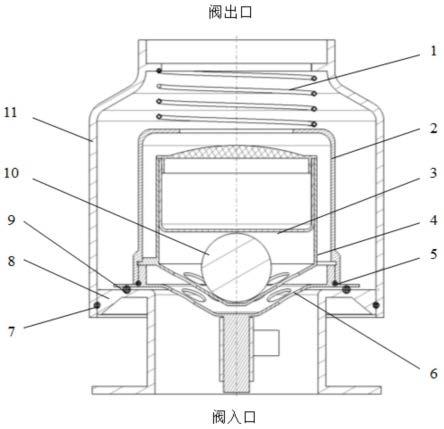
1.本发明涉及直升机燃油系统设计领域,涉及一种用于直升机燃油系统的多功能通气阀。
背景技术:2.在直升机正常飞行及加油时,直升机燃油系统应确保燃油箱与外界环境大气之间的通气管路通畅,通过与外界的大气交换调节油箱内的气体压力,使油箱内部的气体压力与外界环境大气压力之间的差值在燃油箱及机身机构的承压范围内;
3.在直升机翻转或大姿态机动导致燃油箱内燃油进入通气管路时,直升机燃油系统需要在通气管路中设置通气阀,防止燃油箱内的燃油经过通气管路排到机外;
4.在直升机进行压力加油时,当油箱满油后若不能及时停止加油,则需要提供释压阀和溢流管道,使多加的燃油排到机外。
5.现有的通气阀不能同时具备阀正常状态下常开、燃油进入阀入口时阀关闭、阀入口端油压达到指定压力时阀打开这三项功能,导致直升机燃油系统不能利用通气管路作为压力加油溢流管道使用,需要额外设置释压阀和溢流管道,增加了系统重量。因此设计一种同时具备上述三项功能的通气阀对于优化系统设计、减轻系统重量具有实际意义。
技术实现要素:6.本技术提供一种用于直升机燃油系统的多功能通气阀,能够同时具备阀正常状态下常开、燃油进入阀入口时阀关闭、阀入口端油压达到指定压力时阀打开三项功能,能够优化系统设计、减轻系统重量。
7.技术方案:一种用于直升机燃油系统的多功能通气阀,多功能通气阀包括弹簧1、活门组件、阀底座8、壳体11,所述活门组件包括活门腔壳体2、浮子3、浮子腔4、密封圈一5、活门腔底座6、密封圈二7、密封圈三9、钢球10,其中:
8.阀底座8为空心柱状结构,阀底座8的底端为安装法兰结构,阀底座8的上端设置有向外翻的凸台结构;壳体11为空心的柱状结构,阀底座8的上端的凸台装配在壳体11的底端内,壳体11的顶端为多功能通气阀的出口;阀底座8和壳体11组成通气阀外壳,阀底座8和壳体11的内部空腔设置有弹簧1和活门组件;弹簧1的一端固定在壳体11上部,另一端固定在活门腔壳体2的上部;活门组件在弹簧1的作用下压紧在阀底座8上;
9.活门腔壳体2的顶部、活门腔底座6的底部和浮子腔4的底部上均开有通过孔;浮子3和钢球10位于浮子腔4内;活门腔底座6上部安装在阀底座8顶部,活门腔底座6顶部为向下倾斜的锥面并布有通过孔,活门腔壳体2下部安装在活门腔底座6上部,浮子腔4安装在活门腔底座6上部和活门腔壳体2内部,浮子腔4底部为向下倾斜的锥面并布有通过孔,浮子腔4顶部为敞口,浮子3安装在浮子腔4内,浮子3底部压在钢球10上。
10.具体的,浮子腔4通过n个小支臂卡在活门腔壳体2内,使浮子腔4固定在活门腔壳体2内,浮子腔4随活门腔壳体2和活门腔底座6一起移动。
11.具体的,活门腔壳体2和活门腔底座6采用螺纹连接组成,用密封圈一5密封。
12.具体的,所述n的范围为3-6。
13.具体的,浮子腔4与活门腔壳体2之间的空隙范围为7-10mm。
14.具体的,活门腔底座6和阀底座8之间通过密封圈三9进行密封。
15.具体的,阀底座8和壳体11之间采用密封圈二7进行密封。
16.具体的,阀底座8上端的凸台结构的尺寸,外径为内径为厚度为3mm;
17.阀底座8的底端安装法兰结构的尺寸,外径为内径为厚度为3mm。
18.具体的,活门腔底座6的通过孔的数量为4-8个,通过孔的半径范围为5-10mm,浮子腔4的通过孔的数量为4-8个,通过孔的半径范围为5-10mm。
19.综上所述,本技术提供一种用于直升机燃油系统的多功能通气阀,具备以下功能:
20.a正常工作状态下,阀的通道保持开启;
21.b当有燃油进入阀入口时,阀的通道关闭;
22.c当阀入口的燃油压力达到指定压力时,阀的通道重新开启。
附图说明
23.图1为本技术提供的一种用于直升机燃油系统的多功能通气阀的结构示意图;
24.图2为本技术提供的一种浮子腔的结构示意图;
25.图3为本技术提供的一种处于正常工作状态阀通道开启的多功能通气阀的示意图;
26.图4为本技术提供的一种燃油进入阀内,顶起浮子阀通道开启的多功能通气阀的示意图;
27.图5为本技术提供的一种通气阀大姿态下,钢球顶起浮子阀通道关闭的多功能通气阀的示意图;
28.图6为本技术提供的一种燃油压力达到阀开启压力阀通道开启的多功能通气阀的示意图;
29.其中:1-弹簧、2-活门腔壳体、3-浮子、4-浮子腔、5-密封圈一、6-活门腔底座、7-密封圈二、8-阀底座、9-密封圈三、10-钢球、11-壳体。
具体实施方式
30.如图1所示,为本技术提供的一种用于直升机燃油系统的多功能通气阀的结构示意图。所述多功能通气阀为双向常开活门结构形式,多功能通气阀的功能通过活门腔壳体2及活门腔内部的钢球10和浮子3实现。
31.多功能通气阀包括弹簧1、活门组件、阀底座8、壳体11,所述活门组件包括活门腔壳体2、浮子3、浮子腔4、密封圈一5、活门腔底座6、密封圈二7、密封圈三9、钢球10,其中:
32.阀底座8为空心柱状结构,阀底座8的底端为安装法兰结构,阀底座8的上端设置有向外翻的凸台结构;壳体11为空心的柱状结构,阀底座8的上端的凸台装配在壳体11的底端
内,壳体11的顶端为多功能通气阀的出口;阀底座8和壳体11组成通气阀外壳,阀底座8和壳体11的内部空腔设置有弹簧1和活门组件;弹簧1的一端固定在壳体11上部,另一端固定在活门腔壳体2的上部;活门组件在弹簧1的作用下压紧在阀底座8上。
33.活门腔壳体2的顶部、活门腔底座6的底部和浮子腔4的底部上均开有通过孔。浮子3和钢球10位于浮子腔4内。活门腔底座6上部安装在阀底座8顶部,活门腔底座6顶部为向下倾斜的锥面并布有通过孔,活门腔壳体2下部安装在活门腔底座6上部,浮子腔4安装在活门腔底座6上部和活门腔壳体2内部,浮子腔4底部为向下倾斜的锥面并布有通过孔,浮子腔4顶部为敞口,浮子3安装在浮子腔4内,浮子3底部压在钢球10上。
34.具体的,如图2所示,浮子腔4通过n个小支臂卡在活门腔壳体2内,使浮子腔4固定在活门腔壳体2内,浮子腔4随活门腔壳体2和活门腔底座6一起移动。
35.具体的,活门腔壳体2和活门腔底座6采用螺纹连接组成,用密封圈一5密封。
36.具体的,阀底座8的底端安装法兰结构的尺寸,外径为内径为厚度为3mm。
37.阀底座8上端的凸台结构的尺寸,外径为内径为厚度为3mm。
38.具体的,阀底座8和壳体11之间采用密封圈二7进行密封。
39.具体的,活门腔底座6和阀底座8之间通过密封圈三9进行密封。
40.具体的,浮子腔4与活门腔壳体2之间的空隙范围为7-10mm。
41.具体的,所述n的范围为3-6。
42.具体的,活门腔底座6的通过孔的数量为4-8个,通过孔的半径范围为5-10mm,浮子腔4的通过孔的数量为4-8个,通过孔的半径范围为5-10mm。
43.多功能通气阀的工作原理如图3-6所示。
44.如图3所示,多功能通气阀在正常工作状态下,浮子3在重力的作用下压在钢球10上,浮子3顶部与活门腔壳体2顶部之间有5-10mm的空隙,此时通气阀内部的活门组件处于常开状态。当阀入口空气压力大于阀出口空气压力时,空气经过阀入口、活门腔底座6的通过孔、活门腔底座6与浮子腔4间的空隙、浮子腔4与活门腔壳体2的空隙、弹簧1、阀出口,实现空气向外排出。当阀出口空气压力大于阀入口空气压力时,空气经过弹簧1、浮子腔4与活门腔壳体2的空隙、活门腔底座6与浮子腔4间的空隙、活门腔底座6的通过孔、阀入口向内进入。
45.如图4所示,在直升机翻转或负过载的情况下,燃油会由多功能通气阀入口进入阀内,多功能通气阀在燃油进入阀内,顶起浮子,阀通道关闭的工作状态下,燃油经阀入口、活门腔底座6的通过孔、浮子腔4的通过孔进入浮子腔4内后,随着进入浮子腔4的燃油增多,浮子3在燃油作用下上升将活门腔壳体2顶部的开口封堵,从而封闭了活门腔出口,将阀的出口通道关闭,使燃油无法从阀出口流出。
46.如图5所示,多功能通气阀在达到一定的倾斜角度时,钢球顶起浮子,阀通道关闭的工作状态下,随着倾斜角度的增加,钢球10的位置由位于浮子腔4锥面底部到浮子腔4锥面的上端,浮子3会被钢球10顶起,上升的浮子3将活门腔壳体2的开口封堵,从而封闭了活门腔出口,将阀的通道关闭,防止直升机在大姿态机动时有燃油流出。
47.如图6所示,多功能通气阀内燃油压力达到阀开启压力,阀通道开启的工作状态
下,首先,燃油经阀入口、活门腔底座6的通过孔、浮子腔4的通过孔进入浮子腔4内后,随着进入浮子腔4的燃油增多,浮子3在燃油作用下上升将活门腔壳体2顶部的开口封堵,使燃油无法从阀出口流出,活门腔组件中充满燃油,随着阀内燃油的压力不断增大,燃油作用于活门腔底座6的压力增大,当阀入口处的燃油压力大于作用在活门组件上的弹簧1的压力、活门组件的重力、活门组件内燃油的重力之和时,活门组件整体向上移动,燃油经阀底座8和活门组件的空隙、壳体11和活门组件的空隙、弹簧1、阀出口排出多功能通气阀。