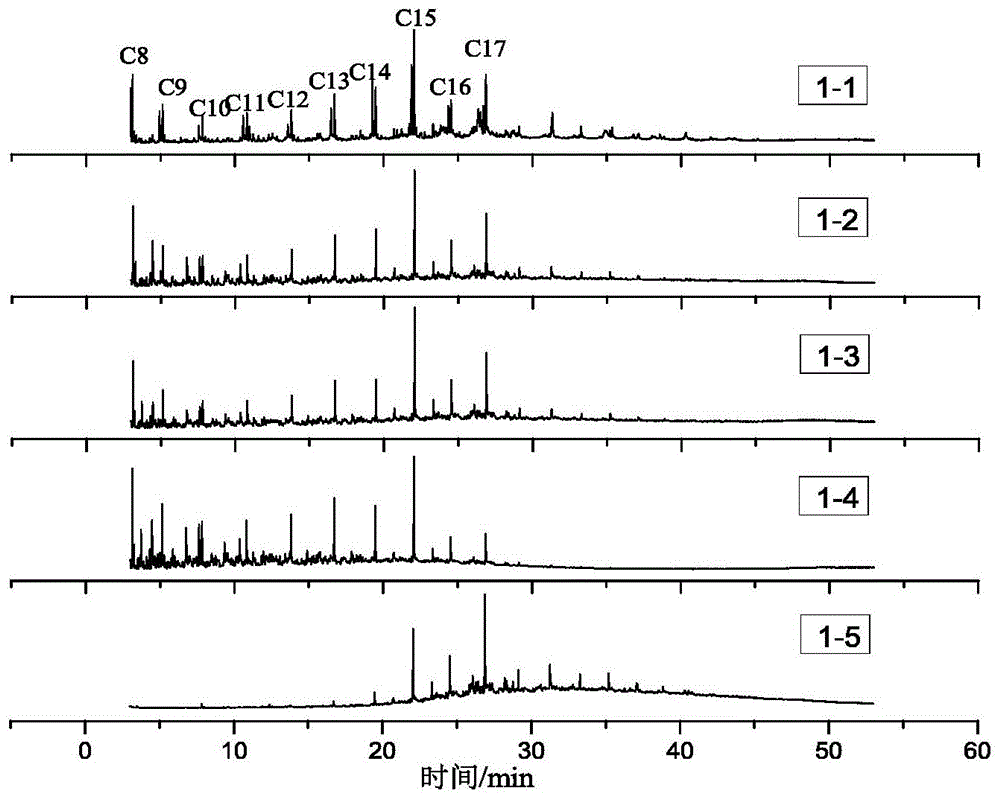
本发明属于生物质能源高值化利用
技术领域:
,具体涉及一种生物油脂热化学转化降低反应活化能制备生物航空燃油和生物柴油的方法。
背景技术:
:目前,在石油资源日益枯竭和碳减排的双重压力下,寻找一种可再生的绿色能源引起了广泛关注。以生物质为原料生产生物燃油是一个非常重要的途径,生物油脂(植物油和动物脂肪)与其他生物质材料相比,其化学结构与石油更为接近。生物油脂转化为生物燃料最常见的方法有酯交换法和加氢,酯交换法可制备车用生物柴油,生物柴油的主要组成是脂肪酸甲酯,与石化燃油组分相差较大,且其低温流动性差,含氧量高,热值低,而加氢制备燃油的缺点在于成本高,反应装置性能要求高,生产操作不安全。生物油脂的催化裂解是生产可再生液体燃料的又一重要途径,在使用不同的催化剂裂解生物油脂时,对热化学转化的反应的活化能是有影响的。低活化能的催化裂解反应相应的裂解温度也低,从而使生物油脂裂解获得燃油的工业化可能性进一步提高。催化裂解得到的组分主要分布在C8-C19的直链烷烃,然而现在的燃油都是链烷烃、环烷烃、烯烃和芳香烃的混合物,单一的成分是不能满足燃油的各种需求,比如:沸点,冰点,闪点,胺点等等。对此,在催化裂解油脂获得裂解油后如何对其进行进一步的分子量和分子结构调控,在获得高收率和高质量的生物航空燃油和生物柴油的同时,使它们也符合燃油的各种需求,成为研究的难点。技术实现要素:发明目的:针对现有技术中存在的不足,本发明提供了一种生物油脂热化学转化降低反应活化能制备生物航空燃油和生物柴油的方法,具有催化裂解温度低的特点,生产的烃类燃油为烷烃、芳香烃和环烷烃的混合物,与石油制取的烃类燃油组分相同,性质相近。技术方案:为了解决上述问题,本发明所采用的技术方案如下:一种生物油脂热化学转化降低反应活化能制备生物航空燃油和生物柴油的方法,对生物油脂通过催化裂解、芳构化、加氢和蒸馏过程,制备得到碳链长度为C8-C15组分的生物航空燃油和碳链长度为C16-C24组分的生物柴油;其中催化裂解制备裂解油的过程中使用的催化剂为氧化锡或氧化铁;裂解催化剂的质量用量为生物油脂的1%-15%,催化裂解温度<410℃。实现对生物油脂热转化组分进行充分利用,得到的生物航空燃油和生物柴油纯度更高,具有更高的利用价值。所述生物油脂热化学转化降低反应活化能制备生物航空燃油和生物柴油的方法,裂解催化剂为氧化锡,用量为生物油脂的15%,催化裂解温度<390℃。所述生物油脂热化学转化降低反应活化能制备生物航空燃油和生物柴油的方法,裂解催化剂为氧化铁,用量为生物油脂的15%,催化裂解温度为350-410℃。所述生物油脂热化学转化降低反应活化能制备生物航空燃油和生物柴油的方法,包括以下步骤:第一步,将所述裂解油和芳构化催化剂加入到高压反应釜中,搅拌加热进行芳构化反应,反应结束后,得到芳构化油;芳构化催化剂的质量用量为裂解油的1%-15%,反应釜温度为300-350℃,反应时间为2-6h;这一过程实现了烯烃芳构化和剩余羧酸脱酸,降低裂解油中的不稳定成分的存在,降低了酸值,提高了芳香烃含量;第二步,将芳构化油和加氢催化剂加入到高压反应釜中,通入2-4MPa氢气,开启搅拌,反应结束后,获得液体燃油;加氢催化剂的质量为芳构化油的1%-20%,反应釜温度为200-220℃,反应时间为2-6h;加氢反应转化芳构化油中的部分芳香烃为环烷烃,得到以烷烃、芳香烃和环烷烃为主要组分的混合物;第三步,对加氢后的液体燃油先进行常压蒸馏得到温度段为90-275℃的馏分,为生物航空燃油;再对剩余液体进行减压蒸馏得到蒸馏温度段为275-340℃的馏分,为生物柴油;本发明指的常压为一个标准大气压,减压蒸馏是在抽真空的环境下进行蒸馏。最后一步再进行分馏过程,从而提高了产物的纯度,大大降低非烃类化合物的含量,即降低了产物中含氧化合物的含量,降低产物酸值。所述生物油脂热化学转化降低反应活化能制备生物航空燃油和生物柴油的方法,生物油脂为大豆油、橡胶籽油、酸化油或地沟油中的任意一种。所述生物油脂热化学转化降低反应活化能制备生物航空燃油和生物柴油的方法,芳构化催化剂为硅铝比为27、38或50的HZSM-5中的任一种,或者芳构化催化剂为所述HZSM-5改性分子筛催化剂中的任一种。所述生物油脂热化学转化降低反应活化能制备生物航空燃油和生物柴油的方法,芳构化催化剂用量为裂解油质量的10%,反应温度为350℃,反应时间4h。所述生物油脂热化学转化降低反应活化能制备生物航空燃油和生物柴油的方法,加氢催化剂为雷尼镍、Pd/C、Pt/C或Rh/C中的任意一种。所述生物油脂热化学转化降低反应活化能制备生物航空燃油和生物柴油的方法,加氢催化剂用量为芳构化油质量的5%,反应温度为220℃,反应时间4h,通入氢气3MPa。有益效果:与现有的技术相比,本发明的优点包括:(1)本发明催化裂解过程中使用氧化锡或氧化铁作为催化裂解过程中的催化剂,能降低裂解反应的活化能,从而降低催化裂解的温度,节约能源。(2)本发明获得的裂解油先通过芳构化过程,实现烯烃芳构化和剩余羧酸脱酸,降低裂解油中的不稳定成分的存在,提高了芳香烃含量;在进行加氢反应转化部分芳香烃为环烷烃,得到以烷烃、芳香烃和环烷烃为主要组分的混合物;最后再通过分馏过程,这一反应过程可以提高产物的纯度,大大降低非烃类化合物的含量,即降低了含氧化合物的含量。(3)本发明生产的烃类燃油为烷烃、芳香烃和环烷烃的混合物,与石油制取的烃类燃油组分相同,性质相近,具有很好的应用前景。附图说明图1为实施例1热化学转化过程中组分变化图,其中1-1为裂解油GC-MS测试结果曲线,1-2为芳构化油GC-MS测试结果曲线,1-3为加氢油GC-MS测试结果曲线,3-4为生物航空燃油GC-MS测试结果曲线,3-5为生物柴油GC-MS测试结果曲线;图2为实施例1和实施例3的氧化锡催化裂解产生的裂解油碳链长度分布图,其中,2-1为酸化油裂解油GC-MS测试结果曲线,2-2为大豆油裂解油GC-MS测试结果曲线。具体实施方式为使本发明的上述目的、特征和优点能够更加明显易懂,下面结合具体实施例对本发明的具体实施方式做详细的说明。本发明每个温度段的馏分产率均指馏分质量与原料的百分比,总计为各温度段馏分产率之和。实施例1将800g大豆油和120g氧化锡加入裂解反应釜,开启搅拌,精馏柱温度升温至300℃,当反应釜升温至330℃,出现冷凝液体,逐渐升温至450℃,保持至无裂解液体流出;其中,分六个温度段收集裂解液体,分别为裂解温度<350℃,350-370℃,370-390℃,390-410℃,410-430℃和430-450℃六个温度段,六个温度段裂解油产率结果如表1所示。对馏分进行GC-MS分析,结果如图2中曲线2-1所示。检测大豆油催化裂解得到的裂解油组分有C8-C24的烃类物质,由图2中的2-1可知,大豆油催化裂解得到的裂解油主要组分为C8-C17的烃类物质,其他组分相对含量较低,在图中没有标出。由表1可知,以氧化锡为裂解催化剂,裂解温度在<390℃时,裂解油产率达到将近50%,占全部裂解油产率的75%左右,所以以氧化锡为裂解催化剂时大豆油的裂解温度为<390℃。实施例2生物油脂催化裂解的方法同实施例1,催化裂解过程中使用的催化剂为氧化铁。收集裂解温度<350℃,350-370℃,370-390℃,390-410℃,410-430℃和430-450℃六个温度段的馏分,结果如表1所示。由表1可知,裂解温度<350℃时,几乎没有裂解油产生;在350-410℃温度范围内,裂解油的产率超过55%,占全部裂解产物的85%左右,所以以氧化铁为裂解催化剂时,大豆油的裂解温度为350-410℃。实施例3生物油脂催化裂解的方法同实施例1,催化裂解过程中使用的催化剂为氧化钙。收集裂解温度<350℃,350-370℃,370-390℃,390-410℃,410-430℃和430-450℃六个温度段的馏分,结果如表1所示。由表1可知,以氧化钙为裂解催化剂时,在裂解温度<370℃时,大豆油裂解油得率很低,在370-430℃温度段时,大豆油的裂解油产率超过45%,占全部裂解油的70%左右,所以当以氧化钙为裂解催化剂时,大豆油的催化裂解温度为370-430℃。实施例4生物油脂催化裂解的方法同实施例1,催化裂解过程中使用的催化剂为碳酸锂。收集裂解温度<350℃,350-370℃,370-390℃,390-410℃,410-430℃和430-450℃六个温度段的馏分,结果如表1所示。由表2可知,以碳酸锂为裂解催化剂时,当裂解温度<390℃时,大豆油的裂解产率非常低,在390-430℃温度段时,大豆油的裂解油的得率超过50%,占全部裂解油产率的75%左右,所以当以碳酸锂为裂解催化剂时,大豆油的裂解温度为390-430℃。实施例5生物油脂催化裂解的方法同实施例1,催化裂解过程中使用的催化剂为碳酸钾。收集裂解温度<350℃,350-370℃,370-390℃,390-410℃,410-430℃和430-450℃六个温度段的馏分,结果如表1所示。由表1可知,以碳酸钾为裂解催化剂时,裂解温度在<390℃时,大豆油的裂解产率非常低,在390-430℃温度段时,大豆油的裂解油的得率将近50%,占全部裂解产率的75%左右,所以当以碳酸钾为裂解催化剂时,大豆油的裂解温度为390-430℃。综合实施例1-5可知,,以氧化锡、氧化铁、氧化钙、碳酸锂和碳酸钾作为催化裂解催化剂时,大豆油的裂解温度分别为<390℃、350-410℃、370-430℃、390-430℃和390-430℃,说明氧化锡在催化裂解过程中效果最好,可以在较低的温度下得到较高的馏分产率,从而降低了大豆油的催化裂解温度。表1实施例1-5催化裂解大豆油过程中不同温度段馏分产率结果实施例6将800g酸化油和120g的氧化锡加入裂解反应釜中,开启搅拌,精馏柱温度升温至300℃,当反应釜升温至350℃,出现冷凝液体,逐渐升温至450℃,其中分六个温度段收集裂解液体,裂解温度分别为<350℃,350-370℃,370-390℃,390-410℃,410-430℃和430-450℃六个温度段,每个温度段的馏分产率如表2所示。由表2可知,以氧化锡为裂解催化剂时,酸化油的裂解油主要产生于<390℃,裂解油产率将近50%,超过全部裂解油产率的75%,所以以氧化锡为裂解催化剂时,酸化油的裂解温度为<390℃。对酸化油的裂解油进行GC-MS分析,结果如图2-2所示。由图2可知,氧化锡可以催化裂解酸化油和催化裂解大豆油,说明氧化锡对生物油脂均有很好的催化裂解效果,裂解温度均低于390℃。实施例7生物油脂催化裂解的方法同实施例6,催化裂解过程中使用的催化剂为碳酸钠加入裂解反应釜中,开启搅拌,精馏柱温度升温至300℃,当反应釜升温至350℃,出现冷凝液体,逐渐升温至450℃,其中分六个温度段收集裂解液体,裂解温度分别为<350℃,350-370℃,370-390℃,390-410℃,410-430℃和430-450℃六个温度段,每个温度段的馏分产率如表2所示。由表2可知,以碳酸钠为裂解催化剂时,裂解温度在<390℃时,酸化油的裂解产率非常低,在390-450℃温度段时,酸化油的裂解产物的得率超过60%,超过全部裂解产率的80%左右,所以当以碳酸钠为裂解催化剂时,大豆油的裂解温度为390-450℃。实施例8生物油脂催化裂解的方法同实施例6,催化裂解过程中使用的催化剂为氧化钙加入裂解反应釜中,开启搅拌,精馏柱温度升温至300℃,当反应釜升温至350℃,出现冷凝液体,逐渐升温至450℃,其中分六个温度段收集裂解液体,裂解温度分别为<350℃,350-370℃,370-390℃,390-410℃,410-430℃和430-450℃六个温度段,每个温度段的馏分产率如表2所示。由表2可知,以氧化钙为裂解催化剂时,裂解温度在<370℃时,酸化油的裂解产率非常低,在370-430℃温度段时,酸化油的裂解产物的得率超过50%,超过全部裂解产率的70%左右,所以当以氧化钙为裂解催化剂时,酸化油的裂解温度为370-430℃。综合实施例6-8可知,,以氧化锡、氧化钙和碳酸钠作为催化裂解催化剂时,酸化油的裂解温度分别为<390℃、370-430℃和390-450℃,说明氧化锡在催化裂解过程中效果最好,可以在较低的温度下得到较高的馏分产率,从而降低了酸化油催化裂解温度。表2实施例6-8催化裂解酸化油过程中不同温度段馏分产率结果实施例9大豆油热化学转化降低反应活化能制备生物航空燃油和生物柴油的方法,包括以下步骤:第一步:催化裂解制备裂解油的方法同实施例1;第二步,芳构化:取30g第一步中的裂解油和1.5gHZSM-5(Si/A1=27)催化剂于50mL的高压反应釜中,开启搅拌,反应釜升温至350℃,反应4h,离心除去催化剂,得到芳构化油;第三步,加氢:取20g第二步中的芳构化油及1.0g雷尼镍催化剂于高压反应釜中,通入氢气3MPa,开启搅拌,反应釜升温至220℃,反应4h,即可得到含有烷烃、芳香烃和环烷烃为主的液体燃油;第四步,分馏:对液体燃油进行常压蒸馏,收集90-275℃的馏分,该温度段的馏分为以碳链长度为C8-C15的烷烃、烯烃和芳香烃为主要成分的生物航空燃油;然后进行减压蒸馏,减压蒸馏是在抽真空的环境下进行蒸馏,获得温度在275-340℃的馏分,获得的是以碳链长度为C16-C24的烷烃和烯烃为主的生物柴油。生物航空燃油和生物柴油的气相色谱-质谱联用仪(GC-MS)分析图谱如图1所示。由图1可知,以氧化锡为裂解催化剂时,首先将大豆油催化裂解为C8-C24的化合物,然后经过芳构化、加氢和分馏操作,得到C8-C15的烷烃、烯烃和芳香烃为主要成分的生物航空燃油和C16-C24的烷烃和烯烃为主的生物柴油,最终得到的产率纯度较高。将最终得到的生物航空燃油和生物柴油与国标中航空燃油和柴油性质比较,结果如表3所示。由表3可知,生物航空燃油和生物柴油的密度、热值、黏度、酸值和冰点等性能,符合RP-3航油和0#柴油的性能指标。反应过程中得到的组分及其含量结果如表4所示。表4中的其他主要是指醛、酮、酸、酯、等含氧类化合物,由表4可知,加氢之后经过分馏得到的生物航空燃油和生物柴油中的含氧化合物有了明显的降低。并且生物航空燃油和生物柴油的产率和纯度非常高。表3实施例9中燃料油性质与国标中航空燃油和柴油性质比较性质生物航油RP-3航油生物柴油0#柴油密度/kg·m-3812775-830854820-860热值/MJ·kg-143.7>42.844.143.5黏度/mm2·s-12.08>1.255.13.0-8.0酸值/mgKOH·g-1-<0.0156.70表4实施例9中反应过程中组分变化当前第1页1 2 3