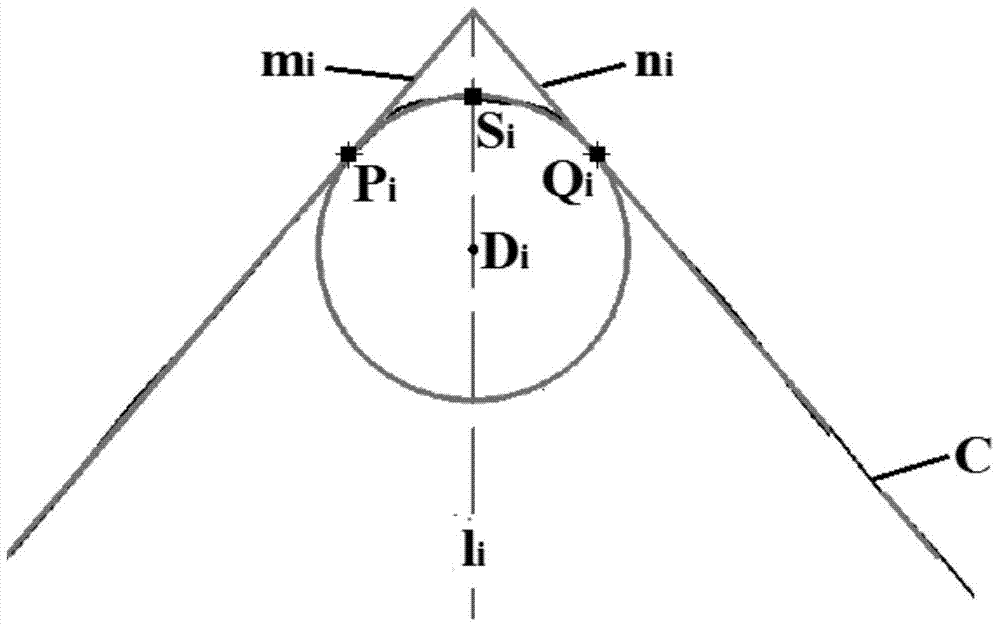
本发明属于刀具几何特征测量技术领域,涉及一种切削刃钝圆半径计算的数据选取方法。
背景技术:切削加工中,刀具磨损在所难免,刀具磨损将严重影响切削加工质量,因此必须对刀具磨损进行定量评价。目前,金属加工中广泛采用后刀面磨损带宽度VB评价刀具的磨损程度。然而刀具磨损的形式众多,尤其针对一些硬脆金属材料及复合材料切削加工,其过程中刀具切削刃刃圆钝化会对后续加工尺寸等产生极大影响,因而切削刃钝圆半径是这类加工过程中刀具磨损的主要评价指标。特别是在碳纤维增强复合材料加工中,在切削刃钝圆半径较小情况下,纤维增强相更易被切断,但刀具切削刃钝圆半径随制孔数量呈现显著上升趋势,刀具切削刃钝圆半径增大后刀具不再锋利,针对纤维增强相切断能力大幅下降,导致轴向力增大,极易诱发分层、毛刺等加工损伤。现有测量刀具切削刃钝圆半径的方法主要是采用接触式或非接触式显微测量方法,获得刀具切削刃磨损后的形貌轮廓,并拟合出钝化后的刀具切削刃钝圆,得到刀具切削刃钝圆半径。如CN201410130213专利,南京航空航天大学李亮、何宁等人发明了“微铣刀刃口钝圆测量装置及方法”,利用表面粗糙度仪探针沿微铣刀径向滑动测量刀具切削刃磨损后的轮廓,在切削刃V型微凸起图形部分绘制内切圆得到半径,并进行多次测量求其平均值,作为微铣刀切削刃钝圆半径的大小。南京航空航天大学宋树权、盐城工学院机械学院赵世田等人在“基于激光扫描共焦显微技术的刀具刃口精密测量”[J].华南理工大学学报,自然科学版,2014,42(7):86-90.中提出了一种基于激光共聚焦技术的刀具切削刃钝圆半径测量方法,利用激光扫描共聚焦显微镜获取切削刃部分形貌数据,拟合切削刃钝圆,完成切削刃钝圆半径表征。上述刀具切削刃钝圆半径测量方法均未明确如何选取参与拟合切削刃钝圆的数据范围,即进行钝圆拟合时,如何确定数据点选取范围,仅利用测量所获得的刀具切削刃轮廓数据直接拟合切削刃钝圆,而实践证明,用于拟合切削刃钝圆的数据范围的不确定性极易造成计算切削刃钝圆半径时产生较大偏差,即选取切削刃轮廓上不同数据点拟合切削刃钝圆,计算后得到的钝圆半径数值存在较大差别,而且即使采用多次测量后取平均值,也难以消除参与切削刃钝圆拟合的数据范围不确定带来的偏差。
技术实现要素:本发明为了解决现有切削刃钝圆半径计算方法无法合理选取参与拟合切削刃钝圆的数据范围的问题,发明了一种切削刃钝圆半径计算的数据选取方法。本方法在显微测量方法获取磨损后刀具切削刃形貌轮廓数据的基础上,采用迭代思想拟合计算并逐次逼近刀具前、后刀面所在直线,从而在切削刃轮廓上选取用于拟合刀具切削刃钝圆的数据范围,消除参与刀具切削刃钝圆拟合数据点范围不确定带来的误差,提高了刀具切削刃钝圆磨损测量的效率。应用本方法拟合计算刀具切削刃钝圆半径更加准确,易于实现程序化。本发明采用的技术方案是一种切削刃钝圆半径计算的数据选取方法,其特征是,本方法在显微测量获取磨损后刀具切削刃形貌轮廓数据的基础上,采用迭代思想拟合计算并逐次逼近刀具前、后刀面所在直线,采用迭代思想拟合计算并逐次逼近刀具前、后刀面所在直线,计算切削刃刃圆钝化半径和左、右距离差,直到左距离差和右距离差均达到迭代终止条件,选取用于拟合切削刃钝圆的数据,即用于切削刃钝圆半径计算的数据范围;该数据选取方法的步骤如下:1)首先采用超景深显微镜利用三维影像合成功能观测得到刀具切削刃形貌,并利用超景深显微镜软件截取刀具切削刃轮廓,提取刀具切削刃轮廓数据点曲线C;在刀具切削刃轮廓数据点曲线C中,设纵坐标最高点A的坐标为(xA,yA),刀具切削刃轮廓数据点曲线C上的左侧坐标点B和右侧坐标点W与纵坐标最高点A的纵坐标差值H为加工参数下的未变形切屑厚度;2)初始条件下拟合刀具切削刃前、后刀面所在直线令:分别为拟合前、后刀面所在直线数据点集合,其中,i=1,2,...,k,k为迭代次数,a为拟合前刀面所在直线数据点集合中数据点个数,b为拟合后刀面所在直线数据点集合中数据点个数。设mi为前刀面所在直线,ni为后刀面所在直线。前刀面所在直线mi的方程为公式(1),后刀面所在直线ni的方程为公式(2):其中,i=1,2,...,k,c=1,2,...,a。其中,i=1,2,...,k,d=1,2,...,b。角平分线为li为前刀面所在直线mi与后刀面所在直线ni所成夹角的角平分线;交点Si为角平分线li与刀具切削刃轮廓数据点曲线C的相交点;内切圆Di为过交点Si作与前刀面所在直线mi及后刀面所在直线ni相切的内切圆,内切圆Di与前刀面所在直线mi和后刀面所在直线ni的切点Pi、Qi分别称为左切点Pi和右切点Qi,其中,i=1,2,...,k,k为迭代次数。3)迭代逼近计算刀具前、后刀面所在直线提取刀具切削刃轮廓数据点曲线C上介于纵坐标最高点A和左侧坐标点B之间的数据点,作为拟合前刀面所在直线数据点集合:提取刀具切削刃轮廓数据点曲线C上介于纵坐标最高点A和右侧坐标点W之间的数据点,作为拟合后刀面所在直线数据点集合取i=1时,用通过公式(1)、(2),利用最小二乘法拟合前刀面所在直线m1和后刀面所在直线n1。作前刀面所在直线m1和后刀面所在直线n1所成夹角的角平分线l1,角平分线l1与刀具切削刃轮廓数据点曲线C交于交点S1,过交点S1作与前刀面所在直线m1及后刀面所在直线n1相切的内切圆D1,得到左切点P1以及与右切点Q1。保证拟合前刀面所在直线数据点集合中数据点个数a和拟合后刀面所在直线数据点集合中数据点个数b不变,依据参与拟合前刀面所在直线的数据点集合和后刀面所在直线的数据点集合,将数据点依次沿纵坐标方向Y向下移动一个坐标位置,i=2,得到参与下一次拟合前、后刀面所在直线的数据点集合:利用公式(1)、(2)拟合前刀面所在直线m2和后刀面所在直线n2,作前刀面所在直线m2和后刀面所在直线n2所成夹角的角平分线l2,角平分线l2与刀具切削刃轮廓数据点曲线C交于交点S2,过交点S2作与前刀面所在直线m2及后刀面所在直线n2相切的内切圆D2,得到左切点P2以及与右切点Q2。4)迭代终止判别设Ei为左切点Pi与Pi+1间的左距离差;Gi为右切点Qi与Qi+1间的右距离差。计算左切点P1与左切点P2之间的左距离差E1,然后计算右切点Q1和右切点Q2之间的右距离差G1;重复上述拟合计算过程进行迭代计算,直到左距离差Ei和右距离差Gi均达到迭代终止条件,即公式(3):Ei<g,Gi<g(3)g为迭代终止条件,g值比测量刀具切削刃形貌数据所用显微镜分辨率小一个数量级。达到迭代终止条件后,提取此时位于左切点Pi和右切点Qi之间的数据点,作为拟合刀具切削刃钝圆数据点集合,依据拟合刀具切削刃钝圆数据点集合,采用最小二乘法拟合刀具切削刃钝圆U,计算得到刀具切削刃钝圆半径R。本发明的效果和益处是采用迭代方法拟合逼近确定到刀具前、后刀面所在直线,并确定用于拟合刀具切削刃钝圆数据点范围,消除参与刀具切削刃钝圆拟合数据点范围不确定带来的误差,应用本数据选取方法选取用于切削刃钝圆半径计算的数据,据此数据拟合切削刃钝圆,计算刀具切削刃钝圆半径更加准确,易于实现程序化,有效提高了刀具切削刃钝圆磨损测量的效率。附图说明图1是刀具切削刃轮廓图,其中,A-纵坐标最高点,B-左侧坐标点,W-右侧坐标点,C-刀具切削刃轮廓数据点曲线,H-纵坐标差值,X-横坐标,Y-纵坐标。图2是刀具前、后刀面所在直线拟合示意图,其中,C-刀具切削刃轮廓数据点曲线,li-角平分线,mi-前刀面所在直线,ni-后刀面所在直线,Di-内切圆,Si-交点,Pi-左切点,Qi-右切点。图3是前后刀面夹角为90°时刀具切削刃钝圆半径拟合结果图,图4是后刀面间夹角为75°时刀具切削刃钝圆半径拟合结果图。其中,R-刀具切削刃钝圆半径,U-刀具切削刃钝圆,X-横坐标方向,Y-纵坐标方向。图5是切削刃钝圆半径计算的数据选取方法流程图。具体实施方式以下结合技术方案和附图详细叙述本发明的具体实施方式。以钻削碳纤维增强复合材料的双顶角钻头的某一切削刃为测量和拟合计算对象,按照图5所示的操作流程选取用于刀具切削刃钝圆半径计算的数据,据此数据拟合切削刃钝圆并对刀具切削刃钝圆半径R进行计算。首先采用超景深显微镜利用三维影像合成功能观测得到刀具切削刃形貌,并利用超景深显微镜软件截取刀具切削刃轮廓,提取刀具切削刃轮廓数据点曲线C,如图1、2所示。刀具切削刃轮廓数据点曲线C列于表1,X、Y分别为横、纵坐标方向。表1刀具切削刃轮廓数据确定刀具切削刃轮廓数据点曲线C上的纵坐标最高点A坐标为序号为164的坐标点(30.97,34.99)。刀具切削刃轮廓数据点曲线C上的左侧坐标点B和右侧坐标点W与纵坐标最高点A的纵坐标差值H均为一定加工参数下的未变形切屑厚度。本具体实施例中未变形切屑厚度为7.217μm,因此纵坐标差值H为7.217μm。分别为拟合前、后刀面所在直线数据点集合,其中,i=1,2,...,k,k为迭代次数,a为拟合前刀面所在直线数据点集合中数据点个数;b为拟合后刀面所在直线数据点集合中数据点个数。提取刀具切削刃轮廓数据点曲线C上介于纵坐标最高点A和左侧坐标点B之间的数据点,作为拟合前刀面所在直线数据点集合,即序号为125~164的数据点。其中,a=40。提取刀具切削刃轮廓数据点曲线C上介于纵坐标最高点A和右侧坐标点W之间的数据点,作为拟合后刀面所在直线数据点集合,即序号为165~206的数据点,其中,b=42。mi为前刀面所在直线,ni为后刀面所在直线,基于上一步提取出的数据点,采用最小二乘法分别拟合前刀面所在直线m1及后刀面所在直线n1。参照前刀面所在直线mi公式(1),后刀面所在直线ni公式(2),令i=1,c=1,2,...,40,d=1,2,...,42,得到前刀面所在直线m1方程和后刀面所在直线n1方程为:作前刀面所在直线m1和后刀面所在直线n1所成夹角的角平分线l1,角平分线l1与刀具切削刃轮廓数据点曲线C交于交点S1,过交点S1作与前刀面所在直线m1及后刀面所在直线n1相切的内切圆D1,得到左切点P1以及与右切点Q1。本实施例中,左切点P1坐标为(29.138,34.)(29.138,34.1953),右切点Q1坐标为(33.046,34.)。保证拟合前刀面所在直线数据点集合中数据点个数a=40和拟合后刀面所在直线数据点集合中数据点个数b=42不变,将参与拟合前刀面所在直线的数据点集合和参与拟合后刀面所在直线数据点集合中的数据点依次沿纵坐标方向Y向下移动一个位置,i=2,得到参与下一次拟合前、后刀面所在直线的数据点集合:即序号为124~163和166~207的数据点。参照前刀面所在直线mi方程(1),后刀面所在直线ni方程(2),c=1,2,...,40,d=1,2,...,42,得到前刀面所在直线m2方程和后刀面所在直线n2方程为:作前刀面所在直线m2和后刀面所在直线n2所成夹角的角平分线l2,角平分线l2与刀具切削刃轮廓数据点曲线C交于交点S2,过交点S2作与前刀面所在直线m2及后刀面所在直线n2相切的内切圆D2,得到左切点P2以及与右切点Q2。左切点P2以及右切点Q2坐标分别为(28.9796,34.0713)、(33.21,34.1351)。计算左切点P1与左切点P2之间的左距离差E1,然后计算右切点Q1和右切点Q2之间的右距离差G1,左距离差E1和右距离差G1分别为0.1812μm、0.1845μm。重复上述迭代拟合计算过程,直到左距离差Ei和右距离差Gi均达到迭代终止条件。本实施例中,测量刀具切削刃形貌所用显微镜分辨率为0.19μm,g值比测量刀具切削刃形貌数据所用显微镜分辨率小一个数量级,因此选择迭代终止条件g=0.02μm。迭代22次后,迭代终止。即此时,E22=0.0102μm,G22=0.0166μm;E22<0.02μm,G22<0.02μm。提取此时位于左切点Pi和右切点Qi之间的数据点,作为拟合刀具切削刃钝圆数据点集合,即序号为142~187的数据点,基于此拟合刀具切削刃钝圆数据点集合,采用最小二乘法拟合刀具切削刃钝圆U,获得刀具切削刃钝圆半径R=4.5209μm。为验证本发明方法的准确性,通过高精度的作图软件,精确作出刀具前后刀面夹角分别为90°和75°时,已知刀具切削刃钝圆半径为8μm的两种刀具切削刃轮廓。并采用本描述方法选取用于切削刃钝圆半径计算的数据,据此数据拟合切削刃钝圆并计算刀具切削刃钝圆半径。经计算,两种不同刀具切削刃轮廓下,刀具切削刃钝圆半径分别为:8.0002μm、7.9999μm,结果如图3、4所示。在刀具前后刀面夹角为90°情况下,依据本专利方法确定的拟合刀具切削刃钝圆的数据点范围为序号为218~266,若采用序号为190~294的数据点,刀具切削刃钝圆半径为10.1494μm,因此,拟合切削刃钝圆数据点选取范围不同可造成拟合后切削刃钝圆半径产生较大偏差。本发明采用迭代思想逐次逼近并确定刀具前、后刀面所在直线,从而确定参与拟合刀具切削刃钝圆的数据点范围,消除切削刃钝圆拟合数据点范围不确定带来的计算切削刃钝圆半径时的误差,选取用于切削刃钝圆半径计算的数据拟合切削刃钝圆,并计算刀具切削刃钝圆半径,结果真实、准确,能够对后续刀具切削刃钝圆磨损研究起到指导性作用。