示的内容,以供熟悉此技术的人士了解与阅读,并非用以限定本实用新型可实施的限定条件,故不具技术上的实质意义,任何结构的修饰、比例关系的改变或大小的调整,在不影响本实用新型所能产生的功效及所能达成的目的下,均应仍落在本实用新型所揭示的技术内容得能涵盖的范围内。同时,本说明书中所引用的如“下”、“底”等的用语,亦仅为便于叙述的明了,而非用以限定本实用新型可实施的范围,其相对关系的改变或调整,在无实质变更技术内容下,当亦视为本实用新型可实施的范畴。
40.在本实用新型的描述中,需要理解的是,使用“第一”、“第二”等词语来限定零部件仅仅是为了便于对相应零部件进行区别,如没有另行声明,上述词语并没有特殊含义,因此不能理解为对本实用新型保护范围的限制。
41.实施例1
42.请参阅图1,图1为本实施例的间苯二甲胺生产系统,该生产系统用于生产高纯间苯二甲胺;
43.如图1所示,本实施例的间苯二甲胺生产系统包括依次连通的氨氧化反应器1、吸收塔2、悬浮结晶器3和固液分离机构4。
44.请继续参阅图1,氨氧化反应器1作为氨氧化反应的反应容器,在氨氧化反应器1中,间二甲苯、氨气和氧气在第一催化剂(第一催化剂为钒系催化剂,钒系催化剂包括钒(v)-铬(cr)、钒(v)-锑(sb)、钒(v)-磷(p)和铁(fe)-锑(sb)和钒(v)-铁(fe)-锑(sb)中的一种或几种,均为市售商品)存在下发生氨氧化反应得到含间苯二甲腈的混合气。氨氧化反应器1设置有温度调节组件(未画出)、压力调节组件(未画出)、进液口(未画出)、进气口(未画出)和进料口(未画出),氨氧化反应器1采用流化床反应器,流化床反应器为现有技术,此处不再赘述。
45.请继续参阅图1,吸收塔2内存储有溶剂(甲基苄腈或烷基吡唑或二者的组合物,烷基吡唑为n-甲基吡唑、n-乙基吡唑和n-异丙基吡唑中的一种或多种),吸收塔2用于作为吸收混合气的容器,以使混合气形成溶液。吸收塔2设置有进液口(未画出),吸收塔2采用喷淋
式吸收塔。喷淋式吸收塔为现有技术,此处不再赘述。
46.请继续参阅图1,悬浮结晶器3作为悬浮结晶的容器,以对混合气体形成的溶液进行分离提纯,进而得到含间苯二甲腈晶体的固液混合物。悬浮结晶器3设置有进料口(未画出)、温度调节组件(未画出)和压力调节组件(未画出),悬浮结晶器3采用悬浮结晶塔。悬浮结晶塔为现有技术,此处不再赘述。
47.具体而言,通过悬浮结晶器3对含间苯二甲腈晶体的固液混合物进行分离提纯,能够提高中间产品间苯二甲腈晶体的纯度,进而提高终产品间苯二甲胺的纯度。
48.请继续参阅图1,固液分离机构4用于对含间苯二甲腈晶体的固液混合物进行固液分离,固液分离机构4底部设置有固相出口(未画出)和液相出口(未画出)。固液分离机构4采用离心塔,离心塔为现有技术,此处不再赘述。
49.请继续参阅图1,固相出口连通有加氢反应器5,加氢反应器5位于固液分离机构4下方。加氢反应器5设置有出液端,加氢反应器5的出液端连通冷却器14的第一端,冷却器14的第二端连通有熔融结晶器6。加氢反应器5与冷却器14之间的连通管道上及冷却器14与熔融结晶器6之间的连通管道上均设置有离心泵13和开关阀12。
50.请继续参阅图1,加氢反应器5用于作为加氢反应的反应容器,在加氢反应器5内苯二甲腈晶体和液氨在第二催化剂(雷尼镍系、负载镍系、铜锌系、铜硅系和贵金属载体催化剂中的一种或多种)存在下发生加氢反应,得到含间苯二甲胺的反应溶液。加氢反应器5设置有液氨进口(未画出)、进料口(未画出)、温度调节组件(未画出)和压力调节组件(未画出),加氢反应器5采用加氢反应釜。加氢反应釜为现有技术,此处不再赘述。
51.请继续参阅图1,冷却器14用于对含间苯二甲胺的反应溶液进行预冷处理,冷却器14可以采用列管式冷却器、板式冷却器、风冷式冷却器等。列管式冷却器、板式冷却器和风冷式冷却器为现有技术,此处不再赘述。
52.请继续参阅图1,熔融结晶器6用于对含间苯二甲胺的溶液进行分离提纯,得到间苯二甲胺晶体。熔融结晶器6采用降膜结晶器,降膜结晶器设置有物料进口(未画出)、物料出口(未画出)、冷热媒进口(未画出)、冷热媒出口(未画出)、温度调节组件(未画出)和压力调节组件(未画出)。降膜结晶器采用管式降膜结晶器,管式降膜结晶器是以结晶管作为结晶组件的结晶设备。管式降膜结晶器为现有技术,此处不再赘述。
53.具体而言,通过熔融结晶器6对含间苯二甲胺的溶液进行分离提纯,能够进一步提高终产品间苯二甲胺的纯度,降低能耗,缩短生产时间。
54.请继续参阅图1,熔融结晶器6的物料进口连通冷却器14的第二端,熔融结晶器6的物料出口经物料循环管道连通熔融结晶器6的物料进口,物料循环管道上设置有循环泵11和开关阀12。熔融结晶器6的冷热媒出口经冷热媒循环管道连通熔融结晶器6的冷热媒进口,冷热媒循环管道上设置有循环泵11、冷媒冷却器15和热媒换热器16。
55.具体而言,通过将熔融结晶器6的物料出口经物料循环管道连通熔融结晶器6的物料进口,并在物料循环管道上设置循环泵11和开关阀12,能够将含间苯二甲胺的溶液中未结晶物料再次送入熔融结晶器6中,以使含间苯二甲胺的溶液中未结晶物料作为下一次结晶原料,进而提高间苯二甲胺的收率。通过将熔融结晶器6的冷热媒出口经冷热媒循环管道连通熔融结晶器6的冷热媒进口,并在冷热媒循环管道上设置循环泵11、冷媒冷却器15和热媒换热器16,能够实现冷热媒的循环利用,提高冷热媒利用率,降低生产成本。
56.请继续参阅图1,冷媒冷却器15用于冷却换热(结晶阶段)后温度升高的冷媒(冷媒可以采用冷却水等物质),以使冷媒再次被送入熔融结晶器6中与未结晶的物料进行换热,使经过初次结晶的待提纯物料中未结晶物料进行再次结晶,进而提高间苯二甲胺的收率。热媒换热器16用于加热经换热(发汗和熔融阶段)后温度降低的热媒(热媒可以采用换热油等),以使热媒经第一冷热媒循环管道被再次进入熔融结晶器6中与结晶管管壁上再次得到的晶体物质进行换热,进而提高间苯二甲胺的纯度。冷媒冷却器15可以采用列管式冷却器、板式冷却器、风冷式冷却器等。热媒换热器16可以采用间壁式换热器、混合式换热器、蓄热式换热器等。管式降膜结晶器、开关阀、离心泵、列管式冷却器、板式冷却器、风冷式冷却器、间壁式换热器、混合式换热器、蓄热式换热器等为现有技术,此处不再赘述。
57.请继续参阅图1,物料出口连通有母液罐8、汗液罐9和产品罐10,母液罐8、汗液罐9和产品罐10均位于熔融结晶器6的下方。
58.请继续参阅图1,母液罐8经管道连通悬浮结晶器3的进料口,汗液罐9经管道连通熔融结晶器6的物料进口。物料出口与母液罐8、汗液罐9及产品罐10之间的连通管道上均设置有离心泵13,母液罐8与悬浮结晶器3的进料口之间的连通管道上设置有离心泵13和开关阀12,汗液罐9与熔融结晶器6的物料进口之间的连通管道上设置有离心泵13和开关阀12。母液罐8和汗液罐9分别为经熔融结晶器6处理后所得母液(结晶后残余溶液,母液中含少量间苯二甲胺)和汗液(升温发汗阶段排出的液体,汗液中含较多的间苯二甲胺)的存储容器。产品罐10作为得到的终产品间苯二甲胺的存储容器。
59.具体而言,通过将物料出口连通母液罐8和汗液罐9,并将母液罐8连通悬浮结晶器3的进料口,汗液罐9连通熔融结晶器6的物料进口,能够将结晶过程中得到的母液(结晶后残余溶液,母液中含少量间苯二甲胺)及汗液(升温发汗阶段排出的液体,汗液中含较多的间苯二甲胺),能够将熔融结晶器6的物料出口排出的母液和汗液分别送入悬浮结晶器3和熔融结晶器6中进行结晶,以回收母液、汗液中的间苯二甲胺,提高间苯二甲胺的收率。
60.请继续参阅图1,液相出口连通有脱溶塔7,脱溶塔7设置有气相出口和废液出口,气相出口经管道连通吸收塔2,废液出口经管道连通有废液罐17,液液相出口与脱溶塔7之间的连通管道及脱溶塔7与吸收塔2之间的连通管道上均设置有离心泵13和开关阀12。
61.请继续参阅图1,脱溶塔7用于回收经固液分离机构4固液分离后得到的液体中的溶剂,进而将经固液分离机构4固液分离后得到的液体中的溶剂与其他物质进行分离,脱溶塔7可以采用蒸馏塔等,蒸馏塔为现有技术,此处不再赘述。
62.具体而言,通过将液相出口连通脱溶塔7,并将脱溶塔7的气相出口经管道连通吸收塔2,在液液相出口与脱溶塔7之间的连通管道及脱溶塔7与吸收塔2之间的连通管道上均设置离心泵13和开关阀12,能够回收经固液分离机构4固液分离后得到的液体中的溶剂,并将回收得到的溶剂送入吸收塔2中进行重复利用,提高溶剂的利用效率,降低生产成本。
63.本实施例的生产系统的工作过程为:
64.s1.通过温度调节组件将氨氧化反应器1内环境温度调节至400-440℃,通过压力调节组件将氨氧化反应器1内压力调节至20kpa;通过进液口向氨氧化反应器1内投放预先预热至400-440℃的原料间二甲苯,通过进气口向氨氧化反应器1内送入氨气和空气,通过进料口向氨氧化反应器1内投放第一催化剂,第一催化剂为钒系催化剂,钒系催化剂为钒(v)-铬(cr)、钒(v)-锑(sb)、钒(v)-磷(p)和铁(fe)-锑(sb)和钒(v)-铁(fe)-锑(sb)中的一
种或几种,均为市售商品;间二甲苯、氨气和空气的摩尔比为1:8-9:38-40。
65.间二甲苯、氨气和氧气在第一催化剂的催化作用下发生反应生成间苯二甲腈,得到含间苯二甲腈的混合气,氨气和空气的停留时间为3-5s;
66.打开氨氧化反应器1与吸收塔2之间的连通管道上的开关阀,混合气经管道进入预先存储有溶剂(甲基苄腈或烷基吡唑或二者的组合物,烷基吡唑为n-甲基吡唑、n-乙基吡唑和n-异丙基吡唑中的一种或多种)的吸收塔2中,溶剂溶解混合气中的间苯二甲腈等物质,得到间苯二甲腈的浓度为90wt%-91wt%的溶液;
67.s2.打开吸收塔2与悬浮结晶器3之间的连通管道上的离心泵13和开关阀12,步骤s1得到的溶液被泵送至悬浮结晶器3中;
68.在此过程中,通过温度调节组件将悬浮结晶器3内环境温度调节至10-15℃,通过压力调节组件将悬浮结晶器3内压力调节至常压;
69.在悬浮结晶器3中,溶液中的间苯二甲腈逐渐析出,析出的晶体颗粒与高浓度熔融液逆流接触从而进一步提高了间苯二甲腈晶体的纯度;一段时间后,得到含间苯二甲腈晶体的固液混合物;
70.s3.打开悬浮结晶器3与固液分离机构4之间的连通管道上的离心泵13和开关阀12,固液混合物被泵送至固液分离机构4内。固液分离机构4对固液混合物进行固液分离处理,得到间苯二甲腈晶体和溶液;
71.手工取出少许间苯二甲腈晶体放入悬浮结晶器3中,在悬浮结晶器3中引入晶种,以便于后续结晶的顺利进行;
72.打开固液分离机构4的固相出口与加氢反应器5之间的连通管道上的开关阀12,间苯二甲胺晶体在重力作用下落入加氢反应器5中;
73.在此过程中,通过温度调节组件将加氢反应器5内环境温度调节至65-80℃,通过压力调节组件将加氢反应器5内压力调节至2-5mpa;通过液氨进口向加氢反应器5中投放液氨,液氨与间苯二甲腈晶体的摩尔比为1:0.8-1,通过进料口向加氢反应器5中加入氢气在第二催化剂的催化作用下进行加氢反应,反应50-60min后得到反应溶液,第二催化剂为雷尼镍系、负载镍系、铜锌系、铜硅系和贵金属载体催化剂中的一种或多种,均为市售商品;
74.s4.打开加氢反应器5与冷却器14之间的连通管道上的离心泵13和开关阀12,反应溶液被泵送至冷却器14中,反应溶液被冷却器预冷至20℃,随后打开冷却器14与熔融结晶器6之间的连通管道上的离心泵13和开关阀12,预冷后的反应溶液被泵送至熔融结晶器6中进行降膜结晶,具体为:
75.s4.1.启动熔融结晶器6的冷热媒系统将结晶管预热至20℃;
76.s4.2.熔融结晶:启动物料循环管道上的循环泵11(未画出),控制流量为0.3m3/h,压力为0.02mpa,电机频率为13hz,使反应溶液沿结晶管的内壁流下,调节冷媒(冷却水)温度,将反应溶液以3-5℃/min的速率快速降温至14-16℃,随后以0.2-1℃/min的速率缓慢降温至-6~-3℃;保持不启动降膜结晶循环保温系统冷热媒进行结晶90-100min,使反应溶液中的间苯二甲胺结晶,得到晶体;然后停止物料循环管道上的循环泵13,打开物料出口与母液罐8之间的连通管道上的开关阀12,未结晶的残液(即母液)在重力作用下流入母液罐8内;
77.打开母液罐8与悬浮结晶器3之间的连通管道上的离心泵13和开关阀12,母液被泵
送至悬浮结晶器3中进行悬浮结晶;
78.s4.3.发汗:调节热媒(换热油)温度,使晶体以3-5℃/min的速率快速升温至7-10℃,随后以0.2-1℃/min的速率缓慢升温至13-15℃;保温系统冷热媒温度控制在20-25℃发汗40-50min;该阶段,晶层部分熔融,晶层中的间苯二甲胺与杂质分离,进而对晶体进行纯化,提高间苯二甲胺的纯度;
79.打开物料出口与汗液罐9之间的连通管道上的开关阀,汗液在重力作用下流入汗液罐9内;
80.打开汗液罐8与熔融结晶器6之间的连通管道上的离心泵13和开关阀12,汗液被泵送至熔融结晶器6中进行熔融结晶,得到间苯二甲胺产品(一级回收产品);
81.s4.4熔融:调节热媒温度至30-40℃,使晶体进行熔融25-35min,熔融完成后,得到产品,对产品进行取样。
82.上述实施例仅例示性说明本实用新型的原理及其功效,而非用于限制本实用新型。任何熟悉此技术的人士皆可在不违背本实用新型的精神及范畴下,对上述实施例进行修饰或改变。因此,举凡所属技术领域中具有通常知识者在未脱离本实用新型所揭示的精神与技术思想下所完成的一切等效修饰或改变,仍应由本实用新型的权利要求所涵盖。