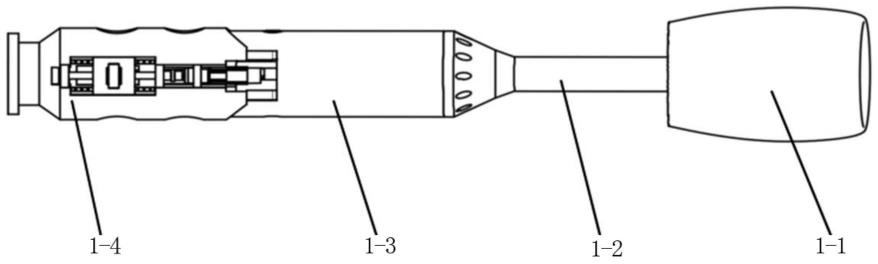
1.本发明属于风洞发动机噪声试验领域,具体涉及一种机翼/风扇安装效应的风洞噪声试验用风扇短舱模拟装置。
背景技术:2.机翼/风扇安装效应测试试验是针对航空发动机受到飞机机翼干扰后,飞机机翼与航空发动机不同位置关系(距离或角度)产生的不同干扰效应下,测试对外界噪声值的大小的试验,并获得因该干扰引起的噪声增量。其中的风扇短舱模拟装置用于模拟航空发动机的工作状态。机翼模型安装在多自由度支撑平台上,多自由度支撑平台可实现水平方向个2自由度和机翼模型迎角变化,风扇短舱模拟装置安装于液压尾撑上,通过液压尾撑实现风扇短舱模拟装置高度变化,通过风扇短舱模拟装置自身的风扇短舱迎角机构实现迎角变化。现有的风扇短舱模拟装置因风扇模型尺寸较小,通常与之匹配的高速电机尺寸较大,无法安装在风扇模型内部,因此需要一种风扇短舱模拟装置。
技术实现要素:3.基于以上不足之处,本发明提供一种机翼/风扇安装效应的风洞噪声试验用风扇短舱模拟装置,实现对航空发动机缩比后风扇模型工作状态的模拟,能够满足机翼/风扇安装效应风洞噪声试验中,对真实航空飞行器特别是民用客机的进场、飞跃、巡航等工况的噪声测试与试验模拟需求。
4.本发明所采用的技术方案是:一种机翼/风扇安装效应的风洞噪声试验用风扇短舱模拟装置,包括风扇模型、风扇模型支撑机构、高速驱动电机和短舱迎角机构,所述的短舱迎角机构固定安装在液压尾撑上,所述的风扇模型为真实航空发动机风扇的缩比模型,所述的风扇模型内壁固定安装多组有测量耙,测量耙上安装有总压测压管、静压测压管或总温传感器,实现试验所需的总压、总温、静压的参数的测量,所述的风扇模型通过法兰与风扇模型支撑机构连接,高速驱动电机的输出轴带动风扇模型的桨叶旋转,达到试验测试工况要求的转速、流量及压比,所述的短舱迎角机构与高速驱动电机的后端转动连接,所述的短舱迎角机构能够改变风扇模型迎风角度。
5.进一步的,所述的风扇模型支撑机构包括轴套和传动长轴,所述的风扇模型包括桨帽、声衬、测量耙、风扇桨叶、轮毂、出口导叶、风扇短舱,桨帽安装于风扇桨叶的前端,风扇桨叶安装在轮毂上,桨帽、风扇桨叶和轮毂位于风扇短舱内部,声衬安装在风扇短舱进气口的内壁上,传动长轴的前端与轮毂固定连接,轴套通过多组轴承套在传动长轴上,出口导叶安装在轴套的前端,轴套的前端还与风扇短舱内壁固定连接,在风扇短舱进气口的内壁上分别安装有三组测量耙,分别位于风扇叶片的前面、风扇叶片和出口导叶之间、出口导叶后面,传动长轴的后端与驱动电机的输出轴连接,轴套的后端与驱动电机的外壳固定连接。
6.进一步的,所述的短舱迎角机构包括安装转轴、连杆组件、关节轴承、电动推杆组
件和迎角机构壳体,电动推杆组件安装在迎角机构壳体上,电动推杆组件的运动方向与迎角机构壳体的轴线平行,电动推杆组件通过关节轴承与连杆组件的一端铰接,连杆组件的另外一端与高速驱动电机的后盖上端连接,迎角机构壳体的前端通过安装转轴与高速驱动电机的后盖平面中心铰接。
7.进一步的,所述的测量耙为米字耙。
8.本发明的优点及有益效果在于:本发明的风扇短舱模型装置可覆盖多种航空发动机的噪声试验工况范围,具有试验模拟设备简单、工况变化易于控制等优点,能够真实地模拟风扇短舱的外涵道气流所产生的噪声。
附图说明
9.图1是本发明的结构外形图
10.图2是本发明的结构轴向剖视图;
11.图3是位于风扇叶片的前面的测量耙上测点布置图;
12.图4是位于风扇叶片和出口导叶之间的测量耙上测点布置图;
13.图5是位于出口导叶后面的测量耙上测点布置图;
具体实施方式
14.下方根据说明书附图,举例对本发明做进一步的说明:
15.实施例1
16.如图1所示,一种机翼/风扇安装效应的风洞噪声试验用风扇短舱模拟装置,主要应用于在风洞噪声试验中机翼/风扇安装效应测试中模拟航空发动机的工况,机翼/风扇安装效应测试试验是针对航空发动机受到飞机机翼干扰后,飞机机翼与航空发动机不同位置关系距离或角度产生的不同干扰效应下,测试对外界噪声值的大小的试验。装置包括风扇模型1-1、风扇模型支撑机构1-2、高速驱动电机1-3和短舱迎角机构1-4,所述的短舱迎角机构1-4固定安装在液压尾撑上,所述的风扇模型1-1为真实航空发动机风扇的缩比模型,所述的风扇模型1-1内壁固定安装多组有测量耙3,测量耙上安装有总压测压管3-1、静压测压管3-2或总温传感器3-3,实现试验所需的总压、总温、静压的参数的测量,所述的风扇模型1-1通过法兰与风扇模型支撑机构1-2连接,高速驱动电机1-3的输出轴带动风扇模型1-1的桨叶旋转,达到试验测试工况要求的转速、流量及压比,所述的短舱迎角机构1-4与高速驱动电机1-3的后端转动连接,所述的短舱迎角机构1-4能够改变风扇模型1-1迎风角度。风扇模型1-1可更换为不同的型号发动机缩比尺寸的模型,风扇模型1-1的旋转方向为顺航向顺时针。
17.如图2所示,所述的风扇模型支撑机构包括轴套9和传动长轴8,所述的风扇模型包括桨帽1、声衬2、测量耙3、风扇桨叶4、轮毂5、出口导叶6、风扇短舱7,桨帽1安装于风扇桨叶4的前端,起到了进气平顺气流的作用,风扇桨叶4安装在轮毂5上,风扇桨叶4旋转对气流起到了增压和加速的作用,桨帽1、风扇桨叶4和轮毂5位于风扇短舱7内部,声衬2安装在风扇短舱7进气口的内壁上,起到了抑制噪声的作用,传动长轴8的前端与轮毂5固定连接,轴套9通过三组轴承10套在传动长轴8上,轴套9主要起到对风扇模型1-1的悬臂支撑作用,出口导叶6安装在轴套9的前端,轴套9的前端还与风扇短舱7内壁固定连接,在风扇短舱7进气口的
内壁上分别安装有三组测量耙3,分别位于风扇叶片4的前面、风扇叶片4和出口导叶6之间、出口导叶后面6,传动长轴8的后端与驱动电机的输出轴连接,轴套9的后端与驱动电机的外壳固定连接。根据不同的试验对象,风扇桨叶4的数量、外形等均可更换。轴套9可适应不同的风扇模型1-1接口,以便更换不同尺寸、型号的风扇模型1-1。高速驱动电机1-3主要由电机本体11和电机后盖12组成。电机本体11在相应变频器的控制下,可以实现试验所需工况的转速和扭矩的输出,电机后盖12用于连接短舱迎角机构1-4与电机本体11,起到了过渡和支撑的作用。
18.如图2所示,所述的短舱迎角机构1-4包括安装转轴13、连杆组件14、关节轴承15、电动推杆组件16和迎角机构壳体17,电动推杆组件16安装在迎角机构壳体17上,电动推杆组件16的运动方向与迎角机构壳体17的轴线平行,电动推杆组件16通过关节轴承15与连杆组件14的一端铰接,连杆组件14的另外一端与高速驱动电机1-3的后盖上端连接,迎角机构壳体17的前端通过安装转轴13与高速驱动电机1-3的后盖平面中心铰接。电动推杆组件16为短舱迎角机构1-4的动力源,电动推杆组件16在其控制器的控制下输出力和直线位移,经过关节轴承15、连杆组件14、安装转轴13传动到电机后盖12处,实现了风扇模型1-1迎风角度的变化。短舱迎角机构1-4后端安装在液压尾撑
ɑ
头上,迎角变化范围:-15
°
~+15
°
,位置控制精度控制在5
′
之内。
19.如图3-5所示,测量耙为米字耙,位于风扇叶片的前面的测量耙上布置了10只总压测压管3-1、6只总温传感器3-3和4只静压测压管3-2,位于风扇叶片和出口导叶之间的测量耙上布置了10只总压测压管3-1和4只静压测压管3-2,位于出口导叶后面的测量耙上布置了10只总压测压管3-1、6只总温传感器3-3和4只静压测压管3-2。风扇短舱7预留了传感器走线位置,总压测压管与静压测压管接至数据采集仪8400设备上,实现试验所需的总压、总温、静压的参数的测量,可用于压比计算,这些米字测量耙均可方便拆卸。出口导叶6既有对风扇桨叶4出口气流的导向作用,又起到了静止支撑的作用。
20.本实施例通过将真实航空发动机风扇尺寸缩比变成风扇模型,缩比后,风扇模型所需的驱动功率减小,为了产生基波效应,风扇的转速需要提高,风扇模型利用转速和功率与之匹配的高速电机驱动,同时在高速驱动电机尾部安装风扇短舱迎角机构,可改变风扇短舱模拟装置在风洞试验中的迎风角度,实现机翼/风扇安装效应风洞噪声试验用航空发动机模型工作状态的模拟,将其应用在机翼/风扇安装效应风洞噪声试验中。