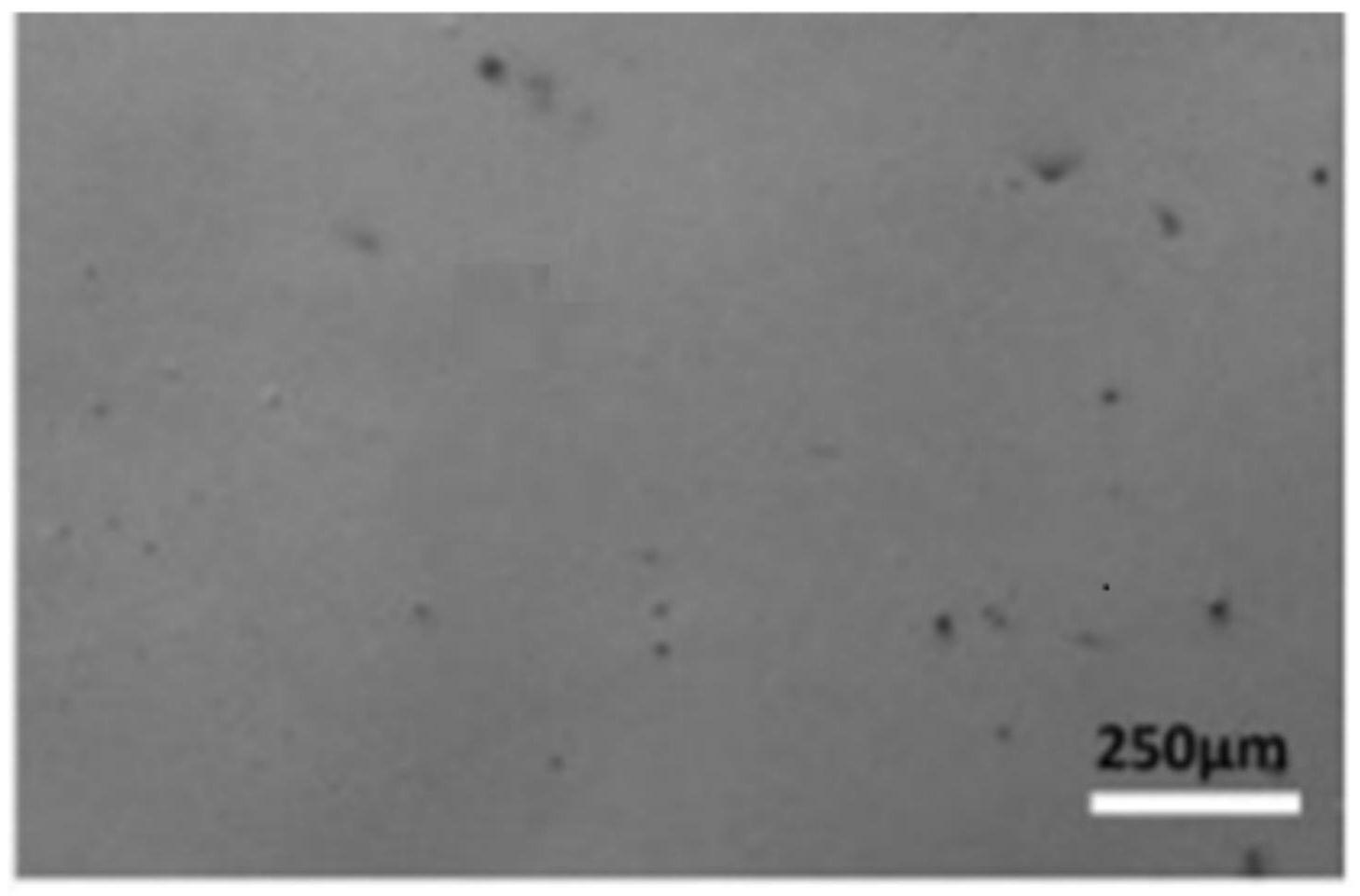
1.本发明属于燃料电池技术领域,涉及一种提高质子交换膜抗氧化自由基降解的方法。
背景技术:2.燃料电池运行过程中,氧气经过膜渗透到阳极侧,在阳极pt及微量过渡金属离子的催化作用下,形成
·
oh和
·
hoo等自由基,
·
oh自由基进攻pbi主链上的含氮基链上的两个端氨基氧化,端羧基发生脱羧反应产生亚苯基自由基。产生的这些自由基会加剧pbi膜的降解,导致电池性能大幅下降。抗自由基氧化稳定性是质子交换膜的又一重要性能,由于自由基氧化而造成质子交换膜的降解劣化是影响燃料电池寿命的重要原因,因此提高质子交换膜的抗自由基氧化稳定性对延长燃料电池使用寿命具有重要意义。研究发现,较高电流密度的工作有利于降低阴极氧浓度、减少阴极自由基形成;氧气在膜中渗透到阳极形成过氧化氢和自由基导致膜在阳极的降解,因此提高膜的致密性或增加膜的厚度有利于减少膜的阳极降解。对于质子交换膜自身来说,在膜中复合具有变价能力的自由基捕获剂以减少双氧水和自由基的浓度,或者消除高分子的末端缺陷基团有利于提高膜的化学耐久性。
3.目前,cn110483822a通过在全氟磺酸膜的一面和或两面分别涂覆一层掺加有添加剂的树脂层以实现提高抗氧化化学稳定性。cn106336518a 提出了一种以聚苯并咪唑为聚合物骨架,磷酸为质子导体,通过将膜内同时掺杂自由基淬灭剂,膜两侧复合含磷酸吸附剂的保护层,有效解决聚苯并咪唑/磷酸类高温质子交换膜因磷酸流失而造成的电导率损失的问题,并同时提升质子交换膜的抗氧化性能,制备具有高抗氧化性能与高电导率的高温质子交换膜。cn110128686a公开了一种具有化学稳定性的质子交换膜的制备方法,通过将聚合物基体材料与含有铁氰配位基团的材料进行物理混合,合用为膜配方,再通过一系列的制膜工序,获得质子交换膜。根据上述现有技术可以得出结论:现有的制备高性能质子交换膜仍然存在工艺过程复杂,原料成本高、耗能大等问题。
技术实现要素:4.本发明的目的是针对现有技术存在的上述问题,提出了一种提高质子交换膜抗氧化自由基降解的方法,通过简单的制备方法制得具有化学稳定性高的质子交换膜。
5.本发明的采用下列技术方案:
6.一种提高质子交换膜抗氧化自由基降解的方法,所述的方法包括以下步骤:将预处理后的玻碳电极和基膜置于电解池中,在三电极系统中循环扫描聚合后得到质子交换膜(pem)。
7.本发明利用现有的基膜,通过三电极体系,将铁氰化物和/或亚铁氰化物基团掺入,使质子交换膜成品具有良好的性能,是对基膜的一种有效改进及再加工。若是在制作基膜的过程中掺入铁氰化物和/或亚铁氰化物基团,成品也能获得相应的性能,但是获得的膜使用范围有限,再加工难度增加,且制备过程工序复杂繁琐。
8.作为优选,所述基膜为全氟磺酸膜。
9.作为优选,所述的质子交换膜厚度为50-55nm。
10.全氟磺酸膜即nafion211膜(购自dupont公司)。将基膜完全浸没在电解液中,使基膜掺杂铁氰化物和/或亚铁氰化物基团,但厚度基本不变。
11.作为优选,所述预处理过程包括:将抛光后的玻碳电极依次用混合溶液超声清洗;然后放入h2so4溶液中进行循环扫描极化处理至循环伏安图稳定后水洗。
12.作为优选,所述抛光过程包括玻碳电极通过金相砂纸和抛光机抛光成镜面。
13.对电极进行抛光能够增加电极表面光滑度,防止因电极表面粗糙不平导致实际电极表面积增大;并且能够清除电极表面杂质。
14.作为优选,所述混合溶液的体积比为hno3:乙醇:纯水=(1.5-3): (0.8-1.5):1。
15.在混合溶液的配比中要注意顺序,先将乙醇和纯水混合均匀,再将硝酸缓慢倒入乙醇和纯水的混合溶液中。
16.作为优选,所述极化处理过程中硫酸的浓度为0.1-0.8mol/l,电压为
ꢀ‑
0.6-2.0v(vs.sce),扫描速度为40-60mv/s,扫描时间为5-20min。
17.极化处理过程在硫酸中扫描可以对电极表面进行清洁,通过cv活化过程发生的氧化还原反应清除电极表面杂质。
18.作为优选,所述电解池中溶液为铁氰化物、亚铁氰化物中的一种或多种,溶液浓度为10-3-10-2
mol/l。
19.进一步优选,铁氰化物包括铁氰化钾、亚铁氰化钾中的一种或多种。
20.作为优选,所述三电极系统中电压为-1.6-2.0v(vs.sce),扫描速度为 50-70mv/s,扫描时间为20-50min。
21.在三电极体系中,基膜作为工作电极,玻碳电极作为对电极,饱和甘汞电极为参比电极。通过亚铁氰化物-铁氰化物的氧化还原循环,亚铁氰化物组分负责减轻自由基对pem的攻击。
22.本发明也提供了一种质子交换膜。
23.本发明的方法制得的质子交换膜通过掺杂铁氰化物和/或亚铁氰化物基团,具有良好的化学稳定性,抗氧化自由基降解性能好,经过芬顿实验后仍能保持完整,表面不发生损坏,不产生气泡。
24.本发明还提供了一种质子交换膜在燃料电池中的应用。
25.燃料电池中的膜电极由质子交换膜、催化剂层、气体扩散层组成,再将膜电极和双极板交替堆叠后组装端板形成电堆;一端为进气端板,一端为承重端板。
26.与现有技术相比,本发明具有以下有益效果:
27.1、本发明制得的质子交换膜不易产生气泡且质量保留率高,具有良好的化学稳定性,抗氧化自由基降解性能好。
28.2、本发明的方法过程简单可控,耗能小,成本低。
29.3、本发明制得的质子交换膜通过掺杂铁氰化物和/或亚铁氰化物基团的方式实现抗氧化自由基降解。
30.4、通过本发明制得的质子交换膜组装而成的燃料电池能量转化效率高、使用寿命长。
31.说明书附图
32.图1为本发明实施例1中制得的质子交换膜的电子扫描电镜图。
33.图2为本发明对比例1中制得的质子交换膜的电子扫描电镜图。
具体实施方式
34.以下是本发明的具体实施例,对本发明的技术方案作进一步的描述,但本发明并不限于这些实施例。
35.获得的质子交换膜需要通过芬顿实验进行性能检测:将制得的产品置于芬顿试剂中进行加速腐蚀处理,48小时后取出清洗干燥。并且称取芬顿实验前后质子交换膜的质量,计算质量保留率。
36.实施例1
37.将抛光后的玻碳电极用体积比为2.1:1.1:1的hno3、乙醇、纯水混合溶液超声清洗15min;然后放入0.5mol/l的h2so4溶液中,在-0.5-1.6v 范围内,50mv/s的扫描速度进行循环扫描极化处理15min至循环伏安图稳定;接着将水洗后的电极和nafion膜移入含有浓度为3
×
10-3
mol/l的的铁氰化钾的电解池中,在三电极系统中,设置电压范围为-1.4-1.8v,以60mv/s 的扫描速度循环扫描聚合30min,得到质子交换膜。获得的质子交换膜通过芬顿实验进行性能检测,用电子扫描显微镜观察质子交换膜表面微观结构,如图1所示可以看到膜表面完整;本实施例中经过处理后的质子交换膜质量保留率为94.64%。
38.实施例2
39.与实施例1相比,区别在于在三电极系统中,设置电压范围为-1.5-1.8v,以50mv/s的扫描速度循环扫描聚合50min。获得的质子交换膜通过芬顿实验进行性能检测,用电子扫描显微镜观察质子交换膜表面微观结构,可以看到膜表面完整;本实施例中经过处理后的质子交换膜质量保留率为 94.78%。
40.实施例3
41.与实施例1相比,区别在于电解池中溶液为亚铁氰化钾。获得的质子交换膜通过芬顿实验进行性能检测,用电子扫描显微镜观察质子交换膜表面微观结构,可以看到膜表面完整;本实施例中经过处理后的质子交换膜质量保留率为94.56%。
42.实施例4
43.与实施例1相比,区别在于玻碳电极不进行预处理,水洗后直接参与三电极反应。获得的质子交换膜通过芬顿实验进行性能检测,用电子扫描显微镜观察质子交换膜表面微观结构,可以看到膜表面出现少量气泡;本实施例中经过处理后的质子交换膜质量保留率为93.49%。
44.实施例5
45.与实施例1相比,与实施例1相比,区别在于在三电极体系中,设置电压范围为-1.6-1.8v,以60mv/s的扫描速度循环扫描聚合15min。获得的质子交换膜通过芬顿实验进行性能检测,用电子扫描显微镜观察质子交换膜表面微观结构,可以看到膜表面出现少量气泡;本实施例中经过处理后的质子交换膜质量保留率为92.58%。
46.对比例1
47.将nafion膜通过芬顿实验进行性能检测,用电子扫描显微镜观察质子交换膜表面
微观结构,如图2所示可以看到膜表面出现部分气泡;本对比例中经过处理后的质子交换膜质量保留率为92.32%。
48.对比例2
49.在制膜的过程中,将铁氰化钾与聚合物基体混合后,通过溶解、静置、成膜、酸化后得到质子交换膜。获得的质子交换膜通过芬顿实验进行性能检测,用电子扫描显微镜观察质子交换膜表面微观结构,可以看到膜表面完整、无气泡;本对比例中处理后的质子交换膜质量保留率为94.06%。
50.综上所述,通过本发明方法制得的质子交换膜表面无破损,说明铁氰化物和/或亚铁氰化物基团可以有效地提高pem的化学稳定性。本发明的方法操作可控、简便,耗能小,成本低;制得的质子交换膜通过实现抗氧化自由基降解,具有良好的化学稳定性。通过本发明制得的质子交换膜组装而成的燃料电池能量转化效率高、使用寿命长。
51.本文中所描述的具体实施例仅仅是对本发明精神作举例说明。本发明所属技术领域的技术人员可以对所描述的具体实施例做各种各样的修改或补充或采用类似的方式替代,但并不会偏离本发明的精神或者超越所附权利要求书所定义的范围。