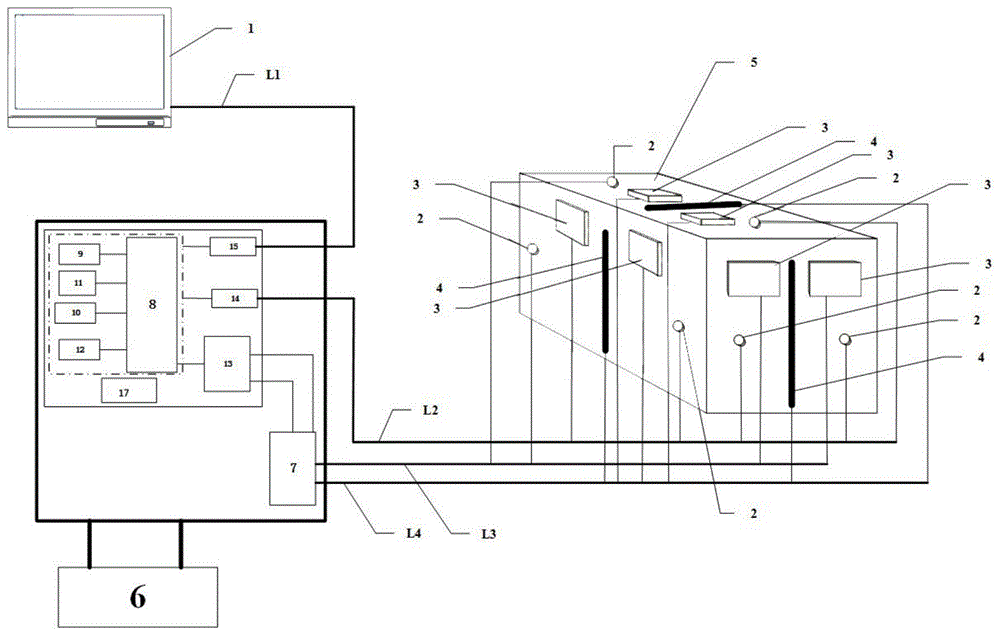
本实用新型涉及ct领域,尤其是涉及一种ct数据采集系统恒温控制装置。
背景技术:
:在ct设备应用过程中,通过数据采集系统来获取病患的检查数据,并通过一定的重建算法对检查数据进行处理,从而获取病患的检查图像。病患的ct检查图像质量,决定了病患病情的诊断分析效率与病因定位准确性,在实际ct应用中,由于ct涉及到各种处理模块,往往包含了各类精密系统,这些精密系统会以各种因素影响ct图像质量,其中数据采集系统作为数据采集的核心部件,数据采集系统采集的数据准确性能够直接影响生成的ct图像质量,数据采集系统中的各个探测器模块会因各种干扰、噪声,导致扫描数据出现失真,从而导致图像出现伪影,严重影响医院技师阅片,而探测器模块特性决定了其对环境温度非常敏感,因此数据采集系统内部温度,作为一个重要干扰的因素,会影响数据采集系统采集数据的准确性,在进行扫描作业时,需要保持数据采集系统内部温度恒定。另外一个方面,探测器的使用寿命也会受环境温度、湿度的影响,即使在ct处于待机或者关机状态时,也要求探测器模块的环境温度处于恒温状态。综上两个方面,对于ct的数据采集系统,需要相应的措施和装置来保持数据采集系统内部温度恒定,进而提高ct扫描的图像质量和探测器的使用寿命。技术实现要素:本实用新型的目的就是为了克服上述现有技术存在的缺陷而提供一种ct数据采集系统恒温控制装置。本实用新型的目的可以通过以下技术方案来实现:一种ct数据采集系统恒温控制装置,包括设置于数据采集箱内部的多个温度传感器、多个加热条和多个散热风扇,所述温度传感器、加热条和散热风扇与温度控制盒连接,所述温度控制盒连接主控设备,所述温度控制盒连接独立电源。多个所述温度传感器分别设置于采集箱的不同箱壁,多个所述加热条分别设置于采集箱的不同箱壁,多个所述散热风扇分别设置于采集箱的不同箱壁。所述的温度控制盒包括主处理单元和驱动电路单元,所述主处理单元包括微处理器和与微处理器连接的电源转换模块、flash模块、ddr内存模块、定时器模块、看门狗模块、io模块、i2c模块和can模块,所述独立电源通过电源转换模块连接微处理器,所述微处理器通过i2c模块与温度传感器连接,所述微处理器通过can模块与主控设备连接,所述微处理器依次通过io模块和驱动电路单元分别与加热条和散热风扇连接。所述微处理器为stm32f103c8t6微处理器。所述散热风扇与蜂窝波导板连接。蜂窝波导板与散热风扇之间设置防尘海绵块。所述蜂窝波导板的蜂窝孔径为6mm。所述的蜂窝波导板的尺寸为70*70*15mm。所述的蜂窝波导板与散热风扇通过螺栓固定在一起。温度传感器为aht10温度传感器。与现有技术相比,本实用新型具有以下优点:(1)采用多个温度传感器、多个加热条和多个散热风扇,多个温度传感器提高了反馈温度值的准确性,多个加热条和多个散热风扇实现了温度的精确调整,进而提高了采集箱内部的温度恒定性和均匀性。(2)采用蜂窝波导板,既满足通风散热要求,又能满足电磁屏蔽性能要求。(3)采用外部独立电源供电,主线路下电或者待机情况下,持续进行恒温控制。附图说明图1为本实用新型的结构示意图;图2为本实用新型的散热风扇和蜂窝波导板示意图;图3为本实用新型的信号传递示意图;图4为本实用新型的流程图;图5为本实用新型的模糊规则视图;图6为普通pid温度阶跃响应曲线;图7为本实用新型的模糊pid温度阶跃响应曲线;附图标记:1为主控设备;2为温度传感器;3为散热风扇;4为加热条;5为采集箱;6为独立电源;7为驱动电路单元;8为微处理器;9为flash模块;10为ddr内存模块;11为定时器模块;12为看门狗模块;13为io模块;14为i2c模块;15为can模块;16为蜂窝波导板;17为电源转换模块。具体实施方式下面结合附图和具体实施例对本实用新型进行详细说明。本实施例以本实用新型技术方案为前提进行实施,给出了详细的实施方式和具体的操作过程,但本实用新型的保护范围不限于下述的实施例。实施例本实施例提供一种ct数据采集系统恒温控制装置,如图1所示,包括设置于数据采集箱5内部的多个温度传感器2、多个加热条4和多个散热风扇3,温度传感器2、加热条4和散热风扇3与温度控制盒连接,温度控制盒连接主控设备1,温度控制盒连接独立电源6,独立电源6指独立于恒温控制装置的电源;多个温度传感器2提高了反馈温度值的准确性,多个加热条4和多个散热风扇3实现了温度的精确调整,进而提高了采集箱5内部的温度恒定性和均匀性。具体而言:主控设备1包括主控制器和液晶显示屏,主要向温度控制盒发送温度设定指令(恒温目标),同时接收温度控制盒发送过来的采集箱5内部温度数据,并显示在液晶显示屏上面,主控设备1与温度控制盒通过线缆l1进行连接,进行can通信协议传输。本实施例的采集箱5为主要由六块金属板拼合形成的长方体金属箱,内部安装有对应的ct数据采集模块,形成封闭的暗室,完成ct扫描数据的采集。采集箱5的前部箱壁、顶部箱壁、左侧箱壁、右侧箱壁的内侧安装有加热条4、温度传感器2、散热风扇3,前、顶、左和右是以图1为参考。多个温度传感器2分别设置于采集箱5的不同内壁,多个加热条4分别设置于采集箱5的不同内壁,多个散热风扇3分别设置于采集箱5的不同内壁。本实施例前部箱壁、顶部箱壁、左侧箱壁、右侧箱壁分别安装两个温度传感器2、一个加热条4和两个散热风扇3,当然采集箱5内的温度传感器2、加热条4和散热风扇3只要均为多个即可,不是必须满足本实施例的安装数量。温度传感器2通过线束l2与温度控制盒连接,通过i2c协议进行通信;加热条4主要在暗室温度过低时,通过加热条4散发热量,提高环境温度;散热风扇3分别安装于散热窗口,散热窗口是开正方形孔形成的窗口。如图2所示,散热窗口处散热风扇3与蜂窝波导板16连接,其中散热风扇3通过线束l3与温度控制盒连接,温度控制盒控制散热风扇3旋转,保证采集箱5内部空气流通,来降低采集箱5的温度。采集箱5通风、散热的需要,不可避免要在箱壁上开孔,但这样一来采集箱5内部的电子设备就会受到外界的电磁干扰,同时也向外界辐射电磁波造成电磁泄露,影响其它设备的正常工作。蜂窝波导板16具有集肤效应,蜂窝波导板16的管状金属结构壁厚可以很小,总开孔面积相应增加;蜂窝波导板16既满足通风散热要求,又能满足电磁屏蔽性能要求。温度传感器2的型号为aht10,测量范围-40至+85℃,温度精度正负0.3摄氏度,供电电压3.3v。散热窗口为正方形,长70mm,宽70mm。散热风扇3为直流风机,驱动电路进行12v供电,尺寸为60*60*15mm,最大转速为5700转每分钟。蜂窝波导板16尺寸为70*70*15mm,内部蜂窝孔径为6mm。散热风扇3与蜂窝波导板16通过螺栓固定在一起。蜂窝波导板16与散热风扇3之间放置防尘海绵块,用于去除灰尘。加热条4采用12v供电,最大功率为5w。加热条4通过线束l4与温度控制盒连接。如图1所示,温度控制盒包括电源转换模块17、主处理单元和驱动电路单元7,主处理单元包括微处理器8和与微处理器8连接的flash模块9、ddr内存模块10、定时器模块11、看门狗模块12、io模块13、i2c模块14和can模块15,本实施例还包括串口通信模块,独立电源6通过电源转换模块17连接微处理器8,微处理器8通过i2c模块14与温度传感器2连接,微处理器8通过can模块15与主控设备1连接,微处理器8依次通过io模块13和驱动电路单元7分别与加热条4和散热风扇3连接,微处理器8通过串口通信模块与外部调试终端进行调试信息交互。微处理器8通过本地系统总线与主处理单元中其他模块连接。驱动电路单元7主要由mos管和三极管以及光耦组成,用于控制加热条4和散热风扇3供电。驱动电路单元7为现有技术。微处理器8通过io模块13输出散热风扇3的pwm控制信号enablefan,控制散热风扇3的转速;微处理器8通过io模块13输出加热条4的pwm控制信号enableheater,控制加热条4的供电电压。微处理器8的型号为stm32f103c8t6,主频为72mhz。ddr内存模块10为主处理单元运行系统程序和应用程序提供内存空间,其内存空间大小为16mb。串口通信模块主要完成调试消息的收发,波特率为1152000bps,使用rs232电平。i2c模块14主要完成i2c数据的交互,波特率为400kbps。can模块15主要完成can消息的收发,支持can协议2.0b,波特率为1mbps,使用差分信号。电源转换模块17将独立电源6的电压转换成3.3v的电压,给主处理单元供电。看门狗模块12主要检测主处理单元的运行状态,当主处理单元出现异常或者程序跑飞的情况,看门狗模块12能够复位主处理单元。定时器模块11为主处理单元提供50ms周期的定时中断信号。微处理器8上运行的操作系统为嵌入式freertos操作系统,freertos操作系统是一款具备微内核特征、安全、实时、可靠的嵌入式操作系统。运行在主处理单元上的主处理软件采用标准c语言和汇编语言进行软件开发。本实施例还提供一种ct数据采集系统恒温控制方法,基本控制框图如图4。系统启动时,温度控制盒按照设置好的温度进行加热,此时散热风扇3停止转动,从而使环境温度能迅速到达目标温度。而一旦环境温度超过目标温度,温度控制盒控制散热风扇3转动进行散热,并且控制加在加热条4上的电压,使加热变缓,并小于散热速度,从而将环境温度下降。当环境温度下降至目标温度以下时,温度控制盒控制散热风扇3电压和加热条4电压,重新加热,这样使环境温度在目标温度附近达到动态平衡。温度控制盒主要接收主控设备1的恒温目标,温度控制盒将恒温目标经过处理后,控制散热风扇3和加热条4,来控制采集箱5的温度达到平衡状态。温度控制盒将主控设备1发送过来的恒温目标作为输入控制信息,将温度传感器2采集的温度数据作为反馈值,温度控制盒依据输入值和反馈值,计算温度控制误差,直到温度误差达到控制精度要求。具体步骤如下:101、装置启动后,对温度控制盒的各个模块进行初始化;102、充电控制盒对i2c、can、串口模块进行初始化,设置正常的通信参数,与主控设备1建立can通信,与温度传感器2建立i2c通信,充电控制盒处于待机状态;103、充电控制盒通过i2c总线与所有的温度传感器2进行通信,初始化温度传感器2,设置温度传感器2采集参数,对温度传感器2进行标定,使温度传感器2)处于待机状态;104、温度控制盒进行逻辑运算处理;105、如果接收到主控设备1通过can发送过来的恒温目标,执行步骤106;否则执行步骤107;106、更新恒温温度设定值,即将默认的恒温值修改为恒温目标;107、通过i2c总线,依次获取8个温度传感器2的温度数据;108、通过温度传感器2信息融合处理逻辑,对获取到的温度数据进行信息处理;109、将8个传感器的温度数据以及融合温度数据发送至主控设备1进行显示;110、如果融合温度数据与恒温目标的差值不在允许的误差范围内,执行步骤111;否则返回执行步骤104;111、如果融合温度数据高于恒温目标,执行步骤112;否则返回执行步骤113;112、温度控制盒通过模糊控制器处理,输出使能enablefan信号,控制散热风扇3转速;然后返回执行步骤104;113、如果融合温度数据低于恒温目标,执行步骤114;否则返回执行步骤104;114、温度控制盒通过模糊控制器处理,输出使能enableheater信号,控制加热条4供电;然后返回执行步骤104;多个温度传感器2的温度数据的融合原理如下:因气流、气压、加热器特性、导热特性等因素,可能导致采集室内部的温度非均匀分布。故在不同的位置的实际温度数据可能与恒温目标的偏差不一致。从而导致内部各个部位的温度不一致。采用多个温度传感器2,并且温度传感器2按照温度分布特征来布置。并将多个温度传感器2的温度数据进行融合,降低温度传感器2布置导致的温度误差。温度传感器2的安装设置要求:1、温度传感器2尽量靠近ct数据采集模块。2、温度传感器2安装个数尽量多,弥补安装位置带来的误差。假设有k个温度传感器,tn为第n个温度传感器实时温度数据,wn为第n个温度传感器的温度分布权重(可以实际实验测试和热设计仿真来确定,与温度传感器距离ct数据采集点的远近有关)。模糊控制器原理如下:ct数据采集系统恒温控制装置是一个多输入多输出的复杂系统,这类温度控制系统具有难以建模、强耦合、非线性、多变量、大滞后、时变性等特点,一般情况下,为了使极点配置、pid等传统控制算法在温度控制系统表现出优良的控制特性,要求已知装置的模型参数和温度响应都有理想的性能。但是在实际应用中,很难满足这些要求。恒温控制装置还存在多个不确定因素:1)材料物理特性、散热特性、气压、气流、传感器信息融合等因素,2)温度时滞、传感器误差。所以,在控制温度时,要求控制算法必须具有很强的鲁棒性来应对这些不确定因素。事实上,因为以上不确定因素的原因,传统的控制方法很难获得较好的控制效果。模糊控制是一种以模糊逻辑推理、模糊语言变量、模糊集理论为基础的智能控制方法,在使用该方法时,先要将人的对某个事件的控制经验转换成模糊规则库,将输入信号和反馈信号进行量化并模糊化,然后利用模糊集中的模糊规则,对输入模糊信息进行模糊推理,得到模糊控制器的数量,经去模糊化装换后施加到被控对象的执行器上,从而实现控制任务。控制经验为:“如果融合温度数据高于恒温目标,则关闭加热条供电,散热风扇旋转进行降温,温度差值越大,控制散热风扇旋转电压越大”;“如果融合温度数据低于恒温目标,则关闭散热风扇,增加加热条供电电压,温度差值越大,控制加热条加热电压越大”。根据以上经验,按下列步骤设计模糊控制规则:1)确定观测量和控制量定义恒温目标的温度为t0,实际测得的融合温度数据为t,选择电压差对应的pwm占空比,将融合温度数据t对于恒温目标的偏差e、偏差变化率ec作为观测量。2)输入量和输出量的模糊化将偏差e分为五个模糊集:负大(nb)、负小(ns)、零(o)、正小(ps)和正大(pb),偏差e、偏差变化率ec模糊论域均为{-30,-20,-10,0,10,20,30}。控制量r为散热风扇转速控制占空比的调节量和加热条控制占空比的调节量。将其分为五个模糊集:负大(nb)、负小(ns)、零(zo)、正小(ps)和正大(pb)。并将r的变化范围分为7个等级:{-100,-50,-25,0,25,50,100}。3)建立模糊规则,描述见表1模糊规则表。表1模糊规则表e\r\ecnbnmnszopspmpbnbnbnbnbnmnmnmnmnmnbnmnmnsnsnsnsnsnmnsnsnsnsnsnszopspszozozonsnspspspspspspspspmpmpspspspspmpmpbpbpmpmpmpmpbpbpb融合温度数据与恒温目标的偏差e和偏差变化率ec计算如下:e=t–t0ec=δe/δtt为融合温度数据,t0为恒温目标,传递函数如下:kt为放大系数,tr为时间常数。图6和图7对比可以看出,本实施例加入模糊控制后pid温度阶跃响应曲线更加平滑。当前第1页12