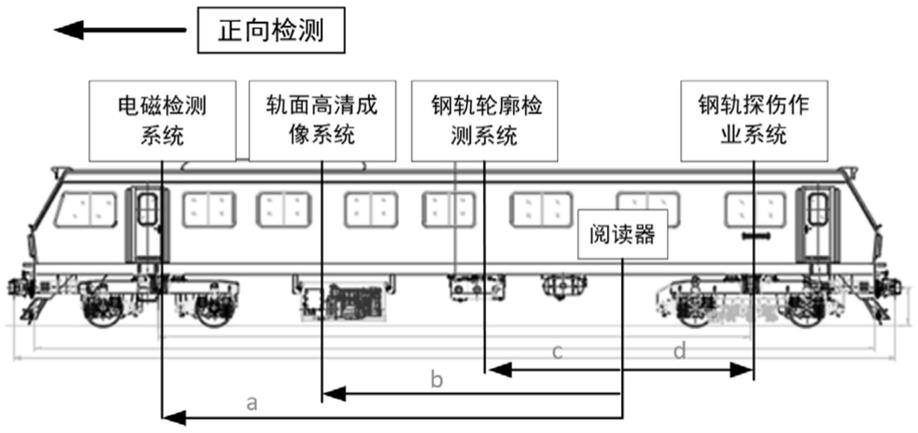
1.本发明涉及数据处理技术领域,尤其涉及钢轨探伤车检测数据空间同步系统及方法。
背景技术:2.本部分旨在为权利要求书中陈述的本发明实施例提供背景或上下文。此处的描述不因为包括在本部分中就承认是现有技术。
3.钢轨在使用过程中会发生影响和限制钢轨使用性能的各种状态,如钢轨内部裂纹、钢轨顶面擦伤、剥离掉块、鱼鳞纹、轨头磨耗、波浪磨耗等。目前对钢轨伤损检测是通过车载式检测系统完成的,如在钢轨探伤作业系统检查钢轨内部裂纹、钢轨轮廓检测系统对钢轨廓形进行检测、轨面高清成像系统对钢轨表面伤损进行检测等。随着工务检测技术的发展,对各项钢轨伤损状态进行同步检测及数据融合分析成为发展趋势之一。
4.现有的钢轨探伤车上不同的位置安装有钢轨探伤作业系统、电磁检测系统、钢轨轨廓检测系统、轨面高清成像系统等检测系统,见图1,可对钢轨表面、内部伤损进行同步检测。
5.为实现对钢轨伤损进行多系统检测数据融合分析,需要将各检测系统的检测数据精确对齐。现有技术仅向各检测系统发送里程同步命令,但由于各系统的传输延迟、存储延迟,造成各系统检测数据在里程同步上难以实现精确对齐,里程偏差较大。例如:探伤车检测速度为80km/h,如果传输延迟时间为0.1秒,则里程偏差约2.2m。各系统的里程信息存储方式也不同,有的在windows系统下待检测数据存储时再粘贴里程信息,有的在realtime系统下的原始数据中粘贴里程信息,存储延迟可达到1-10秒,里程偏差最大可达到20-200m。
6.钢轨伤损的尺寸一般<20mm,较大的里程偏差造成多系统间的数据由于无法对齐不能融合分析。因此,目前缺乏一种钢轨探伤车检测数据空间同步系统,以实现钢轨探伤车多个检测系统数据的精确对齐。
技术实现要素:7.本发明实施例提供一种钢轨探伤车检测数据空间同步系统,用以实现钢轨探伤车多个检测系统的检测数据的精确对齐,该系统包括:
8.空间同步单元、分别与所述空间同步单元连接的编码器和多个检测系统,其中,
9.编码器用于:向空间同步单元发送编码器信号;
10.空间同步单元用于:将接收到的编码器信号发送至每个检测系统;每隔预设编码器计数值,向每个检测系统发送周期同步信号;
11.检测系统用于:在接收到编码器信号后,对编码器信号进行累加计数,获得编码器计数值;在接收到周期同步信号后,计算同步编码器计数值,将当前的编码器计数值修正为同步编码器计数值,并计算当前检测位置的钢轨片段值,对当前检测数据采集周期的检测数据贴上钢轨片段值标签;在根据当前检测数据查找目标检测系统的对应检测数据时,根
据当前检测数据的钢轨片段值标签,获得目标检测系统的对应检测数据。
12.本发明实施例还提供一种钢轨探伤车检测数据空间同步方法,用以实现钢轨探伤车多个检测系统的检测数据的精确对齐,该方法包括:
13.将接收到的编码器信号发送至每个检测系统;所述检测系统在接收到编码器信号后,对编码器信号进行累加计数,获得编码器计数值;
14.每隔预设编码器计数值,向每个检测系统发送周期同步信号;所述检测系统在接收到周期同步信号后,计算同步编码器计数值,将当前的编码器计数值修正为同步编码器计数值,并计算当前检测位置的钢轨片段值,对当前检测数据采集周期的检测数据贴上钢轨片段值标签,在根据当前检测数据查找目标检测系统的对应检测数据时,根据当前检测数据的钢轨片段值标签,获得目标检测系统的对应检测数据。
15.本发明实施例还提供一种钢轨探伤车检测数据空间同步方法,用以实现钢轨探伤车多个检测系统的检测数据的精确对齐,该方法包括:
16.在接收到空间同步单元发送的编码器信号后,对编码器信号进行累加计数,获得编码器计数值;
17.在接收到空间同步单元发送的周期同步信号后,计算同步编码器计数值,将当前的编码器计数值修正为同步编码器计数值,并计算当前检测位置的钢轨片段值,对当前检测数据采集周期的检测数据贴上钢轨片段值标签;
18.在根据当前检测数据查找目标检测系统的对应检测数据时,根据当前检测数据的钢轨片段值标签,获得目标检测系统的对应检测数据。
19.本发明实施例还提供一种计算机设备,包括存储器、处理器及存储在存储器上并可在处理器上运行的计算机程序,所述处理器执行所述计算机程序时实现上述钢轨探伤车检测数据空间同步方法。
20.本发明实施例还提供一种计算机可读存储介质,所述计算机可读存储介质存储有计算机程序,所述计算机程序被处理器执行时实现上述钢轨探伤车检测数据空间同步方法。
21.本发明实施例还提供一种计算机程序产品,所述计算机程序产品包括计算机程序,所述计算机程序被处理器执行时实现上述钢轨探伤车检测数据空间同步方法。
22.本发明实施例中,编码器用于:向空间同步单元发送编码器信号;空间同步单元用于:将接收到的编码器信号发送至每个检测系统;每隔预设编码器计数值,向每个检测系统发送周期同步信号;检测系统用于:在接收到编码器信号后,对编码器信号进行累加计数,获得编码器计数值;在接收到周期同步信号后,计算同步编码器计数值,将当前的编码器计数值修正为同步编码器计数值,并计算当前检测位置的钢轨片段值,对当前检测数据采集周期的检测数据贴上钢轨片段值标签;在根据当前检测数据查找目标检测系统的对应检测数据时,根据当前检测数据的钢轨片段值标签,获得目标检测系统的对应检测数据。在上述系统中,通过周期同步信号,可以实现对当前的编码器计数值的修正;通过计算当前检测位置的钢轨片段值,对当前检测数据采集周期的检测数据贴上钢轨片段值标签,使得在根据当前检测数据查找目标检测系统的对应检测数据时,根据当前检测数据的钢轨片段值标签,获得目标检测系统的对应检测数据,从而实现钢轨探伤车多个检测系统的检测数据的精确对齐。
附图说明
23.为了更清楚地说明本发明实施例或现有技术中的技术方案,下面将对实施例或现有技术描述中所需要使用的附图作简单地介绍,显而易见地,下面描述中的附图仅仅是本发明的一些实施例,对于本领域普通技术人员来讲,在不付出创造性劳动的前提下,还可以根据这些附图获得其他的附图。在附图中:
24.图1为现有的钢轨探伤车的检测系统安装示意图;
25.图2为本发明实施例中钢轨探伤车检测数据空间同步系统的示意图一;
26.图3为本发明实施例中钢轨探伤车检测数据空间同步方法的原理图一;
27.图4为本发明实施例中编码器计数值周期同步示意图;
28.图5为本发明实施例中钢轨钢轨探伤车t1时刻钢轨片段与检测系统之间的关系示意图;
29.图6为本发明实施例中钢轨钢轨探伤车t2时刻钢轨片段与检测系统之间的关系示意图;
30.图7为本发明实施例中钢轨探伤车检测数据空间同步系统的示意图二;
31.图8为本发明实施例中多检测系统的检测数据对齐的原理图;
32.图9为本发明实施例中空间同步单元的接口示意图;
33.图10为本发明实施例中钢轨探伤车检测数据空间同步系统的示意图三;
34.图11为本发明实施例中钢轨探伤车检测数据空间同步方法的原理图二;
35.图12为本发明实施例中里程累加原理;
36.图13为本发明实施例中钢轨探伤车检测数据空间同步方法的流程图一;
37.图14为本发明实施例中钢轨探伤车检测数据空间同步方法的流程图二;
38.图15为本发明实施例中钢轨探伤车检测数据空间同步方法的流程图三;
39.图16为本发明实施例中钢轨探伤车检测数据空间同步方法的流程图四;
40.图17为本发明实施例中钢轨探伤车检测数据空间同步方法的流程图五;
41.图18为本发明实施例中计算机设备的示意图。
具体实施方式
42.为使本发明实施例的目的、技术方案和优点更加清楚明白,下面结合附图对本发明实施例做进一步详细说明。在此,本发明的示意性实施例及其说明用于解释本发明,但并不作为对本发明的限定。
43.图2为本发明实施例中钢轨探伤车检测数据空间同步系统的示意图一,如图2所示,所述系统包括:空间同步单元201、分别与所述空间同步单元201连接的编码器202和多个检测系统203,其中,
44.编码器202用于:向空间同步单元发送编码器信号;
45.空间同步单元201用于:将接收到的编码器信号发送至每个检测系统;每隔预设编码器计数值,向每个检测系统发送周期同步信号;
46.检测系统203用于:在接收到编码器信号后,对编码器信号进行累加计数,获得编码器计数值;在接收到周期同步信号后,计算同步编码器计数值,将当前的编码器计数值修正为同步编码器计数值,并计算当前检测位置的钢轨片段值,对当前检测数据采集周期的
检测数据贴上钢轨片段值标签;在根据当前检测数据查找目标检测系统的对应检测数据时,根据当前检测数据的钢轨片段值标签,获得目标检测系统的对应检测数据。
47.在一实施例中,所述检测系统包括电磁检测系统、轨面高清成像系统、钢轨轮廓检测系统和钢轨探伤作业系统中的其中之一或任意组合。
48.具体地,编码器独立计数,各检测系统接收空间同步单元的编码器信号后,对编码器信号进行累加计数,得到编码器计数值。由于计数开始时间不同、编码器信号干扰,各检测系统之间的编码器计数值会存在累计误差,因此空间同步单元需要进行周期同步。
49.图3为本发明实施例中钢轨探伤车检测数据空间同步方法的原理图一,在一实施例中,空间同步单元还用于:在向每个检测系统发送周期同步信号之前,将下次同步计数值发送每个检测系统;
50.检测系统还用于:在接收到下次同步计数值后记录在各检测系统内部;在接收到周期同步信号后,根据下次同步计数值和预设编码器计数值,计算同步编码器计数值。
51.在上述实施例中,下次同步计数值m0由空间同步单元通过网络发送,m0为每次累加的数值,比如,钢轨探伤车启动后,第一次发送时m0=1,第二次发送时m0=2,依次递加,由于周期同步信号是每隔预设编码器计数值发送的。图4为本发明实施例中编码器计数值周期同步示意图。
52.例如,假设探伤车车轮直径915mm,编码器分辨率5000ppr,车轮旋转100圈行走距离287.31m,预设编码器计数值为500,000(该值一旦设置,可不变)。以500,000为计数同步单位,每隔500,000个脉冲进行一次编码器计数值同步。
53.m0=1,2,3
…
n(n为预设编码器计数值)
54.例如,m0=303时,则同步编码器计数值为303
×
500,000=151,500,000。
55.检测系统在接收到下次同步计数值后记录在各检测系统内部,然后等待周期同步信号。
56.例如:空间同步单元输出周期同步信号,各检测系统收到周期同步信号时,
57.计算出同步编码器计数值151,500,000后,将当前的编码器计数值修正为同步编码器计数值151,500,000。
58.在编码器计数值实现同步后,接下来进行空间同步,首先介绍空间同步原理。
59.以探伤车移动1个编码器脉冲的距离为单位,将钢轨切割成紧密相连的小片段,构成完整的、连续的钢轨坐标系。各个检测系统的检测数据按照钢轨实际位置装配到对应的钢轨坐标系的片段里。同一个钢轨片段可以对应多个检测系统的检测数据,这就是“多系统检测数据空间同步”。
60.多系统检测数据空间同步后,安装在钢轨探伤车不同位置的检测系统的检测数据通过钢轨片段值相互“对齐”。
61.图5为本发明实施例中钢轨钢轨探伤车t1时刻钢轨片段与检测系统之间的关系示意图。
62.从图5中可以看到,钢轨探伤车设置了一个“参考点”,其意义在于:
63.该参考点一直处于钢轨探伤车的后端;
64.起始检测时,该点为钢轨片段值的起始点,钢轨片段值为0;
65.随着钢轨探伤车行走,大于该参考点钢轨片段值的钢轨片段仍处于钢轨探伤车的
检测范围,小于该参考点钢轨片段值的片段已经完成了检测。
66.t1时刻各检测系统的检测数据的钢轨片段值可通过以下计算获得:
67.钢轨探伤作业系统的检测数据的钢轨片段值:
[0068][0069]
轮廓检测系统的检测数据的数据钢轨片段值:
[0070][0071]
轨面系统数据钢轨片段值:
[0072][0073]
电磁检测系统的检测数据的钢轨片段值:
[0074][0075]
其中,l为每个编码器脉冲钢轨探伤车行走的距离;m1为t1时刻参考点的钢轨片段值,也即编码器脉冲计数值;e为射频标签阅读器与参考点的距离。
[0076]
检测车继续行走,当钢轨探伤系统恰巧经过轮廓系统在t1时刻检测的钢轨片段值n2处时(t2时刻),示意图见图6,图6为本发明实施例中钢轨钢轨探伤车t2时刻钢轨片段与检测系统之间的关系示意图。
[0077]
以钢轨探伤作业系统为例,其检测数据的钢轨片段值n2为:
[0078][0079]
t1时刻的n2与t2时刻的n2表示的是钢轨实际位置的同一个钢轨片段,则钢轨探伤作业系统的检测数据与钢轨轮廓作业系统的检测数据就通过钢轨片段值“对齐”了,也即完成了多系统检测数据的空间转换。
[0080]
在一实施例中,检测系统还用于:在接收到周期同步信号后,对当前检测数据采集周期的检测数据贴上钢轨片段值标签的同时,对所述钢轨片段值贴上第一标志位;
[0081]
在未接收到周期同步信号的每个检测数据采集周期,计算当前检测位置的钢轨片段值,对所述检测数据贴上钢轨片段值标签,对所述钢轨片段值贴上第二标志位。
[0082]
其中,贴上第一标志位的钢轨片段值为经过周期同步的准确的钢轨片段值,而贴上第二标志位的钢轨片段值可能存在误差,是不准确的,后续进行空间同步时需要识别该钢轨片段值的标志位以应用准确的钢轨片段值进行计算。
[0083]
图7为本发明实施例中钢轨探伤车检测数据空间同步系统的示意图二,在一实施例中,所述系统还包括射频标签阅读器701;
[0084]
所述检测系统采用如下公式计算当前检测位置的钢轨片段值:
[0085][0086]
其中,n为当前检测位置的钢轨片段值;m为当前时刻参考点的钢轨片段值;e为射频标签阅读器与参考点的距离;x为检测系统与射频标签阅读器的距离;l为每个编码器脉
冲钢轨探伤车行走的距离。
[0087]
图8为本发明实施例中多检测系统的检测数据对齐的原理图。
[0088]
在一实施例中,检测系统还用于:在根据当前检测数据查找目标检测系统的对应检测数据时,根据当前检测数据的钢轨片段值标签n1,查找与所述当前检测位置的钢轨片段值最近的且贴有第一标志位的钢轨片段值m1,计算所述当前检测位置的钢轨片段值与所述最近的且贴有第一标志位的钢轨片段值之间的差值n
1-m1;在目标检测系统的所有检测数据中,查找所述最近的且贴有第一标志位的钢轨片段值,获得目标检测系统的贴有第一标志位的钢轨片段值m1,根据所述差值n
1-m1和目标检测系统的贴有第一标志位的钢轨片段值m1,获得目标检测系统的对应检测数据。
[0089]
在一实施例中,所述检测系统与空间同步单元通过差分同步线缆连接,所述差分同步线缆用于传递周期同步信号。
[0090]
在一实施例中,所述检测系统与所述编码器通过编码器线缆连接,所述编码器线缆用于传递编码器信号。
[0091]
图9为本发明实施例中空间同步单元的接口示意图,其中,网口用于与网络交换机交换,射频标签信号输入接口用于与射频标签阅读器通信,编码器信号输入接口用于与编码器通信,经纬度数据输入接口用于与经纬度获取天线通信,小键盘信号输入接口用于与里程输入小键盘通信,编码器信号输出接口用于与各个检测系统通信,周期同步信号输出接口用于与各个检测系统通信。
[0092]
除了空间同步外,本发明实施例提出的系统还可以实现里程同步,与空间同步使用相同的编码器与周期同步方法。
[0093]
图10为本发明实施例中钢轨探伤车检测数据空间同步系统的示意图三,图11为本发明实施例中钢轨探伤车检测数据空间同步方法的原理图二,图11与图10对应,在一实施例中,所述系统还包括分别与空间同步单元和检测系统连接的网络交换机1001、与空间同步单元连接的里程校正单元1002,所述里程校正单元包括里程输入小键盘、经纬度获取天线、手动输入模块;
[0094]
所述里程校正单元用于:向空间同步单元发送里程校正信号;
[0095]
空间同步单元还用于:将接收到的里程校正信号通过网络交换机发送至检测系统。
[0096]
下面给出里程同步的具体过程。钢轨探伤车中,多个检测系统安装在钢轨探伤车车体上不同位置,在钢轨探伤车运行过程中进行同步检测,对于钢轨上的某一处伤损,不同检测系统的数据应对应相同的钢轨位置,因此需要进行多个检测系统之间里程同步。
[0097]
里程同步由3个步骤完成:里程累加、里程校正、偏差修正。
[0098]
(1)里程累加
[0099]
各检测系统对编码器(例如光电编码器)信号(脉冲信号)进行累加计数,脉冲计数值与脉冲距离的乘积即为里程的相对位置。里程累加原理见图12,其中b点的里程可计算为b=a+m
×
l。
[0100]
各检测系统接收编码器信号、设置相同的脉冲距离值,各自对编码器信号进行里程累加。
[0101]
(2)里程校正
[0102]
空间同步单元通过网络交换机向各检测系统发送网络同步包进行里程校正。里程校正源共有4种方式:里程校正小键盘、射频标签阅读器(rfid)、经纬度获取天线(gnss里程校准)、手动输入模块。
[0103]
第一,里程输入小键盘
[0104]
里程输入小键盘(简称“小键盘”)位于车辆司机台,与空间同步单元通过rs232双向通信。里程校正人员在按小键盘的按键输入线路标识、里程等信息,空间同步单元定时向小键盘发送显示数据包,在小键盘屏幕上显示检测速度、当前里程等内容。
[0105]
空间同步单元接收到小键盘输入的里程校正信息后,通过网络将里程校正信息发送各检测系统进行里程校正。
[0106]
第二,射频标签阅读器
[0107]
射频标签阅读器安装在探伤车车体两侧,经过线路预埋的射频标签时将读取预埋在铁路线路上的rfid里程信息,与空间同步单元通过rs232双向通信。空间同步单元接收到射频标签阅读器输入的里程校正信息后,通过网络将里程校正信息发送各检测系统进行里程校正。
[0108]
第三,经纬度获取天线
[0109]
空间同步单元通过安装在车顶的经纬度获取天线(北斗或gps天线)实时获取经纬度数据,当经纬度数据与里程校正数据库校正点位匹配时,通过网络将里程校正信息发送各检测系统进行里程校正。
[0110]
第四,手动输入模块
[0111]
操作员可在空间同步单元软件的手动输入模块的界面手动输入里程,空间同步单元通过网络将里程校正信息发送各检测系统进行里程校正。
[0112]
(3)偏差修正
[0113]
各检测系统安装在探伤车的不同位置会造成安装偏差。安装偏差通过各检测系统内置安装偏差修正值来解决。以射频标签阅读器作为安装偏差的原点o,测量各检测系统与射频标签阅读器的距离作为偏差修正值。在检测过程中,根据列车的形式方向、里程增减,对安装偏差进行修正。如图1,当正向减里程检测时,里程校正信息o对各检测系统的里程值修正为:钢轨探伤作业系统o+d、电磁检测系统o-d、轨面高清成像系统o-b、钢轨轮廓检测系统o+c。
[0114]
综上所述,在本发明实施例提出的系统具有以下有益效果:
[0115]
(1)将钢轨作为一个完整、连续的坐标系,通过编码器独立计数和周期同步的方式将各检测系统的数据精确映射到钢轨坐标系中,从而完成各检测系统的空间同步。
[0116]
(2)无需各检测系统同步开机或开始检测,在任意时刻开机后均能够接入空间同步系统,使用灵活、方便。
[0117]
(3)通过周期同步信号,可以实现对当前的编码器计数值的修正;通过计算当前检测位置的钢轨片段值,对当前检测数据采集周期的检测数据贴上钢轨片段值标签,使得在根据当前检测数据查找目标检测系统的对应检测数据时,根据当前检测数据的钢轨片段值标签,获得目标检测系统的对应检测数据,从而实现钢轨探伤车多个检测系统的检测数据的精确对齐。
[0118]
(4)在实现空间同步的同时还能够实现里程同步。
[0119]
本发明实施例中还提供了一种钢轨探伤车检测数据空间同步方法,如下面的实施例所述。由于该方法解决问题的原理与系统相似,因此该方法的实施可以参见系统的实施,重复之处不再赘述。
[0120]
图13为本发明实施例中钢轨探伤车检测数据空间同步方法的流程图一,该方法应用于上述系统,包括:
[0121]
步骤1301,将接收到的编码器信号发送至每个检测系统;所述检测系统在接收到编码器信号后,对编码器信号进行累加计数,获得编码器计数值;
[0122]
步骤1302,每隔预设编码器计数值,向每个检测系统发送周期同步信号;所述检测系统在接收到周期同步信号后,计算同步编码器计数值,将当前的编码器计数值修正为同步编码器计数值,并计算当前检测位置的钢轨片段值,对当前检测数据采集周期的检测数据贴上钢轨片段值标签,在根据当前检测数据查找目标检测系统的对应检测数据时,根据当前检测数据的钢轨片段值标签,获得目标检测系统的对应检测数据。
[0123]
图14为本发明实施例中钢轨探伤车检测数据空间同步方法的流程图二,在一实施例中,在向每个检测系统发送周期同步信号之前,还包括:
[0124]
步骤1401,将下次同步计数值发送至每个检测系统,所述检测系统在接收到下次同步计数值后记录在各检测系统内部;在接收到周期同步信号后,根据下次同步计数值和预设编码器计数值,计算同步编码器计数值。
[0125]
本发明实施例中还提供了另一种钢轨探伤车检测数据空间同步方法,图15为本发明实施例中钢轨探伤车检测数据空间同步方法的流程图三,该方法应用于上述系统,包括:
[0126]
步骤1501,在接收到空间同步单元发送的编码器信号后,对编码器信号进行累加计数,获得编码器计数值;
[0127]
步骤1502,在接收到空间同步单元发送的周期同步信号后,计算同步编码器计数值,将当前的编码器计数值修正为同步编码器计数值,并计算当前检测位置的钢轨片段值,对当前检测数据采集周期的检测数据贴上钢轨片段值标签;
[0128]
步骤1503,在根据当前检测数据查找目标检测系统的对应检测数据时,根据当前检测数据的钢轨片段值标签,获得目标检测系统的对应检测数据。
[0129]
图16为本发明实施例中钢轨探伤车检测数据空间同步方法的流程图四,在一实施例中,所述方法还包括:
[0130]
步骤1601,在接收到空间同步单元发送的下次同步计数值后,记录在各检测系统内部;
[0131]
计算同步编码器计数值,包括:根据下次同步计数值和预设编码器计数值,计算同步编码器计数值。
[0132]
图17为本发明实施例中钢轨探伤车检测数据空间同步方法的流程图五,在一实施例中,所述方法还包括:
[0133]
步骤1701,在接收到周期同步信号后,对当前检测数据采集周期的检测数据贴上钢轨片段值标签的同时,对所述钢轨片段值贴上第一标志位;
[0134]
步骤1702,在未接收到周期同步信号的每个检测数据采集周期,计算当前检测位置的钢轨片段值,对所述检测数据贴上钢轨片段值标签,对所述钢轨片段值贴上第二标志位。
[0135]
在一实施例中,所述方法还包括:
[0136]
采用如下公式计算当前检测位置的钢轨片段值:
[0137][0138]
其中,n为当前检测位置的钢轨片段值;m为当前时刻参考点的钢轨片段值;e为射频标签阅读器与参考点的距离;x为检测系统与射频标签阅读器的距离;l为每个编码器脉冲钢轨探伤车行走的距离。
[0139]
在一实施例中,根据当前检测数据的钢轨片段值标签,获得目标检测系统的对应检测数据,包括:
[0140]
根据当前检测数据的钢轨片段值标签,查找与所述当前检测位置的钢轨片段值最近的且贴有第一标志位的钢轨片段值;
[0141]
计算所述当前检测位置的钢轨片段值与所述最近的且贴有第一标志位的钢轨片段值之间的差值;
[0142]
在目标检测系统的所有检测数据中,查找所述最近的且贴有第一标志位的钢轨片段值,获得目标检测系统的贴有第一标志位的钢轨片段值;
[0143]
根据所述差值和目标检测系统的贴有第一标志位的钢轨片段值,获得目标检测系统的对应检测数据。
[0144]
综上所述,在本发明实施例提出的方法具有以下有益效果:
[0145]
(1)将钢轨作为一个完整、连续的坐标系,通过编码器独立计数和周期同步的方式将各检测系统的数据精确映射到钢轨坐标系中,从而完成各检测系统的空间同步。
[0146]
(2)无需各检测系统同步开机或开始检测,在任意时刻开机后均能够接入空间同步系统,使用灵活、方便。
[0147]
(3)通过周期同步信号,可以实现对当前的编码器计数值的修正;通过计算当前检测位置的钢轨片段值,对当前检测数据采集周期的检测数据贴上钢轨片段值标签,使得在根据当前检测数据查找目标检测系统的对应检测数据时,根据当前检测数据的钢轨片段值标签,获得目标检测系统的对应检测数据,从而实现钢轨探伤车多个检测系统的检测数据的精确对齐。
[0148]
(4)在实现空间同步的同时还能够实现里程同步。
[0149]
本发明实施例还提供一种计算机设备,图18为本发明实施例中计算机设备的示意图,所述计算机设备1800包括存储器1810、处理器1820及存储在存储器1810上并可在处理器1820上运行的计算机程序1830,所述处理器1820执行所述计算机程序1830时实现上述钢轨探伤车检测数据空间同步方法。
[0150]
本发明实施例还提供一种计算机可读存储介质,所述计算机可读存储介质存储有计算机程序,所述计算机程序被处理器执行时实现上述钢轨探伤车检测数据空间同步方法。
[0151]
本发明实施例还提供一种计算机程序产品,所述计算机程序产品包括计算机程序,所述计算机程序被处理器执行时实现上述钢轨探伤车检测数据空间同步方法。
[0152]
本领域内的技术人员应明白,本发明的实施例可提供为方法、系统、或计算机程序产品。因此,本发明可采用完全硬件实施例、完全软件实施例、或结合软件和硬件方面的实
施例的形式。而且,本发明可采用在一个或多个其中包含有计算机可用程序代码的计算机可用存储介质(包括但不限于磁盘存储器、cd-rom、光学存储器等)上实施的计算机程序产品的形式。
[0153]
本发明是参照根据本发明实施例的方法、设备(系统)、和计算机程序产品的流程图和/或方框图来描述的。应理解可由计算机程序指令实现流程图和/或方框图中的每一流程和/或方框、以及流程图和/或方框图中的流程和/或方框的结合。可提供这些计算机程序指令到通用计算机、专用计算机、嵌入式处理机或其他可编程数据处理设备的处理器以产生一个机器,使得通过计算机或其他可编程数据处理设备的处理器执行的指令产生用于实现在流程图一个流程或多个流程和/或方框图一个方框或多个方框中指定的功能的装置。
[0154]
这些计算机程序指令也可存储在能引导计算机或其他可编程数据处理设备以特定方式工作的计算机可读存储器中,使得存储在该计算机可读存储器中的指令产生包括指令装置的制造品,该指令装置实现在流程图一个流程或多个流程和/或方框图一个方框或多个方框中指定的功能。
[0155]
这些计算机程序指令也可装载到计算机或其他可编程数据处理设备上,使得在计算机或其他可编程设备上执行一系列操作步骤以产生计算机实现的处理,从而在计算机或其他可编程设备上执行的指令提供用于实现在流程图一个流程或多个流程和/或方框图一个方框或多个方框中指定的功能的步骤。
[0156]
以上所述的具体实施例,对本发明的目的、技术方案和有益效果进行了进一步详细说明,所应理解的是,以上所述仅为本发明的具体实施例而已,并不用于限定本发明的保护范围,凡在本发明的精神和原则之内,所做的任何修改、等同替换、改进等,均应包含在本发明的保护范围之内。