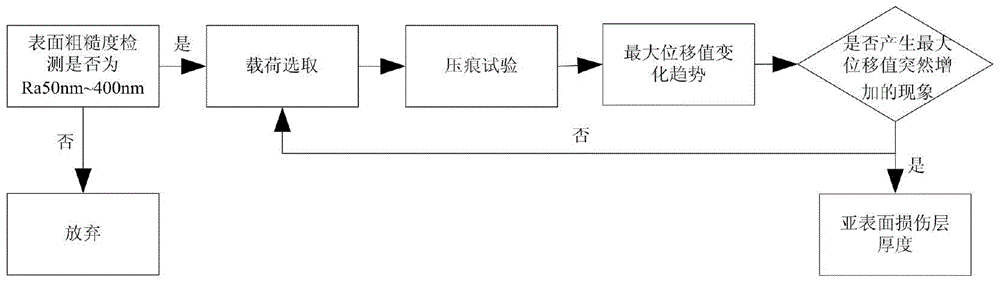
本发明属于材料表面加工质量评估技术领域,具体讲是涉及一种材料亚表面加工损伤层厚度的评估方法。
背景技术:随着我国在能源、空间、国防装备、集成电路等领域对高精度加工要求的日益提高,各类精密元器件表面加工完整性的评估是满足日益提高的技术指标的基础。表面完整性评估主要包括表面粗糙度、表面轮廓度以及亚表面损伤层厚度等。目前,针对表面粗糙度、表面轮廓度等质量评估的手段较多,如表面粗糙度仪、表面轮廓仪等。针对亚表面加工质量的评估主要可以分为两种:有损伤检测及无损伤检测。目前,亚表面损伤层厚度的有损伤检测方法大多基于酸性溶液腐蚀的方法。“光学材料亚表面损伤层厚度的测量方法”(申请公布号CN103017713A)、“脆性材料亚表面损伤层微裂纹全息反演检测方法”(授权公告号CN102426170B)、“一种硬脆性高精元件亚表面损伤程度的表征方法”(申请公布号CN103163154A)等专利中均提出一种基于酸腐蚀的测量方法。同时,亚表面损伤层厚度的有损伤检测方法中也包括破坏性的检测手段,如“硬脆性光学材料亚表面损伤层厚度的测量方法”(授权公告号CN101672625B)中提出一种基于剖切方法的亚表面损伤层检测方法。亚表面损伤层厚度的无损检测大多利用光学材料的透光性等材料特点进行检测,如“大口径光学元件表面损伤检测装置和相应的检测方法”(申请公布号CN103674977A)中则利用光学材料的特性进行检测。压痕试验是采用压头在材料表面进行印压的一种试验方法,经常用来分析材料的可加工性。Zhang等通过对压痕过程的研究,提出压痕过程中存在一个临界深度,且当压痕深度小于临界深度时,压痕产生的变形主要是以亚表面损伤层内的变形为主;当压痕深度大于临界深度时,压痕产生的变形主要是基体材料(即亚表面损伤层之下的材料)的变形为主(参考文献:ZhangT,XuW.SurfaceEffectsonNanoindentation[J].JournalofMaterialsResearch.2002,17(7):1715-1720.)。亚表面损伤厚度的测量,对于进一步提高材料表面加工质量及加工工艺的优化具有重要意义。为使材料表面具有较高的加工质量,通常需要多道工序。在某道工序完成后,进行下一道工序,且为保证加工质量,后一道工序需完全去除上一工序产生的亚表面损伤层。某一工序加工后所产生的亚表面损伤深度值,即是下一工序材料去除厚度的最小值。为实现亚表面损伤层的完全去除,后一工序的材料去除厚度需大于上一工序产生的亚表面损伤层厚度。同时,后一道工序的材料去除效率通常小于前一道工序,从而加工时间通常较长。判断上一工序产生的亚表面损伤层厚度,对于控制该道工序的加工时间具有重要意义。如若无法对某一工序产生的亚表面损伤层厚度进行评估,则下一工序多采用长时间加工以保证完全去除上一工序产生的亚表面损伤层,即为保证质量而牺牲效率。可以看出,对于材料亚表面损伤层厚度的评估,不但影响材料的加工质量,同时对控制下一工序的加工时间具有重要参考价值,且亚表面损伤层厚度的评估值需不小于其实际值。现有的亚表面损伤层厚度的有损伤检测方法大多对样品或环境具有较强的破坏性,无损检测手段则对材料自身性能要求较特殊。例如,石墨材料不是光学材料,且新型高性能石墨的耐腐蚀性较强,如何对石墨材料的亚表面损伤厚度进行检测是亟需解决的技术难题。
技术实现要素:本发明要解决的技术难题是针对目前材料亚表面损伤层厚度无损伤检测困难的现状,克服现有技术的不足,提供一种对样品或环境破坏性小的亚表面加工损伤层厚度的评估方法。本发明提出的技术方案为一种亚表面加工损伤层厚度的评估方法,其基于压痕试验,通过对不同载荷作用下压头产生的位移变化规律进行亚表面损伤层厚度的评估;其特征在于:其包括如下步骤:(1)设定压痕载荷:以45μN为起始载荷,以50~200μN为增加量,设定若干个载荷,载荷的终点为1500μN;(2)进行压痕试验:在材料样品上进行压痕试验,根据所设定的载荷从小至大依次进行加载-卸载试验;记录每个载荷加载-卸载试验中压头产生的最大位移值并进行比较;当所选载荷加载-卸载试验产生的最大位移值较上一载荷加载-卸载试验产生的最大位移值的增大率大于50%时,停止压痕试验,则所选载荷所产生的最大位移值为亚表面损伤层厚度评估值;若未出现所选载荷加载-卸载试验产生的最大位移值较上一载荷加载-卸载试验产生的最大位移值的增大率大于50%,则进行步骤(3);(3)以1μN为起始载荷、2~5μN为增加量设定若干载荷,载荷终点为45μN;在材料样品上进行压痕试验,根据所设定的载荷从小至大依次进行加载-卸载试验;记录每个载荷加载-卸载试验中压头产生的最大位移值并进行比较;当所选载荷加载-卸载试验产生的最大位移值较上一载荷加载-卸载试验产生的最大位移值的的增大率大于50%时,停止压痕试验,所选载荷所产生的最大位移值为亚表面损伤层厚度评估值;若未出现所选载荷加载-卸载试验产生的最大位移值较上一载荷加载-卸载试验产生的最大位移值的增大率大于50%,则进行步骤(4);(4)以1500μN为起始载荷、50~200μN为增加量设定载荷,在材料样品上进行压痕试验,根据所设定的载荷从小至大依次进行加载-卸载试验;记录每个载荷加载-卸载试验中压头产生的最大位移值并进行比较;直到所选载荷加载-卸载试验产生的最大位移值较上一载荷加载-卸载试验产生的最大位移值的增大率大于50%时停止压痕试验,所选载荷所产生的最大位移值为亚表面损伤层厚度评估值。所述步骤(2)和步骤(4)中载荷增加量为50μN、75μN、100μN、150μN、200μN其中之一。所述步骤(3)中载荷增加量为2μN、3μN、4μN、5μN其中之一。所述材料样品的表面粗糙度为50nm~400nm。所述的亚表面损伤层厚度评估值并不一定是亚表面损伤层厚度的确切值,是指该材料的亚表面损伤层厚度在该评估值以下;在进行下一工序的加工时,加工至该评估值位置所示厚度处即可,即可保证所有损伤层被去除。针对下一工序中材料去除厚度比较严格的工件,为进一步获得较为准确的亚表面损伤层厚度评估值或确切值,上述方法还可包括下述工艺步骤:(5)最大位移值为亚表面损伤层厚度评估值的载荷记为Xmax,Xmax的前一个载荷记为Xmax-1,在Xmax和Xmax-1之间设定若干载荷,以Xmax-1为始点载荷,载荷的增加量为0.1μN~1/2(Xmax-Xmax-1),终点载荷为Xmax,根据所设定的载荷从小至大依次进行加载-卸载试验;记录每个载荷加载-卸载试验中压头产生的最大位移值并进行比较;当所选载荷加载-卸载试验产生的最大位移值较上一载荷加载-卸载试验产生的最大位移值的增大率大于50%时,停止压痕试验,则所选载荷所产生的最大位移值为亚表面损伤层厚度评估值。上述步骤(5)中,载荷的增加量主要根据经步骤(1)~(4)所得的Xmax与Xmax-1的差值确定。当Xmax与Xmax-1的差值较大时,可选择较大的载荷的增加量,如10μN、20μN;当Xmax与Xmax-1的差值较小时,可选择较小的载荷的增加量,如0.1μN、0.5μN、1μN、5μN。载荷的增加量优选不小于0.1μN。若需获得更为准确的亚表面损伤层厚度评估值可缩小载荷增加量的范围,重复步骤(5)。但是当选取较小的载荷增加量时,需要测量的数据较多。为了加快检测,也可在步骤(5)中选用较大的载荷增加量,并重复上述步骤(5),逐步缩小最终Xmax与Xmax-1的差值,以获得更为准确的亚表面损伤层厚度的评估值。上述步骤(5)中,优选载荷增加量为0.1μN、0.5μN、1μN、2μN、3μN、4μN、5μN、10μN、20μN、50μN其中之一。本发明的优点:目前大多数高性能材料零件的表面粗糙度要求在50nm~400nm,均可以采用本方法,因此该方法具有广泛的适用性。其首先根据现有大部分工件亚表面损伤层厚度值的出现范围,在载荷45μN~1500μN内进行加载-卸载试验,当在这个范围内未能获得亚表面损伤层厚度评估值,则首先在载荷较小的范围即1~45μN进行测定,如该范围内也未能获得亚表面损伤层厚度评估值,则在载荷大于1500μN的范围内测定;可以有效减少试验的次数,在最短的时间内确定亚表面损伤层厚度评估值。并且采用该方法对亚表面损伤层厚度值进行评估时,虽无法得到亚表面损伤厚度的准确值且对材料的表面产生一定的破坏,但仅在材料表面产生微米尺度上的压痕,破坏的程度显著小于腐蚀及剖切方法,同时未产生对环境的破坏。附图说明为了更清楚地说明本发明实施例,下面将对实施例或现有技术描述中所需要使用的附图作简单地介绍,显而易见地,下面描述中的附图仅仅是本发明的一些实施例,对于本领域普通技术人员来讲,在不付出创造性劳动的前提下,还可以根据这些附图获得其他的附图。图1为亚表面损伤结构示意图;图2为本发明方法的流程图;图3为最大位移值随载荷的变化趋势;图4为压痕试验中压头与材料作用示意图;图5为进一步评估时最大位移值随载荷的变化趋势。具体实施方式本发明所述评估方法,首先检测材料样品表面粗糙度:若材料样品表面粗糙度的范围不在50nm~400nm内,放弃试验;若材料样品表面粗糙度的范围为50nm~400nm;则对材料样品进行压痕试验;其过程如下:首先设定载荷,以45μN为起始载荷,以50~200μN为增加量,依次设定载荷,终点载荷为1500μN;每两个相邻设定载荷间的增加量可相同也可不同;然后在材料样品上进行压痕试验,根据所设定的载荷从小至大依次进行加载-卸载试验并记录每个载荷加载-卸载试验中压头产生的最大位移值;当首次出现当所选载荷加载-卸载试验产生的最大位移值较上一载荷加载-卸载试验产生的最大位移值的增大率大于50%时,则停止实验(无需做完大于所选载荷的加载-卸载试验),则此载荷所产生的最大位移值为亚表面损伤层厚度评估值。当完成45μN~1500μN选定的所有载荷的加载-卸载试验仍未出现当所选载荷加载-卸载试验产生的最大位移值较上一载荷加载-卸载试验产生的最大位移值的增大率大于50%时,则重新设定若干载荷,其以1μN为起始载荷、以2~5μN为增加量,依次设定载荷,终点载荷为45μN,然后在材料样品上进行压痕试验,根据所设定的载荷从小至大依次进行加载-卸载试验并记录每个载荷加载-卸载试验中压头产生的最大位移值;当首次出现所选载荷产生的最大位移值较上一载荷产生的最大位移值的增大率大于50%时,则停止实验(无需做完大于所选载荷的加载-卸载试验),则此载荷所产生的最大位移值为亚表面损伤层厚度评估值。当完成1~45μN和45μN~1500μN选定的所有载荷的加载-卸载试验仍未出现当所选载荷加载-卸载试验产生的最大位移值较上一载荷加载-卸载试验产生的最大位移值的增大率大于50%时,则重新设定若干载荷,以1500μN为起始载荷,以50~200μN为增加量,依次设定载荷,然后在材料样品上进行压痕试验,根据所设定的载荷从小至大依次进行加载-卸载试验并记录每个载荷加载-卸载试验中压头产生的最大位移值;当首次出现所选载荷产生的最大位移值较上一载荷产生的最大位移值的增大率大于50%时,则停止实验,则此载荷所产生的最大位移值为亚表面损伤层厚度评估值。下面结合实施例做进一步说明,本实施例中针对某石墨样品亚表面损伤层厚度进行评估,采用表面粗糙度仪对石墨样品表面粗糙度进行检测,测量结果表明石墨样品表面粗糙度为120nm。具体评估包括如下步骤:(1)设定压痕载荷:所设定的载荷为45μN、250μN、450μN、600μN、750μN、900μN、1100μN、1300μN、1500μN。(2)在石墨样品上选取一处进行压痕试验,即根据所选载荷从小至大依次进行加载-卸载试验。所采用的压痕设备为Triboindenter压痕仪,采用压头为三棱锥形的金刚石压头,为标准的Berkovich压头,压头的棱面与中心线夹角为65.3°,棱边与中心线夹角为77.05°,针尖钝圆半径为50nm;记录每个载荷加载-卸载试验中压头产生的最大位移值,结果如图3所示。当载荷为600μN时,最大位移值增加幅度达到约114%,停止实验。本实施例为了进一步确定该实验的准确性,额外进行了载荷为750μN的加载-卸载试验,其压头产生的最大位移值结果如图3所示。可以看出,当载荷大于等于600μN时,产生的位移出现了持续增加,从而确认压头产生的位移已大于亚表面损伤层的厚度,即提高了结果的可靠性,同时避免了因试验操作不当可能导致的结果误差问题。(3)根据压痕试验中不同载荷条件下压头产生的最大位移值,当首次出现所选载荷产生的最大位移值较上一载荷的最大位移值的增大率50%以上时,此时的最大位移值即为亚表面损伤层厚度评估值。压痕试验中,最大位移值随载荷的变化趋势如图3所示。可以看出,当载荷小于450μN时,随载荷的增大产生的最大值位移值变化较小;当载荷大于450μN时,随载荷的增大最大值位移值逐步增大。当载荷大于450μN时即600μN时,最大位移值急剧增加到712.25nm(增加幅度达到约114%),因此说明该石墨试验样品的亚表面损伤层厚度的评估值为712.25nm,即该石墨试验样品的亚表面损伤层厚度不大于712.25nm。这是由于当载荷较小时,由压头产生的位错,其运动难以突破亚表面损伤层中随机分布的位错、微裂纹等组成的屏障,导致压头产生的位移主要是由损伤层内部的位错运动范围决定的,因此一定变化范围内的载荷产生的位移相近。压痕试验中压头与材料作用示意图如图4所示。当载荷大于450μN时,压痕产生的位错具有足够的能量突破亚表面损伤层的阻碍,且材料基体内部存在较大的变形空间,从而产生的位移值急剧增加(达到712.25nm)。为进一步对亚表面损伤层厚度进行精确评估,采用载荷为450μN、500μN、550μN、600μN,进行加载-卸载试验。当载荷为550μN时,产生的最大位移值出现显著增加,增大量达到97.7%。此时,亚表面损伤层厚度的评估值为673.2nm。本实施例为了进一步确定该实验的准确性,额外进行了载荷为600μN的加载-卸载试验,其压头产生的最大位移值结果如图5所示。可以看出,当载荷大于等于550μN时,产生的位移出现了持续增加,从而确认压头产生的位移已大于亚表面损伤层的厚度,即提高了结果的可靠性,同时避免了因试验操作不当可能导致的结果误差问题。采用剖切方法对石墨样品的亚表面损伤深度进行了检测,结果表明采用该方法得到的亚表面损伤深度值(约为658.4nm)与采用本发明方法得到的结果基本一致。为提高亚表面损伤层厚度评估的准确性,可在产生位移突然增加的载荷范围内,通过再次逐步缩小载荷范围及多次重复实现。