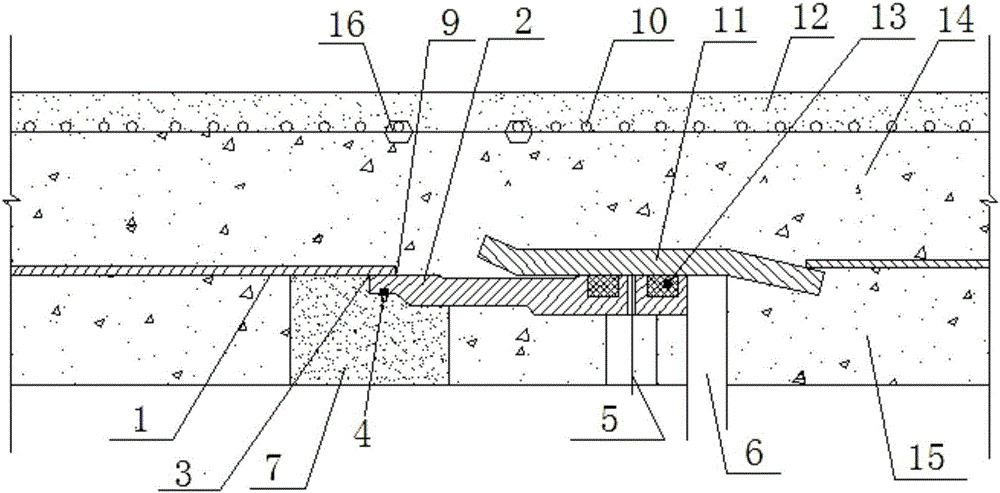
本发明属于管道渗漏处理
技术领域:
,尤其是涉及一种已安装PCCP管道插口环与钢筒焊缝微渗漏处理工艺。
背景技术:
:目前,国内PCCP管道尤其大口径PCCP管道制造及安装工程较多,笔者在从事PCCP管道安装施工过程中发现,部分已安装完管道存在插口环与钢筒焊缝微渗漏现象,因渗漏位置的特殊性,无法直接确定并修复渗漏点,处理难度较大,如二次开挖返工处理,发生费用较多。经过对PCCP管道结构的分析,结合多年施工经验,在不断试验摸索的基础上,总结出了内角焊缝焊接+高压注胶+内缝填充+刮涂聚脲封面的综合处理工艺,经过整体水压试验及长期运行使用验证,该工艺处理后效果非常理想。技术实现要素:有鉴于此,本发明旨在提出一种已安装PCCP管道插口环与钢筒焊缝微渗漏处理工艺,能解决上述技术问题。为达到上述目的,本发明的技术方案是这样实现的:一种已安装PCCP管道插口环与钢筒焊缝微渗漏处理工艺,包括如下步骤:步骤A,确定渗水区段;步骤B,将渗水区段的内层混凝土进行切割并清除;步骤C,清理渗水区段的插口环与钢筒的焊缝间隙灰浆;步骤D,在插口环上渗水区段的靠近两端的位置钻有注浆孔,如渗水区段长度超过500mm,则在两个注浆孔的中间处再增加一个注浆孔,所有注浆孔的钻孔深度穿透插口环钢板,但不破坏钢筒,然后在钻孔内攻丝,选用与螺孔尺寸配套的标准黄油嘴作为注浆针,直接拧入螺孔内;步骤E,将渗水区段上下两端的插口环缝隙及内侧搭接缝使用抗渗剂进行临时封堵;步骤F,验证注浆孔是否连通;步骤G,注浆孔验证结果为连通状态后,剔除内侧搭接缝的临时封堵,然后进行内侧搭接缝内的二次清理,同时将焊接部位打磨除锈,然后将内侧搭接缝进行焊接;步骤H,验证焊接效果;步骤I,通过高压注浆机将浆料注入到注浆孔内;步骤J,内壁衬砌;步骤K,对管道内缝进行清理、打磨,使用双组份聚硫密封胶进行嵌缝,在聚硫密封胶上部填充抗渗剂;步骤L,刮涂聚脲。进一步,所述步骤A中,根据PCCP管道结构图纸,在管道内壁上量出钢筒与插口环内侧搭接部位,在搭接部位处使用水钻钻孔,根据前期出水或钙质析出情况初步判断可能渗水的位置,以管口的截面的竖直直径为中心线划分管左、管右,若初步判断渗水位置在单侧的,单侧钻观察孔;若无法确定渗水位置在哪侧的,先双侧钻观察孔,如一侧观察孔内为干燥状态,则判定渗水位置在另一侧;为减少后期混凝土剔除工作量,采用区段中心取点的方法逐步缩小渗水区段的范围。进一步,所述步骤F中,在管道内靠下方的注浆孔内安装注浆针,使用手动打压泵向靠下方的注浆针注水加压,如相邻注浆孔内出水,说明相互之间连通,依次验证其余注浆孔是否连通。进一步,所述步骤H中,焊接完成后,使用抗渗剂将渗水区段上下两端的插口环缝隙进行二次修补密封,固化后,除打压验证的注浆孔外,其余的注浆孔使用螺栓拧紧封闭,然后使用手动打压泵在打压验证的注浆孔内注水加压,观察角焊缝位置是否有渗水迹象,如果有,二次焊接修补;如果没有,则可进入下道工序施工。进一步,所述步骤I中,把浆料加入高压注浆机的料斗内,将注浆机开关阀组顶端连接口与下部注浆孔的黄油嘴连接,打开高压注浆机开关,缓缓注浆,一次注浆时间不得超过5s,注浆时上部注浆孔暂不安装注浆针,待注浆液从上部注浆孔流出后,下部注浆孔停止注浆,然后上部注浆孔安装黄油嘴;注浆分两遍进行,第二遍注浆在初次注浆固化以后,从上部向下部注浆。进一步,所述步骤J中,注浆完成后,针头不再拆除,已凿除混凝土位置挂网,与原有网片进行连接,内壁修补砂浆,砂浆内掺加8%的抗裂防水剂,压实、抹平,初凝后及时洒水养护。进一步,所述步骤L中,聚脲采用暴露型单组份聚脲防水涂料。进一步,所述步骤L中,包括如下步骤:步骤L1,抗渗剂填缝完成1个半小时后,进行打磨处理,打磨使用角磨机,打磨完成后,使用鼓风机吹净灰尘,并用干抹布擦拭;步骤L2,根据需要处理渗水区段的宽度尺寸,在渗水区段的两侧测量画刻度线,并在刻度线外侧粘贴胶带隔离,胶带与刻度线平行,在胶带范围内均匀涂刷底涂液,底涂液表干时间为3.5~4.5h,表干后进行聚脲涂层涂刷。进一步,所述步骤L2中,涂刷聚脲涂层时使用毛刷,共涂刷三层,涂刷后的聚脲涂层总厚度为1.5~2mm,相邻两次涂刷间隔为1.5小时,在第一层聚脲表干后且在涂刷第二层聚脲前,揭掉两侧的胶带。进一步,所述步骤L2中,底涂液为环氧树脂双组份,双组份包括A组分-界面剂和B组分-固化剂,质量比为A:B=2:1,使用时先将界面剂搅匀,然后加入固化剂再搅拌,均匀后静置3-5分钟可进行施工,并且在半小时内用完。相对于现有技术,本发明所述的已安装PCCP管道插口环与钢筒焊缝微渗漏处理工艺具有以下优势:直接确定并修复PCCP管道的渗漏点,降低处理难度和维修成本,施工效率高,密封效果好,加强防渗处理效果,延长渗漏处理的使用寿命。附图说明构成本发明的一部分的附图用来提供对本发明的进一步理解,本发明的示意性实施例及其说明用于解释本发明,并不构成对本发明的不当限定。在附图中:图1为本发明的原理图;图2为PCCP管道插口环与钢筒焊缝微渗漏处理的结构示意图;图3为渗水区段处理的细部图附图标记说明:1-钢筒;2-插口环;3-内侧搭接缝;4-注浆针;5-打压孔;6-管道内缝;7-渗水区段;8-注浆孔;9-外侧搭接缝;10-预应力钢丝;11-承口钢环;12-保护层;13-橡胶圈;14-外层混凝土;15-内层混凝土;16-预埋锚具。具体实施方式需要说明的是,在不冲突的情况下,本发明中的实施例及实施例中的特征可以相互组合。在本发明的描述中,需要理解的是,术语“中心”、“纵向”、“横向”、“上”、“下”、“前”、“后”、“左”、“右”、“竖直”、“水平”、“顶”、“底”、“内”、“外”等指示的方位或位置关系为基于附图所示的方位或位置关系,仅是为了便于描述本发明和简化描述,而不是指示或暗示所指的装置或元件必须具有特定的方位、以特定的方位构造和操作,因此不能理解为对本发明的限制。此外,术语“第一”、“第二”等仅用于描述目的,而不能理解为指示或暗示相对重要性或者隐含指明所指示的技术特征的数量。由此,限定有“第一”、“第二”等的特征可以明示或者隐含地包括一个或者更多个该特征。在本发明的描述中,除非另有说明,“多个”的含义是两个或两个以上。在本发明的描述中,需要说明的是,除非另有明确的规定和限定,术语“安装”、“相连”、“连接”应做广义理解,例如,可以是固定连接,也可以是可拆卸连接,或一体地连接;可以是机械连接,也可以是电连接;可以是直接相连,也可以通过中间媒介间接相连,可以是两个元件内部的连通。对于本领域的普通技术人员而言,可以通过具体情况理解上述术语在本发明中的具体含义。下面将参考附图并结合实施例来详细说明本发明。PCCP管道包括钢筒1、插口环2、预应力钢丝10、承口钢环11、保护层12、橡胶圈13、外层混凝土14、内层混凝土15和预埋锚具16。插口环2和承口钢环11之间通过橡胶圈13相插接。插口环2和承口钢环11均固定连接于钢筒1。钢筒1与插口环2的连接之间形成内侧搭接缝3和外侧搭接缝9,并均焊接形成角焊缝。问题的判定:PCCP管道插口环与钢筒焊缝出现微渗漏问题的管道接口一般具有以下两方面的明显特征。1、单接口(打压孔5)打压合格,满足设计要求;2、管道插口环2焊缝部位一般会产生一条允许范围内的环向裂缝,如果该管道插口环2与钢筒1焊缝处微渗,初期在环向裂缝部位或内缝砂浆部位出现渗水,长期渗水后会出现白色的钙质析出。需要注意的是,当上述第1条满足后,第2条出现的问题才能判断为插口环2与钢筒1焊缝处微渗。原理:如图1所示,在制造厂区内,钢筒1与插口环2只焊接内侧搭接缝3,我们分析PCCP管道结构后认为,出现上述问题的原因为在制造厂区内焊接的外侧搭接缝9局部存在缺陷,管道安装回填后,管道外侧水压达到一定程度,地下水从焊缝的缺陷部位,沿钢筒1与插口环2的中间空隙进入管道内部,出现渗漏问题。根据上述分析,本工艺的核心原理为:首先判断可能的渗水区段7,将该区段内的内侧搭接缝3焊接,通过注浆针4高压将PU止漏胶注入钢筒1与插口环2的中间空隙部位,PU止漏胶遇水反应后形成弹性的胶体,从而隔断渗水线路,实现渗漏处理。工艺流程:确定渗水区段→内壁混凝土剔除→间隙灰浆清理→插口环钻孔→外侧及端部临时封闭→验证注浆孔是否连通→角焊缝焊接→验证焊接效果→高压注胶→内壁衬砌→填充密封胶、抗渗剂→刮涂聚脲。如图2、3所示,一种已安装PCCP管道插口环与钢筒焊缝微渗漏处理工艺,包括如下步骤:步骤A,确定渗水区段7:根据PCCP管道结构图纸,在管道内壁上量出钢筒1与插口环2内侧搭接部位,在搭接部位处为中心,使用200mm水钻钻孔,根据前期出水或钙质析出情况初步判断可能渗水的位置,以管口的截面的竖直直径为中心线划分管左、管右,若初步判断渗水位置在单侧的,单侧钻观察孔;若无法确定渗水位置在哪侧的,先双侧钻观察孔,如一侧观察孔内为干燥状态,则判定渗水位置在另一侧;为减少后期混凝土剔除工作量,采用区段中心取点的方法逐步缩小渗水区段7的范围。需要注意的是,有极少数情况渗水区段7很难判断,或者渗水区段7较多,这种情况下,我们可以考虑按照500mm的间距均匀钻孔,对管缝进行整体处理。步骤B,将渗水区段7的内层混凝土15进行切割并清除。根据PCCP管道生产图纸及现场已钻出的观察孔,精确定位插口环2与钢筒1搭接处的中心位置,在管道内壁上做出标记。利用原有观察孔,使用金刚锯磨片将渗水区段7内层混凝土15进行切割,宽度为以搭接处为中心100mm。为防止破坏插口环2及钢筒1,切割厚度<200mm,剩余部分采用人工清除。步骤C,清理渗水区段7的插口环2与钢筒1的焊缝间隙灰浆。在PCCP管道内层混凝土15施工过程中,钢筒1与插口环2的内侧搭接缝3的缝隙内进入灰浆。渗水区段7内层混凝土15剔除后,使用订制的薄而坚硬的弯形专用工具人工清理间隙内的灰浆,过程中,使用小锤敲击振动,辅助灰浆清理,直至干净。步骤D,使用手持式电动钻机在插口环2上渗水区段7的靠近两端的位置钻有注浆孔8,如渗水区段7长度超过500mm,则在两个注浆孔8的中间处再增加一个注浆孔8,所有注浆孔8的钻孔深度穿透插口环2钢板,但不破坏钢筒1,然后在钻孔内攻丝,螺孔尺寸与M8螺栓配套,选用与螺孔尺寸配套的M8标准黄油嘴作为注浆针4,直接拧入螺孔内。步骤E,将渗水区段7上下两端的插口环2缝隙及内侧搭接缝3使用抗渗剂进行临时封堵。目的是验证注浆孔8间是否连通。首先将抗渗剂调制成稠状,使用手、小抹子等将其均匀、密实的填充在临时封堵位置。抗渗剂的初凝时间为5min左右,固化速度快,施工效率高,密封效果好。步骤F,验证注浆孔8是否连通:在管道内靠下方的注浆孔8内安装注浆针4,使用手动打压泵向靠下方的注浆针4注水加压,如相邻注浆孔8内出水,说明相互之间连通,依次验证其余注浆孔8是否连通。此验证工序的目的是,确保在后期注浆过程中,注浆通道顺畅,以便注浆密实,效果明显。步骤G,注浆孔8验证结果为连通状态后,剔除内侧搭接缝3的临时封堵,然后使用专用工具进行内侧搭接缝3内的二次清理,同时将焊接部位使用电动钢丝刷打磨除锈,然后将内侧搭接缝3进行焊接。焊接时注意以下几点:1)此焊缝起到密封作用即可,不可过度焊接。2)根据钢筒1及插口环2钢材材质,一般选用J507焊条。3)分2遍焊接成型。4)因为钢筒为薄壁钢板,为防止焊接过程中击穿,采取小电流控制。步骤H,验证焊接效果。焊接完成后,使用抗渗剂将渗水区段7上下两端的插口环2缝隙进行二次修补密封,固化后,除打压验证的注浆孔8外,其余的注浆孔8使用M8螺栓拧紧封闭,然后使用手动打压泵在打压验证的注浆孔8内注水加压,压力控制在0.5MPa以下即可,观察角焊缝位置是否有渗水迹象,如果有,二次焊接修补;如果没有,则可进入下道工序施工。步骤I,通过高压注浆机将浆料注入到注浆孔8内。为确保PU止漏胶注入后形成较密实的状态,准备1台手动打压泵,1台高压注浆机,使用打压泵提前通过黄油嘴注水,注浆机随后注浆,这样能够保证PU止漏胶与水密切接触,有利于在内部缝隙形成良好的状态。注浆顺序为,从偏下侧注浆孔8开始注浆。把浆料加入高压注浆机的料斗内,将注浆机开关阀组顶端连接口与下部注浆孔8的黄油嘴连接,打开高压注浆机开关,缓缓注浆,一次注浆时间不得超过5s,注浆时上部注浆孔8暂不安装注浆针4,待注浆液从上部注浆孔8流出后,下部注浆孔8停止注浆,然后上部注浆孔8安装黄油嘴;注浆时的最大压力控制在2.5MPa以内,不可过高。注浆分两遍进行,第二遍主要作用是在第一遍注浆的基础上补强,PU止漏胶的初固化时间为30min~1h,第二遍注浆在初次注浆固化以后,第二遍注浆从上部向下部注浆。注浆完成后对施工现场进行清理,尤其是擦净表面积水,对管口位置连续观察4-5天,如无继续渗漏迹象,表明处理成功,如出现新的渗漏点,按上述工艺对渗漏点进行处理,直至全部处理完成。步骤J,内壁衬砌。注浆完成后,针头不再拆除,已凿除混凝土位置挂网,与原有网片进行连接,按照管厂内壁修补砂浆要求进行处理,为预防开裂,砂浆内掺加8%的抗裂防水剂,压实、抹平,初凝后及时洒水养护。步骤K,填充密封胶、抗渗剂。对管道内缝6进行清理、打磨,使用双组份聚硫密封胶进行嵌缝,厚度2.5cm,在聚硫密封胶上部填充抗渗剂,要求填充密实、表面平整;步骤L,刮涂聚脲。进行刮涂聚脲施工的目的是,加强防渗处理效果,延长渗漏处理的使用寿命。1)选用材料的特性暴露型单组份聚脲防水涂料,是一种粘稠液体材料,一旦遇到空气则发生化学交连而固化。固化后形成一种聚脲弹性橡胶膜。该材料对混凝土、砂浆等有较好的粘附力。一般情况下,建议使用合适的底涂剂,以使其对基材有更好的粘结性能。材料固化后,其可直接暴露于室外空气中使用,无须保护层。其具有优异的防水性能,表面可供人员维修用通行,但表面不建议有重型车辆碾压。主要物理力学性能见下表。单组份聚脲防水涂料物理力学性能检测项目粘度表干时间比重干燥时间拉伸强度断裂伸长率粘结强度检测结果>3000cps1-3h1±0.1g/cm36-24h>16MPa>350%>2MPa2)施工工艺包括如下步骤:步骤L1,抗渗剂采用抗渗1号,填缝完成1个半小时后,进行打磨处理,打磨使用角磨机,安装金刚锯磨片,对于插口端管芯混凝土有环向裂缝的,打磨宽度需超过裂缝5cm,没有裂缝的管口,打磨宽度为25cm。打磨标准为微露砂粒。打磨完成后,使用鼓风机吹净灰尘,并用干抹布擦拭,确保表面无浮尘;步骤L2,根据需要处理渗水区段7的宽度尺寸,在渗水区段7的两侧测量画刻度线,并在刻度线外侧粘贴胶带隔离,胶带与刻度线平行,在胶带范围内均匀涂刷底涂液,底涂液为环氧树脂双组份,双组份包括A组分-界面剂和B组分-固化剂,A组分为白色粘稠液体,长时间储存后允许有轻微分液,搅拌后可以变为均匀状态。B组份为淡黄色透明粘稠液体。使用时先将A组分搅匀,然后加入B组分再搅拌,质量比为A:B=2:1,均匀后静置3-5分钟可进行施工,并且在半小时内用完。当环境温度低于15℃时,底涂液会变得粘稠,混合前,使用30-40℃热水进行水浴加温。涂刷时,需横向、竖向交替涂刷,尤其是表面的砂眼、裂缝位置,要确保底液涂刷饱满,避免后期产生气泡、裂缝等问题。该底涂液表干时间为4h左右,表干后进行聚脲涂层涂刷。暴露型单组份聚脲防水涂料,在厂内按照工程对固化时间、成膜质量的要求调整完毕,施工现场开封后可直接使用。使用毛刷涂刷聚脲,共涂刷三层,涂刷后聚脲层总厚度要求为1.5~2mm。涂刷原则为先竖向后横向,不得来回涂刷,确保涂刷均匀,避免起包,涂刷时表面如有砂粒等杂质,需将杂质去除后再涂刷。涂刷完成后,首先在管缝中间位置铺贴胎基布,铺贴时2-3人配合作业,务必保证平整,不得出现褶皱、气泡等,铺贴后使用专用刮板从中间分别向上向下刮平,胎基布需要搭接时,搭接长度为100mm。铺贴完成后,在其表面再均匀涂刷一薄层聚脲,目的是保证碳纤维布完全被聚脲涂料浸透,确保整个聚脲涂层的密实性,至此,第一层聚脲涂层施工完毕。该聚脲涂料表干时间为1.5h左右,第一层涂刷完1.5h后可进行第二层涂刷,第二层涂刷完1.5h后可进行第三层涂刷,直至涂刷完成。需注意的问题是,在第一层聚脲表干后且在涂刷第二层聚脲前,粘在两侧的胶带要揭掉,以免后期揭胶带造成涂层两端开口。底涂液及聚脲涂层涂刷后,该管口两侧各20m范围内不得进行管口清理、打磨施工,防止对涂料造成污染。需要说明的是,图2只反应出管道的上半部的截面的结构。如果从工作人员站在管道内部的视角来看,图3也是图2的仰视图。以上所述仅为本发明的较佳实施例而已,并不用以限制本发明,凡在本发明的精神和原则之内,所作的任何修改、等同替换、改进等,均应包含在本发明的保护范围之内。当前第1页1 2 3