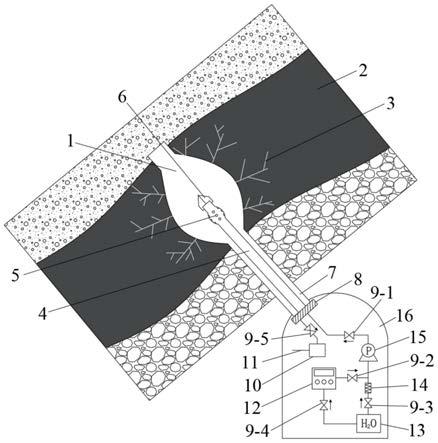
1.本发明属于煤层瓦斯抽采技术领域,具体涉及一种水力冲孔造穴协同蒸汽注入强化瓦斯抽采方法。
背景技术:2.矿井瓦斯是造成煤与瓦斯突出和瓦斯爆炸等灾害的主要因素,严重威胁煤矿的安全生产。煤层瓦斯抽采是消除煤层突出危险性的最直接、最有效的手段。目前,在我国大部分矿井中,应用最广泛的是井下钻孔瓦斯抽采方法,该方法具有成本低、施工灵活、针对性强、效果显著等特点。
3.井下钻孔瓦斯抽采方法主要包括保护层开采、水力压裂、水力割缝、水力冲孔、深孔爆破等。其中,水力冲孔利用高压水射流冲击煤体,使钻孔周围煤体破碎并被高压水冲出,在钻孔周围形成直径较大的孔洞,排出大量瓦斯和煤体,降低钻孔周边煤岩体应力,能大幅提高煤层透气性;此外,该方法还能扩大钻孔有效抽采范围并延长钻孔有效抽采时间,消突效果显著。相对于其他几种方法,水力冲孔具有安全性高、卸压效果好等特点。然而,水力冲孔工程量大,并且煤层中的瓦斯在远离冲孔区域抽采效果不理想,需要在煤层施工较多的钻孔才能有效抽采这些空白带的瓦斯,这进一步增加了工程量。由于煤体瓦斯解吸速度、解吸量与煤体温度密切相关,煤体温度越高,瓦斯解吸速度、解吸量越大。因此,煤层注热能促进瓦斯解吸,强化瓦斯抽采。目前已有的煤体加热方式有红外、微波、射频等非接触式方式,这些方法可快速加热煤体,但具有耗能高、能量衰减速度快、设备易损坏等缺点。近年来行业内提出往煤层注入热水的方法加热煤体,这种方法具有操作简便、耗能低等优势。但是这种方式持续注入一定热水后会堵塞煤层内水力冲孔造穴产生的裂隙,造成“水锁”效应,反而阻碍瓦斯抽采。因此如何能提供一种能有效保证对煤层瓦斯的持续抽采效果,同时降低施工钻孔工作量的方法,是本行业的研究方向。
技术实现要素:4.针对上述现有技术存在的问题,本发明提供一种水力冲孔造穴协同蒸汽注入强化瓦斯抽采方法,能有效提高煤层瓦斯的抽采效果,并持续较长时间,同时降低施工钻孔的工作量。
5.为了实现上述目的,本发明采用的技术方案是:一种水力冲孔造穴协同蒸汽注入强化瓦斯抽采方法,具体步骤为:
6.a、施工穿层钻孔:采用钻冲一体机从岩巷向侧上方的煤层施工穿层钻孔,使钻冲一体机的空心钻杆伸入煤层,直至空心钻杆端部的钻头达到煤层顶板后停止钻进;
7.b、组装水力冲孔及蒸汽压裂系统:将封孔器安装在穿层钻孔的孔口处,对穿层钻孔内部进行密封,然后将增压泵的出口通过管路穿过封孔器与空心钻杆连通,增压泵的进口通过管路分别与蒸汽发生器的出口和热水器的出口连通,水箱通过管路分别与蒸汽发生器的进口和热水器的进口连通,气渣分离器的进口通过管路穿过封孔器与穿层钻孔连通;
气渣分离器的出口与瓦斯抽采管连通;在增压泵与空心钻杆之间的管路上装有第一单向阀,且第一单向阀的进口朝向增压泵;在蒸汽发生器与增压泵之间的管路上装有第二单向阀,且第二单向阀的进口朝向蒸汽发生器;在热水器与水箱之间的管路上装有第三单向阀,且第三单向阀的进口朝向水箱;在蒸汽发生器与水箱之间的管路上装有第四单向阀,且第四单向阀的进口朝向水箱;在气渣分离器与穿层钻孔之间的管路上装有第五单向阀,且第五单向阀的进口朝向穿层钻孔;从而完成水力冲孔及蒸汽压裂系统组装,此时各个单向阀均处于关闭状态;
8.c、施工水力冲孔造穴与瓦斯抽采:打开第一单向阀和第三单向阀,并使热水器和增压泵开始工作,此时水箱内的水经过第三单向阀流入热水器,热水器将水的温度升高至60~80℃,随后水进入增压泵中,经增压泵增压至20~30mpa后经第一单向阀进入空心钻杆,高压水从空心钻杆靠近钻头位置的孔眼处射出,对穿层钻孔周围煤体进行高压水冲击,煤体在高压水压作用下被破碎形成冲孔穴,高压水持续冲击1~1.5h后,关闭第一单向阀和第三单向阀,并停止热水器和增压泵工作,停止冲孔;接着打开第五单向阀,将穿层钻孔内的残渣、废水和已卸压的部分瓦斯气体沿着穿层钻孔排出到气渣分离器中,经过气渣分离器的分离使残渣、废水留在气渣分离器内,已分离的瓦斯气体通过瓦斯抽采管路进行抽采;待穿层钻孔内的残渣、废水排尽后,关闭第五单向阀并拆卸封孔器,完成该位置的冲孔造穴工作;将空心钻杆向孔口方向退钻1~1.5m,然后安装封孔器重复上述冲孔造穴工作,对该位置进行冲孔造穴,如此循环,直至钻头退至距煤层底板0.5~1m后,进行最后一次冲孔造穴工作,最终在煤层中形成直径为0.5~1m的冲孔穴与数条裂缝;完成后通过瓦斯抽采管持续抽采穿层钻孔内的瓦斯;
9.d、蒸汽二次压裂及瓦斯增产:瓦斯抽采10~15小时后,停止抽采并关闭第五单向阀,打开第一单向阀、第二单向阀和第四单向阀,并使蒸汽发生器和增压泵开始工作,此时水箱内的水经过第四单向阀流入蒸汽发生器,蒸汽发生器将水变成100~150℃的饱和蒸汽,饱和蒸汽经第二单向阀被输送至增压泵中,使压力增大到4~6mpa,随后高压蒸汽经第一单向阀从空心钻杆靠近钻头位置的孔眼处喷出,冲孔穴内气压持续升高,高压蒸汽对冲孔穴周围煤层已产生的裂缝施压及加热,煤层裂缝在受到高温和高压力的作用后进一步扩展发育;持续注入高压蒸汽5~8小时后,关闭第一单向阀、第二单向阀和第四单向阀,停止注入蒸汽,并停止蒸汽发生器与增压泵的工作,对冲孔穴进行密封,使高压蒸汽再对冲孔穴周围煤层裂隙进一步施压扩展发育的同时充分加热煤层,煤层温度升高后会降低煤层对瓦斯气体的吸附性,从而在煤层裂缝进一步扩展发育和煤层升温的双重作用下,实现对瓦斯的增产;密封3~5小时后,打开第五单向阀将冲孔穴内的冷凝水排至气渣分离器,同时通过瓦斯抽采管抽采经过气渣分离器分离后的瓦斯;
10.e、监测瓦斯抽采浓度:当抽采出的瓦斯浓度低于15%时,停止瓦斯抽采并关闭第五单向阀,然后重复步骤d,再完成一次瓦斯增产过程,接着继续进行瓦斯抽采工作,并持续监测抽采出的瓦斯浓度,如此重复,直至完成一次瓦斯增产后抽采出的瓦斯浓度仍然低于15%,则完成该穿层钻孔的瓦斯抽采工作;
11.f、施工多个穿层钻孔对煤层进行瓦斯抽采:上述穿层钻孔旁边的煤体再选择一个位置,作为新的穿层钻孔,然后重复步骤a至f,完成该穿层钻孔的瓦斯抽采工作;如此重复,直至完成整个煤层的瓦斯抽采工作。
12.进一步,所述水箱能用井下水管替代。在具有稳定井下水管及水源的矿井中采用水管替代水箱,能持续供水保证施工的持续进行。
13.进一步,所述步骤a中能同时从岩巷向煤层内等间距的施工多个穿层钻孔,然后各个穿层钻孔分别重复步骤b至e,从而同步对整个煤层进行瓦斯抽采工作。采用这种同时并行的方式相比与依次钻孔抽采的方式,能有效缩短对整体煤层的瓦斯抽采时间。
14.与现有技术相比,本发明先向煤层内打设穿层钻孔,并向钻孔内注入高压水进行水力冲孔,从而在穿层钻孔内形成冲孔穴,并且冲孔穴周围的煤体形成数条裂缝,由于注入的高压水的水温为60~80℃,这样在高压水对穿层钻孔进行冲击过程中,也会对煤层进行预热,由于煤层温度会有一定的升高,能降低一些煤层对瓦斯的吸附性,从而增加瓦斯解吸量,同时还能为后续的蒸汽注入时,由于煤体已经具有一定的温度,在高温蒸汽再对煤层进行升温时能降低其热损;然后通过气渣分离器将冲孔穴内的残渣、废水排出并进行瓦斯抽采;瓦斯抽采10~15小时后,再向冲孔穴内注入高温高压蒸汽,高温高压蒸汽进入冲孔穴内后与煤层进行热交换并施加压力,蒸汽进入煤层的裂缝内进一步施加压力,使煤层裂缝在受到高温和高压力的作用后进一步扩展发育实现二次压裂,产生更多裂隙;同时由于蒸汽分子具有很高的能量,能进入煤层产生的微小裂隙内,并与煤进行凝结换热,大幅提高煤层温度,使冲孔卸压范围更远处的煤体温度升高,煤层温度进一步升高后会继续降低煤层对瓦斯的吸附性,从而有效增加瓦斯解吸量;并且由于煤层本身在注入蒸汽之前温度较高,因此蒸汽进入后液化较少,从而提高蒸汽在裂隙内的伸入范围;另外蒸汽的毛细凝聚效应会使其优先在煤层的微小孔内凝结,不会直接凝结在较大的裂隙里,进而不会阻碍已经解析的瓦斯产出;最终在高温水力冲孔和高温高压蒸汽的二次压裂,及煤层升温降低煤层吸附性的多重作用下,实现对瓦斯抽采的增产。另外注入蒸汽后,可大大增加单一水力冲孔钻孔对煤层的泄压及抽采瓦斯的范围,因此能有效增加相邻水力冲孔钻孔之间的施工距离,进而减少钻孔施工数量,减少喷孔、瓦斯超限等问题;并降低施工钻孔的工作量。
附图说明
15.图1是本发明的整体布设示意图;
16.图2是本发明中钻冲一体机的空心钻杆及钻头的结构示意图。
17.图中:1-冲孔穴,2-煤层,3-裂缝,4-空心钻杆,5-孔眼,6-钻头,7-穿层钻孔,8-封孔器,9-1-第一单向阀、9-2-第二单向阀、9-3-第三单向阀、9-4-第四单向阀、9-5-第五单向阀,10-气渣分离器,11-瓦斯抽采管,12-蒸汽发生器,13-水箱,14-热水器,15-增压泵,16-岩巷。
具体实施方式
18.下面将对本发明作进一步说明。
19.如图1所示,本发明的具体步骤为:
20.a、施工穿层钻孔:采用钻冲一体机从岩巷16向侧上方的煤层2施工穿层钻孔7,使钻冲一体机的空心钻杆4伸入煤层2,直至空心钻杆4端部的钻头6达到煤层2顶板后停止钻进;空心钻杆4及钻头6的结构如图2所示;
21.b、组装水力冲孔及蒸汽压裂系统:将封孔器8安装在穿层钻孔7的孔口处,对穿层
钻孔7内部进行密封,然后将增压泵15的出口通过管路穿过封孔器8与空心钻杆4连通,增压泵15的进口通过管路分别与蒸汽发生器12的出口和热水器14的出口连通,水箱13通过管路分别与蒸汽发生器12的进口和热水器14的进口连通,气渣分离器10的进口通过管路穿过封孔器8与穿层钻孔7连通;气渣分离器10的出口与瓦斯抽采管11连通;在增压泵15与空心钻杆4之间的管路上装有第一单向阀9-1,且第一单向阀9-1的进口朝向增压泵15;在蒸汽发生器12与增压泵15之间的管路上装有第二单向阀9-2,且第二单向阀9-2的进口朝向蒸汽发生器12;在热水器14与水箱13之间的管路上装有第三单向阀9-3,且第三单向阀9-3的进口朝向水箱13;在蒸汽发生器12与水箱13之间的管路上装有第四单向阀9-4,且第四单向阀9-4的进口朝向水箱13;在气渣分离器10与穿层钻孔7之间的管路上装有第五单向阀9-5,且第五单向阀9-5的进口朝向穿层钻孔7;从而完成水力冲孔及蒸汽压裂系统组装,此时各个单向阀均处于关闭状态;上述钻冲一体机、封孔器8、气渣分离器10、蒸汽发生器12、热水器14、增压泵15均为现有设备或部件;上述各个单向阀均为带有阀门的单向阀,通过开闭阀门能使单向阀单向流动方向处于开启或关闭状态。
22.c、施工水力冲孔造穴与瓦斯抽采:打开第一单向阀9-1和第三单向阀9-3,并使热水器14和增压泵15开始工作,此时水箱13内的水经过第三单向阀9-3流入热水器14,热水器14将水的温度升高至60~80℃,随后水进入增压泵15中,经增压泵15增压至20~30mpa后经第一单向阀9-1进入空心钻杆4,高压水从空心钻杆4靠近钻头6位置的孔眼5处射出,对穿层钻孔7周围煤体进行高压水冲击,煤体在高压水压作用下被破碎形成冲孔穴1,高压水持续冲击1~1.5h后,关闭第一单向阀9-1和第三单向阀9-3,并停止热水器14和增压泵15工作,停止冲孔;接着打开第五单向阀9-5,将穿层钻孔7内的残渣、废水和已卸压的部分瓦斯气体沿着穿层钻孔7排出到气渣分离器10中,经过气渣分离器10的分离使残渣、废水留在气渣分离器10内,已分离的瓦斯气体通过瓦斯抽采管11进行抽采;待穿层钻孔7内的残渣、废水排尽后,关闭第五单向阀9-5并拆卸封孔器8,完成该位置的冲孔造穴工作;将空心钻杆4向孔口方向退钻1~1.5m,然后安装封孔器8重复上述冲孔造穴工作,对该位置进行冲孔造穴,如此循环,直至钻头6退至距煤层底板0.5~1m后,进行最后一次冲孔造穴工作,最终在煤层2中形成直径为0.5~1m的冲孔穴1与数条裂缝3;完成后通过瓦斯抽采管11持续抽采穿层钻孔7内的瓦斯;
23.d、蒸汽二次压裂及瓦斯增产:瓦斯抽采10~15小时后,停止抽采并关闭第五单向阀9-5,打开第一单向阀9-1、第二单向阀9-2和第四单向阀9-4,并使蒸汽发生器12和增压泵15开始工作,此时水箱13内的水经过第四单向阀9-4流入蒸汽发生器12,蒸汽发生器12将水变成100~150℃的饱和蒸汽,饱和蒸汽经第二单向阀9-2被输送至增压泵15中,使压力增大到4~6mpa,随后高压蒸汽经第一单向阀9-1从空心钻杆4靠近钻头6位置的孔眼5处喷出,冲孔穴1内气压持续升高,高压蒸汽对冲孔穴1周围煤层已产生的裂缝3施压及加热,煤层裂缝3在受到高温和高压力的作用后进一步扩展发育;持续注入高压蒸汽5~8小时后,关闭第一单向阀9-1、第二单向阀9-2和第四单向阀9-4,停止注入蒸汽,并停止蒸汽发生器12与增压泵15的工作,对冲孔穴1进行密封,使高压蒸汽再对冲孔穴1周围煤层裂隙进一步施压扩展发育的同时充分加热煤层2,煤层2温度升高后会降低煤层2对瓦斯气体的吸附性,从而在煤层裂缝3进一步扩展发育和煤层2升温的双重作用下,实现对瓦斯的增产;密封3~5小时后,打开第五单向阀9-5将冲孔穴1内的冷凝水排至气渣分离器10,同时通过瓦斯抽采管11抽采
经过气渣分离器10分离后的瓦斯;
24.e、监测瓦斯抽采浓度:当抽采出的瓦斯浓度低于15%时,停止瓦斯抽采并关闭第五单向阀9-5,然后重复步骤d,再完成一次瓦斯增产过程,接着继续进行瓦斯抽采工作,并持续监测抽采出的瓦斯浓度,如此重复,直至完成一次瓦斯增产后抽采出的瓦斯浓度仍然低于15%,则完成该穿层钻孔7的瓦斯抽采工作;
25.f、施工多个穿层钻孔7对煤层2进行瓦斯抽采:上述穿层钻孔7旁边的煤体再选择一个位置,作为新的穿层钻孔,然后重复步骤a至f,完成该穿层钻孔7的瓦斯抽采工作;如此重复,直至完成整个煤层2的瓦斯抽采工作。
26.作为本发明的一种改进,所述水箱13能用井下水管替代。在具有稳定井下水管及水源的矿井中采用水管替代水箱,能持续供水保证施工的持续进行。
27.作为本发明的另一种改进,所述步骤a中能同时从岩巷16向煤层2内等间距的施工多个穿层钻孔7,然后各个穿层钻孔7分别重复步骤b至e,从而同步对整个煤层2进行瓦斯抽采工作。采用这种同时并行的方式相比与依次钻孔抽采的方式,能有效缩短对整体煤层2的瓦斯抽采时间。
28.以上所述仅是本发明的优选实施方式,应当指出:对于本技术领域的普通技术人员来说,在不脱离本发明原理的前提下,还可以做出若干改进和润饰,这些改进和润饰也应视为本发明的保护范围。