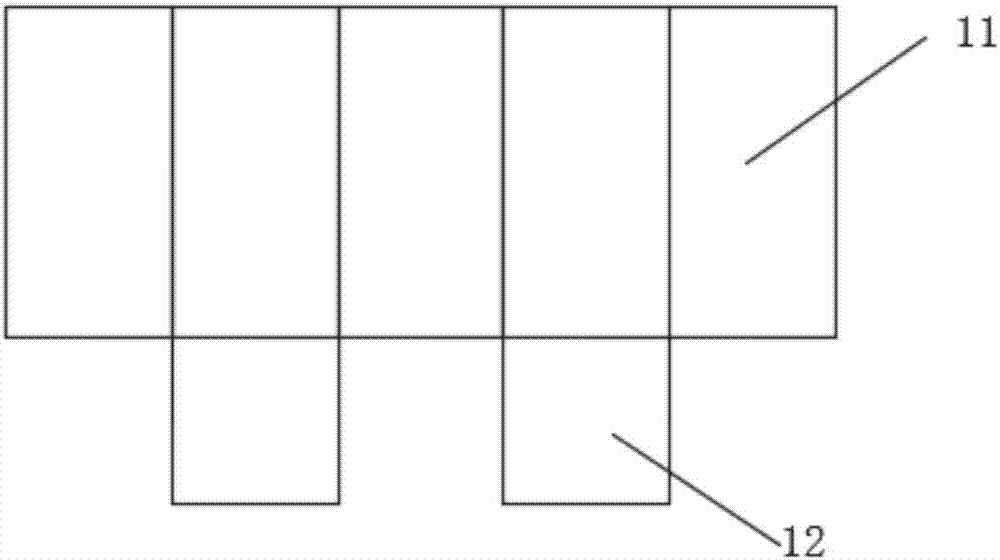
本申请涉及一种闪烁晶体探测器阵列模块,属于闪烁晶体探测领域。
背景技术:
:闪烁晶体探测器是利用电离辐射在某些物质中产生的闪光来进行探测的闪烁探测器具了探测效率高,分辨短等特点,被广泛应用于核医学、安全检查、高能物理和宇宙射线探测的研究中。闪烁晶体探测器通常利用能够有效阻挡和吸收电磁波辐射并与电磁波辐射产生发光作用的闪烁晶体作为探测材料。闪烁晶体探测器模块是由一些相同大小的单根晶体阵列构成的,每根晶体之间夹有反射膜以实现分光效果,用于识别每根晶体的位置。当高能射线入射到闪烁晶体内,根据射线能量,晶体有效原子系数和密度的不同,与晶体发生不同比例的光电效应、康普顿散射效应及电子对效应,将能量沉积在闪烁晶体中,被激发的闪烁晶体退激发出闪烁光。利用光电探测器如pmt(photomu1tip1iertube,光电倍增管)将位于可见光区或紫外光区的闪烁光经过光电转换和倍增,形成脉冲信号。脉冲信号强度反映了高能射线的能量;脉冲信号发生的时间反映了高能射线的入射时间;脉冲信号在多个光电信增管中的强度分配反映了高能射线的入射位置等。当高速度运动的电子流轰击某些固体物质时,被轰物体能产生肉眼不可见的x光,x光的穿透本领很大,无论是人体的组织,还是几厘米厚的钢板,它们都能畅通无阻,因此可用来进行医疗诊断、工业探伤和物质分析等,这些能在x光照射下激发出荧光来的材料叫做闪烁材料,当然闪烁材料除了在x光照射下会发出荧光外,其他像放射性同位素蜕变产生的高能射线如α射线、β射线照射它时也会发出荧光来,人们利用闪烁材料的这种特性做成了测量各种射线的探测器,即当高能射线照射到探测器上后,闪烁材料便发出荧光,射线愈强,发出的荧光愈强,这荧光被光电转换系统接收并转变成电信号,经过电子线路处理后,便能在指示器上指示出来,因此人们将这种探测器比喻为看得见x光和其他高能射线的"眼睛"。目前,闪烁晶体探测器模块的一般是将多个晶体片与反射膜胶粘在一起形成方形模块,然后沿着垂直于晶体表面的方向将模块切成片,之后再将切成的晶体片片再次与反射膜粘在一起形成一个晶体阵列。在粘贴晶体片和反射膜时通常采用液态的光敏固化胶或者环氧胶,在胶水固化之前,模块内部晶体之间会由于相互挤压摩擦使得反射膜容易发生滑动从而造成偏移。这将会使得闪烁晶体探测器模块局部无法识别晶体的位置,导致残次品的出现。由于在制作过程中,闪烁晶体模块中的反射膜滑动问题无法通过肉眼发现,也无法借助观测仪器从外部进行观察,只能等待紫外胶水或者环氧胶胶水固化后采用实验手段进行测量,除此之外,没有其他更好的办法能够应对制作过程中的闪烁晶体阵列出现的反射膜滑动问题。而待胶水固化后才发现反射膜出现滑动偏移,这个时候已经无法再对闪烁晶体模块采取有效的补救措施。此外,常规的技术还存在另一个问题,形成的方形模块在进行切割的过程中容易出现切割尺寸偏差。目前大多数晶体切割采用的多线切割机都存在着大长度切割尺寸会偏移的问题,而这种问题是由于机械原因产生,无法通过设计或者工装来克服。因此,采用常规技术产生的切割尺寸偏差问题将难以解决,而这样的偏差将导致切出的整片无法使用,产生大量的废弃片。这将使制作成本大幅度提高,最终影响阵列模块的制作成功率。因此需要采取一种全新的思路来解决闪烁晶体探测器模块在制作过程中出现的问题。技术实现要素:根据本申请的一个方面,提供了一种闪烁晶体单元片,该闪烁晶体单元片由闪烁晶体排列在具有凹陷空间的包裹体中形成,避免了内部晶体之间会由于相互挤压摩擦使得反射膜容易发生滑动从而造成的偏移,从而得到闪烁晶体排列精度高且无滑动的闪烁晶体单元片,避免了残次品的产生。所述闪烁晶体单元片包括闪烁晶体和包裹体,所述包裹体具有至少一个凹型部,所述闪烁晶体位于所述凹型部内。优选地,所述包裹体具有至少一个朝上的凹型部和至少一个朝下的凹型部。优选地,所述包裹体以s型弯折的方式形成交替排列的朝上的凹型部和朝下的凹型部。本申请中,朝上/朝下,是相对方向,即以其中一个凹型部的开口方向为朝上,则与之开口方向相反的即为朝下。优选地,所述凹型部的截面为矩形,所述闪烁晶体至少一个截面为矩形且与所述凹型部的尺寸匹配,所述闪烁晶体嵌入且粘接固定于所述凹型部。优选地,所述包裹体为反射膜,所述反射膜通过划槽处理产生能够折叠的槽痕,所述槽痕的间距为0.1mm至1mm且与所述闪烁晶体侧面宽度相同,所述槽痕两边的反射膜能够通过槽痕折成直角并形成交替排列的朝上的凹型部和朝下的凹型部;所述凹型部由底面和两个与所述底面垂直的侧面构成。优选地,所述闪烁晶体包括碘化钠、锗酸铋、硅酸钇镥、掺铊碘化铯中的至少一种,所述包裹体包括金属反射膜、涂层树脂反射膜等中的至少一种。根据本申请的又一个方面,提供了一种闪烁晶体阵列模块,由上述一个方面的闪烁晶体单元片堆叠排列而成。由于闪烁晶体单元片中的晶体包裹在具有凹陷空间的包裹体中,避免了内部晶体之间会由于相互挤压摩擦使得反射膜容易发生滑动从而造成的偏移,从而得到闪烁晶体排列精度高且无滑动且精确对齐的闪烁晶体阵列模块。另外,闪烁晶体阵列模块中的晶体均由包裹体隔开,避免了相互影响,避免了残次品的产生。该闪烁晶体阵列模块包括至少两个堆叠排列的上述一个方面的任一种所述闪烁晶体单元片;一个所述闪烁晶体单元片上的任意一个闪烁晶体,与相邻的另一个所述闪烁晶体单元片上距离最近的闪烁晶体间由包裹体的至少一部分隔开。由于反射膜的伸出部具有定位功能,能够很好地保证晶体单元之间的间隙优选地,所述包裹体包括定位部,一个闪烁晶体单元片上的定位部与相邻的另一个闪烁晶体单元片上的定位部对齐;所述定位部为所述凹型部的底面延伸部分且与所述凹型部中的闪烁晶体的通光面尺寸一致,所述通光面为闪烁晶体与所述凹型部接触面垂直的端面。进一步优选地,所述包裹体包括第一定位部和第二定位部,一个所述闪烁晶体单元片上的第一定位部与相邻的另一个所述闪烁晶体单元片上第一定位部对齐,一个所述闪烁晶体单元片上的第二定位部与相邻的另一个所述闪烁晶体单元片上第二定位部对齐。根据本申请的又一个方面,提供了一种闪烁晶体探测器,包括由上述一个方面的闪烁晶体单元片堆叠排列而成的闪烁晶体阵列模块或上述一个方面的闪烁晶体阵列模块。由于闪烁晶体单元片中的晶体包裹在具有凹陷空间的包裹体中,避免了内部晶体之间会由于相互挤压摩擦使得反射膜容易发生滑动从而造成的偏移,从而得到闪烁晶体排列精度高且无滑动且精确对齐的闪烁晶体阵列模块。另外,闪烁晶体阵列模块中的晶体均由包裹体隔开,避免了相互影响,避免了残次品的产生,提高了所述闪烁晶体探测器的测量精度和可靠性。该闪烁晶体探测器,包括上述一个方面的所述闪烁晶体单元片或上述一个方面的所述闪烁晶体阵列模块,所述闪烁晶体探测器包括闪烁探测部,所述闪烁探测部用于探测所述闪烁晶体单元片或所述闪烁晶体阵列模块产生的闪烁。本申请能产生的有益效果包括:1)本申请所提供的闪烁晶体单元片,闪烁晶体排列在具有凹陷空间的包裹体中形成,避免了内部晶体之间会由于相互挤压摩擦使得反射膜容易发生滑动从而造成的偏移,从而得到闪烁晶体排列精度高且无滑动的闪烁晶体单元片,避免了残次品的产生。2)本申请所提供的闪烁晶体阵列模块和探测器,闪烁晶体阵列模块中的晶体均由包裹体隔开,避免了相互影响,避免了残次品的产生,提高了在闪烁晶体探测器中测量精度和可靠性。附图说明图1为本申请一种实施方式中晶体单元结构示意图。图2为本申请一种实施方式中反射膜单元结构示意图。图3为本申请一种实施方式中反射膜单元尺寸示意图。图4为本申请一种实施方式中反射膜单元翻折后具体的凹陷空间结构示意图。图5为本申请一种实施方式中单排晶体阵列效果图。图6为本申请一种实施方式中单排晶体阵列效果图。图7为本申请一种实施方式中100mm*100mm*300mm闪烁晶体阵列模块正面图。图8为本申请一种实施方式中100mm*100mm*300mm闪烁晶体阵列模块背面图。部件和附图标记:11-主体部,12-伸出部,21-朝上凹型空间,22-朝下凹型空间,51-反射膜单元主体部,52-闪烁晶体,71-闪烁晶体,72-反射膜单元主体部,81-反射膜单元主体部,82-反射膜单元伸出部。具体实施方式下面结合实施例详述本申请,但本申请并不局限于这些实施例。如无特别说明,本申请的实施例中的原材料均通过商业途径购买。实施例1闪烁晶体单元片本实施例中闪烁晶体的尺寸为50mm*50mm*100mm,可参见图1,其中50mm*50mm的端面为通光面,其余面为侧面。本实施例中包裹体为反射膜单元,如图2所示,由主体部11和定位部12组成,主体部11的尺寸为250mm*100mm、定位部12尺寸为50mm*50mm。将闪烁晶体的每个侧面以及与侧面垂直的通光面均匀地涂上胶水,反射膜单元按图2和图3所示的折痕进行翻折,形成具有朝上凹型空间21和朝下凹型空间22,可参见图4。将涂抹好胶水的晶体整齐地排列在反射膜单元所形成的凹型空间中,将闪烁晶体的侧面与反射膜单元的主体部11粘结,闪烁晶体的通光面与伸出部对齐,使其能够覆盖住晶体单元的通关面,可参见图5。形成一排尺寸为50mm*100mm*100mm的闪烁晶体单元片,可参见图6,其中反射膜单元主体部51包裹着两个闪烁晶体52。得到的闪烁晶体单元片记为a1#。需要说明的是,本实施例中,在将晶体单元侧表面与反射膜主体部进行粘贴后,与侧表面垂直的通光面与反射膜伸出部可以不必马上进行粘贴,改由阵列制作最后,统一将伸出部与相应的晶体单元通光面进行粘贴接触处理。实施例2闪烁晶体阵列模块制作两个实施例1的闪烁晶体单元片a1#,将两个闪烁晶体单元片a1按照图7的方式堆叠,并在两个闪烁晶体单元片之间涂抹胶水,通过精密平口钳夹具夹紧固化。图7中上下两个闪烁晶体单元片中的反射膜单元主体部71分别包裹着四个闪烁晶体72。固化后可获得100mm*100mm*100mm的闪烁晶体阵列模块,如图8所示,上下两个闪烁晶体单元片中的反射膜单元主体部81分别包裹着四个闪烁晶体82。得到的闪烁晶体阵列模块记为b1#。需要说明的是,本实施例中,在将晶体单元侧表面与反射膜主体部进行粘贴后,与侧表面垂直的通光面与反射膜伸出部可以不必马上进行粘贴,改由阵列制作最后,统一将伸出部与相应的晶体单元通光面进行粘贴接触处理。实施例3闪烁晶体阵列模块闪烁晶体单元片的制作方法同实施例1,闪烁晶体阵列模块的制作方法同实施例2,只是其中的闪烁晶体、尺寸、阵列构成数量等参数不同,详见表1。表1阵列模块序号闪烁晶体反射膜b3-1#碘化钠金属反射膜b3-2#锗酸铋涂层树脂反射膜b3-3#硅酸钇镥金属反射膜b3-4#掺铊碘化铯金属反射膜b3-5#碘化钠金属反射膜实施例4将多个闪烁晶体片与反射膜胶粘在一起形成方形模块,然后沿着垂直于晶体表面的方向将模块切成片,之后再将切成的晶体片片再次与反射膜粘在一起形成一个晶体阵列。在粘贴晶体片和反射膜时通常采用液态的环氧胶固化。得到本对比例的闪烁晶体阵列模块记为db1。实施例5闪烁晶体探测器分别采用100个实施例2的闪烁晶体阵列模块b1#、100个实施例3的闪烁晶体阵列模块b3-1#和100个实施例4的闪烁晶体阵列模块db1#制造300个闪烁晶体探测器,分别记为闪烁晶体探测器c1#、c2#和dc1#。闪烁晶体探测器包括闪烁探测部,闪烁探测部用于探测所述闪烁晶体单元片或所述闪烁晶体阵列模块产生的闪烁。以β射线扫描照射每一个闪烁晶体,获取闪烁探测部的信号,以评价闪烁晶体探测器的工作状态。测试中有至少一个闪烁晶体至少一次收不到闪烁信号记为一个不合格。实施例2、实施例3-1和对比例1的不合格率见表2。表2以上所述,仅是本申请的几个实施例,并非对本申请做任何形式的限制,虽然本申请以较佳实施例揭示如上,然而并非用以限制本申请,任何熟悉本专业的技术人员,在不脱离本申请技术方案的范围内,利用上述揭示的技术内容做出些许的变动或修饰均等同于等效实施案例,均属于技术方案范围内。当前第1页12