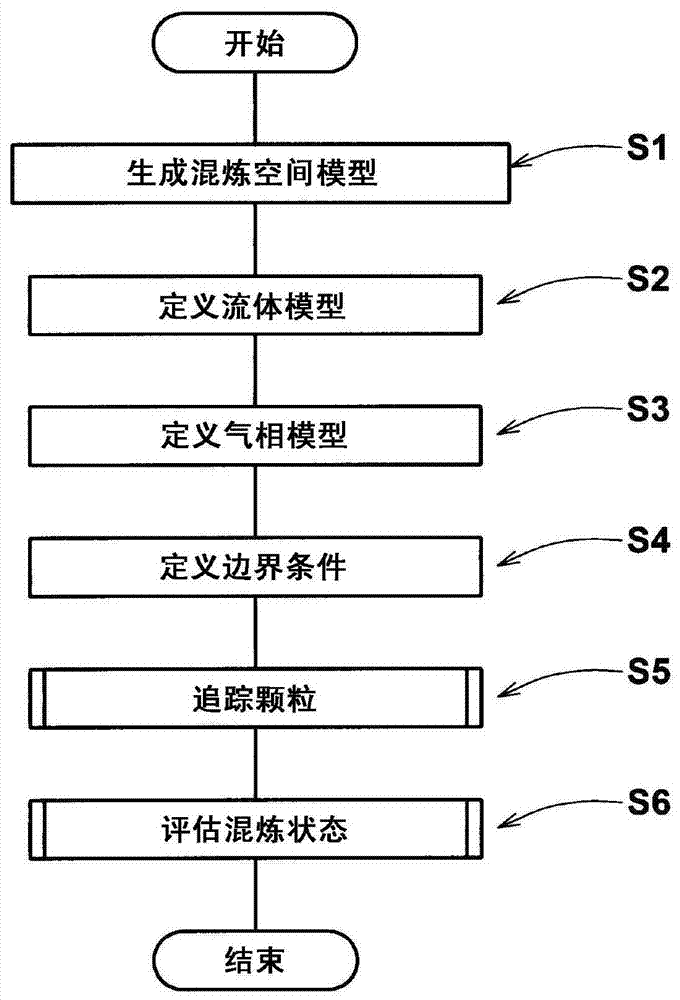
本发明涉及有助于分析流体混炼状态的计算机模拟方法。
背景技术:为了制备待进行交联处理的橡胶或树脂,通常使用班伯里混炼机来混炼用于混合的成分,即聚合物材料、各种添加剂等。在这种混炼工艺中,重要的是以较短的时间均一地混炼用于混合的成分。为此,已经通过需要较高研发成本的试错法(trial-and-errormethod)进行了各种关于其内混炼空间(小室)和转子的形状的研发。因此,近年来,建议使用各种计算机数值模拟。例如,在如下的非专利文献1中,已经建议一种数值模拟,用于在使用班伯里混炼机混炼期间计算塑性材料比如交联前的未硫化橡胶和树脂的流动性。[非专利文献1]“团聚物分散混合的数值和试验研究”,V.Collin(1)*,E.Peuvrel-Disdier(1)等。在如下非专利文献2中,已经建议通过数值模拟来定量地获得塑性材料的混炼状态,其中当前混炼状态与理想的均一混炼状态被比较、并被量化。[非专利文献2]“小组分尺寸的分散和分布以及连续聚合物加工装置中的空间分布的分析”,WinstonWang和IcaManasloczower。在非专利文献2的方法中,理想的均一混炼状态被定义为使得小室或混炼空间完全充满塑性材料,即填充率为100%。然而,在实际混炼工艺中,填充率低于100%。因此,非专利文献2中定义的理想混炼状态没有代表正确的理想混炼状态。例如,如果填充率降低,那么相对于填充率为100%的状态,保留在混炼空间的内表面附近的塑性材料的百分比变高。即,如果填充率降低,那么理想的混炼状态应根据其发生变化使得塑性材料向内表面转移。因此,基于非专利文献2中理想的混炼状态独立于填充率的假定,分散状态被评估为随着填充率的降低而变差是可能的。
技术实现要素:因此,为了解决上述问题,研究出本发明,并且本发明的目的在于提供一种计算机模拟方法,通过该模拟方法可以准确地评估塑性材料的混炼状态,从而可提高开发混炼机器等的效率。根据本发明,用于评估流体混炼状态的计算机模拟方法包括:生成混炼空间模型的步骤,该混炼空间模型是流体在其内被混炼的混炼空间的有限元模型;定义流体的流体模型的步骤;定义混炼空间模型中填充率低于100%的流体模型、并且定义所需混炼条件的步骤;颗粒追踪步骤,其中流体模型的流动计算基于混炼条件进行,并且设置在流体模型中的虚拟颗粒被追踪;评估步骤,其中虚拟颗粒的位置数据与流体模型的理想混炼状态中的那些位置数据被比较,并且流体模型的混炼度被计算;其中,基于颗粒追踪步骤中算出的流体模型的存在位置,在评估步骤中计算理想混炼状态。进一步地,根据本发明的方法可包括如下特征:颗粒追踪步骤包括其中多个第一虚拟颗粒在混炼空间模型中被设置的步骤、其中基于流体模型的物理量移动第一虚拟颗粒的步骤、以及其中第一虚拟颗粒的位置数据被储存的步骤;评估步骤包括其中多个第二虚拟颗粒被任意地/均一地固定设置在混炼空间模型中的步骤、其中由颗粒追踪步骤中追踪的位置计算当前流体模型停留的位置的步骤、以及其中基于停留在流体模型的存在位置处的第二虚拟颗粒定义理想混炼状态的步骤;以及评估步骤进一步包括其中基于第一虚拟颗粒的设置与第二虚拟颗粒的设置之间的符合度来计算流体模型的混炼度的步骤。因此,通过实质上不需要试验性地制造混炼机器的该方法就可对流体的混炼状态进行精确地定量评估。于是,可极大地提高开发效率。附图说明图1为用于混炼塑性材料的班伯里混炼机的主要部分的横截面示意图。图2为显示作为本发明的实施方式的模拟方法的流程图。图3为混炼空间模型的透视图。图4为混炼空间模型的横截面图。图5为单独地显示混炼空间模型的功能部分的横截面图。图6为显示其中流体模型和气相模型被设置的混炼空间模型的状态的横截面图。图7为颗粒追踪步骤的例子的流程图。图8为用于说明颗粒追踪的图表。图9(a)-9(f)为可视化的被追踪的颗粒位置,其中其运动按时间顺序(chronologicalorder)显示。图10为评估步骤的例子的流程图。图11为用于说明颗粒间距离的图。图12为显示颗粒间距离频率分布的直方图。图13为显示实际混炼状态以及理想混炼状态中颗粒间距离频率分布的直方图。图14(a)为显示通过本发明的颗粒追踪步骤获得的实际混炼状态中的第一虚拟颗粒的图。图14(b)为显示与实际混炼状态对照的理想混炼状态中的第二虚拟颗粒的图。图14(c)为显示通过现有技术的模拟方法获得的理想混炼状态中的第二虚拟颗粒的图。图15(a)为显示作为本发明的实施方式的模拟方法的结果的图。图15(b)为显示现有技术的模拟方法的结果的图。具体实施方式现在结合附图对本发明的实施方式进行详细地说明。本发明致力于一种分析方法,用于通过使用计算机(未显示)来评估流体的混炼状态。例如,在塑模橡胶材料或数值材料之前,进行混炼。在混炼期间,原料比如化学品、细颗粒等用液体粘合剂润湿,并均一地分散成均一混合物。这种混炼工艺典型地通过图1所示的班伯里混练机1进行。班伯里混练机1包括:外壳2,其限定在其内原料比如橡胶材料等被捏合的混炼空间4的内表面,以及一对转子3,其可在混炼空间4内旋转。该例子中的混炼空间4具有类似数字8的截面形状。然而,混炼空间不限于这种形状。该实施方式中的流体是粘度与交联前的未硫化橡胶类似的塑性材料。然而,流体不限于具有塑性的未硫化橡胶、树脂、弹性体等。流体可是任何材料,只要其具有稳定的流体状态即可。在交联前的未硫化橡胶的情况中,在约80℃处充分混炼的混合物的状态可被认为是稳定的流体状态。图2显示了作为本发明的实施方式的方法的流程图。根据该流程图,该方法如下所述。*生成混炼空间模型的步骤S1首先,作为由有限数量的单元或元素构成的混炼空间4的有限元模型的混炼空间模型5通过计算机生成并被储存。图3显示了混炼空间模型5的透视图。图4显示了混炼空间模型5的横截面图。如图所示,混炼空间模型5对应于用外周面5o、内周面5i以及沿轴向在转子3两侧的两端表面5s封闭的三维闭合空间,其中外周面5o被外壳2的内表面限定,内周面5i被一对旋转的转子3的外周面限定。该三维闭合空间被分割成三维单元(e)比如四面体单元、六面体单元以及多面体单元作为Euler单元。对于每个单元,计算流体的物理量比如压力、温度和/或速度。外周面5o和两端表面5s不发生移动。然而,内周面5i根据转子3的旋转而移动,于是,混炼空间模型5的形状发生变化。在图5所示的例子中,混炼空间模型由如下四个功能部分构成:一对旋转部分5A和5B,夹在转子之间的中间部分5C,以及围绕这些部分5A、5B和5C的外部框架部分5D。各个旋转部分5A/5B是管状的,并且具有圆柱形的圆周表面5Ao/5Bo和对应于一个转子3的圆周表面的内周面5i。旋转部分5A和5B位于外部框架部分5D中,并被定义为可围绕各个中心轴Oa和Ob旋转,从而代表混炼空间4的体积形状因转子3的旋转而导致的变化。相反,中间部分5C在旋转部分5A与5B之间保持静止不动,并且具有两个邻接各个旋转部分5A和5B的凹面j。在凹面j和各个圆柱形的圆周表面5Ao和5Bo上,作为滑动表面的边界条件被定义。这允许发生在旋转部分5A和5B中的物理行为(力、热等)经由凹面j被传送到存在于中间部分5C中的流体模型。外部框架部分5D是管状的,并且围绕旋转部分5A和5B以及中间部分5C。其两个轴端被两端表面5s封闭。在外部框架部分5D与旋转部分5A和5B之间的界面上,以及在外部框架部分5D与中间部分5C之间的界面上,作为滑动表面的边界条件被定义。这允许发生在旋转部分5A和5B中的物理行为(力、热等)经由其间的界面被传送到外部框架部分5D。外部框架部分5D因转子的操作而经受相对较大的剪切力。因此,为了更详细地计算材料的速度等,优选构成外部框架部分5D的单元在尺寸上被设置成比旋转部分5A和5B以及中间部分5C的尺寸更小。借此可更详细地计算混炼空间模型5的内表面附近的流体模型的速度剖面等。*定义流体模型的步骤S2接下来,通过计算机定义流体模型并储存。流体模型是在混炼空间4中流动或移动的流体的模型。在流体模型中,流体的物理性能比如剪切粘度、比热、热导率以及比重在计算机中被定义并被储存。如上所述,该实施方式中的流体是塑化状态的橡胶混合物,因此,这种橡胶混合物的物理性能被预先输入并储存。至于剪切粘度,分析对象(塑性材料)的粘弹性性能G’和G”在多个温度条件下被测定,并且根据Cox-Merz规则通过转换粘弹性性能而获得剪切粘度。上述获得的剪切粘度η根据幂律用下述表达式(1)进行近似。表达式(1):η=mγ'n-1其中,m:作为绝对温度T的函数的系数,γ':剪切速度,n:系数。分析对象(塑性材料)的比热可通过热绝缘连续加热方法(在25℃)获得,并且将测定的比热值预先输入电脑中并储存。分析对象(塑性材料)的热导率可通过热丝(hotwire)方法(在25℃)获得,并且将该测定值预先输入电脑中并储存。*定义气相模型的步骤S3接下来,通过计算机定义气相模型并储存。气相模型是存在于混炼空间中的气体的模型。在本发明中,混炼空间模型5中流体模型的填充率低于100%,因此,为了可进行流动计算,未被流体模型填充的部分用气相模型填充。在气相模型上,气体的粘度和比重被定义并被储存在计算机中。*定义边界条件的步骤S4接下来,定义用于进行流动计算所需的各种条件比如边界条件。边界条件包括在混炼空间模型5的表面处的流动速度边界条件和温度边界条件。至于流动速度边界条件,根据模拟的目的、所需精确度等定义(a)壁面无滑移条件或(b)壁面滑移条件。在壁面无滑移条件的情况中,混炼空间模型5表面处的流体模型的流动速度始终为零。在壁面滑移条件的情况中,混炼空间模型5表面处的流体模型的流动速度可具有非零值以及零值。在该情况中,在流体模型与混炼空间模型5之间的界面处的滑移现象可根据纳维定律(Navier’sLaw)被模拟。至于温度边界条件,可根据模拟的目的、所需精确度等定义(a)热绝缘条件,其中热量不会经由其表面从混炼空间模型5中逸出,或者(b)其中混炼空间模型5的整个表面具有恒定温度(例如50℃)的条件。进一步地,条件可包括流体模型的初始温度、用旋转部分5A和5B的旋转数表示的转子的旋转数、混炼空间模型5的表面的滑移率、流体模型相对于混炼空间模型5体积的填充率(低于100%)等。更进一步地,条件可包括流动计算的初始状态、用于计算的时间间隔、内部处理中的重复数、计算的最大周期(重复)等。此外,可定义作为模拟结果输出的各种参数。至于初始状态,例如,如图6所示,可以定义成使得在水平界面S(其被定义为延伸穿过混炼空间模型5)的上侧的区域A为气相模型,并使得在水平界面S的下侧的区域M为流体模型。因此,通过改变该界面S的水平(level),可调节流体模型的填充率。*追踪颗粒的步骤S5接下来,进行颗粒追踪步骤S5。图7显示了颗粒追踪步骤S5的例子的流程图。**步骤S51在颗粒追踪步骤中,首先,计算机根据混炼条件使用混炼空间模型5和流体模型进行流动计算。流动计算可使用通用流体分析软件进行。通过流动计算,对于混炼空间模型5中的每一单元,获得用于限定流体运动状态的沿三维轴向(x、y、z)的速度分量以及用于限定流体内部状态的温度T和压力p。因此,这5个物理分量是待解的未知量。由此,计算流动场。**步骤S52接下来,将通过流动计算算出的时间步骤t处的流动场载入计算机中。“流动场”是其中物理量比如速度、压力和密度(通过这些物理量可确定在任意时刻处某一区域(在本案中,为混炼空间模型)中流体的流动)已经被限定的场。**步骤S53接下来,计算机设置或定义在混炼空间模型5内特定位置处的第一虚拟颗粒的具体数量。在数值模拟中,第一虚拟颗粒被定义为如下虚拟颗粒:其没有尺寸和质量,并且对流体模型的流动计算没有影响,并且进一步地根据流体模型的流动而是可移动的。因此,通过使用第一虚拟颗粒的位置数据,可以追踪第一虚拟颗粒,从而获知流体模型的流体化状态。为了获知流体模型的混炼(分散)度,优选第一虚拟颗粒的数量为至少几百,更优选为500以上。第一虚拟颗粒的位置可在混炼空间模型5内任意地设置。其数量和位置在定义边界条件的步骤S4之前定义。**步骤S54接下来,根据关于第一虚拟颗粒的速度的数据,计算机计算第一虚拟颗粒在下一时间步骤t+1处的位置。如图8所示,该计算按如下所述进行。在图8中,仅一个第一虚拟颗粒P1被图示。然而,计算机对每个第一虚拟颗粒进行如下处理。在时间步骤t处,第一虚拟颗粒P1在位置(Xt、Yt、Zt)处。在时间步骤t处的流动场中,在位置(Xt、Yt、Zt)处的流体模型具有其x、y和z分量分别为Vx(t)、Vy(t)和Vz(t)的速度。计算机使用如下表达式计算第一虚拟颗粒P1在下一时间步骤t+1处的位置(Xt+1、Yt+1、Zt+1):Xt+1=Xt+Vx(t)×T,Yt+1=Yt+Vy(t)×T,以及Zt+1=Zt+Vz(t)×T,其中,T为时间步骤t与时间步骤t+1之间的时间间隔。**步骤S55接下来,计算机计算流体模型在计算位置(Xt+1、Yt+1、Zt+1)处的体积分数。在本发明中,需要同时处理两种流体,这两种流体是存在于混炼空间模型5中的气相模型和流体模型。因此,在该实施方式中,用于计算具有自由界面的流动的VOF(流体体积)方法被采用。VOF方法不直接计算两种流体之间的界面的运动。在VOF方法中,自由界面通过定义体积分数来表示,该体积分数相当于在混炼空间模型5的每一单元的体积内流体模型的填充率。因此,如果关于任意单元的流体模型体积分数为0,那么这意味着该单元的整个体积充满气相模型。如果关于任意单元的流体模型体积分数为1(最大值,填充率为100%),那么这意味着这该单元的整个体积充满流体模型。**步骤S56接下来,计算机判断上述体积分数是否不低于预定值比如约0.5。于是,“YES(是)”意味着流体模型实质上存在于第一虚拟颗粒在下一时间步骤t+1处向其移动的位置处。“NO(否)”意味着流体模型在该位置处实质上不存在。**步骤S57如果步骤S56中的结果是“YES”,那么根据关于第一虚拟颗粒的新的计算位置处的速度的数据,计算机计算第一虚拟颗粒在再下一个时间步骤t+2处的位置。**步骤S59如果步骤S56中的结果是“NO”,那么计算机删除关注的第一虚拟颗粒。换句话说,对于被移入气相模型的被关注的第一虚拟颗粒,计算机结束追踪。**步骤S58接下来,计算机判断上述处理是否重复预定数量的时间。该数量基于追踪第一虚拟颗粒的经过时间是否充足来确定。如果步骤S58中的结果为“NO”,那么计算机再次进行步骤S55以及随后的步骤。如果步骤S58中的结果为“YES”,那么计算机进行如图2所示的评估步骤S6。在该时刻,时间步骤的当前数量为L。图9(a)-9(f)显示了颗粒追踪步骤S5的结果,其中第一虚拟颗粒P1(用黑点表示)的运动按时间顺序显示。如图所示,其被较好地模拟为第一虚拟颗粒随着混炼进程而被分散。**步骤S6在评估步骤S6中,计算机通过比较第一虚拟颗粒的位置数据与混炼空间模型5中流体模型的理想混炼状态来计算流体模型的混炼度。基于在颗粒追踪步骤S5中算出的流体模型的存在位置,计算理想混炼状态。图10显示了通过计算机进行的评估步骤S6的流程图。**步骤S61在评估步骤中,首先,计算机将颗粒追踪步骤S5中获得的数据读入存储器中。读入数据包括各个第一虚拟颗粒的三维坐标和速度。**步骤S62接下来,计算机计算在时间步骤的当前数量L处第一虚拟颗粒之间的距离,然后计算距离的频率分布。在图11中,包含于流体模型M的任意区域中的多个第一虚拟颗粒用圆圈表示。在步骤S62中,针对在混炼空间模型5中被追踪的第一虚拟颗粒的每一组合,计算距离。图12为显示频率分布的直方图,其中纵轴表示频率,横轴表示对应于颗粒间距离的组(class)。频率分布可表示为如下表达式2。表达式2:其中,"p"为表示概率的函数,"eps"为用于获得频率分布的组(颗粒间距离)的组间宽度(classintervalwidth)的1/2,"N"为第一虚拟颗粒的数量,i和j为说明第一虚拟颗粒的标号,"l"为两个第一虚拟颗粒i与j之间的距离,是其值为1或0的变量。如果i≠j从而在l-eps与l+eps之间存在颗粒,那么变量如果i=j,那么变量下标“calc”是指实际混炼状态。**步骤S63接下来,计算机计算在时间步骤为当前数量L处的理想混炼状态。在该步骤S63中,首先,针对混炼空间模型5的整个三维空间区域,计算机在混炼空间模型5内均一固定地设置多个第二虚拟颗粒。在该数值模拟中,第二虚拟颗粒被定义为如下虚拟颗粒:其没有尺寸和质量,并且不对流动计算产生影响。例如,第二虚拟颗粒的均一设置可通过利用随机函数而产生。第二虚拟颗粒的数量可任意地确定。然而,优选其数量被设置为与第一虚拟颗粒相当的范围内。接下来,根据颗粒追踪步骤S5的计算结果,计算机计算流体位置或当前流体模型存在的位置。具体地讲,对混炼空间模型5中的每一单元,计算流体模型的体积分数。如果其体积分数不低于预定限值(例如50%),那么可判断当前流体模型存在于所关注的单元的位置处。接下来,仅基于停留在通过上述步骤获得的流体位置处的第二虚拟颗粒,计算机可定义理想混炼状态。具体地讲,计算机会删除所有未停留在流体位置处的第二虚拟颗粒。相应地,仅停留在流体位置处的第二虚拟颗粒被保留。通过上述步骤,计算机可获得用于当前流体模型存在位置的理想混炼状态(均一的分散状态)。**步骤S64接下来,对于上述步骤中算出的处于理想混炼状态的第二虚拟颗粒,计算机计算第二虚拟颗粒之间的距离,然后计算该距离的频率分布。在该步骤中,针对停留在混炼空间模型5中流体位置处的第二虚拟颗粒的每一组合,计算颗粒间的距离。频率分布用如下表达式3表示。表达式3:其中,此处使用的符号与表达式2中的那些符号相同,但“第一虚拟颗粒”应用“第二虚拟颗粒代替。下标"optimum"是指理想混炼状态。**步骤S65接下来,计算机通过比较第一虚拟颗粒的位置数据与理想混炼状态的第二虚拟颗粒的位置数据来计算流体模拟的混炼度。在该实施方式中,基于第一虚拟颗粒的设置与第二虚拟颗粒的设置之间的符合度来计算流体模型的混炼度。于是,混炼度DMI用如下表达式4表示。表达式4:在表达式4中,如图13所示,DMI作为理想混炼状态(由第二虚拟颗粒之间的距离算出)的频率分布(概率函数poptimum)与实际混炼状态的频率分布(概率函数pcalc)(由第一虚拟颗粒之间的距离算出)之间的差值获得。于是,随着DMI的降低,实际混炼状态变得更接近理想混炼状态。如上所述,根据本发明,塑性材料的流体模型的混炼状态可通过进行数值模拟而获得。由于流体模型的当前混炼状态与其理想混炼状态被比较,故有可能定量地获得当前混炼状态。特别地,根据本发明,由于流体模型的混炼状态是基于颗粒追踪步骤S5中算出的流体模型的存在位置而计算的,故可以精确地定量评估流体的理想混炼状态以及相应的混炼状态。在图14(a)-14(c)中,被中心线围绕的是存在流体模型的区域。图14(a)示意性地显示颗粒追踪步骤S5中获得的某一时间步骤处的实际混炼状态,其中较小的白圆圈表示第一虚拟颗粒。图14(b)示意性地显示评估步骤S6中获得的在与图14(a)相同的时间步骤处的理想混炼状态,其中较小的白圆圈表示第二虚拟颗粒。在本发明中,第一虚拟颗粒与第二虚拟颗粒之间的符合度被计算。图14(c)示意性地显示了通过现有技术方法获得的在与图14(a)相同的时间步骤处的理想混炼状态,其中较小的白圆圈表示第二虚拟颗粒。如图所示,与流体模型的存在位置无关地,第二虚拟颗粒被均一地分布。于是,该理想混炼状态是不正确的。因此,通过与这种理想混炼状态比较而获得的模拟结果是不可靠的。对比试验为了确认本发明的有利效果,使用图3-5所示的混炼空间模型、以及未硫化橡胶的流体模型,在如下条件下进行混炼模拟。流体模型的填充率:70%和80%(两种模型被使用)旋转部分(转子)的旋转数:30rpm第一虚拟颗粒的数量:10,000第二虚拟颗粒的数量:10,000第一虚拟颗粒和第二虚拟颗粒的初始位置:在混炼空间模型的中心部分混炼持续时间:20分钟(实际时间)图15(a)显示了试验结果,其显示作为通过本发明实施方式所述的方法获得的经过时间的函数的混炼度DMI变化。图15(b)显示了试验结果,其显示作为通过现有技术方法获得的经过时间的函数的混炼度DMI变化,该现有技术方法基于如上所述的不考虑流体模型存在位置而定义的理想混炼状态。现有技术方法中的试验结果显示出较强的如下趋势:当填充率较低(70%)时,DMI值变得较高,即混炼度变差。根据本发明的方法的试验结果显示,因填充率变化而导致的DMI值改变相对较小,因此,可避免现有技术方法的如下缺陷:当填充率较低时,与实际状态相比,混炼度被估计得更差。