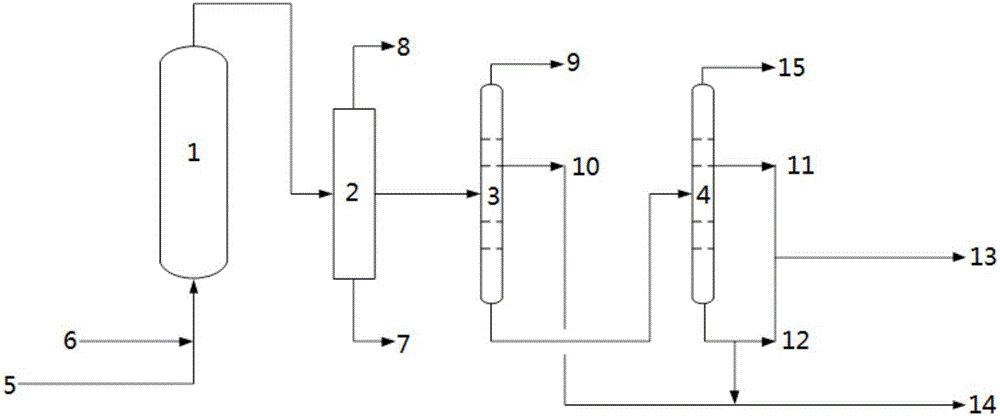
本发明涉及煤焦油加氢领域,具体涉及一种由煤焦油生产船用燃料油的方法。
背景技术:
:随着社会经济持续、高速发展,我国对石油产品的需求也日益增加。然而,石油属于不可再生能源,正面临日趋枯竭的危机。相比之下,中国煤炭储量比较丰富,因此,由煤炭制取液体燃料已成为煤加工利用的一个基本方向。另一方面,随着国际、国内钢铁行业的快速增长,炼焦工业呈现高增长的趋势,煤焦油的产量越来越大,煤焦油的清洁加工和有效利用也变得越来越重要。目前,煤焦油的常规加工方法是经过预处理蒸馏切取组分集中的各种馏分,再对各种馏分用酸碱洗涤、蒸馏、聚合、结晶等方法进行处理提取纯产品;也有一部分煤焦油经过酸碱精制后作为劣质燃料油被直接燃烧,或直接乳化后作为乳化燃料燃烧。煤焦油中所含硫、氮等杂质在燃烧过程中变成硫和氮的氧化物释放到大气中造成大气污染,而酸碱精制过程中又会产生大量污水,会严重污染环境。因此,无论是从环境保护的角度还是从综合利用方面来看,都希望找到一个有效的化学加工途径,使煤焦油得到提质,以扩大其自身利用价值。如何合理利用煤焦油资源,并提高企业的经济效益变得越来越重要。cn1903994a公开了一种煤焦油加氢改质生产燃料油的方法,具体是脱除水分和灰分的全馏分煤焦油与稀释油按比例混合后,经过装有加氢保护剂、预加氢催化剂的浅度加氢单元和装有主加氢催化剂的深度加氢单元,产物经分离、分馏得到低硫燃料油。该方法由于煤焦油原料中需要加入稀释油稀释,降低了装置的处理量并易造成煤焦油中沥青质的析出而生成沉淀,且该方法也会在实际应用过程中受到稀释油的局限。cn103695031a公开了一种由煤焦油原料生产柴油兼产船用燃料油调和组分的方法。具体为煤焦油全馏分原料与氢气混合后进入浆态床反应器进行预加氢反应,预加氢产物经气液分离和分馏后,分出轻组分和重组分,其中部分重组分作为船用燃料油,其余重组分和轻组分进一步进行加氢提质以生产清洁柴油。然而该现有技术提供的方法氢气消耗量高,并且,即便是将该现有技术中的浆态床产物进行分馏以获得柴油组分,该柴油组分的润滑性也不好。技术实现要素:本发明的目的是为了克服现有技术存在的上述缺陷问题,提供工艺流程简单、投资低的方法由煤焦油生产磨痕直径显著降低的船用燃料油。随着环保法规的越来越严,对船舶燃料油的硫含量限制也越来越严,通过加氢方法生产低硫燃料时,加氢产品的润滑性会出现问题。目前车用柴油主要是通过添加润滑性改进剂来解决此类问题。与车用燃料不同的是,船舶燃料对油品馏程没有限制,因此本发明的发明人通过控制煤焦油全馏分原料的加氢处理深度而获得常一线油、减一线油和减底油,并且合理调配获得的上述产物油就能够在不使用润滑性改进剂的前提下获得润滑性能改进的轻质燃料,同时不会影响产品的其他性能指标,能够大幅度降低企业生产成本。据此,本发明的发明人完成了本发明的技术方案。为了实现上述目的,本发明提供一种由煤焦油生产船用燃料油的方法,该方法包括:(1)在非均相浆态床加氢催化剂存在下,将经脱水和机械除杂后的煤焦油全馏分原料引入浆态床加氢反应器中进行加氢处理;(2)将所述加氢处理后得到的浆态床加氢反应器流出物依次进行分离、常压分馏和减压分馏,得到常顶油、常一线油、减一线油和减底油;(3)将常一线油和部分减底油形成的混合物作为船用轻燃料油产品,以及将减一线油和剩余的减底油形成的混合物作为船用重燃料油产品;其中,控制步骤(1)的加氢处理的深度使得步骤(2)中获得的常一线油中的双环以上芳烃含量不高于15重量%,芳烃和环烷烃总含量不低于85重量%;以及使得减底油中四环以上芳烃总含量不高于5重量%,三环芳烃和四环芳烃总含量不低于20重量%。由本发明提供的上述方法获得的轻质燃料油产品无需使用抗磨剂或润滑性改进剂就能够直接作为硫含量低于200μg/g、磨痕直径低于300μm的低硫高润滑性轻质船舶燃料油;同时由本发明提供的上述方法获得的重质燃料油能够直接作为低硫120号或180号船燃调和组分。本发明的方法还具有氢耗低的优点。附图说明图1是本发明的一种优选实施方式的由煤焦油生产船用燃料油的方法流程示意图。附图标记说明1、浆态床加氢反应器2、分离和过滤系统3、常压塔4、减压塔5、煤焦油全馏分原料6、氢气7、固渣8、分离气9、常顶油10、常一线油11、减一线油12、减底油13、船用重燃料油产品14、船用轻燃料油产品15、真空系统具体实施方式在本文中所披露的范围的端点和任何值都不限于该精确的范围或值,这些范围或值应当理解为包含接近这些范围或值的值。对于数值范围来说,各个范围的端点值之间、各个范围的端点值和单独的点值之间,以及单独的点值之间可以彼此组合而得到一个或多个新的数值范围,这些数值范围应被视为在本文中具体公开。如前所述,本发明提供了一种由煤焦油生产船用燃料油的方法,该方法包括:(1)在非均相浆态床加氢催化剂存在下,将经脱水和机械除杂后的煤焦油全馏分原料引入浆态床加氢反应器中进行加氢处理;(2)将所述加氢处理后得到的浆态床加氢反应器流出物依次进行分离、常压分馏和减压分馏,得到常顶油、常一线油、减一线油和减底油;(3)将常一线油和部分减底油形成的混合物作为船用轻燃料油产品,以及将减一线油和剩余的减底油形成的混合物作为船用重燃料油产品;其中,控制步骤(1)的加氢处理的深度使得步骤(2)中获得的常一线油中的双环以上芳烃含量不高于15重量%,芳烃和环烷烃总含量不低于85重量%;以及使得减底油中四环以上芳烃总含量不高于5重量%,三环芳烃和四环芳烃总含量不低于20重量%。本发明的常压是指:一个标准大气压,即为101kpa。本发明提供的方法,无需使用抗磨剂或润滑性改进剂就能够生产硫含量低于200μg/g、磨痕直径低于300μm的低硫高润滑性船舶燃料油,该燃料油尤其适用于近海、内河的中高转速发动机的船舶。在本发明中,对煤焦油全馏分原料首先经初步预处理进行沉降、离心分离以脱除水、机械杂质等的具体操作方法没有特别的限定,只要能达到初步脱除煤焦油全馏分原料中的水、机械杂质的目的即可。在本发明所述的方法中,经初步脱除水、机械杂质后的煤焦油全馏分原料与非均相浆态床加氢催化剂混合均匀后与氢气一起进入浆态床加氢反应器中进行加氢处理。在本发明所述的方法中,煤焦油全馏分原料在浆态床加氢反应器中进行加氢处理,达到脱除金属、机械杂质、硫、氮等目的,并通过控制适宜的加氢深度,以减少浆态床加氢过程中干气、液化气和焦炭等副产物的生成。在本发明的步骤(2)中,将所述加氢处理后得到的浆态床加氢反应器流出物进行分离的目的是除去其中的固渣以及气体(以下命名为分离气)。该分离可以在例如含有气液分离和液固分离的系统中进行。在本发明的步骤(2)中,将所述加氢处理后得到的浆态床加氢反应器流出物进行分馏包括依次进行常压分馏和减压分馏。通过常压分馏获得常顶油和常一线油,将常压分馏塔底的馏出物引入至例如减压塔中进行减压分馏以获得减一线油和减底油。优选情况下,控制步骤(1)的加氢处理的深度使得步骤(2)中获得的常一线油中的双环以上芳烃含量不高于10重量%,芳烃和环烷烃总含量不低于90重量%;以及使得减底油中四环以上芳烃总含量不高于3重量%,三环芳烃和四环芳烃总含量不低于25重量%。采用该优选情况下的加氢处理深度能够在获得更好性能的船用燃料油产品的前提下使得氢耗更低。本发明提供的方法通过采用浆态床加氢反应器,实现金属、机杂、硫、氮等的脱除,并通过控制适宜的加氢处理反应深度,使常一线油中的双环以上芳烃含量不高于15重量%,优选不高于10重量%,芳烃和环烷烃总含量不低于85重量%,优选不低于90重量%;使减底油中四环以上芳烃总含量不高于5重量%,优选不高于3重量%,三环芳烃和四环芳烃总含量不低于20重量%,优选不低于25重量%。通过控制加氢深度在本发明的上述范围内,特别是优选的范围内时,能够提高混合油的互溶性及稳定性,以及能够同时确保产品的润滑性足够高和稳定性足够好。优选地,控制形成所述船用轻燃料油产品的混合物中的减底油的含量使得所述船用轻燃料油产品中三环芳烃和四环芳烃总含量为2.5~5.0重量%。更优选地,控制形成所述船用轻燃料油产品的混合物中的减底油的含量使得所述船用轻燃料油产品中三环芳烃和四环芳烃总含量为3.0~4.5重量%。本发明的所述非均相浆态床加氢催化剂可以为高分散型催化剂。根据一种优选的具体实施方式,所述非均相浆态床加氢催化剂中含有煤粉、焦炭粉和活性炭中的至少一种物质作为分散介质,以及含有作为分散相的活性组分,所述活性组分选自第vib族非贵金属和第viii族非贵金属中的至少一种。更优选地,所述活性组分为铁、钴、镍、钼和钨中的至少一种。例如,所述非均相浆态床加氢催化剂为负载型催化剂。优选情况下,以所述非均相浆态床加氢催化剂的总重量为基准,以元素计的所述活性组分的含量为2~20重量%。更优选地,以所述非均相浆态床加氢催化剂的总重量为基准,以元素计的所述活性组分的含量为5~18重量%。优选地,以所述经脱水和机械除杂后的煤焦油全馏分原料的总重量为基准,所述非均相浆态床加氢催化剂的加入量为1.0~3.0重量%,更优选所述非均相浆态床加氢催化剂的加入量为1.0~2.0重量%。根据一种优选的具体实施方式,步骤(1)中的所述加氢处理的条件包括:反应温度为360~440℃,氢分压为5.0~10.0mpa,体积空速为0.1~1.5h-1,氢油体积比为200~1000nm3/m3。根据另一种更优选的具体实施方式,步骤(1)中的所述加氢处理的条件包括:反应温度为380~420℃,氢分压为5.0~8.0mpa,体积空速为0.5~1.2h-1,氢油体积比为300~800。优选情况下,所述常顶油与所述常一线油的分馏点为150~170℃,所述常一线油与所述减一线油的分馏点为340~360℃,所述减一线油与所述减底油的分馏点为390~400℃。例如,所述常顶油与所述常一线油的分馏点为165℃,所述常一线油与所述减一线油的分馏点为350℃,所述减一线油与所述减底油的分馏点为390℃。优选情况下,经脱水和机械除杂后的煤焦油全馏分原料中的水含量小于0.05重量%,机械杂质含量小于0.20重量%。更优选地,经脱水和机械除杂后的煤焦油全馏分原料中的水含量小于0.03重量%,机械杂质含量小于0.10重量%。本发明的所述煤焦油指煤热解或煤造气或其它过程产生的煤焦油。因此,所述煤焦油可以是煤造气产生的低温煤焦油、也可以是煤热解过程(包括低温炼焦、中温炼焦、高温炼焦过程)产生的低温煤焦油或中温煤焦油或高温煤焦油的全馏分原料。优选情况下,所述煤焦油全馏分原料为低温煤焦油、中温煤焦油和高温煤焦油中的至少一种。本发明结合图1提供一种优选的具体实施方式由煤焦油生产船用燃料油,该方法包括:将经脱水和机械除杂后的煤焦油全馏分原料5和氢气6混合后引入至浆态床加氢反应器1中与其中含有的非均相浆态床加氢催化剂接触以进行加氢处理;将所述加氢处理后得到的浆态床加氢反应器流出物引入至分离和过滤系统2中进行分离,分别获得分离气8和固渣7,分离后的液相引入至常压塔3中进行常压分馏,分别获得常顶油9和常一线油10,以及将常压塔3塔底的物料引入至减压塔4中进行减压分馏,分别获得减一线油11和减底油12,并且将减压塔4顶部的气体引入至后续的真空系统15中进行进一步处理;将常一线油10和部分减底油12形成的混合物作为船用轻燃料油产品14,以及将减一线油11和剩余的减底油12形成的混合物作为船用重燃料油产品13;其中,控制加氢处理的深度使得获得的常一线油中的双环以上芳烃含量不高于15重量%,芳烃和环烷烃总含量不低于85重量%;以及使得减底油中四环以上芳烃总含量不高于5重量%,三环芳烃和四环芳烃总含量不低于20重量%。本发明提供的前述方法还具有如下具体的优点:1、本发明充分利用煤焦油不同馏分段烃类特点,实现不同馏分段的性质互补,在不使用润滑性改进剂的情况下,通过简单的办法生产低硫高润滑性船用燃料;2、本发明提供的方法具有原料适应性强、装置运转周期长的特点。以下将通过实施例对本发明进行详细描述。以下实例在没有特别说明的情况下,根据图1所示的流程图进行。以下实例使用的煤焦油全馏分原料的性质见表1。浆态床加氢反应器中采用高分散非均相浆态床加氢催化剂,该高分散非均相浆态床催化剂为高分散铁系碳基负载型催化剂,其组成为:活性炭作为载体,活性组分为fe和mo。并且,所述高分散铁系碳基负载型催化剂中以元素计的fe和mo的重量比为1:0.2,以所述高分散铁系碳基负载型催化剂的总重量计,以元素计的所述活性组分的含量为15重量%。表1:煤焦油全馏分原料的性质煤焦油全馏分原料密度(20℃)/(g/cm3)0.9998残炭/%4.97氮含量/(μg/g)6100硫含量/(μg/g)2200c含量/重量%83.34h含量/重量%9.61沥青质含量/重量%13.5馏程astmd-1160/℃ibp17250%37095%505金属含量/(μg/g)fe46.9ni<0.1v<0.1na13.3ca130.7al8.1实施例1以表1中煤焦油全馏分为原料,经初步脱除水和机械杂质后,与前述高分散非均相浆态床加氢催化剂混合均匀后,与氢气一起进入浆态床加氢反应器中进行加氢处理。以煤焦油原料的总重量为基准,非均相浆态床加氢催化剂以其中含有的活性金属元素计的用量为1.0重量%。加氢生成物流经分离和分馏系统分出<165℃的常顶油、165~350℃常一线油、350~390℃减一线油、>390℃的减底油。实施例1的反应操作条件见表2。反应氢耗及常一线油和减底油烃类组成见表3,向常一线油中添加3重量%(以常一线油为基准)的减底油,得到高润滑性轻质船用燃料油产品,混合减一线油和剩余减底油,得到低硫重质船用燃料油产品。所得到的轻质船用燃料油产品和重质船用燃料油产品性质见表4。由表4可知,采用本发明的方法,其氢耗仅为1.50重量%,氢耗较低;得到的轻质船用燃料油产品可作为低硫高润滑性的4号轻燃料油;生产的重质船用燃料油产品可作为优质的低硫120号船用燃料油调和组分。表2:实施例1的操作条件氢分压/mpa6.0反应温度/℃400氢油比/(nm3/m3)600体积空速/h-11.0表3:实施例1的氢耗及产品烃组成表4:实施例1产品性质实施例2以表1中煤焦油全馏分为原料,经初步脱除水和机械杂质后,与前述高分散非均相浆态床加氢催化剂混合均匀后,与氢气一起进入浆态床加氢反应器中进行加氢处理。以煤焦油原料的总重量为基准,非均相浆态床加氢催化剂以其中含有的活性金属元素计的用量为1.5重量%。加氢生成物流经分离和分馏系统分出<170℃的常顶油、170~355℃常一线油、355~395℃减一线油、>395℃的减底油。实施例2的反应操作条件见表5。反应氢耗及常一线油和减底油烃类组成见表6,向常一线油中添加6重量%(以常一线油为基准)的减底油,得到高润滑性轻质船用燃料油产品,混合减一线油和剩余减底油,得到低硫重质船用燃料油产品。所得到的轻质船用燃料油产品和重质船用燃料油产品性质见表7。由表7可知,采用本发明的方法,其氢耗仅为1.21重量%,氢耗较低;得到的轻质船用燃料油产品可作为低硫高润滑性的4号轻燃料油;生产的重质船用燃料油产品可作为优质的低硫120号船用燃料油调和组分。表5:实施例2的操作条件氢分压/mpa8.0反应温度/℃390氢油比/(nm3/m3)400体积空速/h-10.55表6:实施例2的氢耗及产品烃组成表7:实施例2产品性质实施例3以表1中煤焦油全馏分为原料,经初步脱除水和机械杂质后,与前述高分散非均相浆态床加氢催化剂混合均匀后,与氢气一起进入浆态床加氢反应器中进行加氢处理。以煤焦油原料的总重量为基准,非均相浆态床加氢催化剂以其中含有的活性金属元素计的用量为0.9重量%。加氢生成物流经分离和分馏系统分出<155℃的常顶油、155~345℃常一线油、345~390℃减一线油、>390℃的减底油。实施例3的反应操作条件见表8。反应氢耗及常一线油和减底油烃类组成见表9,向常一线油中添加8重量%(以常一线油为基准)的减底油,得到高润滑性轻质船用燃料油产品,混合减一线油和剩余减底油,得到低硫重质船用燃料油产品。所得到的轻质船用燃料油产品和重质船用燃料油产品性质见表10。由表10可知,采用本发明的方法,其氢耗仅为1.86重量%,氢耗较低;得到的轻质船用燃料油产品可作为低硫高润滑性的4号轻燃料油;生产的重质船用燃料油产品可作为优质的低硫180号船用燃料油调和组分。表8:实施例3的操作条件氢分压/mpa5.0反应温度/℃420氢油比/(nm3/m3)800体积空速/h-11.2表9:实施例3的氢耗及产品烃组成表10:实施例3产品性质对比例1本对比例采用与实施例1相同的原料进行。本对比例的催化剂、催化剂用量以及反应部分的操作条件同实施例2。仅是工艺流程上与实施例2中不同,具体地:本对比例将加氢生成物流经分离和分馏系统分出<170℃的常顶油、170~355℃常一线油、>355℃重油。同时,本对比例通过表11给出了本对比例获得的常一线油和重油的主要性质。表11:对比例1的产品性质常一线油重油密度(20℃)/(g/cm3)0.88220.9253运动粘度(40℃)/(mm2/s)3.886/运动粘度(50℃)/(mm2/s)/17.35残炭/重量%<0.10.65灰分/重量%<0.0020.01硫含量/(μg/g)143433磨痕直径/μm486馏程astmd-1160/℃ibp17036250%27240895%358489由表11中可以看出,本对比例获得的常一线油的磨痕直径为486μm,远高于本发明的实施例中的船用轻燃料油产品的磨痕直径,表明本发明对改善船用轻燃料油产品的磨痕直径效果显著。以上详细描述了本发明的优选实施方式,但是,本发明并不限于此。在本发明的技术构思范围内,可以对本发明的技术方案进行多种简单变型,包括各个技术特征以任何其它的合适方式进行组合,这些简单变型和组合同样应当视为本发明所公开的内容,均属于本发明的保护范围。当前第1页12