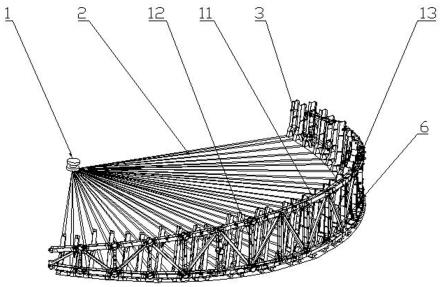
1.本发明涉及不锈钢网壳结构技术领域,具体涉及一种球面网壳结构工厂拼装方法。
背景技术:2.江门中微子实验是继大亚湾中微子实验后人类对中微子的进一步探索,该项目将建造一个有效质量2万吨的液体闪烁体探测器,对人类了解物质微观的基本结构和宏观宇宙的起源与演化具有重要意义。
3.江门中微子实验项目采用一种中心探测器作为核心装置,中心探测器总体形状为球形,置于直径约为43.5m,深44m的水池中。中心探测器主体结构分内层结构和外层结构,其中外层结构为内径40.1m的不锈钢球面网壳,通过一定数量的支撑杆连接将直径(内径)为35.4m的有机玻璃球壳支撑在内层。
技术实现要素:4.本发明主要解决现有技术中存在的不足,提供了一种球面网壳结构工厂拼装方法,在保证螺栓穿孔的情况下,还严格控制与相连预拼装单元连接处的精度,并减少预拼装所需的空间、材料等成本,达到拼装方便、高效率、高精度、高质量并控制拼装成本的生产效果。
5.本发明的上述技术问题主要是通过下述技术方案得以解决的:一种球面网壳结构工厂拼装方法,包括如下操作步骤:第一步:将地面整平,放置中心刻度盘,接着以中心刻度盘为圆心在拼装地面按1:1比例划出待拼装网壳分批构件的定位投影线。
6.第二步:根据定位投影线搭设网壳预拼装胎架,先搭设若干二榀径向钢梁胎架,再在二榀径向钢梁胎架外侧均搭设一榀径向钢梁胎架,相邻的若干一榀径向钢梁胎架间搭设连接节点钢筒胎架。
7.第三步:一榀径向钢梁的定位,将一榀径向钢梁吊至一榀径向钢梁胎架上,一榀径向钢梁上的连接节点钢筒放置到连接节点钢筒胎架上定位,一榀径向钢梁胎架与一榀径向钢梁上的径向钢梁采用定位螺栓连接固定。
8.第四步:一榀径向钢梁胎架上的一榀径向钢梁进行定位检查合格后,将一榀径向钢梁吊装至二榀径向钢梁胎架上,并且连接固定板与二榀径向钢梁胎架采用定位螺栓连接固定为二榀径向钢梁,再在另一个一榀径向钢梁吊至一榀径向钢梁胎架上进行定位检查。
9.第五步:在一榀径向钢梁、二榀径向钢梁上的连接节点钢筒间连接环向梁,然后在两相邻的环向梁间安装与一榀径向钢梁、二榀径向钢梁呈斜角连接固定的交叉支撑钢梁。
10.第六步:完成拼装单元连接后,采用全站仪检测各连接点空间坐标,检查预拼装单元构件位置尺寸准确性,检查无误后方可进行下一批次钢梁的预拼装。
11.第七步:按顺序拆除交叉支撑钢梁、环向梁及一榀径向钢梁,接着将二榀径向钢梁
下挪至一榀径向钢梁胎架上并定位,接着重复第四步至第六步的拼装过程,直至完成全部的钢结构网壳单元的预拼装流程。
12.作为优选,对一榀径向钢梁、二榀径向钢梁进行组装,在连接节点钢筒两侧均焊接过渡连接板,过渡连接板侧边的径向钢梁通过连接固定板与径向钢梁(7)、过渡连接板进行螺栓连接固定。
13.作为优选,最外侧的两定位投影线的角度为120度。
14.作为优选,二榀径向钢梁胎架、连接节点钢筒胎架、一榀径向钢梁胎架均呈等间距环形分布,胎架的布置要以满足构件稳定、避免碰到交叉为原则,置胎架时检查胎架是否牢固,胎架位置尺寸准确。
15.作为优选,预拼装所有构件应按施工图控制尺寸,构件拼装时完全处于自由状态,不允许有外力强制固定。
16.作为优选,预拼装构件控制基准,中心线应明确标示,并与定位投影线相对一致。
17.作为优选,连接固定板采用数控激光切割机加工,加工精度高,过渡连接板和径向钢梁上的螺栓孔均采用连接板套钻加工,保证相邻孔间距尺寸的一致,降低了工程网壳结构拼装过程中出现错孔的问题,预拼装后用比孔公称直径小1.0mm的塞规检查螺栓孔时,每组孔的通过率不小于85%;用比螺栓公称直径大0.3mm的塞规检查螺栓孔时,通过率为100%。
18.作为优选,当出现错孔问题时,严禁强行穿入螺栓,采取将连接板替换的方法,重新加工连接板,保证预拼装时螺栓孔的穿孔率。
19.作为优选,工程网壳结构预拼装时,若出现因为构件本身的变形超标或拼装累积误差造成网壳结构的整体变形超标时,采取将构件重新进行检测并矫正,直至符合技术要求,方可用于拼装;径向钢梁的变形主要为焊接后翼缘变形,该变形可采取油压机配模具进行矫正。
20.本发明能够达到如下效果:本发明提供了一种球面网壳结构工厂拼装方法,与现有技术相比较,在保证螺栓穿孔的情况下,还严格控制与相连预拼装单元连接处的精度,并减少预拼装所需的空间、材料等成本,达到拼装方便、高效率、高精度、高质量并控制拼装成本的生产效果。
附图说明
21.图1是本发明的放样的结构示意图。
22.图2是本发明的搭设胎架的结构示意图。
23.图3是本发明的一榀径向钢梁的定位结构示意图。
24.图4是本发明的一榀径向钢梁定位的局部结构示意图。
25.图5是本发明的环向梁的定位结构示意图。
26.图6是本发明的交叉支撑钢梁的定位结构示意图。
27.图中:中心刻度盘1,定位投影线2,二榀径向钢梁胎架3,连接节点钢筒胎架4,一榀径向钢梁胎架5,一榀径向钢梁6,径向钢梁7,连接固定板8,连接节点钢筒9,过渡连接板10,二榀径向钢梁11,环向梁12,交叉支撑钢梁13。
具体实施方式
28.下面通过实施例,并结合附图,对发明的技术方案作进一步具体的说明。
29.实施例:如图1-6所示,一种球面网壳结构工厂拼装方法,包括如下操作步骤:第一步:将地面整平,放置中心刻度盘1,接着以中心刻度盘1为圆心在拼装地面按1:1比例划出待拼装网壳分批构件的定位投影线2,最外侧的两定位投影线2的角度为120度。
30.第二步:根据定位投影线2搭设网壳预拼装胎架,先搭设若干二榀径向钢梁胎架3,再在二榀径向钢梁胎架3外侧均搭设一榀径向钢梁胎架5,相邻的若干一榀径向钢梁胎架5间搭设连接节点钢筒胎架4。二榀径向钢梁胎架3、连接节点钢筒胎架4、一榀径向钢梁胎架5均呈等间距环形分布,胎架的布置要以满足构件稳定、避免碰到交叉为原则,置胎架时检查胎架是否牢固,胎架位置尺寸准确。
31.第三步:对一榀径向钢梁6、二榀径向钢梁11进行组装,在连接节点钢筒9两侧均焊接过渡连接板10,过渡连接板10侧边的径向钢梁7通过连接固定板8与径向钢梁7、过渡连接板10进行螺栓连接固定。连接固定板8采用数控激光切割机加工,加工精度高,过渡连接板10和径向钢梁7上的螺栓孔均采用连接板套钻加工,保证相邻孔间距尺寸的一致,降低了工程网壳结构拼装过程中出现错孔的问题,预拼装后用比孔公称直径小1.0mm的塞规检查螺栓孔时,每组孔的通过率不小于85%;用比螺栓公称直径大0.3mm的塞规检查螺栓孔时,通过率为100%。
32.当出现错孔问题时,严禁强行穿入螺栓,采取将连接板替换的方法,重新加工连接板,保证预拼装时螺栓孔的穿孔率。
33.预拼装所有构件应按施工图控制尺寸,构件拼装时完全处于自由状态,不允许有外力强制固定。预拼装构件控制基准,中心线应明确标示,并与定位投影线2相对一致。
34.一榀径向钢梁6的定位,将一榀径向钢梁6吊至一榀径向钢梁胎架5上,一榀径向钢梁6上的连接节点钢筒9放置到连接节点钢筒胎架4上定位,一榀径向钢梁胎架5与一榀径向钢梁6上的径向钢梁7采用定位螺栓连接固定。
35.第四步:一榀径向钢梁胎架5上的一榀径向钢梁6进行定位检查合格后,将一榀径向钢梁6吊装至二榀径向钢梁胎架3上,并且连接固定板8与二榀径向钢梁胎架3采用定位螺栓连接固定为二榀径向钢梁11,再在另一个一榀径向钢梁6吊至一榀径向钢梁胎架5上进行定位检查。
36.第五步:在一榀径向钢梁6、二榀径向钢梁11上的连接节点钢筒9间连接环向梁12,然后在两相邻的环向梁12间安装与一榀径向钢梁6、二榀径向钢梁11呈斜角连接固定的交叉支撑钢梁13。
37.工程网壳结构预拼装时,若出现因为构件本身的变形超标或拼装累积误差造成网壳结构的整体变形超标时,采取将构件重新进行检测并矫正,直至符合技术要求,方可用于拼装;径向钢梁7的变形主要为焊接后翼缘变形,该变形可采取油压机配模具进行矫正。
38.第六步:完成拼装单元连接后,采用全站仪检测各连接点空间坐标,检查预拼装单元构件位置尺寸准确性,检查无误后方可进行下一批次钢梁的预拼装;第七步:按顺序先除交叉支撑钢梁13、环向梁12及一榀径向钢梁6,接着将二榀径向钢梁11下挪至一榀径向钢梁胎架5上并定位,接着重复第四步至第六步的拼装过程,直至
完成全部的钢结构网壳单元的预拼装流程。
39.综上所述,该球面网壳结构工厂拼装方法,在保证螺栓穿孔的情况下,还严格控制与相连预拼装单元连接处的精度,并减少预拼装所需的空间、材料等成本,达到拼装方便、高效率、高精度、高质量并控制拼装成本的生产效果。
40.以上所述仅为本发明的具体实施例,但本发明的结构特征并不局限于此,任何本领域的技术人员在本发明的领域内,所作的变化或修饰皆涵盖在本发明的专利范围之中。