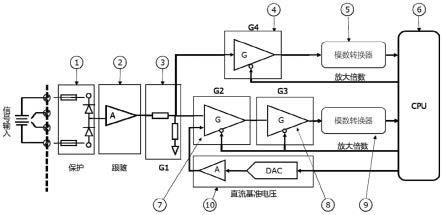
一种提高振动监视仪表信号测量精度的方法及系统
[技术领域]
[0001]
本发明属于汽轮机监视保护仪表技术领域,具体地说是一种提高振动监视仪表信号测量精度的方法及系统。
[
背景技术:]
[0002]
汽轮机监视保护仪表(turbine supervisory instruments,简称tsi仪表),是确保汽轮机安全运行的关键设备之一。tsi仪表需要监测和保护的参数信号很多,常用的测量参数有:振动(包括轴承振动、相对振动)、轴向位移、胀差、偏心、转速、零转速、键相、汽缸膨胀、油动机行程、同步器行程等。在这么多的测量参数中,振动信号的监视保护占了整个tsi仪表的70~80%左右,所以许多用户将tsi仪表称之为振动保护仪表,可见振动测量在tsi仪表中所占的地位,如何提高振动监视保护仪表的测量精度显得尤为重要。
[0003]
振动参数的测量包含轴承振动和相对振动的测量,轴承振动测量可以选择使用的传感器有:磁电式传感器和压电式传感器二类,相对振动使用的传感器有涡流式位移传感器,由于传感器测量原理的不同,所以传感器的输出信号也不一样。磁电式传感器的输出信号特点:在零位电压上叠加一个交流信号,用数学公式描述为:0v+ac,通常交流信号(ac)的信号范围为:0~700mv rms;压电式传感器的输出信号特点:在正直流电压上叠加一个交流信号,用数学公式描述为:+dc+ac;通常直流信号(+dc)的信号范围为:+10vdc~+14vdc,交流信号(ac)的信号范围为:0~200mv rms;涡流式位移传感器的输出信号特点:在负直流电压上叠加一个交流信号,用数学公式描述为:-dc+ac;通常直流信号(-dc)的信号范围为:-10vdc~-14vdc,交流信号(ac)的信号范围为:0~2v rms;但只有传感器输出的交流部分(ac)才是反映振动参数大小的信号,振动参数的大小与直流信号无关,也就是在振动监视器进行信号处理时仅需要处理交流信号。
[0004]
传统的振动监视器采用阻容隔直电路所构成的回路方式来实现,这种方案的处理电路比较简单,但测量精度较低,尤其对低频交流信号和小信号,其测量精度已经不能满足用户对振动测量的精度要求。
[0005]
如图2所示,为传统的振动参数测量信号处理电路框图,传感器信号经输入信号保护回路后,进行信号的阻抗匹配,然后输入到有一个电容元件和一个电阻元件组成回路g1,利用电容元件的隔直传交特性,传感器的直流信号被阻隔在电容之前,不能通过,只有交流信号可以通过电容元件,输入到信号放大器g2,经信号放大、模数转换后,送cpu系统进行振动参数的测量。采用阻容元件所构成的隔直回路,虽然电路简单,但测量精度低。特别是低频交流信号,经过回路g1后,低频交流信号衰减较多,信号频率越低,信号衰减越大。由于电容元件的存在,还影响交流信号的时域,使交流信号产生相移,对后续的振动解析和诊断系统的信号处理带来了困难。
[
技术实现要素:]
[0006]
本发明的目的就是要解决上述的不足而提供一种提高振动监视仪表信号测量精
度的方法,可有效地提高振动参数的测量精度,能够在测量各种不同传感器输入信号时,都能具有很高的测量精度,且不影响交流信号的时域,也不会使交流信号产生相移,保留了原始信号所包含的丰富的振动信息。
[0007]
为实现上述目的设计一种提高振动监视仪表信号测量精度的方法,包括以下步骤:将传感器的原始输出信号输入至输入信号保护回路1,进行输入信号的保护电路处理,然后依次输入信号跟随器回路2和信号放大器g1回路3,对输入信号进行阻抗匹配后分为两路进行信号处理,其中的一路信号处理直流分量,另一路信号处理交流分量;直流分量处理回路中,将完整信号经信号放大器g4回路4调整后,输入到模数转换器回路一5进行模数转换,再输入到cpu系统回路6,经计算后得出输入信号的直流分量;交流分量处理回路中,将输入信号与cpu系统回路6计算并经直流基准电压回路10中d/a转换器产生的直流分量信号,同时输入到信号放大器g2回路7进行相加处理,以消除原始输入信号中的直流分量,然后将处理后的交流信号经信号放大器g3回路8二次放大后,输入到模数转换器回路二9进行模数转换,将模拟量转化为数字量,再输入到cpu系统回路6,经计算得到振动信号。
[0008]
进一步地,所述输入信号保护回路1的输入端连接传感器信号,传感器信号通过差分输入的方式接入输入信号保护回路1,输入信号保护回路1用于对输入信号进行限流、限压,输入信号保护回路1对外接输入信号的限压范围为
±
24v,限流范围为30ma;信号跟随器回路2包含信号跟随器,信号跟随器用于阻抗匹配,信号跟随器提高输入阻抗以及降低输出阻抗。
[0009]
进一步地,所述信号放大器g1回路3采用精密电阻对搭建分压采样电路,并将原始的传感器输入信号衰减至后续放大电路的输入信号范围,以使得所有传感器的输入信号都处于信号放大器的线性放大区域内,且阻性电路不会影响信号的时域以及不会对交流信号产生相移。
[0010]
进一步地,所述信号放大器g4回路4包含信号放大器g4,信号放大器g4连接cpu系统回路6,信号放大器g4的放大倍数由cpu系统控制,cpu系统回路6根据输入信号的幅值大小,自适应地调整放大器的放大倍数,并将输入信号调整到模数转换器回路一5输入的最佳幅值;模数转换器回路一5采用18位的adc模数转换芯片完成模数转换,将规范后的模拟信号转换为原始数字量,并送cpu系统进行信号处理。
[0011]
进一步地,所述cpu系统回路6为以cpu芯片为中心所构成的计算机系统,cpu系统回路6完成数据采集、计算、控制和输出。
[0012]
进一步地,所述信号放大器g2回路7包含信号放大器g2,信号放大器g2采用一片高精度程控仪表放大器,其数字可控增益范围为1/8~128,信号放大器g2为相加放大器,将输入信号与经d/a转换后的直流分量信号,同时输入到相加放大器进行相加处理,消除信号中的直流分量进而隔离直流信号,信号放大器g2的放大倍数由cpu系统控制,cpu系统控制根据输入信号的大小自适应地调整放大器的放大倍数。
[0013]
进一步地,所述信号放大器g3回路8包含信号放大器g3,信号放大器g3采用一片高精度仪表放大器,采用一片低温漂的数字电位器来调整增益,其放大范围为1.5~128倍,信号放大器g3的放大倍数由cpu系统控制,cpu系统控制根据输入信号的幅值自适应地调整放大器的放大倍数,信号放大器g3将输入信号调整到模数转换器回路二9输入的最佳幅值。
[0014]
进一步地,所述模数转换器回路二9采用18位的adc模数转换芯片完成模数转换,
将规范后的模拟信号转换为交流信号的原始数字量,并送cpu系统进行信号处理,得到振动参数的测量值。
[0015]
进一步地,所述直流基准电压回路10的直流基准电压数据来自于cpu系统计算得到的输入信号的直流分量值,cpu系统采集直流分量回路的数据,经过计算处理后输出传感器信号中的直流信号,并送数模转换电路转换成规范后的模拟信号,数模转换电路采用一片16位dac芯片,其总不可调整误差小于0.1%fsr,最大积分非线性误差为
±
16lsb,并且内置+2.5v片内基准电压源,输出一个-10.8v~+10.8v电压,经跟随器电路进行阻抗匹配,用于补偿掉振动信号上叠加的直流信号。
[0016]
本发明还提供了一种提高振动监视仪表信号测量精度的系统,包括输入信号保护回路1、信号跟随器回路2、信号放大器g1回路3、信号放大器g4回路4、模数转换器回路一5、cpu系统回路6、信号放大器g2回路7、信号放大器g3回路8、模数转换器回路二9和直流基准电压回路10,所述输入信号保护回路1的输出端连接信号跟随器回路2的输入端,所述信号跟随器回路2的输出端连接信号放大器g1回路3的输入端,所述信号放大器g1回路3的输出端分成两路,一路连接信号放大器g4回路4,所述信号放大器g4回路4的输出端连接模数转换器回路一5的输入端,所述模数转换器回路一5的输出端连接cpu系统回路6;另一路连接信号放大器g2回路7,所述信号放大器g2回路7的输出端连接信号放大器g3回路8,所述信号放大器g3回路8的输出端连接模数转换器回路二9的输入端,所述模数转换器回路二9的输出端连接cpu系统回路6,所述cpu系统回路6的输出端分别连接信号放大器g2回路7、信号放大器g3回路8、直流基准电压回路10,所述直流基准电压回路10的输出端连接信号放大器g2回路7。
[0017]
本发明同现有技术相比,提供了一种提高振动监视仪表信号测量精度的方法,采取直接采样传感器的原始信号,通过cpu系统计算出原始信号中的直流分量,利用这个直流分量与原始信号进行相加,将消除了绝大部分的直流分量后的交流信号进行放大,根据输入信号的幅值,由cpu系统控制,自适应地调整高精度程控仪表放大器的放大倍数,将输入信号调整到模数转换器输入的最佳幅值,这样就可以充分发挥模数转换器的转换精度,达到提高测量精度的目的;该信号处理电路中,没有电容元件存在,不会影响交流信号的时域,不会使交流信号产生相移,克服了传统的采用阻容元件所构成的隔直回路,测量精度低,低频交流信号衰减大,影响交流信号的时域,使交流信号产生相移等弊病。综上,本发明可有效地提高振动参数的测量精度,此测量电路不影响交流信号的时域,也不会使交流信号产生相移,保留了原始信号所包含的丰富的振动信息;而且,本发明在测量各种不同传感器输入信号时,都能具有很高的测量精度,尤其需要能够测量在大幅直流信号上叠加的小幅交流信号的精度,值得推广应用。
[附图说明]
[0018]
图1是本发明测量电路的电路框图;
[0019]
图2是传统测量电路的框图;
[0020]
图中:1、输入信号保护回路 2、信号跟随器回路 3、信号放大器g1回路 4、信号放大器g4回路 5、模数转换器回路一 6、cpu系统回路 7、信号放大器g2回路 8、信号放大器g3回路 9、模数转换器回路二 10、直流基准电压回路。
[具体实施方式]
[0021]
本发明提供了一种提高振动监视仪表信号测量精度的方法,包括以下步骤:将传感器的原始输出信号输入至输入信号保护回路1,进行输入信号的保护电路处理,然后依次输入信号跟随器回路2和信号放大器g1回路3,对输入信号进行阻抗匹配后分为两路进行信号处理,其中的一路信号处理直流分量,另一路信号处理交流分量;直流分量处理回路中,将完整信号经信号放大器g4回路4调整后,输入到模数转换器回路一5进行模数转换,再输入到cpu系统回路6,经计算后得出输入信号的直流分量;交流分量处理回路中,将输入信号与cpu系统回路6计算并经直流基准电压回路10中d/a转换器产生的直流分量信号,同时输入到信号放大器g2回路7进行相加处理,以消除原始输入信号中的直流分量,然后将处理后的交流信号经信号放大器g3回路8二次放大后,输入到模数转换器回路二9进行模数转换,将模拟量转化为数字量,再输入到cpu系统回路6,经计算得到振动信号。
[0022]
本发明还提供了一种提高振动监视仪表信号测量精度的系统,包括输入信号保护回路1、信号跟随器回路2、信号放大器g1回路3、信号放大器g4回路4、模数转换器回路一5、cpu系统回路6、信号放大器g2回路7、信号放大器g3回路8、模数转换器回路二9和直流基准电压回路10,输入信号保护回路1的输出端连接信号跟随器回路2的输入端,信号跟随器回路2的输出端连接信号放大器g1回路3的输入端,信号放大器g1回路3的输出端分成两路,一路连接信号放大器g4回路4,信号放大器g4回路4的输出端连接模数转换器回路一5的输入端,模数转换器回路一5的输出端连接cpu系统回路6;另一路连接信号放大器g2回路7,信号放大器g2回路7的输出端连接信号放大器g3回路8,信号放大器g3回路8的输出端连接模数转换器回路二9的输入端,模数转换器回路二9的输出端连接cpu系统回路6,cpu系统回路6的输出端分别连接信号放大器g2回路7、信号放大器g3回路8、直流基准电压回路10,直流基准电压回路10的输出端连接信号放大器g2回路7。
[0023]
下面结合附图对本发明作以下进一步说明:
[0024]
输入信号保护回路1,传感器输出的原始信号通过差分输入的方式接入监视器,输入信号保护回路1的主要功能是对输入信号进行限流、限压,防止过大的输入电压或电流,对监视器模块造成损坏。对外接输入信号的限压范围为:
±
24v,限流范围为:30ma。
[0025]
信号跟随器回路2,信号跟随器主要的作用是阻抗匹配,提高输入阻抗,降低输出阻抗,以减少对传感器的影响和增加带负载能力。
[0026]
分压采样电路3,采用精密电阻对,搭建分压采样电路,将原始的传感器输入信号衰减至后续放大电路的输入信号范围,确保所有传感器的输入信号都处于信号放大器的线性放大区域内,阻性电路不会影响信号的时域,不会对交流信号产生相移。
[0027]
信号放大器g4回路4,信号放大器g4的放大倍数是由cpu系统控制,可以根据输入信号的幅值大小,自适应地调整放大器的放大倍数,把输入信号调整到模数转换器输入的最佳幅值,这样可以充分发挥模数转换器的转换精度。
[0028]
模数转换器回路一5,采用18位的adc模数转换芯片完成模数转换,将规范后的模拟信号转换为原始数字量,送cpu系统进行信号处理。
[0029]
cpu系统回路6,以cpu芯片为中心所构成的计算机系统,简称为cpu系统回路,计算机系统是振动监视仪表的核心部件,完成数据采集、计算、控制、输出等功能。
[0030]
信号放大器g2回路7,采用了一片高精度程控仪表放大器,低失调电压,接近零偏
移和增益漂移,1/f噪声极低,数字可控增益范围1/8~128,信号放大器g2是一个相加放大器,将输入信号与经d/a转换后的直流分量信号,同时输入到相加放大器,进行相加处理,以便消除信号中的直流分量,起到隔离直流信号的作用,信号放大器g2的放大倍数是由cpu系统控制,可以根据输入信号的大小,自适应地调整放大器的放大倍数。
[0031]
信号放大器g3回路8,信号放大器g3采用了一片高精度仪表放大器,具有非常低的偏置电压、温度偏移和高共模抑制,采用了一片低温漂的数字电位器用来调整增益,256位,总谐波失真0.006%,放大范围1.5~128倍。信号放大器g3的放大倍数是由cpu系统控制,可以根据输入信号的幅值,自适应地调整放大器的放大倍数,把输入信号调整到模数转换器输入的最佳幅值,可以充分发挥模数转换器的转换精度。
[0032]
模数转换器回路二9,采用18位的adc模数转换芯片完成模数转换,将规范后的模拟信号转换为交流信号的原始数字量,送cpu系统进行信号处理,得到振动参数的测量值。
[0033]
直流基准电压回路10,直流基准电压的数据来自于cpu计算得到的输入信号的直流分量值,cpu系统采集了直流分量回路的数据,经过计算处理后输出传感器信号中的直流信号,送数模转换电路转换成规范后的模拟信号,数模转换电路采用了一片16位dac芯片,总不可调整误差小于0.1%fsr,最大积分非线性(inl)误差为
±
16lsb,噪声很低,典型建立时间为10μs,并且内置+2.5v片内基准电压源。输出一个-10.8v~+10.8v电压,经跟随器电路进行阻抗匹配,用于补偿掉振动信号上叠加的直流信号。自适应的精度调整方法:根据传感器的输入类型和信号特点,磁电式传感器的输出信号特点:在零位电压上叠加一个交流信号,用数学公式描述为:0v+ac,通常交流信号(ac)的信号范围为:0~700mv rms;压电式传感器的输出信号特点:在正直流电压上叠加一个交流信号,用数学公式描述为:+dc+ac;通常直流信号(+dc)的信号范围为:+10vdc~+14vdc,交流信号(ac)的信号范围为:0~200mv rms;涡流是位移传感器的输出信号特点:在负直流电压上叠加一个交流信号,用数学公式描述为:-dc+ac;通常直流信号(-dc)的信号范围为:-10vdc~-14vdc。
[0034]
调整方法如下:1)信号放大器g3的增益调整为3.87,信号放大器g2的增益和直流基准电压输出根据信号类型进行调整。2)交流回路测量静态值,各初始值调整在中值附近。3)若值超量程,缩减信号放大器g3和信号放大器g2的放大倍数(增益),优先缩减信号放大器g2,使测量值调整在量程范围内。4)调整直流基准电压输出,使测量值调整在中值附近。5)在动态测量时发现超量程,也同样调整信号放大器g3和信号放大器g2的放大倍数(增益)。
[0035]
本发明所述的提高振动监视仪表信号测量精度的方法,具体地,(1)将传感器的原始输出信号输入到监视器,信号采用差分输入,首先进行输入信号的保护电路处理,防止因错接线等人为因素造成监视器的损坏,然后对输入信号进行阻抗匹配后分为两路进行信号处理,其中的一路信号处理直流分量,另一路信号处理交流分量;(2)直流分量处理回路,将完整信号经信号放大器调整到模数转换器输入的最佳范围后,输入到模数转换器进行模数转换,再输入到cpu系统,经计算后得出输入信号的直流分量;(3)交流分量处理回路,将输入信号与cpu计算并经数模转换(d/a)并反相后的直流分量信号同时输入到信号放大器,进行相加处理,以便消除原始输入信号中大部分的直流分量,然后将处理后的小幅交流信号经二次放大匹配至模数转换器的最佳范围,输入到模数转换器进行模数转换,将模拟量转化为数字量,再输入到cpu系统,经计算得到振动信号。(4)使用高精度程控仪表放大器,适
时调整高精度程控仪表放大器的放大倍数,将交流信号调整到模数转换器输入的最佳幅值后,这样就可以充分发挥模数转换器的转换精度,达到提供测量精度的目的。
[0036]
即,信号采用差分输入,将原始信号一分为二,分为两路进行信号处理,一路信号处理直流分量,另一路信号处理交流分量。直流分量处理回路,经信号放大器调整到模数转换器输入的最佳幅值后,进行模数转换,将规范后的模拟信号转换为原始数字量,送cpu系统,经计算后得出输入信号的直流分量。交流分量处理回路,将输入信号与cpu计算并经d/a转换器产生的直流分量信号进行相加处理,以便消除信号中的直流分量,交流分量经过二次放大,调整到模数转换器输入的最佳数值后,将模拟量转化为数字量,送cpu系统,经计算得到振动信号。适时调整高精度程控仪表放大器的放大倍数,将交流信号调整到模数转换器输入的最佳幅值后,这样就可以充分发挥模数转换器的转换精度,达到提供测量精度的目的。
[0037]
综上所述,本发明将传感器的输入信号分二部分电路来进行处理。一路将传感器的原始信号直接进行数模转换后,输送至cpu系统经过运算,计算出直流分量;另一路将原始信号和由cpu系统计算出来的直流分量,送线性放大器后进行相加运算,消除绝大部分的直流分量后进行放大,将放大后的交流信号进行数模转换送cpu系统,经过运算后计算得到振动值。经过这样的过程后,所测量的振动信号精度将有大幅度的提高。相较于如附图2所示的传统的振动参数测量信号处理电路,本发明的振动信号处理电路,没有电容元件存在,不会影响交流信号的时域,不会使交流信号产生相移。
[0038]
本发明并不受上述实施方式的限制,其他的任何未背离本发明的精神实质与原理下所作的改变、修饰、替代、组合、简化,均应为等效的置换方式,都包含在本发明的保护范围之内。