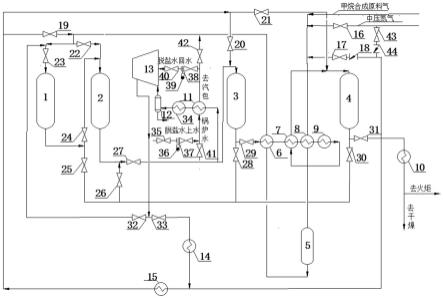
1.本技术涉及甲烷合成工艺中的温控领域,尤其涉及一种甲烷合成装置反应炉内催化剂床层降温结构。
背景技术:2.甲烷合成进行一定时期后,反应炉内碎裂的催化剂碳含量最高可达48.2%,催化剂出现明显积碳现象。co的析炭反应可生成单质碳并附着在催化剂表面上,由于催化剂为多孔结构,单质碳累计到一定程度便可将催化剂内的微孔撑破,从而导致催化剂碎裂;不断累积的单质碳最终成为肉眼可见的碳粉,碎裂的催化剂和析炭反应造成的碳粉共同导致反应炉进出口工艺气压差升高,当压差升高至150kpa以上时,反应炉底部催化剂由于承压过大而碎裂的风险过高,须对催化剂床层进行处理,将催化剂从反应炉内扒出,通过筛分除去已碎裂的催化剂和碳粉后回装,从而降低反应炉进出口工艺气压差。由于甲烷合成反应是一种可以放出大量热的化学反应,在反应炉运行过程中,反应炉内催化剂床层温度可达600℃以上。由于催化剂的扒出、筛分、回装工作均需人工进行,在处理催化剂床层之前,必须将催化剂床层温度降至40℃以下。
3.现有甲烷化合成工艺需要进行两阶段降温,在第一降温阶段降温速率慢、时间长,导致循环压缩机运行时间长,增加装置能耗,并影响装置检修进度。而且第一降温阶段反应炉催化剂床层所能达到的温度在90℃左右,降温能力低,影响工艺气中的水在循环气分离罐中的分离,不利于催化剂保护。
4.在甲烷合成装置停车后,系统内锅炉水由于汽包停止副产蒸汽而停止流动,随着工艺气温度的降低,系统内锅炉水温度同步降低,水的体积有所减小,因锅炉水换热器在锅炉水系统的最高点,最终会在锅炉水换热器壳程顶部形成局部真空,处于局部真空范围内的管程换热管由于壳程无水与其换热,形成干烧,极易造成设备内部膨胀不均匀而将管板与换热管连接处的焊缝拉裂,最终导致换热器内漏。
5.现有甲烷化合成工艺在第二降温阶段,四台反应炉只能为串联流程,工艺流程后端反应炉所用降温氮气来自前端反应炉出口,温度较高,若需检修工艺流程后端反应炉,会导致降温时间过长和氮气的浪费。原料气入口所加中压氮气必须经过一号原料气换热器和二号原料气换热器加热后方可进入反应炉进行降温,降低了氮气的降温能力,同时造成了冷量的损失。
技术实现要素:6.针对上述现有缺陷,本技术的目的在于加快了甲烷合成装置停车后第一、第二降温阶段的降温速率,使催化剂床层脱水更快、更彻底,降低了催化剂床层汽态水冷凝风险,保护催化剂的一种甲烷合成装置反应炉内催化剂床层降温结构。
7.本技术的目的是这样实现的:一种甲烷合成装置反应炉内催化剂床层降温结构,包括在循环压缩机入口锅炉水换热器进口管线侧新增脱盐水上水第一道手阀,在循环压缩
机入口锅炉水换热器进口管线侧新增脱盐水上水管线字盲板,在循环压缩机入口锅炉水换热器进口管线侧新增脱盐水上水第二道手阀;在循环压缩机入口锅炉水换热器出口管线侧新增脱盐水回水第一道手阀,在循环压缩机入口锅炉水换热器出口管线侧新增脱盐水回水管线八字盲板,循环压缩机入口锅炉水换热器出口管线侧新增脱盐水回水第二道手阀;在中压氮气管线上设置有与升温管线连通的连接管线,在连接管线上设置有氮气联通管线手阀和氮气联通管线止逆阀。
8.锅炉水换热器进口管线上设置有循环压缩机入口锅炉水换热器上水管线手阀,锅炉水换热器出口管线上设置有循环压缩机入口锅炉水换热器回水管线手阀。
9.在第一降温阶段开始时,将原锅炉水管线停用并将新增脱盐水管线投用,之后对锅炉水换热器壳程进行顶部排气,使脱盐水在锅炉水换热器中持续流动;同时将锅炉水换热器壳程换热水温度由锅炉水的250℃降至脱盐水的50℃,使进入循环压缩机入口冷却器的工艺气温度降低,加快第一降温阶段降温速率。
10.在第一降温阶段中,将锅炉水换热器所用锅炉水变更为四号反应炉出口脱盐水换热器所用脱盐水,将四号反应炉出口脱盐水换热器的脱盐水上水接至锅炉水换热器的锅炉水上水管线。
11.在第二降温阶段开始时,关闭中压氮气手阀,打开氮气联通管线手阀来引入中压氮气,此时氮气无需经过一号原料气换热器和二号原料气换热器加热便可进入反应炉。
12.在第二降温阶段中,将甲烷合成装置中压氮气入口改为脱硫槽升温进气阀前止逆阀前端管线处。
13.由于实行上述技术方案,本技术具有以下优点:
14.1、加快了甲烷合成装置停车后第一降温阶段的降温速率;
15.2、缩短了甲烷化合成装置停车过程中循环压缩机运行时间,降低了装置能耗;
16.3、使甲烷合成装置停车后第一降温阶段所能达到的温度更低,预计可使反应炉催化剂床层温度可降至70℃,比原工艺降低20℃;
17.4、在第一降温阶段,将原锅炉水管线停用并将新增脱盐水管线投用,之后对锅炉水换热器壳程进行顶部排气,使脱盐水在锅炉水换热器中持续流动,从而避免了锅炉水换热器发生设备干烧;
18.5、第一降温阶段循环压缩机入口温度可降至40℃,比原工艺降低20℃,使催化剂床层脱水更快、更彻底,降低了催化剂床层汽态水冷凝风险,保护催化剂;
19.6、改变了甲烷合成装置停车后第二降温阶段的降温流程和操作方法,可将任意一台需检修的反应炉置于降温流程前端,使降温氮气先进需检修的反应炉,加快需检修反应炉的降温速率,大大提升降温效率;
20.7、由于工艺流程的改变,在第二降温阶段,氮气无需经过一号原料气换热器和二号原料气换热器加热便可进入反应炉,加快了降温速率,降低了氮气消耗。
附图说明
21.本技术的具体结构由以下的附图和实施例给出:
22.图1是本技术的系统结构示意图。
23.图例:1、一号反应炉,2、二号反应炉,3、三号反应炉,4、四号反应炉,5、脱硫槽6、二
号原料气换热器,7、补充甲烷化反应换热器,8、一号原料气换热器,9、脱盐水换热器,10、四号反应炉出口脱盐水换热器,11、锅炉水换热器,12、循环气分离罐,13、循环压缩机,14、蒸汽加热器,15、电加热器,16、中压氮气手阀,17、脱硫槽升温进气阀,18、脱硫槽升温进气阀前止逆阀,19、主反应器升温进气总阀,20、三号反应炉升温进气阀,21、四号反应炉升温进气阀,22、二号反应炉原料气切断阀,23、一号反应炉入口切断阀,24、一号反应炉出口切断阀,25、一号反应炉升温回气切断阀,26、升温回气总阀,27、二号反应炉出口切断阀,28、三号反应炉升温回气切断阀,29、三号反应炉出口切断阀,30、四号反应炉升温回气切断阀,31、四号反应炉出口切断阀,32、循环压缩机出口切断阀,33、循环压缩机出口升温阀,34、循环压缩机入口冷却器,35、上水第一道手阀,36、上水管线八字盲板,37、上水第二道手阀,38、回水第一道手阀,39、回水管线八字盲板,40、回水第二道手阀,41、上水管线手阀,42、回水管线手阀,43、氮气联通管线手阀,44、氮气联通管线止逆阀。
具体实施方式
24.本技术不受下述实施例的限制,可根据本技术的技术方案与实际情况来确定具体的实施方式。
25.实施例:如图1所示,一种甲烷合成装置反应炉内催化剂床层降温结构包括在循环压缩机入口锅炉水换热器11进口管线侧新增脱盐水上水第一道手阀35,在循环压缩机入口锅炉水换热器11进口管线侧新增脱盐水上水管线八字盲板36,在循环压缩机入口锅炉水换热器11进口管线侧新增脱盐水上水第二道手阀37。
26.在循环压缩机入口锅炉水换热器11出口管线侧新增脱盐水回水第一道手阀38,在循环压缩机入口锅炉水换热器11出口管线侧新增脱盐水回水管线八字盲板39,循环压缩机入口锅炉水换热器11出口管线侧新增脱盐水回水第二道手阀40。
27.在中压氮气管线上设置有与升温管线连通的连接管线,在连接管线上设置有氮气联通管线手阀43和氮气联通管线止逆阀44。
28.进一步的,锅炉水换热器11进口管线上设置有循环压缩机入口锅炉水换热器上水管线手阀41,锅炉水换热器11出口管线上设置有循环压缩机入口锅炉水换热器回水管线手阀42。
29.本技术在使用时,在第一降温阶段中,将锅炉水换热器11所用锅炉水变更为四号反应炉出口脱盐水换热器10所用脱盐水(此两台换热器现场距离为5米左右,新增管线长度短,造价低),将四号反应炉出口脱盐水换热器10的脱盐水上水接至锅炉水换热器11的锅炉水上水管线,将四号反应炉出口脱盐水换热器10的脱盐水回水接至锅炉水换热器11的锅炉水回水管线,新增循环压缩机入口锅炉水换热器新增脱盐水上水第一道手阀35、循环压缩机入口锅炉水换热器新增脱盐水上水管线8字盲板36、循环压缩机入口锅炉水换热器新增脱盐水上水第二道手阀37、循环压缩机入口锅炉水换热器新增脱盐水回水第一道手阀38、循环压缩机入口锅炉水换热器新增脱盐水回水管线8字盲板39、循环压缩机入口锅炉水换热器新增脱盐水回水第二道手阀40、循环压缩机入口锅炉水换热器上水管线手阀41、循环压缩机入口锅炉水换热器回水管线手阀42。
30.在第一降温阶段开始时,将原锅炉水管线停用并将新增脱盐水管线投用,之后对锅炉水换热器11壳程进行顶部排气,使脱盐水在锅炉水换热器11中持续流动,从而避免了
锅炉水换热器11发生设备干烧;同时将锅炉水换热器11壳程换热水温度由锅炉水的250℃降至脱盐水的50℃,使进入循环压缩机入口冷却器34的工艺气温度大幅降低,加快了第一降温阶段降温速率,预计可使第一降温阶段循环压缩机13入口温度降至40℃,最终反应炉催化剂床层温度可降至70℃,比原工艺降低20℃,促进了工艺气中的水在循环气分离罐12中的分离,使催化剂床层气态水冷凝风险大幅降低。
31.在第二降温阶段中,将甲烷合成装置中压氮气入口改为脱硫槽升温进气阀前止逆阀18前端管线处,新增了氮气联通管线手阀43和氮气联通管线止逆阀44。在第二降温阶段开始时,关闭中压氮气手阀16,打开氮气联通管线手阀43来引入中压氮气。由于工艺流程的改变,此时氮气无需经过一号原料气换热器8和二号原料气换热器6加热便可进入反应炉,加快了降温速率。
32.利用原甲烷合成工艺中的管线,改变了四台反应炉降温流程,可将任意一台需检修的反应炉置于降温流程前端,使降温氮气先进需检修的反应炉,加快需检修反应炉的降温速率,大大提升降温效率。
33.若一号反应炉1需检修处理催化剂床层,其他反应炉无需将温度降至40℃以下,则在第二降温阶段主要考虑一号反应炉1的降温速率,此时需将氮气联通管线手阀43、主反应器升温进气总阀19、一号反应炉入口切断阀23、一号反应炉出口切断阀24、二号反应炉出口切断阀27、三号反应炉出口切断阀29、四号反应炉出口切断阀31打开,其余阀门关闭,使氮气先进一号反应炉1,而后依次经过二号反应器2、三号反应器3、四号反应器4,最终将吸收热量后的氮气在四号反应器4出口送入火炬。
34.若二号反应炉2需检修处理催化剂床层,此时需将氮气联通管线手阀43、主反应器升温进气总阀19、二号反应炉原料气切断阀22、二号反应炉出口切断阀27、三号反应炉出口切断阀29、四号反应炉出口切断阀31打开,其余阀门关闭,使氮气先进二号反应炉2,而后依次经过三号反应器3、四号反应器4,最终将吸收热量后的氮气在四号反应器4出口送入火炬。
35.若三号反应炉3需检修处理催化剂床层,此时需将氮气联通管线手阀43、三号反应炉升温进气阀20、三号反应炉出口切断阀29、四号反应炉出口切断阀31打开,其余阀门关闭,使氮气先进三号反应炉3,而后经过四号反应器4,最终将吸收热量后的氮气在四号反应器4出口送入火炬。
36.若四号反应炉4需检修处理催化剂床层,此时需将氮气联通管线手阀43、四号反应炉升温进气阀21、四号反应炉出口切断阀31打开,其余阀门关闭,使氮气先进四号反应炉4,而后经过四号反应器4,最终将吸收热量后的氮气在四号反应器4出口送入火炬。
37.上述说明仅仅是为清楚地说明本技术所作的举例,而并非是对本技术的实施方式的限定。凡是属于本技术的技术方案所引申出的显而易见的变化或变动仍处于本技术的保护范围之列。