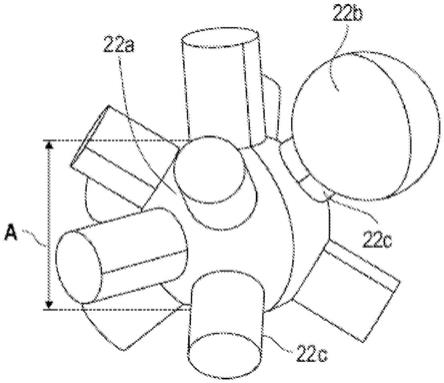
1.本发明特别是涉及一种涡轮机的离心式通气器。
背景技术:2.涡轮机是复杂的系统,该复杂的系统使用许多必须配备有密封装置的旋转组件(涡轮、压缩机等)。这些密封装置通常由布置在旋转组件附近的加压空气的迷宫式部件制成。为此,空气直接从涡轮机的空气管道中获取。然后,该空气通过为此设置的各种迷宫式部件穿过涡轮机,然后排到涡轮机的外部,以限制涡轮机的其他区域(特别是减速齿轮箱、附件齿轮箱等)中压力的升高。穿过涡轮机的不同区域的该空气中充有用于冷却和润滑旋转组件的轴承和小齿轮的油。为了避免含油空气的排出,以降低涡轮机的生态影响,以降低油耗并限制油储量的填充,重要的是提供通气器,该通气器在将空气排出到涡轮机的外部之前,使得油与空气能够分离。
3.这种通气器通常由机械动力输出装置安装和驱动,机械动力输出装置在涡轮机的附件箱或减速齿轮箱处。
4.以已知的方式,这种离心式通气器包括一个或多个离心式空气/油混合物分离外壳,离心式空气/油混合物分离外壳围绕空心轴布置并由外环形壁和内环形壁界定。通气器还包括轴向入口和外周油出口,该轴向入口用于向外壳供给空气/油混合物,该外周油出口设置在外壁中。因此,当通气器通常借助于附件齿轮箱或减速齿轮箱中的小齿轮旋转时,油自然地被离心驱动到设置在通气器的外周上的油出口。另外,无油空气出口形成在内壁中,并且连接到空心轴,这使得空气能够排出到外部。
5.一些通气器,例如在申请wo-a1-2011/004023中描述的通气器,还包括布置在通气器外壳中的过滤器,以改善油滴的收集并因此促进混合物的除油。事实上,过滤器增加了可用的接触表面,并因此提高了由混合物流携带的油滴被挂在壁上的可能性。这些过滤器通常由金属泡沫制成,该金属泡沫例如是以名称出售的泡沫。
6.然而,已知通气器的性能通常受到内部压力下降的阻碍,内部压力下降特别是由于两个原因造成的,即在除油过程中,空气流所占据的管道的形状(包括离心外壳)以及金属泡沫的存在。
7.关于通气器的内部形状界定空气流所占据的管道,然后制造过程可能会限制用于实现最佳几何形状的可能性。
8.就金属泡沫的存在而言,压力损失是由于以下事实造成的:在高速下(例如在大约6000rpm的速度下),由金属泡沫形成的前表面像壁一样起作用,并且空气颗粒渗透到泡沫中的程度很低。
9.因此,需要改进离心式分离外壳的设计,以优化除油性能,同时限制通气器上的压力下降。
技术实现要素:10.为此,本发明涉及一种用于涡轮机的空气/油混合物的离心式通气器的部件,该部件用于围绕对称轴线旋转,形成用于对所述混合物进行离心分离的环形外壳,该环形外壳包括用于供给所述混合物的轴向取向的入口、用于从所述混合物中分离出的无油空气离开的第一径向向内取向的出口和至少一个第二径向向外取向的油出口,第二径向向外取向的油出口用于将从所述混合物中分离出的油排出到通气器的外部,该外壳进一步包括至少一个网状结构,网状结构占据所述管道中的至少一个空间,该至少一个网状结构封闭该轴向入口和该内部径向出口之间的连通。
11.所述部件的特征在于,该网状结构通过由简单形状的互连所产生的单个模块的材料或空隙的空间重复而形成,该简单形状从恒定截面的球体或卵形体和杆中选择,该恒定截面特别是圆形、矩形或八边形,所述模块被布置成使得材料之间的空隙连通,以在形成三面体的空间的至少三个维度中组织通过材料的路径。
12.该研究使得能够验证基于该原理实现的网状物的性能,以通过离心分离对混合物进行除油,同时使压力损失最小化。该验证使用了围绕基本结构的大量几何变化:杆直径的变化、几何元件之间的距离变化、杆长度的变化、圆形截面由其他几何形状(多面体类型)代替,反之亦然。
13.此外,仅由几个几何参数限定的模块的重复适用于例如增材制造的制造方法,并且使得部件更容易制造。
14.优选地,所述网状物的孔隙率介于70%到95%之间。
15.孔隙率是网状物中空隙体积和材料体积之间的比率。高孔隙率限制了压力损失。
16.有利地,网状物的模块提供至少一个空隙体积,空隙体积包含直径或边介于1mm到2.5mm之间的球体或正方体,或者该模块的材料元件的纵向长度介于1mm到2.5mm之间。
17.同样有利地,空隙元件或材料元件的横向尺寸介于0.1mm到1mm之间。
18.这些尺寸适于使得油滴沿着网状物的材料元件捕获,而不阻碍混合物通过网状物的通道。应注意的是,这些参数可根据部件的位置在网状物中逐渐改变,以在混合物通过通气器时考虑混合物的状态。
19.根据本发明的根据网状物的实施例,空隙的模块由与中心球体相交的球体形成。
20.根据其他实施例,空隙的模块由与中心球体相交的杆形成,直径小于中心球体的球体连接到所述杆中的至少一个杆。
21.在其他实施例中,材料模块包括在第一方向上定向且横向交错的第一系列的杆,第一系列的杆与在第二方向上定向且横向交错的第二系列的杆具有交叉点,该第二方向横向于第一方向,该模块进一步包括一系列的互补杆,一系列的互补杆以锯齿形方式分别连接第一系列的杆的行中的和与该行交叉的第二系列的杆交叉的交叉点、所述第二系列的杆的行中的和与该行交叉的所述第一系列的杆交叉的交叉点,以在空隙周围产生材料缠结。
22.在其它实施例中,材料模块包括以六面体互连的杆。
23.在其他实施例中,材料模块包括节点,其中形成第一二面体的两个杆连接到形成第二二面体的两个其它杆,第二二面体沿着公共中间轴线相对于第一二面体旋转大致90度。
24.有利地,所述部件被制成一个部件,例如,增材制造。这使得能够优化部件的形状
并将网状物整合到这些形状中。
25.本发明还涉及一种用于涡轮机的空气/油混合物的离心式通气器,该离心式通气器包括如上所述的部件、与所述部件成一体并被构造成收集从内部径向出口离开的空气的空心轴和用于使组件旋转的小齿轮。
附图说明
26.在阅读以下详细说明时,为了理解该说明对附图进行参照,本发明的其它特征和优点将显现,在附图中:
27.[图1]图1示出了根据对称平面切开的根据本发明的通气器的示意性透视图;
[0028]
[图2]图2示出了根据本发明制造的用于图1的通气器的部件的根据对称平面切开的透视局部示意图;
[0029]
[图3]图3示出了安装在图1的部件中的根据本发明的网状物的第一实施例的空隙体积的模块的示意性透视图;
[0030]
[图4]图4示出了对应于图3的模块的网状物的一部分的示意性透视图;
[0031]
[图5]图5示出了安装在图1的部件中的根据本发明的网状物的第二实施例的空隙体积的模块的示意性透视图;
[0032]
[图6]图6示出了对应于图5的模块的网状物的一部分的示意性透视图;
[0033]
[图7]图7示出了安装在图1的部件中的根据本发明的网状物的第三实施例的空隙体积的模块的示意性透视图;
[0034]
[图8]图8示出了对应于图7的模块的网状物的一部分的示意性透视图;
[0035]
[图9]图9示出了安装在图1的部件中的根据本发明的网状物的第四实施例的空隙体积的模块的示意性透视图;
[0036]
[图10]图10示出了对应于图9的模块的网状物的一部分的示意性透视图;
[0037]
[图11]图11示出了安装在图1的部件中的根据本发明的网状物的第五实施例的材料体积的模块的示意性透视图;
[0038]
[图12]图12示出了对应于图11的模块的网状物的一部分的示意性透视图;以及
[0039]
[图13]图13示出了安装在图1的部件中的根据本发明的网状物的第六实施例的材料体积的模块的示意性透视图。
具体实施方式
[0040]
在附图中,为了说明和清楚起见,不严格遵照比例和比率。
[0041]
如图1所示,使用本发明的通气器包括围绕纵向对称轴线x旋转的可动部件1。如图2更详细地所示,所述可动部件1包括结构部件,该结构部件包括第一壳体2,该第一壳体由第二壳体3包围。两个壳体2、3之间的空间形成围绕对称中心轴线x旋转的管道4,该管道用于使待分离的空气/油混合物流通。
[0042]
管道4包括轴向入口5,该轴向入口用于待分离的空气/油混合物进入。该轴向入口5对应于管道4的第一部分6的一个端部,该管道基本轴向延伸,以使混合物离心。轴向延伸管道的第一部分6用作离心外壳,这是因为在该轴向延伸管道的第一部分处离心力以最大的力施加在空气/油混合物上。因此,在以下描述中将该轴向延伸管道的第一部分称为离心
外壳6。
[0043]
另外,管道4在此还包括围绕对称轴线x周向分布的多个隔室。隔室由径向延伸的纵向隔板7形成。有利地,这些纵向隔板7连接第一壳体2和第二壳体3,因此形成将该第一壳体和该第二壳体保持在一起的连接。每个隔室与混合物的轴向入口5连通。轴向隔板7形成翅片,翅片使进入相邻隔室的混合物旋转。
[0044]
在该离心外壳的第二轴向端部处,离心外壳6由第二壳体3的部分3a轴向封闭,该第二壳体的部分大致垂直于对称轴线x,并且该离心外壳包括在第一壳体2和第二壳体3之间朝向对称轴线x的径向开口9。第二壳体3在入口6和第二壳体的部分3a之间形成离心外壳6的径向外壁3b,该离心外壳的径向外壁是大致环形的,该第二壳体的部分在该离心外壳的第二端部处轴向界定离心外壳6。离心外壳6包括设置在径向外壁3b中的呈通孔形式的多个径向油出口8,并且被构造成能够排放通过通气器的离心力从混合物中分离出的油。管道4的每个隔室连接到一个或更多个径向油出口8。
[0045]
第一壳体2在离心外壳8中形成管道的隔室的径向内壁。该第一壳体从管道的入口6开始、在第二壳体3的轴向部分3a之前轴向停止,以在离心外壳6的第二端部处提供径向向内开口9。该第一壳体的形状可以被优化,以促进油分离并特别是在径向出口处形成的弯曲部处使压力损失最小化。在所示的示例中,径向内壁2从轴向入口5开始是大致环形的,并且包括与径向入口5相对的轴向端部2a,该轴向端部在离心外壳6的第二端部处形成圆形的周向凸缘或板。第一壳体的轴向端部2a的这种形状趋向于在离心外壳6的出口处在管道4中形成的弯曲部的通道处使流体径向向外返回,以优化空气/油混合物流的流动。
[0046]
管道4包括第二部分10,该第二部分通过第一壳体2与第二壳体3之间的径向开口9与离心外壳6连通,并且第二部分被构造成将流体引导到空隙圆柱形空间中的径向出口11,该空隙圆柱形空间在离心外壳6的边界之间轴向延伸。第一壳体2和第二壳体3形成轴环12、13,轴环限制所述空隙圆柱形空间。这些轴环12、13被构造成将部件1连接到轴14,如图1所示,该轴驱动部件旋转。管道4在纵向平面中的横截面具有优化的弯曲形状,以将无油空气引导到内部径向出口12。
[0047]
部件1用在通气器中,该通气器包括用于使部件旋转的小齿轮15,该小齿轮本身包括遮蔽件16。在所示的示例中,遮蔽件16整体地连接到可动部件1,并且包括与轴向入口5相对的开口,该开口用于使混合物进入管道4的隔室中。遮蔽件16还牢固地连接到空心轴14。
[0048]
有利地,部件1的结构部件通过增材制造方法制成,该结构部件由第一壳体2和第二壳体3构成,该方法使得能够实现示例的复杂形状,特别是促进油滴与混合物的分离,同时使压力损失最小化。增材制造可以通过金属粉末的受控激光熔合工艺以已知的方式进行。然而,所呈现的示例并不限制本发明的实施,并且通过机加工或铸造的制造方法也可用于可动部件1中的混合物的通道管道的更常规形状。
[0049]
根据本发明,该部件还包括在每个隔室中由网状物17制成的至少一个蜂窝结构。
[0050]
有利地,网状物17通常不完全延伸到管道4的隔室中。在所示的示例中,网状物主要延伸到离心外壳6中,以在隔室中形成两个不同的连续空间:仅延伸到离心外壳6中的无材料的空间18以及由网状物17填充的空间19。空的空间18通过隔室在轴向入口5处的开口被供给有混合物,并通向由网状物17填充的空间19。由网状物17填充的空间19通向管道的第二部分10。图1和图2所示的构造不是限制性的。特别地,网状物17可以仅占据离心外壳6
的圆柱形部分中的位于入口5和弯曲部之间的空间,使得例如通过将网状物17插入管道4的隔室中而通过组装来制造部件1变得更容易。
[0051]
如图1中的箭头f1所示,因此,含油的空气通过遮蔽件的开口进入可动部件1。在空的空间18中,纵向隔板7驱动混合物旋转。在流f1进入外壳的该第一部分的过程中,第一阶段的除油通过离心作用进行。网状物17具有捕获在第一阶段期间未提取的油滴的功能。通过离心作用,油通过网状物17排到径向出口8,如箭头f2所示。该第二阶段的除油也在由网状物17占据的空间19中进行,不会由于油滴的轴向侵蚀和根据本发明的网状物的结构而造成明显的压力损失。
[0052]
已经穿过管道4中的网状物17的无油空气然后进入空心轴14并排出。
[0053]
同样根据本发明,网状物17通过在以使得材料之间的空隙连通的方式布置的三个空间维度中重复单个模块而形成,以便在三个空间维度中组织通过网状材料的路径,所述路径具有弯曲和/或收缩和/或分叉。参照图3至图13,给出了例如网状物的数个实施例。
[0054]
根据第一实施例,参照图3,空隙形成模块,在模块中,中心球体20a连接到六边形横截面的第一系列的八个圆柱形杆20b,该八个圆柱形杆具有八角对称性。此外,在第一系列的四个杆20b之间,方形截面的圆柱形杆20c连接到所述球体20a,以形成第二系列的六个垂直杆。中心球体20a的直径a通常约为2.5mm。该模块在由第二系列的杆20c限定的三个空间方向上空间地重复,该第二系列的杆将中心球体20a连接到网状物的网络中的六个其他空隙球体。第一系列的杆20b将中心球体20a连接到在网状物的网络中对角地围绕中心球体的八个其它中心球体。调整杆20b和20c的长度以获得非常通风的网状物,该网状物通常具有90%的孔隙率。图4示出了从这种网状物获得的材料网络的类型。从这些图中可以看出,空隙在数个非共面方向上为流体提供通道,但是当流从球体流到杆时,流遇到流通道的横截面变窄,可能在方向上偏转和/或分成数个流。
[0055]
根据第二实施例,参照图5,空隙形成模块,在模块中,直径a介于约2mm到2.2mm之间的中心球体21a与直径较小的一系列四个球体21b以立方网络对称的方式相交。另外,在空间的三个方向上重复的空隙体积的模块给出了用于网状物的材料网络,如图6所示。通过该组织,网状物的孔隙率大约为85%。这里我们再次看到,从中心球体21b流到沿着立方网络的对角线之一的另一个球体的流体在从中心球体21a流到中间球体21b时面临压缩或收缩。
[0056]
根据第三实施例,参照图7,空隙形成模块,在模块中,中心球体22a通过圆柱形截面的杆22c沿着立方网络的对角线连接到一系列其它球体22b。通常,该网络中的球体22a或22b的直径a约为2.5mm。这里调整杆的长度和横截面以获得约77%的孔隙率。图8示出了可以从这种网状物获得的材料网络的类型。这里再次可以看出,流体在不同方向上的通道在杆22c和球体22a或22b之间被收缩或压缩。
[0057]
这前三个实施例结合了高孔隙率,使得装载有液滴的混合物能够通过具有材料和空隙之间的大接触表面的网状物,这可以促进通过网状物捕获液滴。
[0058]
根据第四实施例,参照图10,材料模块包括在第一方向上定向且横向交错的第一系列的杆23a,该第一系列的杆与在第二方向上定向且也横向交错的第二系列的杆23b交叉,该第二方向横向于第一方向。对于包含在同一平面中的来自第一系列的杆23a的杆,来自第二系列的杆23b的杆在交叉点处与这些杆23a相遇,并且杆23b在杆23a之间通过。第一
系列的杆和第二系列的杆交换时会出现相同的现象。该网状物由第一系列的互补杆23c完成,第一系列的互补杆以锯齿形方式在第二系列的杆23b的平面中在两个交叉点和两个杆23b之间与所述平面交叉的第一系列的杆23a之间延伸。第二系列的互补杆23d通过交换第一系列的杆23a和第二系列的杆23b的作用而获得。如图10所示,这会在所有方向上彼此连通的空隙周围产生材料缠结。参照图9,因此产生的空隙体积的模块相当复杂,但是我们可以看到,在这里产生了具有介于约1.2mm到1.8mm之间的边缘a的立方形空隙体积23e,该立方形空隙体积连接到拉伸空隙体积23f。该模块为流体在不同的空间方向上通过网状物的通道产生了压缩和分叉。拉伸空隙体积23f的较大尺寸等于立方形空隙体积23e的边缘a,并且该拉伸空隙体积的较小尺寸为大约0.1mm到1mm。网状物的杆在横截面上都是大致立方形的。空隙体积的较大尺寸a大致等于模块中的杆的长度,并且较小尺寸b大致等于杆截面的边缘。通常,通过调整该网状物的尺寸参数可以获得90%到95%的孔隙率。
[0059]
在第五实施例中,参照图11,材料模块包括沿六面体互连的一系列杆24a。参照图11,六面体在垂直方向上堆叠,并在水平面中以六边形排列组装。所得网状物如图12所示。杆24a是具有圆形横截面的圆柱体,但是杆的横截面也可以是正方形或矩形或正多边形。杆的长度a通常介于约1mm到2mm之间。杆的横截面的直径b通常介于0.1mm到1mm之间。通过调整这些参数可以获得90%到95%的孔隙率。在该网状物中,杆之间的空隙在所有方向上为流体提供通道,但是在每个方向上,杆之间的通道的横截面根据模块的位置而改变,或者插入杆24a将通道分隔成两个通道。
[0060]
在第六实施例中,参照图13,材料模块具有节点,其中形成第一二面体的两个杆25a和25b连接到形成第二二面体的两个其它杆25c和25d,该第二二面体沿着公共中间轴线相对于第一二面体旋转大致90度。模块在空间上重复自身,每个杆的端部形成两个二面体彼此接触的节点。与前述实施例相同,杆25a到杆25d是圆形横截面的圆柱体,但是杆的横截面也可以是正方形或矩形或正多边形。杆的长度通常介于0.4mm到1mm之间。杆的截面的直径通常介于0.1mm到1mm之间。通过调整这些参数可以获得90%到95%的孔隙率。在该网状物中,杆25a到杆25d之间的空隙在所有方向上为流体提供通道,但是在每个方向上,杆之间的通道的横截面根据模块的位置而改变,或者插入杆将通道分隔成两个通道。
[0061]
数种材料可以制成根据本发明的网状物。网状物的增材制造方法例如通过金属粉末的激光熔合,使得能够产生所示的模块。该方法还使得能够根据离心外壳的位置来改变模块的尺寸。在图1和图2所示的部件1的示例中,壁3和壁2以及网状物的一个部件的增材制造使得网状物能够放置在围绕管道的弯曲部的空间19中。该示例不是限制性的,对于可动部件的其它几何形状,离心外壳结构8和具有最终组装的网状结构的单独制造是可能的。
[0062]
在外壳6中的网状物17的实施例的变型中,通过连续地改变几何参数可以沿轴线重复模块。以这种方式,可以获得具有可变密度的网状物。关于轴向变化,这使得能够例如在含油空气f1移动通过网状物时捕获越来越小的液滴,以限制对压力损失的影响。在径向上,网状物模块17的较大尺寸或多或少地使得能够均匀地消除靠近内壁2的区域与靠近外壁3的区域之间的压力损失,该靠近内壁2的区域很少受到离心力的作用,该靠近外壁3的区域高度受到离心力的作用。还可以改变每个隔室内的方位角模块的尺寸。与在径向方向上的离心力效应一样,这使得能够考虑到相对于旋转方向,在后面的隔室的轴向隔板7上可能发生的累积效应。
[0063]
这些实施例使得能够使根据本发明的网状物适应于管道的形状,以使捕获的液滴的数量最大化,同时使相关的压力损失最小化。