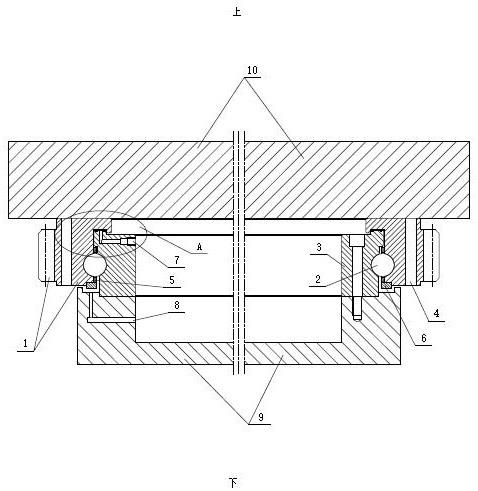
1.本发明属于回转支承技术领域,具体是涉及一种高速传动油浮式回转支承。
背景技术:2.回转支承不仅能承受很大的轴向载荷,还能承受较大的倾覆力矩,普遍应用在低速回转的工程机械上,如挖掘机、塔机、起重机、港口吊装机械等。回转支承集轴承的回转与齿轮的传动于一体,将原来的轴承、轴承座、主轴、齿轮集成在一块,极大简化和优化了设计、制造工作,现已在低速回转的工程机械、焊接机械、灌装机械、打磨机械上得到广泛应用。
3.但是,现有回转支承(以滚道中心直径1000mm为例)只能用在低速回转(设计转速为3rpm)的设备上,不适合高速回转(50rpm),原因在于:(1).滚动钢球在较大轴向载荷作用下,磨损较大;(2).滚动钢球在滚道内的运动不仅有滚动,还有滑动,存在附加冲击,而钢球间采用尼龙隔离块进行缓冲,尼龙隔离块在附加冲击的作用下,易碎裂;(3).现有回转支承的制造精度低,滚道是车削加工而成,未经磨削加工,故其轴向和径向间隙大、跳动大,高速传动时震动大;(4).轮齿热处理后未经磨削加工,故节圆跳动大,不能实现精确和平稳传动,高速回转时,存在很大的附加冲击力。
技术实现要素:4.本发明的目的是提供一种高速传动油浮式回转支承,以实现回转支承(以滚道中心直径1000mm为例)在高速回转(50rpm)传动机械设备上的应用,如立式车床。
5.为解决上述技术问题,本发明提出的技术方案为:一种高速传动油浮式回转支承,包括内圈、外圈以及滚球,所述内圈中设置有至少两个用于液压油流通的液压油进油孔道,所述液压油进油孔道的进油孔开孔于所述内圈的内径表面上,所述液压油进油孔道的出油孔开孔于所述内圈的上端面上;所述外圈上设置有径向向内凸出部,所述径向向内凸出部的下表面遮盖住所述内圈上的液压油进油孔道的出油孔,所述径向向内凸出部的下表面与所述内圈的上端面之间留有缝隙;所述内圈的上端面上设置有两个环形凹槽,液压油进油孔道的出油孔位于内圈上的两个环形凹槽之间;所述径向向内凸出部的下表面上设置有三个环形凹槽,所述外圈上的三个环形凹槽与内圈上的两个环形凹槽形成公母式的间隙配合。
6.优选的,全部的液压油进油孔道在内圈上沿圆周向均匀分布;所述液压油进油孔道由水平孔与竖直孔组成,水平孔与竖直孔连通构成孔道。
7.优选的,高速传动油浮式回转支承还包括铜保持架与保持架挡环,所述滚球内嵌放置在铜保持架上的孔中,所述保持架挡环用于支撑铜保持架以及防止铜保持架脱出,所述保持架挡环安装在所述外圈的内径表面与下端面的拐角处。
8.本技术提供了一种高速传动油浮式回转支承,所述内圈中设置有至少两个用于液压油流通的液压油进油孔道,所述液压油进油孔道的进油孔开孔于所述内圈的内径表面上,所述液压油进油孔道的出油孔开孔于所述内圈的上端面上;所述外圈上设置有径向向内凸出部,所述径向向内凸出部的下表面遮盖住所述内圈上的液压油进油孔道的出油孔,所述径向向内凸出部的下表面与所述内圈的上端面之间留有缝隙;所述内圈的上端面上设置有两个环形凹槽,液压油进油孔道的出油孔位于内圈上的两个环形凹槽之间;所述径向向内凸出部的下表面上设置有三个环形凹槽,所述外圈上的三个环形凹槽与内圈上的两个环形凹槽形成公母式的间隙配合;本技术提供的一种高速传动油浮式回转支承的制备方法,包括碾环成型、机加工、调质处理、磨削加工、成品组装,通过优化工艺步骤与工艺参数,使得滚道经过调质处理后的硬度为58-62hrc,滚道的淬火硬化层的厚度不小于5mm,齿面与齿根经过调质处理后的硬度为50-60hrc,齿面的淬火硬化层的厚度不小于3.2mm,齿根的淬火硬化层的厚度不小于1.2mm,内圈滚道与外圈滚道的轴向间隙与径向间隙≤0.02mm、轴向跳动与径向跳动≤0.02mm,轮齿节圆相对于滚道的径向跳动≤0.03mm;本技术采用油浮结构,抵消了滚球承受的大部分轴向力,降低了滚球的磨损,提高了使用寿命,油浮结构中,高压液压油从内圈的进油孔进入,从上端面出来,直接作用在外圈的油沟槽内,液压油从波浪槽中流出,外圈受到向上的作用力而上浮,在回转支承承受静压负载时,调整高压液压油泵压力,保证回转支承的起动力矩不大于30n.m;本技术采用整体的铜保持架替代单个尼龙隔离块,实现了滚球滚动可控;本技术从结构上提高了回转支承的使用寿命,满足了高速回转的要求,且从制造工艺上提高了回转支承的制造精度,实现了运动的精确性,从而实现了回转支承在高速回转传动机械设备上的应用。
附图说明
9.图1是本技术的实施例提供的水平安装的一种高速传动油浮式回转支承的剖视结构示意图;图2为图1中的油浮结构所在的区域a的放大图(放大展示油浮结构中的液压油进油孔道、进油孔、出油孔、三个环形凹槽与两个环形凹槽形成公母式的间隙配合)。
10.图中:1外圈(有齿),2滚球,3内圈(无齿),4安装孔(丝孔或光孔),5铜保持架,6保持架挡环,7液压油进油孔道的进油孔,8回油孔道;9 固定底座,10转盘。
具体实施方式
11.为使本发明实施例的目的、技术方案和优点更加清楚,下面将结合本发明实施例,对本发明实施例中的技术方案进行清楚、完整地描述,显然,所描述的实施例是本发明的一部分实施例,而不是全部的实施例。基于本发明中的实施例,本领域普通技术人员在没有做出创造性劳动的前提下所获得的所有其他实施例,都属于本发明保护的范围。
12.如图1-2中:外圈1(有齿),滚球2,内圈3(无齿),安装孔(丝孔或光孔)4,铜保持架5,保持架挡环6,液压油进油孔道的进油孔7,回油孔道8;固定底座9,转盘10。
13.本技术提供了一种高速传动油浮式回转支承,包括内圈3、外圈1以及滚球2,所述内圈3中设置有至少两个用于液压油流通的液压油进油孔道,所述液压油进油孔道的进油孔开孔于所述内圈3的内径表面上,所述液压油进油孔道的出油孔开孔于所述内圈3的上端面上;所述外圈1上设置有径向向内凸出部,所述径向向内凸出部的下表面遮盖住所述内圈3上的液压油进油孔道的出油孔,所述径向向内凸出部的下表面与所述内圈3的上端面之间留有缝隙;所述内圈3的上端面上设置有两个环形凹槽,液压油进油孔道的出油孔位于内圈3上的两个环形凹槽之间;所述径向向内凸出部的下表面上设置有三个环形凹槽,所述外圈1上的三个环形凹槽与内圈3上的两个环形凹槽形成公母式的间隙配合。
14.在本技术的一个实施例中,全部的液压油进油孔道在内圈3上沿圆周向均匀分布;所述液压油进油孔道由水平孔与竖直孔组成,水平孔与竖直孔连通构成孔道。
15.在本技术的一个实施例中,高速传动油浮式回转支承还包括铜保持架5与保持架挡环6,所述滚球2内嵌放置在铜保持架5上的孔中,所述保持架挡环6用于支撑铜保持架5以及防止铜保持架5脱出,所述保持架挡环6安装在所述外圈1的内径表面与下端面的拐角处。
16.本技术提供的高速传动油浮式回转支承的制备方法,包括以下依次进行的步骤:1) 将42crmo钢材质的锻件通过碾环成型制得外圈毛坯;将42crmo钢材质的锻件通过碾环成型制得内圈毛坯;2) 将步骤1)制得的外圈毛坯进行机加工,完成后得到外圈半成品;将步骤1)制得的内圈毛坯进行机加工,完成后得到内圈半成品;3) 将外圈半成品与内圈半成品均先进行调质处理,控制滚道经过调质处理后的硬度为58-62hrc,滚道的淬火硬化层的厚度不小于5mm;控制齿面与齿根经过调质处理后的硬度为50-60hrc,齿面的淬火硬化层的厚度不小于3.2mm,齿根的淬火硬化层的厚度不小于1.2mm;4) 磨削加工:将内圈3的滚道、外圈1的滚道、安装端面与轮齿分别先进行粗磨,然后进行去应力退火,再然后分别进行精磨加工,以控制内圈滚道与外圈滚道的轴向间隙与径向间隙≤0.02mm、轴向跳动与径向跳动≤0.02mm,控制轮齿节圆相对于滚道的径向跳动≤0.03mm;5) 成品组装:将内圈3、外圈1以及滚球2组装在一起形成成品的回转支承。
17.本技术中,回油孔道8设置在固定底座9中,回油孔道8用于收集并排出从油浮结构中流出的液压油,将液压油回收并从回转支承中排出,然后送至液压油泵站的储油箱中。
18.本技术提供的一种高速传动油浮式回转支承实现了高速回转的工作原理:(1).在结构设计上采用油浮结构,大大降低了滚动钢球的磨损;油浮结构:内圈3的上端面有2个环形凹槽,在2个环形凹槽之间均布有6个出油孔,外圈1上有3个环形凹槽,与内圈3的2个环形凹槽形成一公一母的间隙配合;所述内圈的内部设置有6个液压油进油孔道,内圈的内径表面有6个进油孔,内圈
的上端面有2个环形凹槽,2个环形凹槽之间设置有6个均布的出油孔;所述外圈的内径方向设置有法兰台阶(径向向内凸出部),法兰台阶的下表面上设置有3个环形凹槽;高压液压油从内圈3上的进油孔7进入,从内圈3的上端面的出油孔出来,直接作用在外圈的中间的那个环形凹槽表面上,再经内圈3与外圈1之间的环形凹槽之间的缝隙中流出,外圈1受到高压液压油的冲出作用力而上浮,在回转支承承受静压负载时,调整高压液压油的泵压力,保证回转支承的起动力矩不大于30n.m;(2).采用整体铜保持架5替代单个的尼龙隔离块,实现钢球滚动的可控;采用整体式的铜保持架5,铜保持架5随外圈1一起转动;钢球被放置在铜保持架的孔中,回转支承运动时,钢球不仅自转,还随着铜保持架一起公转;(3).对回转支承的滚道进行磨削加工,实现精确和平稳传动;对内圈3与外圈1的滚道进行磨削加工,内圈3与外圈1的滚道热处理后再经磨削加工,保证内圈滚道与外圈滚道的轴向间隙与径向间隙≤0.02mm、轴向跳动与径向跳动≤0.02mm;(4).对外圈上的轮齿进行磨削加工,提高轮齿的精度等级,消除高速传动时的冲击;轮齿热处理后再经磨削加工,精度达到7级,同时保证轮齿节圆相对于滚道的径向跳动≤0.03mm。
19.本技术中,调质处理是指淬火加高温回火的双重热处理方法,其目的是使工件具有良好的综合机械性能。高温回火是指在500-650℃之间进行回火。调质处理可以使钢的性能,材质得到很大程度的调整,其强度、塑性和韧性都较好,具有良好的综合机械性能。调质处理后得到回火索氏体,回火索氏体是马氏体于回火时形成的。
20.本技术中,上述“内”这个方位与内圈中的“内”相同,“外”这个方位与外圈中的“外”相同。
21.本发明未详尽描述的方法和装置均为现有技术,不再赘述。
22.以上实施例的说明只是用于帮助理解本发明的方法及其核心思想。应当指出,对于本技术领域的普通技术人员来说,在不脱离本发明原理的前提下,还可以对本发明进行若干改进和修饰,这些改进和修饰也落入本发明权利要求的保护范围内。