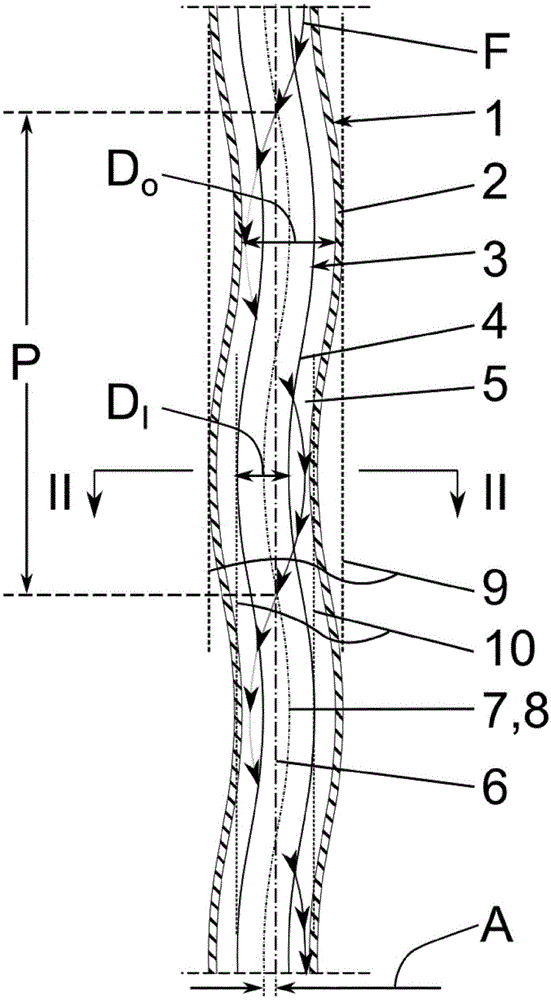
本发明涉及一种裂解炉,其包括用于承载流体流(诸如,气体或液体)的热解管。
背景技术:
:在乙烯裂解炉中,燃烧器设置在燃烧室中,至少一个热解管通过该燃烧室,同时携载作为工艺气体的烃原料流。在裂解炉中希望烃原料尽可能快地转化成所需产物,诸如乙烯、丙烯和丁二烯。在最高可能的温度和尽可能低的烃分压下在热解管中的低停留时间是决定对有利产物的选择性的主要参数。裂解炉中的热解管的内表面经历焦炭形成,并且一旦达到热解管运行条件结束,就需要以规则的间隔脱焦。运行条件结束取决于在热解管内表面上积聚的焦炭的程度,并且可以通过热解管长度上的最大允许压降或最大允许热解管金属温度来限制。通过该焦炭沉积在热解管的内表面上,压降和热解管金属温度都增加。过热的热解管金属温度是不可取的,因为热解管的操作接近其冶金极限会导致蠕变和渗碳。焦炭形成的速率取决于原料转化率和形成焦炭的热解管内表面的温度。原料转化率越高并且内表面温度越低,焦炭形成越少。从wo2005/068926中已知通过在管内提供圆柱形主体来增加从热解管到沿管流动的流体的总热传递。该主体接收来自周围管的辐射并且将其传递到主体周围的流体。该热解管中的流动沿着管的长度主要是轴向的。从wo2006/032877或wo2010/032024中已知提供具有螺旋几何形状的热解管,其促进减小管内表面处的层状层的厚度的旋流并且促进从内壁进入管的中心区域中的质量传递,从而与直管相比增加了远离壁的对流热传递。这种设计具有额外的优点,即,相对于额外的压降,它以最小的损失增加了热传递。从wo2005/075607中已知提供一种具有热解管的裂解炉,其提供通过裂解炉的流的双通道。存在两个上游部分,并且当两个上游部分进入共同的下游部分时,然后在流动方向上逆转。技术实现要素:根据本发明,提供了一种裂解炉,其包括用于承载流体流的热解管,所述热解管包括径向内部主体和径向外壁,所述径向内部主体和径向外壁一起限定环形流动通道,其中径向内部主体和径向外壁中的至少一个具有中心线,该中心线在热解管的纵向方向上成螺旋形地延伸,以便当流体沿着热解管流动时促进流体的旋转。促进环形流动通道中的流体流动的旋转改善了进入流体的热传递。旋转流动可导致流体紧接着轴向速度分量具有切向和径向速度分量,即,所谓的旋流。因此,至少在实施例的描述中,环形通道可以被认为是环形旋流通道。环形通道中的旋流改善了对流传热,而内部主体的存在产生了环形流动通道并且同时增加了表面与体积比。可以实现低停留时间并提高产率,即,产生所需的裂化产物。环形旋流通道的示例包括:第一类型的热解管,其中径向内部主体和径向外壁都具有沿热解管的纵向方向成螺旋形延伸的相应中心线;第二类型的热解管,其中径向内部主体具有直中心线(或仅在一个平面内弯曲的中心线)并且径向外壁具有成螺旋形延伸的中心线;第三类型的热解管,其中径向内部主体具有成螺旋形延伸的中心线并且径向外壁具有直中心线(或仅在一个平面中的曲线)。第三类型的实施例具有的优点是,仅径向内部主体必须形成有成螺旋形延伸的中心线,并且径向外壁可以由常规管提供。这使得制造起来相对便宜。流体可以是气体,如用于生产乙烯和/或其它气态产物的裂解炉的情况,或者它可以是液体,如在减粘裂化炉裂解炉的情况下。热解管可以在裂解炉中基本上沿其全长具有环形流动通道,例如,其全长通过裂解炉的炉腔或燃烧室。在某些实施例中,热解管包括由环形流动通道下游的径向外壁限定的非环形流动通道。通过提供环形流动通道,获得了改善的流体热通量,并且更早地开始热解。然而,至少在用于生产乙烯或其他气态产物的裂解炉的情况下,由于环形区域的宽度有限,这是以降低容纳焦炭沉积的能力为代价的,因此与在高焦炭形成的区域中的非环形流动通道相比,导致相对压降增加。因此,通过在环形流动通道下游提供非环形流动通道,减少了由于增加的焦炭形成而导致的压降增加,并且使得更多的横截面积可用于处理增加的焦炭沉积。另外,在该下游通道中,所需反应产物的浓度增加,因此通过二次反应产生副产物以及焦炭沉积物的倾向也增加。在该区域中有利的是具有低烃分压,使得产物的浓度和次级反应的相应反应速率尽可能低。所有这些都是通过非环形流动通道实现的。因此,在环形流动通道下游提供非环形流动通道使得可获得更大的横截面积,以适应焦炭层厚度并且使压降对所需反应产物的产率的影响最小化。在这些实施例中,在非环形流动通道中,径向外壁内的整个横截面区域可用于流动。换句话说,没有径向内部主体。热解管可具有环形通道,该环形通道延伸小于或等于裂解炉中热解管长度的75%。在这些实施例中,环形流动通道可以延伸小于或等于裂解炉中热解管长度的70%或65%或60%或55%或50%。裂解炉中的热解管的剩余部分可包括非环形通道。非环形流动通道可以由径向外壁限定,该径向外壁具有沿热解管的纵向方向成螺旋形地延伸的中心线。或者,非环形流动通道可以由径向外壁限定,该径向外壁在热解管的纵向方向上具有直中心线(或仅在单个平面中弯曲)。环形流动通道的径向外壁的内径可以大于非环形流动通道的径向外壁的内径。这有助于减少平均轴向流速随着流动进入非环形流动通道而降低的任何趋势。过渡部分可以设置在环形流动通道的径向外壁和非环形流动通道的径向外壁之间。热解管可包括多个分支,每个分支具有相应的径向内部主体和相应的径向外壁,它们一起限定相应的环形流动通道,每个分支的径向内部主体和径向外壁中的至少一个被构造为促进流体流动的旋转,分支在结点处接合在一起并且非环形流动通道设置在结点处的下游。这样的布置可以理想地增加表面与体积比并且促进特别是产生旋流的流体流动的旋转,从而改善热解管的存在多个分支的更多上游部分中的热传递。在下游,通过提供非环形流动通道可以使压降最小化。可能存在两个分支,因此该结点可以是y结点。在热解管包括分支的实施例中,至少一个分支中的环形通道的长度可小于或等于该分支的长度加上在结点下游延伸的热解管的长度的75%或70%或65%或60%或55%或50%。热解管可以从其入口向下延伸。因此,沿着热解管的流体流动可以是向下的方向。在热解管顶部的入口处,任何剥落的焦炭都不会堵塞入口,并且可能最终在去焦化期间焦炭可能快速燃烧的位置用完。这与管通道的数量无关(下面进一步讨论)。热解管可以具有通过裂解炉的腔室的单通道。它可以例如在腔室的一端具有入口而在另一端具有出口。这种布置显著缩短了停留时间。在一些单通道实施例中,热解管从入口向下延伸,由此流体流沿着热解管的通道处于向下的方向。这具有上面讨论的与剥落的焦炭有关的益处。热解管可以两次通过裂解炉的腔室,即,双通道热解管。在这些实施例中,相应的通道可以通过u形弯头接合。这种布置对于裂解诸如乙烷和丙烷的气态原料可能更具吸引力,这需要比裂解诸如石脑油和瓦斯油的液体原料更长的停留时间。例如,热解管可以在腔室的上部区域具有入口和出口,流体流在第一通道中首先向下,然后在第二通道中向上。在单通道布置中,例如在顶部到底部向下流动布置中,在环形流动通道的下游可以存在非环形流动通道。在双通道布置中,第一通道可包括环形流动通道,第二通道包括非环形流动通道。在热解管提供通过裂解炉的流的双通道的实施例中,热解管可包括第一通道中的上游部分和第二通道中的下游部分,并且下游部分可至少在某种程度上为在相对于裂解炉的燃烧器的上游部分的遮蔽中。因此,上游部分可以比下游部分更多地暴露于辐射热,其优点是在下游部分的外侧上接收的热量更均匀。这可以降低该下游部分中热解管壁中的峰值温度,并且因此降低峰值热解管壁温度接近冶金极限的趋势。这可以延长炉子可以在脱焦程序之间操作的时间。在环形流动通道分支接合的实施例中,分支可以设置为流动方向通常保持相同,例如向下的流动方向。因此,在单通道布置中,各自限定环形流动通道的两个分支可以在y形结点处接合,然后流动可以在相同的总体方向(例如,向下)上在非环形流动通道中继续。在替代的布置中,多个分支中的流体流可以大致平行并且在相同的方向(例如,向下)上,并且在分支接合的结点处下游的非环形流动通道中的流体流动方向可以是相反的方向,例如,向上。因此,可以在结点之后提供u形弯头,或者可以提供多个u形弯头,每个分支提供一个u形弯头,其中结点设置在u形弯头的下游。在任一情况下,非环形流动通道可至少在某种程度上处于相对于裂解炉的燃烧器的至少一个上游分支的遮蔽中。因此,具有环形流动通道的分支比下游非环形流动通道更多地暴露于辐射热,其优点是在下游部分的外侧上接收的热量更均匀。如上所述,这可以降低该下游部分中热解管壁中的峰值温度,从而降低峰值热解管壁温度接近冶金极限的趋势,从而延长炉子可能在脱焦程序之间操作的时间段。对于向裂解炉提供热量的方式有几种选择。至少一个燃烧器可以设置在炉腔的上部区域中或炉腔的底部区域中或炉腔的顶部和底部之间的中间区域(即,侧面点火),或者可以是前述任何组合。在仅仅顶部点火的情况下,烟道气或废气可以向下流动。在顶部和侧面点火的组合的情况下,烟道气可以向下流动。在仅仅侧面点火的情况下,烟道气可以向下或向上流动。在仅仅底部点火的情况下,烟道气可以向上流动。在底部和侧面点火的组合的情况下,烟道气可以向上流动。在某些实施例中,裂解炉包括在裂解炉的点火区域中的至少一个燃烧器,热解管在点火区域中延伸,并且热解管在炉子中在远离点火区域的下游延伸。在顶部点火炉的情况下,热解管可以在炉子中在点火区域下游并远离点火区域向下延伸。通过最大化到热解管的上游部分的热通量,任何焦炭更均匀地分布在管内表面上,管材料被充分利用并且更有效地使用内部主体。当流体以低于其离开时的温度进入热解管时,通过在热解管的上游部分设置点火区域,可获得更大的余量达到最大管表皮温度,从而允许更高的热通量。此外,如果环形流动通道设置在热解管的上游部分,当外管温度通过至少一个燃烧器升高时,则从径向外壁到内部主体的辐射热传递增加。这改善了流体温度进展到热解开始的点,提高了热解反应转化率并且提高了反应温度水平,从而提高了产率,即,所需反应产物的输出流体中的浓度。热解管可以从其入口向下延伸。例如,热解管的入口可以位于炉腔的顶部,出口可以位于炉腔的底部。任何剥落的焦炭可能远离入口而从管道落下,因此不会堵塞入口,并且最终可能在去焦化期间其可能快速燃烧的位置结束。在热解管中流体向下流动的情况下,顶部和/或侧面点火是有益的。通过径向内部主体和/或径向外壁可以进一步改善流体流动的旋转促进,所述径向内部主体和/或径向外壁具有至少一个突出到环形流动通道中的螺旋形突起,例如螺旋形翅片。例如,径向内部主体可以具有主体,该主体设置有至少一个螺旋突起以促进流体流动的旋转。环形通道可以基本上连续且不间断地围绕内部主体延伸。因此,当环形通道围绕内部主体周向延伸时,可能没有挡板或翅片中断环形通道。在径向内部主体和径向外壁都具有在热解管的纵向方向上成螺旋形地延伸的相应中心线的实施例中,螺旋旋转的轴线和螺旋中心线可以重合。因此,螺旋中心线可以具有相同的节距和振幅,并且可以是同相的。在这样的布置中,垂直于热解管的纵向方向测量的环形流动通道的宽度在管周围的不同圆周点处将是相同的。该宽度优选地小于或等于径向外壁的直径的50%,更优选地小于或等于径向外壁的直径的40%或35%或30%或25%。如果使内部主体和径向外壁之间的间隙相对较小,则是有利的。这可以降低径向外壁的温度,因为给定流速的平均流体速度随着较小的径向宽度的增加而增加,并且相应地增加了热传递。但是,压降增加。然后可以将管设计成受压降而不是管金属温度的限制。通过降低管金属温度,蠕变和渗碳速率降低。垂直于热解管的纵向方向测量的环形流动通道的宽度可以在管的圆周方向上变化。宽度可以在圆周方向上从内部主体的第一侧上的最小值增加到在与第一侧径向相对的第二侧上的最大值。宽度可以在圆周方向上从第一侧到第二侧逐渐增加。在相同的圆周方向上继续,宽度可以从第二侧到第一侧逐渐减小。例如对于第二类型的热解管,将发生垂直于热解管的纵向方向测量的环形流动通道的变化宽度,其中内部主体具有直中心线(或在单个平面中弯曲的中心线)并且径向外壁具有螺旋中心线。对于第三种类型的热解管也会发生,其中内部主体具有螺旋中心线,并且径向外壁具有直(或在单个平面中弯曲)的中心线。在某些实施例中,垂直于热解管的纵向方向测量的环形流动通道的最大宽度小于或等于径向外管的直径,并且可以小于或等于该直径的一半。如果内部主体具有相对高的辐射率是有利的。实际上,这意味着它具有无光面而不是光滑面。在表面上形成焦炭层的情况下获得这种无光面。可以提供至少一个支撑件以支撑热解管中的内部主体。可以提供纵向间隔开的支撑件。第一个这样的支撑件可以固定到径向外壁和内部主体,并且第二个这样的支撑件可以包括至少一个支撑构件,该支撑构件固定到径向外壁并且定位在内部主体的径向外侧但不固定到内部主体。第一支撑件可承受内部主体的重量。第二支撑件可有助于定位内部主体,同时允许径向外壁和内部主体之间的相对运动。这在差热运动和差动蠕变的情况下是有益的。第二支撑件的支撑构件可以是位于内部主体的径向外侧但不固定到其上的环。支撑构件可以通过从外壁径向向内突出到支撑构件的径向肋固定到径向外壁。可以防止内部主体接触径向外壁。它可以保持在大致中心的位置,以便为环形流动通道提供一致的形状并且提供相对均匀的热量分布。内部主体可以是实心的或空心的。在一些实施例中,内部主体是中空主体。这在重量上比实体更轻。而且,中空主体内的气体可以帮助从内部主体的一部分到另一部分的热传递,例如从下部较热的下游部分到上部较冷的上游部分的垂直热传递。在其他实施例中,例如对于较小直径的内部主体,内部主体可以是实心主体。附图说明现在将通过示例并参考附图来描述本发明的某些优选实施例,其中:图1是第一类型的热解管的一部分的示意性纵向剖视图;图2是沿图1中线ii-ii贯穿图1的热解管的横向剖视图;图3是第二类型的热解管的一部分的示意性纵向剖视图;图4是沿图3中线iv-iv贯穿图3热解管的横向剖视图;图5是第三类型的热解管的一部分的示意性纵向剖视图;图6是沿图5中线vi-vi贯穿图5的热解管的横向剖视图;图7是第一类型的热解管的示意性纵向剖视图,显示其全长;图8是第二类型的热解管的示意性纵向剖视图,显示其全长;图9是沿图8中线ix-ix的横向剖视图;图10是沿图8中线x-x的横向剖视图;图11是第三类型的热解管的示意性纵向剖视图,显示其全长;图12是第一类型的热解管的示意性纵向剖视图,显示其全长,并且修改为包括翅片;图13是第二类型的热解管的示意性纵向剖视图,示出了其全长,并且修改为包括翅片;图14是第三类型的热解管的示意性纵向剖视图,显示其全长,并且修改为包括翅片;图15是第二类型的热解管的示意性纵向剖视图,用于双通道装置,其中热解管两次通过裂解炉的长度;图16是第二类型的热解管的变型的示意性纵向剖视图,用于双通道装置,其中热解管两次通过裂解炉的长度;图17-23是在具有热解管的裂解炉的垂直平面中的示意剖视图;以及图24-29是穿过热解管的进一步变型的示意性纵向剖视图。具体实施方式参照图1和图2,热解管1包括径向外部管状壁2,该管状壁2以周向延伸的方式围绕内部主体3。内部主体3是中空主体并且为热解管提供径向内壁4,因此,径向内壁和径向外部管状壁一起限定了用于流体流f的环形流动通道5,在所示和所述的该实施例和其他实施例中,流体流f是气体。这些实施例适用于生产乙烯的裂解炉,即乙烯裂解炉。热解管1具有中心纵向轴线6,在该实施例中该中心纵向轴线6是直的,并且也可以称为螺旋旋转的轴线。中心纵向轴线6沿假想的圆柱形封套9的中心轴线设置,当沿纵向方向观察时,该封套包含热解管的“覆盖区”。径向外部管状壁2具有中心线7,该中心线7沿着围绕中心纵向轴线6的螺旋路径。内部主体3具有中心线8,该中心线8沿着围绕中心纵向轴线6的螺旋路径。在该实施例中,径向外部管状壁2的螺旋中心线7和内部主体3的螺旋中心线8重合,即,中心线具有相同的节距和振幅并且彼此同相。流动通道5是螺旋缠绕的环形流动通道。内部主体3包含在假想的圆柱形封套10中,当沿纵向观察时,该封套10包含内部主体的“覆盖区”。中心纵向轴线6沿着假想的圆柱形封套10的中心轴线。螺旋中心线7、8具有振幅a和节距p。径向外部管状壁2的内径被示为do,并且内部主体3的外径被示为di。在本说明书中,螺旋线的相对振幅被认为是螺旋线的振幅a除以径向外部管状壁的内径do,即a/do。相对节距被认为是节距p除以径向外部管状壁的内径do,即p/do。环形流动通道5在径向方向上相对于中心纵向轴线6具有宽度w。在该第一类型的热解管中,宽度w在流动通道5的环形空间周围是恒定的。图3和图4示出了第二种类型的热解管1。在适当的地方使用了与图1和图2中使用的附图标记相对应的附图标记。第二种类型与第一种类型的不同之处在于内部主体3是圆柱形的而不是具有螺旋构造。内部主体3是中空主体并且为热解管提供径向内壁4,由此径向内壁和径向外部管状壁一起限定用于气体流f的环形流动通道5。圆柱形内部主体3的中心线8位于热解管的中心纵向轴线6上,该中心纵向轴线6沿着当沿纵向观察时包含径向外部管状壁2的假想圆柱形封套9的中心轴线设置。因此,对于该第二类型的热解管,内部主体3具有直中心线8。在这种情况下,当在纵向方向上观察时包含内部主体3的“覆盖区”的假想的圆柱形封套10对应于内部主体本身的圆柱形形状。径向外部管状壁2具有螺旋形的中心线7,并且该中心线具有振幅a和节距p。效果是环形流动通道5具有螺旋构型。如图4所示,其示出了在横向于纵向方向的平面中的流动通道,流动通道5在横向平面中具有最小宽度wmin并且在横向平面中具有最大宽度wmax。当在横向平面中观察时,最小宽度wmin和最大宽度wmax的位置沿着热解管的长度,即,相对于纵向方向旋转。因此,流动通道5是螺旋缠绕的环形流动通道。径向外部管状壁2的内径显示为do,并且内部主体3的外径显示为di。图5和图6示出了第三种类型的热解管1。在适当的情况下,在图5和图6中使用与图1和图2中使用的附图标记相对应的附图标记。第三种类型与第一种类型的不同之处在于径向外部管状壁2是圆柱形的,而不是具有螺旋构造。内部主体3是中空主体并且为热解管提供径向内壁4,由此径向内壁和径向外部管状壁一起限定用于气体流f的环形流动通道5。当在纵向方向上观察时,用于该第三类型的热解管的中心纵向轴线6也是径向外部管状壁2的中心线7。在这种情况下,当在纵向方向上观察时,包含热解管的“覆盖区”的假想圆柱形封套9对应于圆柱形径向外部管状壁2。内部主体3是螺旋形的,并且其中心线8沿着围绕热解管的中心纵向轴线6的螺旋路径。内部主体3包含在假想的圆柱形封套10中,当沿纵向观察时,该封套包含内主体的“覆盖区”。中心纵向轴线6沿着假想的圆柱形封套10的中心轴线设置。内部主体3的螺旋中心线8具有间距p和振幅a。因此,对于该第三种类型的热解管,径向外部管状壁2具有直线的中心线7,而内部主体3具有螺旋形的中心线8。效果是环形流动通道5具有螺旋构型。如图6所示,其示出了在横向于纵向方向的平面中的流动通道,流动通道5在横向平面中具有最小宽度wmin并且在横向平面中具有最大宽度wmax。当在横向平面中观察时,最小宽度wmin和最大宽度wmax的位置沿着热解管的长度,即相对于纵向方向旋转。因此,流动通道5是螺旋缠绕的环形流动通道。径向外部管状壁2的内径被显示为do,并且内部主体3的外径显示为di。图1至图6示出了第一种类型、第二种类型和第三种类型的热解管。径向外壁2和/或内部主体3可以通过挤压形成为具有螺旋中心线。在这种情况下,径向外壁2和/或内部主体3在垂直于螺旋旋转轴线(即,中心纵向轴线6)的平面中可以是圆形的。或者,径向外壁2和/或内部主体3可以由圆柱形管或棒形成,以具有螺旋中心线。在那种情况下,径向外壁2和/或内部主体3在垂直于螺旋中心线7和/或8的平面中可以是圆形的。图7示出了第一种类型的热解管1,其形式为安装在裂解炉中以提供通过该炉的单通道。热解管1具有环形旋流部段31形式的主要部分,其具有径向外部管状壁2和内部主体3。当热解管是第一类型时,径向外部管状壁2和内部主体3具有螺旋中心线。在上端,热解管1具有入口部分40,并且在下端,其具有出口部分42。入口部分40和出口部分42都是圆柱形的并且具有各自的直中心线。第一上过渡部分47位于上入口部分40和环形流动部段31之间,并且第一下过渡部分50设置在环形流动部段31和出口部分42之间。在其下端处,第一上过渡部分47接合到热解管1的环形旋流部段31的径向外部管状壁2。它提供从具有其直中心纵向轴线的上入口部分40到具有其螺旋中心线7(见图1)的外部管状壁2的过渡。第一下过渡部分50的上端接合到环形旋流部段31的径向外部管状壁2的下端。因此,第一下过渡部分50提供从具有其螺旋中心线7的径向外部管状壁2到具有其直中心线的出口部分42的过渡。内部主体3在其上端具有一个葱形部60,该葱形部60布置成引导流f从第一上过渡部分47进入围绕内部主体3的外部和径向外部管状壁2的内部的环形流动通道5。径向外部管状壁2和内部主体3都具有重合的螺旋中心线。内部主体3在其下端具有第二葱形部60,该第二葱形部60布置成在流f离开环形流动通道时引导流f。提供第一支撑装置51,用于在内部主体3的下端处将内部主体3保持在径向外部管状壁2中。为图8中所示的第二类型的热解管提供类似的支撑装置51,进一步的细节在图9和图10中可以看到。支撑件61设置在内部主体3的下部区域,并且由三个等角度间隔的径向支撑构件75组成,径向支撑构件75在径向外部管状壁2和内部主体3之间沿径向延伸。径向支撑构件75在纵向方向上具有低轮廓,以便使对通过热解管1的流f的破坏最小化。支撑件61的径向支撑构件75将内部主体3相对于径向外部管状壁2保持在中心位置。支撑件61支承内部主体3的重量。返回参照图7,在内部主体3的上端设置有第二支撑装置52,用于将内部主体3居中地保持在径向外部管状壁2中。第二支撑装置包括引导销68,该引导销68向上突出到间隔环(未示出)径向向内限定的空间。间隔环由三个等角度间隔开的径向支撑构件67支撑,径向支撑构件67从径向外部管状壁2径向向内突出到间隔环,从而将间隔环保持就位。引导销68被间隔环松散地保持,使得它保持在径向外部管状壁2内部的大致中心位置。径向外部管状壁2和内部主体3的相对热膨胀由于间隔环在内部主体3的顶部处对引导销68提供的松散支撑而被允许。图8示出了基于第二类型的热解管1(如图3和图4所示),用作裂解炉中的单通道热解管。图示的热解管1具有环形旋流部段31形式的主要部分,其具有带有螺旋中心线的径向外部管状壁2,以及具有直中心线的内部主体3。第一上过渡部分47位于上入口部分40和环形流动部段31之间,并且第一下过渡部分50布置在环形流动部段31和出口部分42之间。在其下端,第一上过渡部分47接合到热解管1的环形旋流部段31的径向外部管状壁2。它提供从具有其直的中心纵向轴线的上入口部段40到具有其螺旋中心线7(见图3)的径向外部管状壁2的过渡。第一下过渡部分50的上端接合到环形旋流部段31的径向外部管状壁2的下端。因此,第一下过渡部分50提供从具有其螺旋形中心线7的径向外部管状壁2到具有其直中心线的出口部分42的过渡。内部主体3在其上端具有葱形部60,该葱形部60布置成引导流f从第一上过渡部分47进入围绕内部主体3的外部和径向外部管状壁2的内部的环形流动通道5。内部主体3在其下端具有第二葱形部60,该第二葱形部60布置成在流f离开环形流动通道时引导流f。内部主体3尽管在这种情况下具有直中心线而不是螺旋形中心线,但是内部主体3在其下端以与关于图7所述的类似方式被支撑。进一步的细节在图9中被示出。因此,支撑装置51具有设置在内部主体3的下部区域中的支撑件61。支撑件61由三个等角度间隔的径向支撑构件75组成,径向支撑构件75在径向外部管状壁2和内部主体3之间沿径向延伸。如图9所示,径向支撑构件75在纵向方向上具有低轮廓,以便使对通过热解管1的流f的破坏最小化。支撑件61的径向支撑构件75将内部主体3相对于径向外部管状壁2保持在中心位置。支撑件61承载内部主体3的重量。在图9中示出了周向相邻的径向支撑构件75之间的角度120°。在内部主体3的上端设置有第二支撑装置52,用于将内部主体3居中地保持在径向外部管状壁2中。第二支撑装置52包括间隔环71,该间隔环71限定其径向向内空间,内部主体3在该空间内延伸。间隔环71由3个等角度间隔的径向支撑构件67支撑,该径向支撑构件67从径向外部管状壁2径向向内突出到间隔环71,从而将间隔环保持就位。在图10中示出了在周向相邻的径向支撑构件67之间的角度120°。内部主体3由间隔环71和内部主体的顶部松散地保持,使得其保持在径向外部管状壁2内的大致中心位置。径向外部管状壁2和内部主体3的相对热膨胀由于间隔环71在内部主体3顶部处向内部主体3提供的松散支撑而被允许。图11示出了基于第三种类型的热解管1(如图5和图6所示),用作裂解炉中的单通道热解管。图示的热解管1具有环形旋流部段31形式的主要部分,其具有带有直中心线的径向外部管状壁2和具有螺旋中心线的内部主体3。第二上过渡部分48位于上入口部分40和环形流动部段31之间,第二下过渡部分53布置在环形流动部段31和出口部分42之间。在其下端,第二上过渡部分48接合到热解管1的环形旋流部段31的径向外部管状壁2上。它是圆锥形的并且提供从上入口部分40的过渡,上入口部分40具有笔直中心纵向轴线并且直径小于具有其直中心线7(见图5)的径向外部管状壁2的直径。第二下过渡部分53的上端接合到环形旋流部段31的径向外部管状壁2的下端。第二下过渡部分53是圆锥形的并且提供从径向外部管状壁2的过渡,该径向外部管状壁2具有直中心线7并且直径大于具有其直中心纵向轴线的出口部分42的直径。内部主体3在其上端具有葱形部60,该葱形部60设置成引导流f从第二上过渡部分48进入围绕内部主体3的外部和径向外部管状壁2的内部的环形流动通道5。内部主体3在其下端具有第二葱形部60,该第二葱形部60布置成在流f离开环形流动通道时引导流f。内部主体3在其下端由第一支撑装置51支撑,第一支撑装置51与关于图7所描述的相同。内部主体3的上端由第二支撑装置52支撑,该第二支撑装置52与关于图7所描述的相同。图12示出了基于第一类型(如图1和图2所示)的热解管1,其用作裂解炉中的单通道热解管。在这种情况下,内部主体设置有螺旋形弯曲的纵向翅片66。螺旋形翅片66具有螺旋构造,其具有与内部主体3的螺旋构造相同的旋向。螺旋形翅片66的相位,内部主体3的相位和径向外部管状壁2的相位是同相的。图13示出了基于第二种类型的热解管1(如图3和图4所示),用作裂解炉中的单通道热解管。在这种情况下,圆柱形内部主体3设置有螺旋形弯曲的纵向翅片66。螺旋形翅片66具有螺旋构造,其具有与径向外部管状壁2的螺旋构造相同的旋向。螺旋形翅片66的相位和径向外部管状壁2的相位是同相的。图14示出了基于第三种类型的热解管1(如图5和图6所示),用作裂解炉中的单通道热解管。在这种情况下,内部主体设置有螺旋形弯曲的纵向翅片66。螺旋形翅片66具有螺旋构造,其具有与内部主体3的螺旋构造相同的旋向。螺旋形翅片66具有与内部主体3的螺旋构造同相的螺旋构造。图15示出了基于第二种类型的热解管1(如图3和图4所示),用于双通道布置,其中热解管两次通过裂解炉的长度。热解管通常为u形,并且在其上游部分up中,即“u”的上游分支中具有环形旋流部段31,在其下游部分dp中,即“u”的下游分支中具有旋流部段35。与本文公开的所有其他旋流部段35一样,旋流部段31没有内部主体,因此限定在其中的通道是非环形的。通道具有大致圆形的横截面形状。气体流f经由直入口部分40进入并且经由直出口部分42离开。第一上过渡部分47布置在入口部分40下方,在入口部分40和环形旋流部段31之间。第三上过渡部分49布置在出口部分42下方,在旋流部段35和出口部分42之间。第三上过渡部分49在具有其螺旋中心线的旋流部段35和具有其直中心纵向轴线的出口部分42之间提供过渡。第一下过渡部分50布置在环形旋流部段31下方,在该环形旋流部段和第一直中间部段37之间。第三下过渡部分54布置在第二直中间部段37上方,在该部段37与旋流部段35之间。第三下过渡部分54在具有其直纵向中心轴线的第二直中间部段37与具有其螺旋中心线的旋流部段35之间提供过渡。u形弯头部段36布置成连接第一和第二直中间部段37。环形旋流部段31包括内部主体3,该内部主体3由位于其下端的第一支撑装置51以及位于其上端的第二支撑装置52支撑。内部主体3、其中支撑内部主体3的径向外管2以及内部主体3的支撑装置51和52的构造与关于图8、图9和图10描述的构造相同。图16示出了类似于图15的热解管1,不同之处在于,代替在u形弯头部段36的下游设置旋流部段35,存在常规流动部段33。流动部段33在其下端直接连接到u形弯头部段36,并且在其上端直接连接到到出口部分42。图17示出了具有顶部燃烧室12的裂解炉11,热解管1穿过顶部燃烧室12。在燃烧室12的顶部设置有一对下点火燃烧器20。燃烧器布置成接收燃料/空气混合物21,燃烧器火焰22向下指向燃烧室12。燃烧室12具有l形并且包括烟道气出口部分24,在使用中,烟道气23通过烟道气出口部分24从燃烧室排出。热解管1布置成提供通过燃烧室12的单通道。热解管具有带有环形旋流部段31的上游部分up和带有旋流部段35的下游部分dp。直入口部分40布置成接收气流f。入口部分40连接到第一上过渡部分47,该第一上过渡部分47连接到在燃烧室的燃烧区域25中的环形旋流部段31。中间过渡部分34设置在环形旋流部段31下方,在该环形旋流部段和旋流部段35之间。第三下过渡部分54设置在旋流部段35下方,在该旋流部段和出口部分42之间。环形旋流部段31具有与第二种类型的热解管相对应的结构,如相对于图3和图4所描述。它具有圆柱形内部主体3,螺旋形径向外部管状壁2和环形流动通道5,环形流动通道5是螺旋缠绕环形流动通道。环形旋流部段31的包括位于内部主体3下端的第一支撑装置51和位于内部主体上端的第二支撑装置52的进一步结构细节,对应于图8、图9和图10中所描述的结构细节。图17的布置提供螺旋形流动通道上游的螺旋缠绕环形流动通道。图18示出了类似于图17的裂解炉的另一个实施例,因此使用相同的附图标记表示相同的特征。图18的实施例包括裂解炉11,其具有:顶部燃烧炉室或燃烧室12;以及以单通道布置延伸用于气体流f的热解管1。热解管1的上游部分up根据第二种类型的热解管构造,具有环形旋流部段31,该环形旋流部段31以与图17的实施例相同的方式具有圆柱形内部主体3和螺旋形径向外部管状壁2。然而,在上游部分up的下游,下游部分dp包括常规流动部段33(即,具有直中心线的圆柱形径向外部管状壁的流动部段),而不是如图17所示的旋流部段35。环形旋流部段31经由第二中间过渡部分39连接到常规流动部段33,以提供从螺旋形到直线的过渡。因此,在图18的实施例中,热解管1具有上游部分up和下游部分dp,上游部分up具有是螺旋缠绕的环形流动通道的流动通道5,下游部分dp是常规的圆柱形流动部段,具有圆柱形径向外部管状壁并且没有内部主体。图19示出了裂解炉11的另一个实施例,其具有燃烧室12和用于从顶部到底部的气体流f的单通道热解管1。热解管1具有与图17相同的结构,因此该图的描述适用于图19的实施例。图19的燃烧室具有下点火燃烧器20,其也与图17的点火燃烧器相同,因此其描述也适用于此。图19的实施例与图17的实施例之间的区别在于,燃烧室12设置有一对侧壁燃烧器26,每个侧壁燃烧器26都用于接收燃料/空气混合物21的输入以产生火焰27。图20示出了裂解炉11的另一个实施例,在这种情况下具有底部燃烧的燃烧室12。在燃烧室12的底板中设置一对上点火燃烧器20,用于接收相应的燃料/空气混合物流21。燃烧室12形状为倒置的“l”形状,并且具有烟道气出口24,用于排出烟道气23。图20的裂解炉设置有热解管1,热解管1具有与图17相同的结构。气体流f从顶部到底部以单通道通过热解管1。关于图17的热解管1的描述也适用于图20的热解管1。在图20的实施例的情况下,燃烧区25位于燃烧室12的下部。因此,在使用中,气流f从流动通道5流动进入燃烧室的燃烧区25中的旋流部段35(非环形),流动通道5是位于燃烧室的非燃烧区域中的螺旋缠绕的环形流动通道。图21示出了具有燃烧室12和热解管1的裂解炉11的另一个实施例。该实施例的特征与图20实施例的特征相同,因此,图20实施例的描述适用于图21的实施例。图21的实施例与图20的实施例的不同之处在于另外设置侧壁燃烧器26,燃料/空气混合物21被供给到侧壁燃烧器26中以产生火焰27。图22示出了裂解炉11的另一个实施例,其具有燃烧室12和以单通道延伸通过其中的热解管1。热解管1的结构与图17的结构相同,因此图17的描述也适用于图22的实施例。图22的实施例与图17的实施例的不同之处在于,裂解炉具有侧点火燃烧室。多个侧壁燃烧器26设置在燃烧室12的侧壁中,每个侧壁燃烧器26接收燃料/空气混合物21的输入以产生燃烧火焰27。侧壁燃烧器布置成三层,上层靠近燃烧室12的顶部,然后两个相应层位于上层下方。因此,燃烧室12的燃烧区通常位于燃烧室的上半部分中,并且热解管1的环形旋流部段31穿过该燃烧区。不具有环形流动通道的旋流部段35设置在燃烧区25的下游。图23示出了具有燃烧室12和热解管1的裂解炉11的另一个实施例。热解管1的结构与图20的结构相同,因此该图的描述也适用于图23。在图23的实施例中,用于排出烟道气23的烟道气出口24与图20的相同,但燃烧器布置是不同的。在图23中,燃烧室12具有多个侧面安装的燃烧器26,其接收燃料/空气混合物流21以在燃烧室内产生火焰27。侧壁燃烧器26布置成三层,在燃烧室的底板附近有一个较低层,然后两层在其上方。在使用中,气体流f向下通过热解管1的没有燃烧区的上游部分up,部分地进入燃烧区25,环形旋流部段31的下部位于侧壁燃烧器26的上层附近。然后,流f继续向下进入完全位于燃烧区25中的旋流部段35。可以看出,在图15至图23的实施例中,每个都具有上游部分up和下游部分dp,上游部分up具有环形旋流部段31,下游部分dp具有非环形流动部段(常规流动部段33或旋流部段35),环形流动部段的径向外部管状壁2的内径大于非环形流动部段的径向外壁2的内径。图24-29示出了热解管1的设计的变化。在所有这些变型中,热解管1具有两个上游部分up1和up2,其进入单个下游部分dp。在每种情况下,每个上游部分都包括环形旋流部段31。每个下游部分都包括旋流部段35或常规流动部段33,即,包括具有直中心线的圆柱形径向外部管状壁的流动部段33。图24和图25的实施例提供了气流f通过裂解炉的单通道。在每种情况下,两个上游部分up1和up2在y形结点部分38处接合,其中在两个上游部分中的每一个中流动的分离气体在下游部分dp中合并成单股流。每个上游部分根据第二类型的热解管设计构造并且具有彼此相同的特征。每个上游部分up1、up2在顶部处具有入口部分40,在入口部分下方具有第一上过渡部分47,并且在第一上过渡部分下方具有环形旋流部段31,环形旋流部段31提供流动通道5,该流动通道5是螺旋缠绕的环形流动通道。在其下端,环形旋流部段31通过第二中间过渡部分39连接到y形结点部分38,以提供从螺旋形到直线的过渡。提供环形流动通道5的两个上游部分up1和up2的部分的构造对应于关于图8、图9和图10所描述的部分。圆柱形内部主体3通过在内部主体3的下端处的第一支撑装置51和在内部主体的上端处的第二支撑装置52支撑在螺旋形径向外部管状壁2内部。以上在图8、图9和图10的描述中解释了关于支撑装置的更多细节。上游和下游部分up1、up2的特征在图24和图25的实施例中是相同的。下游部分dp在这两个实施例之间不同。在图24的实施例中,下游部分dp具有螺旋形外部管2,以便提供旋流部段35。旋流部段35没有内部主体,因此限定在其中的通道是非环形的。通道具有大致圆形的横截面形状。第三下过渡部分54布置在旋流部段35下方,在该旋流部段和直出口部分42之间,提供从螺旋形到直线的过渡。在图25的实施例中,在y形结点部分38的下游设置有常规流动部段33,而不是如图24所示的旋流部段35。常规流动部段33直接连接到出口部分42。图26、图27、图28和图29的实施例涉及热解管,这些热解管提供流f通过裂解炉的双通道。在每种情况下,流动方向通过一个或多个u形弯头从两个上游部分up1和up2中的向下流动方向反转到单个下游部分dp中的向上流动方向。在每种情况下,两个上游部分up1、up2具有环形旋流部段31,其具有第二类型的热解管设计。因此,它们各自具有圆柱形内部主体3,具有螺旋构造的径向外部管状壁2,以及作为螺旋缠绕环形流动通道的流动通道5。参照图26的实施例,两个上游部分up1、up2具有彼此相同的结构,因此将仅描述它们中的一个。每个上游部分up1、up2设置有相应的入口部分40。第一上过渡部分47位于入口部分40下方并且接合到环形旋流部段31,即,热解管1的具有螺旋缠绕环形流动通道5的那部分。在环形旋流部段31的下端处,第一下过渡部分50连接到直中间部段37,该中间部段又连接到u形弯头部段36的一个分支。u形弯头部段36的另一个分支连接到另一个直中间部段37,并且该另一个直中间部段连接到y形结头部分38。在y形结头部分38的上方设置有第三中间过渡部分41,该第三中间过渡部分41连接到下游部分dp的旋流部段35。这提供了从y形结头部分的直线部分到螺旋形旋流部段35的过渡,螺旋形旋流部段35的径向外部管状壁2具有螺旋中心线。第三上过渡部分49设置在旋流部段35的下游端和出口部分42的上游端之间,以提供从螺旋形到直线的过渡。在图27的实施例中,两个上游部分up1和up2、下过渡部分50、直中间部段37、u形弯头部段36和y形结点部分38的结构与图26的实施例的等同物特征的那些结构相同并且其相对于图26的描述适用于图27。图27的实施例与图26的实施例的不同之处在于,下游部分dp具有常规流动部段33而不是旋流部段35。在其上游端,常规流动部段33直接连接到y形结点部分38,并且在其下游端,它直接连接到直出口部分42。可以看出,在图26和图27的实施例中,每个上游部分up1和up2经由相应的u形弯头部段36接合到y形结点部分38,在y形结点部分中来自各个上游部分up1和up2的流动被合并。在一个y形结点部分38的下游有两个u形弯头部段36。在图26和图27的热解管中,下游部分dp位于上游部分up1和up2之间。当这种热解管位于裂解炉中的燃烧器之间时,例如如图17至图23的任何布置所示,下游部分dp比上游部分up1和up2与燃烧器更隔热。效果是来自炉子的热输入在形成下游部分dp的热解管部分的圆周周围相对均匀,而不是在管子直接暴露于来自燃烧器的辐射的地方更多且在未暴露的地方更少。这种设计的优点在于,在下游部分上径向穿过管壁的热通量分布接近理想状态,趋向于在管的圆周周围具有大致相似的轮廓。这减小了峰值热通量和平均热通量之间的差异,使得峰值管金属温度和平均管金属温度之间的差异最小,从而延长了在除焦操作之间热解管的运行长度。图28和图29的实施例类似于图26和图27的实施例,因为存在两个上游部分up1和up2,从两个上游部分的流出物结合到单个下游部分dp。然而,在这些实施例的情况下,存在单个u形弯头部段36,其由y形结点部分38供给,y形结点部分38本身通过两个上游部分up1和up2经由相应的第一下过渡部分50供给。除此之外,图28和图29的实施例中的两个上游部分up1和up2的结构与图26实施例的上游部分up1和up2的结构相同,并且其描述适用于图28和图29的实施例。参照图28的实施例,其具有包括旋流部段35的下游部分dp,即,旋流部段具有带有螺旋中心线的径向外部管状壁2。u形弯头部段36连接到直中间部段37,该中间部段37又连接到第三下过渡部分54。这提供了到旋流部段35的过渡。图29的实施例与图28的实施例的不同之处在于,下游部分dp是常规流动部段33,即,它具有带有直中心线的圆柱形的径向外部管状壁。常规流动部段33在其上游端直接连接到u形弯头部段36,并且在其下游端直接连接到直出口部分42。图15-29的实施例示出了第二类型的热解管,但是这些热解管也可以是第一类型或第三类型。无论是第一类型、第二类型、还是第三类型,它们都可以包括至少一个突出到环形流动通道中的螺旋突起。在上述所有实施例中,存在螺旋缠绕的环形流动通道,其中促进了气体沿着热解管流动时的旋转。促进环形流动通道中的气流旋转改善了向气体中的热传递。旋转流动可导致气体紧接着在轴向速度分量具有径向速度分量,即,所谓的旋流。环形通道中的旋流改善了对流传热,而内部主体用于产生促进环形流动通道的旋转流动。因为改善了对流传热,所以与常规热解管相比,可以使用更短长度的热解管来实现进入气体中的相同量的热传递。这反过来实现了低停留时间并且提高了产率,即,产生所需的裂化产物。比较例参考:vangoethem,m.w.m.,jelsma,e.,2014。高温应用中强化传热和压降的数值和实验研究;化学工程研究与设计92,663-671。本文包含比较常规流动和旋流的计算流体动力学(cfd)研究的结果。对于本说明书,在相同的基础上进行环形旋流的cfd研究。对裂解炉中三种热解管的性能进行了比较。结果如下表所示。参数常规旋流环形旋流流速单位:千克/时500500500外部管外径单位:m0.060.0640.089外部管内径单位:m(do)0.0520.0560.078内部主体外径单位:m(di)0.047长度单位:m12.008.686.49负载率100%100%100%压降100%100%100%热解管长度100%72%54%停留时间100%84%77%表头为“常规”的列涉及具有直中心线的常规热解管。表头为“旋流”的列涉及从wo2010/032024中已知类型的热解管,其具有螺旋中心线和无阻塞的流动腔,即,没有内部主体。在这种情况下,螺旋的振幅a为16.8mm,并且节距p为434mm。从表中可以看出,管的内径do为56mm。因此,螺旋中心线的相对振幅a/do为30%。相对节距p/do为7.75。表头为“环形旋流”的列涉及本发明的基于第三种类型的热解管的实施例,其中内部主体3具有螺旋中心线并且径向外部管2具有直中心线。螺旋中心线的振幅a为23.4mm,并且节距p为605mm。因此,相对振幅a/do为0.3,并且相对节距p/do为7.75。应注意,在该研究中,对于所有实例,某些参数被设定为相同。因此,所有热解管具有500千克/小时的相同质量流速。所有管的尺寸使得它们具有相同的100%“负载率”。这意味着在每个示例中,来自炉腔的在管出口处的管的外表面温度比在出口处的管内的平均气体温度大相同的量。该温差为190℃。在所有情况下,热解管的平均气体入口温度和平均气体出口温度也设定为相等。因此,管的尺寸(长度和直径)被设计为使得“负载率”,即,在如上所述的出口处具有温差,在每种情况下是相同的。所有管都具有不同的摩擦特性。在该研究中,调整尺寸(长度和直径)使得所有情况下的压降也相同。然后可以说压降对产量的影响对于所有情况都是相同的。结果是一张突出了热解管几何形状对管长度和停留时间的影响的表格。从表中可以看出,具有螺旋中心线(旋流)的热解管导致热解管长度减少至常规热解管长度的72%,并且对于常规的热解管而言,停留时间减少至84%。然而,使用本发明实施例的示例(“环形旋流”)导致这些参数的更大减少。长度减少了46%,从100%减少到54%。重要的是,停留时间从100%减少到77%,减少了23%。停留时间是最感兴趣的参数,因为这决定了该过程的选择性。在相同的温度和压力条件下减少停留时间导致对初级裂化产物,即,乙烯、丙烯、丁二烯的选择性提高。当前第1页12