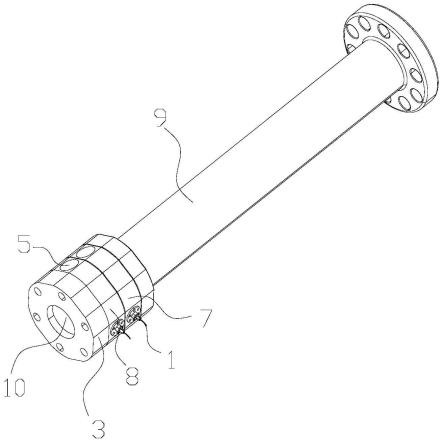
1.本发明涉及燃烧化学反应动力学实验装置技术领域,具体为一种自燃型推 进剂气相着火延迟时间测量装置及测量方法。
背景技术:2.使用计算流体动力学(cfd)耦合化学反应动力学机理,对推进剂流动燃 烧过程进行仿真是航天推进器设计的发展趋势。准确的化学反应动力学机理是 实现推进剂燃烧过程高精度仿真的关键,化学反应机理的可靠性需通过基础燃 烧实验数据的验证,如激波管和快速压缩机测得的着火延迟时间等。这些基础 燃烧实验通常需要制备燃料和氧化剂的预混气体,以排除化学反应过程中组分 输运带来的影响。然而自燃型推进剂常温常压下“接触即反应”的本质属性决 定传统的预混实验方法无法开展,即使进行较高程度的稀释,燃料和氧化剂仍 可以在较低的温度和压力下发生显著的化学反应。现有的自燃型推进剂基础燃 烧特性实验研究方法均存在物理混合过程与化学反应过程高度耦合的问题,难 以用于推进剂化学反应动力学的研究。
技术实现要素:3.针对现有技术中存在的问题,本发明提供一种自燃型推进剂气相着火延迟 时间测量装置及测量方法,实现自燃型推进剂混合和化学反应着火过程的解耦, 得到燃料和氧化剂的着火延迟时间。
4.本发明是通过以下技术方案来实现:
5.一种自燃型推进剂气相着火延迟时间测量装置,包括压缩缸,其内部设置 有活塞,压缩缸的端部设置有燃烧反应腔,燃烧反应腔中设置有隔膜,将燃烧 反应腔分割为两个腔室,两个腔室中用于分别注入推进剂燃料和氧化剂,当隔 膜破裂后两个腔室中燃料和氧化剂混合并燃烧。
6.优选的,所述燃烧反应腔包括同轴设置的第一腔体板、第二腔体板和端盖;
7.所述第一腔体板中设置第一腔室,第二腔体板中设置第二腔室,第一腔体 板的一侧与压缩缸的端部密封固接,隔膜密封压装在第一腔体板和第二腔体板 之间,并使第一腔室和第二腔室相互独立,端盖密封设置在第二腔体板的端部。
8.优选的,所述隔膜为铝制隔膜。
9.优选的,所述隔膜上设置有切痕,用于控制隔膜破裂方向。
10.优选的,所述第一腔体板和第二腔体板上均设置有压力传感器,用于测量 各自腔室的压力。
11.优选的,所述第一腔体板和第二腔体板中还分别埋设有加热装置,用于控 制对应腔室的温度。
12.优选的,所述燃料为燃料和稀释气的混合气体;所述氧化剂为氧化剂和稀 释气的混合气体。
13.一种自燃型推进剂气相着火延迟时间测量装置的测量方法,包括以下步骤:
14.步骤1、将配制的氧化剂和稀释气的混合气体注入第一腔室,将燃料和稀 释气的混合气体注入第二腔室,记录该时刻两个腔室的初始参数;
15.步骤2、对第一腔室施加压力使隔膜破裂,燃料和氧化剂快速混合并燃烧;
16.步骤3、获取第二腔室0时刻至第二腔室压力上升的斜率最大值对应时刻 的时间,得到腔室设定初始参数条件下自燃型推进剂气相的着火延迟时间;
17.所述0时刻为隔膜破裂后第二腔室压力第一次陡升的最高值对应的时刻。
18.优选的,,所述腔室的初始参数包括腔室的温度、体积以及压力。
19.优选的,,还包括以下步骤,获取0时刻时第二腔室的压力值pc并结合理 想气体状态方程,确定0时刻燃烧反应腔中的平均温度tc;
[0020][0021]
其中,t0为两个腔室的初始温度,p
0-1
为第一腔室的初始压力,p
0-2
为第二 腔室的初始压力,v1第一腔室的初始体积,v2第二腔室的初始体积。
[0022]
与现有技术相比,本发明具有以下有益的技术效果:
[0023]
本发明提供的一种自燃型推进剂气相着火延迟时间测量装置,利用铝质隔 膜将自燃型推进剂的燃烧反应腔分为两个腔室,第一腔室靠近快速压缩机的压 缩缸,通过活塞的快速压缩对其内部的气体进行升温和加压;远离活塞的为第 二腔室,当第一腔室中的气体压力升高到一定程度时,铝膜在压差的作用下发 生破裂,两腔室中的气体在较高的压力梯度和破膜产生的强湍流作用下发生快 速均匀混合,混合时间时间尺度小于1.5ms。此时间尺度远小于所研究的自燃 型推进剂气相着火延迟时间101–
102ms量级,然后根据第二腔室的0时刻至第 二腔室压力上升的斜率最大值对应的时刻,得到腔室设定初始参数条件下的自 燃型推进剂气相着火延迟时间。
附图说明
[0024]
图1为本发明测量装置的结构示意图;
[0025]
图2为本发明测量装置的内部结构示意图;
[0026]
图3为本发明测量装置的燃烧反应腔的结构示意图;
[0027]
图4为本发明双腔快速压缩机燃烧反应腔压力曲线;
[0028]
图5为本发明双腔快速压缩机破膜过程温度分布图;
[0029]
图6为本发明双腔快速压缩机的压力/温度/组分浓度变化曲线图。
[0030]
图中:1、压力传感器;2、隔膜;3、端盖;4、密封圈;5、径向视窗;6、 活塞;7、第一腔体板;8、第二腔体板;9、压缩缸;10、端盖视窗。
具体实施方式
[0031]
下面结合附图对本发明做进一步的详细说明,所述是对本发明的解释而不 是限定。
[0032]
参阅图1-3,一种自燃型推进剂气相着火延迟时间测量装置,包括压缩缸9, 其内部设置有活塞6,压缩缸9的端部设置有燃烧反应腔,燃烧反应腔中设置 有隔膜,将燃烧反
应腔分割为两个腔室,两个腔室中用于分别注入推进剂燃料 和氧化剂,当隔膜破损两个腔室连通并使燃料和氧化剂快速混合。
[0033]
所述燃烧反应腔包括第一腔体板7、第二腔体板8和端盖,第一腔体板7 中设置第一腔室,第二腔体板8的中心设置第二腔室,第一腔体板7和第二腔 体板8和端盖同轴设置在压缩缸的端部,第一腔体板7的一侧与压缩缸的端部 固接,隔膜设置在第一腔体板7和第二腔体板8之间,并且隔膜的两侧均设置 有密封圈4,端盖、第二腔体板8和第一腔体板7通过螺栓连接。
[0034]
第一腔体板7和第二腔体板8上均设置有压力传感器1,用于测量各自腔 室的压力,第一腔体板7和第二腔体板8的侧壁上设置有径向视窗5,用于观 察腔室,端盖的中心设置有端盖视窗10,通过径向视窗5和端盖视窗10从多 个方向对腔室进行观察,所述第一腔体板和第二腔体板上均设置有进料口并与 腔室连通,实现燃料和氧化剂的分别注入。
[0035]
第一腔体板7和第二腔体板8中还分别埋设有加热棒,用于对气态的燃烧 和氧化剂进行加热,避免其转化为液态。
[0036]
所述隔膜为铝质隔膜,隔膜上设置有切痕,铝膜的厚度和切痕的深度共同 决定破膜时所需的压差;同时切痕在铝膜破裂时起导向作用,在试验的过程中, 通过控制切痕方向和深度引导隔膜向无光学窗口处破裂,避免干扰径向视窗的 观察光路。
[0037]
例如,在隔膜上设置有米字型切痕,并且其中一个切痕与径向视窗5的轴 向平行,在压力下隔膜沿切痕由中心向边缘破裂,避免铝膜破裂后对径向视窗 5形成遮挡。
[0038]
下面对一种自燃型推进剂气相着火延迟时间的测量方法进行详细的说明, 具体包括以下步骤:
[0039]
步骤1、将配制的氧化剂和稀释气的混合气体注入第一腔室,将燃料和稀 释气的混合气体注入第二腔室,并记录该时刻两个腔室的初始温度t0和第一腔 室初始压力p
0-1
和第二腔室的初始压力p
0-2
。
[0040]
该步骤中启动第一腔体板和第二腔体板上的加热棒,对混合气体进行加热, 保证燃料和氧化剂不发生液化,搭配pid温控器对实验前的初始温度进行准确 调节。各组分的进气量由腔室体积、进气压力和温度计算确定。
[0041]
步骤2、启动快速压缩机,活塞对第一腔室进行加压,第一腔室内部的压 力和温度快速升高,当第一腔室的压力达到一定值使隔膜沿预定方向破裂,使 第一腔室和第二腔室连通形成燃烧反应腔,同时使燃料和氧化剂快速混合并着 火,混合时间不高于1.5ms,隔膜破裂后,第一腔室中压力迅速下降,第二腔 室中压力迅速升高,并迅速达到相同压力值,通过压力传感器获取0时刻时第 二腔室的压力值pc。
[0042]
定义:
[0043]
1、将隔膜破裂后第二腔室压力第一次陡升的最高值对应的时刻为0时刻;
[0044]
2、将燃料和氧化剂由于化学反应释热导致第二腔室压力上升的斜率最大值 处为着火时刻,即着火延迟时间。
[0045]
3、着火的温度工况定义为0时刻燃烧反应腔内的平均温度tc。
[0046]
对于化学反应释热缓慢的研究工况,可使用光电倍增管-光纤连接至可视化 窗口处,使用光电倍增管测得的光信号的最大值处定义为着火时刻。
[0047]
步骤4、根据第一腔室和第二腔室的初始温度、初始压力和体积、0时刻时 第二腔
室的压力值pc并结合理想气体状态方程,确定0时刻燃烧反应腔中的平 均温度tc;
[0048][0049]
其中,t0为初始温度,两个腔室的初始温度相同,p
0-1
为第一腔室的初始压 力,p
0-2
为第二腔室的初始压力,v1第一腔室的初始体积,v2第二腔室的初始 体积。
[0050]
步骤5、根据第二腔室0时刻,以及第二腔室压力上升的斜率最大值对应 的时刻确定火延迟时间,得到在设定燃料和氧化剂浓度、初始压力和燃烧反应 腔平均温度tc下的着火延迟时间。
[0051]
步骤6、通过改变燃料和氧化剂浓度、初始压力p
0-1
和p
0-2
、初始温度t0重复步骤1-5,即可得到自燃型推进剂在不同氧燃比、不同压力pc和燃烧反应 腔平均温度tc下的着火延迟时间。
[0052]
在测试过程中,第一腔室中的气体在活塞压缩的作用下,压力和温度快速 升高,其中50%的压力上升集中在最后2ms。压缩终点附近,第一腔室和第二 腔室间的压差达到预定设计值,使铝膜发生破裂,第一腔室中高温高压的气体 和第二腔室中低温低压气体在压力和温度梯度下产生强湍流混合,同时膜片的 破裂过程也会对两个腔室内的气体起到一定的搅拌作用。由于腔室尺寸较小(内 径《50mm,轴线长度《50mm),气体的混合过程十分迅速,从开始混合到燃烧 反应腔大部分区域的温度不再发生剧烈波动的时间控制在1.5ms内。两腔体内 的气体在破膜混合后,达到设定的特征温度和压力,同时发生化学反应,在一 定时间后由于化学放热导致燃烧反应腔内的压力发生升高,从压力信号第一次 由于破膜而发生陡升/陡降的时刻到压力再次上升最大斜率间的时间间隔定义 为着火延迟时间,如图2所示。对于可能存在的弱着火而导致压力上升不明显 的情况,使用光电倍增装置测量混合气特定波长的光信号来判断着火时刻。
[0053]
下面对采用cfd模拟的方法对双腔快速压缩机膜片破裂过程和气体掺混 过程进行的仿真结果进行详细的说明。
[0054]
20bar压差下铝质膜片完全破裂时间小于0.5ms,燃烧腔室中心部分区域 温度平衡时间和组分平衡时间约在1
–
1.5ms,如图3所示。破膜瞬间,燃烧反 应腔的双腔界面存在极大的压力/密度/温度梯度产生激波,在激波的作用下第二 腔室气体的温度瞬间升高,而第一腔室气体受膨胀波的影响发生冷却,随后气 体在强湍流作用下扩散混合。与快速压缩机燃烧反应腔尺寸相似的相关研究表 明,当雷诺数大于800时,可以保证混合的均匀性,而双腔快速压缩机破膜后 的雷诺数在0-5ms范围内可保持在105–
103量级,湍动能可高达103m2/s2,因 此可以保证气体快速均匀混合。
[0055]
分别选取如第一腔室腔体和第二腔室中两个特征点,绘制其温度、压力和 组分浓度历史如图4所示,破膜后两腔体中的压力迅速平衡(《1ms),温度和 组分浓度(co2为例)在1.5ms内也逐渐趋于稳定,组分浓度达到充分混合理 论水平。因此,可以使用该方法测量101–
102ms量级着火延迟时间,且可满足 气体混合时间尺度远小于化学反应时间尺度。
[0056]
本发明提供的一种自燃型推进剂气相着火延迟时间测量装置,利用铝质隔 膜(铝膜)将自燃型推进剂的燃烧反应腔分为两个腔室,第一腔室靠近快速压 缩机的压缩缸,通过活塞的快速压缩对其内部的气体进行升温和加压;远离活 塞的为第二腔室。当第一腔室中的气体压力升高到一定程度时,铝膜在压差的 作用下发生破裂,两腔体中的气体在较高
的压力梯度和破膜产生的强湍流作用 下发生快速均匀混合,混合时间时间尺度小于1.5ms。此时间尺度远小于所研 究的自燃型推进剂气相着火延迟时间101–
102ms量级,因此可实现自燃型推进 剂混合和化学反应着火过程的解耦,得到燃料和氧化剂近似充分的着火延迟时 间。
[0057]
以上内容仅为说明本发明的技术思想,不能以此限定本发明的保护范围, 凡是按照本发明提出的技术思想,在技术方案基础上所做的任何改动,均落入 本发明权利要求书的保护范围之内。