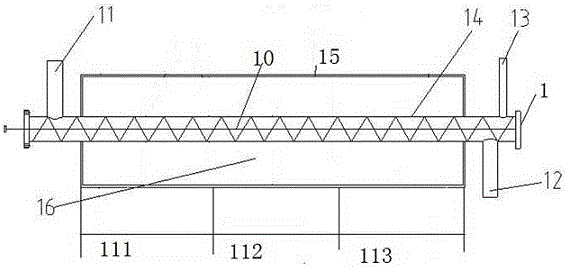
本发明涉及热解领域,尤其指一种电子垃圾热解回收处理的系统及方法。
背景技术:
:经济的发展和科技的进步使得电子工业迅猛发展,因此电子废弃物也成为世界上增长最快的垃圾之一。电子废弃物俗称电子垃圾,主要由废弃的家用电器、通信工具、电池类产品等组成,涵盖了生活各个领域废旧电子电器设备以及工业制造领域产生的电子电器废品或者报废品,成分复杂,种类繁多。其中含有大量可利用的聚酯、塑料、玻璃、贵金属等资源,随意处置会给环境带来潜在的危害,又必然造成资源的极大浪费,合理有效的利用电子废弃物已成当务之急。近年来,随着能源与资源的短缺和环境污染的日益严重,寻找可替代能源和资源已成为世界各国亟待解决的问题。为缓解资源与发展的矛盾,世界各国对资源的循环利用越来越重视,大力发展循环经济,改变传统的“资源-产品-排放”的线性经济模式,建立“资源-产品-再生资源”强调资源永续利用的闭环流动经济模式,把电子垃圾当做次生资源看待,通过回收循环利用可节约资源,以减少对原生资源的开采,从而缓解资源开采带来的环境压力。目前,国内外有很多对电子垃圾处理技术的研究,主要集中在对其中贵金属和一般金属的分离提取,而对处理困难且经济效益相对较低的非金属部分的利用研究则较少。因此,如何设计一种高效回收处理电子垃圾、系统结构和工艺流程都简单的系统成为本领域亟需解决的问题。技术实现要素:本发明的目的是针对现有技术的不足,提供一种电子垃圾热解回收处理的系统及方法,该系统回收电子垃圾中金属的同时对非金属部分进行热解回收处理,综合利用电子垃圾中的有效资源,变废为宝,且该方法具有热解效率高、节能效果显著等优点。为解决上述技术问题,本发明采用的技术方案为:本发明提出了一种电子垃圾热解回收处理的系统。根据本发明的实施例,该系统包括:原料处理系统、金属回收系统和有机质反应系统;其中,所述原料处理系统包括破碎装置和分选装置,用于将电子垃圾分选为金属部分和有机质部分;所述金属回收系统包括酸浸池和电解池,用于将分选得到的金属部分送入所述酸浸池中,向其中加入强酸溶液,金属被完全溶解后,剩余的不含金属部分经所述有机质反应系统产生的烟气干燥后,与所述的有机质部分混合,进入所述有机质反应系统进行热解反应,金属溶解后得到的富含金属离子的强酸溶液送入所述电解池中进行电解反应,回收金属铜;所述有机质反应系统包括:电子垃圾热解反应器、蓄热式燃气加热系统和冷却分离系统,其中,所述电子垃圾热解反应器包括:物料热解组件和反应器壳体,所述物料热解组件横跨所述反应器壳体的两侧,并且所述物料热解组件的两个末端裸露在所述反应器壳体的外部,所述物料热解组件包括螺旋壳体和物料推进螺旋,其中,所述螺旋壳体自所述反应器壳体一侧沿所述反应器壳体内腔延伸穿过所述反应器壳体的另一侧,所述螺旋壳体的两个末端裸露在所述反应器壳体的外部,使得所述反应器壳体与所述螺旋壳体之间形成密闭空间,所述密闭空间构成所述蓄热式燃气加热系统的反应器壳体烟气通道;所述蓄热式燃气加热系统包括:用于产生热烟气的蓄热式燃烧装置和用于输送热烟气的反应器壳体烟气通道,其中燃气和空气经预热后进入所述燃烧装置进行燃烧产生热烟气,并通过所述热烟气在所述反应器壳体烟气通道里输送来加热所述电子垃圾热解反应器;所述冷却分离系统包括:气体产物冷却分离系统和固体产物冷却分离系统;其中,所述气体产物冷却分离系统包括间接换热器和用于将高温气体产物经冷却得到不凝气和焦油的冷却塔,所述间接换热器的入口与所述电子垃圾热解反应器相连,出口与所述冷却塔的入口相连,所述冷却塔的出气口与所述蓄热式燃气加热系统相连;所述固体产物冷却分离系统包括冷却室,用于对高温固体产物进行冷却处理得到固体产品。发明人发现,根据本发明实施例的该系统,将电子垃圾分为有机质和金属部分分别处理,充分回收电子垃圾中的有效资源;可实现稳定、连续、高效的处理电子垃圾,可根据需要满足不同处理量的要求。本发明的系统在热解过程中,物料随着螺旋推进器在反应器内翻动,受热均匀,能够充分热解,同时,在物料推进螺旋转动的机械力作用下,可以避免热解过程中物料结焦,导致出料不畅或出料口堵塞等问题;利用反应过程产生的不凝气,并采用蓄热式燃烧系统对反应器进行加热,充分利用燃烧过程中产生的高温烟气的余热,提高燃料利用率,同时,利用所述蓄热室回收余热的烟气干燥经酸浸后的有机质部分,能源利用效率高。根据本发明的实施例,裸露在所述反应器壳体外部的所述螺旋壳体上设置有物料进口、油气出口、渣料出口,并且所述物料进口位于所述螺旋壳体右上部,所述油气出口位于所述螺旋壳体左上部,所述渣料出口位于所述螺旋壳体左下部;所述蓄热式燃气加热系统在所述反应器壳体上设有进气口和出气口,所述进气口位于所述反应器壳体右上部,所述出气口位于所述反应器壳体左上部;所述物料推进螺旋位于所述螺旋壳体内部,并且所述物料推进螺旋包括螺旋轴和螺旋叶片,所述螺旋叶片固定于所述螺旋轴上并被设置为可与所述螺旋轴同轴转动,所述螺旋轴在所述物料进口一侧伸出所述螺旋壳体,所述螺旋叶片的长度与所述螺旋壳体相同。根据本发明的实施例,所述蓄热式燃气加热系统还包括蓄热室,所述蓄热室的进气口与所述冷却塔上的出气口相连,出气口与所述酸浸池的出口相连,用于利用部分经所述蓄热室回收余热的烟气对所述酸浸池得到的不含金属的有机质进行干燥;优选的,经所述蓄热室回收余热后的烟气温度为90-140℃。根据本发明的实施例,所述强酸溶液为王水、硫酸、盐酸、硝酸、过氧化氢等强酸或强氧化溶液或两者的混合物,溶液浓度0.5-2mol/L。根据本发明的实施例,所述燃气加热系统在长度方向上分为至少三个区,并能分别控制各区的升温速度。根据本发明的实施例,所述螺旋壳体是耐热钢壳体,厚度是5-8mm;所述反应器壳体的外部包裹有保温材料,优选的,所述保温材料是保温棉,且所述保温棉外用镀锌铁板包裹。根据本发明的实施例,所述电解池中阳极材料可以为石墨、Pd-Ag合金或者钛材,阴极材料可以为铜板或不锈钢板;所述电解池的电压范围0.1-3V,电流密度为1-10A/dm2,电解池内温度为20-80℃。根据本发明的实施例,所述不凝气富含甲烷、氢气和一氧化碳的可燃性和还原性气体,其一部分用于所述加热系统原料燃气,加热自身循环利用,另一部分可用作还原气。在本发明的另一个方面,本发明提供了一种利用前面所述的电子垃圾热解回收处理的系统对电子垃圾进行热解回收的方法。根据本发明的实施例,该方法包括以下步骤:(1)原料处理:电子垃圾原料进入所述破碎装置进行破碎,再经过分选装置进行筛分,得到金属和有机质;(2)金属回收:将金属部分送入酸浸池中,金属被完全溶解后,剩余的不含金属部分经烟气干燥后,与所述有机质部分混合,所述有机质反应系统进行热解反应,金属溶解后得到的富含金属离子的强酸溶液送入电解池中进行电解反应,回收金属铜;(3)开启蓄热式燃气加热系统:燃气和空气进入所述蓄热式燃气加热系统进行燃烧,产生高温烟气,加热所述电子垃圾热解反应器;(4)有机质热解过程:所述蓄热式燃气加热系统稳定后,螺旋壳体被加热,在物料进口放入所述电子垃圾原料的有机质部分,所述有机质部分进入到推进螺旋之后边向前移动边被热解,直至移动到渣料出口被热解完毕,得到固体产物和气体产物;(5)热解产物的冷却分离:高温气体产物进入气体产物冷却分离系统,依次经过间接换热器和冷却塔进行冷却处理,得到不凝气和焦油;固体产物进入固体产物冷却分离系统,在冷却室进行冷却处理,得到固体产品。根据本发明的实施例,所述步骤(1)中,电子垃圾原料被破碎为0-30mm的电子垃圾颗粒;所述步骤(3)中,在开启所述蓄热式燃气加热系统初期,所述燃气为天然气、液化石油气或焦炉煤气;所述步骤(4)中,在所述蓄热式燃气加热系统稳定后,所述燃气为热解气,所述电子垃圾热解反应器被加热到600-700℃,并且所述反应器内压力控制在0.1MPa以内。本发明至少具有以下有益效果:(1)可实现稳定、连续、高效的处理电子垃圾,可根据需要满足不同处理量的要求。(2)将电子垃圾分为有机质和金属部分分别处理,充分回收电子垃圾中的有效资源。(3)热解过程中物料随着螺旋推进器在反应器内翻动,受热均匀,能够充分热解。同时,在螺旋推进器转动的机械力作用下,可以避免热解过程中物料结焦,导致出料不畅或出料口堵塞等问题。(4)利用反应过程产生的不凝气,并采用蓄热式燃烧系统对反应器进行加热,充分利用燃烧过程中产生的高温烟气的余热,提高燃料利用率,同时,利用所述蓄热室回收余热的烟气干燥经酸浸后的有机质部分,能源利用效率高。附图说明图1是根据本发明实施例的电子垃圾热解前处理回收金属的工艺流程图。图2是根据本发明实施例的电子垃圾热解反应器的侧视图。其中,1、电子垃圾热解反应器,10、推进螺旋,11、物料进口,12、渣料出口,13、油气出口,14、螺旋壳体,15、反应器壳体,16、烟气通道,111、一区,112、二区,113、三区。具体实施方式为了使本领域技术人员更好地理解本发明的技术方案,下面结合具体实施例对本发明作进一步的详细说明。下面描述的实施例是示例性的,仅用于解释本发明,而不能理解为对本发明的限制。本发明提出了一种电子垃圾热解回收处理的系统。根据本发明的实施例,图1是根据本发明实施例的电子垃圾热解前处理回收金属的工艺流程图,参照图1所示,该系统包括:原料处理系统、金属回收系统和有机质反应系统;其中,所述原料处理系统包括破碎装置和分选装置,用于将电子垃圾分选为金属部分和有机质部分;所述金属回收系统包括酸浸池和电解池,用于将分选得到的金属部分送入所述酸浸池中,向其中加入强酸溶液,金属被完全溶解后,剩余的不含金属部分经所述有机质反应系统产生的烟气干燥后,与所述的有机质部分混合,进入所述有机质反应系统进行热解反应,金属溶解后得到的富含金属离子的强酸溶液送入所述电解池中进行电解反应,回收金属铜;所述有机质反应系统包括:电子垃圾热解反应器1、蓄热式燃气加热系统和冷却分离系统,其中,图2是根据本发明实施例的电子垃圾热解反应器的侧视图,如图2所示,所述电子垃圾热解反应器1包括:物料热解组件和反应器壳体15,所述物料热解组件横跨所述反应器壳体的两侧,并且所述物料热解组件的两个末端裸露在所述反应器壳体的外部,所述物料热解组件包括螺旋壳体14和物料推进螺旋10,其中,所述螺旋壳体自所述反应器壳体一侧沿所述反应器壳体内腔延伸穿过所述反应器壳体的另一侧,所述螺旋壳体的两个末端裸露在所述反应器壳体的外部,使得所述反应器壳体与所述螺旋壳体之间形成密闭空间,所述密闭空间构成所述蓄热式燃气加热系统的反应器壳体烟气通道16;所述蓄热式燃气加热系统包括:用于产生热烟气的蓄热式燃烧装置和用于输送热烟气的反应器壳体烟气通道,其中燃气和空气经预热后进入所述燃烧装置进行燃烧产生热烟气,并通过所述热烟气在所述反应器壳体烟气通道里输送来加热所述电子垃圾热解反应器;所述冷却分离系统包括:气体产物冷却分离系统和固体产物冷却分离系统;其中,所述气体产物冷却分离系统包括间接换热器和用于将高温气体产物经冷却得到不凝气和焦油的冷却塔,所述间接换热器的入口与所述电子垃圾热解反应器相连,出口与所述冷却塔的入口相连,所述冷却塔的出气口与所述蓄热式燃气加热系统相连;所述固体产物冷却分离系统包括冷却室,用于对高温固体产物进行冷却处理得到固体产品。发明人发现,根据本发明实施例的该系统,将电子垃圾分为有机质和金属部分分别处理,充分回收电子垃圾中的有效资源;可实现稳定、连续、高效的处理电子垃圾,可根据需要满足不同处理量的要求。本发明的系统在热解过程中,物料随着螺旋推进器在反应器内翻动,受热均匀,能够充分热解,同时,在物料推进螺旋转动的机械力作用下,可以避免热解过程中物料结焦,导致出料不畅或出料口堵塞等问题;利用反应过程产生的不凝气,并采用蓄热式燃烧系统对反应器进行加热,充分利用燃烧过程中产生的高温烟气的余热,提高燃料利用率,同时,利用所述蓄热室回收余热的烟气干燥经酸浸后的有机质部分,能源利用效率高。根据本发明的实施例,参照图1所示,所述原料处理系统包括破碎装置和分选装置,所述原料处理系统的分选装置分别与金属回收系统和有机质反应系统连接,用于将电子垃圾拆解、破碎、分选为金属部分和有机质部分。根据本发明的具体实施例,电子垃圾原料经过简单拆解后送入破碎装置中进行破碎,将原料破碎至0-30mm的电子垃圾颗粒,然后将电子垃圾颗粒进入分选装置进行分选,将之分选为金属部分和有机质部分,分选得到的所述金属部分进入所述金属回收系统进行金属回收处理,分选得到的所述有机质部分送入所述有机质反应系统进行热解反应回收利用。进一步的,所述分选装置可以选用磁选设备。根据本发明的具体实施例,所述原料处理系统可处理家用电器、信息技术和远程通讯设备、电子电器设备、检测控制器械、医用设备等废弃的电子垃圾。根据本发明的实施例,参照图1所示,所述金属回收系统,包括酸浸池和电解池,用于将分选得到的金属部分送入所述酸浸池中,向其中加入强酸溶液,金属被完全溶解后,剩余的不含金属部分经所述有机质反应系统产生的烟气干燥后,与所述的有机质部分混合,进入所述有机质反应系统进行热解反应,金属溶解后得到的富含金属离子的强酸溶液送入所述电解池中进行电解反应,回收金属铜等。根据本发明的实施例,所述电解池中阳极材料可以为石墨、Pd-Ag合金或者钛材,阴极材料可以为铜板或不锈钢板;所述电解池的电压范围0.1-3V,电流密度为1-10A/dm2,电解池内温度为20-80℃。所述电解池可以根据目标产物或者产物纯度要求的不同,选择适合的阳极、阴极材料,采用上述方法可以回收电子垃圾中目标金属含量的95%~100%。根据本发明的具体实施例,所述电解池1中阳极材料为石墨,阴极材料为铜板。该电解池的电压范围,电流密度为3A/dm2,电解池内温度为35℃。在电解池1中可以回收较为纯净的铜,产物铜的纯度接近100%,回收所得的金属铜的回收率约98%。根据本发明的具体实施例,所述电解池2中阳极材料为石墨,阴极材料为纯金板。该电解池的电压为1V,电流密度为8A/dm2,电解池内温度为70℃。在电解池1中可以回收较为纯净的金,产物金的纯度接近100%,回收所得的贵金属金的回收率约98%。根据本发明的实施例,所述酸浸池中的所述强酸溶液为王水、硫酸、盐酸、硝酸、过氧化氢等强酸或强氧化溶液或两者的混合物,溶液浓度0.5-2mol/L。向所述富含金属离子的强酸溶液中加入碱性固体物质,调节溶液的PH值至中性或弱酸性,以便减轻对后续工段设备、管道的腐蚀作用。根据本发明的具体实施例,所述酸浸池的出口与蓄热室的出气口相连,用于利用部分经所述蓄热室回收余热的烟气对所述酸浸池得到的不含金属的有机质进行干燥。酸浸池中的非金属部分,经沥干、清洗后,由所述蓄热室回收余热的烟气脱除有机质表面残留的酸液并对其进行干燥,以免腐蚀后续设备及管道,得到纯净的不含金属的固体部分。优选的,经所述蓄热室回收余热后的烟气温度为90-140℃。根据本发明的实施例,所述有机质反应系统包括:电子垃圾热解反应器1、蓄热式燃气加热系统和冷却分离系统,用于对电子垃圾的有机质部分进行热解反应回收利用。根据本发明的实施例,图2是根据本发明实施例的电子垃圾热解反应器的侧视图,如图2所示,所述电子垃圾热解反应器1包括:物料热解组件和反应器壳体15,所述物料热解组件横跨所述反应器壳体的两侧,并且所述物料热解组件的两个末端裸露在所述反应器壳体的外部,所述物料热解组件包括螺旋壳体14和物料推进螺旋10,其中,所述螺旋壳体自所述反应器壳体一侧沿所述反应器壳体内腔延伸穿过所述反应器壳体的另一侧,所述螺旋壳体的两个末端裸露在所述反应器壳体的外部,使得所述反应器壳体与所述螺旋壳体之间形成密闭空间,所述密闭空间构成所述蓄热式燃气加热系统的反应器壳体烟气通道16。进一步的,裸露在所述反应器壳体外部的所述螺旋壳体上设置有物料进口11、油气出口13、渣料出口12,并且所述物料进口位于所述螺旋壳体右上部,所述油气出口位于所述螺旋壳体左上部,所述渣料出口位于所述螺旋壳体左下部。根据本发明的具体实施例,所述螺旋壳体可以是耐热钢壳体,厚度是5-8mm;所述反应器壳体的外部包裹有保温材料,优选的,所述保温材料是保温棉,且所述保温棉外用镀锌铁板包裹。根据本发明的实施例,所述物料推进螺旋,用于对所述有机质部分向前推进。位于所述螺旋壳体内部,并且所述物料推进螺旋包括螺旋轴和螺旋叶片,所述螺旋叶片固定于所述螺旋轴上并被设置为可与所述螺旋轴同轴转动,所述螺旋轴在所述物料进口一侧伸出所述螺旋壳体,所述螺旋叶片的长度与所述螺旋壳体相同。根据本发明的具体实施例,电子垃圾热解反应器设置为螺旋推进形式,当系统正常工作时,物料在反应器内发生热解反应的同时随着物料推进螺旋向前推进,直至到达出料口。物料在反应器内受热发生热解反应,生成高温气体产物和高温固体产物,所述高温气体产物和高温固体产物分别从反应器末端的油气出口和渣料出口排出。进一步的,在热解反应过程中,反应器内压力控制在0.1MPa以内,通过设置在冷却塔后的引风机控制反应器内压力。由于物料在电子垃圾热解反应器内被平铺,与螺旋壳体接触充分,高温螺旋壳体通过辐射和导热两种方式给物料加热,因此,物料能够被充分快速的热解,且物料在热解过程中被推进螺旋逐渐向前推进,实现了边热解边推进的功能,从而保证了连续进出物料。根据本发明的实施例,所述蓄热式燃气加热系统,主要是通过燃气蓄热燃烧对所述电子垃圾热解反应器供热。所述蓄热式燃气加热系统包括:用于产生热烟气的蓄热式燃烧装置和用于输送热烟气的反应器壳体烟气通道,其中燃气和空气经预热后进入所述燃烧装置进行燃烧产生热烟气,并通过所述热烟气在所述反应器壳体烟气通道里输送来加热所述电子垃圾热解反应器。根据本发明的实施例,所述蓄热式燃气加热系统在所述反应器壳体上设有进气口和出气口,所述进气口位于所述反应器壳体右上部,所述出气口位于所述反应器壳体左上部;所述蓄热式燃气加热系统还包括蓄热室,所述蓄热室的进气口与所述冷却塔上的出气口相连,出气口与所述酸浸池的出口相连,用于利用部分经所述蓄热室回收余热的烟气对所述酸浸池得到的不含金属的有机质进行干燥;优选的,经所述蓄热室回收余热后的烟气温度为90-140℃。根据本发明的实施例,蓄热式燃气加热系统加热过程:空气和燃气分别通过空气管线和燃气管线进入蓄热室吸收热量,经预热后进入蓄热式燃烧装置混合燃烧,燃烧产生高温烟气通过所述反应器壳体上的进气口进入到反应器壳体内的烟气通道,用于加热所述电子垃圾热解反应器;反应器壳体烟气通道内的高温烟气加热所述电子垃圾热解反应器的同时被冷却,然后烟气通过所述冷却塔上的出气口进入到所述蓄热室,最后进入所述酸浸池,用于利用部分经所述蓄热室回收余热的烟气对所述酸浸池得到的不含金属的有机质进行干燥。根据本发明的具体实施例,在系统开始运行初期,所述燃气可以为天然气、液化石油气、焦炉煤气等燃料气,系统正常运行后,该燃气可以为电子垃圾热解所产生的气体产物经冷却、净化后得到的不凝气。根据本发明的实施例,所述燃气加热系统在长度方向上分为至少三个区,并能分别控制各区的升温速度。根据本发明的具体实施例,所述燃气加热系统在长度方向上分为三个区:一区111、二区112、三区113。根据物料的不同阶段升温要求,通过控制各个区蓄热式燃烧系统的燃烧强度来分别控制各区的升温速度。例如,一区升温速率设置为40-80℃/min,二区升温速率设置为30-60℃/min,三区升温速率设置为20-60℃/min。进一步的,所述蓄热式燃气加热系统将所述反应器的运行温度控制在600-700℃。根据本发明的实施例,所述冷却分离系统包括:气体产物冷却分离系统和固体产物冷却分离系统;其中,所述气体产物冷却分离系统包括间接换热器和用于将高温气体产物经冷却得到不凝气和焦油的冷却塔,所述间接换热器的入口与所述电子垃圾热解反应器相连,出口与所述冷却塔的入口相连,所述冷却塔的出气口与所述蓄热式燃气加热系统相连;所述固体产物冷却分离系统包括冷却室,用于对高温固体产物进行冷却处理得到固体产品。进一步的,所述不凝气富含甲烷、氢气和一氧化碳的可燃性和还原性气体,其一部分用于所述加热系统原料燃气,加热自身循环利用,另一部分可用作还原气。在本发明的另一个方面,本发明提供了一种利用前面所述的电子垃圾热解回收处理的系统对电子垃圾进行热解回收的方法,其特征在于,包括以下步骤:(1)原料处理:电子垃圾原料进入所述破碎装置进行破碎,再经过分选装置进行筛分,得到金属和有机质。根据本发明的具体实施例,电子垃圾原料经过简单拆解后送入破碎装置中进行破碎,将原料破碎至0-30mm的电子垃圾颗粒,然后将电子垃圾颗粒进入分选装置进行分选,将之分选为金属部分和有机质部分,分选得到的所述金属部分进入所述金属回收系统进行金属回收处理,分选得到的所述有机质部分送入所述有机质反应系统进行热解反应回收利用。(2)金属回收:将金属部分送入酸浸池中,金属被完全溶解后,剩余的不含金属部分经烟气干燥后,与所述有机质部分混合,所述有机质反应系统进行热解反应,金属溶解后得到的富含金属离子的强酸溶液送入电解池中进行电解反应,回收金属铜。根据本发明的实施例,所述电解池中阳极材料可以为石墨、Pd-Ag合金或者钛材,阴极材料可以为铜板或不锈钢板;所述电解池的电压范围0.1-3V,电流密度为1-10A/dm2,电解池内温度为20-80℃。所述电解池可以根据目标产物或者产物纯度要求的不同,选择适合的阳极、阴极材料,采用上述方法可以回收电子垃圾中目标金属含量的95%-100%。根据本发明的具体实施例,所述电解池1中阳极材料为石墨,阴极材料为铜板。该电解池的电压范围,电流密度为3A/dm2,电解池内温度为35℃。在电解池1中可以回收较为纯净的铜,产物铜的纯度接近100%,回收所得的金属铜的回收率约98%。根据本发明的具体实施例,所述电解池2中阳极材料为石墨,阴极材料为纯金板。该电解池的电压为1V,电流密度为8A/dm2,电解池内温度为70℃。在电解池1中可以回收较为纯净的金,产物金的纯度接近100%,回收所得的贵金属金的回收率约98%。根据本发明的具体实施例,酸浸池中的非金属部分,经沥干、清洗后,由所述蓄热室回收余热的烟气脱除有机质表面残留的酸液并对其进行干燥,以免腐蚀后续设备及管道,得到纯净的不含金属的固体部分。优选的,经所述蓄热室回收余热后的烟气温度为90-140℃。(3)开启蓄热式燃气加热系统:燃气和空气进入所述蓄热式燃气加热系统进行燃烧,产生高温烟气,加热所述电子垃圾热解反应器。根据本发明的实施例,所述蓄热式燃气加热系统包括:蓄热式燃烧装置和反应器壳体烟气通道,其中燃气和空气经预热后进入所述燃烧装置进行燃烧产生热烟气,并通过所述热烟气在所述反应器壳体烟气通道里输送来加热所述电子垃圾热解反应器。所述蓄热式燃气加热系统还包括蓄热室,利用部分经所述蓄热室回收余热的烟气对所述酸浸池得到的不含金属的有机质进行干燥;优选的,经所述蓄热室回收余热后的烟气温度为90-140℃。根据本发明的具体实施例,在开启所述蓄热式燃气加热系统初期,所述燃气为天然气、液化石油气或焦炉煤气等燃料气。系统正常运行后,该燃气可以为电子垃圾热解所产生的气体产物经冷却、净化后得到的不凝气。根据本发明的实施例,所述燃气加热系统在长度方向上分为至少三个区,并能分别控制各区的升温速度。根据本发明的具体实施例,所述燃气加热系统在长度方向上分为三个区:一区、二区、三区。根据物料的不同阶段升温要求,通过控制各个区蓄热式燃烧系统的燃烧强度来分别控制各区的升温速度。例如,一区升温速率设置为40-80℃/min,二区升温速率设置为30-60℃/min,三区升温速率设置为20-60℃/min。进一步的,所述蓄热式燃气加热系统将所述反应器的运行温度控制在600-700℃。(4)有机质热解过程:所述蓄热式燃气加热系统稳定后,螺旋壳体被加热,在物料进口放入所述电子垃圾原料的有机质部分,所述有机质部分进入到推进螺旋之后边向前移动边被热解,直至移动到渣料出口被热解完毕,得到固体产物和气体产物。根据本发明的具体实施例,电子垃圾热解反应器设置为螺旋推进形式,当所述蓄热式燃气加热系统稳定后,螺旋壳体被加热,高温螺旋壳体通过辐射和导热两种方式给物料加热,物料在反应器内发生热解反应的同时随着物料推进螺旋向前推进,直至到达出料口。物料在反应器内受热发生热解反应,生成高温气体产物和高温固体产物,所述高温气体产物和高温固体产物分别从反应器末端的油气出口和渣料出口排出。进一步的,在所述蓄热式燃气加热系统稳定后,所述燃气为热解气,所述电子垃圾热解反应器被加热到600-700℃,并且所述反应器内压力控制在0.1MPa以内。当系统正常工作时,物料在电子垃圾热解反应器内被平铺,与螺旋壳体接触充分,高温螺旋壳体通过辐射和导热两种方式给物料加热,因此,物料能够被充分快速的热解,且物料在热解过程中被推进螺旋逐渐向前推进,实现了边热解边推进的功能,从而保证了连续进出物料。(5)热解产物的冷却分离:高温气体产物进入气体产物冷却分离系统,依次经过间接换热器和冷却塔进行冷却处理,得到不凝气和焦油;固体产物进入固体产物冷却分离系统,在冷却室进行冷却处理,得到固体产品。根据本发明的实施例,高温气体产物进入气体产物冷却分离系统,依次经过间接换热器和冷却塔进行冷却处理,得到不凝气和焦油;固体产物进入固体产物冷却分离系统,在冷却室进行冷却处理,得到固体产品。进一步的,所述不凝气富含甲烷、氢气和一氧化碳的可燃性和还原性气体,其一部分用于所述加热系统原料燃气,加热自身循环利用,另一部分可用作还原气。实施例一:(1)原料准备将电子垃圾原料经过简单拆解,送入机械破碎机中进行破碎,将原料破碎至0-30mm的电子垃圾颗粒。然后进行分选,将之分选为金属部分和有机质部分。(2)金属回收将分选得到的金属部分送入酸浸池中,向其中加入配置好的王水(V浓盐酸:V浓硝酸=3:1)溶液,金属被完全溶解后得到富含金属离子的强酸溶液送入电解池中进行电解反应。所述电解池1中阳极材料为石墨,阴极材料为铜板。该电解池的电压范围,电流密度为3A/dm2,电解池内温度为35℃。在电解池1中可以回收较为纯净的铜,产物铜的纯度接近100%,回收所得的金属铜的回收率约98%。所述电解池2中阳极材料为石墨,阴极材料为纯金板。该电解池的电压为1V,电流密度为8A/dm2,电解池内温度为70℃。在电解池1中可以回收较为纯净的金,产物金的纯度接近100%,回收所得的贵金属金的回收率约98%。酸浸池中的非金属部分,经沥干、清洗后,由热解反应器加热单元产生的120℃的烟气干燥,得到纯净的不含金属的固体部分。(3)有机质热解将上述步骤(1)和(2)中产生的有机质和固体部分送入热解反应器(反应器主体)中,物料在反应器内发生热解反应的同时随着推进螺旋推进器向前推进,直至到达出料口。所述反应器由加热单元加热至750℃,物料进入反应器后受热发生热解反应,生成高温气体产物和高温固体产物。该加热单元为蓄热式燃气加热单元,燃料为高温气体产物经冷却后得到的不凝气,燃气和/或空气经过设置在烧嘴处的蓄热装置预热后进入加热单元进行燃烧,产生高温烟气用来加热热解反应器后,再经蓄热回收装置回收热量,经热量回收后的高温烟气降温至120℃左右,该部分烟气送入上述步骤(2)中得到的非金属部分,对其进行干燥。本发明所述工艺方法可长期平稳操作,原料成分分析结果如表1,所得到比较稳定的热解产物的产率和主要性质见表2,所得到比较稳定的热解气的成分分析结果见表3。表1原料分析结果表2数据结果实施例焦油净煤气半焦110.8714.7563.1表3热解气成分分析名称H2CO2O2N2CH4CO含量(%)39.56.71.22.425.924.3在本发明的描述中,需要理解的是,术语“上”、“下”、“左”、“右”、“内”、“外”等指示的方位或位置关系为基于附图所示的方位或位置关系,仅是为了便于描述本发明和简化描述,而不是指示或暗示所指的装置或元件必须具有特定的方位、以特定的方位构造和操作,因此不能理解为对本发明的限制。此外,术语“第一”、“第二”仅用于描述目的,而不能理解为指示或暗示相对重要性或者隐含指明所指示的技术特征的数量。由此,限定有“第一”、“第二”的特征可以明示或者隐含地包括一个或者更多个该特征。在本发明的描述中,除非另有说明,“多个”的含义是两个或两个以上。在本发明的描述中,需要说明的是,除非另有明确的规定和限定,术语“安装”、“相连”、“连接”应做广义理解,例如,可以是固定连接,也可以是可拆卸连接,或一体地连接;可以是机械连接,也可以是点连接;可以是直接相连,也可以通过中间媒介间接相连,可以是两个元件内部的连通。对于本领域的普通技术人员而言,可以具体情况理解上述术语在本发明中的具体含义。在本说明书的描述中,参考术语“一个实施例”、“一些实施例”、“示意性实施例”、“示例”、“具体示例”或“一些示例”等的描述意指结合该实施例或示例描述的具体特征、结构、材料或者特点包含于本发明的至少一个实施例或示例中。在本说明书中,对上述术语的示意性表述不一定指的是相同的实施例或示例。而且,描述的具体特征、结构、材料或者特点可以在任何的一个或多个实施例或示例中以合适的方式结合。尽管已经示出和描述了本发明的实施例,本领域的普通技术人员可以理解:在不脱离本发明的原理和宗旨的情况下可以对这些实施例进行多种变化、修改、替换和变型,本发明的范围由权利要求及其等同物限定。当前第1页1 2 3