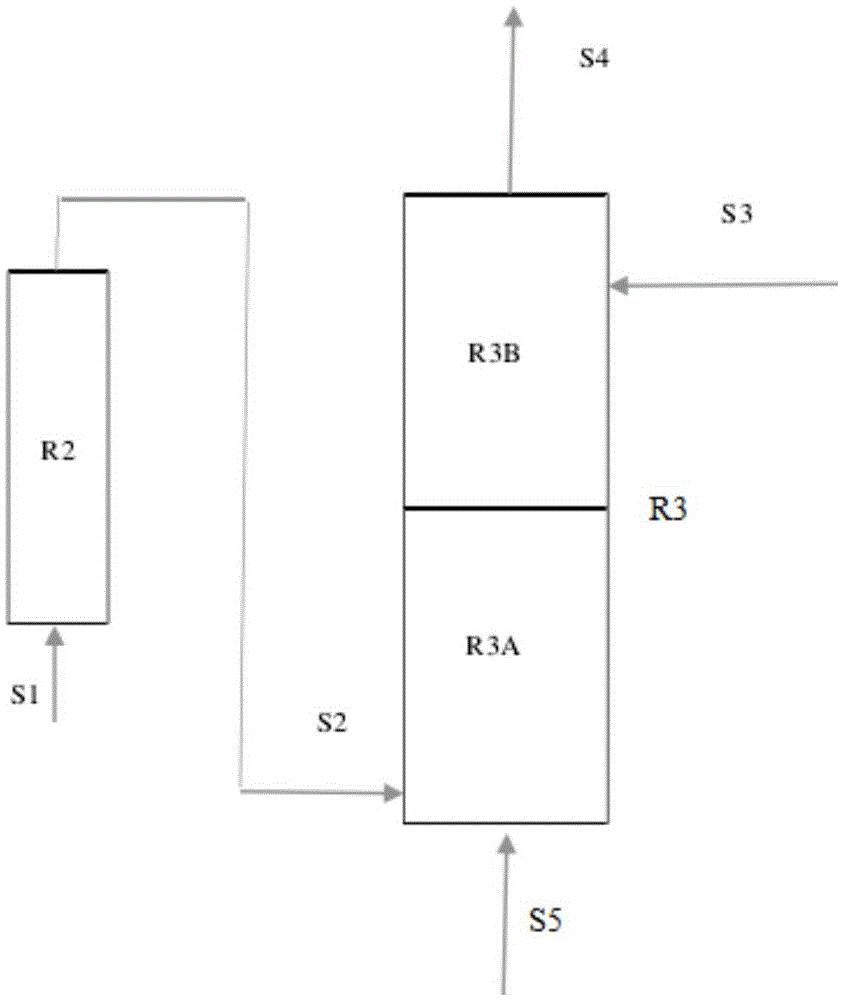
本发明涉及一种生产低碳烯烃产生的裂解气的处理方法。
背景技术:
:在炼油厂和聚烯烃等装置上产生的废气如不饱和烯烃或其烃类衍生物,由于经济价值较高往往进行综合回收利用甚至转化为其他价值更高的产品,例如现有公开报道的裂解气加氢催化技术,往往采用较低温度(例如约40~90℃)下的选择加氢工艺,尽可能除去炔烃,这样可以尽可能地减少烯烃和丁二烯的损失,从而可以利于裂解气回收烯烃等有机气体。而石油化工小试和中试试验装置,产生的VOC(挥发性有机化合物)总量小且分散,缺乏经济效益回收综合利用比较困难,同时这类废气的排放处理往往未能引起足够的重视。近些年来国内雾霾现象不断的加剧,社会对VOC的治理越来越重视,各科研机构特别是在市区的化工试验产生的三废的治理也提上了日程,但至今国内外尚缺乏针对往往认为经济价值相对较大不饱和烃类的催化燃烧技术。在现有蒸汽裂解乙烯模拟实验装置中,每小时常常有数个立方米或数十个立方米的裂解气直接排放在大气中。采用直接燃烧点火炬处理,不仅存在安全隐患,而且物料流燃烧需要提供大量的热量。一般来说,裂解气中的组分含有H2、CO、CH4、C1~C5饱和烷烃和不饱和烃类(例如单烯烃类、以及相应的二烯烃和炔烃等)。这些大多易燃易爆的组分,相对于相应的单烯烃和烷烃来说,其中的乙炔尤其易燃易爆。H2、乙炔和乙烯的爆炸限分别为4~7.5vol%,1.5~100vol%和2.8~32vol%。如果这些组分不经过处理直接燃烧,存在着巨大的安全隐患。技术实现要素:本发明的目的在于克服因裂解气直接燃烧存在安全隐患的缺陷提供一种新型的生产低碳烯烃产生的裂解气的处理方法。为了实现上述目的,本发明提供一种生产低碳烯烃产生的裂解气的处理方法,其中,该方法包括:(1)在非选择性加氢的条件下,在加氢催化剂存在下,将所述裂解气进行非选择性加氢处理,使得裂解气中的炔烃和二烯烃转化为单烯烃和/或烷烃;其中,所述加氢催化剂为以Ni和选自Zn和/或Sb为金属活性组分的负载型Ni系催化剂;(2)将步骤(1)加氢后的裂解气在负载型Pd-Pt系催化剂存在下,与空气进行燃烧反应;其中,所述负载型Pd-Pt系催化剂以Pd和Pt为金属活性组分。本发明采用的生产低碳烯烃产生的裂解气的处理方法,通过先对裂解气非选择性加氢然后再进行燃烧的方式,能够较好地避免因裂解气直接燃烧存在安全隐患的问题,且该方法特别适用于石油化工小试和中试试验,有利于环境保护。本发明的其它特征和优点将在随后的具体实施方式部分予以详细说明。附图说明附图是用来提供对本发明的进一步理解,并且构成说明书的一部分,与下面的具体实施方式一起用于解释本发明,但并不构成对本发明的限制。在附图中:图1是根据本发明的实施例1的方法所采用的裂解气的处理系统。图2是对比例1的方法所采用的裂解气的处理系统。附图标记说明R2——加氢反应单元;R3——燃烧反应单元;R3A——起燃段;R3B——飞温段;S1——裂解气;S2——加氢后的裂解气;S3——冷却水;S4——燃烧后的尾气;S5——空气。具体实施方式以下对本发明的具体实施方式进行详细说明。应当理解的是,此处所描述的具体实施方式仅用于说明和解释本发明,并不用于限制本发明。本发明提供一种生产低碳烯烃产生的裂解气的处理方法,其中,该方法包括:(1)在非选择性加氢的条件下,在加氢催化剂存在下,将所述裂解气进行非选择性加氢处理,使得裂解气中的炔烃和二烯烃转化为单烯烃和/或烷烃;其中,所述加氢催化剂为以Ni和选自Zn和/或Sb为金属活性组分的负载型Ni系催化剂;(2)将步骤(1)加氢后的裂解气在负载型Pd-Pt系催化剂存在下,与空气进行燃烧反应;其中,所述负载型Pd-Pt系催化剂以Pd和Pt为金属活性组分。根据本发明,所述裂解气是生产低碳烯烃产生的含有多种C5以下的不饱和烯烃和烷烃以及氢气、一氧化碳等尾气,特别是生产蒸汽裂解生产乙烯的尾气,作为这样的蒸汽裂解生产乙烯的尾气例如可以是石脑油蒸汽裂解产生的尾气,优选情况下,本发明所述的裂解气是指上述的生产低碳烯烃产生的尾气经过气液分离处理,气液分离所得的液相将分离除去尾气中可能含有的水蒸汽和C5以上的烃类,而气相即可理解为本发明所述的裂解气。作为这样的裂解气中,H2的含量为5-20体积%,C1-C4的烷烃的含量为20-40体积%,C2-C4的炔烃和二烯烃的含量为0.1-3体积%,C2-C4的单烯烃的含量为40-60体积%。优选地,作为这样的裂解气中,H2的含量为10-18体积%,C1-C4的烷烃的含量为30-40体积%,C2-C4的炔烃和二烯烃的含量为1-2.5体积%,C2-C4的单烯烃的含量为40-50体积%。其中,C1-C4的烷烃例如为甲烷、乙烷、丙烷、丁烷(包括正丁烷、异丁烷)中的一种或多种。C2-C4的单烯烃例如可以为乙烯、丙烯、正丁烯、异丁烯、顺-2-丁烯、反-2-丁烯中的一种或多种。C2-C4的炔烃例如可以为乙炔、丙炔等中的一种或多种。C2-C4的二烯烃例如可以为丙二烯和/或1,3-丁二烯。根据本发明,所述裂解气还可以含有少量的C5以上的烃类(例如为2体积%以下)。作为C5以上的烃类例如可以为苯、甲苯、戊烷等中的一种或多种。根据本发明,所述裂解气还可以含有多种在气液分离中不能从气体中除去的气体,例如CO、CO2等,但是含量较少,例如CO的含量为0.1体积%以下,CO2的含量为0.1体积%以下(更优选不含有CO2)。在本发明的一种实施方式中,当采用石脑油蒸汽裂解产生的尾气经过气液分离处理后的裂解气作为本发明的裂解气时,所述裂解气中所述裂解气中,H2的含量为10-20体积%,CO的含量为0.1体积%以下,甲烷的含量为20-35体积%,乙烷的含量为5-10体积%,乙烯的含量为20-40体积%,乙炔的含量为0.1-2体积%,丙烷的含量为0.1-5体积%,丙烯的含量为5-15体积%,丙二烯和丙炔的含量为0.1-2体积%,丁烷(包括正丁烷和异丁烷)的含量为1体积%以下,丁烯(包括正丁烯、异丁烯、顺-2-丁烯和反-2-丁烯)的含量为0.5-2体积%,1,3-丁二烯的含量为0.5-5体积%,C5以上的烃类含量为2体积%以下。更优选地,所述裂解气中,H2的含量为10-18体积%,CO的含量为0.1体积%以下,甲烷的含量为20-35体积%,乙烷的含量为5-7体积%,乙烯的含量为30-35体积%,乙炔的含量为0.1-1体积%,丙烷的含量为0.1-1体积%,丙烯的含量为6-10体积%,丙二烯和丙炔的含量为0.1-1体积%,丁烷(包括正丁烷和异丁烷)的含量为0.5体积%以下,丁烯(包括正丁烯、异丁烯、顺-2-丁烯和反-2-丁烯)的含量为0.5-2体积%,1,3-丁二烯的含量为0.5-2体积%,C5以上的烃类含量为1.5体积%以下。根据本发明,对步骤(1)中所述裂解气的用量并无特别限定,可以根据不同的规模进行适当地调整,例如,所述裂解气的体积流量为0.1-100m3/h,优选为0.5-10m3/h,更优选为1-6m3/h。根据本发明,所述负载型Ni系催化剂将催化非选择性加氢反应,从而使得裂解气中的炔烃和二烯烃转化为单烯烃和/或烷烃,作为这样的负载型Ni系催化剂以Ni和选自Zn和/或Sb为金属活性组分,即可以以Ni和Zn为金属活性组分,也可以以Ni和Sb的组合为金属活性组分,也可以是以Ni、Zn和Sb的组合为金属活性组分。优选地,所述负载型Ni系催化剂为在具有Al2O3涂层的蜂窝型堇青石上负载有Ni、Zn和Sb的Ni-Al2O3催化剂,也可称作Ni/Zn/Sb-Al2O3。当采用该Ni/Zn/Sb-Al2O3催化剂进行催化加氢时,还可以防止不饱和烃类之间发生聚合反应,从而不易造成反应装置发生堵塞。其中,所述负载型Ni系催化剂需要具有能够催化非选择性加氢反应的活性,作为这样的负载型Ni系催化剂优选为在具有Al2O3涂层的蜂窝型堇青石上负载有Ni和选自Zn和/或Sb的Ni-Al2O3催化剂。更优选地,以所述Ni-Al2O3催化剂的总重量为基准,以NiO计的Ni元素的含量为0.1-5重量%,优选为2-5重量%;当含有Zn时,以ZnO计的Zn元素的含量为0.1-5重量%,优选为2-5重量%;当含有Sb时,以Sb2O3计的Sb元素的含量为0.01-1重量%,优选为0.01-0.1重量%。上述负载型Ni系催化剂还可以含有助剂组分,所述助剂组分例如可以为选自Mo、W、Zr、Mn、La和Cu等的一种或多种。在含有助剂组分的情况下,可以认为所述负载型Ni系催化剂中含有的Ni和选自Zn和/或Sb为主活性组分。对所述助剂组分的含量并无特别的限定,可以根据较宽的范围内变动,优选地,在含有助剂组分的情况下,以所述负载型Ni系催化剂的总重量为基准,以助剂组分的氧化物计的所述助剂组分的含量为0.01-1重量%。其中,提供Al2O3的可以是γ-Al2O3、α-Al2O3、θ-Al2O3和η-Al2O3中的一种或多种,优选为γ-Al2O3。以所述负载型Ni系催化剂的总重量为基准,Al2O3的含量为1-20重量%,更优选为5-15重量%,更进一步优选为8-10重量%。作为本发明的负载型Ni系催化剂可以是市售品,也可以通过本领域常规的方法制得,以Ni/Zn/Sb-Al2O3催化剂为例,其制备方法优选包括:(a)将拟薄水铝石的浆体涂覆在蜂窝型堇青石(可以采用蜂窝型堇青石陶瓷)上,干燥后进行焙烧,得到具有含铝涂层的蜂窝型堇青石,以作为载体;(b)将含镍化合物和选自含锌化合物和/或含锑化合物的溶液涂覆在上述载体上,干燥后焙烧,从而制得负载型Ni系催化剂。其中,所述含镍化合物例如可以为硝酸镍、硫酸镍、碳酸镍和氯化镍中的一种或多种。所述含锌化合物例如可以为硝酸锌、醋酸锌和碳酸锌中的一种或多种。所述含锑化合物例如可以为三氧化二锑、醋酸锑和乙二醇锑中的一种或多种。采用的溶液的溶剂可以为水、氨水、乙醇和乙二醇中的一种或多种。应当理解的是,本发明中的含镍化合物和选自含锌化合物和/或含锑化合物的溶液可以是溶解于溶剂中的溶液形式,也可以是部分溶解部分不溶解的悬浊液或分散液的形式,本发明对此并无特别的限定。其中,对所述含镍化合物和选自含锌化合物和/或含锑化合物的溶液并无特别的限定,只要能够制备得到负载型Ni系催化剂即可,例如所述含镍化合物的含量可以为5-25重量%,在含有Zn的情况下,所述含锌化合物的含量可以为10-30重量%,在含有Sb的情况下,所述含锑化合物的含量可以为0.01-1重量%。其中,步骤(a)中,所述拟薄水铝石的浆体可以采用本领域常规的方法制得,例如将拟薄水铝石粉末与水进入球磨便可获得该浆体。优选地,所述拟薄水铝石和水的重量比为5-30:100,更优选为10-20:100。步骤(a)将拟薄水铝石的浆体涂覆在蜂窝型堇青石上可以采用本领域常规的方式进行,例如采用喷涂或浸渍的方式。步骤(a)中,干燥的条件优选包括:温度为60-240℃(优选为120-200℃),时间为1-24h(优选为12-20h)。为了便于焙烧,步骤(a)还可以包括将干燥后的载体在挤条机中成型后,再进行焙烧。焙烧的条件优选包括:温度为400-1400℃(优选为400-800℃,更优选为500-700℃),时间为1-24h(优选为5-7h)。其中,优选情况下,拟薄水铝石的浆体和蜂窝型堇青石的用量,使得最后所得的负载型Ni系催化剂中,以Al2O3计的铝元素的含量为1-20重量%,更优选为5-15重量%,更进一步优选为8-10重量%。步骤(b)中,将含镍化合物和选自含锌化合物和/或含锑化合物的溶液涂覆在步骤(a)制得的载体上可以采用本领域常规的方式进行,例如采用喷涂或浸渍的方式。其中,优选情况下,所述含镍化合物和选自含锌化合物和/或含锑化合物的溶液和载体的用量,使得最后所得的负载型Ni系催化剂中,以NiO计的Ni元素的含量为0.1-5重量%,优选为2-5重量%;当含有Zn时,以ZnO计的Zn元素的含量为0.1-5重量%,优选为2-5重量%;当含有Sb时,以Sb2O3计的Sb元素的含量为0.01-1重量%,优选为0.01-0.1重量%。其中,步骤(b)中,干燥的条件优选包括:温度为80-240℃(优选为120-200℃),时间为0.5-10h(优选为3-5h)。焙烧的条件优选包括:温度为300-800℃(优选为400-600℃),时间为1-10h(优选为3-5h)。根据本发明,优选情况下,所述负载型Ni系催化剂的体积空速(以裂解气计)为100-5,000h-1,优选为800-2,000h-1。根据本发明,本发明对所述加氢处理的条件并没有特别的限定,只要能够使得裂解气中的炔烃和二烯烃非选择地加氢为单烯烃和/或烷烃即可,为了即可以获得较好的加氢效果,又可以获得较好的脱硝效果,步骤(1)中,所述非选择性加氢的温度为200-450℃,更优选为200-350℃。根据本发明,经过加氢后的裂解气将获得炔烃和二烯烃基本都不存在的裂解气,这样可以更为安全地进行燃烧,优选地,所述加氢后的裂解气中,C1-C4的烷烃的含量为40-70体积%(优选为55-70体积%),C2-C4的炔烃和二烯烃的含量为0.1体积%以下(优选为0.001体积%以下),C2-C4的单烯烃的含量为20-60体积%(优选为30-40体积%)(该体积含量是在不计氢气下所得)。在本发明的一种实施方式中,当采用石脑油蒸汽裂解产生的尾气经过气液分离处理后的裂解气作为本发明的裂解气时,所述加氢后的裂解气中,CO的含量为0.1体积%以下,甲烷的含量为30-40体积%,乙烷的含量为10-20体积%,乙烯的含量为20-40体积%(例如25-35体积%),乙炔的含量为0.2体积%以下(优选为0.001体积%以下),丙烷的含量为1-10体积%(例如5-8体积%),丙烯的含量为1-10体积%(例如4-7体积%),丙二烯和丙炔的含量为0.1体积%以下(优选为0.001体积%以下),丁烷(包括正丁烷和异丁烷)的含量为5体积%以下,丁烯(包括正丁烯、异丁烯、顺-2-丁烯和反-2-丁烯)的含量为0.5体积%以下(优选为0.1体积%以下),1,3-丁二烯的含量为0.1体积%以下(优选为0.001体积%以下),C5以上的烃类含量为3体积%以下(该体积含量是在不计氢气下所得)。根据本发明,将上述成分含量范围的加氢后的裂解气与空气进行燃烧可以获得更高的安全性,且可以使得燃烧后的尾气基本没有有害气体,符合尾气的VOC排放标准。优选情况下,所述加氢后的裂解气的体积流量为0.1-100m3/h(优选为0.5-50m3/h,更优选为1-10m3/h),空气的体积流量为10-2000m3/h(优选为20-200m3/h,更优选为40-100m3/h)。根据本发明,步骤(2)中的燃烧反应在负载型Pd-Pt系催化剂存在下进行,所述负载型Pd-Pt系催化剂具有良好的低温催化起燃作用,本发明对所述负载型Pd-Pt系催化剂并无特别的限定,只要能够催化所述燃烧反应、并且获得较好的低温催化起燃作用即可,优选地,步骤(2)中,所述负载型Pd-Pt系催化剂为在具有Al2O3涂层的蜂窝型堇青石上负载有Pd和Pt的Pd/Pt-Al2O3催化剂,其中,以所述Pd/Pt-Al2O3催化剂的总重量为基准,,Pd元素的含量为0.01-1重量%(优选为0.5-1重量%),Pt元素的含量为0.01-1重量%(优选为0.5-1重量%)。其中,提供Al2O3的可以是γ-Al2O3、α-Al2O3、θ-Al2O3和η-Al2O3中的一种或多种,优选为γ-Al2O3。以所述Pd-Pt催化剂的总重量为基准,Al2O3的含量为1-20重量%,更优选为5-15重量%,更进一步优选为8-10重量%。其中,所述负载型Pd-Pt系催化剂可以是市售品,也可以是本领域常规的方法制得,优选地,所述负载型Pd-Pt系催化剂的制备方法包括:(a-1)将拟薄水铝石的浆体涂覆在蜂窝型堇青石(可以采用蜂窝型堇青石陶瓷)上,干燥后进行焙烧,得到具有含铝涂层的蜂窝型堇青石,以作为载体;(b-1)将含钯化合物和含铂化合物的溶液涂覆在上述载体上,干燥后焙烧,从而制得负载型Pd-Pt系催化剂。其中,所述含钯化合物例如可以为硝酸钯、氯化钯、四氯钯酸钠和乙酰丙酮钯中的一种或多种。所述含铂化合物例如可以为氯铂酸、四氯合铂酸钾和六氯合铂酸钾中的一种或多种。采用的溶液的溶剂可以为水、甲醇、乙醇、乙二醇和异丙醇中的一种或多种。对所述含钯化合物的溶液的浓度没有特别的限定,只要能够制备得到负载型Pd-Pt系催化剂即可,例如所述含钯化合物的浓度可以为0.01-3重量%(优选为1-3重量%),含铂化合物的浓度可以为0.01-3重量%(优选为1-3重量%)。其中,步骤(a-1)的载体的蜂窝型堇青石载体的制备如上文中步骤(a)所描述的,这里不再赘述。步骤(b-1)中,将含钯化合物和含铂化合物的溶液涂覆在步骤(a-1)制得的载体上可以采用本领域常规的方式进行,例如采用浸渍的方式。其中,优选情况下,所述含钯化合物和含铂化合物的溶液和载体的用量,使得最后所得的负载型Pd-Pt系催化剂中,Pd元素的含量为0.01-1重量%(优选为0.5-1重量%),Pt元素的含量为0.01-1重量%(优选为0.5-1重量%)。其中,步骤(b-1)中,干燥的条件优选包括:温度为60-240℃(优选为100-150℃),时间为0.5-24h(优选为2-12h,更优选为3-5h)。的焙烧的条件优选包括:温度为300-800℃(优选为400-600℃),时间为1-10h(优选为3-5h)。根据本发明,所述负载型Pd-Pt系催化剂的体积空速(以加氢后的裂解气计)为1,000-100,000h-1,更优选为1,000-10,000h-1,更进一步优选为2,000-3,000h-1。根据本发明,为了能够使得加氢后的裂解气与空气达到起燃点,优选地,在进行燃烧反应前,将空气和裂解气加热至120-200℃,优选为120-160℃,更优选为120-140℃,。而当燃烧反应进行的过程中,便不需要进行这样的加热,因为,所述燃烧反应一旦开始,能够为后续的气体的燃烧提供足够的热量达到燃点。根据本发明,为了能够更好地控制燃烧反应,优选地,该方法还包括采用冷却水将燃烧反应后的气体的温度控制在850℃以下,优选控制在450-800℃。提供冷却水的方式可以采用本领域常规的方式,例如可以设置在进行所述燃烧反应的装置的周围或内部设置冷却水的流通管道,从而便于冷却水携带热量。特别是当温度超高850℃时,需要尽可能地提高冷却水的流速和流量,以尽快降温,防止负载型Pd-Pt系催化剂失活。根据本发明,优选情况下,该方法包括在裂解气的处理系统中进行生产低碳烯烃产生的裂解气的处理,该系统包括:加氢反应单元R2,用于进行所述非选择性加氢处理;燃烧反应单元R3,用于进行所述燃烧反应。如图1所示,如果所述方法包括上文中提及的气液分离处理的过程,那么该系统还可以包括气液分离单元,以将生产低碳烯烃产生的尾气进行气液分离得到本发明所述的裂解气。生产低碳烯烃产生的尾气从气液分离单元的上部进入、下部流出,重组分(主要为甲苯、二甲苯、碳八芳烃、裂解汽油、裂解柴油和燃料油等)以液态的形式回收,轻组分以气态的形式流出即从侧线流出的裂解气进入到加氢反应单元R2。其中,所述加氢反应单元R2可以是加氢固定床反应器,其中填充有用于非选择性加氢反应催化的负载型Ni系催化剂,而裂解气从加氢固定床反应器的下部进入,上部流出,上部流出的加氢后的裂解气进入到燃烧反应单元R3中。其中,所述燃烧反应单元R3可以是填充有负载型Pd-Pt系催化剂的固定床反应器,该燃烧反应单元R3优选包括设置在下部的起燃段R3A和设置在上部的飞温段R3B,其中,所述加氢后的裂解气和空气从起燃段R3A的下部进入并在起燃段R3A开始燃烧。其中,所述飞温段R3B用于将燃烧反应后的气体的温度控制在850℃以下,优选控制在450-800℃,也即上文中提及的冷却水可以配置在飞温段R3B,以控制温度。为了能够更好地实现对裂解气的燃烧处理,在飞温段R3B的燃烧后的尾气排出口处还配置有VOC报警仪和温度报警仪,从而当VOC超标时,可以控制冷却水的流量和流速小点,以提高温度使得VOC足以燃烧掉;如果温度过高,则控制冷却水的流量和流速高点,以降低温度保证安全。通过本发明的方法能够较好地避免因裂解气直接燃烧存在安全隐患的问题,且该方法特别适用于石油化工小试和中试试验,有利于环境保护。以下将通过实施例对本发明进行详细描述。以下实施例和对比例中,以下实施例采用的是图1所示的裂解气的处理系统,其中加氢反应单元R2为填充有加氢催化剂的固定床反应器,其配置有加热装置以便为加氢反应提供热量,该固定床反应器底部设置有裂解气入口,以使得经过气液分离单元的裂解气由此进入,其顶部设置有气体出口,以使得加氢后的裂解气由该出口流出;燃烧反应单元为填充有负载型Pd-Pt系催化剂的固定床反应器,该固定床范围两个区域,下半段(约占整个固定床反应器的1/2体积)为燃烧段R3A,上半段(即该固定床反应器的另外的1/2体积)为飞温段R3B,飞温段R3B配置有冷却水的流通管道,以及在尾气出口处设置有VOC报警仪和温度报警仪,且该反应器的下部设置有裂解气入口,底部设置有空气入口,从而使得加氢后的裂解气和空气在燃烧段R3A开始燃烧,燃烧后的气体通过飞温段R3B时进行温度的控制。以下对比例采用图2所示的裂解气的处理系统,与图1不同的是,不采用加氢反应单元而是直接将气液分离后的裂解气送入燃烧反应器中。制备例1本制备例用于说明本发明采用的加氢催化剂。(a)将150g的拟薄水铝石粉体(购自淄博泰光化工有限公司GL-2牌号)和1000g水在球磨机(南京莱步科技实业有限公司QM型号)中以50rpm转速球磨2h,得到悬浮状的浆体,将该浆体采用浸渍方式涂覆在1000g蜂窝型堇青石陶瓷(购自江西兴丰化工填料公司方孔型载体)上,并在120℃下干燥12h,并于挤条机中挤出成型,再在600℃下焙烧6h,得到具有γ-Al2O3涂层的蜂窝型堇青石载体。(b)将含20重量%的硝酸镍、25重量%的硝酸锌和0.2重量%的三氧化二锑的水溶液以喷涂的方式涂覆在步骤(a)所得的载体上,然后于120℃下干燥4h,再于500℃下焙烧4h,从而获得负载有Ni、Zn和Sb的加氢催化剂C1,以该催化剂的总量为基准,以NiO计的Ni元素的含量为2重量%,以ZnO计的Zn元素的含量为2重量%,以Sb2O3计的Sb元素的含量为0.01重量%,γ-Al2O3的含量为10重量%。制备例2本制备例用于说明本发明采用的加氢催化剂。根据制备例1所述的方法,不同的是,步骤(b)的溶液中不含有三氧化二锑,从而获得负载有Ni和Zn的加氢催化剂C2,以该催化剂的总量为基准,以NiO计的Ni元素的含量为2重量%,以ZnO计的Zn元素的含量为2重量%,γ-Al2O3的含量为10重量%。制备例3本制备例用于说明本发明采用的加氢催化剂。根据制备例1所述的方法,不同的是,步骤(b)的溶液中还含有5重量%的硝酸铜,从而获得负载有Ni、Zn、Sb和Cu的加氢催化剂C3,以该催化剂的总量为基准,以NiO计的Ni元素的含量为2.5重量%,以ZnO计的Zn元素的含量为2.5重量%,以Sb2O3计的Sb元素的含量为0.01重量%,以CuO计的Cu元素的含量为0.5重量%,γ-Al2O3的含量为10重量%。制备例4根据制备例1的步骤(a)的制备方法制得载体;(b)将含0.02重量%的硝酸钯和0.04重量%的硝酸银的水溶液以喷涂的方式涂覆在步骤(a)所得的载体上,然后于120℃下干燥4h,再于500℃下焙烧4h,从而获得负载有Pd和Ag的加氢催化剂DC1,以该催化剂的总量为基准,Pd元素的含量为0.02重量%,Ag元素的含量为0.04重量%,γ-Al2O3的含量为10重量%。制备例5本制备例用于说明本发明采用的负载型Pd-Pt系催化剂。(a)将100g的拟薄水铝石粉体(购自淄博泰光化工有限公司GL-1牌号)和400g水在球磨机(南京莱步科技实业有限公司QM型号)中以50rpm转速球磨2h,得到悬浮状的浆体,将该浆体采用浸渍的方式涂覆在1000g蜂窝型堇青石陶瓷(购自江西兴丰化工填料公司方孔型载体)上,并在120℃下干燥24h,并于挤条机中挤出成型,再在700℃下焙烧6h,得到具有γ-Al2O3涂层的蜂窝型堇青石载体。(b)将步骤(a)所得的载体在含1重量%的氯铂酸和1重量%的氯化钯的水溶液中浸渍12h,然后于120℃下干燥4h,再于500℃下焙烧4h,从而制得Pd/Pt-Al2O3催化剂C4,以该催化剂的总量为基准,Pd元素的含量为0.5重量%,Pt元素的含量为0.5重量%,γ-Al2O3的含量为9重量%。实施例1本实施例用于说明本发明的生产低碳烯烃产生的裂解气的处理方法。采用图1所示的裂解气的处理系统,将表1所示成分组成的石脑油蒸汽裂解气通过气液分离后所得气相(成分见表1所示)从加氢反应单元的底部入口进入,在加氢催化剂存在下进行加氢,加氢后的裂解气从加氢反应单元的顶部出口排出,并从燃烧反应单元下部入口进入,以与从燃烧反应单元底部入口进入的空气在燃烧段起燃,燃烧后的气体通过飞温段之后从飞温段的顶部出口排出,其中:加氢反应单元:气液分离后的裂解气以5m3/h的体积流量通入到加氢反应单元中;采用的加氢催化剂为加氢催化剂C1,装填量为5L,占加氢反应的固定床的80体积%,催化剂的体积空速为1,000h-1(以裂解气计);加氢反应的温度为225℃;燃烧反应单元:采用的催化剂为催化剂C4,装填量为2L(燃烧段和飞温段各一半),占燃烧反应的固定床的60体积%,催化剂的体积空速为2,500h-1(以加氢后的裂解气计);燃烧段:加氢后的裂解气以4m3/h的体积流量通入到燃烧段,空气以46m3/h的体积流量通入到燃烧段;加热温度为125℃;飞温段:控制排出的燃烧后的气体的温度为600-800℃。运行100h,其中,加氢反应单元排出的加氢后的裂解气的成分见表2所示,其气体乙炔转化率、乙烯转化率、丙烯转化率见表3所示,燃烧反应单元排出的燃烧后的尾气中甲烷含量、乙烯含量、丙烯含量见表3所示。实施例2本实施例用于说明本发明的生产低碳烯烃产生的裂解气的处理方法。根据实施例1所述的方法,所不同的是,加氢反应单元采用的加氢催化剂为加氢催化剂C2,从而加氢反应单元排出的加氢后的裂解气的成分见表2所示,其气体乙炔转化率、乙烯转化率、丙烯转化率见表3所示,燃烧反应单元排出的燃烧后的尾气中甲烷含量、乙烯含量、丙烯含量见表3所示。实施例3本实施例用于说明本发明的生产低碳烯烃产生的裂解气的处理方法。根据实施例1所述的方法,所不同的是,加氢反应单元采用的加氢催化剂为加氢催化剂C3,从而加氢反应单元排出的加氢后的裂解气的成分见表2所示,其气体乙炔转化率、乙烯转化率、丙烯转化率见表3所示,燃烧反应单元排出的燃烧后的尾气中甲烷含量、乙烯含量、丙烯含量见表3所示。对比例1根据实施例1所述的方法,不同的是,加氢反应单元采用的加氢催化剂为加氢催化剂DC1,从而加氢反应单元排出的加氢后的裂解气的成分见表2所示,其气体乙炔转化率、乙烯转化率、丙烯转化率见表3所示,燃烧反应单元排出的燃烧后的尾气中甲烷含量、乙烯含量、丙烯含量见表3所示。对比例2根据实施例1所述的方法,不同的是,采用图2所示的系统,即不包括加氢反应单元和加氢反应的步骤,从而燃烧反应单元排出的燃烧后的尾气中甲烷含量、乙烯含量、丙烯含量见表3所示。表1:石脑油蒸汽裂解气通过气液分离后所得气相成分的重量百分含量(重量%)H216.99异丁烷0.06CO0.04正丁烷0.12CO20正丁烯0.35CH429.96异丁烯0.65乙烷6.17反-2-丁烯0.11乙烯32.48顺-2-丁烯0.08乙炔0.541,3-丁二烯1.28丙烷0.5C5以上烃类1.19丙烯9.02苯0.05丙二烯和丙炔0.4甲苯0.03注:此处的C5以上烃类的含量不计算甲苯和苯的量。表2:经过加氢后的裂解气的气体成分的体积百分含量(体积%,1h)实施例1实施例2实施例3对比例1H2////CO0.0430.040.0410.048CO20000CH436.09636.09636.09636.096乙烷15.9116.6919.0419.82乙烯31.3130.5228.1827.39乙炔0000.48丙烷6.35.977.68.15丙烯5.655.984.353.8丙二烯和丙炔0000异丁烷0.2910.2880.2920.301正丁烷2.0691.9621.982.109正丁烯0.020.090.010异丁烯0.040.130.020反-2-丁烯0000顺-2-丁烯00001,3-丁二烯0000C5以上烃类1.431.4251.3891.435苯0.050.040.040甲苯0.0060.0120.0090注:此处的C5以上烃类的含量不计算甲苯和苯的量;进行体积含量计算时,不计H2含量。表3*尾气含量进行体积计算时,不包含N2、O2和H2O。通过表1-3的数据对比可以看出,本发明的方法,通过先对裂解气非选择性加氢然后再进行燃烧的方式,能够获得更好地低碳烯烃产生的裂解气的处理效果,其燃烧尾气中的烃类含量得到非常明显地降低。而采用了Sb的负载型Ni系催化剂进行加氢比不采用Sb的负载型Ni系催化剂进行加氢的方法来说,具有更好的加氢稳定性,从而在长周期运行(如100小时以上)后,尾气的处理效果更好些。以上详细描述了本发明的优选实施方式,但是,本发明并不限于上述实施方式中的具体细节,在本发明的技术构思范围内,可以对本发明的技术方案进行多种简单变型,这些简单变型均属于本发明的保护范围。另外需要说明的是,在上述具体实施方式中所描述的各个具体技术特征,在不矛盾的情况下,可以通过任何合适的方式进行组合,为了避免不必要的重复,本发明对各种可能的组合方式不再另行说明。此外,本发明的各种不同的实施方式之间也可以进行任意组合,只要其不违背本发明的思想,其同样应当视为本发明所公开的内容。当前第1页1 2 3