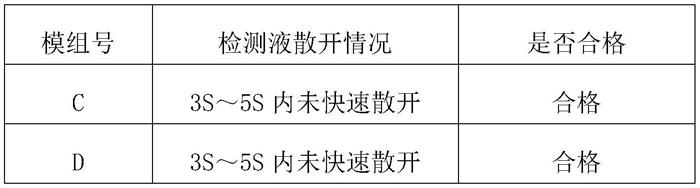
1.本发明属于熔模铸造领域,具体涉及一种检验模组除油质量的方法。
背景技术:2.随着熔模铸造行业的发展,现今,对铸件的尺寸精度和表面粗糙度要求日益提高。而铸件 的尺寸精度和表面粗糙度直接受蜡模和型壳的影响。因此,保证蜡模模组质量至关重要。良好 的型壳要求蜡模模组表面无多余油脂,有良好的润湿性。但常规的模型蜡是憎水的,在蜡模表 面很难进行涂料涂挂,因此,需要进行模组除油蚀刻,除去蜡模表面多余油脂,保证制壳料浆 均匀涂挂蜡模表面,避免撒砂时砂粒直接接触蜡模表面或堆聚,浇注时形成麻点或粘砂等缺陷。 但是,由于型壳面层涂挂质量受零件结构及每批次涂料粘结剂粘度影响,涂挂质量不稳定,且 模组表面状态缺少检查方法,导致制壳浇注后,表面缺陷才暴露出来,致使铸件报废。
技术实现要素:3.本发明的目的在于克服上述不足,提供一种检验模组除油质量的方法,用于判定模组除油 情况,在制壳、浇注前判定蜡模模组表面质量是否合格,减少因为除油不净导致的铸件表面缺 陷,提升产品合格率。
4.为了达到上述目的,本发明包括以下步骤:
5.s1,根据硅溶胶中sio2质量分数、粒子比表面积及粒径范围,判断除油检测液的粘度范 围及特定结构零件的适用性;
6.s2,根据sio2质量分数、粒子比表面积及粒径范围,判断模组表面质量;
7.s3,确定除油检测液的试验研究对象;
8.s4,制备除油检测液;
9.s5,清洁待检模组表面;
10.s6,采用除油检测液对待检模组进行除油;
11.s7,对除油后的情况进行判定。
12.s1中,选用硅溶胶和润湿剂作为除油检测液主要成分。
13.硅溶胶和润湿剂的体积比为1:5
‰
14.s3中,试验研究对象采用大弯扭型面、大平面的蜡模件或具有内腔及盲孔的结构的零 件。
15.s4中,将25kg硅溶胶与125g润湿剂混合,搅拌均匀后静置,待液体表面大量气泡消失 后,完成除油检测液的制备。
16.s5中,若待检模组表面存在多余物,使用压缩空气吹干净。
17.s6中,将待检验模组置于除油检测液中2~3s,或将除油检测液泼洒至待检模组表面。
18.s7中,若除油检测液在3~5s内未散开,则表明模组表面达到蚀刻效果,具备制壳
料浆 涂挂要求,除油合格;若除油检测液在3s~5s内散开,则表明除油不合格。
19.与现有技术相比,本发明以硅溶胶作为粘结剂为主的涂料制壳面层涂挂过程,提炼一种检 验模组表面除油质量是否达到制壳工序涂料涂挂要求的方法。并将其作为一种检验手段,从源 头甄别产品质量,避免不合格模组流入后工序,减少因为除油不净导致的铸件报废,提高产品 质量、提升产品合格率。本发明节能环保、经济效益高,不需采购额外试剂及原料,使用制壳 面层料浆作为原材料,操作方便,现场实用性强。
具体实施方式
20.下面结合实施例对本发明做进一步说明。
21.本发明包括以下步骤:
22.s1,根据硅溶胶中sio2质量分数、粒子比表面积及粒径范围,判断除油检测液的粘度范 围及特定结构零件的适用性;为保证检验过程不影响模组质量及后续制壳,且该模拟检测试 验与制壳料浆涂挂的工艺性相符,选用硅溶胶和润湿剂作为除油检测液主要成分,硅溶胶和 润湿剂的体积比为1:5
‰
23.s2,根据sio2质量分数、粒子比表面积及粒径范围,判断模组表面质量;sio2含量越 高,粘度值越大,粒子比表面积越大,粘度越大,零件结构越复杂,要求粘结剂粘度越小, 因此根据以上等参数进行试验,判断模组表面质量。
24.所需工装如下:
25.盛放除油检测液不锈钢筒尺寸:φ420mm
×
400mm;
26.除油检测液主要成分及用量:
27.所需硅溶胶体积量:选取规格为25kg/桶的硅溶胶1桶。
28.所需润湿剂体积量:使用量筒,按照硅溶胶:润湿剂=1:5
‰
(体积比)配制检测溶液备 用。
29.s3,确定除油检测液的试验研究对象;大弯扭型面或大平面的蜡模件表面除油时,由于 蜡模性质为憎水亲油型,水性除油剂在大平面上流动较快,容易出现表面除油不净的现象。 同时,具有内腔及盲孔的结构的零件,容易存在除油剂接触不到导致除油不净的现象。因 此,本次选取具有此两类结构的零件作为试验件更具代表性。
30.s4,制备除油检测液;按照硅溶胶+5
‰
润湿剂(体积比)配制除油检测液。首先,将 25kg硅溶胶倒入准备好的不锈钢桶中,使用量筒量取125g润湿剂,倒入装有硅溶胶的不锈 钢桶中搅拌至均匀,静置,待液体表面大量气泡消失后,方可用于模组检验。
31.s5,清洁待检模组表面;用于除油检测的模组,应避免表面出现蜡屑、水渍等多余物干 扰。若表面存在多余物,应使用压缩空气吹干净。
32.s6,采用除油检测液对待检模组进行除油;经反复试验,模拟制壳面层涂挂过程,总结 下述方法判断较为准确:将待检验模组置于装有除油检测液的不锈钢桶中保持2s~3s,或将 检测液泼洒至待测零件表面,再观察模组表面检测液流动情况。
33.s7,对除油后的情况进行判定。若检测液在3s~5s内未快速散开,表明模组表面达到 蚀刻效果,具备制壳料浆涂挂要求,除油合格;反之,若蜡模表面的检测液在3s~5s内快 速散开,则表明除油不合格。
34.实施例1:
35.某机高压涡轮工作叶片弯扭大,叶型截面曲线曲率大,为保证制造工艺性,面层主要成分 采用快干硅溶胶和锆英粉,其中硅溶胶中sio2质量分数选取在10%~35%,粒子比表面积在50 m2/g~400m2/g,粒径范围一般在5nm~100nm即可。实际生产过程中,由于该叶片叶身面积 大,缘板转接部位呈锐角,液体流经过程中易出现死角,导致除油质量波动性大,铸件最终表 面质量差,合格率低的问题。
36.针对以上问题,对该铸件模组进行除油检查,1、确定成分及原料:结合该零件结构确定 除油检测液成分为对应粘结剂的类面层料浆硅溶胶+润湿剂。去除制壳工序面层中的锆英粉, 只选取硅溶胶和润湿剂按照溶胶:润湿剂=1:5
‰
(体积比)量取润湿剂,配制检测液。2、配 制检测溶液:按照模组高度选取φ420mm
×
400mm的不锈钢桶作为容器,将25kg硅溶胶倒入 准备好的不锈钢桶中,按照硅溶胶:润湿剂=1:5
‰
(体积比),使用量筒量取润湿剂125g,将 润湿剂倒入搅拌至均匀,静置,待液体表面大量气泡消失后待用。3、对选定的四组模组表面 进行质量确认,去除蜡屑、水渍等多余物。4、进行除油情况试验,将待检验模组a置于装有 除油检测液的不锈钢桶中保持2s~3s,观察到检测液未在3s~5s内快速散开,表示a模组 表面除油彻底,达到制壳要求;再将模组b置于装有除油检测液的不锈钢桶中保持2s~3s, 观察到检测液在3s~5s内快速散开,表示b模组表面除油不彻底,未达到制壳要求,试验结 果记录对比见表1。
37.表1
38.模组号检测液散开情况是否合格a3s~5s内未快速散开合格b3s~5s内快速散开不合格
39.实施例2:
40.某机高压涡轮导向叶片存在大平面及盲孔,为保证制造工艺性,面层主要成分采用硅溶胶 和锆英粉,其中硅溶胶中sio2质量分数选取在10%~25%,粒子比表面积在50m2/g~300m2/g, 粒径范围一般在5nm~100nm即可。实际生产过程中,由于该叶片叶身存在大平面,且下缘板 处存在定位盲孔,液体流经过程中易出现死角,导致除油质量波动性大,铸件最终表面质量差, 合格率低的问题。
41.针对以上问题,对模组进行除油检查:1、确定检测液成分2、按照比例配制该零件结构对 应检测液。3、对选定的四组模组表面进行质量确认,去除蜡屑、水渍等多余物。4、进行除油 情况试验,将检测液泼洒至待测模组c表面,观察模组表面检测液流动情况,发现检测液未在 3s~5s内快速散开,说明c模组表面除油彻底,达到制壳要求;将检测液泼洒至待测模组d 表面,观察检测液在3s~5s内未快速散开,说明d模组表面除油彻底,达到制壳要求;将检 测液泼洒至待测模组e表面,观察检测液在3s~5s内快速散开,说明e模组表面除油不彻 底,未达到制壳要求。试验结果记录对比见表2。
42.表2
[0043][0044][0045]
目前,该方法现已形成有效文件,同时固化至相关生产环节中,结果表明,采用该方法检 测后,能针对性的根据不同结构适用面层涂料粘度配制检测液,准确筛查表面存在除油不彻底 缺陷的问题模组,减少后工序抱怨,提高产品质量,能有效在本工序对问题模组进行控制,降 低制造成本。按照本发明方法追踪后续产品质量,得到表3及表4。表3追溯的是未采用该检 测方法铸件质量情况表,表4追溯的是采用该方法铸件质量情况表。
[0046]
表3
[0047][0048]
表4
[0049][0050]
从表3、表4中可以看出,采用该发明进行模组控制,对后续铸件产品质量有明显提升。 同时,该发明不针对特定材料、结构、领域,具有一定的可推广性:
[0051]
(1)除硅溶胶制壳材料外,该发明还可应用于其他粘结剂构成的特定结构型壳的模组表 面质量的检查。
[0052]
(2)除航空发动机熔模铸造行业外,该发明还可应用于军民融合或其他民用熔模铸造行 业的通用模组表面质量检查。
[0053]
本发明是根据具体的优选实施方案进行编写,不能将本发明的具体实施方案认定只局限于 本说明,对发明所述技术领域的技术人员来讲,在不脱离本发明总体构思的前提下,可以派生 出一些系列方法,做若干简单的推演及替换,都应视为所属本发明所交的权利要求书确定的专 利保护范围。