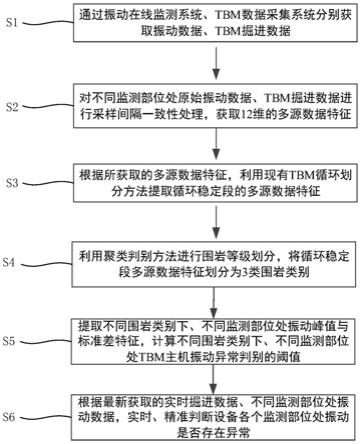
一种tbm主机振动异常自适应判别方法及tbm
技术领域
1.本发明提供了一种tbm主机振动异常自适应判别方法及tbm,属于盾构设备检测技术领域。
背景技术:2.当tbm进入至不同地层时,滚刀与岩石相互作用产生的切削力发生变化,此时通过刀轴依次向刀盘、驱动箱、主梁、撑靴传递的振动的幅值也随之变化。因此,不同围岩类别下tbm主机振动异常判断的阈值也需要自适应变化。
3.然而,现有tbm振动状态分析大多侧重于在线监测及振动数据实时获取,针对tbm主机振动异常判别的研究较少。另一方面,现有用于判别tbm主机振动异常的阈值通常设置为某一定值,当tbm遇到地层变化需要变更振动阈值时,工程师需现场跟踪一段时间,再根据当前地层条件下设备的振动情况对阈值进行人为修改。
4.综上来看,现有tbm主机振动异常判别方法不能随岩体变化自适应调整阈值,容易出现tbm主机振动异常漏报、误报警现象。
技术实现要素:5.本发明的目的在于提供一种tbm主机振动异常自适应判别方法及tbm,用于解决在判别tbm主机振动是否异常时不能随围岩变化实时调整异常判断的阈值导致漏报、误报警的问题。
6.为了实现上述目的,本发明提供了一种tbm主机振动异常自适应判别方法,包括如下步骤:
7.1)获取tbm历史数据,所述tbm历史数据包括历史掘进数据和若干监测位置处的历史振动数据;
8.2)从历史振动数据中提取反映对应监测位置处振动特性的振动特征,还从历史掘进数据中提取反映掘进特性的掘进特征,将时间上相互对应的振动特征和掘进特征合并,形成多源数据特征;
9.3)采用聚类判别方法,根据多源数据特征进行围岩类别划分,得到若干组围岩类别;
10.4)从不同围岩类别的多源数据特征中提取不同监测位置处的振动特征,将不同围岩类别、不同监测位置处的振动特征的设定百分位数作为判断tbm在对应围岩类别、对应监测位置处振动是否异常的判别阈值;
11.5)获取tbm掘进时的实时掘进数据和不同监测位置处的实时振动数据,提取实时振动数据的振动特征和实时掘进数据的掘进特征进行合并,得到实时多源数据特征,根据不同围岩类别的多源数据特征对实时多源数据特征进行判断,得出tbm掘进时的围岩类别,在该围岩类别下,若当前监测位置处的振动特征大于对应围岩类别、对应监测位置处的判别阈值,则该监测位置处振动异常。
12.获取tbm的历史掘进数据和历史振动数据,从中提取出可以反映振动特性的振动特征和反映掘进特性的掘进特征,将时间上相互对应的振动特征和掘进特征合并,得到多源数据特征;对多源数据特征进行围岩类别划分,得出不同的围岩类别;对不同围岩类别、不同监测部位处的振动特征进行百分位数划分,将处于设定百分位数处的振动特征作为判断tbm在对应围岩类别、对应监测位置处振动是否异常的判别阈值;在tbm掘进时实时采集掘进数据和不同监测部位处的振动数据,从中提取出掘进特征和振动特征进行合并,根据不同围岩类别的多源数据特征对其进行识别,得出当前tbm掘进时遇到的岩体的围岩类别,若当前监测位置处的振动特征大于对应当前围岩类别、当前监测位置的判别阈值,则该监测位置处振动异常。采用本发明,可以实现在tbm掘进时,根据围岩变化实时调整振动异常判别的阈值,并以此做出相应的判断,降低tbm主机振动异常误报、漏报等问题发生的可能。
13.进一步地,在上述方法中,步骤2)中,历史振动数据和历史掘进数据在采集时采用相同的采样间隔。
14.采用相同的采样间隔得到的历史振动数据和历史掘进数据,易于合并,以此计算得到的判别阈值,准确度更高。
15.进一步地,在上述方法中,步骤2)中,将相同起始时间的振动特征和掘进特征进行合并,形成多源数据特征。
16.采用相同起始时间的振动特征和掘进特征进行合并,多源数据特征的数据一致性更好。
17.进一步地,在上述方法中,采用tbm循环划分方法,提取多源数据特征中循环稳定段的多源数据特征用于围岩类别划分。
18.提取多源数据特征中循环稳定段的多源数据特征用于围岩类别划分,可以降低围岩类别划分的工作量,提高处理效率。
19.进一步地,在上述方法中,所述tbm循环划分方法为经验阈值划分方法或otsu自适应循环划分方法。
20.针对tbm循环划分方法,提出两种具体的实施方法。
21.进一步地,在上述方法中,所述振动特征包括振动信号的峰值和设定时间内振动信号的标准差。
22.针对上述提到的振动特征,采用振动信号的峰值可以反映振动信号的幅度,振动信号峰值过大的则认为振动异常;采用一定时间段内振动信号的标准差反映振动信号的波动程度,振动信号标准差过大的则认为振动异常。
23.进一步地,在上述方法中,所述设定百分位数为95%~97.5%。
24.设备异常属于少数情况,采用百分位数进行分类,将大于百分位数处振动特征的振动特征标定异常,采用95%~97.5%的范围可以有效提高判断的可靠性。
25.进一步地,在上述方法中,步骤4)中,将不同围岩类别、不同监测位置处的振动特征的设定百分位数处的振动特征乘以设定系数,作为判断tbm在对应围岩类别、对应监测位置处振动是否异常的判别阈值。
26.将处于设定百分位数处的振动特征乘以设定系数,可以实现误报率可控。
27.进一步地,在上述方法中,所述设定系数为1.2~1.5。
28.根据实际工况,设定系数的范围采用1.2~1.5,以提高本发明的实用性。
29.本发明还提供一种tbm,包括用于获取振动数据的振动在线监测系统、用于获取掘进数据的tbm数据采集系统和控制器,控制器通信连接振动在线监测系统和tbm数据采集系统,所述控制器执行指令实现上述的tbm主机振动异常自适应判别方法。
附图说明
30.图1为本发明实施例中tbm主机振动异常自适应判别方法的流程框图。
具体实施方式
31.为了使本发明的目的、技术方案及优点更加清楚明了,以下结合附图及实施例,对本发明进行进一步详细说明。
32.方法实施例:
33.如图1所示,本发明的一种tbm主机振动异常自适应判别方法,其步骤如下:
34.s1、振动数据、掘进数据获取:通过振动在线监测系统、tbm数据采集系统分别获取振动历史数据、tbm掘进历史数据,其中振动历史数据包含刀盘主驱动电机、减速机、轴承隔板、主梁等监测部位处的单向加速度振动信号,tbm掘进历史数据包含推进力、刀盘扭矩、刀盘转速、推进速度等plc现有参数。
35.s2、振动数据、掘进数据的采样间隔一致性处理:考虑到振动历史数据与tbm掘进历史数据采样间隔差异显著的特点,本发明对不同监测部位处振动历史数据、tbm掘进历史数据进行采样间隔一致性处理,使得振动历史数据中任意相邻两个振动数据之间的时间间隔相同,tbm掘进历史数据中任意相邻两个掘进数据之间的时间间隔相同,此处设置振动历史数据与tbm掘进历史数据的采样间隔为1分钟。
36.以1分钟为单位,提取每分钟刀盘主驱动电机、减速机、轴承隔板、主梁处振动历史数据的峰值特征、标准差特征,共获取8维的振动特征;以1分钟为单位,提取每分钟推进力、刀盘扭矩、刀盘转速、推进速度等tbm掘进历史数据的均值特征,共获取4维的tbm掘进特征。
37.本实施例中,每分钟内振动信号的若干峰值组成一组峰值特征,一段时间内若干振动信号的标准差组成一组标准差特征。
38.通过比对振动历史数据和tbm掘进历史数据的时间戳,搜索确定振动特征时间戳与tbm掘进特征时间戳一致的起始时间,将tbm掘进特征与振动特征合并,形成12维的多源数据特征。
39.s3、循环稳定段的多源数据特征提取:步骤s2所获取的12维多源数据特征,包含tbm循环空推段、上升段和稳定段的所有历史数据。为了便于后续围岩判别分析,利用现有tbm循环划分方法提取循环稳定段的多源数据特征。现有tbm循环划分方法包含经验阈值划分方法、otsu自适应循环划分方法。
40.s4、围岩判别分析:以循环稳定段的12维多源数据特征中tbm掘进特征与振动特征作为输入,利用聚类判别方法进行围岩等级划分,将循环稳定段多源数据特征划分为3类围岩类别,从而得到不同围岩类别的多源数据特征。围岩类别分别为ii~iiia类围岩、iiib~iva类围岩、ivb~v类围岩。聚类判别方法采用高斯混合聚类、k-means聚类或层次聚类方法中的一种。
41.s5、根据步骤s4中围岩聚类判别结果,提取不同围岩类别下、不同监测部位处振动
峰值特征与标准差特征,并利用统计学知识分别计算不同围岩类别下、不同监测部位处tbm主机振动异常判别的阈值,具体步骤如下:
42.s5.1、根据步骤s4中围岩判别结果,分别提取同一围岩类别下、同一监测部位处振动峰值特征、振动标准差特征。
43.s5.2、由于设备状态异常属于少数情况,因此利用统计学中百分位数思想解决误报警问题。本发明采用同一围岩类别下、同一监测部位处振动历史数据中的振动峰值特征的95%分位数thres_peak与标准差特征的95%分位数thres_std作为判断同一围岩类别下、同一监测部位处tbm主机振动是否异常的重要条件。作为其他实施方式,在确定阈值时,百分位数的取值范围为95%~97.5%。
44.例如,tbm在掘进ii~iiia类围岩时,从减速机处采集的振动历史数据中提取出100个振动峰值特征,选取振动峰值特征的95%分位数作为对应ii~iiia类围岩、对应减速机处的振动峰值判别阈值,即:将这100个振动峰值特征从小到大排列,然后选择第95个振动峰值特征作为振动峰值判别阈值,由于减速机的振动异常属于少数情况,因此,从减速机处检测的振动信号对应这100个振动峰值特征中的前95个振动峰值特征,则减速机处的振动正常,否则减速机处的振动异常。
45.此外,为了保证振动异常判别的误报率控制在5%以下,以同一围岩类别下、同一监测部位处振动峰值的95%分位数thres_peak、标准差的95%分位数thres_std乘以冗余系数α,例如1.2~1.5,作为同一围岩类别下、同一监测部位处振动异常判别的最终阈值,如表1所示。
46.表1不同围岩类别下、不同监测部位处振动峰值、标准差阈值统计表
47.[0048][0049]
s6、根据步骤s5.2所获取的不同围岩类别下、不同监测部位处tbm振动异常判别的阈值,对新获取的实时振动数据加以判断,确认对应围岩类别下不同监测部位处振动是否存在异常。
[0050]
以ii~iiia类围岩类别下不同监测部位处振动为例阐述振动异常判断的过程:
[0051]
当tbm处于ii~iiia类围岩类别时,如果轴承隔板处振动峰值特征≥bearingthres_peak1且振动标准差特征≥bearingthres_std1同时满足,则判断tbm轴承隔板处振动出现异常,提示tbm主司机当前设备轴承隔板处振动幅值和波动性过大,请及时关注设备运行状态和前方地质情况;反之,则判断tbm轴承处于正常运行状态。
[0052]
当tbm处于ii~iiia类围岩类别时,如果刀盘主驱动电机处振动峰值特征≥motorthres_peak1且振动标准差特征≥motorthres_std1同时满足,则判断tbm刀盘主驱动电机处振动出现异常,提示tbm主司机当前设备刀盘主驱动电机处振动幅值和波动性过大,请及时关注设备运行状态和前方地质情况;反之,则判断tbm主驱动电机处于正常运行状
态。
[0053]
当tbm处于ii~iiia类围岩类别时,如果减速机处振动峰值特征≥reducerthres_peak1且振动标准差特征≥reducerthres_std1同时满足,则判断tbm减速机处振动出现异常,提示tbm主司机当前设备减速机处振动幅值和波动性过大,请及时关注设备运行状态和前方地质情况;反之,则判断tbm减速机处于正常运行状态。
[0054]
当tbm处于ii~iiia类围岩类别时,如果主梁处振动峰值特征≥beamthres_peak1且振动标准差特征≥beamthres_std1同时满足,则判断tbm主梁处振动出现异常,提示tbm主司机当前设备主梁处振动幅值和波动性过大,请及时关注设备运行状态和前方地质情况;反之,则判断tbm主梁处于正常运行状态。
[0055]
根据最新获取的实时掘进数据、不同监测部位处振动数据,按照步骤s2~s4判断当前tbm所处围岩类别,再按照步骤s6中判断振动是否异常的过程,实时、精准判断设备各个监测部位处振动是否存在异常。采用本发明可以实现tbm主机振动异常阈值的自适应计算,鲁棒性强、误报率低且可操作性强。
[0056]
tbm实施例:
[0057]
本发明的一种tbm,包括振动在线监测系统、tbm数据采集系统和控制器,控制器连接振动在线监测系统和tbm数据采集系统,以获取振动数据和掘进数据,控制器执指令实现方法实施例中的tbm主机振动异常自适应判别方法。关于该方法的实现过程,在方法实施例中已经介绍的清楚明白,此处不再赘述。