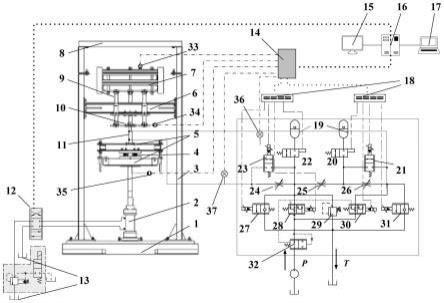
1.本发明属于农业装备测试与控制领域,涉及一种基于硬件在环面向农机装备悬架系统的试验平台,适用于各类农业机械装备的悬架高度调节及减振系统控制策略的研究与验证。
背景技术:2.随着我国农业装备技术的提高以及电子技术的广泛应用,智能化、舒适化和安全化成为今后研究发展的趋势和方向。就农业机械装备而言,除具有显著的季节性作业优势外,还能适应田间复杂开放工作环境,因而在农田作业中被广泛使用。而随着田间作业需求的复杂化,各种作业工况对整车的操纵稳定性和行驶平顺性提出了更高要求。
3.为应对上述情况,国外农机装备已普遍选配底盘悬架及座椅悬架等减振机构。国内农机装备减振装置的研究起步较晚,在研究适用于农机装备的悬架系统领域仍处在初步阶段。而悬架及控制方法的开发过程较为复杂,可细分为需求分析、物理样机设计、台架试验、实车验证与调校完善等一系列流程,由于减振研究基础薄弱,设计的产品性能无法保障,加上控制系统中的控制逻辑的复杂性,导致产品可靠性与安全性仍需进一步考证,这些问题极大提升了研发成本,增加产品的开发周期。为避免事故的发生,提高农机装备减振系统的研发与生产效率,在进行整机试验时,需对系统的软硬件进行调试,直至两者达到最佳状态。因此,硬件在环试验台的搭建对悬架系统的开发具有重要作用。
4.硬件在环试验台既能模拟极端工况下的测试环境,其特点使得不同农机装备的测试皆有较好的适应性,可快速实现自动和重复测试,又可验证多种控制方法,有效降低控制器研发中的试验成本与开发周期,能够在农机装备不进行实际田间测试的情况下,验证设计悬架的在特殊工况下的合理性及控制方法的可行性。
5.国内关于农业机械悬架系统及控制的研发和验证的实验平台较少,且大多数硬件在环实验平台的所能模拟的工况较简单,尚无法完全满足复杂田间工况下悬架系统与控制算法的快速开发要求,往往不能实现多种工况的模拟加载;同时现有的试验台结构复杂、制造难度大,但只能进行单个的两自由度悬架的性能与控制策略验证,导致成本极高。因此,开发一种基于硬件在环的农机装备悬架系统试验平台,已成为当务之急。
技术实现要素:6.针对农机装备悬架系统及控制方法开发过程中存在的问题,如悬架各零部件参数设计合理性、悬架的性能参数难以测得、控制方法应用困难。虽然计算机能利用精确的数学模型仿真,具有效率高等特点,但建模过程繁琐,不能准确反映真实的转场运输和田间作业工况,本发明的目的是提供一种基于硬件在环的面向农机装备悬架系统的试验平台,将农机装备悬架系统模拟在该平台上,实现减振控制测试、减振效果分析等功能。通过模拟作业工况加载及实车布局,测试不同控制方法下的悬架系统减振效果,并根据试验结果对农机装备的实际悬架和控制的开发进行相应的优化及改进。
7.为了实现上述目的,本发明提供了如下技术方案:
8.一种基于硬件在环面向农机装备悬架系统的试验平台,包括振动试验台、悬架液压系统、数据采集系统及远程控制系统。
9.所述振动试验台包括基座1、伺服作动缸2、振动台纵梁3、组合式弹簧4、承载平台5、导向架横梁6、簧载质量块7、横梁8、直线轴承9、支撑平板10和伺服阀12。
10.所述悬架液压系统包括液压缸11及油路系统。
11.所述基座1由多个螺栓水平固定在地面上,两个振动台纵梁3由螺栓垂直固定在基座1上,水平布置的横梁8和导向架横梁6分别固接在两个振动台纵梁3的顶部和上部。
12.竖直布置的所述伺服作动缸2的缸筒端通过螺栓固接在基座1上,所述承载平台5用于模拟非簧载质量,包括通过滑动连接柱连接的上承载板和下承载板;所述组合式弹簧4布置在上承载板与下承载板之间;所述伺服作动缸2的活塞杆端通过法兰和螺栓与承载平台5的下承载板固接。
13.所述伺服作动缸2通过伺服阀12与油箱13连接,所述伺服阀12与远程控制系统连接,通过远程控制系统控制伺服作动缸2工作,模拟农机作业时田间作业路面环境,实现作业工况加载。
14.所述液压缸11的缸体端与承载平台5的上承载板固接,伸缩杆端与支撑平板10固接;所述直线轴承9竖直地固接在导向架横梁6上,直线轴承9的下端与支撑平板10固接,直线轴承9的上端与用于模拟实车质量的簧载质量块7固接;所述承载平台5、液压缸11与簧载质量块7的结构位置能准确还原农机装备的悬架布局安排,实现实车布局的模拟;所述簧载质量块7与伺服作动缸2的上端之间的距离即为悬架高度,通过液压缸11的位移调整悬架高度,实现悬架高度调节和减振控制功能。
15.所述油路系统包括蓄能器19、第一电磁开关阀20、第一比例阀21、第二电磁开关阀22、第二比例阀23、第一可调节流阀24、第二可调节流阀25、第三可调节流阀26、左比例下降阀27、左比例提升阀28、溢流阀29、右比例提升阀30、右比例下降阀31和定差减压阀32。
16.所述定差减压阀32的进油口与液压油箱连接,定差减压阀32的出油口分别与左比例提升阀28的进油口和右比例提升阀30的进油口连接,流量在定差减压阀32的作用下保持稳定。
17.所述左比例提升阀28的出油口、左比例下降阀27的进油口、溢流阀29的第一油口、第一可调节流阀24的第二油口、第二可调节流阀25的第一油口、第二电磁开关阀22的进油口和第二比例阀23的第二油口相互连接;所述第一可调节流阀24的第一油口、液压缸11的无杆腔油口和第二比例阀23的第一油口相互连接。
18.所述右比例提升阀30的出油口、右比例下降阀31的进油口、第三可调节流阀26的第二油口、第一比例阀21的第二油口和液压缸11的有杆腔油口相互连接;所述第三可调节流阀26的第一油口、第二可调节流阀25的第二油口、第一电磁开关阀20的进油口和第一比例阀21的第一油口相互连接。
19.所述第一电磁开关阀20的出油口和第二电磁开关阀22的出油口分别与一个蓄能器19的进油口连接。
20.所述溢流阀29的第二油口与左比例下降阀27的回油口和右比例下降阀31的回油口连接,并通向液压油箱。
21.其中,左比例下降阀27、左比例提升阀28和第一可调节流阀24组成左油路。
22.第二可调节流阀25、第一电磁开关阀20、第一比例阀21、第二电磁开关阀22和第二比例阀23组成中间油路。
23.第三可调节流阀26、右比例提升阀30和右比例下降阀31组成右油路。
24.所述数据采集系统包括比例阀放大板18、振动传感器33、第一位移传感器34、第二位移传感器35、第一压力传感器36和第二压力传感器37。
25.所述比例阀放大板18与油路系统的第一电磁开关阀20、第一比例阀21、第二电磁开关阀22、第二比例阀23、左比例下降阀27、左比例提升阀28、右比例提升阀30和右比例下降阀31的电磁开关连接。
26.所述振动传感器33设置在簧载质量块7上,用于检测簧载质量块7的垂直方向的加速度。
27.所述第一位移传感器34设置在导向横梁6与支撑平板10之间,用于检测簧载质量块7的位移。
28.所述第二位移传感器35设置在承载平台5与基座1之间,用于检测路面谱,并通过计算得到承载平台5的位移。
29.所述第一压力传感器36设置在液压缸11的有杆腔与油路系统的连接油路上,用于检测液压缸11的有杆腔的压力。
30.所述第二压力传感器37设置在液压缸11的无杆腔与油路系统的连接油路上,用于检测液压缸11的无杆腔的压力。
31.所述远程控制系统包括下位机14、上位机和控制台17。
32.所述上位机包括显示器15和pc主机16;所述下位机14为dspace工控机,用于控制模型代码运行及数据采集;所述下位机14内装有ds2002信号采集板卡、ds1007控制板卡和ds2102信号传送板卡。
33.所述pc主机16分别与伺服阀12、ds1007控制板卡和控制台17连接;所述ds1007控制板卡分别与ds2002信号采集板卡和ds2102信号传送板卡连接;所述ds2102信号传送板卡与比例阀放大板18连接。
34.所述ds2002信号采集板卡将采集到的簧载质量块7的垂直方向的加速度、簧载质量块7的位移、承载平台5的位移、液压缸11的有杆腔压力和无杆腔的压力数据信号处理后传送给ds1007控制板卡;ds1007控制板根据簧载质量块7的位移和承载平台5的位移计算获得液压缸11的位移;所述pc主机16根据ds1007控制板卡获得的数据生成高度控制和/或减振控制策略,并通过ds1007控制板卡将决策信号传给ds2102信号传送板卡;所述ds2102信号传送板卡将决策信号转化为pwm信号后发送到比例阀放大板18,比例阀放大板18根据pwm信号驱动第一电磁开关阀20、第一比例阀21、第二电磁开关阀22、第二比例阀23、左比例下降阀27、左比例提升阀28、右比例提升阀30、右比例下降阀31、定差减压阀32,进而实现悬架的高度控制和/或减振控制。
35.所述pc主机16通过其内部的整机模型、路面模型控制伺服阀12控制油箱13的输出流量,实现伺服作动缸2的上下运动,模拟加载路面谱和车辆振动状态,并发送给下位机14的ds1007控制板卡,通过显示器15的用户界面反馈给实验人员。
36.所述显示器15还用于显示振动传感器33、第一位移传感器34、第二位移传感器35、
第一压力传感器36和第二压力传感器37传输的油路压力信号、簧载质量块7的位移信号、承载平台5的位移信号、簧载质量块7的加速度信号。
37.所述控制台17监控伺服作动缸2的运行,进行数据自动存储,具有参数安全保护功能。
38.当外界负载发生变化时,根据第一位移传感器34识别出的簧载质量块7的位移,和/或第一压力传感器36和第二压力传感器37检测的压力变化,判断外界负载增加或减小;当外界负载增加时,簧载质量块7产生向下位移,同时第一压力传感器36检测的压力变大,第二压力传感器37检测的压力变小,液压缸11的活塞杆收缩,液压油被挤出液压缸11的无杆腔,并通过第二电磁开关阀22和第二比例阀23进入蓄能器19,当前悬架高度h下降;当外界负载减小时,液压油从蓄能器19流向液压缸11的无杆腔,液压缸11的活塞杆伸长,第一压力传感器36检测的压力变小,第二压力传感器37检测的压力变大,簧载质量块7产生向上位移,当前悬架高度h升高。
39.如果当前悬架高度h处于农田作业的预设高度范围h1~h2内时,各个比例阀关闭,不调节悬架高度。
40.如果当前悬架高度h小于预设最低高度h1时,ds1007控制板卡通过ds2102信号传输板卡将控制信号传给比例阀放大板18,比例阀放大板18分别驱动左比例提升阀28和右比例下降阀31调节开度,使液压缸11的无杆腔进油,有杆腔放油,液压缸11的活塞杆伸长,直到悬架高度回到预设高度范围h1~h2内,左比例提升阀28和右比例下降阀31关闭。
41.如果当前悬架高度h大于预设最高高度h2时,ds1007控制板卡通过ds2102信号传输板卡将控制信号传给比例阀放大板18,比例阀放大板18分别驱动右比例提升阀30和左比例下降阀27调节开度,使液压缸11的有杆腔进油,无杆腔放油,液压缸11的活塞杆收缩,直到悬架高度回到预设高度范围h1~h2内,右比例提升阀30和左比例下降阀27关闭。
42.所述伺服作动缸2模拟农机装备实际作业路况,根据采集到簧载质量块7的垂直方向的加速度以加速度最小为目标,ds1007控制板卡通过ds2102信号传输板卡将控制信号传给比例阀放大板18,比例阀放大板18驱动第一比例阀21和第二比例阀23调节开度,从而调节液压缸11与蓄能器19之间的油液产生的阻尼力,实现悬架的减振控制。
43.与现有技术相比,本发明的有益效果在于:
44.1、本发明利用硬件在环技术搭建试验平台,采用数学模型描述整机动力学模型及其控制策略,悬架系统以实物形式接入仿真回路,能最大程度地验证控制策略的合理性。
45.2、本发明可对不同规格的农机装备进行定制化悬架检测,为悬架各参数的优化提供实验数据支持,大大加快了硬件的开发周期。
46.3、dspace工控机满足虚拟仿真模型运行的速度,与物理模型交互的实时性。本发明的车身高度调节及减振控制系统既实现了底盘的快速升降,用于提高路面通过性,又兼顾行驶平顺性与操纵稳定性。
47.4、不同农机装备的工况复杂多变,振动试验台中的伺服作动缸2可模拟各工况下的路面环境,台架针对不同类型的试验装置预留有安装位置,可进行弹簧特性试验和单自由度1/4悬架特性试验,减少了试验成本。
附图说明
48.图1为本发明的面向农机装备悬架系统的试验平台的示意图;
49.图2为本发明的油气悬架车身高度和减振控制原理图;
50.图3为本发明的减振控制流程示意图。
51.其中的附图标记为:
52.1、基座
ꢀꢀꢀꢀꢀꢀꢀꢀꢀꢀꢀꢀꢀꢀꢀꢀꢀꢀꢀꢀꢀꢀꢀ
2、伺服作动缸
53.3、振动台纵梁
ꢀꢀꢀꢀꢀꢀꢀꢀꢀꢀꢀꢀꢀꢀꢀꢀꢀꢀ
4、组合式弹簧
54.5、承载平台
ꢀꢀꢀꢀꢀꢀꢀꢀꢀꢀꢀꢀꢀꢀꢀꢀꢀꢀꢀꢀ
6、导向架横梁
55.7、簧载质量块
ꢀꢀꢀꢀꢀꢀꢀꢀꢀꢀꢀꢀꢀꢀꢀꢀꢀꢀ
8、横梁
56.9、直线轴承
ꢀꢀꢀꢀꢀꢀꢀꢀꢀꢀꢀꢀꢀꢀꢀꢀꢀꢀꢀꢀ
10、支撑平板
57.11、液压缸
ꢀꢀꢀꢀꢀꢀꢀꢀꢀꢀꢀꢀꢀꢀꢀꢀꢀꢀꢀꢀꢀ
12、伺服阀
58.13、油箱
ꢀꢀꢀꢀꢀꢀꢀꢀꢀꢀꢀꢀꢀꢀꢀꢀꢀꢀꢀꢀꢀꢀꢀ
14、下位机
59.15、显示器
ꢀꢀꢀꢀꢀꢀꢀꢀꢀꢀꢀꢀꢀꢀꢀꢀꢀꢀꢀꢀꢀ
16、pc主机
60.17、控制台
ꢀꢀꢀꢀꢀꢀꢀꢀꢀꢀꢀꢀꢀꢀꢀꢀꢀꢀꢀꢀꢀ
18、比例阀放大板
61.19、蓄能器
ꢀꢀꢀꢀꢀꢀꢀꢀꢀꢀꢀꢀꢀꢀꢀꢀꢀꢀꢀꢀꢀ
20、第一电磁开关阀
62.21、第一比例阀
ꢀꢀꢀꢀꢀꢀꢀꢀꢀꢀꢀꢀꢀꢀꢀꢀꢀ
22、第二电磁开关阀
63.23、第二比例阀
ꢀꢀꢀꢀꢀꢀꢀꢀꢀꢀꢀꢀꢀꢀꢀꢀꢀ
24、第一可调节流阀
64.25、第二可调节流阀
ꢀꢀꢀꢀꢀꢀꢀꢀꢀꢀꢀꢀꢀ
26、第三可调节流阀
65.27、左比例下降阀
ꢀꢀꢀꢀꢀꢀꢀꢀꢀꢀꢀꢀꢀꢀꢀ
28、左比例提升阀
66.29、溢流阀
ꢀꢀꢀꢀꢀꢀꢀꢀꢀꢀꢀꢀꢀꢀꢀꢀꢀꢀꢀꢀꢀ
30、右比例提升阀
67.31、右比例下降阀
ꢀꢀꢀꢀꢀꢀꢀꢀꢀꢀꢀꢀꢀꢀꢀ
32、定差减压阀
68.33、振动传感器
ꢀꢀꢀꢀꢀꢀꢀꢀꢀꢀꢀꢀꢀꢀꢀꢀꢀ
34、第一位移传感器
69.35、第二位移传感器
ꢀꢀꢀꢀꢀꢀꢀꢀꢀꢀꢀꢀꢀ
36、第一压力传感器
70.37、第二压力传感器
具体实施方式
71.下面结合附图和实施例对本发明进行进一步说明。
72.如图1所示,本发明的基于硬件在环面向农机装备悬架系统的试验平台,包括振动试验台、悬架液压系统、数据采集系统及远程控制系统。
73.所述振动试验台包括基座1、伺服作动缸2、振动台纵梁3、组合式弹簧4、承载平台5、导向架横梁6、簧载质量块7、横梁8、直线轴承9、支撑平板10和伺服阀12;
74.所述悬架液压系统包括液压缸11及油路系统。
75.所述基座1由多个螺栓水平固定在地面上,两个振动台纵梁3由螺栓垂直固定在基座1上,水平布置的横梁8和导向架横梁6分别固接在两个振动台纵梁3的顶部和上部。
76.竖直布置的所述伺服作动缸2的缸筒端通过螺栓固接在基座1上,所述承载平台5用于模拟非簧载质量,包括通过滑动连接柱连接的上承载板和下承载板;所述组合式弹簧4布置在上承载板与下承载板之间;所述伺服作动缸2的活塞杆端通过法兰和螺栓与承载平台5的下承载板固接。
77.所述伺服作动缸2通过伺服阀12与油箱13连接,所述伺服阀12与远程控制系统连
接,通过远程控制系统控制伺服作动缸2工作,模拟农机作业时田间作业路面环境,实现作业工况加载。
78.所述液压缸11的缸体端与承载平台5的上承载板固接,伸缩杆端与支撑平板10固接。所述直线轴承9竖直地固接在导向架横梁6上,直线轴承9的下端与支撑平板10固接,直线轴承9的上端与用于模拟实车质量的簧载质量块7固接。所述承载平台5、液压缸11与簧载质量块7的结构位置能准确还原农机装备的悬架布局安排,实现实车布局的模拟。所述簧载质量块7与伺服作动缸2的上端之间的距离即为悬架高度,通过液压缸11的位移调整悬架高度,实现悬架高度调节和减振控制功能。
79.所述油路系统包括蓄能器19、第一电磁开关阀20、第一比例阀21、第二电磁开关阀22、第二比例阀23、第一可调节流阀24、第二可调节流阀25、第三可调节流阀26、左比例下降阀27、左比例提升阀28、溢流阀29、右比例提升阀30、右比例下降阀31和定差减压阀32。
80.所述定差减压阀32的进油口与液压油箱连接,定差减压阀32的出油口分别与左比例提升阀28的进油口和右比例提升阀30的进油口连接,流量在定差减压阀32的作用下保持稳定。
81.所述左比例提升阀28的出油口、左比例下降阀27的进油口、溢流阀29的第一油口、第一可调节流阀24的第二油口、第二可调节流阀25的第一油口、第二电磁开关阀22的进油口和第二比例阀23的第二油口相互连接;所述第一可调节流阀24的第一油口、液压缸11的无杆腔油口和第二比例阀23的第一油口相互连接。
82.所述右比例提升阀30的出油口、右比例下降阀31的进油口、第三可调节流阀26的第二油口、第一比例阀21的第二油口和液压缸11的有杆腔油口相互连接;所述第三可调节流阀26的第一油口、第二可调节流阀25的第二油口、第一电磁开关阀20的进油口和第一比例阀21的第一油口相互连接。
83.所述第一电磁开关阀20的出油口和第二电磁开关阀22的出油口分别与一个蓄能器19的进油口连接。
84.所述溢流阀29的第二油口与左比例下降阀27的回油口和右比例下降阀31的回油口连接,并通向液压油箱,起保护作用。
85.其中,左比例下降阀27、左比例提升阀28和第一可调节流阀24组成左油路。
86.第二可调节流阀25、第一电磁开关阀20、第一比例阀21、第二电磁开关阀22和第二比例阀23组成中间油路;
87.第三可调节流阀26、右比例提升阀30和右比例下降阀31组成右油路。
88.所述数据采集系统包括比例阀放大板18、振动传感器33、第一位移传感器34、第二位移传感器35、第一压力传感器36和第二压力传感器37;
89.所述比例阀放大板18与油路系统的第一电磁开关阀20、第一比例阀21、第二电磁开关阀22、第二比例阀23、左比例下降阀27、左比例提升阀28、右比例提升阀30和右比例下降阀31的电磁开关连接;
90.所述振动传感器33设置在簧载质量块7上,用于检测簧载质量块7的垂直方向的加速度;
91.所述第一位移传感器34设置在导向横梁6与支撑平板10之间,用于检测簧载质量块7的位移;
92.所述第二位移传感器35设置在承载平台5与基座1之间,用于检测路面谱,并通过计算得到承载平台5的位移;
93.所述第一压力传感器36设置在液压缸11的有杆腔与油路系统的连接油路上,用于检测液压缸11的有杆腔的压力;
94.所述第二压力传感器37设置在液压缸11的无杆腔与油路系统的连接油路上,用于检测液压缸11的无杆腔的压力。
95.如图1和图2所示,所述远程控制系统包括下位机14、上位机和控制台17。
96.所述上位机包括显示器15和pc主机16;所述下位机14为dspace工控机,用于控制模型代码运行及数据采集。所述下位机14内装有ds2002信号采集板卡、ds1007控制板卡和ds2102信号传送板卡。
97.所述pc主机16分别与伺服阀12、ds1007控制板卡和控制台17连接。所述ds1007控制板卡分别与ds2002信号采集板卡和ds2102信号传送板卡连接;所述ds2102信号传送板卡与比例阀放大板18连接。
98.所述ds2002信号采集板卡将采集到的簧载质量块7的垂直方向的加速度、簧载质量块7的位移、承载平台5的位移、液压缸11的有杆腔压力和无杆腔的压力数据信号处理后传送给ds1007控制板卡;ds1007控制板根据簧载质量块7的位移和承载平台5的位移计算获得液压缸11的位移;所述pc主机16根据ds1007控制板卡获得的数据生成高度控制和/或减振控制策略,并通过ds1007控制板卡将决策信号传给ds2102信号传送板卡;所述ds2102信号传送板卡将决策信号转化为pwm信号后发送到比例阀放大板18,比例阀放大板18根据pwm信号驱动第一电磁开关阀20、第一比例阀21、第二电磁开关阀22、第二比例阀23、左比例下降阀27、左比例提升阀28、右比例提升阀30、右比例下降阀31、定差减压阀32,进而实现悬架的高度控制和/或减振控制。
99.所述pc主机16通过其内部的整机模型、路面模型控制伺服阀12控制油箱13的输出流量,实现伺服作动缸2的上下运动,模拟加载路面谱和车辆振动状态,并发送给下位机14的ds1007控制板卡,通过显示器15的用户界面反馈给实验人员。
100.所述显示器15还用于显示振动传感器33、第一位移传感器34、第二位移传感器35、第一压力传感器36和第二压力传感器37传输的油路压力信号、簧载质量块7的位移信号、承载平台5的位移信号、簧载质量块7的加速度信号。
101.所述控制台17监控伺服作动缸2的运行,进行数据自动存储,具有参数安全保护功能。
102.本发明的工作过程如下:
103.高度控制:
104.如图3所示,当外界负载发生变化时,根据第一位移传感器34识别出的簧载质量块7的位移,和/或第一压力传感器36和第二压力传感器37检测的压力变化,判断外界负载增加或减小;当外界负载增加时,簧载质量块7产生向下位移,同时第一压力传感器36检测的压力变大,第二压力传感器37检测的压力变小,液压缸11的活塞杆收缩,液压油被挤出液压缸11的无杆腔,并通过第二电磁开关阀22和第二比例阀23进入蓄能器19,当前悬架高度h下降;当外界负载减小时,液压油从蓄能器19流向液压缸11的无杆腔,液压缸11的活塞杆伸长,第一压力传感器36检测的压力变小,第二压力传感器37检测的压力变大,簧载质量块7
产生向上位移,当前悬架高度h升高;
105.如果当前悬架高度h处于农田作业的预设高度范围h1~h2内时,各个比例阀关闭,不调节悬架高度;
106.如果当前悬架高度h小于预设最低高度h1时,ds1007控制板卡通过ds2102信号传输板卡将控制信号传给比例阀放大板18,比例阀放大板18分别驱动左比例提升阀28和右比例下降阀31调节开度,使液压缸11的无杆腔进油,有杆腔放油,液压缸11的活塞杆伸长,直到悬架高度回到预设高度范围h1~h2内,左比例提升阀28和右比例下降阀31关闭;
107.如果当前悬架高度h大于预设最高高度h2时,ds1007控制板卡通过ds2102信号传输板卡将控制信号传给比例阀放大板18,比例阀放大板18分别驱动右比例提升阀30和左比例下降阀27调节开度,使液压缸11的有杆腔进油,无杆腔放油,液压缸11的活塞杆收缩,直到悬架高度回到预设高度范围h1~h2内,右比例提升阀30和左比例下降阀27关闭。
108.减振控制:
109.本试验台除了可以对农机装备的悬架进行高度调节,还可实现在某一高度范围内的减振控制。伺服作动缸2模拟农机装备实际作业路况,所述伺服作动缸2模拟农机装备实际作业路况,根据采集到簧载质量块7的垂直方向的加速度以加速度最小为目标,ds1007控制板卡通过ds2102信号传输板卡将控制信号传给比例阀放大板18,比例阀放大板18驱动第一比例阀21和第二比例阀23调节开度,从而调节液压缸11与蓄能器19之间的油液产生的阻尼力,实现悬架的减振控制。
110.所述振动试验台可根据不同农机装备的数学模型建立并验证多种控制算法,也可搭建基于同一农机装备的不同控制算法并进行效果对比,通过所搭建的硬件在环实验平台验证所建控制策略是否正确,并确定最优算法。