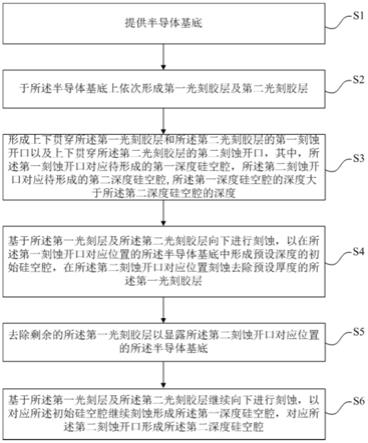
1.本发明涉及半导体封装领域,特别是一种微系统模组不同深度硅空腔的一次刻蚀方法。
背景技术:2.随着硅基微机电(mems)和射频硅通孔(rf tsv)工艺技术的发展,三维异构集成微系统技术成为下一代军用高集成电子系统技术发展重要方向。三维异构集成是将不同尺寸质地的芯片埋入硅基衬底上的硅空腔通过后布线技术扇出,再通过硅通孔来实现高密度集成的集成方法。
3.但是,随着硅转接板上集成度越来越高功能越来越多,一个硅转接板上只内埋同一种芯片(即一种厚度的芯片)已经无法满足其集成度要求。故需要在同一个硅转接板上制作不同芯片的内埋空腔,即在在同一个硅转接板上制作不同深度的硅空腔。然而,现有的不同深度硅空腔的刻蚀往往容易对空腔形貌造成影响,其工艺往往比较复杂,也会存在造成晶圆制造的工艺设备场所浪费时间减少工作效率以及晶圆容易受到污染等问题。
4.因此,如何提供一种微系统模组不同深度硅空腔的一次刻蚀方法以解决现有技术中的上述问题实属必要。
技术实现要素:5.鉴于以上所述现有技术的缺点,本发明的目的在于提供一种微系统模组不同深度硅空腔的一次刻蚀方法,用于解决现有不同深度硅空腔的刻蚀的过程中对刻蚀空腔形貌造成影响以及工艺浪费污染等问题。
6.为实现上述目的及其他相关目的,本发明提供一种微系统模组不同深度硅空腔的一次刻蚀方法,包括如下步骤:
7.提供半导体基底;
8.于所述半导体基底上依次形成第一光刻胶层及第二光刻胶层;
9.形成上下贯穿所述第一光刻胶层和所述第二光刻胶层的第一刻蚀开口以及上下贯穿所述第二光刻胶层的第二刻蚀开口,其中,所述第一刻蚀开口对应待形成的第一深度硅空腔,所述第二刻蚀开口对应待形成的第二深度硅空腔,所述第一深度硅空腔的深度大于所述第二深度硅空腔的深度;
10.基于所述第一光刻层及所述第二光刻胶层向下进行刻蚀,以在所述第一刻蚀开口对应位置的所述半导体基底中形成预设深度的初始硅空腔,在所述第二刻蚀开口对应位置刻蚀去除预设厚度的所述第一光刻胶层;
11.去除剩余的所述第一光刻胶层以显露所述第二刻蚀开口对应位置的所述半导体基底;
12.基于所述第一光刻层及所述第二光刻胶层继续向下进行刻蚀,以对应所述初始硅空腔继续刻蚀形成所述第一深度硅空腔,对应所述第二刻蚀开口形成所述第二深度硅空
腔。
13.可选地,形成所述第一光刻胶层之后还包括对所述第一光刻胶层进行温度介于85℃-135℃之间及时间介于2min-10min之间的软烘烤的步骤。
14.可选地,形成所述第二光刻胶层之后还包括对所述第二光刻胶层及所述第一光刻胶层进行温度介于85℃-135℃之间及时间介于2min-10min之间的软烘烤的步骤。
15.可选地,所述第一光刻胶层的厚度介于1-100μm之间;所述第二光刻胶层的厚度介于1-100μm之间。
16.可选地,形成所述第一刻蚀开口及所述第二刻蚀开口的步骤包括:
17.采用第一光刻工艺于所述第二光刻胶层中形成第一开口及第二开口,所述第二开口构成所述第二刻蚀开口;
18.采用第二光刻工艺对应所述第一开口于所述第一开口下方的所述第一光刻胶层中形成第三开口,所述第一开口与所述第三开口构成所述第一刻蚀开口。
19.可选地,所述第一光刻工艺包括第一曝光及第一显影的工艺;所述第二光刻工艺包括第二曝光及第二显影的工艺,其中,所述第二曝光之后包括步骤:进行温度介于50℃-100℃之间及时间介于1min-30min之间的烘烤;所述第二显影之后包括步骤:进行温度介于50℃-150℃之间及时间介于0.5h-1.5h之间的硬烘烤。
20.可选地,形成所述第一刻蚀开口及所述第二刻蚀开口的步骤包括:
21.对所述第二光刻胶层进行第三曝光工艺,于所述第二光刻胶层中形成第一曝光区及第二曝光区,其中,所述第一曝光区对应所述第一刻蚀开口的位置,所述第二曝光区对应所述第二刻蚀开口的位置;
22.对所述第二光刻胶层及所述第一光刻胶层进行第四曝光工艺,于所述第一光刻胶层中形成第三曝光区,所述第三曝光区与所述第一曝光区上下对应;
23.进行温度介于50℃-100℃之间及时间介于1min-30min之间的后烘烤;
24.对所述第一光刻胶层及所述第二光刻胶层进行第三显影工艺,以对应所述第一曝光区和所述第三曝光区形成所述第一刻蚀开口,对应所述第二曝光区形成所述第二刻蚀开口;
25.进行温度介于50℃-150℃之间及时间介于0.5h-1.5h之间的硬烘烤。
26.可选地,形成所述第一刻蚀开口及所述第二刻蚀开口的步骤包括:
27.a)采用第三光刻工艺于所述第二光刻胶层中形成第四开口,所述第四开口构成所述第二刻蚀开口;
28.b)通过第四光刻工艺于所述第二光刻胶层及所述第一光刻胶层中形成上下贯穿的第五开口,所述第五开口构成所述第一刻蚀开口;
29.其中,步骤a)先于步骤b)进行或者步骤b)先于步骤a)进行。
30.可选地,所述第三光刻工艺包括第五曝光及第四显影的工艺;所述第四光刻工艺包括第六曝光及第五显影的工艺,其中,所述第六曝光之后包括步骤:进行温度介于50℃-100℃之间及时间介于1min-30min之间的后烘烤;所述第五显影之后包括步骤:进行温度介于50℃-150℃之间及时间介于0.5h-1.5h之间的硬烘烤。
31.可选地,形成所述第一刻蚀开口及所述第二刻蚀开口的步骤包括:
32.c)对所述第二光刻胶层进行第七曝光工艺,于所述第二光刻胶层中形成第四曝光
区,其中,所述第四曝光区对应所述第二刻蚀开口的位置;
33.d)对所述第二光刻胶层及所述第一光刻胶层进行第八曝光工艺,于所述第一光刻胶层及所述第二光刻胶层中形成上下贯穿的第五曝光区,其中,所述第五曝光区对应所述第一刻蚀开口的位置;其中,步骤c)先于步骤d)进行或者步骤d)先于步骤c)进行;
34.e)进行温度介于50℃-100℃之间及时间介于1min-30min之间的后烘烤;
35.f)对所述第一光刻胶层及所述第二光刻胶层进行第六显影工艺,以对应所述第四曝光区形成所述第二刻蚀开口,对应所述第五曝光区形成所述第一刻蚀开口;
36.g)进行温度介于50℃-150℃之间及时间介于0.5h-1.5h之间的硬烘烤。
37.可选地,所述预设深度介于50-150μm之间;所述预设厚度大于所述第一光刻胶层厚度的3/5。
38.可选地,所述第一深度硅空腔的深度介于200μm-350μm之间,所述第二深度硅空腔的深度介于100μm-200μm之间。
39.如上所述,本发明的微系统模组不同深度硅空腔的一次刻蚀方法,通过形成上下两层光刻胶层,即第一光刻胶层及第二光刻胶层,在一次刻蚀之前形成所有不同深度空腔的光刻胶图形,刻蚀过程中,通过更换刻蚀气氛与刻蚀能量等实现上一个深度的硅空腔刻蚀与下一个深度硅空腔刻蚀前表面光胶的清洗,从而实现不同深度硅空腔的一次刻蚀,避免了深硅空腔上涂胶时光刻胶覆盖性差的问题,同时也提高了工作效率,减少污染。
附图说明
40.图1显示为本发明实施例中微系统模组不同深度硅空腔的一次刻蚀方法的流程图。
41.图2显示为本发明实施例中不同深度硅空腔一次刻蚀方法中提供半导体基底的示意图。
42.图3显示为本发明实施例中不同深度硅空腔一次刻蚀方法中形成第一光刻胶层的图示。
43.图4显示为本发明实施例中不同深度硅空腔一次刻蚀方法中形成第二光刻胶层的图示。
44.图5显示为本发明实施例中不同深度硅空腔一次刻蚀方法中形成第一刻蚀开口及第二刻蚀开口的结构示意图。
45.图6显示为本发明实施例中不同深度硅空腔一次刻蚀方法形成第一刻蚀开口及第二刻蚀开口的一种示例中形成第一开口和第二开口的结构示意图。
46.图7显示为对应图6的示例中形成第三开口的结构示意图。
47.图8显示为本发明实施例中不同深度硅空腔一次刻蚀方法形成第一刻蚀开口及第二刻蚀开口的另外一种示例中形成第四开口的结构示意图。
48.图9显示为对应图6的示例中形成第五开口的结构示意图。
49.图10显示为本发明实施例中不同深度硅空腔一次刻蚀方法中形成初始硅空腔的示意图。
50.图11显示为本发明实施例中不同深度硅空腔一次刻蚀方法中去除剩余第一光刻胶层的结构示意图。
51.图12显示为本发明实施例中不同深度硅空腔一次刻蚀方法中形成第一深度硅空腔及第二深度硅空腔的结构示意图。
52.图13显示为本发明实施例中不同深度硅空腔一次刻蚀方法中去除光刻胶层的示意图。
53.图14显示为本发明对比例中不同深度硅空腔刻蚀各步骤的结构示意图。
54.元件标号说明
55.100
ꢀꢀꢀꢀꢀꢀꢀꢀꢀꢀꢀꢀꢀꢀꢀꢀꢀꢀꢀꢀ
半导体基底
56.101
ꢀꢀꢀꢀꢀꢀꢀꢀꢀꢀꢀꢀꢀꢀꢀꢀꢀꢀꢀꢀ
第一光刻胶层
57.102
ꢀꢀꢀꢀꢀꢀꢀꢀꢀꢀꢀꢀꢀꢀꢀꢀꢀꢀꢀꢀ
第二光刻胶层
58.103
ꢀꢀꢀꢀꢀꢀꢀꢀꢀꢀꢀꢀꢀꢀꢀꢀꢀꢀꢀꢀ
第一刻蚀开口
59.104
ꢀꢀꢀꢀꢀꢀꢀꢀꢀꢀꢀꢀꢀꢀꢀꢀꢀꢀꢀꢀ
第二刻蚀开口
60.105
ꢀꢀꢀꢀꢀꢀꢀꢀꢀꢀꢀꢀꢀꢀꢀꢀꢀꢀꢀꢀ
第一开口
61.106
ꢀꢀꢀꢀꢀꢀꢀꢀꢀꢀꢀꢀꢀꢀꢀꢀꢀꢀꢀꢀ
第二开口
62.107
ꢀꢀꢀꢀꢀꢀꢀꢀꢀꢀꢀꢀꢀꢀꢀꢀꢀꢀꢀꢀ
第三开口
63.108
ꢀꢀꢀꢀꢀꢀꢀꢀꢀꢀꢀꢀꢀꢀꢀꢀꢀꢀꢀꢀ
第四开口
64.109
ꢀꢀꢀꢀꢀꢀꢀꢀꢀꢀꢀꢀꢀꢀꢀꢀꢀꢀꢀꢀ
第五开口
65.110
ꢀꢀꢀꢀꢀꢀꢀꢀꢀꢀꢀꢀꢀꢀꢀꢀꢀꢀꢀꢀ
初始硅空腔
66.111
ꢀꢀꢀꢀꢀꢀꢀꢀꢀꢀꢀꢀꢀꢀꢀꢀꢀꢀꢀꢀ
剩余第一光刻机层
67.112
ꢀꢀꢀꢀꢀꢀꢀꢀꢀꢀꢀꢀꢀꢀꢀꢀꢀꢀꢀꢀ
第六开口
68.113
ꢀꢀꢀꢀꢀꢀꢀꢀꢀꢀꢀꢀꢀꢀꢀꢀꢀꢀꢀꢀ
第一深度硅空腔
69.114
ꢀꢀꢀꢀꢀꢀꢀꢀꢀꢀꢀꢀꢀꢀꢀꢀꢀꢀꢀꢀ
第二深度硅空腔
70.200
ꢀꢀꢀꢀꢀꢀꢀꢀꢀꢀꢀꢀꢀꢀꢀꢀꢀꢀꢀꢀ
第一掩膜版
71.201
ꢀꢀꢀꢀꢀꢀꢀꢀꢀꢀꢀꢀꢀꢀꢀꢀꢀꢀꢀꢀ
第二掩膜版
72.202
ꢀꢀꢀꢀꢀꢀꢀꢀꢀꢀꢀꢀꢀꢀꢀꢀꢀꢀꢀꢀ
第三掩膜版
73.203
ꢀꢀꢀꢀꢀꢀꢀꢀꢀꢀꢀꢀꢀꢀꢀꢀꢀꢀꢀꢀ
第四掩膜版
74.300
ꢀꢀꢀꢀꢀꢀꢀꢀꢀꢀꢀꢀꢀꢀꢀꢀꢀꢀꢀꢀ
硅基底
75.301
ꢀꢀꢀꢀꢀꢀꢀꢀꢀꢀꢀꢀꢀꢀꢀꢀꢀꢀꢀꢀ
光刻胶
76.302
ꢀꢀꢀꢀꢀꢀꢀꢀꢀꢀꢀꢀꢀꢀꢀꢀꢀꢀꢀꢀ
第二个深度的硅空腔
77.303
ꢀꢀꢀꢀꢀꢀꢀꢀꢀꢀꢀꢀꢀꢀꢀꢀꢀꢀꢀꢀ
第一个深度的硅空腔
78.304
ꢀꢀꢀꢀꢀꢀꢀꢀꢀꢀꢀꢀꢀꢀꢀꢀꢀꢀꢀꢀ
坏点
79.s1~s6
ꢀꢀꢀꢀꢀꢀꢀꢀꢀꢀꢀꢀꢀꢀꢀꢀꢀ
步骤
具体实施方式
80.以下通过特定的具体实例说明本发明的实施方式,本领域技术人员可由本说明书所揭露的内容轻易地了解本发明的其他优点与功效。本发明还可以通过另外不同的具体实施方式加以实施或应用,本说明书中的各项细节也可以基于不同观点与应用,在没有背离本发明的精神下进行各种修饰或改变。
81.如在详述本发明实施例时,为便于说明,表示器件结构的剖面图会不依一般比例作局部放大,而且所述示意图只是示例,其在此不应限制本发明保护的范围。此外,在实际
制作中应包含长度、宽度及深度的三维空间尺寸。
82.为了方便描述,此处可能使用诸如“之下”、“下方”、“低于”、“下面”、“上方”、“上”等的空间关系词语来描述附图中所示的一个元件或特征与其他元件或特征的关系。将理解到,这些空间关系词语意图包含使用中或操作中的器件的、除了附图中描绘的方向之外的其他方向。此外,当一层被称为在两层“之间”时,它可以是所述两层之间仅有的层,或者也可以存在一个或多个介于其间的层。
83.在本技术的上下文中,所描述的第一特征在第二特征“之上”的结构可以包括第一和第二特征形成为直接接触的实施例,也可以包括另外的特征形成在第一和第二特征之间的实施例,这样第一和第二特征可能不是直接接触。
84.需要说明的是,本实施例中所提供的图示仅以示意方式说明本发明的基本构想,遂图示中仅显示与本发明中有关的组件而非按照实际实施时的组件数目、形状及尺寸绘制,其实际实施时各组件的型态、数量及比例可为一种随意的改变,其组件布局形态也可能更为复杂。
85.如图1所示,本发明提供一种微系统模组不同深度硅空腔的一次刻蚀方法,包括如下步骤:
86.s1:提供半导体基底;
87.s2:于所述半导体基底上依次形成第一光刻胶层及第二光刻胶层;
88.s3:形成上下贯穿所述第一光刻胶层和所述第二光刻胶层的第一刻蚀开口以及上下贯穿所述第二光刻胶层的第二刻蚀开口,其中,所述第一刻蚀开口对应待形成的第一深度硅空腔,所述第二刻蚀开口对应待形成的第二深度硅空腔,所述第一深度硅空腔的深度大于所述第二深度硅空腔的深度;
89.s4:基于所述第一光刻层及所述第二光刻胶层向下进行刻蚀,以在所述第一刻蚀开口对应位置的所述半导体基底中形成预设深度的初始硅空腔,在所述第二刻蚀开口对应位置刻蚀去除预设厚度的所述第二光刻胶层;
90.s5:去除剩余的所述第二光刻胶层显露所述第二刻蚀开口对应位置的所述半导体基底;
91.s6:基于所述第一光刻层及所述第二光刻胶层继续向下进行刻蚀,以对应所述初始硅空腔继续刻蚀形成所述第一深度硅空腔,对应所述第二刻蚀开口形成所述第二深度硅空腔。
92.下面将结合附图详细说明本发明的微系统模组不同深度硅空腔的一次刻蚀方法,其中,需要说明的是,上述顺序并不严格代表本发明微系统模组不同深度硅空腔的一次刻蚀方法步骤的顺序,本领域技术人员可以依据实际工艺步骤进行改变,图1仅示出了一种示例中的微系统模组不同深度硅空腔的一次刻蚀方法的步骤。
93.如图1中的s1及图2所示,首先进行步骤s1,提供半导体基底100。所述半导体基底100为需要形成不同深度凹槽的结构,可以是本发明中所指的需要形成不同深度空腔的结构,如需要形成不同深度硅空腔。其中,所述半导体基底100可以是单层材料层结构,也可以是由多层材料层构成的叠层结构。本示例中,所述半导体基底100选择为硅衬底。当然,在其他示例中,也可以是绝缘体上硅(soi)等,并不以此为限。
94.如图1中的s2及图3-4所示,接着进行步骤s2,于所述半导体基底100上依次形成第
一光刻胶层101及第二光刻胶层102。其中,所述第一光刻胶层101可以为正胶,也可以为负胶,所述第二光刻胶层102可以为正胶,也可以为负胶。另外,在一示例中,所述第一光刻胶层101的材料与所述第二光刻胶层102的材料可以为同种光刻胶也,可为不同种类的光刻胶。其中,可以采用现有工艺形成所述第一光刻胶层101及第二光刻胶层102。本示例中,所述第一光刻胶层101及所述第二光刻胶层102选择为相同种类,均为正胶。其中,这里本领域技术人员可以理解的是,为了达到需要的刻蚀效果,两层光刻胶的刻蚀选择比的差异与两层光刻胶的厚度任意实现,例如,可以通过改变光刻胶种类,材料成分,型号或者是两层光刻胶的烘烤时间、温度实现基于二者进行刻蚀过程中的刻蚀特征。
95.作为示例,所述第一光刻胶层101的厚度介于1-100μm之间,可以是2μm、20μm、50μm;所述第二光刻胶层102的厚度介于1-100μm之间,可以是50μm、60μm、80μm。
96.作为示例,形成所述第一光刻胶层101之后还包括对所述第一光刻胶层101进行温度介于85℃-135℃之间及时间介于2min-10min之间的软烘烤的步骤。在一示例中,形成第一光刻胶层101(下光刻胶层)之后的所述软烘烤的温度可以是90℃、100℃、105℃、110℃,所述软烘烤的时间可以是3min、5min、6min、8min。
97.作为示例,形成所述第二光刻胶层102之后还包括对所述第二光刻胶层102及所述第一光刻胶层101进行温度介于85℃-135℃之间及时间介于2min-10min之间的软烘烤的步骤。在一示例中,形成第二光刻胶层102(上光刻胶层)之后的所述软烘烤的温度可以是90℃、100℃、105℃、110℃,所述软烘烤的时间可以是3min、5min、6min、8min。
98.如图1中的s3及图5-9所示,接着进行步骤s3,形成上下贯穿所述第一光刻胶层101和所述第二光刻胶层102的第一刻蚀开口103以及上下贯穿所述第二光刻胶层102的第二刻蚀开口104,其中,所述第一刻蚀开口103对应待形成的第一深度硅空腔,所述第二刻蚀开口104对应待形成的第二深度硅空腔。
99.通过上述工艺,本发明在一次刻蚀之前通过不同的光刻胶层(如所述第一光刻胶层101及所述第二光刻胶层102)形成所有不同深度空腔的图形,如形成后续第一深度硅空腔113和第二深度硅空腔114的光刻胶图形,当然,也可以在所述第一光刻胶层101及所述第二光刻胶层102中形成其他深度的硅空腔的刻蚀开口。从而可以基于上述图形,通过后续一次刻蚀的工艺同时形成不同深度的硅空腔。
100.如图6-7所示,提供一种形成所述第一刻蚀开口103及所述第二刻蚀开口104的示例,具体形成工艺的步骤包括:
101.首先,如图6所示,采用第一光刻工艺于所述第二光刻胶层102中形成第一开口105及第二开口106,所述第二开口106构成所述第二刻蚀开口104,所述第一光刻工艺可以基于第一掩膜版200得到。
102.在一可选示例中,所述第一光刻工艺包括第一曝光及第一显影的工艺,即,形成上下两层光刻胶层之后,首先通过半曝光(所述第一曝光及所述第一显影)工艺,同时半曝光两个不同深度空腔上方的光刻胶,形成第一开口105及第二开口106。其中,所述第一光刻工艺可以在所述第一掩膜版200下进行。
103.接着,如图7所示,采用第二光刻工艺对应所述第一开口105,于所述第一开口105正下方的所述第一光刻胶层101中形成第三开口107,所述第一开口105与所述第三开口107构成所述第一刻蚀开口103。
104.在一可选示例中,所述第二光刻工艺包括第二曝光及第二显影的工艺,即,经过所述第一光刻工艺之后,再通过过曝光(所述第二曝光及第二显影)工艺,曝光先刻蚀的深度较大的空腔上方的光刻胶(所述第一光刻胶层),使其完全显影出来形成5所示的结构。其中,所述第二曝光之后包括步骤:进行温度介于50℃-100℃之间及时间介于1min-30min之间的烘烤,烘烤的温度可以是60℃、70℃、80℃、9℃,烘烤的时间可以是10min、15min、20min、25min;在另一示例中,所述第二显影之后包括步骤:进行温度介于50℃-150℃之间及时间介于0.5h-1.5h之间的硬烘烤,烘烤的温度可以是90℃、100℃、105℃、110℃,烘烤的时间可以是0.8h、1h、1.2、1.3h。其中,所述第二光刻工艺可以在所述第二掩膜版201下进行。
105.参考图6-7,提供另外一种形成所述第一刻蚀开口103及所述第二刻蚀开口104的方法,其具体步骤包括:
106.首先,对所述第二光刻胶层102进行第三曝光工艺,于所述第二光刻胶层102中形成第一曝光区及第二曝光区(图中未示出),其中,所述第一曝光区对应所述第一刻蚀开口103的位置,所述第二曝光区对应所述第二刻蚀开口104的位置。
107.接着,对所述第二光刻胶层102及所述第一光刻胶层101进行第四曝光工艺,于所述第一光刻胶层101中形成第三曝光区(图中未示出),所述第三曝光区与所述第一曝光区上下对应;即,在第一次曝光(所述第三曝光工艺)之后不进行显影直接进行第二次过曝光(所述第四曝光工艺)。
108.接着,在两次曝光完之后,进行温度介于50℃-100℃之间及时间介于1min-30min之间的后烘烤;烘烤的温度可以是60℃、70℃、80℃、9℃,烘烤的时间可以是10min、15min、20min、25min。
109.接着,对所述第一光刻胶层101及所述第二光刻胶层102进行第三显影工艺,即,在两次曝光之后进行后烘烤,在后烘烤之后进行显影(所述第三显影),以对应所述第一曝光区和所述第三曝光区形成第一刻蚀开口103,对应所述第二曝光区形成第二刻蚀开口104;
110.最后,显影(所述第三显影)之后,进行温度介于50℃-150℃之间及时间介于0.5h-1.5h之间的硬烘烤;烘烤的温度可以是90℃、100℃、105℃、110℃,烘烤的时间可以是0.8h、1h、1.2、1.3h。
111.如图8-9所示,本发明还提供再一种形成所述第一刻蚀开口103及所述第二刻蚀开口104的示例,具体形成步骤包括:
112.首先,如图8所示,进行步骤a),采用第三光刻工艺于所述第二光刻胶层中形成第四开口108,所述第四开口108构成所述第二刻蚀开口104。
113.作为示例,所述第三光刻工艺包括第五曝光及第四显影的工艺,即,首先通过半曝光工艺(所述第五曝光工艺及所述第四显影工艺)曝光得到后刻蚀的深度较小的空腔(所述第二深度硅空腔)的光刻胶图形。其中,所述第三光刻工艺可以在所述第三掩膜版202下进行。
114.接着,如图9所示,进行步骤b),通过第四光刻工艺于所述第二光刻胶层102及所述第一光刻胶层101中形成上下贯穿的第五开口109,所述第五开口109构成所述第一刻蚀开口103;其中,所述第四光刻工艺可以在所述第四掩膜版203下进行。
115.作为示例,所述第四光刻工艺包括第六曝光及第五显影的工艺,即,再通过过曝光
工艺(所述第六曝光工艺及所述第五显影工艺),曝光并完全显影出先刻蚀的深度较大的空腔(所述第一深度硅空腔)的光刻胶图形,其中,所述第六曝光之后包括步骤:进行温度介于50℃-100℃之间及时间介于1min-30min之间的后烘烤,其中,烘烤的温度可以是60℃、70℃、80℃、9℃,烘烤的时间可以是10min、15min、20min、25min;所述第五显影之后包括步骤:进行温度介于50℃-150℃之间及时间介于0.5h-1.5h之间的硬烘烤,其中,烘烤的温度可以是90℃、100℃、105℃、110℃,烘烤的时间可以是0.8h、1h、1.2、1.3h。
116.其中,步骤a)先于步骤b)进行或者步骤b)先于步骤a)进行。即,可以是先形成深度较小的所述第二深度硅空腔的光刻胶图形,也可以是先形成深度较大的所述第一深度硅空腔的光刻胶图形。
117.参考图8-9,本发明还提供又一种形成所述第一刻蚀开口103及所述第二刻蚀开口104的示例,具体的步骤包括:
118.首先,进行步骤c),对所述第二光刻胶层102进行第七曝光工艺,于所述第二光刻胶层102中形成第四曝光区(图中未示出),其中,所述第四曝光区对应所述第二刻蚀开口104的位置;
119.接着,进行步骤d),对所述第二光刻胶层102及所述第一光刻胶层101进行第八曝光工艺,于所述第一光刻胶层101及所述第二光刻胶层102中形成上下贯穿的第五曝光区(图中未显示),其中,所述第五曝光区对应所述第一刻蚀开口103的位置;即,在第一次半曝光(所述第七曝光工艺)之后不进行显影直接进行第二次过曝光(所述第八曝光工艺)。
120.其中,步骤c)先于步骤d)进行或者步骤d)先于步骤c)进行;即,可以是先形成深度较小的所述第二深度硅空腔的光刻胶图形的曝光图形,也可以是先形成深度较大的所述第一深度硅空腔的光刻胶图形的曝光图形。
121.接着,进行步骤e),在进行完上述两个图形的曝光这一步骤之后,进行温度介于50℃-100℃之间及时间介于1min-30min之间的后烘烤;其中,烘烤的温度可以是60℃、70℃、80℃、9℃,烘烤的时间可以是10min、15min、20min、25min。
122.接着,进行步骤f),后烘烤之后,对所述第一光刻胶层101及所述第二光刻胶层102进行第六显影工艺,以对应所述第四曝光区形成所述第二刻蚀开口104,对应所述第五曝光区形成所述第一刻蚀开口103;同时对两种空腔对应的图形进行显影。
123.最后,进行步骤g),进行温度介于50℃-150℃之间及时间介于0.5h-1.5h之间的硬烘烤,烘烤的温度可以是90℃、100℃、105℃、110℃,烘烤的时间可以是0.8h、1h、1.2、1.3h。
124.如图1中的s4及图10所示,进行步骤s4,基于上述光刻后的所述第一光刻层101及所述第二光刻胶层102向下进行刻蚀,以在所述第一刻蚀开口103对应位置的所述半导体基底100中形成预设深度d1的初始硅空腔110,在所述第二刻蚀开口104对应位置刻蚀去除预设厚度h的所述第一光刻胶层101。
125.该步骤中,对应深度较大的所述第一深度硅空腔首先形成所述初始硅空腔110,作为示例,所述预设深度d1介于50-150μm之间,可以是80μm、100μm、120μm。在此过程中,同时,由于刻蚀作用使得小空腔上方的半曝光残留下来的下层光刻胶(所述第一光刻胶层)也几乎全部刻蚀掉,得到剩余第一光刻胶层111,作为示例,所述预设厚度h大于所述第一光刻胶层101厚度的3/5,可以是4/5,当然,所述预设厚度也可以依据实际选择为其他值,以达到理想的刻蚀效果。此处刻蚀方法可选用干法刻蚀也可以选用湿法刻蚀。该步骤中,基于之前步
骤在第一光刻胶层101和第二光刻胶层102中形成的刻蚀图形进行刻蚀,使得刻蚀掉预设深度的半导体基底100的同时去除大部分第一光刻胶层101,这一过程可以通过刻蚀过程中选择比实现,例如,可以在所述半导体基底100及所述第一光刻胶层101的材料选定的情况下,选择合适的刻蚀气氛以及对应设计所述第一光刻胶层101的厚度实现;另外,还可以通过控制所述第一光刻胶层101在形成过程以及曝光显影过程中控制烘烤的温度和时间等控制材料层的刻蚀特征;此外还可以通过改变第二光刻胶的种类(比如不同材料成分不同型号的光刻胶)从而可以或本发明所需要特征的光刻胶层。本领域技术人员可以理解到此处刻蚀硅的气氛(或药液)对两层光刻胶刻蚀选择比的差异、两层光刻胶的厚度以及大空腔所刻蚀的深度可任意调整以达到理想的刻蚀效果。
126.如图1中的s5及图11所示,进行步骤s5,去除剩余的所述第一光刻胶层(即,所述剩余第一光刻胶层111),以显露所述第二刻蚀开口104对应位置的所述半导体基底100,形成第六开口112,使得所述第六开口112位置半导体基底100的表面清洁。该步骤中,在上一步刻蚀形成所述初始硅空腔110之后更换刻蚀腔体内的反应气氛(或者刻蚀药液),使得后刻蚀空腔上方残余的光刻胶(所述剩余第一光刻胶层111)完全清理干净,下层硅基体(所述半导体基底100)暴露出来。此处去除残余光刻胶(所述剩余第一光刻胶层111)的方法可以是干法清洗去除也可以是湿法清洗去除。即,该步骤中,可以基于剩余第一光刻胶层111的材料特性与半导体基底100的材料特性选择合适的刻蚀气氛,从而可以去除所述剩余第一光刻胶层111,保证不会吃掉初始空腔中的半导体基底,可以通过更换刻蚀气氛、刻蚀能量等实现上一个深度的硅空腔刻蚀与下一个深度硅空腔刻蚀前表面光胶的清洗。进一步,该步骤后,可以使得需要进一步刻蚀位置的半导体基底100表面不存在光刻胶。本领域技术人员可以理解到此处清洗残余光刻胶的气氛(或药液)对两层光刻胶刻蚀选择比的差异与两层光刻胶的厚度可任意调整以达到理想的清洗去除效果。
127.如图1中的s6及图12-13所示,进行步骤s6,基于所述第一光刻层101及所述第二光刻胶层102继续向下进行刻蚀,以对应所述初始硅空腔110继续刻蚀形成所述第一深度硅空腔113,对应所述第二刻蚀开口104形成所述第二深度硅空腔114。
128.该步骤中,最终在所述半导体基底100中形成不同深度的所述第一深度硅空腔113及所述第二深度硅空腔114,可选地,所述第一深度硅空腔113的深度d3介于200μm-350μm之间,可以是250μm、280μm、300μm;所述第二深度硅空腔114的深度d2介于100μm-200μm之间,可以是50μm、120μm、180μm。在一示例中,如图13所示,还包括最后再去除光刻胶(所述第一光刻胶层101及所述第二光刻胶层102)形成同时含有两个不同深度硅空腔的晶圆,此处刻蚀方法可选用干法刻蚀也可以选用湿法刻蚀。
129.另外,如图14所示,本发明还提供一种对比例,该对比例中,在硅基底300中制作不同深度的硅空腔的方法为两步刻蚀法,即涂胶曝光显影形成一个深度硅腔的图形刻蚀出来后去除光刻胶,之后再涂覆一层光刻胶301,并曝光显影出另一个深度硅腔的图形并刻蚀出来。由于在深硅空腔上涂胶时光刻胶覆盖性差的问题,这种现有的方法在第二次涂覆光刻胶301时无法将第一次刻蚀出来的硅空腔第一个深度的硅空腔303完全覆盖,如图14(a)所示,从而会导致刻蚀第二个深度的硅空腔302时,之前刻好的硅空腔303形貌被破坏掉,形成坏点304,如图14(b)和图14(c)所示。而且两步刻蚀方法牵涉到涂胶曝光
--
刻蚀
--
再涂胶曝光
--
再刻蚀的过程,由于光刻与刻蚀是在不同的工艺设备内,故如此反复的晶圆制造的工
艺设备场所会浪费时间减少工作效率,晶圆也容易在交换设备的过程中受到污染。通过本发明的方案,通过涂覆两层刻蚀选择不同、厚度不同的光刻胶(第一光刻胶层及第二光刻胶层)以及半曝光或过曝光等不同的曝光工艺来实现在一次刻蚀之前形成所有不同深度空腔的图形(第一刻蚀开口及第二刻蚀开口)。通过更换等离子体刻蚀气氛与刻蚀气体的能量来实现上一个深度的硅空腔(如所述第一深度硅空腔)刻蚀与下一个深度硅空腔(如所述第二深度硅空腔)刻蚀前表面光胶的清洗。从而实现不同深度硅空腔(所述第一深度硅空腔及所述第二深度硅空腔)的一次刻蚀,避免了深硅空腔(所述第一深度硅空腔)上涂胶时光刻胶覆盖性差的问题,同时也提高了工作效率。
130.综上所述,本发明的通过形成上下两层光刻胶层,即第一光刻胶层及第二光刻胶层,在一次刻蚀之前形成所有不同深度空腔的光刻胶图形,刻蚀过程中,通过更换刻蚀气氛与刻蚀能量等实现上一个深度的硅空腔刻蚀与下一个深度硅空腔刻蚀前表面光胶的清洗,从而实现不同深度硅空腔的一次刻蚀,避免了深硅空腔上涂胶时光刻胶覆盖性差的问题,同时也提高了工作效率,减少污染。本发明有效克服了现有技术中的种种缺点而具高度产业利用价值。
131.上述实施例仅例示性说明本发明的原理及其功效,而非用于限制本发明。任何熟悉此技术的人士皆可在不违背本发明的精神及范畴下,对上述实施例进行修饰或改变。因此,举凡所属技术领域中具有通常知识者在未脱离本发明所揭示的精神与技术思想下所完成的一切等效修饰或改变,仍应由本发明的权利要求所涵盖。