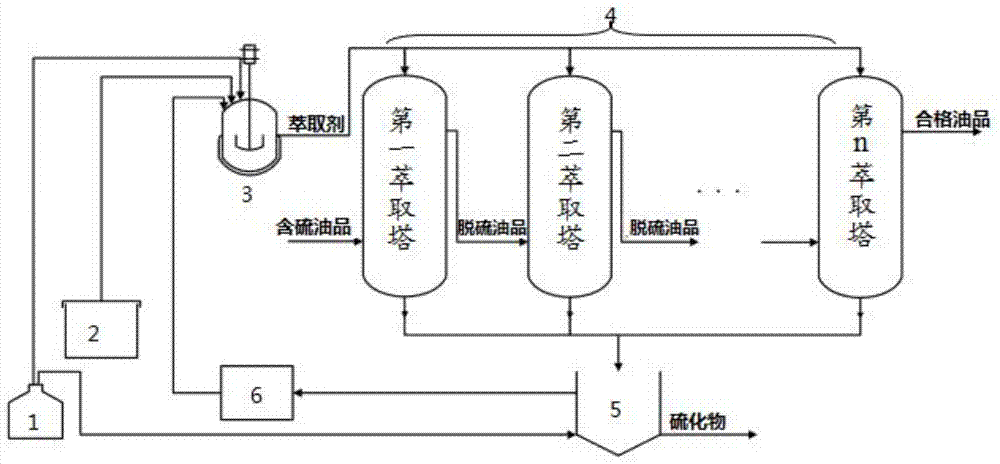
本发明涉及油品脱硫的
技术领域:
,特别涉及一种水基低共熔溶剂及其制备方法和一种油品萃取脱硫方法。
背景技术:
:工业的迅猛发展给环境带来的污染越来越严重,其中含硫化合物的燃烧对环境的污染尤为严重。燃油中含硫化合物燃烧产生的SOx会对人体的黏膜和呼吸道的粘膜有着强烈的刺激,严重会引发支气管炎甚至于肺水肿呼吸麻痹。另外,排放到空气中的SO2会与水汽发生反应形成硫酸型酸雨,严重污染环境。在现今环境问题亟待解决的情况下,国家对于燃油中硫的含量给出了日益严格的标准,直至目前要求低于10ppm。目前工业上广泛使用的脱硫方法是加氢脱硫,加氢脱硫是指将含硫化合物用高选择性的催化剂作用,在氢气的氛围下反应转化为硫化氢的反应。然而,由于催化剂表面吸附的空间位阻效应,这种脱硫方法对于芳香性有机硫化物的脱去效果不佳,并且脱硫过程是在高温高压的苛刻条件下进行的。这些局限性使得加氢脱硫的方法已经难以满足目前人们对于高品质燃油的需求,必须找寻新的脱硫方法。如今,非加氢脱硫的方法主要有吸附脱硫、生物脱硫、氧化脱硫和萃取脱硫。其中,萃取脱硫以温和的操作条件以及简单的操作流程得到了研究者们的青睐,成为非常有前景的新型脱硫技术。目前常用脱硫用萃取剂一般为N,N-二甲基甲酰胺、N-甲基吡咯烷酮等,这些萃取剂本身具有毒害性,且萃取剂再生困难、脱硫方法复杂。低共熔溶剂是指由两种或三种化合物组成的低共熔混合物,其凝固点显著低于各个组分纯物质的熔点。相比于传统的有机溶剂,低共熔溶剂具有极低蒸汽压、高的热力学和化学稳定性、极低的毒害性等诸多优点;而对于离子液体来说,低共熔溶剂也有着更加容易制备,原料来源更加广泛、更加廉价等优点。但是,目前的低共熔溶剂多以有机溶剂为氢键供体,不具备环保性,且应用于萃取脱硫时脱硫率不高。此外,萃取剂再生时,往往会加入有机溶剂如乙醚等反萃取剂对硫组分进行反萃取,再生过程中有机溶剂的加入会造成环境污染和再生后萃取剂的污染。技术实现要素:有鉴于此,本发明目的在于提供一种水基低共熔溶剂及其制备方法和一种油品萃取脱硫方法。本发明提供的水基低共熔溶剂以水为氢键供体,绿色环保、具有可生物降解性;使用该水基低共熔溶剂对油品进行萃取脱硫,脱硫方法简单,效果好,且再生性好,可循环使用。为了实现上述发明目的,本发明提供以下技术方案:一种水基低共熔溶剂,包括氢键供体和氢键受体,所述氢键受体为季铵盐和/或季磷盐,所述氢键供体为水;所述氢键受体和氢键供体的摩尔比为1:0.5~20。优选的,所述季铵盐的阳离子具有式I所示结构;式I中,R1、R2、R3和R4独立地为C1~C10的烷基;所述季铵盐的阴离子为氯离子或溴离子。优选的,所述季磷盐的阳离子具有式Ⅱ所示结构;式Ⅱ中,R5、R6、R7和R8独立地为C1~C10的烷基;所述季磷盐的阴离子为氯离子或溴离子。本发明提供了上述方案所述水基低共熔溶剂的制备方法,包括以下步骤:在20~80℃条件下将氢键受体与水混合,得到水基低共熔溶剂,所述氢键受体包括季铵盐和/或季磷盐。本发明提供了一种利用上述方案所述水基低共熔溶剂或上述方案所述制备方法制备的水基低共熔溶剂进行油品萃取脱硫的方法,包括以下步骤:将水基低共熔溶剂和含硫油品混合进行萃取脱硫,分液后得到萃取相和脱硫油品。优选的,所述水基低共熔溶剂和含硫油品的质量比为1:10~10:1。优选的,所述萃取脱硫的温度为20~80℃。优选的,所述萃取脱硫包括依次进行的搅拌和静置;所述搅拌的转速为500~1400rpm,所述搅拌的时间为0.2~3h;所述静置的时间为0.2~5h。优选的,所述分液后还包括水基低共熔溶剂的再生;所述再生包括以下步骤:将所述萃取相和水混合使硫化物析出,将所述析出的硫化物分离后得到低共熔溶剂溶液相;将所述低共熔溶剂溶液相蒸馏,得到再生水基低共熔溶剂。优选的,所述水的加入量以加至萃取相和水的混合溶液的摩尔含水量为20~99.1%为准。本发明提供了一种水基低共熔溶剂,包括氢键供体和氢键受体,所述水基低共熔溶剂的氢键受体为季铵盐和/或季磷盐,氢键供体为水;所述氢键受体和氢键供体的摩尔比为1:0.5~20。本发明提供的水基低共熔溶剂以水为氢键供体,相比传统低共熔溶剂使用有机溶剂为氢键供体,本发明提供的水基低共熔溶剂具有很高的绿色环保性;本发明提供的水基低共熔溶剂毒性极低,具有可生物降解性,且其制备方法简单,无腐蚀性,脱硫能力强,可再生性好,使用本发明提供的水基低共熔溶剂为萃取剂进行油品脱硫时,对设备以及操作方式无特殊要求。本发明提供了一种利用上述方案所述水基低共熔溶剂进行油品萃取脱硫的方法,包括以下步骤:将水基低共熔溶剂和含硫油品混合进行萃取脱硫,分液后得到萃取相和脱硫油品。本发明提供的萃取脱硫方法以水基低共熔溶剂为萃取剂,水基低共熔溶剂的氢键受体为季铵盐和/或季磷盐,季铵盐和季磷盐可与油品中的硫化物产生氢键和/或CH-π相互作用,从而将硫化物萃取到水基低共熔溶剂相中,本发明提供的脱硫方法简单,效果好。进一步的,本发明通过向萃取相中加入氢键供体(水)即可对萃取剂进行再生,整个萃取剂再生过程,无需加入反萃取剂等其他物质,使得整个脱硫系统中油品和萃取剂都不会受到其他污染,且对环境也无污染;并且在萃取剂再生的同时,可以分离出高纯度的硫化物进行再利用。本发明提供的方法整个脱硫过程与萃取剂再生过程条件温和,操作简单并且易连续化,适合于工业生产。实施例结果表明,本发明提供的萃取脱硫方法的单级脱硫率可达到70.4%,且经过四级脱硫后,油品硫含量可降至5.1ppm;萃取剂再生8次后的脱硫率与新鲜低共熔溶剂的脱硫率基本一致。附图说明图1为本发明的萃取流程示意图。图1中:1-水槽,2-原料槽,3-搅拌釜,4-萃取塔系统,5-沉淀池,6-干燥箱。具体实施方式本发明提供了一种水基低共熔溶剂,包括氢键受体和氢键供体,所述水基低共熔溶剂的氢键受体为季铵盐和/或季磷盐,氢键供体为水;所述氢键受体和氢键供体的摩尔比为1:0.5~20。本发明提供的水基低共熔溶剂的氢键受体为季铵盐和/或季磷盐。在本发明中,所述季铵盐的阳离子优选具有式I所示结构;在本发明中,式I中R1、R2、R3和R4独立地优选为C1~C10的烷基,更优选为C1~C8的烷基,更优选为甲基、乙基、正丙基、异丙基、正丁基、异丁基、正戊基、异戊基、正己基、2-甲基戊基、3-甲基戊基、正庚基或正辛基。在本发明中,所述季铵盐的阳离子优选为四乙基铵阳离子、四乙基磷阳离子、四丁基铵阳离子、四丁基磷阳离子、四己基铵阳离子或四己基磷阳离子。在本发明中,所述季铵盐的阴离子优选为氯离子或溴离子;在本发明中,所述季铵盐具体的优选为四丁基氯化铵和/或四丁基溴化铵。在本发明中,所述季磷盐的阳离子优选具有式Ⅱ所示结构;在本发明中,所述R5、R6、R7和R8的种类独立的优选和上述方案所述R1、R2、R3和R4的种类一致,在此不再赘述。在本发明的具体实施例中,所述季磷盐的阴离子优选为氯离子或溴离子;在本发明中,所述季磷盐具体的优选为四丁基氯化磷和/或四丁基溴化磷。在本发明中,所述水基低共熔溶剂的氢键供体为水。本发明对所述水没有特殊要求,使用本领域技术人员熟知的水即可。在本发明中,所述氢键受体和氢键供体的摩尔比优选为1:0.5~20,更优选为1:0.5~10。本发明将氢键受体和氢键供体的摩尔比控制在此范围内,可保证氢键供体和氢键受体之间形成氢键,且对硫化物有较好的萃取能力。本发明提供了上述方案所述水基低共熔溶剂的制备方法,包括以下步骤:在20~80℃条件下将氢键受体和水混合,得到水基低共熔溶剂;所述氢键受体为季铵盐和/或季磷盐。在本发明中,所述混合的温度为20~80℃,优选为30~60℃,更优选为40℃;本发明优选在搅拌条件下进行混合,所述搅拌的转速优选为100~1000rpm,优选为300~600rpm;所述的搅拌时间优选为0.01~3h,更优选为0.2~1h。本发明直接在20~80℃条件下将氢键供体和氢键受体混合即可,制备方法简单。在本发明的具体实施例中,优选将氢键受体和水混合后在搅拌条件下升温至20~80℃;本发明的搅拌时间自升温至所需的混合温度时开始计算。本发明提供了一种利用上述方案所述水基低共熔溶剂进行油品萃取脱硫的方法,包括以下步骤:将水基低共熔溶剂和含硫油品混合进行萃取脱硫,分液后得到萃取相和脱硫油品。在本发明中,所述含硫的油品优选为本领域常规的石油产品,如未经过深度脱硫处理的油品,优选为待深度脱硫汽油、柴油、煤油、石脑油、重油中的一种或多种,更优选为待深度脱硫的汽油和/或柴油;本发明对所述的含硫油品中硫化物的含量没有特殊要求,所有待深度脱硫的油品都可以使用本发明的方法进行脱硫,在本发明的具体实施例中,所述含硫油品的硫化物的含量优选在10ppm以上。在本发明中,所述水基低共熔溶剂和含硫油品的质量比优选为1:10~10:1,更优选为1:5~5:1,进一步优选为1:3~3:1。在本发明中,所述萃取脱硫的温度优选为20~80℃,更优选为25~65℃,所述萃取脱硫优选包括依次进行的搅拌和静置;所述搅拌的转速优选为500~1400rpm,更优选为600~1100rpm;所述搅拌的时间优选为0.2~3h,更优选为0.5~2h;所述静置的时间优选为0.2~5h,更优选为0.5~2h。在本发明中,所述搅拌和静置均在20~80℃条件下进行,静置后得到上层的含硫油品和下层的萃取相。静置分层后,本发明进行分液。本发明对所述分液的具体方法没有特殊要求,能够将两相分离即可。在本发明的具体实施例中,优选使用倾析法将两相分离。在本发明中,萃取过程中水基低共熔溶剂中的氢键受体和硫化物相互作用,从而将硫化物萃取到水基低共熔溶剂相中。萃取后得到的脱硫油品可根据硫含量的水平直接作为产品或进入下一级萃取脱硫,后续的萃取过程和上述方案一致,在此不再赘述;本发明提供的方法可反复进行多级萃取脱硫,直至油品中的硫含量符合标准为止。在本发明中,所述分液后还包括水基低共熔溶剂的再生;所述再生包括以下步骤:将所述萃取相和水混合使硫化物析出,将所述析出的硫化物分离后得到低共熔溶剂溶液相;将所述低共熔溶剂溶液相蒸馏,得到再生水基低共熔溶剂。本发明将所述萃取相和水混合使硫化物析出,所述析出的硫化物分离后得到硫化物和低共熔溶剂溶液相。在本发明中,所述水的加入量优选以加至萃取相和水的混合溶液的摩尔含水量为20~99.1%为准,更优选为30~90%;本发明向萃取相中加入氢键供体水,破坏硫化物和氢键受体的氢键和/或CH-π结合作用,从而使硫化物析出。硫化物析出后,本发明将所述析出的硫化物分离。本发明优选在硫化物析出后进行静置,使硫化物析出完全后再进行分离;所述静置的时间优选为0.5~48h,更优选为2~45h,最优选为5~36h;所述静置的温度优选为-10~30℃,更优选为10~25℃。在本发明中,当所述的含硫油品中的硫化物的熔点较高时,静置后硫化物以固体析出,本发明优选通过沉降和/或过滤将固态硫化物分离;当所述的含硫油品中的硫化物的熔点较低时,静置后硫化物以液体析出,本发明优选通过倾析将硫化物分离。本发明分离得到的硫化物为高纯硫化物,可直接进行再利用。将硫化物分离后,本发明将得到的低共熔溶剂溶液相蒸馏,得到再生水基低共熔溶剂。在本发明中,所述蒸馏的温度优选为50~100℃,更优选为60~80℃;所述蒸馏的压力优选为1~101kPa,更优选为10~100kPa,进一步优选为30~80kPa;所述蒸馏处理的时间优选为0.5~8h,更优选为1~6h。本发明通过蒸馏将所述低共熔溶剂溶液相中的水蒸除,在本发明的具体实施例中,通过蒸馏将低共熔溶剂溶液相中过量的水蒸除,若剩余物中氢键受体和水的摩尔比符合1:0.5~20的比例,则剩余物即为再生水基低共熔溶剂;若剩余物中含水量较少,可向剩余物中再加入部分水,使氢键受体和水的摩尔比符合1:0.5~20的比例;或,若蒸馏使低共熔溶剂溶液相中的水基本全部蒸出,而氢键受体以固态析出,此时可将固态氢键受体和水混合再次制备水基低共熔溶剂,从而得到再生水基低共熔溶剂。在本发明中,再生水基低共熔溶剂可作为萃取剂继续进行含硫油品的萃取脱硫。本发明提供的萃取脱硫方法的整个脱硫过程与萃取剂再生过程条件温和,操作简单,易连续化,适合于工业生产;在本发明的具体实施例中,优选按照图1所示系统进行工业化连续萃取脱硫。图1所示系统包括水槽(1)、原料槽(2)、入口和水槽以及原料槽出口相连的搅拌釜(3)、入口和搅拌釜出口相连的萃取塔系统(4);和萃取塔系统中各个萃取塔底部出口相连的沉淀池(5)、和沉淀池出口相连的干燥箱(6);所述沉淀池设置有硫化物出口;所述沉淀池设置有和水槽出口相连的入水口;所述萃取塔系统包括n个萃取塔,依次为第一萃取塔至第n萃取塔,其中n≥1,n个萃取塔串联相接,第n个萃取塔设置有合格油出口。当使用图1所示系统进行萃取脱硫时,将氢键受体置于原料槽(2)中,和水槽(1)中的水一同进入搅拌釜(3)中进行搅拌,得到萃取剂(即水基低共熔溶剂),然后萃取剂进入萃取塔系统(4)中进行萃取脱硫,萃取后得到合格油品,萃取相进入沉淀池(5)中,同时水槽向沉淀池中输入水,使硫化物析出并分离,分离后的水基低共熔溶剂溶液相进入干燥箱(6)中干燥,得到再生的氢键受体,再生氢键受体进入搅拌釜(3)中循环使用。下面结合实施例对本发明提供的水基低共熔溶剂及其制备方法和一种油品萃取脱硫方法进行详细的说明,但是不能把它们理解为对本发明保护范围的限定。下述实施例中,使用模型油进行相应的实验,所述的模型油的制备方法为:将一定量的硫化物(噻吩,苯并噻吩,二苯并噻吩)溶解在一定比例的正庚烷、正辛烷和甲苯的混合液中;所述模型油中硫化物的初始含量为500ppm~600ppm(含硫化物的油品中硫化物的常规含量即为500~600ppm)。实施例1将5g四丁基溴化磷和0.53g水加入烧瓶中,在常压搅拌下升温至40℃,搅拌转速500rpm,搅拌30min即可得到澄清透明的水基低共熔溶剂。将5g合成的水基低共熔溶剂和5g含硫(二苯并噻吩)500ppm的模型油加入到烧瓶中,在常压、温度为25℃下,搅拌30min,搅拌转速800rpm,静置30min分层,通过倾析将油相与萃取相分离,其中萃取相通过后续的再生操作回收低共熔溶剂进行重复利用。用硫氮分析仪准确检测上层油相的硫含量,结果显示上层油相硫含量降至148ppm,单级脱硫率为70.4%。实施例2将5g四丁基溴化磷和0.79g水加入烧瓶中,在常压搅拌下升温至40℃,搅拌转速500rpm,搅拌30min即可得到澄清透明的水基低共熔溶剂。将5g合成的水基低共熔溶剂和5g含硫(二苯并噻吩)500ppm的模型油加入到烧瓶中,在常压、温度为25℃下,搅拌30min,搅拌转速800rpm,静置30min分层,通过倾析将油相与萃取相分离,其中萃取相通过后续的再生操作回收低共熔溶剂进行重复利用。用硫氮分析仪准确检测上层油相的硫含量,结果显示上层油相硫含量降至166ppm,单级脱硫率为66.8%。实施例3将5g四丁基溴化磷和1.33g水加入烧瓶中,在常压搅拌下升温至40℃,搅拌转速500rpm,搅拌30min即可得到澄清透明的水基低共熔溶剂。将5g合成的水基低共熔溶剂和5g含硫(二苯并噻吩)500ppm的模型油加入到烧瓶中,在常压、温度为25℃下,搅拌30min,搅拌转速800rpm,静置30min分层,通过倾析将油相与萃取相分离,其中萃取相通过后续的再生操作回收低共熔溶剂进行重复利用。用硫氮分析仪准确检测上层油相的硫含量,结果显示上层油相硫含量降至214ppm,单级脱硫率为57.3%。实施例4将5g四丁基氯化铵和0.65g水加入烧瓶中,在常压搅拌下升温至40℃,搅拌转速500rpm,搅拌30min即可得到澄清透明的水基低共熔溶剂。将5g合成的水基低共熔溶剂和5g含硫(二苯并噻吩)500ppm的模型油加入到烧瓶中,在常压、温度为25℃下,搅拌30min,搅拌转速800rpm,静置30min分层,通过倾析将油相与萃取相分离,其中萃取相通过后续的再生操作回收低共熔溶剂进行重复利用。用硫氮分析仪准确检测上层油相的硫含量,结果显示上层油相硫含量降至138ppm,单级脱硫率为72.4%。实施例5将5g四丁基溴化磷和0.53g水加入烧瓶中,在常压搅拌下升温至40℃,搅拌转速500rpm,搅拌30min即可得到澄清透明的水基低共熔溶剂。将5g所合成的水基低共熔溶剂和5g含硫(苯并噻吩)500ppm的模型油加入到烧瓶中,在常压、温度为25℃下,搅拌30min,搅拌转速800rpm,静置30min分层,通过倾析将油相与萃取相分离,其中萃取相通过后续的再生操作回收低共熔溶剂进行重复利用。用硫氮分析仪准确检测上层油相的硫含量,结果显示上层油相硫含量降至155ppm,单级脱硫率为69.1%。实施例6将5g四丁基溴化磷和0.53g水加入烧瓶中,在常压搅拌下升温至40℃,搅拌转速500rpm,搅拌30min即可得到澄清透明的水基低共熔溶剂。将5g所合成的水基低共熔溶剂和5g含硫(噻吩)500ppm的模型油加入到烧瓶中,在常压、温度为25℃下,磁力搅拌30min,搅拌转速800rpm,静置30min分层,通过倾析将油相与萃取相分离,其中萃取相通过后续的再生操作回收低共熔溶剂进行重复利用。用硫氮分析仪准确检测上层油相的硫含量,结果显示上层油相硫含量降至166ppm,单级脱硫率为66.8%。实施例7将5g四丁基溴化磷和0.53g水加入烧瓶中,在常压搅拌下升温至40℃,搅拌转速500rpm,搅拌30min即可得到澄清透明的水基低共熔溶剂。将5g合成的水基低共熔溶剂和5g含硫(二苯并噻吩)600ppm的模型油加入到烧瓶中,在常压、温度为25℃下,搅拌30min,搅拌转速800rpm,静置30min分层,通过倾析将油相与萃取相分离,其中萃取相通过后续的再生操作回收低共熔溶剂进行重复利用。用硫氮分析仪准确检测上层油相的硫含量。上层油相硫含量降至177ppm,单级脱硫率为70.5%。为探究多级萃取的可行性,将萃余相导入下一级进行萃取操作,各级萃取操作的条件与步骤和第一级保持一致,经过连续四级的萃取脱硫操作,油品硫含量降至5.1ppm,满足深度脱硫要求,各级脱硫率保持稳定,第一级到第四级脱硫率分别为70.5%、69.8%、69.3%和69.0%。实施例8将5g四丁基溴化磷和0.53g水加入烧瓶中,在常压搅拌下升温至40℃,搅拌转速500rpm,搅拌30min即可得到澄清透明的水基低共熔溶剂。将5g所合成的水基低共熔溶剂和5g含硫(二苯并噻吩)600ppm的模型油加入到烧瓶中。在常压下,分别在温度为20℃、25℃、30℃、40℃、50℃下搅拌30min,搅拌转速800rpm,静置30min分层,通过倾析将油相与萃取相分离。用硫氮分析仪准确检测上层油相的硫含量,各温度条件下的脱硫率列于表1中。表1不同脱硫温度条件下的脱硫率温度/℃2025304050脱硫率%69.470.168.766.962.5根据表1中的数据可以看出,在20~50℃条件下均有较高的脱硫率,且随着温度的升高,脱硫率有一个先上升后下降的趋势,25℃条件下脱硫率最好。实施例9将5g四丁基溴化磷和0.53g水加入烧瓶中,在常压搅拌下升温至40℃,搅拌转速500rpm,搅拌30min即可得到澄清透明的水基低共熔溶剂。将5g合成的低共熔溶剂和5g含硫(二苯并噻吩)500ppm的模型油加入到烧瓶中,在常压、温度为25℃下,搅拌30min,搅拌转速800rpm,静置30min分层,通过倾析将油相与萃取相分离。用硫氮分析仪准确检测上层油相的硫含量,结果显示上层油相硫含量降至148ppm,单级脱硫率为70.4%。向萃取相中加入12.73g水,然后在常压、温度为25℃下静置12h,静置过后溶液中有明显的白色针状晶体析出,析出的晶体为二苯并噻吩,将静置后的溶液用滤孔直径为0.22微米的滤头过滤;随后将滤液在80℃、1kPa下旋蒸5h得到白色固体实现四丁基溴化磷的再生,将再生后的四丁基溴化磷继续与水合成水基低共熔溶剂进行萃取脱硫操作,操作条件与之前保持一致。再生之后的脱硫率为68.4%,较新鲜低共熔溶剂的脱硫率仅略有降低。实施例10将5g四丁基溴化磷和0.53g水加入烧瓶中,在常压搅拌下升温至40℃,搅拌转速500rpm,搅拌30min即可得到澄清透明的水基低共熔溶剂。将5g合成的水基低共熔溶剂和5g含硫(二苯并噻吩)500ppm的模型油加入到烧瓶中,在常压、温度为25℃下,搅拌30min,搅拌转速800rpm,静置30min分层。用硫氮分析仪准确检测上层油相的硫含量,结果显示上层油相硫含量降至147.5ppm,单级脱硫率为70.5%。脱硫操作完成后,通过倾析将油相与萃取相分离,向萃取相中加入15.38g水,然后在常压、温度为25℃下静置12h,静置过后溶液中有明显的白色针状晶体析出,析出的晶体为二苯并噻吩,将静置后的溶液用滤孔直径为0.22微米的滤头过滤;随后将滤液在80℃、1kPa下旋蒸5h得到白色固体实现四丁基溴化磷的再生。将再生后的四丁基溴化磷继续与水合成水基低共熔溶剂进行萃取脱硫操作,操作条件与之前保持一致。再生之后的脱硫率为69.11%,较新鲜低共熔溶剂的脱硫率略微有些降低。实施例11将5g四丁基溴化磷和0.53g水加入烧瓶中,在常压搅拌下升温至40℃,搅拌转速500rpm,搅拌30min即可得到澄清透明的水基低共熔溶剂。将5g合成的水基低共熔溶剂和5g含硫(二苯并噻吩)500ppm的模型油加入到烧瓶中,在常压、温度为25℃下,搅拌30min,搅拌转速800rpm,静置30min分层。用硫氮分析仪准确检测上层油相的硫含量。上层油相硫含量降至149ppm,单级脱硫率为70.2%。脱硫操作完成后,通过倾析将油相与萃取相相分离。向萃取相中加入20.69g水,然后在常压、温度为25℃下静置12h,静置过后溶液中有明显的白色针状晶体析出,析出的晶体为二苯并噻吩,将静置后的溶液用滤孔直径为0.22微米的滤头过滤;随后将滤液在80℃、1kPa下旋蒸1.5h,得到的液体中氢键受体和水的摩尔比1:2,实现水基低共熔溶剂的再生。将再生后的水基低共熔溶剂进行萃取脱硫操作,操作条件与之前保持一致。再生之后的脱硫率为69.88%,与新鲜低共熔溶剂的脱硫率基本一致。实施例12将5g四丁基溴化磷和0.53g水加入烧瓶中,在常压搅拌下升温至40℃,搅拌转速500rpm,搅拌30min即可得到澄清透明的水基低共熔溶剂。将5g合成的水基低共熔溶剂和5g含硫(二苯并噻吩)500ppm的模型油加入到烧瓶中,在常压、温度为25℃下,搅拌30min,搅拌转速800rpm,静置30min分层。用硫氮分析仪准确检测上层油相的硫含量,结果显示上层油相硫含量降至148.5ppm,单级脱硫率为70.3%。脱硫操作完成后,通过倾析将油相与低共熔溶剂相分离。向萃取相中加入25.99g水,然后在常压、温度为25℃下静置12h。静置过后溶液中有明显的白色针状晶体析出,析出的晶体为二苯并噻吩。将静置后的溶液用滤孔直径为0.22微米的滤头过滤;随后将滤液在80℃、1kPa下旋蒸5h得到白色固体实现四丁基溴化磷的再生。将再生后的四丁基溴化磷继续与水合成水基低共熔溶剂与水进行萃取脱硫操作,操作条件与之前保持一致。再生之后的脱硫率为70.2%,与新鲜低共熔溶剂的脱硫率一致。实施例13将5g四丁基溴化磷和0.53g水加入烧瓶中,在常压搅拌下升温至40℃,搅拌转速500rpm,磁力搅拌30min即可得到澄清透明的水基低共熔溶剂。将5g合成的水基低共熔溶剂和5g含硫(二苯并噻吩)500ppm的模型油加入到烧瓶中,在常压、温度为25℃下,磁力搅拌30min,搅拌转速800rpm,静置30min分层。用硫氮分析仪准确检测上层油相的硫含量,结果显示上层油相硫含量降至148ppm,单级脱硫率为70.4%。脱硫操作完成后,通过倾析将油相与低共熔溶剂相分离。向萃取相中加入12.73g水,然后在常压、温度为25℃下静置12h。静置过后溶液中有明显的白色针状晶体析出,析出的晶体为二苯并噻吩。将静置后的溶液用滤孔直径为0.22微米的滤头过滤;随后将滤液在80℃、1kPa下旋蒸5h得到白色固体实现四丁基溴化磷的再生。按之前的操作,将再生后的四丁基溴化磷与水继续合成水基低共熔溶剂进行萃取脱硫操作,重复进行上述萃取-再生的过程8次,各次萃取条件保持一致,将循环萃取的脱硫实验结果列于表2中。表2循环萃取脱硫实验结果再生周期012345678脱硫率/%70.468.468.667.968.968.368.569.168.1表2中,0代表新鲜水基低共熔溶剂,1~8代表再生次数。根据表2中数据可以看出,再生后循环使用的水基低共熔溶剂仍然具有较高的脱硫率,说明本发明提供的水基低共熔溶剂再生性好,可循环使用。以上实施例表明,本发明提供的水基低共熔溶剂脱硫能力强,对油品无污染,可再生性好;本发明提供的萃取脱硫方法步骤简单,效果好,且萃取剂再生过程无需加入反萃取剂等其他物质,使得整个脱硫系统中油品和萃取剂都不会受到其他污染。以上所述仅是本发明的优选实施方式,应当指出,对于本
技术领域:
的普通技术人员来说,在不脱离本发明原理的前提下,还可以做出若干改进和润饰,这些改进和润饰也应视为本发明的保护范围。当前第1页1 2 3