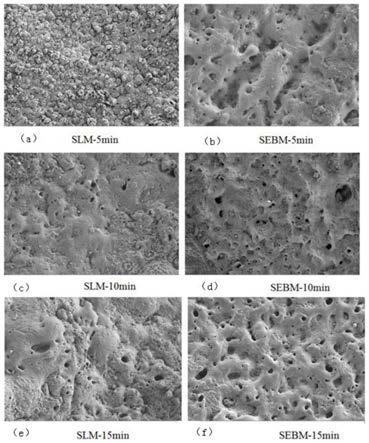
1.本发明属于增材制造表面处理技术领域,涉及一种钛合金高致密度微弧氧化膜层的制备方法。
背景技术:2.增材制造(additive manufacture,am)技术具有不需模具、设计与制造自由度大、原料可重复利用无浪费、快速成形复杂形状零件等独特优势。该技术在制造理念和模式上的创新成为引领科技创新和产业变革的关键技术之一,在航空航天,生物医疗和汽车制造等多个领域快速发展。目前,主要的金属am材料有ti64、316l不锈钢、al10simg和inconel718等,其中ti64合金是研究最多、最深入的一种合金。ti64合金具有低密度,高强度,优异的耐腐蚀性能、生物相容性和综合力学性能,采用增材制造技术可直接制备力学性能优异的钛合金零件,实现快速制造的目的。
3.然而,am技术独特的“快热快冷”的热历史使得零部件显微组织紊乱,通过后续热处理可改善;其次是凝固过程中零部件形成的内部缺陷,可通过工艺参数优化及热等静压(heat isostatic pressing,hip)处理解决;最后是零部件的表面缺陷,这主要是由于表面未熔粉末粘附和计算机模型与切片策略之间的不匹配形成的台阶效应。表面缺陷导致零件的疲劳和耐腐蚀性能远不能达到工业化应用的需求。这些表面缺陷使应力在缺陷处集中,诱发裂纹源萌生,降低材料的疲劳强度,同时导致缺陷处的应力腐蚀,使得材料过早失效。因此,需要进行后处理技术以改善am技术制备零件的表面质量。
4.目前,对于形状简单、规则的板状和块状试样,可采用常规的表面处理方法如车削加工;而对于具有内、外表面的复杂结构,采用化学或电化学抛光处理具有很多缺点:1)削弱了表层厚度(去除0.5mm),不适用于薄壁件(≤5mm)的表面处理;2)化学药品会在样品晶界处残留,削弱了晶界,进一步弱化零件力学性能;3)化学腐蚀剂对环境不友好。因此,需要寻找既是一种环境友好型的、又能针对am技术制备的复杂结构零件进行高效且方便的表面处理的技术,如微弧氧化(micro
‑
arc oxidation,mao)技术。
5.mao技术可在基体表面原位生长出以基体金属氧化物为主的陶瓷膜层,膜层的厚度和形貌均可控;同时基体与陶瓷膜之间形成冶金结合,结合力强。本发明以am技术两种典型的激光选区熔化(laser selective melting,slm)和电子束选区熔化(electron beam selective melting,sebm)技术制备的ti64合金为研究对象,通过sem(scanning electron microscope)对膜层表面形貌进行表征。在此基础上,进一步研究了膜层的腐蚀行为,拓宽了mao技术的应用领域,为am技术的进一步应用提供理论支撑。
技术实现要素:6.本发明的目的是提供一种钛合金高致密度微弧氧化膜层的制备方法,通过微弧氧化技术,在恒压和恒流模式下对slm与sebm技术制备的ti64进行微弧氧化表面处理,通过在表面制备高致密度的tio2陶瓷膜层,来提升零件的耐腐蚀性能。
7.本发明所采用的技术方案是,一种钛合金高致密度微弧氧化膜层的制备方法,具体按以下步骤实施:
8.步骤1,首先采用slm和sebm设备制备钛合金板状工件;
9.步骤2,将步骤1制备的钛合金板状工件在恒压、恒流模式下进行微弧氧化表面处理,得到钛合金高致密度微弧氧化膜层。
10.本发明的特点还在于:
11.其中步骤1中钛合金粉末为ti64;
12.其中步骤1中slm设备型号为mlabcusing r,其参数设置为:基板的预热温度为180℃~200℃,激光功率100w,光斑直径45μm,铺粉层厚25μm,扫描速度1500mm/s;
13.sebm设备型号为arcam a2,其参数设置为:基板的预热温度为730℃,电子束功率50
‑
3500w连续可调,光斑直径100μm,铺粉层厚50μm,扫描速度500mm/s;
14.其中步骤2中微弧氧化设备为mao75
‑ⅲ
型微机自动控制设备;
15.其中步骤2中微弧氧化处理的具体过程是:电解液为na2sio3体系溶液,ti64合金试样作为阳极,不锈钢板作为阴极,通过在阴极和阳极之间施加电压,在金属基体表面产生等离子体进而形成与基体冶金结合的陶瓷膜层,得到了一种高致密度的tio2陶瓷膜层,并对膜层进行了耐腐蚀性能测试;
16.其中na2sio3体系电解液的具体配方为:2%na2sio3、0.4%koh和1%(napo3)6;
17.其中步骤2中微弧氧化技术分别在恒压和恒流模式下进行对ti64试样进行表面处理,恒流模式的具体参数为:电流密度1.5a/cm2,时间为5min,10min和15min;恒压模式的具体参数为:时间5min,电压400v,420v,450v;
18.其中耐腐蚀性能测试的腐蚀液为3.5%nacl溶液,极化曲线数据的拟合采用cview软件,得出试样的腐蚀电流密度icorr和腐蚀电位ecorr。
19.本发明的有益效果是:
20.本发明提供了一种钛合金高致密度微弧氧化膜层的制备方法,增材制造技术制备出的钛合金试样具有严重的表面缺陷,在外力的作用下,裂纹源会在缺陷处产生,降低疲劳性能和耐腐蚀性能;通过微弧氧化技术在ti64基体表面生成均匀致密的tio2陶瓷膜层,改善表面缺陷并提高了基体的耐腐蚀性能。
附图说明
21.图1为本发明的一种钛合金高致密度微弧氧化膜层的制备方法中slm和sebm试样在恒流模式下形成微弧氧化膜层的表面形貌;
22.图2为本发明的一种钛合金高致密度微弧氧化膜层的制备方法中slm试样在恒流模式下形成微弧氧化膜层的极化曲线;
23.图3为本发明的一种钛合金高致密度微弧氧化膜层的制备方法中sebm试样在恒流模式下形成微弧氧化膜层的极化曲线;
24.图4为本发明的一种钛合金高致密度微弧氧化膜层的制备方法中slm和sebm试样在恒压模式下形成微弧氧化膜层的表面形貌;
25.图5为本发明的一种钛合金高致密度微弧氧化膜层的制备方法中slm试样在恒压模式下形成微弧氧化膜层的极化曲线;
26.图6为本发明的一种钛合金高致密度微弧氧化膜层的制备方法中sebm试样在恒压模式下形成微弧氧化膜层的极化曲线。
具体实施方式
27.下面结合附图和具体实施方式对本发明进行详细说明。
28.本发明中,由于slm和sebm技术制备的ti64零件存在未熔粉末粘附和台阶效应的表面缺陷,因而采用微弧氧化使得表面粘附粉末氧化形成陶瓷层的同时,还能够同时大幅度提高其耐腐蚀性能,使得材料的综合性能优异,从而使得slm和sebm技术制备的钛合金材料的应用范围更加广泛;
29.本发明提供一种钛合金高致密度微弧氧化膜层的制备方法,具体按以下步骤实施:
30.步骤1,分别采用激光选区熔化和电子束选区熔化技术制备沉积态ti64工件,成型的方法为:首先通过solidworks软件进行三维实体建模,将文件导入magics软件进行分层切片和添加支撑,接着导出工件和支撑的stl格式文件;然后导入设备的计算机系统内,进行打印参数设置;将粒径分布为45~106μm的超低间隙球形ti64粉末置于3d打印设备的供粉仓中,当抽真空至5
×
10
‑3pa时开始进行工件打印,制备出沉积态ti64工件;
31.slm设备采用德国的concept laser公司的mlabcusing r型激光金属增材制造设备,其设备参数为:基板的预热温度为180℃~200℃,激光功率100w,光斑直径45μm,铺粉层厚25μm,扫描间距为25μm,扫描速度1500mm/s;
32.sebm设备采用瑞典arcam公司的arcam a2型电子束金属增材制造设备,其设备参数为:基板的预热温度为730℃,激光功率50
‑
3500w连续可调,光斑直径100μm,铺粉层厚50μm,扫描间距为80μm,扫描速度500mm/s;
33.步骤2,将经步骤1得到的沉积态ti64工件分别在恒压和恒流模式下进行对ti64试样进行微弧氧化表面处理,恒流模式的具体参数为:电流密度1.5a/cm2,时间为5min,10min和15min;恒压模式的具体参数为:时间5min,电压400v,420v,450v;处理的具体过程是:na2sio3体系溶液为电解液(2%na2sio3、0.4%koh和1%(napo3)6),ti64合金工件作为阳极,不锈钢板作为阴极,通过在阴极和阳极之间施加电压,在金属基体表面产生等离子体,进而形成与基体冶金结合的高致密度tio2陶瓷膜层;
34.步骤3,将经步骤2恒流模式得到的ti64试样进行表面3d形貌观察,如图1所示;
35.步骤4,将步骤1得到的沉积态ti64试样和经步骤2恒流模式得到的微弧氧化处理后的ti64试样进行电化学腐蚀性能测试,腐蚀液为3.5%的nacl溶液,结果如图2和图3所示;
36.步骤5,将经步骤2恒压模式得到的ti64试样进行表面3d形貌观察,如图4所示;
37.步骤6,将步骤1得到的沉积态ti64试样和经步骤2恒压模式得到的微弧氧化处理后的ti64试样进行电化学腐蚀性能测试,腐蚀液为3.5%的nacl溶液,结果如图5和图6所示;
38.从制备方法与原理解释本发明一种钛合金的高致密度微弧氧化膜层的制方法的优点:微弧氧化技术是通过电参数与电解液的结合在铝、镁和钛等阀金属表面生成以基体金属为主的致密氧化物陶瓷膜层,形成的膜层具有硬度高、耐腐蚀性能强和膜基结合强度
高等优点。
39.实施例1:
40.步骤1,采用激光选区熔化技术制备沉积态ti64块状工件,尺寸为:20mm
×
20mm
×
5mm(长
×
宽
×
高),成形粉末的粒径分布为15~53μm;成形工艺参数为激光功率100w,光斑直径45μm,铺粉层厚25μm,扫描间距为25μm,扫描速度1500mm/s,得到沉积态ti64工件;
41.步骤2,将经步骤1得到的沉积态ti64工件在恒流模式下进行微弧氧化表面处理,电解液为na2sio3体系溶液:2%na2sio3、0.4%koh和1%(napo3)6,脉宽120us,频率500hz,占空比20%,电流密度j=1.5a/cm2,时间5min;
42.步骤3,将经步骤2得到的微弧氧化后的ti64工件进行表面3d形貌观察表面形貌如图1(a)所示;
43.步骤4,将经步骤2制备的微弧氧化膜层的表面膜层致密度测量,结果为90%。
44.步骤5,将经步骤1和步骤2得到的ti64工件进行电化学腐蚀性能测试,极化曲线如图2所示;
45.电化学测试后沉积态试样的icorr=6.212
×
10
‑5a/cm2,ecorr=
‑
0.334v,微弧氧化5min后ti64工件的icorr=2.734
×
10
‑5a/cm2,ecorr=
‑
0.226v(线条slm
‑
5min),通过对比发现,本发明制备的微弧氧化ti64工件与沉积态ti64工件相比,耐腐蚀性能提升。
46.实施例2:
47.步骤1,采用电子束选区熔化技术制备沉积态ti64块状工件,尺寸为:20mm
×
20mm
×
5mm(长
×
宽
×
高),成形粉末的粒径分布为45~106μm。成形工艺参数为激光功率50
‑
3500w连续可调,束斑直径100μm,铺粉层厚50μm,扫描间距为80μm,扫描速度500mm/s,真空度5
×
10
‑3pa,得到沉积态ti64工件;
48.步骤2,将经步骤1得到的沉积态ti64工件在恒流模式下进行微弧氧化表面处理,电解液为na2sio3体系溶液:2%na2sio3、0.4%koh和1%(napo3)6,脉宽120us,频率500hz,占空比20%,电流密度j=1.5a/cm2,时间5min;
49.步骤3,将经步骤2得到的微弧氧化后的ti64工件进行表面3d形貌观察表面形貌如图1(b)所示;
50.步骤4,将经步骤2制备的微弧氧化膜层的表面膜层致密度测量,结果为97.55%;
51.步骤5,将经步骤1和步骤2得到的ti64工件进行电化学腐蚀性能测试,极化曲线如图3所示;
52.电化学测试后沉积态试样的icorr=5.04
×
10
‑5a/cm2,ecorr=
‑
0.249v(线条sebm),微弧氧化5min后ti64工件的icorr=1.76
×
10
‑5a/cm2,ecorr=
‑
0.141v(线条sebm
‑
5min)。通过对比发现,本发明制备的微弧氧化ti64工件与沉积态ti64工件相比,耐腐蚀性能提升。
53.实施例3:
54.步骤1,采用激光选区熔化技术制备沉积态ti64块状工件,尺寸为:20mm
×
20mm
×
5mm(长
×
宽
×
高),成形粉末的粒径分布为15~53μm。成形工艺参数为激光功率100w,光斑直径45μm,铺粉层厚25μm,扫描间距为25μm,扫描速度1500mm/s,得到沉积态ti64工件;
55.步骤2,将经步骤1得到的沉积态ti64工件在恒流模式下进行微弧氧化表面处理,电解液为na2sio3体系溶液:2%na2sio3、0.4%koh和1%(napo3)6,脉宽120us,频率500hz,占
空比20%,电流密度j=1.5a/cm2,时间10min;
56.步骤3,将经步骤2得到的微弧氧化后的ti64工件进行表面3d形貌观察表面形貌如图1(c)所示;
57.步骤4,将经步骤2制备的微弧氧化膜层的表面膜层致密度测量,结果为96.93%;
58.步骤5,将经步骤1和步骤2得到的ti64工件进行电化学腐蚀性能测试,极化曲线如图2所示;
59.电化学测试后沉积态试样的icorr=6.212
×
10
‑5a/cm2,ecorr=
‑
0.334v,微弧氧化10min后ti64工件的icorr=1.918
×
10
‑5a/cm2,ecorr=
‑
0.150v(线条slm
‑
10min)。通过对比发现,本发明制备的微弧氧化ti64工件与沉积态ti64工件相比,耐腐蚀性能提升。
60.实施例4:
61.步骤1,采用电子束选区熔化技术制备沉积态ti64块状工件,尺寸为:20mm
×
20mm
×
5mm(长
×
宽
×
高),成形粉末的粒径分布为45~106μm。成形工艺参数为激光功率50
‑
3500w连续可调,束斑直径100μm,铺粉层厚50μm,扫描间距为80μm,扫描速度500mm/s,真空度5
×
10
‑3pa,得到沉积态ti64工件;
62.步骤2,将经步骤1得到的沉积态ti64工件在恒流模式下进行微弧氧化表面处理,电解液为na2sio3体系溶液:2%na2sio3、0.4%koh和1%(napo3)6,脉宽120us,频率500hz,占空比20%,电流密度j=1.5a/cm2,时间10min;
63.步骤3,将经步骤2得到的微弧氧化后的ti64工件进行表面3d形貌观察表面形貌如图1(d)所示;
64.步骤4,将经步骤2制备的微弧氧化膜层的表面膜层致密度测量,结果为97.88%;
65.步骤5,将经步骤1和步骤2得到的ti64工件进行电化学腐蚀性能测试,极化曲线如图3所示;
66.电化学测试后沉积态试样的icorr=6.212
×
10
‑5a/cm2,ecorr=
‑
0.334v(线条sebm),微弧氧化10min后ti64工件的icorr=4.528
×
10
‑5a/cm2,ecorr=
‑
0.130v(线条sebm
‑
10min)。通过对比发现,本发明制备的微弧氧化ti64工件与沉积态ti64工件相比,耐腐蚀性能提升。
67.实施例5:
68.步骤1,采用激光选区熔化技术制备沉积态ti64块状工件,尺寸为:20mm
×
20mm
×
5mm(长
×
宽
×
高),成形粉末的粒径分布为15~53μm。成形工艺参数为激光功率100w,光斑直径45μm,铺粉层厚25μm,扫描间距为25μm,扫描速度1500mm/s,得到沉积态ti64工件;
69.步骤2,将经步骤1得到的沉积态ti64工件在恒流模式下进行微弧氧化表面处理,电解液为na2sio3体系溶液:2%na2sio3、0.4%koh和1%(napo3)6,脉宽120us,频率500hz,占空比20%,电流密度j=1.5a/cm2,时间15min;
70.步骤3,将经步骤2得到的微弧氧化后的ti64工件进行表面3d形貌观察表面形貌如图1(e)所示;
71.步骤4,将经步骤2制备的微弧氧化膜层的表面膜层致密度测量,结果为97.62%;
72.步骤5,将经步骤1和步骤2得到的ti64工件进行电化学腐蚀性能测试,极化曲线如图2所示;
73.电化学测试后沉积态试样的icorr=5.04
×
10
‑5a/cm2,ecorr=
‑
0.249v,微弧氧化
15min后ti64工件的icorr=1.532
×
10
‑5a/cm2,ecorr=
‑
0.130v(线条slm
‑
15min)。通过对比发现,本发明制备的微弧氧化ti64工件与沉积态ti64工件相比,耐腐蚀性能提升。
74.实施例6:
75.步骤1,采用电子束选区熔化技术制备沉积态ti64块状工件,尺寸为:20mm
×
20mm
×
5mm(长
×
宽
×
高),成形粉末的粒径分布为45~106μm。成形工艺参数为激光功率50
‑
3500w连续可调,束斑直径100μm,铺粉层厚50μm,扫描间距为80μm,扫描速度500mm/s,真空度5
×
10
‑3pa,得到沉积态ti64工件;
76.步骤2,将经步骤1得到的沉积态ti64工件在恒流模式下进行微弧氧化表面处理,电解液为na2sio3体系溶液:2%na2sio3、0.4%koh和1%(napo3)6,脉宽120us,频率500hz,占空比20%,电流密度j=1.5a/cm2,时间15min;
77.步骤3,将经步骤2得到的微弧氧化后的ti64工件进行表面3d形貌观察表面形貌如图1(f)所示;
78.步骤4,将经步骤2制备的微弧氧化膜层的表面膜层致密度测量,结果为96.84%;
79.步骤5,将经步骤1和步骤2得到的ti64工件进行电化学腐蚀性能测试,极化曲线如图3所示;
80.电化学测试后沉积态试样的icorr=5.04
×
10
‑5a/cm2,ecorr=
‑
0.249v(线条sebm),微弧氧化15min后ti64工件的icorr=11.38
×
10
‑5a/cm2,ecorr=
‑
0.118v(线条sebm
‑
15min)。通过对比发现,本发明制备的微弧氧化ti64工件与沉积态ti64工件相比,耐腐蚀性能提升。
81.实施例7:
82.步骤1,采用激光选区熔化技术制备沉积态ti64块状工件,尺寸为:20mm
×
20mm
×
5mm(长
×
宽
×
高),成形粉末的粒径分布为15~53μm。成形工艺参数为激光功率100w,光斑直径45μm,铺粉层厚25μm,扫描间距为25μm,扫描速度1500mm/s,得到沉积态ti64工件;
83.步骤2,将经步骤1得到的沉积态ti64工件在恒压模式下进行微弧氧化表面处理,电解液为na2sio3体系溶液:2%na2sio3、0.4%koh和1%(napo3)6,脉宽120us,频率500hz,占空比20%,电压为400v,时间5min;
84.步骤3,将经步骤2得到的微弧氧化后的ti64工件进行表面3d形貌观察表面形貌如图4(a)所示;
85.步骤4,将经步骤2制备的微弧氧化膜层的表面膜层致密度测量,结果为96.94%;
86.步骤5,将经步骤1和步骤2得到的ti64工件进行电化学腐蚀性能测试,极化曲线如图5所示;
87.电化学测试后沉积态试样的icorr=6.212
×
10
‑5a/cm2,ecorr=
‑
0.150v,400v电压条件下微弧氧化5min后ti64工件的icorr=1.648
×
10
‑5a/cm2,ecorr=
‑
0.148v(线条slm
‑
400v)。通过对比发现,本发明制备的微弧氧化ti64工件与沉积态ti64工件相比,耐腐蚀性能提升。
88.实施例8:
89.步骤1,采用电子束选区熔化技术制备沉积态ti64块状工件,尺寸为:20mm
×
20mm
×
5mm(长
×
宽
×
高),成形粉末的粒径分布为45~106μm。成形工艺参数为激光功率50
‑
3500w连续可调,束斑直径100μm,铺粉层厚50μm,扫描间距为80μm,扫描速度500mm/s,真空
度5
×
10
‑3pa,得到沉积态ti64工件;
90.步骤2,将经步骤1得到的沉积态ti64工件在恒流模式下进行微弧氧化表面处理,电解液为na2sio3体系溶液:2%na2sio3、0.4%koh和1%(napo3)6,脉宽120us,频率500hz,占空比20%,电压为400v,时间5min;
91.步骤3,将经步骤2得到的微弧氧化后的ti64工件进行表面3d形貌观察表面形貌如图4(b)所示;
92.步骤4,将经步骤2制备的微弧氧化膜层的表面膜层致密度测量,结果为97.41%;
93.步骤5,将经步骤1和步骤2得到的ti64工件进行电化学腐蚀性能测试,极化曲线如图6所示;
94.电化学测试后沉积态试样的icorr=5.04
×
10
‑5a/cm2,ecorr=
‑
0.249v(线条sebm),400v电压条件下微弧氧化5min后ti64工件的icorr=2.408
×
10
‑5a/cm2,ecorr=
‑
0.132v(线条sebm
‑
400v)。通过对比发现,本发明制备的微弧氧化ti64工件与沉积态ti64工件相比,耐腐蚀性能提升。
95.实施例9:
96.步骤1,采用激光选区熔化技术制备沉积态ti64块状工件,尺寸为:20mm
×
20mm
×
5mm(长
×
宽
×
高),成形粉末的粒径分布为15~53μm。成形工艺参数为激光功率100w,光斑直径45μm,铺粉层厚25μm,扫描间距为25μm,扫描速度1500mm/s,得到沉积态ti64工件;
97.步骤2,将经步骤1得到的沉积态ti64工件在恒压模式下进行微弧氧化表面处理,电解液为na2sio3体系溶液:2%na2sio3、0.4%koh和1%(napo3)6,脉宽120us,频率500hz,占空比20%,电压为420v,时间5min;
98.步骤3,将经步骤2得到的微弧氧化后的ti64工件进行表面3d形貌观察表面形貌如图4(c)所示;
99.步骤4,将经步骤2制备的微弧氧化膜层的表面膜层致密度测量,结果为97.39%;
100.步骤5,将经步骤1和步骤2得到的ti64工件进行电化学腐蚀性能测试,极化曲线如图5所示;
101.电化学测试后沉积态试样的icorr=6.212
×
10
‑5a/cm2,ecorr=
‑
0.334v,400v电压条件下微弧氧化5min后ti64工件的icorr=1.61
×
10
‑5a/cm2,ecorr=
‑
0.141v(线条slm
‑
420v)。通过对比发现,本发明制备的微弧氧化ti64工件与沉积态ti64工件相比,耐腐蚀性能提升。
102.实施例10:
103.步骤1,采用电子束选区熔化技术制备沉积态ti64块状工件,尺寸为:20mm
×
20mm
×
5mm(长
×
宽
×
高),成形粉末的粒径分布为45~106μm。成形工艺参数为激光功率50
‑
3500w连续可调,束斑直径100μm,铺粉层厚50μm,扫描间距为80μm,扫描速度500mm/s,真空度5
×
10
‑3pa,得到沉积态ti64工件;
104.步骤2,将经步骤1得到的沉积态ti64工件在恒流模式下进行微弧氧化表面处理,电解液为na2sio3体系溶液:2%na2sio3、0.4%koh和1%(napo3)6,脉宽120us,频率500hz,占空比20%,电压为420v,时间5min;
105.步骤3,将经步骤2得到的微弧氧化后的ti64工件进行表面3d形貌观察表面形貌如图4(d)所示;
106.步骤4,将经步骤2制备的微弧氧化膜层的表面膜层致密度测量,结果为97.98%;
107.步骤5,将经步骤1和步骤2得到的ti64工件进行电化学腐蚀性能测试,极化曲线如图6所示;
108.电化学测试后沉积态试样的icorr=5.04
×
10
‑5a/cm2,ecorr=
‑
0.249v(线条sebm),420v电压条件下微弧氧化5min后ti64工件的icorr=1.359
×
10
‑5a/cm2,ecorr=
‑
0.131v(线条sebm
‑
420v)。通过对比发现,本发明制备的微弧氧化ti64工件与沉积态ti64工件相比,耐腐蚀性能提升。
109.实施例11:
110.步骤1,采用激光选区熔化技术制备沉积态ti64块状工件,尺寸为:20mm
×
20mm
×
5mm(长
×
宽
×
高),成形粉末的粒径分布为15~53μm。成形工艺参数为激光功率100w,光斑直径45μm,铺粉层厚25μm,扫描间距为25μm,扫描速度1500mm/s,得到沉积态ti64工件;
111.步骤2,将经步骤1得到的沉积态ti64工件在恒压模式下进行微弧氧化表面处理,电解液为na2sio3体系溶液:2%na2sio3、0.4%koh和1%(napo3)6,脉宽120us,频率500hz,占空比20%,电压为450v,时间5min;
112.步骤3,将经步骤2得到的微弧氧化后的ti64工件进行表面3d形貌观察表面形貌如图4(e)所示;
113.步骤4,将经步骤2制备的微弧氧化膜层的表面膜层致密度测量,结果为97.07%;
114.步骤5,将经步骤1和步骤2得到的ti64工件进行电化学腐蚀性能测试,极化曲线如图5所示;
115.电化学测试后沉积态试样的icorr=6.212
×
10
‑5a/cm2,ecorr=
‑
0.334v,450v电压条件下微弧氧化5min后ti64工件的icorr=1.546
×
10
‑5a/cm2,ecorr=
‑
0.115v(线条slm
‑
450v)。通过对比发现,本发明制备的微弧氧化ti64工件与沉积态ti64工件相比,耐腐蚀性能提升。
116.实施例12:
117.步骤1,采用电子束选区熔化技术制备沉积态ti64块状工件,尺寸为:20mm
×
20mm
×
5mm(长
×
宽
×
高),成形粉末的粒径分布为45~106μm。成形工艺参数为激光功率50
‑
3500w连续可调,束斑直径100μm,铺粉层厚50μm,扫描间距为80μm,扫描速度500mm/s,真空度5
×
10
‑3pa,得到沉积态ti64工件;
118.步骤2,将经步骤1得到的沉积态ti64工件在恒流模式下进行微弧氧化表面处理,电解液为na2sio3体系溶液:2%na2sio3、0.4%koh和1%(napo3)6,脉宽120us,频率500hz,占空比20%,电压为450v,时间5min;
119.步骤3,将经步骤2得到的微弧氧化后的ti64工件进行表面3d形貌观察表面形貌如图4(f)所示;
120.步骤4,将经步骤2制备的微弧氧化膜层的表面膜层致密度测量,结果为96.37%;
121.步骤5,将经步骤1和步骤2得到的ti64工件进行电化学腐蚀性能测试,极化曲线如图6所示;
122.电化学测试后沉积态试样的icorr=5.04
×
10
‑5a/cm2,ecorr=
‑
0.249v(线条sebm),450v电压条件下微弧氧化5min后ti64工件的icorr=11.04
×
10
‑5a/cm2,ecorr=
‑
0.108v(线条sebm
‑
450v)。通过对比发现,本发明制备的微弧氧化ti64工件与沉积态ti64工
件相比,耐腐蚀性能提升。
123.综合上述实施例可以看出,本发明通过采用微弧氧化技术,在恒压和恒流模式下对slm与sebm技术制备的ti64进行微弧氧化表面处理,通过在表面制备高致密度的tio2陶瓷膜层,在本发明中,恒流和恒压模式下均可使得试样表面氧化膜层致密度达97%以上。图1和图3清晰的表明了本发明所采用的电解液与工艺参数可以制的高致密度的微弧氧化膜层,且图2、3和图5、6表明在得到高致密的微弧氧化膜层的同时提高了样品的耐腐蚀性能。