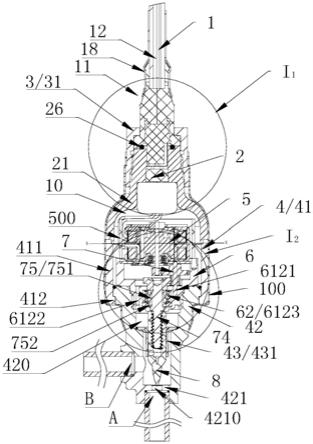
1.本实用新型涉及流体控制技术领域,特别是涉及一种电动控制阀。
背景技术:2.图1所示为背景技术一种电动控制阀的局部结构示意图。该电动控制阀包括丝杆01、输出齿轮03、轴承02、齿轮座04、阀芯部件05、阀体06、电机07、金属底座08和密封圈09。丝杆01能够周向转动,阀芯部件05与丝杆01螺纹连接,阀芯部件05能够在丝杆01的带动下相对于阀体06轴向移动。电机07内置于阀体06内,电机07与齿轮座04固定连接,阀体06与玻璃接线组件的金属底座08铆压固定,并设置图示的密封圈09用于密封。
技术实现要素:3.本技术的目的是提供一种电动控制阀,改善壳体与阀体组件焊接时对电机引线的热影响。
4.本技术提供的一种电动控制阀,包括阀体组件、电机组件,还包括隔离套和壳体,所述隔离套呈筒状,所述隔离套由塑料制成,所述壳体由金属材料制成,所述电机组件设置于所述电动控制阀的阀腔,所述电机组件包括外壳部件和电机引线,所述外壳部件包括引出部,所述电机引线自所述引出部伸出,所述电机引线包括绝缘层和线芯,所述绝缘层包裹所述线芯,所述壳体与所述阀体组件焊接固定,所述壳体与所述阀体组件的焊接部位位于所述隔离套的外侧,所述引出部位于所述隔离套的内侧。
5.该电动控制阀,包括隔离套,所述隔离套由塑料制成,所述壳体与所述阀体组件的焊接部位位于所述隔离套的外侧,所述引出部位于所述隔离套的内侧,改善壳体与阀体组件焊接时对电机引线的热影响。
附图说明
6.图1所示为背景技术一种电动控制阀的局部结构示意图;
7.图2所示为本实用新型电动控制阀的具体实施例-的结构示意图;
8.图3a所示为图2中i2处的局部放大示意图;
9.图3b所示为图2中玻璃座组件2的结构示意图;
10.图3c所示为图2中i1处的细节剖视图;
11.图4所示为图2中卡位器的立体图;
12.图5所示为图2中电机的部分结构示意图;
13.图6所示为图2中下固定组件的结构示意图;
14.图7a所示为图2中电机组件的立体图;
15.图7b所示为图2中电机组件的另一视角下的立体图;
16.图8所示为图2中座体的俯视图;
17.图9所示为图2中座体的一个角度的立体图;
18.图10所示为图2中传动螺纹件的剖视图;
19.图11所示为图2中输出齿轮的立体图;
20.图12所示为图2中阀芯的立体图;
21.图13所示为本实用新型电动控制阀的具体实施例二的结构示意图;
22.图14所示为图13中i3处的局部放大示意图;
23.图15所示为图13中传动螺纹件的结构示意图。
具体实施方式
24.需要先说明的是,本文中若使用方位词,如“上”和“下”等,均是以本文说明书附图中图示位置为基准定义的,应当理解,所述方位词的使用只是为了描述技术方案的清楚及方便,不应当对保护范围构成限制。
25.为了使本技术领域技术人员更好地理解本技术技术方案,下面结合附图和具体实施例对本技术技术方案作进一步的说明。
26.如图2所示,该电动控制阀包括引线组件1、玻璃座组件2、固定螺母3、阀体组件4、电机组件5、支撑座组件6、传动组件7和阀芯部件8。
27.阀体组件4与玻璃座组件2固定连接后形成阀腔10,支撑座组件6、传动组件7 和阀芯部件8内置于阀腔10中。
28.如图2及图3a所示,阀体组件4包括第二阀体41和与第二阀体41焊接固定的第一阀体42、以及内置于第一阀体42内的卡位器43。第二阀体41呈圆筒状,由不锈钢材料制成,其外径大致呈等径设置。第二阀体41包括本体部411和下支撑部412,下支撑部412相对于本体部411的内壁向第二阀体41的中心轴线方向径向延伸,下支撑部412的内径小于本体部411的内径。本体部411与下支撑部412基本呈垂直设置。
29.第一阀体42包括上定位部423,上定位部423包括第一部4231和第二部4232,第一部4231与第二部4232为圆环形,第二部4232的外径小于第一部4231的外径,第二部4232位于第一部4231的下侧。第一部4231的外壁与本体部411的内壁相对,第二部4232的外壁与下支撑部412的内壁相对。如图3所示,上定位部423还包括在第一部4231的上侧的第三部4233,第三部4233的外壁与本体部411的内壁相对设置,第三部4233的外径小于第一部4231的外径。第三部4233与第一部4231及第二阀体41的本体部的内壁形成环形的容纳空间c,该环形的容纳空间c内用于放置焊料对第二阀体41和第一阀体42进行焊接使二者固定连接。
30.第一阀体42具有向第一阀体42的中心轴线方向伸出的圆环形的内凸部421,内凸部421形成有阀口4210。第一阀体42包括第一接口端a和第二接口端b,第一接口端a和第二接口端b二者由阀芯部件8与阀口4210的配合控制连通或断开。
31.如图2、图3a及图4所示,卡位器43呈开口的筒状,卡位器43通过金属板材冲压制成或通过金属粉末冶金制成,其包括筒部431和圆环状的固定部432,其中,筒部431的内壁和外壁的横截面轮廓大致呈四方形,筒部431包括两组相对设置的四个平板部4311,相邻的平板部4311之间分别包括弧形的过渡部4312。第一阀体42的内壁包括台阶面朝上的第一定位台阶部422,卡位器43的固定部432坐落于第一定位台阶部422并与第一定位台阶部422炉焊焊接固定。具体地,卡位器43与第一定位台阶部422焊接固定前,卡位器43可以先通过压装方式压入第一阀体42内,使固定部432座落于第一定位台阶部422,并使卡位器43的过渡部
4312与第一阀体42的内壁配合,使卡位器43与第一阀体42二者预定位,方便二者之间的焊接。
32.如图2和图5
‑
图7a所示,电机组件5内置于阀腔10中,并且,电机组件5与玻璃座组件2电连接。具体地,电机组件5包括外壳部件51、上固定组件、下固定组件、转子部件、与转子部件固定连接的输入齿轮57及3根以上的电机引线58,各电机引线58分别连接有一端子581。转子部件包括转子52、与转子52固定连接的转轴53,上固定组件与外壳部件51的上端固定连接,下固定组件与外壳部件51的下端固定连接。其中,转轴53与转子52注塑固定,转轴53的两端伸出转子52。上固定件组件、下固定组件与外壳部件51共同围成一个电机腔,电机的导磁体等设置于该电机腔内。
33.上固定组件包括上固定件54和上轴承55,上固定件54和外壳部件51由金属材料制成,上固定件54呈板状。上固定件54与外壳部件51通过铆压或焊接固定。上固定件54套设于上轴承55,上轴承55贯穿上固定件54,本实施例中,上轴承55为铜基轴承,上轴承55与上固定件54套接后,二者通过挤压上轴承55的一端使上轴承55与上固定件54铆接固定,上轴承55的内壁与转轴53的外壁间隙配合,上轴承 55用以减少转轴53的上端部的磨损。
34.下固定组件包括下固定件50及与下固定件50固定连接的限位件56,下固定件 50及限位件56由金属板材制成,呈板状。下固定件50与外壳部件51通过点焊或铆接固定,可以采用上固定件54与外壳部件51相同的固定方式,下固定件50与限位件 56焊接或铆接固定。
35.如图5
‑
图7a所示,转子52包括第一套接部522和第二套接部523,转子52包括开口朝向阀口4210侧的圆形的容纳槽521。第一套接部522与第二套接部523均呈圆柱形,第一套接部522的外径大于第二套接部523的外径,第一套接部522和第二套接部523的外壁亦是容纳槽521的壁。
36.下固定件50包括环形的支撑部501、圆筒部502及环形的翻边状部503,从形状上看,翻边状部503自圆筒部502的一端向靠近转轴53的方向径向延伸,支撑部501 自圆筒部502的另一端向远离转轴53的方向径向延伸。翻边状部503和圆筒部502 位于容纳槽521内,翻边状部503套设于第一套接部522的外周并与第一套接部522 间隙配合。
37.第一套接部522与第二套接部523共同形成台阶面520,下固定组件还包括第二轴承59,第二轴承59套设于第二套接部523,则第二轴承59位于容纳槽521中并位于转子52的第二套接部523与下固定件50的圆筒部502之间。
38.如图5所示,第二轴承59具体为滚珠轴承,其包括轴承内圈591、轴承外圈592 位于轴承内圈591与轴承外圈592之间的滚珠593。轴承内圈591与第二套接部523 的外壁固定连接,例如过渡或过盈配合,使轴承内圈591能够与转子部件一起转动。而轴承外圈592不与转子52接触,轴承外圈592在轴向限位于下固定件50的翻边状部503与限位件56之间,限位件56可以在轴向将第二轴承59限位,防止第二轴承59 脱离转子52。
39.进一步地,轴承外圈592的上下两端可以与下固定件50的翻边状部503与限位件56分别抵接。本实施例中,下固定件50、限位件56与转子52三者为第二轴承59 提供了安装空间,转子52与转轴53注塑固定,并设置第二轴承59,当转子52转动时,转子52与转轴53一起转动,转子52带着轴承内圈591同步转动,而轴承外圈592不发生转动,转子52与转轴53二者不发生相对转动,转轴53不受第二轴承59 摩擦,转动摩擦只发生在滚珠593与轴承内圈591及滚珠593与轴承外圈592之间,能够改善电动控制阀的噪音,并改善转轴53的动作寿命。
40.本实施例中,下固定件50的支撑部501呈平板状,下固定件50还包括相对于支撑部501的下表面凸出的若干间隔设置的固定凸筋504。图5所示实施例中,本实施例中,具体地,限位件56大致呈平板状,限位件56包括若干间隔设置的定位孔561,定位孔561的个数与下固定件50的固定凸筋504相对应,各固定凸筋504分别至少部分插入各定位孔561中,通过对各固定凸筋504进行挤压铆接,使限位件56与下固定件50固定连接。固定凸筋504和定位孔561的个数至少分别为两个,使下固定件50与限位件56固定可靠,本实施例中,固定凸筋504和定位孔561的个数分别为三个,作用相当于三点定位,更加稳定。
41.如图2所示,电机组件5的下固定件50坐落于支撑座组件6。其中,支撑座组件 6包括座体61。图8所示为图2中座体61的俯视图,图9所示为图2中座体的立体图。如图3a及图8、图9所示,座体61由黄铜材料制成,座体61呈筒状,其包括安装筒部611和连接部612,其中,安装筒部611包括环形的壁部6111、底部6112,壁部6111的外壁呈多边形设置,便于座体61与第一阀体42安装时的操作。壁部6111 的内壁呈圆形。底部6112与壁部6111大体呈垂直设置,底部6112与连接部612衔接。壁部6111包括朝向电机组件5的外壳部件51的开口部6110,开口部6110包括朝向外壳部件51的支撑面6113。电机组件5的下固定件50与支撑面6113搭接,使座体61支撑电机组件5,并且,座体61的开口部6110与下固定件50的外缘部铆压或焊接固定。
42.如图2、3a
‑
3b所示,连接部612的外壁具有外螺纹,第一阀体42具有内螺纹,座体61与第一阀体42通过前述外螺纹与内螺纹的配合螺纹连接固定,在二者连接过程中,座体61的安装筒部611的壁部6111的外壁作为操作部,便于安装工具操作。
43.支撑座组件6包括座体腔60。传动组件7包括齿轮组和传动螺纹部件。其中,齿轮组包括传动齿轮71和输出齿轮72、齿轮定位轴73。传动齿轮71和输出齿轮72及输入齿轮57位于座体腔60中。
44.如图3a、图7a和图8
‑
9所示,电机组件5的下固定件50包括第一插入部505,本实施例中,第一插入部505为一轴向通孔,座体61的连接部612包括盲孔6121,齿轮定位轴73的一端插入第一插入部505后与转子52下端抵接或不抵接均可,齿轮定位轴73的另一端部插入盲孔6121内并与连接部612压装配合(是过盈、过渡?)。座体61的连接部612还包括与盲孔6121间隔设置的第一轴向通孔6122。座体61与第一阀体42之间包括下腔420,第一轴向通孔6122连通下腔420与座体腔60,更进一步地,在座体61的安装筒部611的侧壁上设置有第二通孔6116。第二通孔6116 连通座体腔60和位于座体61与第二阀体41之间的环形空间e。再进一步地,下固定件50具有第三轴向通道507,上固定件54具有第四轴向通道541。图2所示实施例中,第三轴向通道507为设置于支撑部501上并沿下固定件50轴向贯通的通孔,第四轴向通道541为沿上固定件54的轴向贯通的通孔。此处需要说明的是,第三轴向通道507和第四轴向通道541的形状不限于圆形的通孔,第一轴向通孔6112、第二通孔6116、第三轴向通道507及第四轴向通道541均用于起到压力平衡通道的作用。第三轴向通道507及第四轴向通道541的具体形状不限于通孔形式,只要能实现其目的即可,并且,第一轴向通孔6112、第二通孔6116、第三轴向通道507及第四轴向通道541的个数不作限制,均可以设置为1个或2个以上。
45.传动齿轮71套设在齿轮定位轴73上,输出齿轮72及输入齿轮57分别与传动齿轮71啮合。则通过齿轮定位轴73与电机组件5的座体61的配合,再通过传动齿轮 71与齿轮定位
轴73的配合,使齿轮组与电机组件5和支撑座组件6的位置相对固定。
46.如图2和图3b及图7a、图8所示,座体61的开口部6110的上端还包括第二周向定位部6114,下固定件50还包括第三周向定位部506。具体地,第二周向定位部 6114为一个凹槽,第三周向定位部506为一个位于下固定件50的外缘部的缺口。电机定位轴9部分位于第三周向定位部506,部分位于第二周向定位部6114。电机定位轴9与第二周向定位部6114和第三周向定位部506配合使电机组件5与支撑座组件6 周向相对限位。此外,电机定位轴9与齿轮定位轴73二者共同作用还进一步防止电机组件5相对于支撑座组件6的座体61的转动。
47.如图2及图3a、图10和图11所示,输出齿轮71与传动螺纹部件固定连接,并且输出齿轮71带动传动螺纹部件使传动螺纹部件能够相对于阀体组件4周向转动。传动螺纹部件包括传动螺纹件74和支撑套75。传动螺纹件74由金属材料制成,本实施例中,由不锈钢材料制成,如图所示,传动螺纹件74包括螺纹部741、径向凸出部 742、输出齿轮连接部744和位于输出齿轮连接部744与径向凸出部742之间的圆柱部743。螺纹部741包括外螺纹,用于与阀芯部件8螺纹连接,输出齿轮72的内壁呈非圆形。本实施例中,具体地,输出齿轮连接部744的外壁与输出齿轮72的内壁配合。输出齿轮连接部744包括缺口部7441,输出齿轮72的内壁包括凸部721,输出齿轮72套设至输出齿轮连接部744后,缺口部7441与凸部721卡接,输出齿轮连接部744的上端外翻与输出齿轮72铆接固定,则输出齿轮72能够带动传动螺纹件74同步转动,传动螺纹件74不轴向移动。
48.如图2和图3a所示,传动螺纹件74跟随齿轮组转动,并将齿轮组输出的转动传递为阀芯部件8的轴向移动,从而使阀芯部件8与阀口4210接触或离开以控制电动控制阀的流量。在传动螺纹件74转动过程中,传动螺纹件74的传动可靠性直接影响电动控制阀的动作性能。若传动螺纹件74发生磨损,传动螺纹件74有发生卡死的隐患。为此,如图2和图3a所示,支撑座组件6还包括第一轴承62,第一轴承62包括轴承内圈621、轴承外圈622及设置于轴承内圈621与轴承外圈622之间的滚珠623。连接部612包括轴承安装孔6123和圆环形的第一轴承限位部6124。第一轴承62位于轴承安装孔6123内。第一轴承限位部6124的孔壁与输出齿轮72的外壁间隙配合。
49.传动螺纹部件还包括套设于传动螺纹件74的圆柱部743的支撑套75,支撑套75 通过压装与传动螺纹件74固定连接。支撑套75包括套环部751和第二轴承限位部 752。第二轴承限位部752相对于套环部751径向向外伸出,套环部751与第一轴承 62的轴承内圈621配合,轴承内圈621的两端部分别与输出齿轮712的下端、支撑套 75的第二轴承限位部752抵接。即输出齿轮72和支撑套75将第一轴承62的轴承内圈621压住,使轴承内圈621跟随传动螺纹件74转动。第一轴承62的轴承外圈622 的一端与座体61的第一轴承限位部6124相对设置,轴承外圈622的另一端与支撑座组件6的连接件63接触或间隙配合,轴承外圈622与轴承安装孔6123的孔壁适配。具体地,轴承外圈622与轴承安装孔6123的孔壁可以过盈配合,二者之间也可以间隙配合,传动螺纹件74转动过程中不会受到转动摩擦,防止传动螺纹件74发生卡死现象。这样,如图3a所示,连接件63的作用之一是可以支撑第一轴承62,并间接支撑着输出齿轮72。连接件63由不锈钢材料制成,具体地,连接件63呈具有第一台阶孔630的环形,包括第二限位部631和第一限位部632。座体61的连接部612包括连接件限位部610,本实施例中,连接件限位部610为连接部612的内壁的朝下的台阶面,第二限位部631与连接件限位部610抵接后,座体61的下端与第二限位部631 铆压配合,从而使连接件63、座体61及
第一轴承62限位连接(此处限位连接指连接件63、第一轴承62及座体61三者不脱离,可以三者固定连接,也可以是三者之间相互有适当位移)。在座体61与连接件63连接后,连接件63支撑着第一轴承62的轴承外圈622,轴承内圈621支撑着输出齿轮72,而输出齿轮72又与传动螺纹件74固定连接,则相应地,连接件63也相当于支撑着传动螺纹件74。此处需要说明的是,第二限位部631与连接件限位部610在装配时可以不抵接,但在阀芯81与第一限位部631抵接后,第二限位部631才与连接件限位部610抵接。第一轴承限位部6124 与作为连接件限位部610的台阶面610之间的距离不小于轴承外圈622的上端面与轴承外圈622的下端面之间的距离。目的是,连接件63的主要作用是在阀芯81与第一限位部631抵接后,连接件63受到的阀芯81的作用力传动至座体61,而不传递到第一轴承62,避免第一轴承62因轴承外圈622受力变形而导致第一轴承62失效或性能不良。例如,轴承外圈622受力变形导致其内的滚珠623发生卡死,而使第一轴承62 失效。第一轴承限位部6124与连接部的内壁的朝下的台阶面之间的距离等于轴承外圈622的上端面与轴承外圈622的下端面之间的距离,或第一轴承限位部6124与连接部的内壁的朝下的台阶面之间的距离比轴承外圈622的上端面与轴承外圈622的下端面之间的距离至少大0.01mm。
50.第一限位部632位于支撑套75的第二轴承限位部752的下侧,进一步防止传动螺纹部件74脱离座体61。第一限位部632的内壁与传动螺纹件74的径向凸出部742 的外壁之间具有间隙配合,以使连接件63对传动螺纹件74的转动不产生干涉。
51.图3a所示结构中,需要说明的是,支撑套75的设置,原因之一是由于在产品标准化过程中,传动螺纹件74的圆柱部743的外径尺寸及第一轴承62的轴承内圈621 的内径尺寸限制而设置的。因此,可以理解的是,当传动螺纹件74的尺寸与第一轴承62的轴承内圈621的尺寸相适配时,不设置支撑套75也是可以的。
52.如图2和图3b、图3c所示,玻璃座组件2包括壳体21、限位套22、玻璃座23 和间隔设置的若干玻璃座插针24。各玻璃座插针24与玻璃座23烧结固定。具体地,玻璃座23由玻璃通过烧结方式形成于壳体21内,在该过程中,玻璃座插针24也一并与玻璃座固定连接。玻璃座插针24的个数与电机组件5的端子581的个数相同。壳体21由不锈钢材料制成,壳体21包括罩壳部211和连接筒部212,罩壳部211与第二阀体41激光焊等焊接方式固定。
53.如图2和图7b所示,外壳部件51包括引出部510,引出部510具体为开设于电机外壳51的侧壁的开口,电机引线自引出部510伸出后与玻璃座插针24电连接。电机引线58为三个以上,各电机引线58均包括绝缘层和线芯,绝缘层包裹线芯,本实施例中,电机引线58为4根,如图2、图7a所示,本实施例中,由于壳体21与第二阀体 41均为金属材质,二者激光焊焊接固定,为了避免或者说减小二者焊接时对电机部件 5的若干电机引线58的热影响,电动控制阀还包括隔离套500,隔离套500为圆筒状,由ptfe或具有类似性能的材料制成,隔离套500套设在外壳部件51和上固定组件的外侧,隔离套500的下端可以坐落于下固定件50或座体61的安装筒部611上。引出部510位于隔离套500的内侧。如图2及图7a、图7b所示,在阀体组件4的轴向,第二阀体41与壳体21的焊接部位在电动控制阀的轴向的投影位于外壳部件21的上端与下端之间,隔离套将焊接部位与电机引线隔离,即焊接部位呈环形,定义过焊接部位的横截面为x
‑
x,则横截面x
‑
x与外壳部件51相交。隔离套500设置于电机引线 58与壳体21及电机引线58与第二阀体41之间,隔离套500能够改善壳体21与第二阀体41焊接时对电机引线58的热影响,防止各电机引线58之间因受热导致电机引线58的绝缘层熔化,引起
两个绝缘层内的线芯搭接短路,影响电动控制阀的动作可靠性。
54.连接筒部212的外壁具有外螺纹,在壳体21作为零件时,连接筒部212为轴向贯通结构,玻璃座23由玻璃在连接筒部212的内腔烧结固定形成。各玻璃座插针24 间隔设置并与玻璃座23固定连接,各玻璃座插针24的两端位于玻璃座23外部,即从玻璃座23伸出。限位套22固定在连接筒部212内。限位套22包括与电机组件5 的端子581个数相应的隔离腔,各端子581分别至少部分位于隔离腔中,即每个隔离腔中均设有端子581。各玻璃座插针24的下端分别与一个端子581电连接。各玻璃座插针24的另一端与引线组件1电连接。
55.如图2和图3a、图3b、图3c所示,引线组件1包括保护套11、绝缘套12、连接体13、包封体14、与玻璃座组件2的玻璃座插针24个数相应的引线15、至少部分位于连接体13内的间隔设置的与引线15数目相应的连接体插针17,连接体插针17 与连接体13注塑固定连接为一体。连接体插针17的数量为3个以上。
56.绝缘套12包裹各引线15,且,各引线15的连接端位于绝缘套12外。其中,本实施例中,包括四根引线15和四根连接体插针17。各连接体插针17的一端分别与各相应的引线15的连接端锡焊连接,各连接体插针17的另一端不伸出连接体12,以防在与其它零件装配前碰伤。各引线15与各连接体插针17的连接部位被包封体14包裹,包封体14与连接体13密封连接。包封体14的材料为聚乙烯(pe),连接体13的材料为聚己二酰己二胺(pa66)。包封体14能够防止水分等与引线15或连接体插针17 接触,以免影响引线15与连接体插针17电连接的可靠性,从而提高电动控制阀的动作可靠性。
57.如图3c所示,连接体13基本呈圆柱状,包括沿径向伸出的凸环状的加固部131、设置于连接体13的外壁的径向凹槽部132、以及位于连接体13的上端部的轴向凹槽部133,轴向凹槽部133的开口朝上。轴向凹槽部133的凹槽被部分保护套11填充。
58.保护套11的材质为聚氯乙烯(pvc),保护套11通过注塑方式与绝缘套12和连接体13连接,如图2和图3c所示,保护套11的一端包裹绝缘套12的一端,保护套11 的另一端位于连接体13的外周并包裹加固部131,即,保护套11将绝缘套12的下端与连接体13的加固部131之间的区域也包裹。保护套11对引线15和连接体插针17 起到二次保护作用,防止流体对引线15和连接体插针17的侵蚀影响二者电连接可靠性。
59.在保护套11成型过程中,保护套11位于连接体13的外部并包裹连接体13的加固部131和径向凹槽部132、轴向凹槽部133。加固部131和径向凹槽部132、轴向凹槽部133的设置,使得保护套11与连接体13的连接可靠性好。此处可以理解的是,加固部131和径向凹槽部132、轴向凹槽部133三者可以都设置,也可以仅设置其中一者。加固部131和径向凹槽部132、轴向凹槽部133的设置对于本技术方案的实现不是必须有的,但是对提高产品性能可靠性是有益的。
60.如图3b及图3c所示,玻璃座组件2包括由壳体21和玻璃座23形成的容纳腔25,容纳腔25位于玻璃座23的上方。引线组件1的连接体13包括位于加固部131下侧的插入部134,插入部134置于容纳腔25内,插入部134插入容纳腔25后,各引线组件1的各连接体插针17与玻璃座组件2中的各玻璃座插针24分别电连接。其中,玻璃座插针24的数量与连接体插针17的数量相同,连接体插针17与玻璃座插针24 电连接的连接部位位于容纳腔25区域内。
61.如图2和图3b所示,壳体21的连接筒部212的上端部包括密封件容纳部,具体为一开口朝上的环形的密封件容纳槽2121。密封环26置于密封件容纳槽2121。本实施例中,密封
件容纳槽2121和密封环26都为圆环形。装配时,密封环26置于密封件容纳槽2121后,将引线组件1的插入部134插入容纳腔25,使连接体插针17与玻璃座插针24电连接,之后,用带有内螺纹的固定螺母3将引线组件1的保护套11与壳体21可拆卸地固定连接,密封环26与保护套11和连接筒部212弹性抵接。
62.具体地,如图3c所示,固定螺母3包括环形的下压部31和与下压部31呈垂直设置的套筒部32,套筒部32的内壁包括与壳体21螺纹连接的内螺纹。引线组件1 的保护套11包括基部111和环形部112,环形部112位于基部111的下侧,环形部 112的外壁相对于基部111的外壁呈径向伸出设置,固定螺母3自基部111与保护套 11套接后,下压部31套设于基部111外周,套筒部32与壳体21的连接筒部212螺纹连接。此时,保护套11的环形部112位于下压部31和壳体21之间,密封环26分别与环形部112和壳体21的连接筒部212抵接,在引线组件1与玻璃座组件2之间形成一道软密封,防止流体自固定螺母3的下压部31与保护套11的基部111之间渗入,改善连接体插针17与玻璃座插针24电连接的可靠性,从而提高电动控制阀的动作可靠性。
63.如图3c所示,固定螺母3的下压部31还包括密封凸筋311,密封凸筋311具有为位于下压部31的下端面并呈环形设置,在固定螺母3与引线组件1的保护套11及玻璃座组件2的壳体21连接时,密封凸筋311与保护套11的环形部112的上表面抵接压紧,密封凸筋311的有益效果是形成一道硬密封,改善流体进入电动控制阀与连接体插针17或玻璃座插针42接触的风险,改善了电动控制阀的动作可靠性,并且,当电动控制阀应用于海运场合时,密封凸筋311能很好的防止流体从下压部31的内壁与保护套11的外壁之间进入堆积在固定螺母3与壳体21之间对壳体21造成盐雾腐蚀。
64.如图3c所示,保护套11还包括第一周向定位部113,本实施例中,第一周向定位部为一个轴向凸起。具体地,第一定位部113位于环形部112的下侧,自环形部112 的下表面向壳体21的轴向方向延伸形成。壳体21的连接筒部212的上端部包括第二定位部2122,第二定位部2122为设置于壳体21的上端部的槽部或缺口部,在引线组件1与玻璃座组件2装配过程中,第一定位部113与第二定位部2122二者配合以限定各连接体插针与各玻璃座插针的对应关系,第一定位部113至少部分位于第二定位部2122中,使引线组件1与玻璃座组件2二者在周向进行一个相对定位,便于引线组件1的各连接体插针17与玻璃座组件2的各玻璃座插针24的装配,起到防插错的作用。
65.如图2及图3b所示,本实施例中,密封件容纳槽2121包括内壁部2123和外壁部2124,第二定位部2122位于密封件容纳槽2121的外壁部2124的外侧,固定螺母 3与保护套11和壳体21连接后,保护套11的环形部112与密封环26及内壁部2123 和外壁部2124均抵接,或保护套11的环形部112与密封件26抵接,并与内壁部2123 和外壁部2124二者之一抵接。则,内壁部2123和/或外壁部2124对密封环26的变形量起到限制作用,防止密封环26过度变形影响密封环26的使用寿命。
66.如图2和图3c所示,引线组件1还包括第一热塑管18,第一热塑管18的一端套设于绝缘套12外,第一热塑管18的另一端套设于保护套11外。并且,在第一热塑管18与绝缘套12及第一热塑管18与保护套11之间涂覆有密封胶。第一热塑管18 用以防止外部流体与引线组件1中的连接体插针17接触,导致引线组件1失效。需要说明的是,图2及图3c所示中的第一热塑管18是成型后的形状,第一热塑管18 在套设于绝缘套12及保护套11上之后热塑成
型。
67.如图3a和图12所示,阀芯部件8包括阀芯81,阀芯81为塑料材质,阀芯质量轻,与金属材料制成的传动螺纹件配合,二者之间相对磨损小,减小阀芯81相对传动螺纹件74轴向移动时受到的摩擦阻力,阀芯81耐磨性好,动作更加顺畅,改善阀芯81的动作性能。阀芯81通过注塑成型,阀芯81包括导向部811和流量调节部812。导向部811的外壁的形状与卡位器43的筒部431的内壁的形状相适配。导向部811 包括配合平面部8111和配合过渡部8112,配合平面部8111能够与卡位器43的平面部4311滑动配合,配合过渡部8112能够与卡位器43的过渡部4312滑动配合,流量调节部812能够与阀口4210配合控制的通流面积。本实施例中,阀芯81由自润滑peek 塑料制成,阀芯81耐磨性好,加工方便,能够加工出复杂形状的阀芯。并且,在阀芯81相对于卡位器43轴向滑动过程中,能够有效改善阀芯81与卡位器43产生的摩擦。本实施例中,具体地,阀芯81的外壁为与卡位器43的筒部431的内壁成相适应的四边形结构,阀芯81具有非自锁的内螺纹。传动螺纹件74为金属材质,本实施例中具体为不锈钢材料。传动螺纹件74的螺纹部741具有非自锁外螺纹,阀芯81与传动螺纹件74螺纹连接。传动螺纹件74转动过程中,卡位器43限制阀芯81周向转动,阀芯81能够相对于传动螺纹件74轴向移动,阀芯81相对于传动螺纹件74轴向移动过程中,在阀芯81的内螺纹与传动螺纹件74的外螺纹之间会产生摩擦,摩擦严重会有使阀芯81卡死的隐患,为此,传动螺纹件74的螺纹部741具有耐磨层,以增加传动螺纹件74的润滑性。耐磨层的材料为dw
‑
1605减磨涂层,厚度为0.01mm
‑
0.02mm。传动螺纹件74与阀芯81配合时摩擦阻力减小,使阀芯81的轴向移动更加灵活和可靠,且保证电动控制阀的开阀力不会由于摩擦阻力而衰减。另使得传动螺纹件74润滑无需系统冷冻油的帮助,使得产品能更好地适应无油或者少油系统。本实施例中,在传动螺纹件74的螺纹部741及螺纹部741与径向凸出部742之间的外表面均设置有耐磨层。
68.如图12和图3a所示,阀芯81的流量调节部812包括第一段8122和第二段8121, 第一段8122呈一端细,一端粗的流线形,在阀芯81的轴向,阀芯81的纵截面的轮廓呈曲线状。第二段8121设置于导向部811与第一段8122之间,第二段8121呈锥台状,第二段8121与第一段8122相接的一端的直径小于其另一端的直径。在阀芯81 随传动螺纹件74轴向移动过程中,阀芯81的远离阀口4210达最大行程时,阀芯81 与连接件63抵接。也即,连接件63的又一作用是对阀芯81的最大行程的限位作用。具体地,阀芯81的上端面与连接件63的第一限位部632的下端面接触时,阀芯81 自阀口4210向远离阀口4210方向轴向移动行程达最大值。如图3a所示,为了保证连接件63对阀芯81的轴向行程的限位作用,当阀芯81与连接件63的第一限位部632 抵接时,阀芯81与传动螺纹件74的径向凸出部742之间具有轴向间隙,即,进一步确保阀芯81与径向凸出部742不接触,以防径向凸出部742对阀芯81产生干涉。
69.上述,通过设置与座体61固定连接的连接件63对阀芯81进行上止动,连接件 63又对第一轴承62可以起到防止第一轴承62轴向脱出的作用,座体61、第一轴承 62、连接件63固定连接,阀芯81能够相对于传动螺纹部件轴向移动,阀芯81能够与连接件63抵接,即一个连接件63既用于固定第一轴承62,又用于对阀芯81的轴向行程进行限位。阀芯81轴向向上达最大行程时与第一限位部632抵接,抵接的作用力由连接件63承担,而不是直接作用于第一轴承62上,该作用力进一步通过连接件63传递到座体61上,不会作用到第一轴承62上,避免第一轴承62受压而导致开阀力增大。由于上止动位置未设置在丝杆上,能有效防止在上止动时,阀杆与丝杆螺纹完全啮合咬死,导致不能正常开阀。
70.如图13所示为本技术电动控制阀的实施例二的结构示意图,图14所示为图13 中i2处的局部放大图,图15所示为图14中传动螺纹件的剖视图。本实施例二与实施例一所示电动控制阀的主要区别在于传动螺纹件和阀芯的区别。其它与实施例一相同之处采用相同标记,本实施例中下文未详述的零件及零部件之间的连接作用关系与实施例一中相同,不赘述。
71.如图13
‑
15所示,该电动控制阀包括阀芯81a和连接件63,连接件63的结构及附图标记援引实施例一中相关描述,连接件63包括第一台阶孔630a,传动螺纹部件包括传动螺纹件74a。阀芯81a由金属粉末注射成型,如此加工的有益之处是阀芯81a 的形状更易于加工,相比于金属车加工等方式制成的阀芯,阀芯形状更为灵活。此处,金属粉末注射利用模具可注射成型坯件并通过烧结快速制造高密度、高精度、三维复杂形状的阀芯。阀芯81a包括螺杆部811a、导向部812a和流量调节部813a,导向部 812a的外壁的形状与卡位器43的筒部431的内壁的形状相适配。导向部812a的形状与实施例一中的导向部811的形状相同,可以参照理解。导向部812a包括配合平面部8121a,在第一阀体42的轴向,配合平面部8121a能够与卡位器43的平面部4311 滑动配合,配合过渡部8122a能够与卡位器43的过渡部4312滑动配合,流量调节部 813a能够与阀口4210配合控制的通流面积,螺杆部811a的外壁包括外螺纹,在螺杆部811a的设置有外螺纹的部分设置有耐磨层,耐磨层的材料、厚度及作用与前述实施例一中耐磨层的作用相同,在此不再赘述。
72.如图14和图15所示,传动螺纹件74a由两种材料加工而成,传动螺纹件74a包括嵌件741a和基体742a。嵌件741a由金属材料制成,本实施例中为不锈钢材料,具有轴向通孔。基体742a由非金属材料制成,嵌件741a与基体742a注塑固定。嵌件 741a呈筒状,嵌件741a包括齿轮连接部744a,齿轮连接部744a包括缺口部7441a,缺口部7441a与输出齿轮72的凸部721卡接,缺口部7441a与输出齿轮72铆接固定,阀芯81a的螺杆部811a伸入嵌件741a并与基体742a的内螺纹螺合,通过阀芯81a 与塑料制的基体742a之间的螺纹配合,能够改善阀芯81a动作过程中发生卡死的风险。传动螺纹件74a只转动不轴向移动,传动螺纹件74a能够带动阀芯81a,使阀芯 81a相对于传动螺纹件74a轴向移动,从而远离或靠近阀口4210。阀芯81a轴向移动至最大行程时,阀芯81a的导向部812a与连接件63抵接以限制阀芯81a的轴向向上移动,即对阀芯81a进行上止动。本实施例中具体由peek或具有类似性能的塑料制成,例如,阀芯81a由自润滑peek塑料制成,阀芯81a耐磨性好,加工方便,并且,在相阀芯81a相对于卡位器43轴向滑动过程中,能够有效改善阀芯81a与卡位器43 产生的摩擦。
73.如图15所示,嵌件741a与基体742a的外壁整体呈圆形(嵌件741a的缺口部7441a 除外)。嵌件741a的外径小于基体742a的外径,并且基体742a具有小径段7421a和大径段7422a,大径段7422a的外径大于小径段7421a的外径。则基体742a的外壁与嵌件741a的外壁形成第一级台阶面745a,基体742a的外壁包括第二级台阶面746a。基体742a部分置于第一台阶孔630a中。
74.输出齿轮72的部分下端面与第一级台阶面745a抵接,第一轴承62的轴承内圈621与小径段7421a的外壁过盈或过渡连接,轴承内圈621的下端与第二级台阶面746a 抵接。
75.如图15所示,为了使连接件13不对阀芯81a和传动螺纹件74a的动作产生干涉,传动螺纹件74a的大径段7422a与连接件63之间具有轴向间隙。
76.上述电动控制阀能够应用于海运场合,第一阀体42和第二阀体41采用不锈钢材
料,但虽然采用不锈钢材质,若长期在高温高湿环境下极易对第一阀体42和第二阀体41造成盐雾腐蚀,此外,若上述电动控制阀应用于co2系统时,由于系统压力非常高,使得壳体21、第二阀体41与第一阀体42的焊接部位存在质量安全隐患。如图 2所示,电动控制阀还包括第二热塑管100,第二热塑管100的材质为ptfe,第二热塑管100的一端位于固定螺母3的外周,第二热塑管100的另一端位于第一阀体42的外周,从而,第二热塑管100将部分固定螺母3、及固定螺母3与第一阀体42之间的部分、第二阀体41与第一阀体42的焊接部位均包裹,进一步提高电动控制阀的防水、抗冰冻、抗系统压力性能。
77.以上对本技术所提供的电动控制阀进行了举例介绍。本文中应用了具体个例对本技术的原理及实施方式进行了阐述,以上实施例的说明只是用于帮助理解本技术的方法及其核心思想。应当指出,对于本技术领域的普通技术人员来说,在不脱离本技术原理的前提下,还可以对本技术进行若干改进和修饰,这些改进和修饰也落入本技术权利要求的保护范围内。