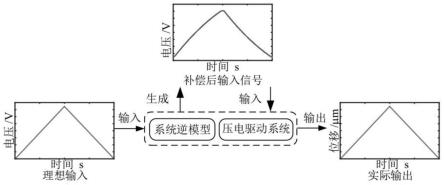
一种基于rayleigh模型的压电驱动系统迟滞非线性抑制方法
技术领域
1.本发明涉及微机电系统技术领域,特别是涉及一种基于rayleigh模型的压电驱动系统迟滞非线性抑制方法。
背景技术:2.压电驱动系统具有刚度高,尺寸紧凑,位移分辨率高,快速响应以及低功耗的优点,已被广泛应用于精密定位、纳米制造系统、原子力显微镜扫描和光学测试等领域。然而,压电驱动系统的定位精度受到由压电陶瓷驱动器固有迟滞特性导致的迟滞非线性的限制,为了减小系统内迟滞作用、提高定位精度,需要对压电驱动系统的迟滞非线性进行控制。目前针对迟滞非线性的控制方法主要有前馈控制方法或反馈控制方法,反馈控制方法具有控制结构简单、可以有效消除状态变量误差等优点,因而被广泛应用于低频和准静态压电驱动系统响应的非线性控制。
3.在高频响应用中,压电驱动系统不确定度增加,传统pid控制方法提供的控制增益难以实现对迟滞非线性的动态补偿,并且也受到建模复杂、逆模型求解困难等缺点的限制。
技术实现要素:4.为了克服上述现有技术的缺点,本发明的目的在于提供一种基于rayleigh模型的压电驱动系统迟滞非线性抑制方法,对压电驱动系统的迟滞和蠕变进行有效控制,具有逆模型建模简单、求解计算简单等优点。
5.为了达到上述目的,本发明采用了如下技术方案:
6.一种基于rayleigh模型的压电驱动系统迟滞非线性抑制方法,包括以下步骤:
7.(1)采用rayleigh模型对压电驱动系统静态迟滞特性进行建模;
8.(2)基于压电陶瓷拟压电系数d
33
与驱动频率对数值线性负相关的物理规律,构建压电驱动系统动态迟滞模型;
9.(3)基于能量法构建迟滞非线性的逆模型,通过前馈控制方法实现动态补偿。
10.所述的步骤(1)使用rayleigh模型表示压电陶瓷应变s(e)与逆压电系数d
33
间关系,表达式为:
[0011][0012][0013]
d(e0)=d
init
+αe0[0014]
其中,d
init
为可逆压电响应系数,α为rayleigh系数,e0为施加电场幅值,e为电场强度;
[0015]
引入压电陶瓷驱动位移d与应变s,电场强度e与电压v,即利用rayleigh模型描述压电陶瓷驱动器位移-电压响应,表达式为:
[0016][0017][0018][0019]
其中,n为驱动器压电层数目,h为驱动器压电层厚度,v0施加电压的幅值。
[0020]
所述的步骤(2)利用了压电陶瓷驱动器位移响应实验平台,基于输入信号电压幅值与逆压电系数相关性测试和输入信号驱动频率与逆压电系数相关性测试,对rayleigh模型进行修正,建立了频率相关rayleigh模型。
[0021]
所述的步骤(2)中利用输入信号电压幅值与逆压电系数进行相关性测试试验数据,使用最小二乘拟合得到d
33
=d
init
+αv0/h以及系数d
init
和系数α的值,最终得到rayleigh表达式。
[0022]
采用两组rayleigh变量分别描述电压上升段及下降段位移响应的建模方法建立非对称迟滞曲线rayleigh系数的求解方法,其表达式为:
[0023][0024][0025]
其中,di为位移上升段rayleigh模型,dd为位移下降段rayleigh模型,d
init
为位移上升段逆压电系数,d
inid
位移下降段逆压电系数。
[0026]
所述的步骤(3)通过在迟滞模型上的数学积分补偿,改变扫描过程的瞬时电压,实现对能量损耗的补偿,使压电陶瓷驱动器实际输出位移等于理论位移。
[0027]
所述的步骤(3)使用二次曲线拟合d
33
,一次线型曲线表达v0随时间变化率,通过升压、降压曲线积分所得能量损失求解得到输入位移补偿信号,其表达式为:
[0028][0029]
其中,d(v)'u为升压补偿曲线,d(v)'d为降压补偿曲线,ω为驱动频率,a0、a、b0、b、d0和d为线型拟合得到系数;
[0030]
系统补偿后输入电压信号表达式为:
[0031][0032]
其中,gv是压电驱动系统位移电压耦合系数。
[0033]
与现有技术相比,本发明具有以下有益效果:由于本发明采取基于rayleigh模型的前馈控制方法,对压电驱动系统的迟滞和蠕变进行有效控制,所以具有算简单、无需大量实验数据、逆模型建模简单、频率相关等优点;满足了现代精密制造对压电定位装置高精度、高跟踪性能的要求,提高了工作效率。
附图说明
[0034]
图1为实施例位移及压电系数测量及拟合结果。
[0035]
图2为实施例压电陶瓷驱动器频率相关测试图。
[0036]
图3为实施例压电驱动系统前馈控制原理图。
[0037]
图4为实施例30hz输入信号时压电驱动系统位移响应及误差图。
具体实施方式
[0038]
下面结合实施例和附图对本发明进行详细说明。
[0039]
一种基于rayleigh模型的压电驱动系统迟滞非线性抑制方法,包括以下步骤:
[0040]
(1)采用rayleigh模型对压电驱动系统静态迟滞特性进行建模:在逆压电响应情况下,对压电陶瓷畴壁不可逆运动造成压电材料迟滞效应,使用rayleigh模型表示压电陶瓷应变s(e)与逆压电系数d
33
之间关系,表达式为:
[0041][0042]
[0043]
d(e0)=d
init
+αe0[0044]
其中,d
init
为可逆压电响应系数,α为rayleigh系数,e0为施加电场幅值,e为电场强度;
[0045]
引入压电陶瓷驱动位移d与应变s,电场强度e与电压v,即利用rayleigh模型描述压电陶瓷驱动器位移-电压响应,表达式为:
[0046][0047][0048][0049]
其中,n为驱动器压电层数目,h为驱动器压电层厚度,v0为施加电压的幅值;
[0050]
(2)基于压电陶瓷拟压电系数d
33
与驱动频率对数值线性负相关的物理规律,构建压电驱动系统动态迟滞模型:
[0051]
利用了压电陶瓷驱动器位移响应实验平台,基于输入信号电压幅值与逆压电系数相关性测试和输入信号驱动频率与逆压电系数相关性测试,对rayleigh模型进行修正,建立了频率相关rayleigh模型;
[0052]
如图1所示,利用大量输入信号电压幅值与逆压电系数进行相关性测试试验数据,使用最小二乘拟合得到d
33
=d
init
+αv0/h以及系数d
init
和系数α的值,最终得到rayleigh表达式;
[0053]
使用相关系数r2作为评价指标定量分析最小二乘拟合结果与实际测量结果之间的关系,其表达式为:
[0054][0055]
其中:di为逆压电系数,为拟合逆压电系数取值,为逆压电系数的平均值;
[0056]
如图2所示,基于在不同频率作用下对压电陶瓷驱动器测试试验数据,采用一阶线性方程来描述频率对数值与rayleigh参数α及逆压电系数初始值d
init
之间的关系,表达式为:
[0057]
α(ω)=a0+aln(ω)
[0058]dinit
(ω)=d0+dln(ω)
[0059]
其中,ω为驱动频率,a0、a、d0和d为线型拟合得到系数;
[0060]
根据频率对数值与rayleigh参数α及逆压电系数初始值d
init
之间的关系,可得到频率相关rayleigh模型,表达式为:
[0061]
[0062][0063]
采用两组rayleigh变量分别描述电压上升段及下降段位移响应的建模方法建立非对称迟滞曲线rayleigh系数的求解方法,其表达式为:
[0064][0065][0066]
其中,di为位移上升段rayleigh模型,dd为位移下降段rayleigh模型,d
init
为位移上升段逆压电系数,d
inid
位移下降段逆压电系数;
[0067]
对建模精度进行评价,将实验数据及其相关时域rayleigh模型进行对比,不同电压幅值作用下的非对称迟滞曲线建模误差如表1所示,随着驱动电压的增加,rayleigh模型的误差也逐渐增加,最大误差发生在v0=80v时,误差大小为43.80nm,占位移量的6.04%。
[0068]
表1不同幅值下rayleigh模型的误差
[0069][0070]
(3)基于能量法构建迟滞非线性的逆模型,通过前馈控制方法实现动态补偿:
[0071]
通过在迟滞模型上的数学积分补偿,改变扫描过程的瞬时电压,实现对能量损耗的补偿,从而使压电陶瓷驱动器实际输出位移等于理论位移;
[0072]
压电驱动系统rayleigh模型前馈信号构建如图3所示,使用二次曲线拟合d
33
,一次线型曲线表达v0随时间变化率,通过升压、降压曲线积分所得能量损失求解得到输入位移补偿信号,其表达式为:
[0073][0074]
其中,d(v)'u为升压补偿曲线,d(v)'d为降压补偿曲线;
[0075]
系统补偿后输入电压信号表达式为:
[0076][0077]
其中,gv是压电驱动系统位移电压耦合系数。
[0078]
本实施例所用仪器设备:压电驱动模块主要由柔性机构、pi p-887.51压电陶瓷驱动器、pi e-836.1g压电陶瓷控制器组成;测量模块由micro-epsilon capancdt6110位移传感器和位移传感器控制器组成;数据采集模块由ni-pxi6133pxi采集卡和ni-pxi 1031主机组成。
[0079]
实验结果如图4所示:当输入信号频率为30hz时,位移响应误差为10.16%,位移响应上升段和下降段与参考信号的相关系数r2分别为(0.99446,0.99288)。通过信号补偿方法可以实现系统非线性有效控制,将位移响应相关系数r2提高为(0.99955,0.99942),位移误差降低为3.53%。