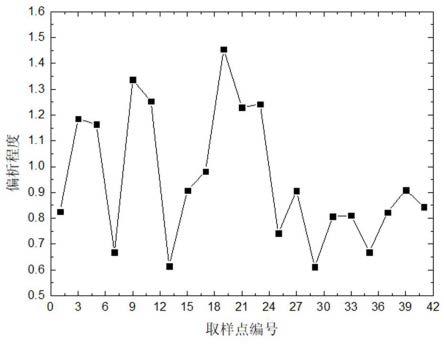
1.本发明属于金属冶金分析技术领域,具体的说是一种用于铜基铁系合金铸坯宏观偏析分析的方法。
背景技术:2.针对铁含量为4~50%的铜铁合金,铜基铁合金固液相线温度区间较宽,铁相优先析出,且铁相密度小,在选分结晶和枝晶凝固特征下,铸锭内部铁元素的分布存在显著的差异,进而影响轧制过程和产品性能。目前为止,铜铁合金中这种铁元素的分布差异无法消除。在生产过程中,铁相偏析程度是考察铸坯质量的一个重要指标,铸坯偏析分布的分析对生产工艺控制及提高铸坯质量具有很高的指导价值。
3.针对成分偏析,在钢铁冶炼铸坯成分偏析的分析方法中,碳偏析常用的方法为:根据铸坯低倍组织金相与偏析标准图比对进行分析,碳偏析主要发生在凝固的中心线区域。
4.而铜基铁系合金在凝固过程中首先析出的是以铁元素为主的铁相,其次为以铜元素为主的铜基体相,铁相与铜相不互溶。铁相形貌和尺寸在铸坯内部位置不同,存在显著差异,从而影响铸坯内不同位置铁元素含量。实践中发现,直接影响铸坯质量的是先析出的铁相偏析程度,而铁相偏析主要是以铁相枝晶的不均匀分布形成。针对该类型的偏析评估目前无法使用偏析程度图谱进行对比,而且使用定点光谱化学分析时,偏析程度结果随检测位置轻微偏移有很大的波动,造成偏析评估准确率较低,甚至失效。
技术实现要素:5.为了解决现有技术中针对铜铁合金铸坯铁元素偏析评估方法失效的技术问题,本发明提供了一种铜基铁系合金铸坯的宏观偏析分析方法,该方法以局部析出铁相面积为计量值,能够较为客观的反映铸坯内部铁元素的偏析位置分布和偏析程度,进而更为准确和有效地对铜基铁系合金凝固铸坯中铁元素的偏析进行评估。
6.本发明为解决上述技术问题所采用的技术方案为:一种铜基铁系合金铸坯的宏观偏析分析方法,包括以下步骤:步骤一、取样以铜基铁系合金铸坯的凝固界面为分析试样的采集区,从铸坯宽度方向的中心位置切取宽度大于1cm,长度与铸坯凝固界面的长度相同的铸坯块作为试样;步骤二、试样加工以铸坯的横截面作为检测面,对步骤一制得试样的检测面进行表面加工处理,使检测面的粗糙度ra≤1.0μm,且检测面上不存在磨痕和油污;步骤三、酸洗使用酸溶液对步骤二加工后的试样进行酸洗,之后,进行冲水和表面吹干,使检测面上无水渍印产生;步骤四、低倍组织图获取
使用金相显微镜或高倍照相机,沿检测面长度方向上的中轴线均匀间隔10~50mm进行取点拍照,对所得系列照片进行1,2,3
……
n顺序编号和同步放大处理后,制得n张低倍组织图,备用;步骤五、图像处理使用图像处理软件,以每张低倍组织图的图片中心为基准,截取5~10mm边长的正方形作为分析区域图片,制得n张大小一致的待分析组织图,备用;步骤六、偏析率分析定义 为每个分析区域点的铁相含量,公式中,i=1,2,3
……
n,s(fei)为第i张待分析组织图内铁相的面积,s(ai)为第i张待分析组织图的总面积,n(ai)为第i张待分析组织图内铁相枝晶的个数;定义p(i)= fe(i)/ fe(均值)为每个分析区域点中铁元素的偏析率,公式中,fe(均值)为第1,2,3
……
n个分析区域点中fe(i)的平均值。
7.步骤七、绘制趋势图对步骤六得到的偏析数据进行整理,并绘制成偏析程度变化趋势图,即可对铜基铁系合金铸坯进行铁元素偏析的宏观分析。
8.优选的,在步骤一中,所述试样的厚度为0.5-2cm。
9.优选的,在步骤三中,所述的酸溶液为浓硝酸与水的体积比为1:1的硝酸溶液。
10.优选的,在步骤三中,所述酸洗的具体方式为,采用酸溶液进行室温侵蚀3-7min。
11.优选的,在步骤五中,所述的图像处理软件为photoshop。
12.有益效果:本发明的一种铜基铁系合金铸坯的宏观偏析分析方法,利用低倍金相图像,基于局部区域铁相组织面积比例变化,以及铁相枝晶的个数作为偏析程度考察因素,能够较为客观的获得铜铁合金内铁元素偏析程度,避免化学分析法因为取样点偏移引起偏析结果明显波动情况。由于铁相组织对性能影响更大,因此,本发明的铁相组织面积法得到的偏析程度更具有指导价值。
附图说明
13.图1为从铸坯上取样的示意图;图2为检测面上低倍组织图获取的示意图;图3为实施例1中检测点2处的待分析组织图;图4为图3使用图像处理软件处理后的图;图5为实施例1中检测点3处的待分析组织图;图6为图4使用图像处理软件处理后的图;图7为沿中心线铁含量偏析程度变化趋势图。
具体实施方式
14.为了更清楚地说明本发明具体实施方式,下面结合附图和具体实施例对本发明的技术方案做进一步详细的阐述和说明。下面描述中的附图和实施例仅是本发明的一些实施
方式,对于本领域普通技术人员来讲,还可以根据这些实施例和附图获得其他的实施例和附图。
15.如图所示,本发明的一种铜基铁合金铸坯的宏观偏析分析方法,包括:获得待分析铸坯横断面中心线上连续检测点附近组织图像;以检测图像几何中心为准,截取分析区域;对分析区域的图片进行处理,基于面积比例法并考虑分析区域铁相枝晶数量计算检测点的铁相成分含量;根据偏析程度计算公式计算得到各检测点偏析率;绘制沿铸坯横断面沿中心线上铁元素的偏析波动图。
16.本发明的偏析分析方法针对的是铜铁难混溶合金,其偏析是由先析出铁相的随机分布引起。由于铁相尺寸可达毫米,传统单点检测或微区域分析易于导致分析结果失真。本发明方法在获得检测点铁相成分含量时考虑分析区域内铁相枝晶数量对偏析结果的影响。本发明提出以毫米级分析区域为检测点,通过图像比例法实现偏析度检验结果的定量化,解决铜铁难混溶合金因宏观偏析严重导致传统方法测量失真的不足,为生产工艺控制及提高铸坯质量提供指导。
17.具体的分析步骤为:(1)取样:以铸坯界面为分析试样的采集区,从铸坯上切取试样,经铸坯中心几何点沿宽面方向,切割宽度大于1cm试样;(2)试样加工:对铸坯横截面进行加工、抛磨,使检测面粗糙度ra≤1.0μm,且检测面上不存在磨痕和油污;(3)酸洗:使用酸溶液对加工试样进行酸洗,酸洗后冲水并吹干检测面,防止水渍印产生;(4)低倍组织图获取:使用金相显微镜或高倍照相机沿中心线宽度方向均匀间隔10~50mm进行拍照,对所得系列照片进行1,2,3
……
n顺序编号和同步放大处理后,制得n张低倍组织图;(5)偏析率分析:
①ꢀ
使用photoshop图形处理软件或相关分析软件,以间隔取样拍照图片中心为基准分别截取5~10mm边长的正方形分析区域图片i(1,2,3,4
……
),对图片进行处理计算获得每张图片中的铁相面积比s(fei)/ s(ai),其中,s(fei)为正方形图片i内铁相的面积,s(ai) 正方形图片i的总面积。
18.②
定义 为分析区域铁相含量,其中,s(fei)为正方形图片i内铁相的面积,s(ai) 正方形图片i的总面积,n(i)为图片i内铁相枝晶个数(一个枝晶数的定义是存在于铜基体,与周围铁相枝晶不存在相接触)。则各检测点铁元素的偏析率计算公式为:p(i)= fe(i)/ fe(均值)。其中,fe(均值)为第1、2、3、4
……
检测点fe(i)的平均值。定义检测点铁相成分含量时考虑分析区域内铁相枝晶数量对偏析结果的影响。
19.实施例1本实施的一种铜基铁合金铸坯的宏观偏析分析方法,包括以下步骤:(1)铸坯取样:如附图1所示,从铜基铁合金铸坯上切取试样,经铸坯中心沿宽面方向,切割宽度为3cm,长度与铸坯长度相同,厚度为2cm的试样,附图1中a指铸坯的长度,为420mm;b指铸坯
的宽度,为160mm;a指试样的长度,为420mm;b指试样的宽度,为30mm;c指铸坯的厚度,为20mm;图中d所指方向为铸坯的铸造方向;(2)试样加工:以铸坯的横截面作为检测面,对试样的检测面进行铣、抛磨,使检测面粗糙度ra≤1.0μm,且检测面上不存在磨痕和油污;(3)酸洗:使用水:浓硝酸体积比为1:1的硝酸溶液,对检测面进行室温侵蚀处理5min,酸洗后冲水并吹干检测面,防止水渍印产生;(4)低倍组织图获取:如附图2所示,使用金相显微镜,沿检测面长度方向上的中轴线方向均匀间隔20mm进行取点拍照,对所得系列照片进行1,2,3
……
n顺序编号,并同步放大5x后,制得n张低倍组织图;附图2中,a指试样的长度,为420mm;b指试样的宽度,为30mm;c指铸坯的厚度,为20mm;图中m所指方向为试样的长度方向上的中轴线方向;n=2的位置指的是检测点2;n=3的位置指的是检测点3;检测点2和检测点3之间的间距为20mm;(5)偏析率分析:
①ꢀ
使用图形处理软件,对沿中心线方向得到照片,以拍照区域几何中心点为基准,截取10mm边长的正方型图片i(1,2,3,4
……
)、对图片进行处理,计算获得图像中铁相面积比s(fei) /s(ai),其中,s(fei)为正方形图片i内铁相的面积;s(a i
) 为正方形图片i的总面积。如附图3和5所示,分别为检测点2和检测点3处的待分析组织图,图中的黑色部分为铁相组织;
②
定义 为每个分析区域点的铁相含量,其中,s(fei)为正方形图片i内铁相的面积,s(ai) 正方形图片i的总面积,n(ai)为图片i内铁相枝晶个数;经计算,检测点2处的铁相含量fe(2)== =0.0006248,其中,s(fe2)为图4中处理后黑色区域的面积17.065 mm2;s(a 2
) 为图4中正方形图片的总面积100mm2,n(a2)为图4内铁相枝晶个数273。
20.检测点2处铁元素的偏析率为:p(2)= fe(2)/fe(均值)=1.185。其中,fe(均值)为第1、2、3、4
……
检测点fe(i)的平均值。同理,计算不同测量点处铁元素的偏析率,绘制偏析程度变化结果,如附图7所示。