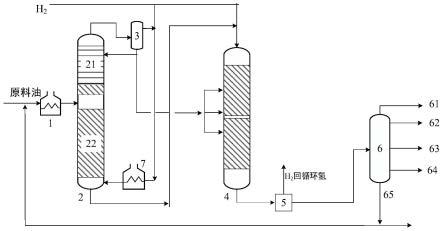
一种用于生产柴油和高密度喷气燃料以及副产btx的系统和方法
技术领域
1.本发明涉及一种用于生产柴油和高密度喷气燃料以及副产btx的系统和方法。
背景技术:2.催化裂化装置的轻循环油(light cycle oil,简称lco),即催化裂化柴油,是催化裂化单元产物之一。催化裂化工艺主要是对进料中的链烷烃和环烷烃进行裂解,对芳烃基本不具备开环裂化的能力,因此在催化裂化柴油中通常富集了大量稠环芳烃。面对新燃油质量标准(国vi)的规定,尽管传统的加氢精制或加氢改质技术能够脱除lco中的硫和氮,但是加氢过程氢耗高,柴油产品中芳烃含量高、十六烷值低,达不到车用柴油标准,难以直接掺入成品柴油中。并且lco中富含的芳香烃成分也不能得到有效利用。中国芳烃资源比较少,需要充分利用有限的芳烃资源,催化柴油中芳烃质量分数高达70-90%,从芳烃构成上来看主要为单环、双环及三环芳烃,其中的双环及以上芳烃在加氢处理的条件下易饱和为单环芳烃。因此将lco中易于转化的芳烃转化为btx(苯、甲苯和二甲苯,简称btx)以提升lco的价值。在lco中单环芳烃中茚满和四氢萘类占比较高,多环芳烃中大多为萘类和苊类。以石炼lco为例,单环芳烃主要集中在较轻的柴油馏分段(<260℃),双环芳烃主要出现在》260℃以上的馏分段,而三环芳烃则集中在较重的柴油馏分段(>310℃)。石炼lco的碳数分布主要集中在c9-c21,质量分数超过10%的碳数分布于c12-c16;质量分数最高的化合物种类是萘类(约27%)、茚满和萘满类(约11%)。
3.在加氢裂化反应中双环及以上的芳烃能很快被部分加氢饱和成双环烷基苯类,再进一步,环烷烃发生开环,而带侧链的单环芳香烃很容易发生侧链断裂反应。但是而这些多环芳烃类物质大多均含有烷基侧链,根据热力学计算,加氢优先发生在无烷基取代的芳环上,这就导致在后续的裂化过程中会产生价值不高的均三甲苯,而该物质可进一步加氢裂化,形成航煤或柴油组分。
4.高密度喷气燃料又称大比重航煤,是一类具有高密度(一般为0.835g/cm3以上)、高体积热值(一般为35.8mj/m3以上)的喷气燃料。与普通的喷气燃料(密度一般为0.77-0.81g/cm3)相比,高密度喷气燃料可以提高燃料单位体积的热值,在燃料箱容积一定时,可以有效增加燃料箱携带燃料的能量,是航天飞行器高航速、远航程飞行的重要保障。例如:密度为845kg/m3(体积发热量约为36
×
103mj/m3)的燃料与密度为780kg/m3(体积发热量约为33
×
103mj/m3)的燃料相比,在同样载油体积条件下可使飞行器多载约9%的能量。因此,开发高密度喷气燃料成为研究热点之一。
5.lco由于芳烃含量高,直接制取柴油时存在氢耗高、操作苛刻度高等问题,并且装置建设投资大;最大量生产柴油的加氢改质技术在加氢精制的基础上增加了选择性开环,在保证柴油收率的前提下,十六烷值增幅可达8~25个单位,但同样存在氢耗高、装置投资大的问题。
6.cn108070403公开了一种从直馏柴油,通过加氢精制和加氢裂化来制备喷气燃料
的方法。该方法只是利用直馏柴油,也使用了加氢精制精馏塔和加氢裂化,其目的是,将直馏柴油中的大分子物质,通过不断的循环、裂化,最终全部转化为喷气燃料。并未产出其他产品,尤其是高附加值的btx产品。
7.cn106047404b中只是利用催化裂化柴油,经过加氢处理后,形成了高辛烷值的汽油,该专利在轻质化反应中采用贵金属催化剂,成本较高,且产物单一,没有实现对催化裂化柴油的芳香环物质的充分利用。cn110938469a以蜡油为原料,进行加氢裂化处理,最终得到高芳潜的重石脑油,以及航煤和柴油组分,但是无法得到高附加值的btx产物。
技术实现要素:8.本发明的目的是提供一种用于生产柴油和高密度喷气燃料以及副产btx的系统和方法,本发明的方法能够最大程度地保留btx组分,同时生产柴油和高密度喷气燃料。
9.为了实现上述目的,本发明第一方面提供一种生产柴油和高密度喷气燃料以及副产btx的方法,该方法包括:
10.s1、使原料油进入反应精馏塔,与从塔底进入的氢气在所述反应精馏塔下段与加氢精制催化剂接触,进行加氢精制反应,从所述反应精馏塔的塔底得到加氢精制重组分;
11.s2、使所述反应精馏塔内的轻组分随氢气进入所述反应精馏塔上段的精馏区进行精馏处理,得到塔顶气体,将所述塔顶气体进行冷凝得到含氢气体和液相产物;
12.s3、将至少部分的所述液相产物由侧线引入加氢裂化塔,将所述加氢精制重组分由顶部引入所述加氢裂化塔,与氢气、加氢裂化催化剂接触进行加氢裂化反应。
13.本发明第二方面提供一种用于生产柴油和高密度喷气燃料以及副产btx的系统,该系统包括:反应精馏塔、冷凝器和加氢裂化塔;
14.所述反应精馏塔包括进料口、塔底气体入口、塔顶气体出口、塔底液体出口、回流液入口、精馏区和加氢精制区,所述精馏区位于所述进料口的上方,所述加氢精制区位于所述进料口的下方;所述加氢裂化塔包括塔顶入口、侧线入口和塔底出口;所述冷凝器包括气体入口、气体出口和液体出口;
15.所述反应精馏塔的所述塔顶气体出口与所述冷凝器的气体入口流体连通,所述冷凝器的液体出口分别与所述反应精馏塔的回流液入口和所述加氢裂化塔的所述侧线入口流体连通,所述反应精馏塔的塔底液体出口与所述加氢裂化塔的所述塔顶入口流体连通。
16.与现有技术相比较,本发明的方法具有如下优点:
17.(1)本发明的方法中为了避免原料油中的轻组分过度加氢饱和,将原料油在一个塔中完成轻组分的精馏分离和重组分的加氢精制;
18.(2)本发明的方法中将加氢裂化反应分为两段,轻组分经过精馏后从加氢裂化塔的侧线进入,避免其过度裂化,使产物中最大程度的保留btx组分;加氢精制重馏分则从顶部引入加氢裂化塔中,经过加氢裂化反应后即可得高密度喷气燃料以及低硫柴油调和组分。
19.本发明的其他特征和优点将在随后的具体实施方式部分予以详细说明。
附图说明
20.附图是用来提供对本发明的进一步理解,并且构成说明书的一部分,与下面的具
体实施方式一起用于解释本发明,但并不构成对本发明的限制。在附图中:
21.图1是本发明用于生产柴油和高密度喷气燃料以及副产btx的系统的一种具体实施方式的结构示意图。
22.附图标记说明
23.1第一加热炉
ꢀꢀꢀꢀꢀꢀꢀꢀꢀꢀꢀꢀ
2反应精馏塔
ꢀꢀꢀꢀꢀꢀꢀꢀꢀꢀꢀꢀ
3冷凝器
24.4加氢裂化塔
ꢀꢀꢀꢀꢀꢀꢀꢀꢀꢀꢀꢀ
5降压气液分离装置
ꢀꢀꢀꢀꢀꢀ
6分馏装置
25.7第二加热炉
ꢀꢀꢀꢀꢀꢀꢀꢀꢀꢀꢀꢀ
21精馏区
ꢀꢀꢀꢀꢀꢀꢀꢀꢀꢀꢀꢀꢀꢀꢀ
22加氢精制区
26.61烃出口
ꢀꢀꢀꢀꢀꢀꢀꢀꢀꢀꢀꢀꢀꢀꢀ
62粗石脑油出口
ꢀꢀꢀꢀꢀꢀꢀꢀꢀ
63btx粗产品出口
27.64高密度喷气燃料出口
ꢀꢀꢀ
65柴油调和组分出口
具体实施方式
28.以下结合附图对本发明的具体实施方式进行详细说明。应当理解的是,此处所描述的具体实施方式仅用于说明和解释本发明,并不用于限制本发明。
29.在本发明中,在未作相反说明的情况下,使用的方位词如“上、下”通常是指本公开的系统可以正常使用时的“上、下”,“内、外”是指相对于图面中装置轮廓的“内、外”。
30.本发明第一方面提供一种生产柴油和高密度喷气燃料以及副产btx的方法,该方法包括:
31.s1、使原料油进入反应精馏塔,与从塔底进入的氢气在反应精馏塔下段与加氢精制催化剂接触,进行加氢精制反应,从反应精馏塔的塔底得到加氢精制重组分;
32.s2、使反应精馏塔内的轻组分随氢气进入反应精馏塔上段的精馏区进行精馏处理,得到塔顶气体,将塔顶气体进行冷凝得到含氢气体和液相产物;
33.s3、将至少部分的液相产物由侧线引入加氢裂化塔,将加氢精制重组分由顶部引入加氢裂化塔,与氢气、加氢裂化催化剂接触进行加氢裂化反应。
34.根据本发明,轻组分包括加氢精制反应产生的轻组分及原料油中的轻组分,轻组分中含有碳原子数为6-8的芳烃、碳原子数为3-8的环烷烃和碳原子数为1-8的链烷烃中的一种或几种。加氢精制重组分中含有9以上的芳烃、碳原子数为9以上的环烷烃和碳原子数为9以上链烷烃中的一种或几种。
35.本发明的方法巧妙地使轻组分和重组分在反应精馏塔中分离,再将重组分和含有轻组分的液相产物分别进行加氢裂化反应,有效地避免了单环芳烃的加氢饱和,最大程度地保留了btx组分,同时有利于生产低硫柴油和高密度喷气燃料。
36.根据本发明的一种具体实施方式,反应精馏塔包括设置于精馏塔上段的精馏区和设置于精馏塔下段的加氢精制区,其中,精馏区为本领域的技术人员所常规采用的,精馏区内可以设置有塔板或填料,本发明对塔板的个数或填料的种类不做具体限制,可以根据需要选择;加氢精制区也为本领域的技术人员所常规采用的,加氢精制区内设置有加氢精制催化剂。
37.在一种优选地具体实施方式中,在反应精馏塔内氢气由反应精馏塔的塔底引入,在加氢裂化塔内氢气由加氢裂化塔的塔顶引入。
38.在本发明的一种具体实施方式中,步骤s1中,加氢精制反应的条件包括:体积空速在0.5-10h-1
,压力为3-10mpa,氢油体积比为50-200,反应精馏塔的塔顶温度为230-350℃,
塔底温度为280-400℃。其中,氢油体积比是指循环氢与原料油的体积比。
39.在一种优选的具体实施方式中,步骤s1中,使原料油从反应精馏塔的中部引入。
40.在本发明的一种具体实施方式中,步骤s2中,精馏处理的的塔顶回流比为1.5-4,优选地,塔顶回流比为1.8-3。
41.在本发明的一种具体实施方式中,步骤s3中,加氢裂化反应的条件包括:压力为2-12mpa,体积空速为0.5-10h-1
,氢油体积比为50-4000,优选为500-1500,加氢裂化塔的塔顶温度为300-450℃。在一种优选地具体实施方式中,步骤s3中的侧线可以为多条,例如可以为1条、2条或3条,侧线进料的温度为310-460℃,以根据原料油的性质和液相产物的性质调节将液相产物引入加氢裂化塔的位置,有利于提高本发明方法的灵活性,减少操作成本,最大程度的获得btx产物并生产柴油和高密度喷气燃料。
42.在本发明的一种具体实施方式中,步骤s3中,将至少部分的液相产物由侧线引入加氢裂化塔,与氢气、第一加氢裂化催化剂接触进行第一加氢裂化反应,将加氢精制重组分由顶部引入加氢裂化塔,与氢气、第二加氢裂化催化剂、第一加氢裂化催化剂接触进行加第二氢裂化反应。其中,加氢裂化催化剂含有第二活性金属和第二载体,第二活性金属选自co、mo、ni和w中的一种或几种,第二载体含有分子筛以及可选的氧化铝和/或氧化硅。分子筛为本领域的技术人员所熟知的,例如可以为y型分子筛、β型分子筛等。本发明中第一加氢裂化催化剂和第二加氢裂化催化剂可以相同或者不同,且各自独立地选自ric-3和/或rhc-100。优选地,第一加氢裂化反应的体积空速为0.5-1.5h-1
,第二加氢裂化反应的体积空速为0.5-1.5h-1
。
43.根据本发明,原料油的密度可以为850-1000kg/m3,总芳烃的含量可以为60-95重量%,95重量%馏出温度可以为380℃以上,对原料油的其他性质不做具体限制。优选地,原料油为催化裂化柴油。在一种更优选的具体实施方式中,将原料油预热后再引入反应精馏塔,例如原料油的进料温度可以为280-400℃。
44.在本发明的一种具体实施方式中,该方法还包括步骤s4:将加氢裂化塔的塔底流出物进行分馏,得到碳原子数为1-4的烃、粗石脑油、btx粗产品、高密度喷气燃料以及柴油调和组分;将至少部分的柴油调和组分与原料油混合后返回反应精馏塔,优选地,以柴油调和组分和原料油的总重量为基准,将1-50重量%的柴油调和组分与原料油混合后返回反应精馏塔。其中,高密度喷气燃料的初馏点为170-190℃,终馏点为270-290℃;柴油调和组分的初馏点为260-290℃,终馏点为340-360℃;btx粗产品的馏程为70-170℃,,初馏点为65-75℃,终馏点为150-180℃。在一种实施方式中,将btx粗产品进行萃取以提高其纯度;在另一种实施方式中,将btx粗产品与来自重整装置的btx混合物混合后,再进行精馏分离。
45.根据本发明,加氢精制催化剂为本领域的技术人员所常规采用的,可以为市售商品或采用本领域的常规方法进行制备,例如可以为柴油加氢精制催化剂。在本发明的一种具体实施方式中,加氢精制催化剂含有第一活性金属和第一载体,第一活性金属选自co、mo、ni和w中的一种或几种,第一载体选自氧化铝、氧化硅和氧化钛的一种或多种;更优选地,加氢精制催化剂选自rs-2100、rs-2200、rs-3100和rs-2000中的一种或几种。在本发明的方法中,加氢裂化塔中沿塔高方向上的设置的加氢精制催化剂可以相同也可以不同,本发明在此不做限制。
46.如图1所示,本发明第二方面提供一种用于生产柴油和高密度喷气燃料以及副产
btx的系统,该系统包括:反应精馏塔2、冷凝器3和加氢裂化塔4;
47.反应精馏塔2包括进料口、塔底气体入口、塔顶气体出口、塔底液体出口、回流液入口、精馏区21和加氢精制区22,精馏区21位于进料口的上方,加氢精制区22位于进料口的下方;加氢裂化塔包括塔顶入口、侧线入口和塔底出口;冷凝器包括气体入口、气体出口和液体出口;
48.反应精馏塔2的塔顶气体出口与冷凝器3的气体入口流体连通,冷凝器3的液体出口分别与反应精馏塔2的回流液入口和加氢裂化塔4的侧线入口流体连通,反应精馏塔2的塔底液体出口与加氢裂化塔4的塔顶入口流体连通。
49.本发明的系统中反应精馏塔包括精馏区和加氢精制区,巧妙地实现了在一个塔中对原料油中轻重组分的分离后再有针对性地进行加氢精制处理和精馏处理,且加氢裂化塔设置有侧线入口,使得来自反应精馏塔的轻组分可以由侧线引入加氢裂化塔,本发明系统中上述结构的反应精馏塔和加氢裂化塔相结合能够最大程度地保留btx组分,并生产柴油和高密度喷气燃料。
50.根据本发明,冷凝器的温度可以在较大的范围内变化,在一种具体实施方式中,冷凝器3的温度为50℃以下,优选为30-40℃。
51.为了调控反应精馏塔和加氢裂化塔间的压力关系,在一种具体实施方式中,本发明的系统还包括压力调节装置,压力调节装置的入口与反应精馏塔的塔底液体出口连通,压力调节装置的出口与加氢裂化塔的塔顶入口连通。对压力调节装置的具体形式不做限制,可以根据反应精馏塔和加氢裂化塔间的压力关系来选择,若反应精馏塔的压力高于加氢裂化塔的压力,则压力调节装置为降压形式的压力调节装置,并相应设置气体循环系统;若反应精馏塔的压力低于加氢裂化塔的压力,则压力调节装置为增压形式的压力调节装置,并相应设置防止反串回流系统。压力调节装置为本领域的技术人员所熟知的,在此不再赘述。
52.在本发明的一种具体实施方式中,加氢裂化塔4包括加氢裂化反应区,加氢裂化塔4的侧线入口与加氢裂化反应区底部间的距离占加氢裂化反应区高度的比例为0.1-0.6,优选为0.3-0.5;加氢裂化塔4内设置有加氢裂化催化剂。
53.根据本发明,该系统还可以包括分馏装置6,分馏装置6包括物料入口和产物出口,分馏装置6的物料入口与加氢裂化塔4的塔底出口流体连通。分馏装置可以包括一个或多个串联的分馏塔,本发明对分馏塔的具体个数不做限制,例如可以为2个、3个、4个或5个,每个分馏塔各自独立地具有回流系统。在一种优选的具体实施方式中,产物出口包括烃出口61、粗石脑油出口62、btx粗产品出口63、高密度喷气燃料出口64和柴油调和组分出口65,柴油调和组分出口65与反应精馏塔2的进料口流体连通。
54.根据发明,如图1所示,该系统还可以包括降压气液分离装置5,降压气液分离装置5包括串联设置的高压分离器和低压分离器;高压分离器的入口与加氢裂化塔4的塔底出口流体连通,低压分离器的出口与分馏装置6的物料入口流体连通。
55.在一种优选的具体实施方式中,该系统还包括第一加热炉1和第二加热炉7,第一加热炉1用于给引入反应精馏塔中的原料油加热,第二加热炉7用于给引入反应精馏塔中的氢气加热。
56.在一种具体实施方式中,冷凝器3的气体出口与反应精馏塔2的塔底气体入口流体
连通,以实现对氢气的回收利用。
57.根据本发明,对反应精馏塔的精馏区的具体形式不做限制,例如可以为填料式或者塔板式。在一种具体实施方式中,反应精馏塔1的精馏区21为填料式,填料为本领域的技术人员所常规采用的,例如可以选自丝网波纹型填料、拉西环、螺旋环、陶瓷波纹填料、金属波纹填料、木栅填料、金属丝网填料、瓷环、钢质填圈、鞍形填料、焦块、石英和玻璃弹簧中的一种或几种;在另一种具体实施方式中,反应精馏塔1的精馏区21为塔板式,塔板的个数可以在较大的范围内变化,例如可以为3-40个,优选为3-20个,更优选为5-10个。根据本发明,反应精馏塔1的精馏区21的底部可以设置加氢精制催化剂也可以不设置加氢精制催化剂,优选地,当原料油的初馏点到50%馏分点的馏分中,若氮含量小于50mg/kg,则不设置加氢精制催化剂;若氮含量为50mg/kg以上,则设置加氢精制催化剂。在一种优选的具体实施方式中,设置在精馏区21底部的加氢精制催化剂为具有较强的脱氮性能的加氢精制催化剂,体积空速可以为0.5-10h-1
。
58.下面通过实施例来进一步说明本发明,但是本发明并不因此而受到任何限制。
59.以下实施例及对比例中所用到的原料油为催化裂化装置的轻循环油(催化裂化柴油),其性质见下表1。
60.表1
[0061][0062][0063]
实施例1
[0064]
如图1所示,本实施例用于生产柴油和高密度喷气燃料以及副产btx的系统包括反应精馏塔2、冷凝器3、加氢裂化塔4、分馏装置6、第一加热炉1、第二加热炉7和降压气液分离装置5;
[0065]
反应精馏塔2包括进料口、塔底气体入口、塔顶气体出口、塔底液体出口、回流液入口、精馏区21和加氢精制区22,精馏区21位于进料口的上方,加氢精制区22位于进料口的下方,加氢精制反应区22内设置有第一加氢精制催化剂,精馏区21的底部设置有第二加氢精制催化剂;加氢裂化塔4包括塔顶入口、侧线入口和塔底出口,加氢裂化塔4的侧线入口与加氢裂化反应区底部间的距离占加氢裂化反应区高度的比例为0.5;冷凝器包括气体入口、气体出口和液体出口;分馏装置6包括物料入口、烃出口61、粗石脑油出口62、btx粗产品出口63、高密度喷气燃料出口64和柴油调和组分出口65;降压气液分离装置5包括串联设置的高压分离器和低压分离器;
[0066]
其中,第一加热炉1的出口与反应精馏塔2的进料口连通,反应精馏塔2的塔顶气体出口与冷凝器3的气体入口流体连通,冷凝器3的液体出口分别与反应精馏塔2的回流液入口和加氢裂化塔4的侧线入口流体连通,冷凝器3的气体出口与第二加热炉7入口连通,第二加热炉的出口与反应精馏塔2的塔底气体入口流体连通,反应精馏塔2的塔底液体出口与加氢裂化塔4的塔顶入口流体连通,加氢裂化塔4的塔底出口与高压分离器的入口连通,低压分离器的出口与分馏装置6的物料入口流体连通,柴油调和组分出口65分别与第一加热炉1的入口和系统的产物出口连通。
[0067]
实施例2-5
[0068]
采用实施例1的系统来生产柴油、高密度喷气燃料以及副产btx,其中,以柴油调和组分和原料油的总重量为基准,将7重量%的柴油调和组分与原料油混合后返回反应精馏塔,各步骤的条件参数如表2中所示,产物的性质参数如表3所示。
[0069]
表2
[0070][0071]
表3
[0072][0073]
实施例6
[0074]
采用实施例1的系统、按照与实施例2相同的方法来生产柴油、高密度喷气燃料以及副产btx,不同之处仅在于,加氢精制反应的体积空速为0.4h-1
,反应压力为2.5mpa,氢油体积比为4100,反应精馏塔的塔顶温度为360℃,塔底温度为410℃。产物的性质参数如表4所示。
[0075]
实施例7
[0076]
采用与实施例1相同的系统,不同之处仅在于,本实施例的系统中加氢裂化塔4的侧线入口与加氢裂化反应区底部间的距离占加氢裂化反应区高度的比例为0.7。按照与实施例2相同的方法来生产柴油、高密度喷气燃料以及副产btx。产物的性质参数如表4所示。
[0077]
表4
[0078][0079]
对比例1
[0080]
采用常规的加氢精制塔和加氢裂化塔串联的工艺流程来处理原料油,加氢精制塔和加氢裂化塔均采用上进下出的进料方式,原料油与氢气混合后,经过加热,一起先从加氢精制塔的顶部进入,由加氢精制塔的塔底流出的物流再由加氢裂化塔的顶部引入,从加氢裂化塔底出来的物流经过分馏后,得到不同的产品。相关的工艺条件见表5,产品性质见表6。
[0081]
表5
[0082][0083]
表6
[0084][0085]
[0086]
由实施例和对比例的结果可知,本发明的方法能够在生产低硫柴油和高密度喷气燃料的同时,最大程度地保留btx组分以副产btx,可以实现原料油,尤其是催化裂化装置的轻循环油(lco)的高效利用。
[0087]
以上结合附图详细描述了本发明的优选实施方式,但是,本发明并不限于上述实施方式中的具体细节,在本发明的技术构思范围内,可以对本发明的技术方案进行多种简单变型,这些简单变型均属于本发明的保护范围。
[0088]
另外需要说明的是,在上述具体实施方式中所描述的各个具体技术特征,在不矛盾的情况下,可以通过任何合适的方式进行组合,为了避免不必要的重复,本发明对各种可能的组合方式不再另行说明。
[0089]
此外,本发明的各种不同的实施方式之间也可以进行任意组合,只要其不违背本发明的思想,其同样应当视为本发明所公开的内容。