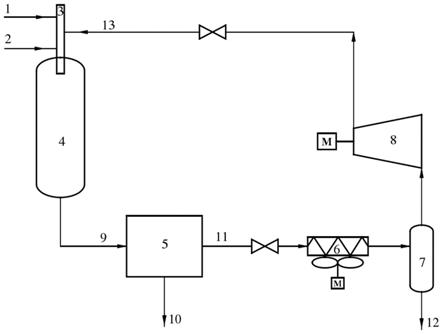
1.本发明属于能源化工技术领域,具体涉及一种可变负荷运行的煤气化装置及运行方法。
背景技术:2.气流床气化是煤炭气化的一种重要形式。以水煤浆气化为例,水煤浆与氧气通过工艺烧嘴送入气化炉,氧气高速喷出与水煤浆混合并将水煤浆雾化,在气化炉内进行非催化部分氧化反应,最终生成以co、h2为主要组分的粗合成气。考虑到工艺烧嘴的雾化性能并避免回火,气化炉不宜长时间在低负荷下运行,一般应在80%以上,当需要以更低负荷运行时,必须重新设计并停炉更换烧嘴。因此,气化装置可调节性能及连续操作性能较差。
3.申请号为zl201810148656.6的中国专利公开了一种可调式气化烧嘴,该气化烧嘴通过位移调节装置驱动煤浆通道沿轴向上下移动,由此改变煤浆通道和环氧通道的间隙来调整烧嘴负荷。但由于烧嘴各喷口尺寸不发生改变,低负荷时,在水煤浆及氧气流量均大幅减少的情况下,仅改变环氧间隙,调节作用有限,并不能很好的匹配工况。
技术实现要素:4.本发明解决的技术问题是:克服现有技术的不足,提供了一种可变负荷运行的煤气化装置,通过将净化后的合成气加压后循环供入工艺烧嘴来抵消低负荷运行时气化燃料和氧化剂减少量对工艺烧嘴运行的影响,从而实现气化装置在低负荷下的高效稳定运行。
5.本发明的技术解决方案是:一种可变负荷运行的煤气化装置,包括气化炉、工艺烧嘴、净化单元、冷却器、分液罐和压气机,工艺烧嘴安装在气化炉上,将气化燃料和氧化剂送入气化炉发生欠氧燃烧反应,生成粗合成气并送入净化单元去除灰尘杂质,净化单元出口合成气分为两部分,一部分送往下游再利用,另一部分作为循环合成气进入冷却器降温,再经分液罐分离冷凝液后进入压气机增压,增压后形成高压合成气送入工艺烧嘴并重新进入气化炉;当气化炉由正常负荷降低负荷运行时,减少进入工艺烧嘴的气化燃料和氧化剂流量,并增加进入工艺烧嘴的循环合成气流量;当气化炉由低负荷提升负荷运行时,恢复进入工艺烧嘴的气化燃料和氧化剂流量,并减少进入工艺烧嘴的循环合成气流量。
6.可选的,所述的冷却器可以采用空气冷却方式,或者采用换热器将热量传递给氧化剂。
7.可选的,所述的净化单元通过洗涤或者过滤方法去除灰尘杂质,包括应用于激冷流程的文丘里洗涤器+水洗塔方式,或应用于废锅流程的金属陶瓷滤芯过滤方式。
8.可选的,所述的工艺烧嘴包括同轴套置的n个通道,n≥3。
9.可选的,所述的n=3时,工艺烧嘴由内向外分别为:高压合成气通道、气化燃料通道及氧化剂通道。
10.可选的,所述的n=4时,工艺烧嘴由内向外分别为:第一氧化剂通道、高压合成气通道、气化燃料通道及第二氧化剂通道,其中第一氧化剂通道、第二氧化剂通道内的氧化剂
比例根据工况调整。
11.可选的,所述的气化燃料为气体、液体或者固体,气体为天然气或者焦炉煤气,液体为水煤浆、渣油、多元料浆或者有机废液,固体为流动状态的煤粉。
12.可选的,所述的氧化剂为氧气、空气或者水蒸气。
13.本发明与现有技术相比的优点在于:
14.(1)本发明通过将净化后的合成气加压后循环供入工艺烧嘴的方法来补充气化装置低负荷运行时进入工艺烧嘴的气化燃料和氧化剂的减少量,从而使工艺烧嘴出口混合射流流速始终维持在正常范围内,保证气化装置在低负荷下高效稳定运行;
15.(2)本发明循环供入气化炉的高压合成气由气化炉内引出,为气化反应产物,循环供入后对气化炉内气化反应影响较小。并且当工况稳定后循环合成气量维持不变,不会额外增加气化反应的燃料消耗,也不会对进入下游工段的主合成气量产生影响。
附图说明
16.图1为本发明煤气化装置的一种实现方式示意图;
17.图2为本发明煤气化装置的另一种实现方式示意图。
18.附图标记:
19.1为气化燃料;2为氧化剂;3为工艺烧嘴;4为气化炉;5为净化单元;6为冷却器;7为分液罐;8为压气机;9为粗合成气;10为主合成气;11为循环合成气;12为冷凝液;13为高压合成气。
具体实施方式
20.下面结合说明书附图和具体实施例对本发明装置作进一步详细说明。
21.如图1所示,本发明的可变负荷运行的煤气化装置,包括气化炉4、工艺烧嘴3、净化单元5、冷却器6、分液罐7和压气机8。
22.工艺烧嘴3安装在气化炉4上,将气化燃料1和氧化剂2送入气化炉4发生欠氧燃烧反应,生成的粗合成气9进入净化单元5去除灰尘等杂质。
23.净化单元5出口合成气分为两部分,其中小部分合成气,称为循环合成气11进入冷却器6降温,内部水蒸气冷凝,经分液罐7分离冷凝液12后进入压气机8增压,增压后形成高压合成气13送入工艺烧嘴3并重新进入气化炉4;其余大部分合成气,称为主合成气10,去往下游变换、合成等工段,进一步提取氢气或用于合成氨、制甲醇、制乙二醇、合成油等。
24.循环合成气11冷却去除水蒸气的目的在于避免合成气中水蒸气在压缩过程中析出,造成压气机8积液。冷却器6可以采用空气冷却方式,如图1所示;也可以采用换热器将高温合成气热量传递给氧化剂2而回收部分能量,更加节能,如图2所示。
25.净化单元5通过洗涤、过滤等方法去除合成气中的灰尘等杂质,包括:应用于激冷流程的文丘里洗涤器+水洗塔方式或应用于废锅流程的金属陶瓷等滤芯过滤方式。
26.工艺烧嘴3包括同轴套置的n个通道,n≥3。当n=3时,工艺烧嘴3由内向外分别为:高压合成气通道、气化燃料通道及氧化剂通道。当n=4时,工艺烧嘴3由内向外分别为:第一氧化剂通道、高压合成气通道、气化燃料通道及第二氧化剂通道,其中第一、第二氧化剂通道内的氧化剂比例可根据工况进行调整。当然,也可以根据实际情况对四个通道的由内及
外的顺序进行调整。
27.气化燃料1可以为天然气、焦炉煤气等气体,或为水煤焦浆、渣油、多元料浆、有机废液等液体,或为流动状态的煤粉等固体。
28.氧化剂2为氧气、空气、水蒸气等气体。
29.当气化炉4由正常负荷降低负荷运行时,减少进入工艺烧嘴3的气化燃料1和氧化剂2流量,通过增加进入工艺烧嘴3的循环合成气11流量来将工艺烧嘴3出口混合射流流速维持在正常范围内。
30.当气化炉4由低负荷提升负荷运行时,恢复进入工艺烧嘴3的气化燃料1和氧化剂2流量,并减少进入工艺烧嘴3的循环合成气11流量来将工艺烧嘴3逐渐恢复到正常工况。
31.本发明说明书中未作详细描述的内容属本领域技术人员的公知技术。
技术特征:1.一种可变负荷运行的煤气化装置,其特征在于:包括气化炉(4)、工艺烧嘴(3)、净化单元(5)、冷却器(6)、分液罐(7)和压气机(8),工艺烧嘴(3)安装在气化炉(4)上,将气化燃料(1)和氧化剂(2)送入气化炉(4)发生欠氧燃烧反应,生成粗合成气(9)并送入净化单元(5)去除灰尘杂质,净化单元(5)出口合成气分为两部分,一部分送往下游再利用,另一部分作为循环合成气(11)进入冷却器(6)降温,再经分液罐(7)分离冷凝液(12)后进入压气机(8)增压,增压后形成高压合成气(13)送入工艺烧嘴(3)并重新进入气化炉(4);当气化炉(4)由正常负荷降低负荷运行时,减少进入工艺烧嘴(3)的气化燃料(1)和氧化剂(2)流量,并增加进入工艺烧嘴(3)的循环合成气(11)流量;当气化炉(4)由低负荷提升负荷运行时,恢复进入工艺烧嘴(3)的气化燃料(1)和氧化剂(2)流量,并减少进入工艺烧嘴(3)的循环合成气(11)流量。2.根据权利要求1所述的一种可变负荷运行的煤气化装置,其特征在于:所述的冷却器(6)可以采用空气冷却方式,或者采用换热器将热量传递给氧化剂(2)。3.根据权利要求1所述的一种可变负荷运行的煤气化装置,其特征在于:所述的净化单元(5)通过洗涤或者过滤方法去除灰尘杂质,包括应用于激冷流程的文丘里洗涤器+水洗塔方式,或应用于废锅流程的金属陶瓷滤芯过滤方式。4.根据权利要求1所述的一种可变负荷运行的煤气化装置,其特征在于:所述的工艺烧嘴(3)包括同轴套置的n个通道,n≥3。5.根据权利要求4所述的一种可变负荷运行的煤气化装置,其特征在于:所述的n=3时,工艺烧嘴(3)由内向外分别为:高压合成气通道、气化燃料通道及氧化剂通道。6.根据权利要求4所述的一种可变负荷运行的煤气化装置,其特征在于:所述的n=4时,工艺烧嘴(3)由内向外分别为:第一氧化剂通道、高压合成气通道、气化燃料通道及第二氧化剂通道,其中第一氧化剂通道、第二氧化剂通道内的氧化剂比例根据工况调整。7.根据权利要求1所述的一种可变负荷运行的煤气化装置,其特征在于:所述的气化燃料(1)为气体、液体或者固体,气体为天然气或者焦炉煤气,液体为水煤浆、渣油、多元料浆或者有机废液,固体为流动状态的煤粉。8.根据权利要求1所述的一种可变负荷运行的煤气化装置,其特征在于:所述的氧化剂(2)为氧气、空气或者水蒸气。
技术总结一种可变负荷运行的煤气化装置,工艺烧嘴(3)安装在气化炉(4)上,将气化燃料(1)和氧化剂(2)送入气化炉(4)发生欠氧燃烧反应,生成粗合成气(9)并送入净化单元(5)去除灰尘杂质,净化单元(5)出口合成气分为两部分,一部分送往下游再利用,另一部分作为循环合成气(11)进入冷却器(6)降温,再经分液罐(7)分离冷凝液(12)后进入压气机(8)增压,增压后形成高压合成气(13)送入工艺烧嘴(3)并重新进入气化炉(4)。当气化炉(4)由正常负荷降低负荷运行时,增加进入工艺烧嘴(3)的循环合成气(11)流量;当气化炉(4)由低负荷提升负荷运行时,减少进入工艺烧嘴(3)的循环合成气(11)流量,由此实现可变负荷运行。负荷运行。负荷运行。
技术研发人员:马利锦 郭莹 赵顶 刘金勇 于鸿胤 辛争秋 唐强
受保护的技术使用者:北京航化节能环保技术有限公司
技术研发日:2021.11.29
技术公布日:2022/3/25