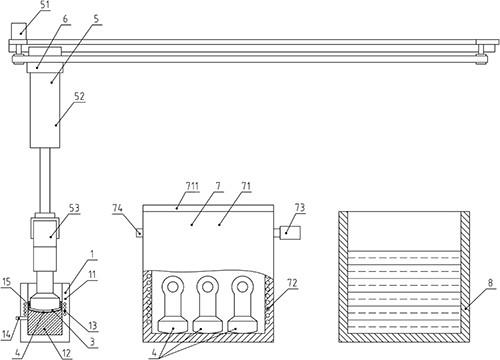
1.本发明涉及人工智能生产系统技术领域,涉及一种矿山设备维修维护的自动化智能化处理系统,具体涉及一种合金板锤磨损工作面远程控制智能修复设备。
背景技术:2.在矿石开采过程中,把大块矿石破碎的主流设备还是锤式破碎机。锤式破碎机的主要工作部件是板锤,板锤包括锤头和锤柄,锤头的基体材质是高锰钢,高锰钢具有良好的韧性,不易断裂。
3.为了提高锤头工作面的硬度和耐磨性能,往往在锤头工作面上使用特殊的工艺增加钒的碳化物涂层,这样能使板锤的使用寿命大幅提高,具体方法是,在板锤铸造型腔内、锤头工作面部位预先放置一张石墨纸当作碳源,再重叠放一张钒板,然后把热的钢液倒入型腔内铸造成型,在高温的环境下钒元素、石墨中的碳发生化学反应生成梯度复合涂层即碳化物涂层,所述碳化物涂层包括依次呈梯度分布的准单晶相v2c致密陶瓷层、微米v8c7致密陶瓷层和v8c7与基体的融合层。即便如此,锤头工作面在如此恶劣的工况下,锤头工作面上的钒 的碳化物涂层在使用三四个月后就磨损脱落,裸露的高锰钢基体就会很快破坏,不能继续使用,需要更换新的板锤,更换下的板锤被当作废品处理掉,一般都被送去铸造厂熔为钢液重新铸造,这要消耗很多能源,耗费劳动力,成本较高,矿山生产单位重新采购新的板锤当作配件,维修维护的费用较高。
4.如果在碳化物涂层部分脱落之后进行修复,那无疑会节省很多工艺过程,板锤基体重新铸造费用、制造工时费都可以节省下来,矿石开采单位可以自己配置一套修复工具,周转运输费可以节省下来。然而到目前为止还没有人研究板锤磨损工作面修复技术。
技术实现要素:5.本发明就是针对现有技术存在的上述不足,提供一种延长板锤的使用寿命、节省能源和劳动力、节省维修维护的费用、节省周转运输费用、操作简单易用的合金板锤磨损工作面远程控制智能修复设备。
6.为实现上述目的,本发明提供如下技术方案:一种合金板锤磨损工作面远程控制智能修复设备,包括plc可编程控制器,plc可编程控制器包括cpu单元、模拟输入单元、数字输入单元和数字输出单元;模拟输入单元、数字输入单元和数字输出单元分别通过数据总线与cpu单元联接; 还包括砂箱组件、搬运机器人和测力单元;砂箱组件包括砂箱、第一加热单元和第一测温传感器;第一加热单元包括第一线圈;砂箱是一个开口朝上的容器,砂箱内装有铸造砂;第一线圈和第一测温传感器装在砂箱的壁内;第一线圈与plc可编程控制器的数字输出单元联接;第一测温传感器与plc可编程控制器的模拟输入单元联接;搬运机器人包括横移组件、升降液压缸和夹持组件;横移组件的支架和机架固定
联接,横移组件的活动部件与力传感器的上端固定联接,力传感器的下端和升降液压缸的上端固定联接,夹持组件和升降液压缸的下端固定联接;横移组件、升降液压缸和夹持组件分别与plc可编程控制器的数字输出单元联接;横移组件驱动升降液压缸、力传感器和夹持组件的组合沿水平方向移动;砂箱内的铸造砂上表面做成和板锤的锤头工作面形状相吻合的凹坑,在凹坑内表面上铺上石墨纸和钒板,石墨纸敷贴在凹坑内表面上,钒板敷贴在石墨纸上面;夹持组件夹持住板锤,板锤的锤头工作面朝下,升降液压缸驱动板锤向下平移,板锤的锤头工作面嵌入凹坑,并保持1500n至4500n的压力,由力传感器检测并反馈压力信号;然后第一线圈通电对板锤的锤头部位电感应加热至1450~1480℃,接近于融熔的温度,在此温度下钒板也软化,锤头工作面和钒板贴合在一起形成高锰钢基体和钒的复合体,外表面还粘附有石墨成份;第一测温传感器获取锤头工作面的温度,把锤头工作面的温度反馈给plc可编程控制器,以便于调整第一加热单元的工作参数。
7.以上所述的板锤的锤头工作面嵌入凹坑,并保持1500n至4500n的压力是指钒板厚度是0.3毫米时的压力,钒板厚度越厚则需要越大的压力,板锤的锤头部位加热的温度越低则需要越大的压力,以保证钒板能产生足够大的变形,变形后的钒板与板锤的锤头工作面的外形充分贴附在一起。
8.本发明还包括保温箱组件,保温箱组件包括保温箱、第二加热单元和保温箱盖,保温箱是开口朝上的容器,第二加热单元包括第二线圈,板锤放置在保温箱里面,第二线圈与plc可编程控制器的数字输出单元联接,plc可编程控制器发送指令使第二线圈对板锤电感应加热;保温箱盖密封地联接在保温箱的上口。
9.搬运机器人把板锤从砂箱中取出来,放入保温箱,相比人工搬运,节省劳动力,提高安全性,工作现场气温非常高,板锤表面的温度非常高,容易发生烫伤事故,人工操作危险性非常高,工作环境非常恶劣。改成搬运机器人搬运能避免现场工作的工人受伤,提高生产安全性。
10.本发明还包括第二测温传感器,第二测温传感器安装在保温箱内,第二测温传感器与plc可编程控制器的模拟输入单元联接,第二测温传感器用于检测板锤表面的温度,以便于确定第二线圈的加热参数,使板锤的温度控制在需要的范围内。
11.本发明还包括通氮气管道,通氮气管道上设置氮气电磁阀;通氮气管道与保温箱内腔联通,氮气电磁阀与plc可编程控制器的数字输出单元联接,通过氮气电磁阀向保温箱内腔通入氮气,使板锤表面不与空气接触,防止板锤表面氧化。
12.本发明还包括水槽,水槽中装有水,搬运机器人把板锤从保温箱取出来立刻放入水槽进行淬火处理。
13.使用本发明修复板锤的工作过程如下所述。
14.1)砂箱内的铸造砂上表面做成和板锤的锤头工作面形状相吻合的凹坑,在凹坑内表面上铺上石墨纸和钒板,石墨纸敷贴在凹坑内表面上,钒板敷贴在石墨纸上面;2)夹持组件夹持住板锤,板锤的锤头工作面朝下,升降液压缸驱动板锤向下平移,板锤的锤头工作面嵌入凹坑,石墨纸和钒板夹在锤头工作面和凹坑表面之间,并保持1500n至4500n的压力,由力传感器检测并反馈压力信号,以便于调整升降液压缸的工作参数;在砂箱内壁与板锤外侧之间的缝隙中还设置有密封装置,防止下面的铸造砂向上溢出,密封
装置还不能妨碍板锤从中间通过;3)第一线圈通电对板锤电感应加热,加热至锤头部位温度在1450~1480℃,并保持一至三分钟,锤头工作面接近于融熔的温度,在此温度下钒板也软化,锤头工作面和钒板贴合在一起形成高锰钢基体和钒的复合体;第一测温传感器获取锤头工作面的温度,反馈给plc可编程控制器,根据温度参数调整第一加热单元的工作参数;由于铸造砂具有流动性,锤头工作面上有不规则的凸起或凹陷,凹坑表面上与凸起接触的铸造砂能自动流向凹陷处,在铸造砂的压力作用下锤头工作面、钒板和石墨纸紧密地贴合在一起,中间不留空隙;4)保持1500n至4500n的压力,保持一定的接触压强,保持一定的温度,持续一定的时间,然后随室温冷却,得到的板锤工作面带有梯度复合涂层,而锤头基体是钢基体,外表面还粘附有一层石墨;5)升降液压缸把板锤向上提起,离开砂箱;6)搬运机器人把板锤放入保温箱;7)plc可编程控制器发送指令,开启氮气电磁阀,通氮气管道向保温箱中通入氮气,并保持比大气压高50至100kpa的氮气压力,使板锤表面与空气隔离;比大气压高的压力能促使碳元素和钒元素向锤头基体内渗透,提高涂层的附着力;8)第二加热单元通过电感应加热锤头至1000-1160℃的保温温度,升温速度控制在7℃/min,保温时间为10至11小时;在这个过程中,钒元素、石墨中的碳发生化学反应生成梯度复合涂层即钒的碳化物涂层,所述钒的碳化物涂层包括依次呈梯度分布的准单晶相v2c致密陶瓷层、微米v8c7致密陶瓷层和v8c7与基体的融合层;9)第二测温传感器获取板锤的温度,反馈给plc可编程控制器,以便于调整第二加热单元的工作参数;10)板锤随炉冷却至室温;11)第二加热单元通过电感应加热锤头至1000℃:第一小时升温至300℃,然后按每小时50℃的速度升温到1000℃,使高锰钢充分进行奥氏体化,保温1.8至2.2小时;12)第二测温传感器获取板锤的温度,反馈给plc可编程控制器,以便于调整第二加热单元的工作参数;13)搬运机器人把板锤从保温箱中取出淬入水中,最终得到包覆有致密陶瓷层的工作面。
15.本发明通过热敷的方式在锤头工作面上形成钒的碳化物涂层,涂层与锤头基体之间为冶金结合,结合力很强,形成了致密的v2c陶瓷层,大幅度提高了涂层的力学性能,锤头工作面的硬度能达到hrc50-60,相对耐磨性是基体的8-14倍,能达到铸造的性能的八成,重新安装在锤式破碎机上能有将近三个月的寿命期,板锤能经过多次回收修复使用,本修复设备和方法比较简单,成本低廉,矿石开采企业自己可以配置并操作使用,大幅节省了维修维护的费用和周转运输的费用。
16.本发明的电控系统还包括上位机, plc可编程控制器还包括通讯单元,上位机和通讯单元电联接。所述的上位机用于预先设定控制对象的参数。所述的控制对象是指第一加热单元、第二加热单元或升降液压缸,所述的控制对象的参数是指第一加热单元的加热功率w1、第二加热单元的加热功率w2或升降液压缸的压力f1,根据板锤工作面磨损程度的
不同、使用钒板厚度的不同、板锤基体材质的差异、周围环境温度的差异等等因素,这些控制对象的参数需要调整。
17.本发明还包括触摸屏,触摸屏和通信单元联接;通过触摸屏监控设备的运行状态、修改控制对象的参数。
18.本发明的电控系统还包括信号转换设备、传输设备和信号终端设备;信号转换设备和通信单元联接;其中的信号转换设备把预先设定的控制对象的参数转换成能通过物联网传输的信号;传输设备以物联网为载体;信号终端设备是指可操作智能移动设备,比如手机或者计算机,信号终端设备通过传输单元从信号转换单元获取并远程修改“预先设定的控制对象的参数”,高层管理者可以远程监控本发明的自动运行情况,可以远程调整控制对象的参数。
19.与现有技术相比,本发明的有益效果是:1、板锤基体回收利用,相比重新铸造板锤基体,节省了很多加热能源和劳动力。
20.2、尽管修复后的板锤使用性能比不上在专业加工厂中铸造得到的性能,但是也能使其使用寿命期延长80%,并且还能反复的修复和使用三四次,以低廉的成本使总体寿命期延长三四倍,大幅节省了维修维护的费用和周围转运输的费用。
21.3、本修复设备和方法操作简单,易学易用,造价低,矿石开采企业自己可以配置并操作使用。
附图说明
22.图1是本发明实施例的电路原理框图;图2是本发明实施例的结构示意图;图中:1-砂箱组件;11-砂箱;12-铸造砂;13-第一线圈;14-第一测温传感器;15-密封装置;2-石墨纸;3-钒板;4-板锤;5-搬运机器人;51-横移组件;52-升降液压缸;53-夹持组件;6-力传感器;7-保温箱组件;71-保温箱;711-保温箱盖;72-第二线圈;73-氮气电磁阀;74-第二测温传感器;8-水槽;9-plc可编程控制器;91-数据总线;图1中
①
代表通讯单元的通讯接口,
②
至
⑦
代表数字输入输出接口,
⑧
至
⑩
代表模拟输入接口。
具体实施方式
23.下面将结合实施例及附图,对本发明中的技术方案进行清楚、完整地描述,显然,所描述的实施例仅仅是本发明一部分实施例,而不是全部的实施例。基于本发明中的实施例,本领域普通技术人员在没有做出创造性劳动前提下所获得的所有其他实施例,都属于本发明保护的范围。
24.实施例:一种合金板锤磨损工作面远程控制智能修复设备,如图1-2所示,包括plc
可编程控制器,plc可编程控制器包括cpu单元、模拟输入单元、数字输入单元和数字输出单元;模拟输入单元、数字输入单元和数字输出单元分别通过数据总线与cpu单元联接; 还包括砂箱组件1、搬运机器人5和测力单元;砂箱组件1包括砂箱11、第一加热单元和第一测温传感器14;第一加热单元包括第一线圈13;砂箱11是一个开口朝上的容器,砂箱11内装有铸造砂12;第一线圈13和第一测温传感器14装在砂箱11的壁内;第一线圈13与plc可编程控制器的数字输出单元联接;第一测温传感器14与plc可编程控制器的模拟输入单元联接;搬运机器人5包括横移组件51、升降液压缸52和夹持组件53;横移组件51的支架和机架固定联接,横移组件51的活动部件与力传感器6的上端固定联接,力传感器6的下端和升降液压缸52的上端固定联接,夹持组件53和升降液压缸52的下端固定联接;横移组件51、升降液压缸52和夹持组件53分别与plc可编程控制器电联接;横移组件51驱动升降液压缸52、力传感器6和夹持组件53的组合沿水平方向移动;砂箱11内的铸造砂12上表面做成和板锤4的锤头工作面形状相吻合的凹坑,在凹坑内表面上铺上石墨纸2和钒板3;夹持组件53夹持住板锤4,板锤4的锤头工作面朝下,升降液压缸52驱动板锤4向下平移,板锤4的锤头工作面嵌入凹坑,并保持1500n至4500n的压力,由力传感器6检测并反馈压力信号;然后第一线圈13通电对板锤4的锤头部位加热至1450~1480℃,接近于融熔的温度,在此温度下钒板也软化,锤头工作面和钒板贴合在一起形成高锰钢基体和钒的复合体,外表面还粘附有石墨成份;第一测温传感器14获取锤头工作面的温度,反馈给plc可编程控制器,以便于调整第一加热单元的工作参数。
25.以上所述的板锤4的锤头工作面嵌入凹坑,并保持1500n至4500n的压力是指钒板3厚度是0.3毫米时的压力,钒板3厚度越厚则需要越大的压力,板锤4的锤头部位加热的温度越低则需要越大的压力,以保证钒板3能产生足够大的变形,变形后的钒板3与板锤4的锤头工作面的外形充分贴附在一起。石墨纸2是柔软的,只需要很小的压力就能使它与变形后的钒板3充分贴附在一起。
26.本实施例还包括保温箱组件7,保温箱组件7包括保温箱71、第二加热单元和保温箱盖711,保温箱是开口朝上的容器,第二加热单元包括第二线圈72,板锤4放置在保温箱71里面,第二线圈72与plc可编程控制器的数字输出单元联接,plc可编程控制器发送指令使第二线圈72对板锤4电感应加热;保温箱盖711密封地联接在保温箱71的上口。
27.搬运机器人5把板锤4从砂箱11中取出来,放入保温箱71,相比人工搬运,节省劳动力,提高安全性,工作现场气温非常高,板锤4表面的温度非常高,容易发生烫伤事故,人工操作危险性非常高,工作环境非常恶劣。改成搬运机器人5搬运能避免现场工作的工人受伤,提高生产安全性。
28.本实施例还包括第二测温传感器74,第二测温传感器74安装在保温箱71内,第二测温传感器74与plc可编程控制器的模拟输入单元联接,第二测温传感器74用于检测板锤4表面的温度,以便于确定第二线圈72的加热参数,使板锤4的温度控制在需要的范围内。
29.本实施例还包括通氮气管道,通氮气管道上设置氮气电磁阀73;通氮气管道与保温箱71内腔联通,氮气电磁阀73与plc可编程控制器电联接,通过氮气电磁阀73向保温箱71内腔通入氮气,使板锤4表面不与空气接触,防止板锤4表面氧化。
30.本实施例还包括水槽8,水槽8中装有水,搬运机器人5把板锤4从保温箱71取出来
立刻放入水槽8进行淬火处理。
31.使用本实施例修复板锤4的工作过程如下所述。
32.1)砂箱11内的铸造砂12上表面做成和板锤4的锤头工作面形状相吻合的凹坑,在凹坑内表面上铺上石墨纸2和钒板3,石墨纸2敷贴在凹坑内表面上,钒板3敷贴在石墨纸2上面;2)夹持组件53夹持住板锤4,板锤4的锤头工作面朝下,升降液压缸52驱动板锤4向下平移,板锤4的锤头工作面嵌入凹坑,石墨纸2和钒板3夹在锤头工作面和凹坑表面之间,并保持1500n至4500n的压力,由力传感器6检测并反馈压力信号,以便于调整升降液压缸52的工作参数;在砂箱11内壁与板锤4外侧之间的缝隙中还设置有密封装置15,防止下面的铸造砂12向上溢出,密封装置15还不能妨碍板锤4从中间通过;3)第一线圈13通电对板锤4电感应加热,加热至锤头部位温度在1450℃,并保持二分钟,锤头工作面接近于融熔的温度,在此温度下钒板也软化,锤头工作面和钒板贴合在一起形成高锰钢基体和钒的复合体;第一测温传感器14获取锤头工作面的温度,反馈给plc可编程控制器,根据温度参数调整第一加热单元的工作参数;由于铸造砂12具有流动性,锤头工作面上有不规则的凸起或凹陷,凹坑表面上与凸起接触的铸造砂12能自动流向凹陷处,在铸造砂12的压力作用下锤头工作面、钒板3和石墨纸2紧密地贴合在一起;4)保持4500n的压力,保持一定的接触压强,保持一定的温度,持续一定的时间,然后随室温冷却,得到的板锤4工作面带有梯度复合涂层,而锤头基体是钢基体,外表面还粘附有一层石墨;5)升降液压缸52把板锤4向上提起,离开砂箱11;6)搬运机器人5把板锤4放入保温箱71;7)plc可编程控制器发送指令,开启氮气电磁阀73,通氮气管道向保温箱71中通入氮气,并保持比大气压高100kpa的氮气压力p,使板锤4表面与空气隔离;比大气压高的压力能促使碳元素和钒元素向锤头基体内渗透,提高涂层的附着力;8)第二加热单元加热锤头至1160℃的保温温度t,升温速度控制在7℃/min,保温时间t为11小时;在这个过程中,钒元素、石墨中的碳发生化学反应生成梯度复合涂层即钒的碳化物涂层,所述钒的碳化物涂层包括依次呈梯度分布的准单晶相v2c致密陶瓷层、微米v8c7致密陶瓷层和v8c7与基体的融合层;9)第二测温传感器74获取板锤4的温度,反馈给plc可编程控制器,以便于调整第二加热单元的工作参数;10)板锤4随炉冷却至室温;11)第二加热单元加热锤头至1000℃:第一小时升温至300℃,然后按每小时50℃的速度升温到1000℃,使高锰钢充分进行奥氏体化,保温2小时;12)第二测温传感器74获取板锤4的温度,反馈给plc可编程控制器,以便于调整第二加热单元的工作参数;13)搬运机器人5把板锤4从保温箱71中取出淬入水中,最终得到包覆有致密陶瓷层的工作面。
33.本发明通过热敷的方式在锤头工作面上形成碳化物涂层,涂层与锤头基体之间为冶金结合,结合力很强,形成了致密的v2c陶瓷层,大幅度提高了涂层的力学性能,锤头工作
面的硬度能达到hrc50-60,相对耐磨性是基体的8-14倍,能基本上达到铸造的性能的八成,重新安装在锤式破碎机上能有将近三个月的寿命期,板锤4能经过多次回收修复使用,本修复设备和方法比较简单,成本低廉,矿石开采企业自己可以配置并操作使用,大幅节省了维修维护的费用和周转运输的费用。
34.本实施例的电控系统还包括上位机, plc可编程控制器还包括通讯单元,上位机和通讯单元电联接。所述的上位机用于预先设定控制对象的参数。所述的控制对象是指第一加热单元、第二加热单元、升降液压缸52,所述的控制对象的参数是指第一加热单元的加热功率w1、第二加热单元的加热功率w2、升降液压缸52的压力f1等,根据板锤4工作面磨损程度的不同、使用钒板3厚度的不同、板锤4基体材质的差异、周围环境温度的差异等等因素,这些控制对象的参数需要调整。
35.本实施例还包括触摸屏,触摸屏和通信单元联接;通过触摸屏监控设备的运行状态、修改控制对象的参数。
36.本实施例的电控系统还包括信号转换设备、传输设备和信号终端设备;信号转换设备和通信单元联接;其中的信号转换设备把预先设定的控制对象的参数转换成能通过物联网传输的信号;传输设备以物联网为载体;信号终端设备是指可操作智能移动设备,比如手机或者计算机,信号终端设备通过传输单元从信号转换单元获取并远程修改“预先设定的控制对象的参数”,高层管理者可以远程监控本实施例的自动运行情况,可以远程调整控制对象的参数。
37.以上的第7)、8)和9)步中严格控制保温温度、保温时间和保温压力的关系,获得所述准单晶相v2c致密陶瓷层,该陶瓷层呈现出较为明显的准单晶组织,光学显微镜下表现为晶界减少,影响断裂韧性的位错也相应减少,代之亚晶界增多,有效提高该陶瓷层的抗裂能力。
38.以上的第7)、8)和9)步中严格控制保温温度t、保温时间t和保温压力p与最终能够获得的梯度复合涂层的总厚度符合如下公式,l=kptlogt
1/2
+b0其中:l——梯度复合涂层的总厚度(um)k——是常数,取值为0-1,k≠0,p——氮气压力(kpa),t——保温温度(k),t——保温时间(s),bo——初始厚度(m),即板锤工作在磨损后残留的复合层的厚度。
39.以下表格是矿山生产部门提供的修复板锤与铸造板锤使用寿命统计对照表,两种零件都统计了100件样品。使用寿命/天50-6060-7070-8080-9090-100修复件失效数量/件38183227铸造件失效数量/件036910
40.续表
使用寿命/天100-110110-120120-130130-140140-150总数量/件
修复件失效数量/件102000100铸造件失效数量/件122324121100
从表中可以看出,修复板锤的使用寿命期多数集中分布在80-90天、90-100天这两个使用寿命期间,铸造板锤的使用寿命期多数集中分布在110-120天和120-130天这两个使用寿命期间,铸造板锤在高温液态时进行冶金结合,加工条件优越,修复板锤在高温接近融熔状态时进行冶金结合,加工条件不如前者优越,理所当然地,前者工作面致密陶瓷复合层比较厚、比较均匀、结合力较强,抗磨损能力较强,但是后者也不算太差,综合指标能达到前者的八层。
41.矿山生产部门只给提供了10天一个区间的失效数量统计数据,没提供一天当作一个区间的失效数量统计数据。取各个10天使用寿命区间的中点当作寿命期d,即55、65、75、85、95、105、115、125、135和145天,每个区间的寿命期d与修复板锤的数量相乘再求和,即近似计算出100件修复板锤总的寿命期为:m1=55
×
3+65
×
8+75
×
18+85
×
32+95
×
27+105
×
10+115
×
2=8600天;平均寿命期为:m2=(8600件.天)
÷
(100件)=86天;同样地,对于铸造板锤,近似计算出100件总的寿命期为:n1=65
×
3+75
×
6+85
×
9+95
×
10+105
×
12+115
×
23+125
×
24+135
×
12+145
×
1=11030件.天;平均寿命期为:n2=(11030件.天)
÷
(100件)=110.3天;修复板锤的平均寿命期占铸造板锤平均寿命期的比例为:86
÷
110.3
×
100%=78.0%;花费很小的代价,一次修复就使板锤4的使用寿命延长了78.0%,并且板锤4还可以四至五次修复使用,相当于又延长了三至四倍的寿命期,能为矿山生产企业节省大量的维修维护的费用和周转运输的费用。
42.显然,本领域的技术人员可以对本发明进行各种改动和变型而不脱离本发明的精神和范围。这样,倘若本发明的这些修改和变型属于本发明权利要求及其等同技术的范围之内,则本发明也意图包含这些改动和变型在内。