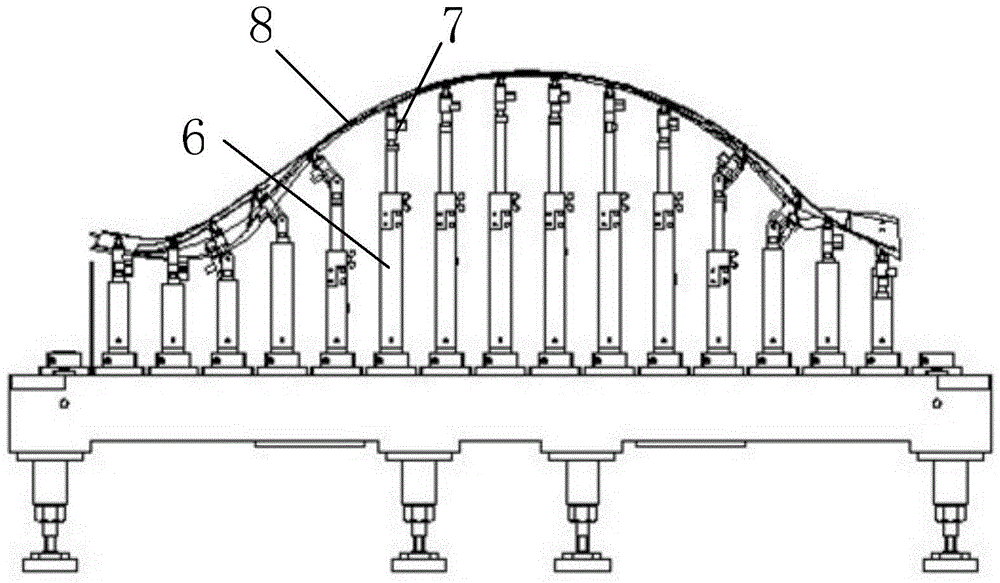
本发明涉及一种毛坯件的激光测量系统及其检测方法,尤其涉及一种适用于无特征空间曲面毛坯件的激光测量系统及其加工定位方法,可优选实施在钛合金毛坯件上。
背景技术:
:由于钛合金优良的综合性能,在航空航天工业中得到了广泛应用。钛板材料由于其塑形成形能力差等问题,一般采用热冲压成形工艺。考虑到钛板成形后取件变形的问题,在其热成形过程中不能用孔或槽等特征来定位,是一种无压边力的自由状态成形,即,在成形过程中,毛坯处于完全自由的拉伸状态。由此造成的问题是,毛坯件成形后不能确定其在毛坯中的具体位置。目前通常的解决办法是,首先制造一种完全吻合毛坯件型面的“靠模”(国外称“inspectionfixture”),工人将成形后的毛坯大致贴合在“靠模”上,通过按压、敲击等人工办法来判断是否存在“空谷”,如有,则继续调整毛坯位置,直至操作人员判断已基本贴合。然后,通过翻转机构在定位好的毛坯上钻定位孔,从而确定了定位孔与毛坯件在毛坯中的相对位置关系,并通过钻好的定位孔,将相对位置关系传递至下一制造工序。这种方法不但需要一比一来定制毛坯件靠模工装,而且检测过程耗时耗工,效率低下,最大的问题是测量的精度非常差,检测过程中存在人工的、主观的判断,由此造成的毛坯件定位和测量偏差,不但影响毛坯件成品率,还会增加装配难度,并降低了毛坯件的疲劳寿命,出现一系列质量问题。技术实现要素:本发明的目的就是为了解决现有技术中存在的上述问题,提供一种适用于无特征空间曲面毛坯件的激光测量系统及其加工定位方法。本发明的目的通过以下技术方案来实现:适用于无特征空间曲面毛坯件的激光测量系统,包括有导轨,其中:所述的导轨上安装有柔性支架,在柔性支架外围设置有机器人设备,所述机器人设备的检测端头上设备上安装有激光传感器,所述机器人设备与激光传感器的通讯端口上连接有工控机,所述机器人设备对自身设备运动范围内的毛坯件进行数据采集,所述的柔性支架和激光传感器由工控机控制,再由工控机和PLC组件完成时实时通讯,通过激光传感器采集被测毛坯件表面数据,对采集到的数据进行处理和分析得到检测结果。上述的适用于无特征空间曲面毛坯件的激光测量系统,其中:所述的柔性支架,包括有通用底板,所述的通用底板上设置有承载组件,所述的承载组件包括有可伸缩支杆,所述可伸缩支杆头部设置有真空吸附头。进一步地,上述的适用于无特征空间曲面毛坯件的激光测量系统,其中:所述的柔性支架外围还设置有安全组件,所述安全组件包括安全光栅与安全门,所述安全光栅用于检测人员闯入,所述安全门主用于检修。再进一步地,上述的适用于无特征空间曲面毛坯件的激光测量系统,其中:所述的导轨、机器人设备、激光传感器、工控机采用以太网方式互联通讯。适用于无特征空间曲面毛坯件的激光测量加工定位方法,其特征在于包括以下步骤:步骤①,进行初始化。步骤②,工控机内PLC组件确认准备就绪后,导入机器人轨迹程序,开始启动扫描工作。步骤③,在扫描完成后,机器人回到初始工作原点,工控机通过坐标变换矩阵进行点云数据处理。步骤④,导轨将毛坯件连同柔性支架一起运送到下一个制造工位进行加工,坐标变换矩阵将作为下一个加工工序的输入条件导入。上述的适用于无特征空间曲面毛坯件的激光测量加工定位方法,其中:步骤①所述的初始化中,导入所需测量的毛坯件数模,调整柔性支架的位置和高度,实现对待测毛坯件的定位,完成测量数据的清空和归零,等待检测系统的自检工作。进一步地,上述的适用于无特征空间曲面毛坯件的激光测量加工定位方法,其中:若所述毛坯件为首次被检测毛坯件,应先导入毛坯件的CAD数模,计算并设置柔性支架上的支杆位置和高度,随后用柔性支架定位好毛坯件,然后进行机器人的示教编程,确保毛坯件的全部数据能够有效的被采集到,在测量数据确认无误后,柔性支架的初始化信息和机器人的轨迹程序将绑定到该毛坯件上并存储在工控机内。更进一步地,上述的适用于无特征空间曲面毛坯件的激光测量加工定位方法,其中:步骤③所述的点云数据处理过程为,首先,对点云数据与毛坯件CAD数模进行匹配定位,得到最佳的对应关系,输出坐标变换矩阵;之后,进行点云数据和理论CAD数模的偏差比对,进行分析,形成测量分析报告;如果毛坯件尺寸超差,则报警通知现场负责人员处理,所述的超差为超过形位公差正负0.5mm;如果毛坯件实际尺寸在公差范围之内,则可根据预设模版出具标准的测量报告。更进一步地,上述的适用于无特征空间曲面毛坯件的激光测量加工定位方法,其中:步骤③所述的点云数据处理中,首先,计算点云数据曲面上每一个点的法向量属性、曲率属性;然后在这些属性的基础上,构造点的特征描述函数;通过特征描述函数来寻找点云与理论数模之间的对应点对,既分别寻找理论数模上的一个点与实际点云上的一个点组成一个点对,若实际点云与理论数模完全一致,则叠放在一起,这两个点将完全重合;通过多组对应点对完成实际点云与理论数模的配准;最后运用迭代最近点算法进行精确配准,配准的迭代过程停止后,计算配准误差,并分析毛坯件的尺寸质量,进行坐标变换求解。再进一步地,上述的适用于无特征空间曲面毛坯件的激光测量加工定位方法,其中:所述的步骤④完成后,柔性支架用于后续激光切割的加工,与毛坯件在同一工装下测量和加工。本发明技术方案的优点主要体现在:利用柔性支架对不同毛坯进行了吸附定位,进一步减少了对固定工装的依赖性。通过机器人离线编程完成对毛坯的扫描,可将系统用于多种不同毛坯件的测量和定位工作。同时,通过理论数模与点云数据的比对完成匹配定位,计算出的理论位置与实际位置的差值,即变换矩阵,连同通用柔性支架一起传递到激光切割机处,可利用该支架和变换矩阵完成对毛坯件的切割加工。并且,在定位匹配后,还可以通过对点云与理论数模的比对,全面分析毛坯件的成形质量。本发明实现了测量和定位匹配过程的数字化、自动化,系统还具备高柔性的特点,能够适用于不同毛坯件的测量和定位。再者,有效消除了由于人工测量带来的偏差,而且无需定制每个毛坯件的“靠模”,降低了成本。对于一个1.2mX0.8m的空间曲面毛坯件,系统的测量精度可以达到0.2mm,全过程效率为50s左右,精度相比以往做法提高了至少一个数量级,综合效率是原有的10倍以上,效果非常显著。附图说明图1是适用于无特征空间曲面毛坯件的激光测量系统构造示意图。图2是柔性支架构造及使用示意图。图3是色差云图示意图。图4是适用于无特征空间曲面毛坯件的激光测量加工定位方法实施流程示意图。图中各附图标记的含义如下:1导轨2柔性支架3机器人设备4激光传感器5工控机6可伸缩支杆7真空吸附头8毛坯件9安全光栅10安全门11PLC组件12激光切割机具体实施方式如图1~4所示的适用于无特征空间曲面毛坯件8的激光测量系统,其包括有用于传输的导轨1,尤其以直线导轨1为优选方案,其与众不同在于:为了对需要进行测量的钛合金毛坯件8进行有效定位,在导轨1上安装有柔性支架2。同时,考虑到自动化的高精度测量,在柔性支架2外围设置有机器人设备3,该机器人设备3的检测端头上设备上安装有激光传感器4。为了便于控制,采用机器人设备3与激光传感器4的通讯端口上连接有工控机5,令机器人设备3对自身设备运动范围内的毛坯件8进行数据采集。并且,柔性支架2和激光传感器4由工控机5控制,再由工控机5和PLC组件11完成时实时通讯,通过激光传感器4采集被测毛坯件8表面数据,对采集到的数据进行处理和分析得到检测结果。由PLC组件11完成对机器人设备3、导轨1,以及后续可能安装的安防系统进行控制。当然,为了便于针对不同的毛坯件8进行高精度测量,需要激光传感器4针对每个产品都要进行示教编程,完成毛坯全尺寸的扫描轨迹规划,保证扫描数据的可靠性。同时,激光传感器4,通过主动式的结构光原理,对环境因素不敏感,测量精度可达到0.05mm,采样频率可达到1000Hz,可以满足各方面的测量要求。就本发明一较佳的实施方式来看,所采用的柔性支架2包括有通用底板,该通用底板上设置有承载组件。同时,为了进行有效的调节,承载组件包括有可伸缩支杆6,在可伸缩支杆6头部设置有真空吸附头7。这样,可实现三自由度的调整,完成对不同钛板毛坯件的吸附定位,并能同时完成测量和激光切割等过程中的毛坯件8固定。进一步来看,考虑到实施期间的安全性,在柔性支架2外围还设置有安全组件。具体来说,安全组件包括安全光栅9与安全门10,该安全光栅9用于检测人员闯入,而安全门10主用于检修。同时。考虑到各个设备之间的控制通讯需要,导轨1、机器人设备3、激光传感器4、工控机5采用以太网方式互联通讯。亦可以方便整个系统的扩充拓展。为了更好的利用上述提供的系统,现提供一种适用于无特征空间曲面毛坯件8的激光测量方法,其特包括以下步骤:首先,进行初始化。在初始化的过程中,导入所需测量的毛坯件8数模,便于后续检测比对。与此同时,对柔性支架2的位置和高度进行调整,配合后续需要承载的毛坯件8规格。之后,吸附定位待测毛坯件8的即可。再者,为了提高测量精确,需要完成测量数据的清空和归零,等待检测系统的自检工作。并且,结合实际实施来看,若毛坯件8为首次被检测毛坯件8,应先导入毛坯件8的CAD数模,计算并设置柔性支架2上的支杆位置和高度,随后用柔性支架2定位好毛坯件8。然后对机器人进行示教编程,确保毛坯件8的全部数据能够有效的被采集到。在测量数据确认无误后,柔性支架2的初始化信息和机器人的轨迹程序将绑定到该毛坯件8上并存储在工控机5内,便于后续的调取使用。待工控机5内PLC组件11确认准备就绪后,导入机器人轨迹程序,开始启动扫描工作。接着,待扫描完成后,机器人回到初始工作原点,工控机5通过坐标变换矩阵进行点云数据处理。本发明采用的点云数据处理过程为:首先,对点云数据与毛坯件8CAD数模进行匹配定位,得到最佳的对应关系,输出坐标变换矩阵。之后,进行点云数据和理论CAD数模的偏差比对,进行色差云图分析,如图3所示。具体来说,在点云数据处理中,首先,计算点云数据曲面上每一个点的法向量属性、曲率属性等一些简单的具有欧式不变性的属性。然后在这些简单属性的基础上,构造点的特征描述函数。在本发明的实际实施时,该特征描述函数以能用最简单的方式独一无二地表达每一个点为最终目标。之后,通过特征描述函数来寻找点云与理论数模之间的对应点对,既分别寻找理论数模上的一个点与实际点云上的一个点组成一个点对,若实际点云与理论数模完全一致,则叠放在一起,这两个点将完全重合。随后,通过多组对应点对完成实际点云与理论数模的配准。在此期间,由于实际点云存在制造误差及扫描误差,此时配准仅为粗配准。最后,运用迭代最近点算法(ICP)进行精确配准。在配准的迭代过程停止后,计算配准误差,并分析毛坯件的尺寸质量,进行坐标变换求解。换句话说,为了提高分析的准确性,采用基于局部几何特征的曲面识别配准方法。由此,可通过自由曲面上任意点的法线、曲率及其周围相邻的法线曲率等信息,描述了该局部的特性,这一特性具有欧式不变性。通过选择具有多尺度的局部几何特征点,建立模型与测量点云的对应性。同时,通过Ransac滤除错误对应点,选择具有最大概率的匹配结果。进而,使用非线性最小二乘优化对整个点云进行姿态微调,确定最优解。相比而言,传统的ICP方法不仅会收敛于局部解,无法确定最优解,且计算时间太长。然后,形成质量分析报告,供品管部门进行根源问题分析,进行质量的持续改进。如果毛坯件8尺寸超差,则报警通知现场负责人员处理,该超差为超过形位公差正负0.5mm。这样,则该潜在质量问题毛坯件8将不被运输到下一个工位进行加工,而需人工干预来判断处理。如果毛坯件8实际尺寸在公差范围之内,则可根据预设模版出具标准的测量报告。这样,在采用点云采集后,可在工控机5内进行图像的最优匹配,找到现有定位状态与理论状态的差值。同时,能够输出坐标变换矩阵,供下一激光切割工序使用,可以利用该矩阵调整加工程序。由此,无需对毛坯件8重新安装定位,减少了工装环节,进一步降低了加工误差。最终,通过导轨1将毛坯件连同柔性支架2一起运送到下一个制造工位进行加工,而坐标变换矩阵将作为下一个加工工序的输入条件导入。在此期间,柔性支架2能用于后续激光切割的加工,与毛坯件在同一工装下测量和加工,进一步提高了制造精度。通过上述的文字表述可以看出,采用本发明后,利用柔性支架对不同毛坯进行了吸附定位,进一步减少了对固定工装的依赖性。通过机器人离线编程完成对毛坯的扫描,可将系统用于多种不同毛坯件的测量和定位工作。同时,通过理论数模与点云数据的比对完成匹配定位,计算出的理论位置与实际位置的差值,即变换矩阵,连同通用柔性支架一起传递到激光切割机12处,可利用该支架和变换矩阵完成对毛坯件的切割加工。并且,在定位匹配后,还可以通过对点云与理论数模的比对,全面分析毛坯件的成形质量。本发明实现了测量和定位匹配过程的数字化、自动化,系统还具备高柔性的特点,能够适用于不同毛坯件的测量和定位。再者,有效消除了由于人工测量带来的偏差,而且无需定制每个毛坯件的“靠模”,降低了成本。对于一个1.2mX0.8m的空间曲面毛坯件,系统的测量精度可以达到0.2mm,全过程效率为50s左右,精度相比以往做法提高了至少一个数量级,综合效率是原有的10倍以上,效果非常显著。这些实施例仅是应用本发明技术方案的典型范例,凡采取等同替换或者等效变换而形成的技术方案,均落在本发明要求保护的范围之内。当前第1页1 2 3