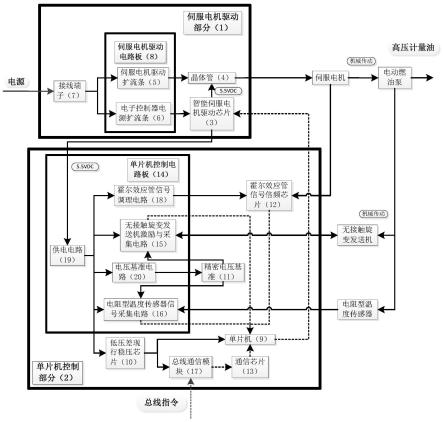
1.本发明属于燃油控制技术领域,涉及一种高精度燃油计量电子控制装置及控制方法。
背景技术:2.在传统机械液压控制领域,燃油控制装置结构一般为发动机主轴带动燃油泵转动,泵的转速由发动机状态决定,不可实现自我调节,泵后输出的高压燃油流量远大于实际需求,再通过装置中的计量模块对泵后高压燃油进行计量后输出。在该工作模式下,泵的转速跟随发动机转速,燃油控制装置结构相对复杂,在满足燃油供给的同时存在大量回油,造成装置燃油温升较大,效率较低。
3.随着多电发动机的快速发展以及分布式电子控制技术在航空发动机燃油控制系统上的应用,燃油控制装置既要保证对燃油的高精度计量,同时又要追求燃油控制的高效率及快速响应,这对燃油控制装置的设计提出了更高的要求。然而现有技术尚缺乏基于分布式电子控制的高精度航科燃油计量电子控制技术,因此急需发展以解决现有燃油控制响应慢、效率低、精度较低的问题。
技术实现要素:4.本发明的目的是:提供了一种既能提高工作效率,也为燃油泵根据发动机实际燃油需求进行工作状态的调节提供了可能的高精度燃油计量电子控制装置。
5.另外,基于上述控制装置,还提供了一种高精度燃油计量电子控制方法。
6.本发明的技术方案是:
7.一种高精度燃油计量电子控制装置,其包括伺服电机驱动部分1、单片机控制部分2;所述伺服电机驱动部分1与单片机控制部分2通过对接插座连接,固定在电动燃油泵壳体上,所述伺服电机驱动部分1负责接收单片机控制部分的控制指令,将供电电源提供的电压经变电后,按照需求提供给相应伺服电机各项绕组,驱动伺服电机运转,再驱动电动燃油泵工作;所述单片机控制部分2用于与总线通信,接收外部流量指令后转化为转速指令,对伺服电机进行无极调速;接收无接触旋变发送机及燃油温度传感器的反馈信号,向伺服电机驱动部分及各元器件发送电气指令,实现控制逻辑,对转速进行闭环调节,保证输出燃油流量的精度。
8.所述伺服电机驱动部分1包括智能伺服电机驱动芯片3、晶体管4、伺服电机驱动扩流条5、电子控制器电源扩流条6、接线端子7及伺服电机驱动电路板8;其中,供电电源与接线端子7连接,通过伺服电机驱动扩流条5、电子控制器电源扩流条6及伺服电机驱动电路板8,传导强电电流,驱动智能伺服电机驱动芯片3及晶体管4工作,实现伺服电机控制功能。
9.所述的伺服电机驱动电路板8,用于安装伺服电机驱动部分的各元器件,并实现整体电气功能,接收伺服电机中霍尔效应位置传感器传回的伺服电机转子位置信息,对其进行解码,同时根据单片机控制部分通过pwm给定的转速信息和功率信息生成伺服电机所需
要的控制时序;然后驱动场效应管提供伺服电机所需要的驱动电压和电流。伺服电机各相的驱动电流通过采样电阻进行采样,然后对采样的电压进行滤波和放大,反馈给单片机控制部分。
10.所述的伺服电机驱动扩流条5为长宽与电路板焊条尺寸一致,厚度增加的长条形铜板,与伺服电机驱动电路板8焊接,提高电路板上供电部分覆铜的供电能力,将电源经变电后形成强电传递至伺服电机,驱动伺服电机工作。
11.所述的电子控制器电源扩流条6为长宽与电路板焊条尺寸一致,厚度增加的长条形铜板,与伺服电机驱动电路板8焊接,提高电路板上供电部分覆铜的供电能力,将电源经变电后形成弱电传递至智能伺服电机驱动芯片3,实现芯片通电工作,进而控制伺服电机实现驱动。
12.所述单片机控制部分2包括单片机9、低压差现行稳压芯片10、精密电压基准11、霍尔效应管信号倍频芯片12、通信芯片13、单片机控制电路板14。
13.所述的单片机控制电路板14包括无接触旋变发送机激励与采集电路15、电阻型温度传感器信号采集电路16、总线通信模块17、霍尔效应管信号调理电路18、供电电路19及电压基准电路20,单片机部分主要实现单片机相关的电路,如单片机的供电、时钟、调试接口、自带温度传感器接口、与伺服电机驱动部分接口等;通信接口部分实现rs422和can通信电路;传感器实现pt100信号调理电路、无接触旋变发送机信号激励和调理电路、霍尔效应管供电电路及备频电路等。
14.所述的无接触旋变发送机激励与采集电路15,电路采用交流耦合的方式,减少零漂对输出的影响。
15.所述的电阻型温度传感器信号采集电路16,电路采用双运放结构的差分放大器,为深度负反馈电路,可以消弱运算放大器本身增益变化对电路增益的影响。
16.一种利用所述的高精度燃油计量电子控制装置的控制方法,其特征在于,通过总线,主控设备可获取该智能设备的内部参数、采集的数据;可以设置设备的内部参数、输出指令;可以对设备进行校准。燃油流量的控制以电机转速为控制量,以阀芯的旋转角位移为输出量,旋变传感器的输出为反馈量,进行闭环控制;以燃油的温度、旋变传感器等的故障状态作为监控状态,对算法进行相应处理;控制算法采用经典的抗积分饱和pid控制算法,算法的pid参数、周期参数可以在线调节;伺服电机采用了智能伺服电机控制芯片,不需要单片机的干预即可进行伺服电机的控制。
17.所述的高精度燃油计量电子控制方法,其过程如下:
18.步骤1:通过总线接收外部流量给定指令;
19.步骤2:将流量给定指令解算为转速给定指令,驱动伺服电机按给定转速工作;
20.步骤3:接收输出燃油流量反馈信号、燃油温度反馈信号及伺服电机转速反馈信号;
21.步骤4:根据反馈信号及流量给定指令解算转速给定指令,完成对伺服电机的闭环控制。
22.本发明的优点是:与现有技术相比,本发明使用电子控制装置直接控制电动燃油泵,采集其高压泵后反馈信号对输入指令进行调整,形成闭环控制,最终通过对其转速的精确控制直接达到精准输出需求高压燃油流量。
23.本发明实现了电子控制装置与电动燃油泵的一体式设计以及分布式控制,具备总线通讯能力,在接受中央控制器流量需求指令后可自动精准调节流量,减轻中央控制器的功能、性能负担,为发动机燃油控制系统的分布式控制提供了可能。同时,本发明使得燃油控制系统中无需附加独立燃油计量设备,有效简化了燃油控制系统的结构及控制难度,相对于现有技术具有实质性的技术特点和显著的技术进步。
24.另外,本发明由电子控制装置直接向伺服电机发送指令,其电磁响应速度快,接收控制器指令后可快速调节转速,减少调节器响应时间,保证流量及时输出。
附图说明
25.图1为本发明的结构框图,图中:伺服电机驱动部分1、单片机控制部分2、智能伺服电机驱动芯片3、晶体管4、伺服电机驱动扩流条5、电子控制器电源扩流条6、接线端子7、伺服电机驱动电路板8、单片机9、低压差现行稳压芯片10、精密电压基准11、霍尔效应管信号倍频芯片12、通信芯片13、单片机控制电路板14、无接触旋变发送机激励与采集电路15、电阻型温度传感器信号采集电路16、总线通信模块17、霍尔效应管信号调理电路18、供电电路19、电压基准电路20。
26.图2为高精度燃油计量电子控制方法结构框图。
具体实施方式
27.下面结合附图和实施例对本发明作进一步的说明,但并不作为对本发明限制的依据。
28.实施例1
29.本发明高精度燃油计量电子控制装置由伺服电机驱动部分1、单片机控制部分2组成,如图1所示。
30.所述伺服电机驱动部分1包括智能伺服电机驱动芯片3、晶体管4、伺服电机驱动扩流条5、电子控制器电源扩流条6、接线端子7及伺服电机驱动电路板8;其中,供电电源与接线端子7连接,通过伺服电机驱动扩流条5、电子控制器电源扩流条6及伺服电机驱动电路板8,传导强电电流,驱动智能伺服电机驱动芯片3及晶体管4工作,实现伺服电机控制功能。
31.所述智能伺服电机驱动芯片3支持3个半桥高端和低端的驱动,支持100%占空比的脉冲输出,可控制电机转速及功率;驱动支持10ma20ma~1a2a的峰值驱动电流,电流的大小可以几个档位调整;集成了6~60v输入、0.6a输出的bulk电源控制器,可以直接产生3~5.5v的电源供控制部分使用;集成了增益可设定的差分电压放大器,可以直接对各半桥的驱动电流进行调理;支持通过外部的3个伺服电机中的霍尔效应位置传感器直接解算三个半桥的驱动芯片,提高了实时性,降低了对控制系统的需求。
32.所述晶体管4采用绝缘栅型场效应管来实现驱动半桥,该mosfet支持6mm x5mm的表贴封装,具有1.4mω的典型导通电阻,可大大降低导通功耗。该场效应管的源栅级电压可到60v,最大导通电流120a,内部做了最大电流限制,防止芯片意外烧毁。该场效应管的crss/ciss非常小,因此可获得比较好的emi效果。
33.所述伺服电机驱动扩流条5采用铜板机械加工定制的方式,为长宽与电路板焊条尺寸一致,厚度增加的长条形铜板,在弥补电路板覆铜导线电流不足的同时,满足大电流的
输出,并且考虑控制器的具体安装形式,体积小巧。
34.所述电子控制器电源扩流条6采用铜板机械加工定制的方式,为长宽与电路板焊条尺寸一致,厚度增加的长条形铜板,在弥补电路板覆铜导线电流不足的同时,满足大电流的输出,焊接在电路板背面。两个扩流条之间用耐高温的绝缘导热硅胶片进行绝缘。
35.所述伺服电机驱动电路板8中:伺服电机功率驱动电路共有三路,分别驱动伺服电机的三相。三路采用完全相同的电路,都是采用2个n沟道绝缘栅型场效应管构成半桥功率驱动,功率芯片并联大功率肖特基二极管进行续流及保护。相电流通过3mω采样电阻进行采样,然后经过滤波和限幅后输出到智能伺服电机驱动芯片的差分放大器进行电压放大。晶体管的驱动来自智能伺服电机驱动芯片的半桥晶体管驱动输出,同时增加了稳压管对伺服电机驱动芯片进行保护,增加rc滤波来限制晶体管的最大开关速率,降低噪声产生。
36.智能伺服电机驱动芯片电路主要包括内部升压电源电路、5.5v电源降压稳压电路、伺服电机相电流放大和滤波电路、与单片机控制部分2的spi接口电路等。电路板上利用bulk电源控制器产生1路5.5v/0.6a输出的直流电源,用于给霍尔位置传感器和单片机控制部分2供电。伺服电机的驱动板的电源vbus经过电阻分压、滤波后输出到单片机控制部分2进行监控。
37.为了方便调试,在电路板上预留了伺服电机霍尔位置传感器的电源和信号采集接口。该接口在实际应用中,放在单片机控制板上,方便接线。
38.所述单片机控制部分2包括单片机9、低压差现行稳压芯片10、精密电压基准11、霍尔效应管信号倍频芯片12、通信芯片13、单片机控制电路板14、供电电路19。
39.所述单片机9为采用qfn48封装的小型芯片,采用cortex-m4内核,具有80mhz主频,支持单精度浮点处理器,支持ad采集、da输出、uart通信等功能。
40.所述通信芯片13采用rs422和can通信。rs422电平转换芯片支持输出控制,支持输出信号斜率控制,可以有效降低总线上的噪声,最高支持500kbps的波特率。
41.所述的单片机控制电路板14包括无接触旋变发送机激励与采集电路15、电阻型温度传感器信号采集电路16、总线通信模块17、霍尔效应管信号调理电路18、供电电路19及电压基准电路20。其中,供电电路一端连接伺服电机驱动部分1的智能伺服电机驱动芯片3,另一端分别输出连接无接触旋变发送机激励与采集电路15、电阻型温度传感器信号采集电路16、霍尔效应管信号调理电路18、电压基准电路20以及低压差现行稳压芯片10。所述霍尔效应管信号调理电路18驱动霍尔效应管倍频芯片12工作,该霍尔效应管倍频芯片12采集伺服电机转速信号反馈至单片机9;所述无接触旋变发送机激励与采集电路15驱动无接触旋变发送机工作,并采集其反馈的位置信号反馈至单片机9;所述电阻型温度传感器信号采集电路16采集电阻型温度传感器反馈的温度信号反馈至单片机9;单片机9采集上述三种信号后,经解算形成新的转速指令发送至智能伺服驱动芯片3,形成伺服电机转速闭环控制。所述无接触旋变发送机激励与采集电路15采用数字方式dds方式产生正弦波激励信号,激励信号具有良好的频率、幅值和相位稳定性,激励信号的相位可由控制器准确获取。为了简化电路,采用两路dac输出互补电压的方式,电路采用完全相同的输出方式,降低电源电压,减少零电位电平。所述电压基准电路20通过精密电压基准分别与无接触旋变发送机激励与采集电路15、电阻型温度传感器信号采集电路16,用于为电阻型温度传感器温度采集的信号调理提供基准,以及为电阻型温度传感器信号采集和无接触旋变发送机的信号调理提供偏
置电压。单片机控制部分2主要实现单片机相关的电路,如单片机的供电、时钟、调试接口、自带温度传感器接口、与伺服电机驱动部分接口等;通信接口部分实现rs422和can通信电路;传感器部分实现电阻型温度传感器信号采集电路16、无接触旋变发送机激励与采集电路15、霍尔效应管信号调理电路18等。
42.所述总线通信模块17智能设备的总线接口采用rs422总线及can总线,其中rs422为主要总线接口,can为可选的备用接口,接收总线指令,同时输入端连接低压差现行稳压芯片10,其输出端经通信芯片13连接到单片机9,实现对单片机9的控制。
43.rs422通信的线路保护采用了三级方式,第一级采用tvs进行总线上的静电保护;利用上下拉电阻保证在总线高阻态时具有合适的电位,提高总线上数据的可靠性;第二级利用共模电感,减少总线上的共模干扰;第三级利用陶瓷放电管进行总线保护,具有抗雷击、强电磁干扰功能。此外,为了降低总线上的噪声,rs422驱动芯片选择具有边沿斜率控制的型号,信号地通过y电容接大地,减少总线上对地的差模噪声。rs422总线与主控芯片间实现了电气隔离,减少总线噪声对系统运行的干扰。
44.can总线的线路采用了四级保护,第一级采用tvs二极管进行总线上的静电保护;第二级利用共模电感,减少总线上的共模干扰;第三级利用ptc电阻降低总线上的浪涌电流;第四级采用陶瓷放电管进行总线保护,具有抗雷击、强电磁干扰功能。此外,利用总线上的对地电容调节总线信号的跳变边沿斜率,从而调节总线上边沿的斜率,从而降低噪声。can总线与主控芯片间实现了电气隔离,减少总线噪声对系统运行的干扰。
45.所述霍尔效应管信号调理电路18霍尔效应管信号调理电路分为两部分,第一部分进行供电和保护,第二部分连接霍尔效应管信号倍频芯片12进行信号倍频,以提高转速测量的精度和快速性。
46.霍尔效应管采用5.5v供电,其输出为集电极开路输出,因此采用1.5k的上拉电阻上拉到3.3v,以匹配单片机io电平以得到高、低电平的输出。信号的输出通过电容进行滤噪,通过限流电阻进行保护。
47.霍尔效应管的输出通过3输入异或门进行信号倍频,将相差120
°
电相位角的三相方波进行3倍频,通过上升沿、下降沿的同时捕捉,可得到6倍频的信号,从而提高伺服电机转速测量的精度和快速性。
48.所述伺服电机驱动部分1与单片机控制部分2通过对接插座连接,通过螺钉固定在电动燃油泵壳体上,实现外部指令接收解码、伺服电机驱动控制、流量指令解算、流量闭环控制功能;单片机控制部分2通过rs422总线接收中央控制器外部流量指令并将其转化为伺服电机驱动信号,对伺服电机进行无极调速,通过改变伺服电机转速向发动机提供满足指令需求的燃油流量。
49.请参阅图2,本发明高精度燃油计量电子控制方法,采用伺服电机自带的转子位置传感器进行电机转子转速测量和转子位置信息解码,智能伺服电机驱动芯片(3)驱动功率管产生所需的伺服电机的驱动电压、电流波形,从而控制伺服电机的转速。通过无接触旋变发送机激励与采集电路15采集无接触旋变发送机的转角信号获得活门的位移,通过电阻型温度传感器信号采集电路16采集电阻型温度传感器的温度信号获得燃油温度,综合两个参数获取燃油流量。单片机控制部分2通过采集上述的燃油流量反馈,控制需求的燃油流量。
50.控制算法采用自适应抗积分饱和pid控制算法。同时,以燃油的温度、旋变传感器
等的故障状态作为监控状态,对算法进行相应处理。当电阻型温度传感器有断线时,电阻型温度传感器信号采集电路16采集将会是一个比较小的值,该值不在测量的范围内,从而可以判断出这种故障。如果电阻型温度传感器短路,电阻型温度传感器信号采集电路16采集将会一个极大值,这样故障同样可以被监测出来。同时根据无接触旋变发送机激励与采集电路15采集的无接触旋变发送机正弦输出电压和余弦输出电压有效值的和是否在一定的范围内,来判断无接触旋变发送机的输出是否有断线的情况。根据伺服电机的转速变化与无接触旋变发送机的输出进行对比,可以判断旋变传感器阀芯是否卡滞。自适应抗积分饱和pid控制算法的pid参数、周期参数可以在线调节。该算法吸收了自适应控制与常规pid控制两者的优点,控制逻辑具备自动辨识被控过程参数、自动整定控制器参数、能够适应被控过程参数的变化能力,同时又具有常规pid控制器结构简单、鲁棒性好、可靠性高等特点。
51.本发明方法,实施时,具体过程如下:
52.步骤1:通过单片机部分2中的总线通信模块17及通信芯片13实现与总线通信,接收外部流量给定指令;
53.步骤2:单片机9从通信芯片13接收外部流量给定指令,将其解算为驱动信号,发送至伺服电机驱动部分的智能伺服电机驱动芯片3,通过控制晶体管4打开或关闭,驱动伺服电机按给定转速工作;
54.步骤3:无接触旋变发送机激励与单机电路15采集燃油流量反馈信号,电阻型温度传感器信号采集电路采集燃油温度反馈信号,霍尔效应管信号倍频芯片采集的伺服电机转速信号,由单片机9接收上述三种反馈信号;
55.步骤4:根据反馈信号及流量给定指令解算转速给定指令,由单片机9通过控制算法完成对伺服电机的闭环控制。
56.本发明所控制的装置为电动燃油泵,采用齿轮泵作为增压部件,通过无刷直流电动机、永磁同步电动机等伺服电机驱动泵工作,结合总线通信、智能控制等技术,实时控制燃油泵转速,形成一种高精度燃油计量与控制结构,可实现对电机转速及燃油流量的闭环控制,提升电动燃油泵输出燃油流量精度,减轻中央控制器的功能、性能负担,为发动机燃油控制系统的分布式控制提供了可能。同时,本发明使得燃油控制系统中无需附加独立燃油计量设备,有效简化了燃油控制系统的结构及控制难度,相对于现有技术具有实质性的技术特点和显著的技术进步。
57.相对于现有技术,本发明的控制方法在燃油控制方面的优势在于:
58.1)对无接触旋变发送机激励与采集电路15采集的数据进行了自适应rc滤波算法,使得流量换算数据在稳态下具有很高的稳定性(实际测量波动在0.15%以下),从而提高燃油流量控制精度,达到给定值的
±
1%;
59.2)控制算法中增加了抗积分饱和处理,提高了控制的精度;通过合理的处理,将稳态控制算法与加、减速控制算法结合,在保证快速性的同时,提高稳态控制精度,燃油流量超调量不大于给定值的
±
1%,燃油流量震荡不大于1.5次。
60.实施例2
61.该实施例与实施例1原理及结构类似,只是在输出燃油流量反馈环节,使用压差流量计及压差信号采集电路,代替无接触旋变发送机及其激励、采集电路。该方案以压差信号代替位移信号向单片机反馈输出燃油流量,同样可实现对电机转速及燃油流量的闭环控
制,提升电动燃油泵输出燃油流量精度。